Do you ever think about why some plastic items just do not last as expected?
Bad pretreatment harms injection molded items. It weakens their strength, ruins the nice surface and reduces their resistance to chemicals. These problems result in products failing design requirements and really lowering their performance. Products might not meet expectations.
I recall a time when we ignored the drying process for our material only once and it was a big mistake. The product lost strength because bubbles formed inside. We learned this after a few items came back broken. This taught me that these early steps are really important. Each piece needs to be as good as promised.
Problems from improper pretreatment often appear in the final product. Reduced strength is one issue. Poor weather resistance is another. Each problem teaches a valuable lesson. It is crucial to understand these issues. Solving them helps improve the final result.
Improper pretreatment reduces mechanical strength.True
Materials not properly pretreated can lead to weaker product structures.
Pretreatment has no effect on surface quality.False
Surface defects often result from inadequate material preparation.
What are the mechanical consequences of poor pretreatment?
Recall when you missed an important step and everything went wrong? In manufacturing, poor preparation is very similar – it probably leads to even bigger problems.
Avoiding proper pretreatment can really mess up your product’s strength and toughness. Products might not work as you hope if you skip this step. Thorough pretreatment is very important.
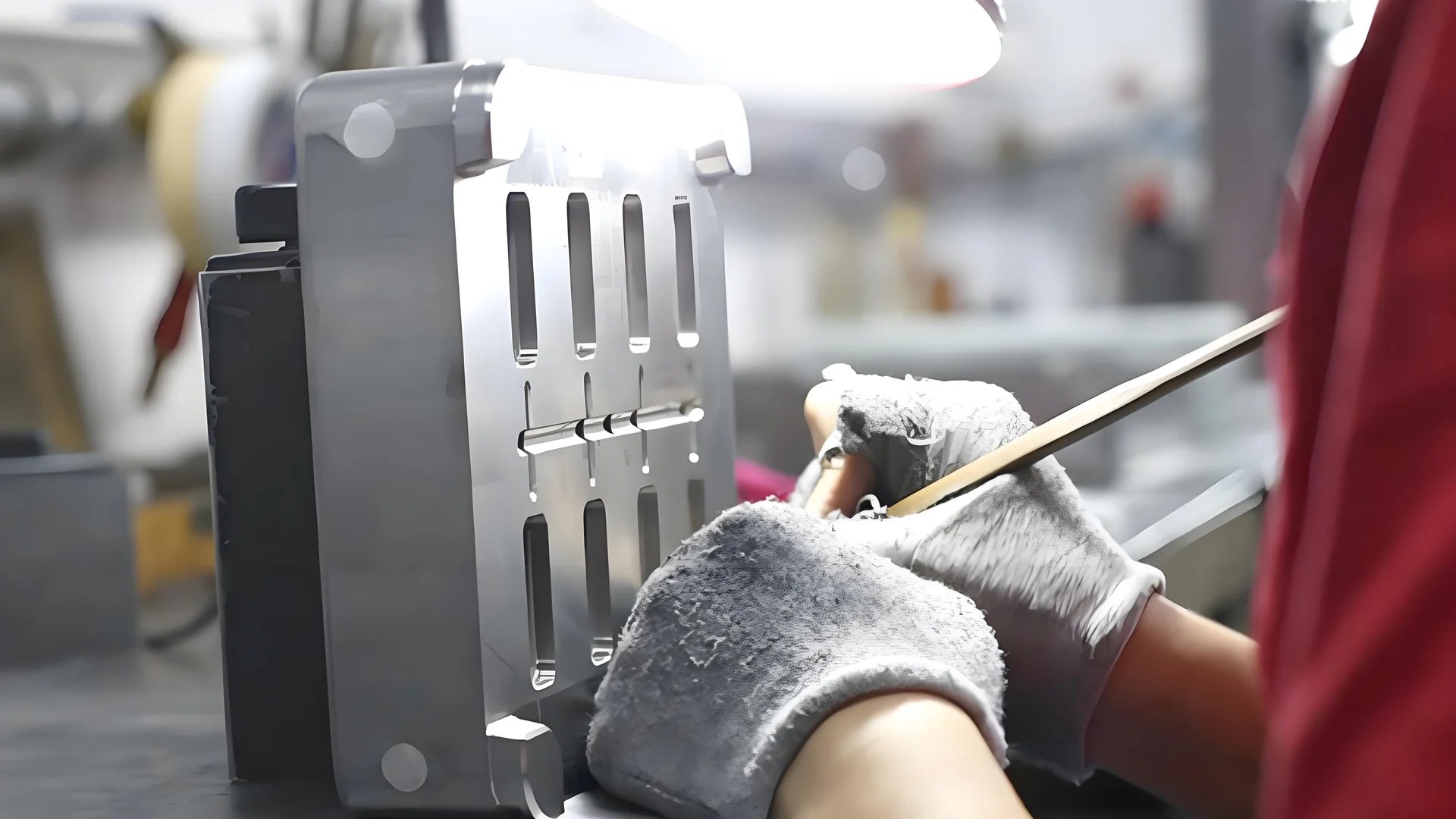
Reduced Strength and Durability
I remember a project when we did not dry the materials well before shaping them. At the time, it looked like a small issue, but those tiny bubbles inside? They turned a strong structure into something much weaker. Those strong car parts couldn’t take the stress and pressure they were meant for. This lesson showed me that good drying is key to keeping strength in different forms.
Think of it like baking a cake without mixing the batter right. You get lumps and uneven texture. In the same way, uneven mixing of support elements can create weak spots. These weak spots break under pressure first.
Mechanical Property | Consequence of Poor Pretreatment |
---|---|
Compressive Strength | Significant reduction |
Tensile Strength | Reduced |
Flexural Strength | Decreased |
Deteriorated Toughness
Once, I hurried through heating, making the temperature too high. That heat stress caused cracks and made parts brittle, which could have been avoided. It was like baking bread too hot – things become brittle and break quickly.
Improper preheating can lead to thermal stress, affecting the product’s toughness. This stress alters the molecular chain structure, weakening bonds between chains. Consequently, the material loses its ability to absorb impact energy efficiently,
leading to cracking and brittleness.
Hardness Variations
In a rush, I once failed to mix fillers evenly, causing some parts to be much harder than others. Imagine biting into a cookie and finding just one big chocolate chunk. It doesn’t taste as good as one might think. This unevenness affected the product’s resistance to wear, which is very important for precise tools.
Uneven mixing during pretreatment can cause varied hardness across a product.
Areas with concentrated fillers might become excessively hard while others remain soft.
This unevenness affects wear resistance and deformation resistance crucial for precision instruments or any product requiring uniform hardness.
Appearance and Surface Quality
Appearance is important. I’ve seen moisture ruin surfaces, leaving ugly streaks on sleek surfaces. These flaws not only looked bad but also signaled deeper issues. It’s like getting a new phone with a scratched screen – instantly disappointing.
- Surface Defects: Moisture and bad mixing cause these issues.
- Dimensional Accuracy: Inner stress causes deformation affecting assembly precision in products like electronic cases.
Chemical Performance Implications
One project taught me that ignoring pretreatment allows corrosion at weak spots. It’s like leaving a bike in the rain and not drying it – rust starts unexpectedly.
Deficient pretreatment can compromise chemical resistance by creating weak spots where corrosion can initiate.
in environments exposed to corrosive substances; these spots become points of failure accelerating degradation.
Knowing these issues is very important for designers like me; understanding these mechanical consequences1 is critical to achieving both functional and aesthetic goals in product design.
Poor pretreatment reduces tensile strength.True
Insufficient drying and uneven mixing lead to decreased tensile strength.
Uneven hardness improves wear resistance.False
Uneven hardness negatively affects wear resistance, causing inconsistency.
Why Does Surface Quality Suffer with Poor Material Preparation?
Have you ever thought about why some products fail to last long? The tiny details in how materials are prepared probably play a big role.
Poor material preparation results in surface problems such as lines, roughness, weak strength and inaccurate sizes. Drying, mixing and preheating really help maintain excellent surface quality. Drying, mixing, preheating – these steps are crucial.
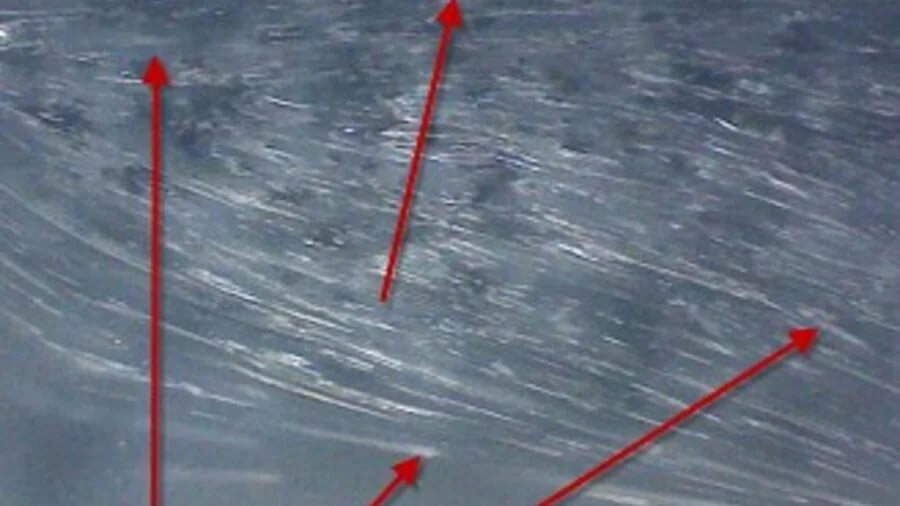
The Role of Material Preparation in Surface Quality
Material preparation is setting the stage for perfection in manufacturing. Imagine a chef who carefully prepares ingredients before cooking. Each step – drying, mixing, preheating – matters for success. These steps help create a product without defects, similar to crafting the perfect dish.
Mechanical Properties and Surface Degradation
- Reduced Strength: Think of a cake with bubbles weakening it – it collapses. Bad drying creates bubbles in materials, weakening things like car parts2. These parts might fail under stress exactly when you need them most.
- Uneven Mixing: Have you baked with poorly mixed ingredients? Some parts taste bland, others too salty. This inconsistency in mixing causes weak spots, leading to early failure.
Appearance Performance
- Surface Defects: Improper drying traps moisture, making silver streaks on items. It’s like a beautiful painting with water stains. These defects hurt looks and suggest hidden structural problems.
- Color Uniformity: Recall painting a wall and seeing patchy colors halfway through? Uneven mixing in materials can cause similar issues with color or texture.
Dimensional Accuracy
Imagine building a puzzle but pieces do not fit due to warping. Incorrect preheating or drying can deform products, affecting their precision. Accuracy is vital for things like electronic casings.
Factor | Effect on Surface Quality |
---|---|
Drying | Prevents bubble formation |
Mixing | Ensures uniform strength and appearance |
Preheating | Reduces internal stresses |
Chemical Performance
- Corrosion Resistance: Just like metal rusts in rain, bubbles from bad mixing leave products open to chemical harm.
- Weather Resistance: Remember leaving a toy outside and finding it faded and cracked? Weakness in materials makes products prone to environmental damage.
Knowing these details in material preparation3 helps in creating reliable and long-lasting products with high aesthetic standards. By tackling these preparation problems, defects are reduced, improving performance and user satisfaction.
Improper drying causes surface silver streaks.True
Moisture entrapment from poor drying leads to silver streaks on surfaces.
Uneven mixing enhances product strength.False
Inconsistent mixing creates weak points, reducing overall product strength.
How Does Improper Pretreatment Affect Dimensional Accuracy?
Minor mistakes in preparing materials sometimes ruin whole projects. Focusing on the details is really important. Ignoring small things often leads to very big problems. Remember, every little step matters.
Improper pretreatment harms the size accuracy of materials. This results from internal stresses and uneven mixing. These problems change the material’s shape. A product that isn’t precise can’t serve its purpose well.
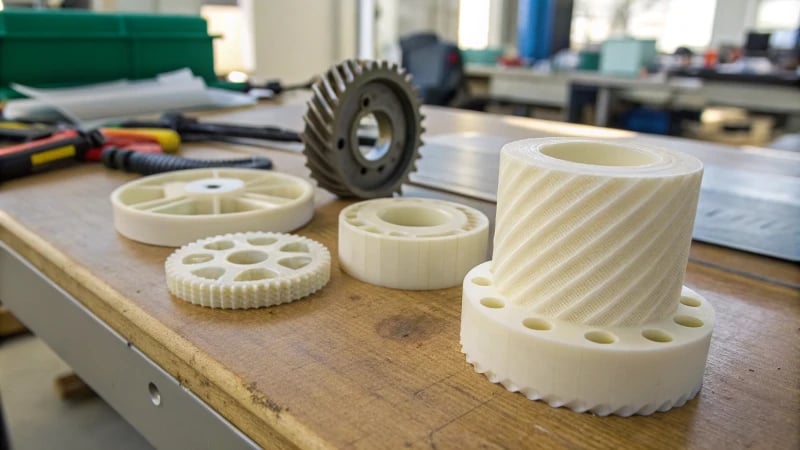
Understanding Dimensional Accuracy
Dimensional accuracy is the overlooked champion in making things and 3D printing, yet it’s essential. When designing parts for gadgets or custom molds, every tiny bit matters. Exactness is key. Precision means everything fits just right. No one wants the dreaded "Doesn’t Fit!" moment. Precision is crucial. This separates products that work well from costly mistakes.
Internal Stress and Its Impact
Once, I rushed a project and skipped vital material preparation steps. I learned the hard way how internal stress creates chaos. Poor preparation, like too much preheating or not drying materials well, can trap moisture. Imagine bubbles growing during the work – tiny air pockets can disrupt the whole structure. It’s like building a house on shaky ground.
In places like cars, high stress means these issues cause failure. It’s a painful lesson I remember well – especially when a part failed under pressure and didn’t match design needs.
Uneven Material Mixing
Now, consider mixing. Ever baked with lumpy flour? Think on a large scale with glass fibers and other additives. Uneven mixing creates weak spots ready to break. I’ve witnessed weak components because of uneven blending.
Appearance and Surface Defects
Aesthetics matter – everyone loves a smooth finish. Insufficient drying causes silver streaks during molding. Beautiful designs ruined by these defects suggest deeper structural issues.
In gadgets, where appearance is as crucial as function, such flaws can ruin first impressions and affect sales.
Table: Effects of Improper Pretreatment on Mechanical Properties
Issue | Effect |
---|---|
Insufficient Drying | Bubbles causing deformation and stress |
Excessive Preheating | Thermal stress leading to cracks |
Uneven Mixing | Stress concentration reducing strength |
Implications for Precision Assembly
Precision assembly deals with alignment. Poor pretreatment and deformed materials can ruin projects. I’ve redone projects often because parts didn’t align correctly. That’s a costly error in time and resources.
Recognizing and fixing these pretreatment errors is vital to keep projects efficient and harmonious.
For those curious about 3D printing and improving dimensional accuracy, much remains to explore.
Consider looking into resources on 3D printing techniques4 to dive deeper into improving dimensional accuracy with proper material preparation.
Improper pretreatment causes material deformation.True
Improper pretreatment leads to internal stress, causing deformation.
Uneven mixing does not affect dimensional accuracy.False
Uneven mixing causes stress concentration, affecting accuracy.
How Can Chemical Resistance Be Compromised in Injection Molded Products?
Have you ever thought about why some molded items fail against chemicals? Reason isn’t only chance. Often, decisions during design and production lead to this.
Wrong material choice, poor mixing and not drying enough reduce chemical resistance in molded items. These issues create internal flaws. Internal defects make products weak against chemicals.
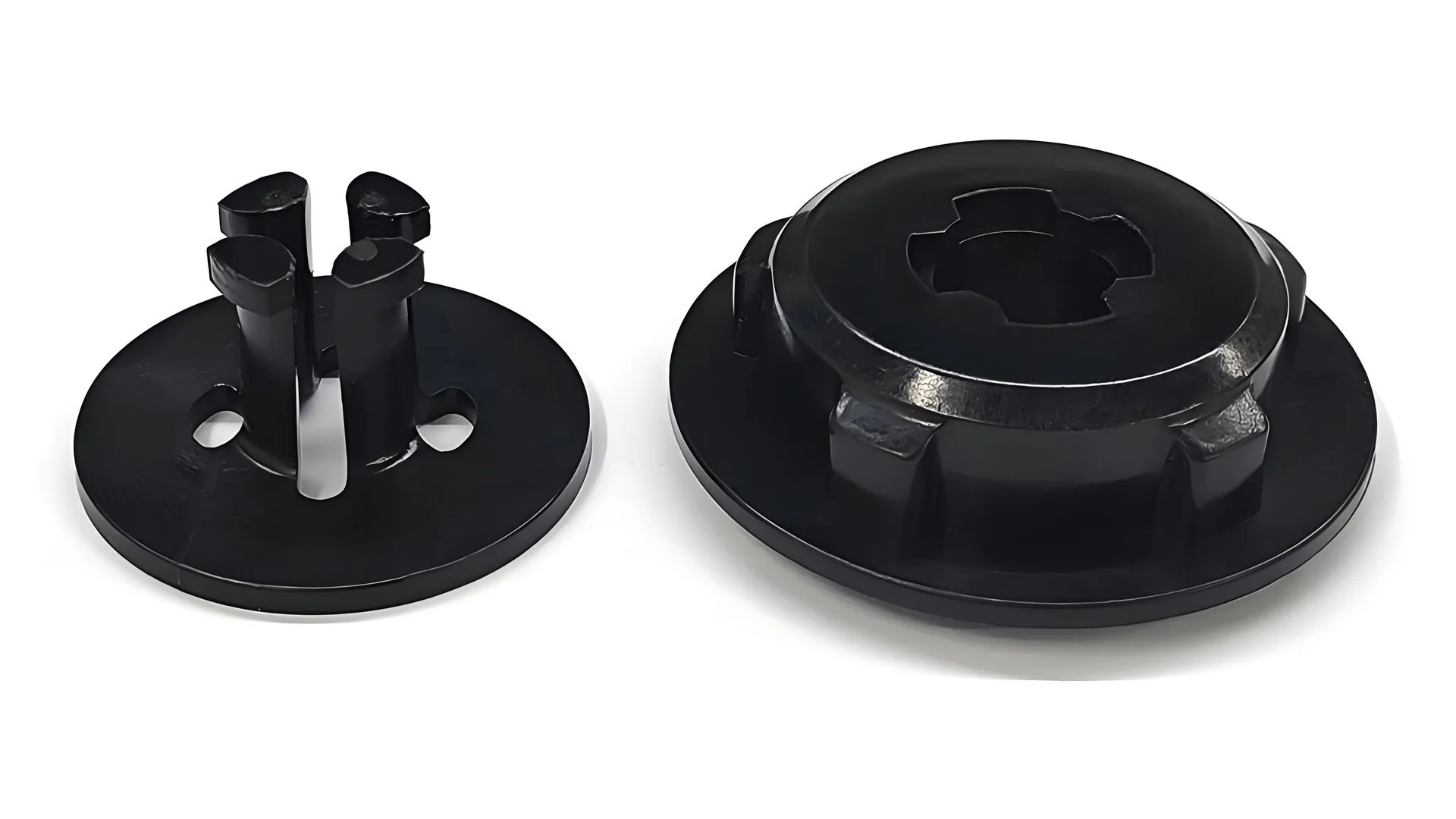
Material Selection and Mixing
I remember my first problem with a product’s chemical resistance. It was a very important lesson. Picking the right material is crucial. Choosing a material without chemical resistance5 causes trouble. The product breaks down in harsh conditions. It’s like picking the wrong plastic for a raincoat and getting soaked!
Success often hides in the small details, such as good mixing of reinforcing agents like glass fibers. Bad mixing creates weak spots, small areas that chemicals can damage. It’s like making a cake with lumpy batter; some parts turn out great, while others fall apart.
Material | Chemical Resistance Rating | Notes |
---|---|---|
Polypropylene | High | Suitable for most acids |
Polycarbonate | Moderate | Prone to stress cracking |
Processing Techniques
Handling processing conditions well is vital for product durability. Once, I skipped drying properly before molding. Tiny bubbles formed inside. These became paths for chemicals to get in – this was a costly mistake.
Thermal stresses from uneven heating or cooling silently weaken products. They break down polymer molecule chains, taking away chemical resistance. These stresses are like invisible cracks in a dam; they become real problems under pressure.
Environmental Factors
Outdoor products bring unique challenges. Sunlight and changing temperatures can worsen defects, slowly destroying chemical resistance6. It’s like leaving a book in the sun – the pages fade and weaken over time.
Understanding Mechanical Properties
- Reduced Strength: Bubbles from poor drying drastically lower compressive strength. Imagine this with car parts – they could suddenly fail under stress.
- Deteriorated Toughness: High preheating temperatures cause thermal stress, making products more likely to crack when hit.
Mechanical properties, like strength and toughness, directly affect chemical endurance. Problems like uneven distribution or bad drying create internal stress points. These weaken the product, reducing its life span and overall product longevity7. Each design choice helps products not just to survive but to succeed in tough environments.
Polypropylene is suitable for most acids.True
Polypropylene has a high chemical resistance rating, ideal for acids.
Improper drying increases chemical resistance.False
Improper drying forms bubbles, reducing chemical resistance by creating weak points.
Conclusion
Improper pretreatment in injection molding leads to reduced strength, toughness, and surface quality, ultimately compromising product performance and longevity due to internal defects and inconsistent material properties.
-
Gain insight into various mechanical issues caused by inadequate pretreatment processes. ↩
-
Explore common injection molding defects to understand how they affect product strength and performance. ↩
-
Learn how effective material preparation processes enhance the durability and appearance of manufactured goods. ↩
-
Gain insights into techniques for achieving better print precision through proper preparation. ↩
-
Discover why selecting materials with inherent chemical resistance is vital for product durability and safety. ↩
-
Learn how thermal stresses during processing can weaken polymers against chemical exposure. ↩
-
Explore how mechanical properties impact the long-term durability of injection molded products. ↩