Ever wondered why those tiny vents in injection molds are such a big deal?
Injection molds require vents to release trapped air and gases, preventing defects and ensuring smooth, high-quality production.
I remember my first project where I overlooked the importance of venting. The result? A batch of flawed plastic components filled with air bubbles. It was a learning curve that taught me how crucial proper venting is in ensuring flawless, efficient production. Now, let’s explore how fine-tuning these vents can transform your manufacturing outcomes, avoid common pitfalls, and lead to superior product quality.
Vents prevent air traps in injection molding.True
Vents allow trapped air to escape, preventing air trap defects.
Venting is unnecessary for high-quality injection molds.False
Venting is crucial to avoid defects and ensure smooth production.
- 1. What Happens If Injection Molds Are Not Properly Vented?
- 2. How Do Vents Affect the Quality of Molded Products?
- 3. What Are the Best Practices for Designing Mold Vents?
- 4. How Can You Identify Venting Issues in Injection Molding?
- 5. What Tools and Technologies Help in Optimizing Mold Venting?
- 6. How Does Venting Impact Production Efficiency and Cost?
- 7. Conclusion
What Happens If Injection Molds Are Not Properly Vented?
Picture yourself meticulously crafting a design, only to have it ruined by unsightly defects. Could improper venting in injection molds be the silent saboteur?
Improperly vented injection molds cause defects such as burn marks, short shots, and poor finishes due to trapped air and gases, compromising product quality.
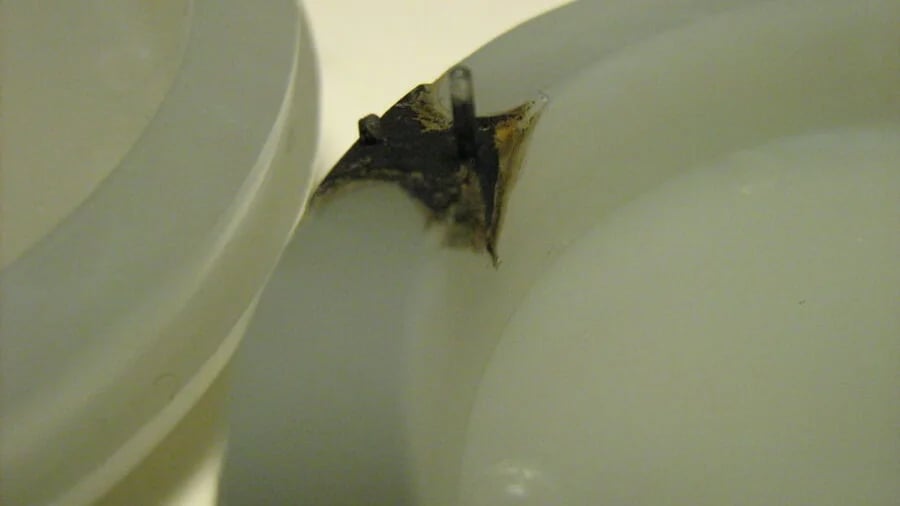
The Role of Venting in Injection Molding
I remember the first time I encountered a major defect in one of my designs. It was frustrating to see all that hard work result in a flawed product. That’s when I learned how crucial proper venting is in injection molding. Venting isn’t just a technical detail—it’s the difference between success and failure. It ensures that trapped air and gases can escape, preventing those defects that haunt every designer’s nightmares.
Consider exploring various venting techniques1 for improved outcomes.
Common Defects from Improper Venting
- Burn Marks: Imagine seeing your beautiful design marred by dark patches. Burn marks happen when trapped air heats up too much, burning the plastic. I’ve been there, wondering if my product would ever look right.
- Short Shots: Have you ever held a product that just feels incomplete? Short shots are like that—when air stops the molten plastic from filling the mold completely. It’s like pouring a glass of water and ending up with half.
- Poor Surface Finish: When you’re creating something meant to be seen and admired, surface imperfections are a big deal. Trapped gases can make a product look unprofessional, which I’ve seen firsthand with clients who demand perfection.
Defect Type | Impact on Product |
---|---|
Burn Marks | Aesthetic degradation |
Short Shots | Structural compromise |
Poor Finish | Reduced visual appeal |
Strategies for Effective Mold Venting
Finding solutions for these venting issues became my mission. Here’s what I discovered:
- Design Optimization: It’s crucial to ensure mold designs have enough venting channels. I’ve spent countless hours tweaking designs, adjusting vent size and placement to get it just right. It’s an art as much as a science.
- Evaluate existing designs and consider adjustments to the vent size and placement.
- Learn about optimizing mold design2 for better venting.
- Use of Vacuum Systems: Some molds truly benefit from vacuum systems that actively remove air before injection. It’s like opening a window in a stuffy room—everything just works better.
- Regular Maintenance: Over time, vents can clog with debris or material. I make it a point to inspect and clean regularly to keep things running smoothly.
By focusing on these strategies, I’ve managed to reduce defects significantly and improve product quality. For professionals like Jacky, aiming to refine their design processes, these insights are invaluable as they help achieve optimal results in manufacturing environments.
For a deeper understanding of these strategies, consider investigating mold maintenance practices3.
Improper venting causes burn marks in injection molded parts.True
Trapped air heats up, burning the plastic and causing dark patches.
Vacuum systems are ineffective for removing air from molds.False
Vacuum systems actively remove air, preventing defects like short shots.
How Do Vents Affect the Quality of Molded Products?
Ever wondered how vents can make or break the quality of your molded products? I was surprised to find out just how pivotal they are in achieving flawless results.
Vents in mold design enhance product quality by releasing trapped gases, preventing defects such as short shots, and ensuring smooth surface finishes.
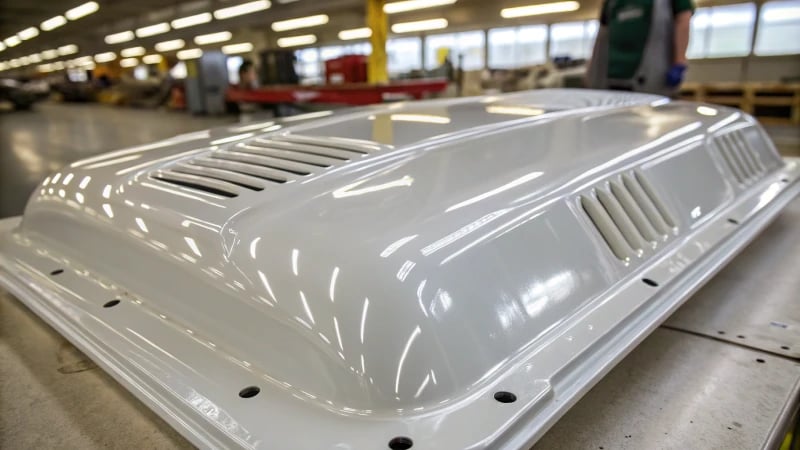
Understanding Mold Venting
Let me take you back to my early days in mold design. I vividly remember a project where I thought I’d nailed the design, only to find burn marks on the final product. It was a humbling moment that taught me the invaluable role of vents in mold design.
In injection molding, these little heroes—vents—are strategically placed channels that allow trapped air and gases to escape. Imagine trying to fill a balloon without letting any air out; that’s what molding would be like without proper venting. Trapped gases can lead to defects like short shots, where the mold isn’t filled completely, or those pesky burn marks that haunted me.
Proper venting ensures molten plastic flows smoothly, fills the cavity entirely, and mirrors the intended design. Skimping on venting can jeopardize both the strength and look of the product.
Types of Vents and Their Applications
Over time, I’ve learned there’s an art to choosing the right vent for each job:
Type of Vent | Description |
---|---|
Edge Vents | Located at the edge of the mold cavity; essential for venting large volumes of air. |
Parting Line Vents | Positioned along the parting line; allows air escape during mold closing. |
Pin Vents | Small vents used in high-pressure zones prone to gas entrapment. |
Grasping these types aids in selecting the optimal vent for any molding need, boosting product dependability.
The Impact on Product Quality
I’ve seen firsthand how missing or misplacing vents can wreak havoc:
- Short Shots: Happen when molds don’t fill completely.
- Burn Marks: Surface when trapped air burns due to friction.
- Surface Imperfections: Caused by gas entrapment affecting finish.
Using effective venting techniques4 is key to overcoming such challenges. Proper venting not only ensures defect-free products but also streamlines production by cutting cycle time and reducing waste.
Incorporating vents might seem minor, but their impact on product quality is profound. By optimizing material flow and minimizing gas defects, vents enhance both functionality and aesthetics of molded products. Exploring different vent designs and placements is a vital step for any mold designer5 aiming for excellence.
Vents prevent burn marks in molded products.True
Vents allow trapped gases to escape, preventing burn marks caused by friction.
Edge vents are used in low-pressure zones.False
Edge vents handle large air volumes, typically in high-pressure areas.
What Are the Best Practices for Designing Mold Vents?
Ever felt like your mold designs just aren’t cutting it? I’ve been there, and trust me, nailing those mold vents is a game-changer.
Best practices for designing mold vents include optimizing vent size and placement, ensuring regular maintenance, and selecting appropriate materials, which minimize defects and enhance mold performance.
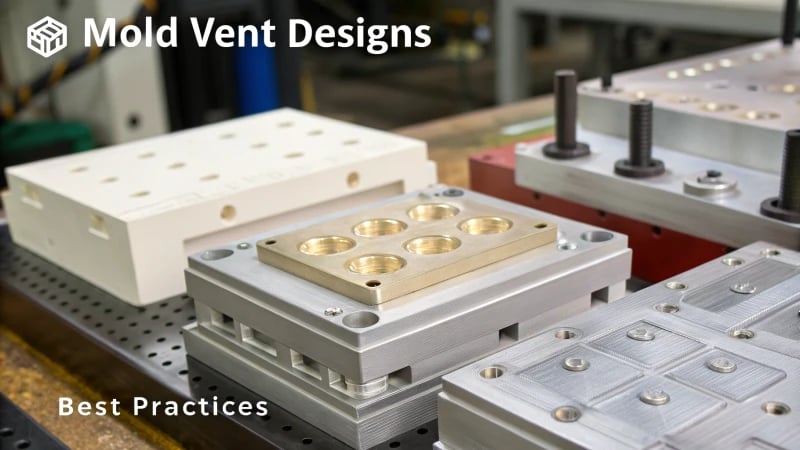
Importance of Vent Size and Location
The vent size and location are critical factors in mold design. When I first started designing molds, getting the vent size just right was like solving a puzzle. A vent that’s too small may not effectively release trapped gases, leading to defects such as burns or incomplete fills. On the other hand, oversized vents can cause flash6 on the molded parts. Now, I usually start with a vent depth between 0.0005 to 0.002 inches for thermoplastics—it’s my go-to range.
The placement of vents should be at the end of the flow path to facilitate easy escape of air and gases. This placement strategy helps in preventing gas entrapment, which often leads to poor surface finish and structural integrity issues in the final product.
Material Selection for Vents
Choosing the right material for mold vents is equally important. I remember the first time I realized how crucial material selection was for mold vents. Materials that are resistant to corrosion and wear can prolong the life of the mold. Metals like beryllium copper and stainless steel are commonly used due to their thermal conductivity and durability.
Material | Properties | Applications |
---|---|---|
Beryllium Copper | High thermal conductivity | Suitable for heat-sensitive materials |
Stainless Steel | Corrosion-resistant | Ideal for general use |
Explore different vent materials7 to find what suits your specific application.
Regular Maintenance of Mold Vents
Regular maintenance is something I can’t stress enough to ensure vents are functioning correctly. Once, I neglected cleaning my vents for a while, and they got clogged with debris—a nightmare! Over time, vents can become clogged with debris, reducing their effectiveness. Implementing a cleaning schedule can help maintain optimal performance using tools like micro drills and air jets for vent maintenance8.
Utilizing Advanced Venting Techniques
Exploring advanced techniques like vacuum venting opened up new possibilities for me by actively removing air and gases from the mold cavity. It’s been especially useful in complex mold designs where standard venting just doesn’t cut it. This technique is beneficial in complex mold designs where traditional venting might fall short.
Consider learning more about vacuum venting techniques9 to expand your skillset in mold design.
Following these best practices has helped me reduce defects and improve both product quality and manufacturing efficiency dramatically.
Optimal vent size is 0.0005 to 0.002 inches for thermoplastics.True
This range is recommended to effectively release gases without causing flash.
Beryllium copper is unsuitable for heat-sensitive materials.False
Beryllium copper's high thermal conductivity makes it suitable for heat-sensitive materials.
How Can You Identify Venting Issues in Injection Molding?
Have you ever found yourself puzzled by unexpected defects in your injection molded parts?
Identify venting issues in injection molding by checking for defects like burn marks, assessing mold design and vent placement, and monitoring the filling process to maintain high-quality production.
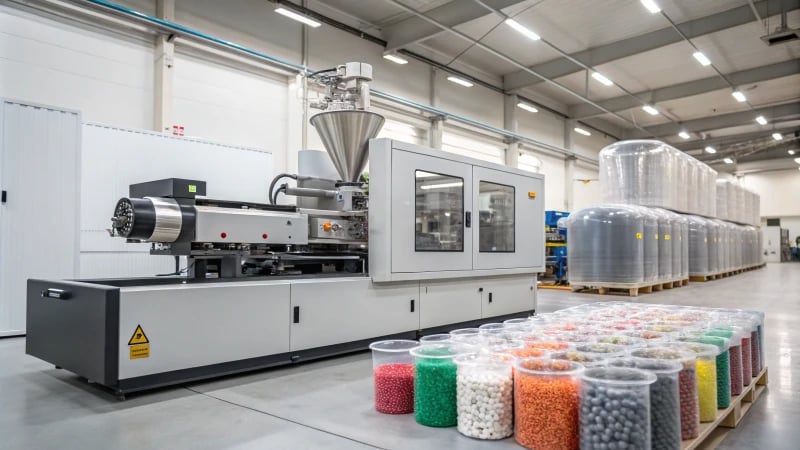
Recognizing Surface Defects
You know that moment when you’re examining a part and suddenly spot a dark streak or a silver line? It’s like finding a scratch on your new car. These surface defects—burn marks, splay, or even short shots—are often the first clues that something’s amiss with the venting. By closely examining these imperfections, I’ve been able to diagnose underlying venting problems before they escalate.
Defect | Description |
---|---|
Burn Marks | Dark streaks on the surface |
Splay | Silver streaks caused by gas entrapment |
Short Shots | Incomplete filling of the mold cavity |
Evaluating Mold Design
It’s funny how something that seems so straightforward can be so intricate. When I look at mold design, I always picture it like a puzzle. Every piece—the vent width, depth, and placement—needs to fit just right to let air escape during the injection process. A flaw here can lead to trapped gases, and suddenly, you’ve got defects on your hands.
Considerations include:
- Vent width and depth
- Vent placement near flow paths
I’ve learned that even minor design missteps can snowball into significant issues. For more insights on how I optimize my mold designs, check out these mold design strategies10.
Monitoring the Filling Process
There’s something almost therapeutic about watching the filling process, ensuring everything flows smoothly. But beyond the zen, I’m always on the lookout for signs of gas entrapment. Using sensors or even simple visual inspections has helped me catch potential issues early on.
For further understanding of how I adjust my filling processes, explore these injection molding techniques11.
Examining Vent Locations and Sizes
Think of vents like the lungs of your mold—they need to be just the right size and in the right place to breathe properly. Too small or misplaced vents can lead to air pockets that wreak havoc on your product quality. Regularly checking and adjusting these parameters has become a staple in my routine.
To learn more about how I tweak vent parameters, check out these vent placement tips12.
Venting issues can truly be a thorn in the side of injection molding, but with keen observation and timely intervention focused on surface defects, mold design evaluation, process monitoring, and correct venting practices, I’ve managed to greatly improve my molding outcomes.
Burn marks indicate venting issues in injection molding.True
Burn marks are dark streaks on the surface caused by trapped gases.
Vents should be placed away from flow paths in molds.False
Vents should be near flow paths to allow air to escape effectively.
What Tools and Technologies Help in Optimizing Mold Venting?
Ever wondered how we can tweak our molds to perfection? It’s all about venting!
Optimize mold venting with advanced simulation software, precision CNC machining, and innovative venting materials for efficient air escape during injection molding, improving production efficiency and product quality.
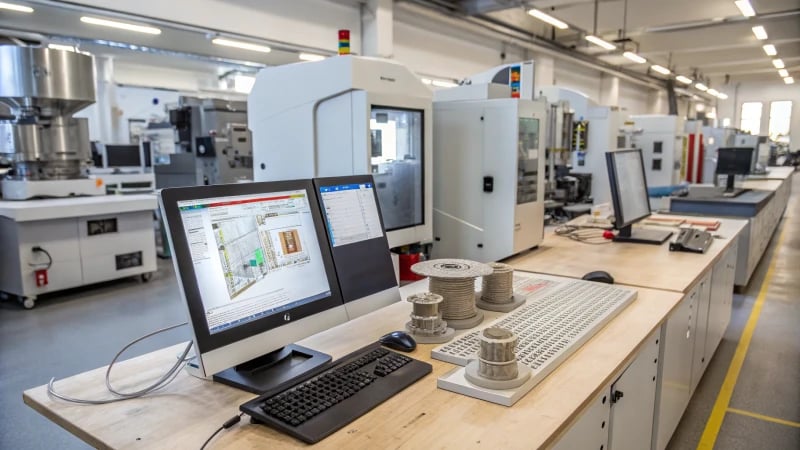
Understanding the Basics of Mold Venting
When I first dipped my toes into the world of injection molding, I quickly learned that mold venting was like the unsung hero of the process. Allowing trapped air to escape is crucial to preventing those pesky defects like burn marks and incomplete fills. Trust me, getting this right is half the battle won.
Advanced Simulation Software
Ah, the wonders of technology! Advanced simulation software like Moldex3D13 feels like having a crystal ball for mold design. It predicts where vents should be, showing airflow and pressure distribution in vivid detail. This means fewer surprises when we hit actual production.
- Benefits:
- Spots potential air traps
- Optimizes vent placement
- Cuts down trial and error
Precision CNC Machining
I remember the first time I watched a CNC machine14 in action—it was mesmerizing. The precision it offers is just what we need to get those vents just right. Accurate machining is the key to consistent production quality.
Machine Type | Accuracy Level |
---|---|
3-Axis CNC | Moderate |
5-Axis CNC | High |
Innovative Venting Materials
When I discovered porous metals15, it felt like finding a secret ingredient that no one else knew about. These materials allow air to escape effortlessly while keeping the mold strong and reliable.
- Advantages:
- High permeability
- Durability under pressure
- Seamless integration into designs
Exploring IoT in Mold Monitoring
In our tech-driven world, IoT technologies have revolutionized mold monitoring. Sensors now do what used to take hours, monitoring conditions in real-time. This data is gold, letting us optimize venting as if the mold could think for itself.
- Key Features:
- Real-time data analysis
- Automated adjustments
- Predictive maintenance capabilities
By integrating these cutting-edge tools and technologies, we can significantly improve mold venting. This leads not only to better production efficiency but also to a marked reduction in defects. Embracing these innovations keeps us on the cutting edge, ensuring high-quality standards while optimizing processes for stellar outcomes.
Simulation software predicts vent locations accurately.True
Simulation tools like Moldex3D predict vent locations and sizes effectively.
IoT in mold monitoring does not provide real-time data.False
IoT technologies offer real-time monitoring of mold conditions, enhancing venting.
How Does Venting Impact Production Efficiency and Cost?
When I first dove into the world of mold design, I quickly learned that venting wasn’t just a side note—it was a game-changer for efficiency and cost. Here’s why.
Venting in manufacturing enhances production efficiency by improving product quality, reducing cycle times, and cutting costs through waste and energy reduction, leading to significantly better outcomes.
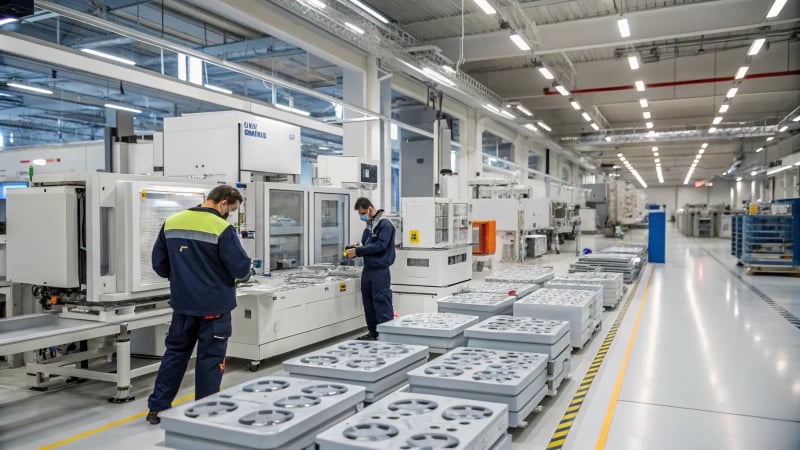
The Role of Venting in Mold Design
I remember one of my early projects where I underestimated the importance of venting16. The mold came out with tiny bubbles, like an air pocket had burst during the process, ruining several units. This experience taught me that venting is crucial for releasing trapped air and gases during molding. Without it, defects like bubbles and burn marks creep in, leading to more rejections, wasted materials, and increased energy use. It’s a lesson that stuck with me.
Improving Production Efficiency
Once I got the hang of efficient venting, everything changed. By allowing gases to escape quickly, I noticed molds cooled faster, and production cycles sped up. For manufacturers17 like me, this means churning out more units in less time. It’s a satisfying feeling to see those production numbers tick up, knowing that venting played a big part.
Aspect | Impact of Venting |
---|---|
Product Quality | Fewer defects, higher acceptance rate |
Cycle Time | Reduced due to faster cooling |
Material Waste | Lowered through defect prevention |
Cost Implications of Venting
Proper venting has saved me more than a few headaches—and dollars. It cuts costs by reducing the need for rework and scrapping faulty products. Plus, optimizing the cooling process means less energy consumption, further trimming expenses. Implementing effective ventilation strategies18 has proven to be a smart move for boosting profitability.
Venting Strategies
Over the years, I’ve tried various strategies to enhance our manufacturing processes. Adding vent grooves or using vent pins has been particularly effective for expelling gases efficiently. And diving into computational fluid dynamics (CFD) has allowed me to design more efficient venting systems19, ensuring optimal air release.
- Vent Grooves: Channels designed to allow air escape.
- Vent Pins: Movable pins that open vents during molding.
- CFD Analysis: Used to simulate and optimize gas flow.
By leveraging these strategies, I’ve been able to optimize both the design and function of molds, leading to significant improvements in production efficiency and cost reduction. It’s a continuous learning journey but one that keeps delivering tangible results.
Venting reduces mold cycle time by 20%.False
While venting reduces cycle time, the exact percentage depends on specific conditions.
Improper venting increases defect rates in products.True
Trapped gases cause defects like bubbles, leading to higher rejection rates.
Conclusion
Injection molds require vents to release trapped air and gases, preventing defects like burn marks and short shots, ensuring high-quality production and efficiency in manufacturing processes.
-
Explore various venting techniques to enhance your injection molding process and prevent common defects. ↩
-
Learn how to adjust mold designs for effective venting, reducing defects like burn marks and short shots. ↩
-
Understand essential mold maintenance practices that ensure efficient venting and improve overall product quality. ↩
-
Learn effective venting techniques to avoid common defects in injection molding processes. ↩
-
Understand why strategic vent placement is crucial for successful mold design. ↩
-
Understanding flash defects can guide you in optimizing vent sizes to avoid these common molding issues. ↩
-
Selecting appropriate vent materials can increase mold lifespan and improve thermal management. ↩
-
Regular maintenance can prevent clogging, ensuring your vents operate efficiently and extend mold longevity. ↩
-
Explore advanced techniques like vacuum venting to enhance your expertise in mold design and improve output quality. ↩
-
Enhances understanding of effective mold designs that prevent venting issues, ensuring smoother production processes. ↩
-
Offers valuable methods to adjust the filling process, minimizing defects caused by poor venting. ↩
-
Provides guidance on vent location and size adjustments, crucial for effective air evacuation. ↩
-
Discover how Moldex3D enhances mold design through precise airflow simulations, improving product quality. ↩
-
Explore top CNC machines known for their precision, ensuring accurate mold venting designs. ↩
-
Learn about porous metals that improve mold venting efficiency while maintaining strength. ↩
-
Explore why venting is crucial in mold design to prevent defects like bubbles and burn marks. ↩
-
Understand how effective venting strategies can speed up production cycles and improve efficiency. ↩
-
Learn about the cost-saving benefits of implementing efficient ventilation systems in manufacturing. ↩
-
Discover how CFD helps in creating optimal venting systems for better air flow management. ↩