Selecting the right plastic is not only a technical choice. It is a crucial moment that determines your product’s success. Understanding material properties really changes how you think about molding.
The properties of plastic materials are crucial when choosing molding processes like injection molding. Flowability, thermal stability, shrinkage rate, toughness and brittleness really matter. These characteristics help decide processing steps. They also affect the quality of your final product. The cost of production is influenced by these factors too.
I have worked deeply in product design and felt the weight of each decision about materials. It is very exciting to choose a high-flow plastic like polypropylene for a project. This plastic easily fills complex mold spaces. I still remember the thrill of seeing a complicated mobile phone shell take shape. Every button and slot was perfectly formed. However, not all materials behave so nicely. Tougher plastics like PEEK need many careful adjustments to flow smoothly. Each experience taught me important lessons about material properties and molding techniques. I really want to share them with you.
Material flowability directly affects injection molding efficiency.True
Higher flowability allows for better filling of molds, improving efficiency in the injection molding process.
Brittleness is not a significant factor in molding process selection.False
Brittleness impacts how materials behave under stress, influencing the choice of molding techniques significantly.
How does flowability affect injection molding performance?
Flowability goes beyond being just a technical term in injection molding. It is truly the core of the process. It affects everything from part quality to production efficiency. This concept significantly influences what we produce.
Flowability is very important in injection molding. It determines how well molten plastic fills mold cavities. High-flow materials improve product quality. They reduce defects. Low-flow materials may cause problems. These challenges need careful management.
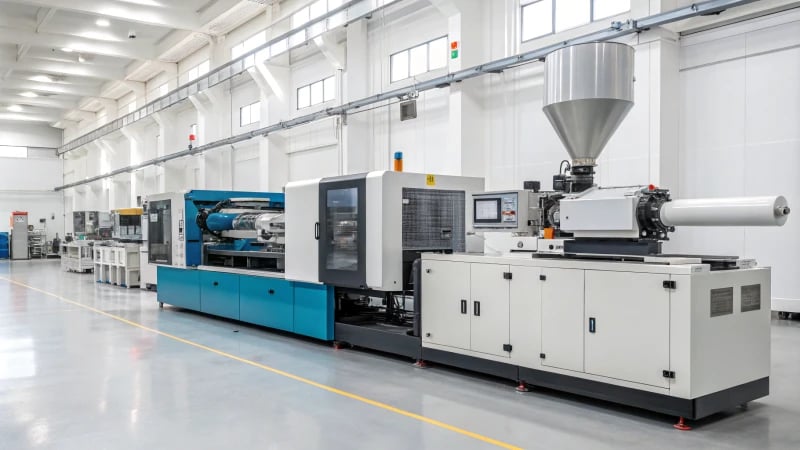
Understanding Flowability in Injection Molding
Flowability refers to how easily a material flows during the injection molding process. I have seen how this impacts the way molten plastics fill mold cavities fully, which is crucial for producing high-quality parts. High-flow materials, such as polyethylene (PE)1 and polypropylene (PP), are my favorites for complex shapes. These materials quickly fill intricate mold spaces, making sure every tiny detail, like buttons on a mobile phone shell, is perfectly copied. However, working with low-flow materials like polyetheretherketone (PEEK) has been a challenge. They need more pressure and temperature to fill molds, often leading to issues that demand careful handling.
Impacts of Flowability on Part Quality
The final product quality greatly depends on flowability. It is difficult to see a batch with defects like flow marks or inconsistent thickness, especially after investing so much effort in the design. Here are some examples:
Material Type | Flowability | Effect on Quality |
---|---|---|
High-flow plastics | Good | Minimal flow marks, uniform thickness |
Low-flow plastics | Poor | Risk of defects like warping and incomplete fills |
Understanding these differences can help designers select the appropriate materials for their specific applications.
Role of Temperature and Pressure
Temperature and pressure are vital in this process. I remember tweaking machine settings for materials like PVC2. Higher temperatures improve flow for low thermal stability materials, but too much heat risks decomposition. Thus, maintaining proper temperatures is crucial for desired flowability while keeping material quality.
Applications of Flowable Plastics
Different projects require different flowability levels. For instance:
- Mobile Phone Shells: High-flow plastics ensure every detail, like buttons and card slots, is precisely replicated.
- Pipes and Profiles: In extrusion molding, high-flow materials help maintain smooth surfaces at higher speeds.
- Blow Molded Containers: High-flow materials achieve an even wall thickness during parison formation.
Sometimes, low-flow materials are needed for strength or rigidity despite processing challenges.
Mitigating Flowability Issues
To tackle low flowability problems, I consider a few strategies:
- Adjusting Mold Design: Changing gate and runner designs has helped improve material flow.
- Increasing Injection Speed: Raising speed can sometimes overcome resistance in stubborn low-flow materials.
- Temperature Control: Tweaking processing temperatures can improve flow without harming material quality.
Focusing on these factors has helped me optimize the injection molding process, leading to products I am proud of.
High-flow plastics minimize defects in injection molding.True
High-flow plastics fill mold cavities quickly, reducing flow marks and ensuring uniform wall thickness, which leads to better quality parts.
Low-flow materials require lower temperatures for molding.False
Low-flow materials often need higher temperatures to improve flowability, contrary to the claim of needing lower temperatures.
How does thermal stability impact mold design?
Have you ever wondered why some plastic products look perfect while others have defects? The reason often depends on the thermal stability of the materials used in mold design. I want to share my insights and experiences on this important topic. This knowledge might really improve the quality of your products.
Thermal stability is crucial in mold design. It directly affects material flow and precision during injection molding. High thermal stability materials probably provide better processing environments. This choice significantly lowers defects. Product quality improves greatly.
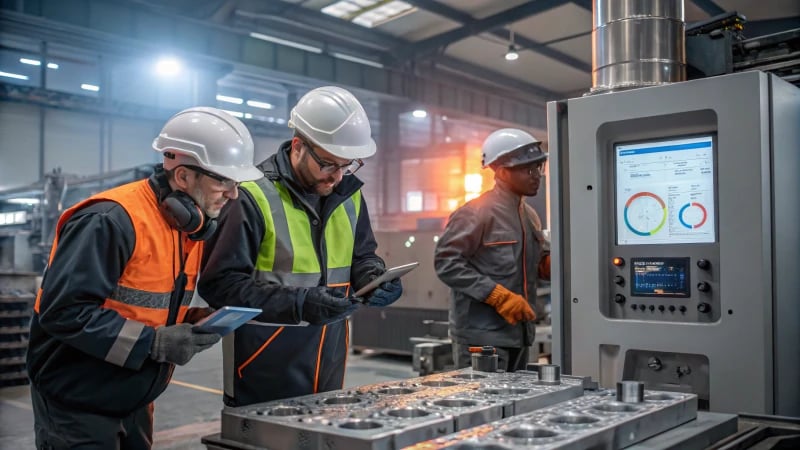
Understanding Thermal Stability in Mold Design
Thermal stability is a critical factor in mold design, particularly when working with various plastics in injection molding, extrusion, and blow molding processes.
High Thermal Stability Materials
Materials such as polyphenylene sulfide (PPS) and polyimide (PI) are known for their excellent thermal stability.
- Advantages:
- They withstand higher processing temperatures, allowing for better fluidity during injection molding. One project involved creating complex shapes and using PPS really made it possible.
- Enhanced thermal stability permits longer exposure to high temperatures during the cooling stages, which is essential for large, thick-walled products. When I worked on a thick-walled part, PPS greatly reduced material wear.
For instance, using PPS in injection molds can significantly improve product quality by reducing the chances of material degradation at elevated temperatures.
In extrusion, these materials maintain integrity under higher temperatures, ensuring the production of high-quality extruded products without degradation.
When it comes to blow molding, materials like PPS enable efficient processing as they adapt well to high-temperature environments during parison molding. This adaptability is crucial for maintaining product quality during the blow molding process. Learn more about high thermal stability plastics3.
Property | High Thermal Stability Plastics | Low Thermal Stability Plastics |
---|---|---|
Processing Temp. | Can withstand higher temps | Requires strict temp control |
Mold Quality | Higher quality with reduced defects | Risk of discoloration and gas generation |
Applications | Ideal for thick-walled products | Limited to lower performance applications |
Low Thermal Stability Materials
Conversely, materials like polyvinyl chloride (PVC) have lower thermal stability, making them more susceptible to temperature variations.
- Challenges:
- Strict temperature control is essential during injection molding to prevent decomposition. I rushed a project once and ended up with major discoloration; it’s an unforgettable lesson.
- In extrusion and blow molding, precise temperature management is critical to avoid thermal degradation, which can lead to quality issues such as discoloration or gas generation.
For example, controlling the temperature during the injection of PVC is vital; too high a temperature can cause significant product defects. Explore best practices for handling low thermal stability materials4.
Impact of Thermal Stability on Production Processes
The role of thermal stability extends beyond just material selection; it significantly influences production efficiency and part quality.
- Flowability: High thermal stability can improve flowability in injection molding, allowing complex shapes to be filled more completely and uniformly.
- Dimensional Accuracy: Maintaining a stable temperature helps ensure that parts do not warp or shrink excessively, leading to higher dimensional accuracy and reduced post-processing work.
- Defect Reduction: Proper thermal management mitigates risks of defects such as sink marks and voids caused by uneven cooling and solidification rates.
Key Considerations for Mold Designers
For mold designers, understanding the implications of thermal stability is crucial. Here are a few considerations:
- Material Selection: Choose plastics with appropriate thermal properties based on the intended application and processing method.
- Mold Design: Incorporate features that support effective heat distribution and cooling to enhance the performance of thermal stability materials.
- Process Parameters: Adjust processing parameters such as temperature and pressure based on material specifications to optimize the molding process.
By focusing on these aspects, mold designers can effectively leverage thermal stability to enhance product quality while minimizing defects in production. Discover advanced mold design techniques5.
High thermal stability materials improve injection molding quality.True
Materials with high thermal stability enhance product quality by reducing degradation during processing, leading to fewer defects and better fluidity in injection molding.
Low thermal stability plastics require strict temperature control.True
Plastics like PVC, with low thermal stability, need careful temperature management during processing to avoid issues like discoloration and gas generation.
How do shrinkage rates affect the dimensions of molded products?
Understanding shrinkage rates resembles discovering a secret for producing high-quality molded products. This exploration is my experience. Every detail truly matters! Let us explore why these rates are very important for creating the perfect design.
Shrinkage rates influence the size of the final product. Materials contract as they cool. High shrinkage probably leads to defects like warping or marks. Low shrinkage really helps keep dimensions stable. Designers find it crucial to consider these factors.
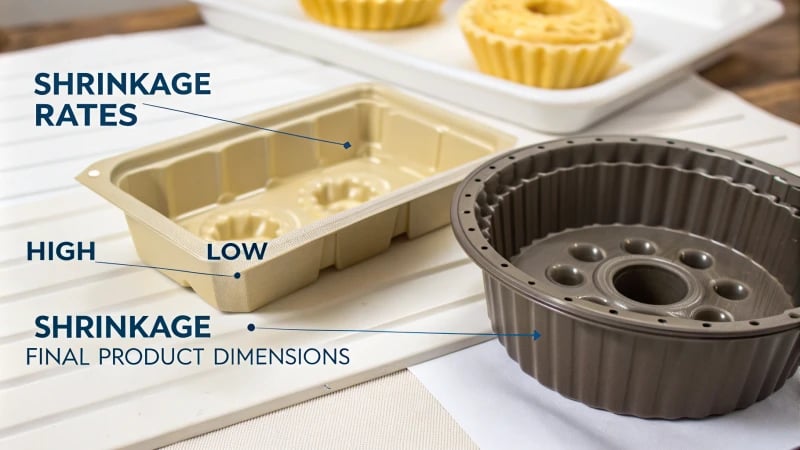
Understanding Shrinkage Rates
Shrinkage rates are critical in determining the final dimensions of molded products. When plastics cool, they contract, and the extent of this contraction varies significantly across different materials. High-shrinkage plastics, like nylon (PA), can lead to dimensional discrepancies if not properly managed during the molding process.
The Impact of High Shrinkage Materials
In injection molding, high shrinkage rates can result in defects such as:
Defect Type | Description |
---|---|
Shrinkage Marks | Surface irregularities that occur when the material cools too quickly. |
Warping Deformation | Distortion of the product shape due to uneven cooling and shrinkage. |
To mitigate these issues, designers must:
- Adjust holding parameters carefully.
- Account for shrinkage in mold design.
For example, when designing parts like mobile phone shells, it’s essential to consider the mold’s shrinkage margin to ensure accurate replication of fine structures within the mold.
Challenges with Low Shrinkage Plastics
Conversely, low shrinkage plastics offer advantages in terms of dimensional stability. Materials that are modified or filled can maintain consistent dimensions, allowing for higher precision in the final product. This is particularly beneficial in applications requiring tight tolerances.
Benefits include:
- Reduced need for post-processing adjustments.
- Enhanced uniformity in wall thickness across the product.
Influence on Extrusion and Blow Molding Processes
During extrusion molding, the shrinkage rate significantly affects how well the product retains its dimensions after cooling. High-shrinkage materials can lead to considerable size changes, necessitating careful calibration of traction devices to ensure product size stability.
In blow molding, the parison’s behavior is critical:
- High shrinkage can complicate maintaining wall thickness and dimensional accuracy post-blowing.
- A deeper understanding of material properties can help mitigate these challenges.
Practical Strategies for Managing Shrinkage
To effectively manage shrinkage, several strategies can be employed:
- Material Selection: Choose plastics with low shrinkage rates for critical applications.
- Process Parameters: Optimize injection speeds and temperatures based on material characteristics to control cooling rates.
- Mold Design: Consider using features that compensate for expected shrinkage during the cooling phase.
For additional insights on effective design strategies, check advanced mold design techniques6.
Conclusion
Ultimately, understanding how shrinkage rates influence final product dimensions is crucial for designers like Jacky, who aim to ensure that their products meet stringent quality and dimensional standards. As such, adopting a comprehensive approach to managing these variables will enhance overall production outcomes.
High shrinkage rates can cause product warping during cooling.True
High shrinkage rates lead to uneven cooling, which can distort the shape of molded products, resulting in warping defects.
Low shrinkage plastics guarantee zero dimensional changes.False
While low shrinkage plastics enhance stability, they do not guarantee zero changes; environmental factors may still affect dimensions.
Why is understanding toughness and brittleness crucial for product durability?
Have you ever wondered why some products last a very long time while others break easily? Toughness and brittleness play a big role in product strength. These two qualities determine how durable a product is.
Understanding toughness and brittleness is very important for product durability. These properties show how materials respond under stress and impacts. Designers really need this knowledge to choose suitable materials. This way, products perform reliably in real-world situations. Products probably last longer too.
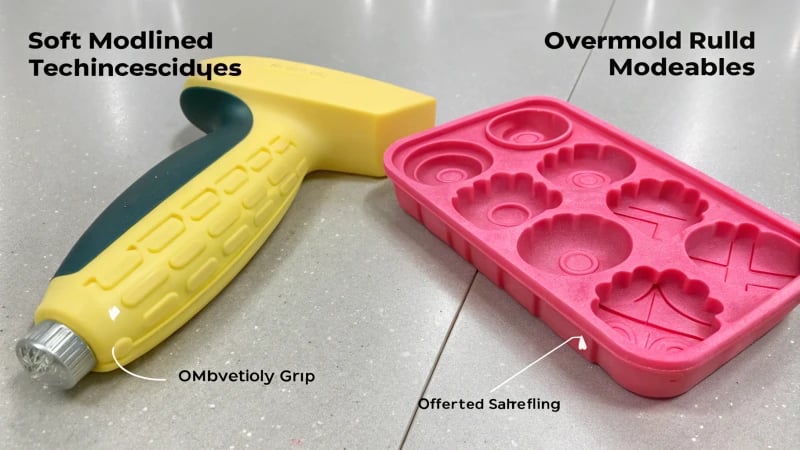
The Importance of Toughness in Material Selection
As a product designer, I often think about the materials I choose for my designs. It’s not just about looks or price. It’s about knowing the true nature of the materials. Toughness and brittleness are very important for how a product performs over time, especially under stress and impact. When I started in this field, each material choice felt huge. I learned that the right material could really improve a product’s success.
Toughness refers to a material’s ability to absorb energy and deform plastically before fracturing. For instance, thermoplastic elastomers (TPE) exhibit high toughness, making them ideal for components that must endure impacts without breaking.
When selecting materials for injection molding, considering toughness can prevent product failure during the demolding process. Tough materials reduce the risk of damage during manufacturing, ensuring that parts remain intact and functional.
Examples of tough plastics include:
Material Type | Characteristics | Applications |
---|---|---|
TPE | High impact resistance | Consumer electronics, automotive parts |
Nylon (PA) | Good flexibility under stress | Sporting goods, industrial parts |
For further insights on material selection, check out this detailed guide7.
The Role of Brittleness in Product Design
Brittleness can ruin a well-made design if ignored. I learned a tough lesson with polystyrene (PS) about material selection. Brittle materials fracture easily, leading to failures in important situations.
In one project, PS caused unexpected cracks during demolding. It was a real surprise! This makes them less suitable for applications where durability is critical.
In injection molding, brittle materials are prone to cracking during demolding. This necessitates careful attention to the demolding techniques and the overall structural design of the product. To illustrate:
Material Type | Risk Factors | Mitigation Strategies |
---|---|---|
PS | Cracks during assembly | Use flexible design principles |
PVC | Degradation under heat | Strict temperature control |
Designers like Jacky must consider these factors to prevent product failures that can arise from the use of brittle materials. For more information about preventing material failures, visit this resource8.
Balancing Toughness and Brittleness for Optimal Durability
Finding a balance between toughness and brittleness is key to creating durable products. Each product faces unique use conditions which guide our material picks. If a product faces impacts, tougher materials are the best choice; for static uses, more brittle materials might work without losing function.
The right choice not only enhances product durability but also improves customer satisfaction by reducing returns and warranty claims. To learn more about achieving this balance, explore our insightful article .
Tough materials enhance product durability under stress.True
Tough materials can absorb energy and deform without breaking, making them ideal for high-stress applications, thus improving overall product longevity.
Brittle materials are suitable for high-impact applications.False
Brittle materials fracture easily under stress, making them unsuitable for applications where impact resistance is crucial for durability.
Conclusion
This article explores how the properties of plastic materials influence molding process selection, affecting product quality and production efficiency.
-
Explore deeper insights on how flowability influences injection molding to enhance your understanding of material selection and process optimization. ↩
-
Learn best practices for managing flowability issues in injection molding, which can lead to improved production efficiency and product quality. ↩
-
Clicking this link will provide you with deeper insights into how high thermal stability materials can optimize your mold design processes. ↩
-
This link offers valuable information on managing low thermal stability materials effectively during production. ↩
-
Learn advanced techniques in mold design that leverage thermal stability for better manufacturing outcomes by visiting this link. ↩
-
Explore techniques to manage shrinkage in manufacturing processes effectively. ↩
-
Explore this link to discover how toughness and brittleness influence material selection and product longevity in manufacturing. ↩
-
Learn why balancing toughness and brittleness is essential for effective product design by following this insightful resource. ↩