I remember my first experience with the delicate art of injection molding. It’s like a dance between accuracy and force.
Low injection pressure during plastic injection molding causes molds to fill incompletely. This results in weak structures, inaccurate dimensions and poor surface finish. These problems reduce the product’s strength and toughness. They impact the overall performance.
Reflecting on those first days in the mold industry, I quickly discovered the importance of having the pressure set correctly. There was a moment when a wrong pressure choice made the difference between a strong part and a fragile, weak one. When discussing how low injection pressure affects product performance, keep in mind that each small change in your process might really affect your final product. Everything counts, from the strength of the structure to the appearance of the surface. Everything.
Low pressure causes incomplete filling in molds.True
Insufficient pressure leads to incomplete filling, causing structural issues.
Low injection pressure improves product toughness.False
Low pressure leads to uneven molecular orientation, reducing toughness.
- 1. How Does Low Injection Pressure Affect Mechanical Properties?
- 2. What Are the Dimensional Stability Concerns with Low Injection Pressure?
- 3. Why does surface quality degrade with insufficient injection pressure?
- 4. How Does Low Injection Pressure Impact Product Sealing Ability?
- 5. What Steps Can Be Taken to Mitigate the Effects of Low Injection Pressure?
- 6. Conclusion
How Does Low Injection Pressure Affect Mechanical Properties?
Had that moment when a small change could transform everything in your project?
Low injection pressure causes molds to not fill correctly. This results in weaker mechanical strength. Reduced toughness happens, too. Dimensional stability becomes poor. Adjusting this pressure is key. It is very important for achieving the desired material qualities.
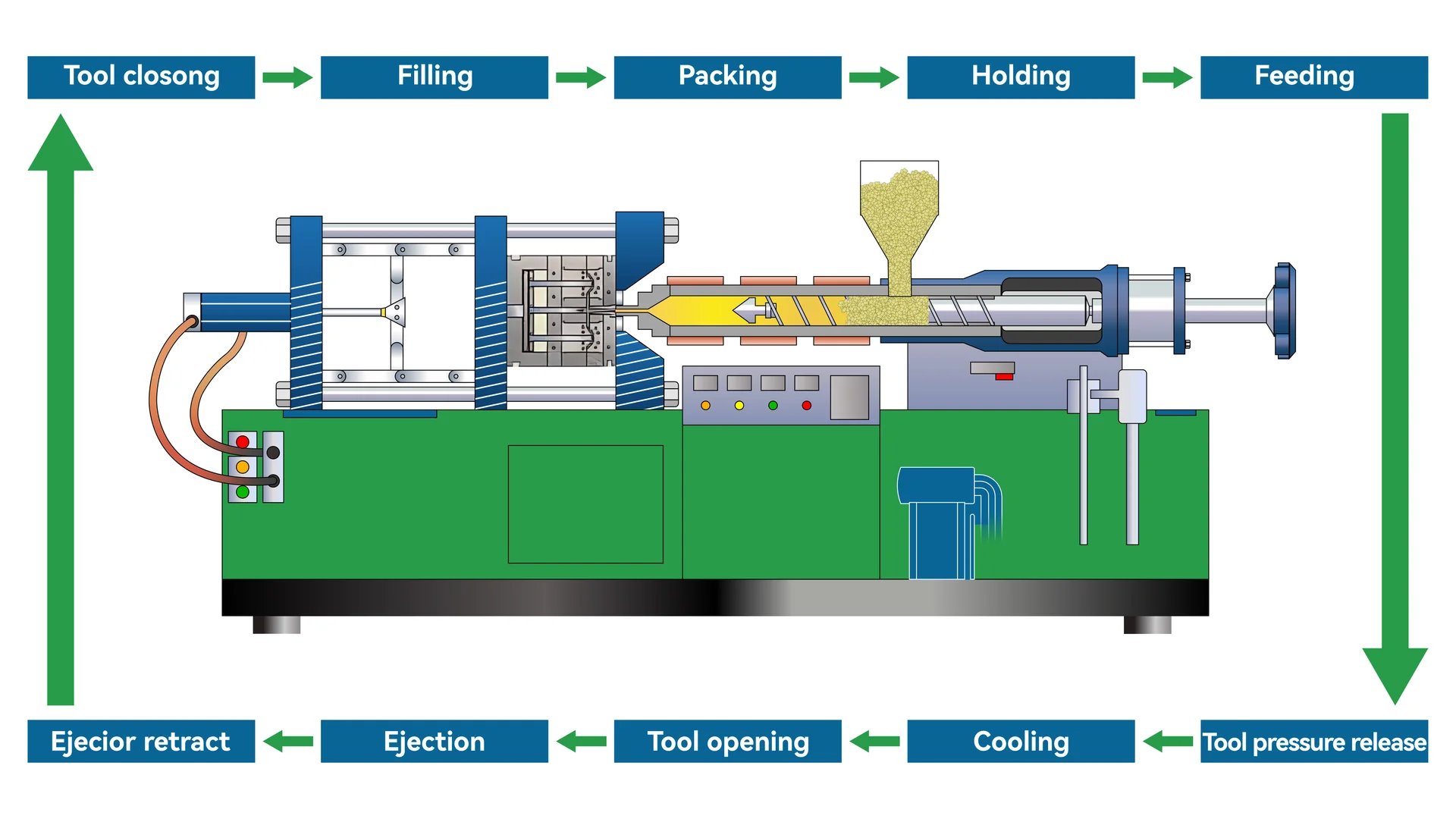
Insufficient Strength and Filling
Once, earlier in my career, I was designing a plastic bracket. I felt excited about the design and wanted to see it grow. But then, reality hit – some parts of the mold didn’t fill well because of low injection pressure, resulting in a weak and flimsy product. This taught me an important lesson about having enough pressure. It’s like baking a cake without enough batter – it really falls flat.
Problem | Example | Impact |
---|---|---|
Incomplete fill | Plastic brackets | Reduced strength |
For more insights on optimizing these parameters and improving overall product quality, exploring mold filling techniques1 could provide valuable solutions.
Toughness Reduction
Another time, I worked on a project with plastic toys. Sounds fun, right? But here’s the twist: low pressure led to brittle breaks because of poorly arranged molecular chains. Imagine a toy that breaks with a little hit. This showed me that toughness really depends on the right pressure settings.
- Example: Plastic toys molded at low pressure might display brittle fractures due to poor molecular chain entanglement.
- Impact: Critical where impact resistance is needed.
Dimensional Stability Challenges
Working with precision parts can be quite tricky. I remember crafting electronic housings and low pressure caused parts to be small and misaligned. It’s frustrating when parts don’t fit together as planned – like mismatched puzzle pieces. Uneven cooling made this worse with surface flaws. That’s never good when looks matter.
- Dimensional Deviation: Small products don’t meet assembly standards.
- Uneven Shrinkage: Causes surface dents or bends.
Utilizing appropriate injection pressures is essential for achieving robust mechanical properties and ensuring that products meet both functional and aesthetic requirements across applications.
Surface Quality and Sealing Performance
It’s disheartening to see shrink marks and flow lines on a sleek product. I experienced this when we worked on plastic shells. Visual quality matters greatly and low pressure can ruin that beauty. Don’t forget sealing power; if a bottle cap doesn’t close right because of pressure problems, it’s a real loss for keeping liquids in.
For more insights into defect prevention strategies, investigating further into defect prevention strategies2 might offer practical approaches to mitigate these challenges.
Low injection pressure reduces product strength.True
Insufficient pressure leads to incomplete filling, reducing structural integrity.
High injection pressure causes uneven shrinkage.False
Insufficient, not high, pressure results in uneven cooling and shrinkage.
What Are the Dimensional Stability Concerns with Low Injection Pressure?
Curious about how a small change in injection pressure could significantly affect your molding project?
Low injection pressure often causes parts to shrink and have surface problems. Molded parts become too small and uneven. Proper pressure keeps products the same size and high quality.
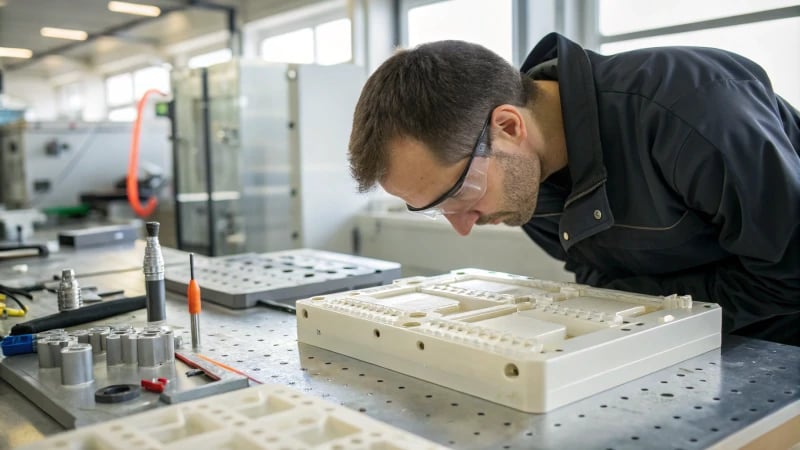
Mechanical Properties Impact
In my early days in the mold industry, I worked on a plastic bracket that wasn’t strong enough. The problem was not enough injection force. The material did not fill the mold fully, leaving weak spots. These weak areas broke easily under pressure. Imagine large pipes with these problems – weak inside because of low pressure, ruining their strength. It’s like baking bread without yeast; you get a heavy, unsatisfying loaf!
Low injection pressure can compromise mechanical properties3 of the product. When pressure is insufficient, it may cause structural incompleteness and reduce strength, particularly in thick-walled products, leading to voids and a decrease in density.
Dimensional Deviation and Uneven Shrinkage
Precision counts a lot, especially with complex parts like electronic housings. I once worked on such a housing, but the size kept straying from the design. Low injection power was again the cause, not filling the mold fully. It’s like pouring pancake batter with too little force; some parts just don’t fill! As it cools, it gets worse, causing uneven shrinking and bumpy surfaces, much like a cake sinking in the middle without support.
Dimensional stability is highly influenced by injection pressure. Insufficient pressure can cause the mold to not fully fill, leading to undersized products.
Product Type | Potential Issue |
---|---|
Plastic Housing | May not meet design dimensions |
Plastic Containers | Uneven surface affecting appearance |
This is especially problematic for precision parts such as electronic housings where exact dimensions are crucial for proper assembly.
Surface Quality and Sealing
Good surface quality really matters. A client making plastic shells for electronics saw ugly marks and lines on their products. It was like trying to cover cracks – they were still visible.
Low pressure can degrade the surface quality and sealing capabilities of products. Defects such as shrink marks or flow lines can mar the surface appearance.
For items needing a seal like bottle caps, not enough force means they seal badly. Imagine opening a juice bottle and finding it leaked in your bag because the cap didn’t fit right.
Importance of Optimal Pressure Settings
Adjusting injection power is like finding the perfect balance in a recipe – it’s essential for quality. Correct settings help avoid low-pressure problems.
To avoid these issues, it’s essential to calibrate the injection molding machine to ensure adequate pressure throughout the molding process.
Changing factors like temperature and mold design4 can lead to better outcomes.
It’s very important to know how low pressure affects stability and quality for anyone in this field aiming to improve their production process.
Low pressure leads to undersized molded parts.True
Insufficient pressure fails to fill mold cavity, causing smaller dimensions.
High injection pressure improves product toughness.False
High pressure can lead to uneven molecular orientation, reducing toughness.
Why does surface quality degrade with insufficient injection pressure?
Ever think about why some plastic items seem a little strange or don’t fit well? Injection pressure probably affects them!
Low injection pressure harms surface quality. It results in poor filling and compaction of mold cavities. Thus, defects appear. Shrink marks and flow lines become visible. Such flaws damage product looks and function.
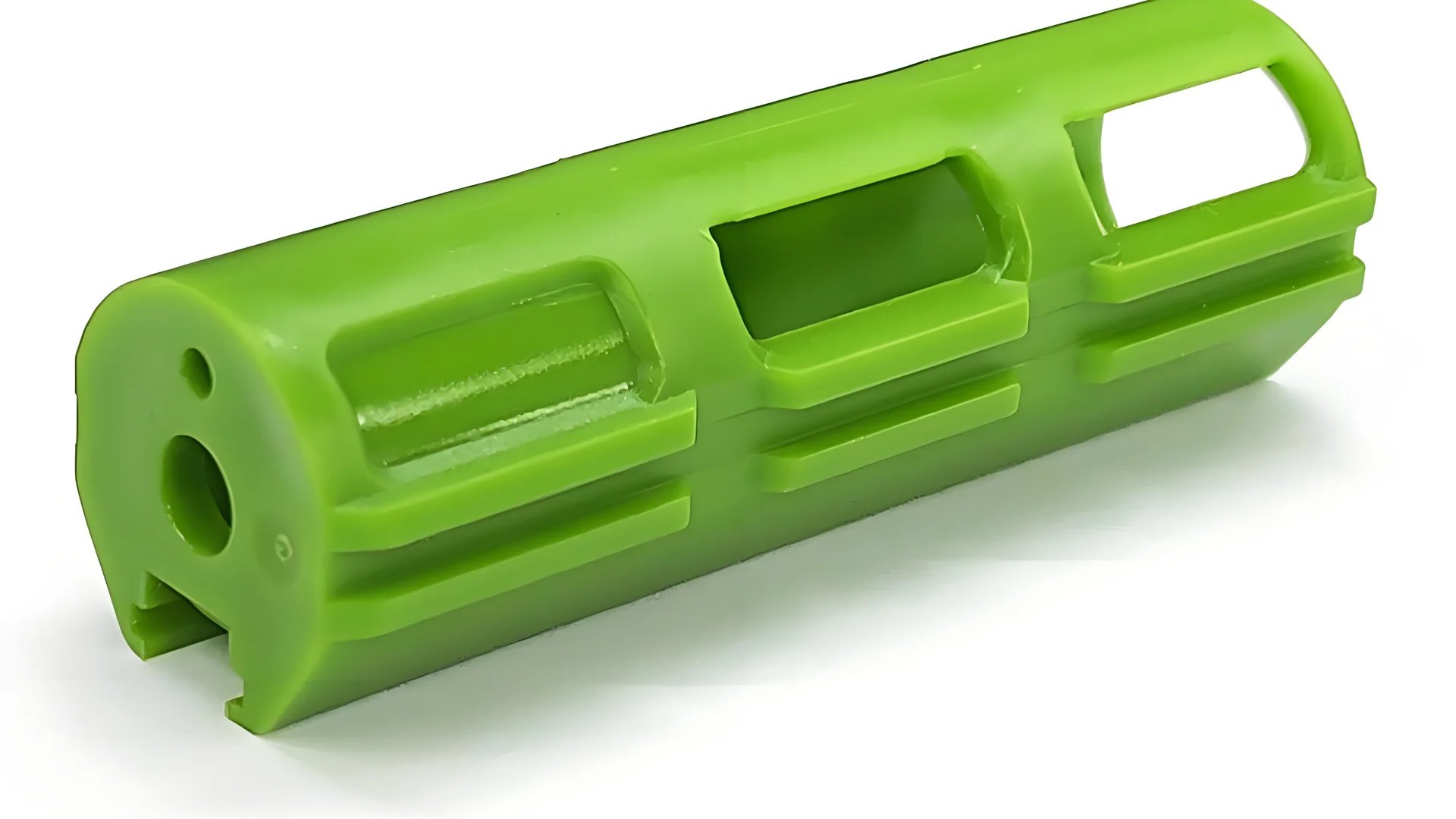
Effect on Mechanical Properties
Injection pressure is crucial in the molding process. It’s like baking a cake; too little pressure and the plastic product doesn’t form right. Insufficient pressure weakens products, leading to insufficient filling5 of the mold cavity.
For example, I once worked on designing a plastic bracket. Sounds easy, right? But low pressure left parts unfilled and weak. It felt like building a house on soft ground. Low pressure in thick plastic pipes created sponge-like areas inside, making them very fragile.
Challenges with Size
Imagine building a puzzle, but the pieces don’t fit. That happens with low pressure during molding. Products become small and misshaped due to incomplete filling, affecting their dimensional stability6. I learned this when electronic housings wouldn’t fit their internal parts due to wrong sizes.
During cooling, inconsistent contraction can cause surface depressions or deformation. Containers with uneven surfaces were also common—another typical day for a mold designer!
Surface Quality Problems
Visible defects upset perfectionists greatly. Shrink marks and flow lines ruin a product’s smooth finish, like smudges on new glasses. Once, our team redid an entire batch of plastic shells due to poor looks.
In addition to aesthetic issues, low pressure affects sealing performance in products like bottle caps where the melt cannot form a complete seal.
Defect Type | Cause | Effect |
---|---|---|
Shrink Marks | Inadequate Pressure | Reduced Aesthetic Quality |
Flow Lines | Uneven Flow | Visible Surface Imperfections |
Incomplete Seal | Insufficient Filling | Compromised Functional Performance |
These struggles show how important proper injection pressure really is. Precision is vital—not just a target—to ensure high-quality surface finishes7 and unwavering reliability.
Insufficient pressure causes incomplete product filling.True
Low injection pressure leads to incomplete cavity filling, causing defects.
Low pressure improves the toughness of molded products.False
Low pressure causes uneven molecular orientation, reducing product toughness.
How Does Low Injection Pressure Impact Product Sealing Ability?
Have you ever asked yourself why certain products never close properly, even with a great design?
Low injection pressure during molding often leads to incomplete filling of the mold. This results in problems like shrink marks and weak bonds. These defects might cause leaks or structural weaknesses. These issues are very serious.
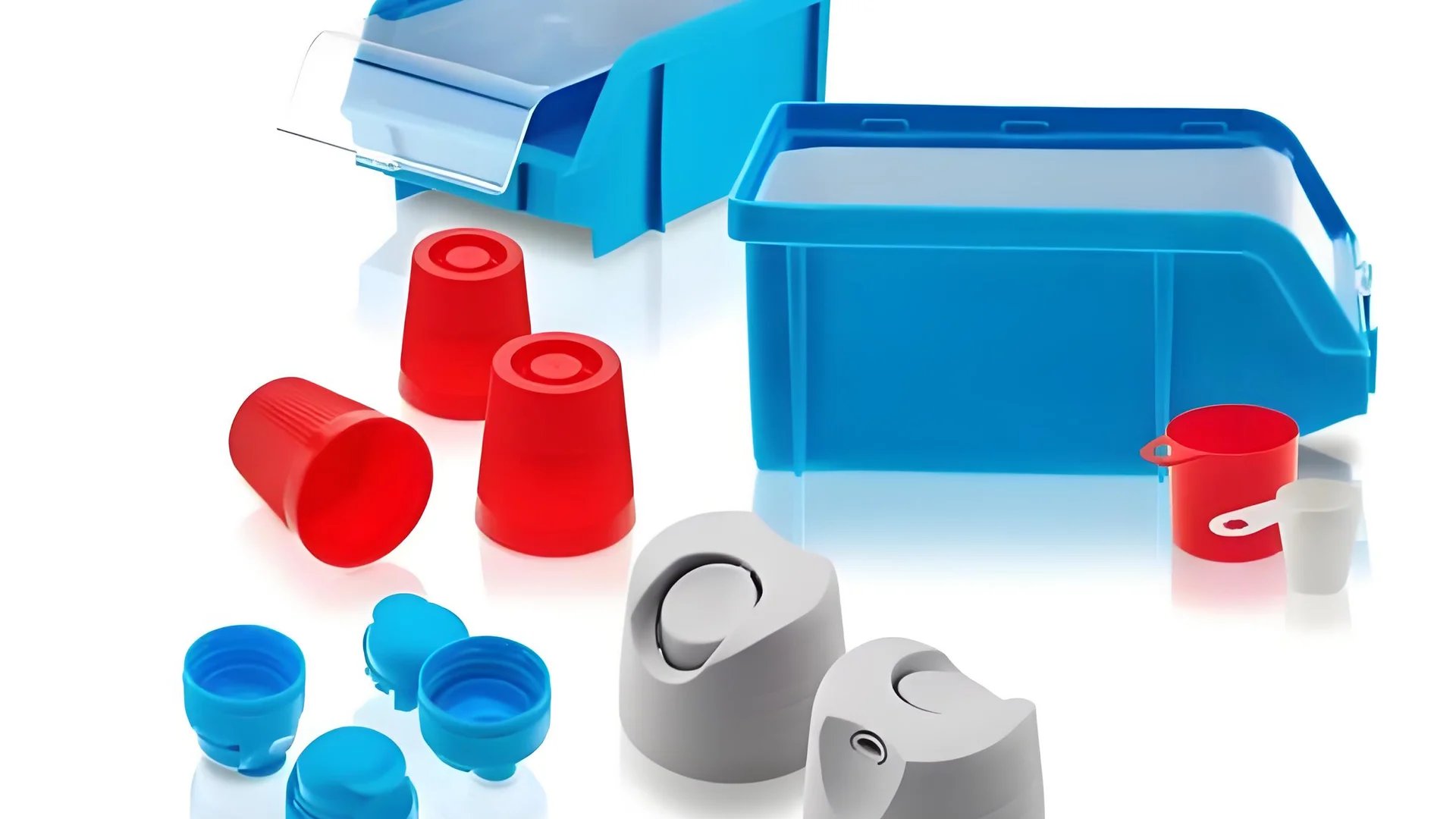
Mechanical Properties and Sealing
I learned early in my career the importance of correct injection pressure in product design. Low pressure fills molds poorly, causing products with weak structures. Weak structures are troublesome for items needing strong seals like plastic containers.
For instance, during a project with plastic bottle caps8, the pressure was too low during production. The plastic did not fill the mold properly, resulting in void spots. Caps did not fit properly, causing leaks everywhere.
Impact | Description |
---|---|
Insufficient strength | The lack of pressure leads to incomplete filling, resulting in structural weaknesses and potential failure under stress. |
Voids in material | Low pressure causes air pockets or voids within the product, compromising its integrity and ability to seal effectively. |
Dimensional Stability and Surface Quality
Low injection pressure affects more than structure; it also impacts dimensional stability and surface quality. Some products have bad surface defects like shrink marks that are unsightly9 and harm function.
Imagine a plastic container with uneven walls due to uneven cooling and shrinkage. It was surprising to me how gaps form at seal points, causing seals to fail. These defects cause big problems as parts don’t fit or seal correctly—very frustrating.
Aspect | Effect |
---|---|
Dimensional deviation | Variability in dimensions due to incomplete mold filling can lead to improper fitting and ineffective sealing. |
Surface defects | Marks and lines that occur due to low pressure can lead to aesthetic issues and may affect how components fit together or seal. |
To end, controlling injection pressure is important for ensuring products look good and work well. Understanding these factors helps achieve good production results and high-quality outcomes, especially for seals where pressure is key10.
Low injection pressure reduces product strength.True
Insufficient pressure leads to incomplete filling, decreasing structural integrity.
High injection pressure improves sealing ability.True
Adequate pressure ensures the melt fits tightly, enhancing sealing performance.
What Steps Can Be Taken to Mitigate the Effects of Low Injection Pressure?
Ever struggled with low injection pressure during manufacturing? I have experienced that and it’s definitely a tough problem.
I discovered that changing mold temperature, increasing injection speed, reworking gate design and improving material qualities really help. These changes really help with filling, strength and stability.
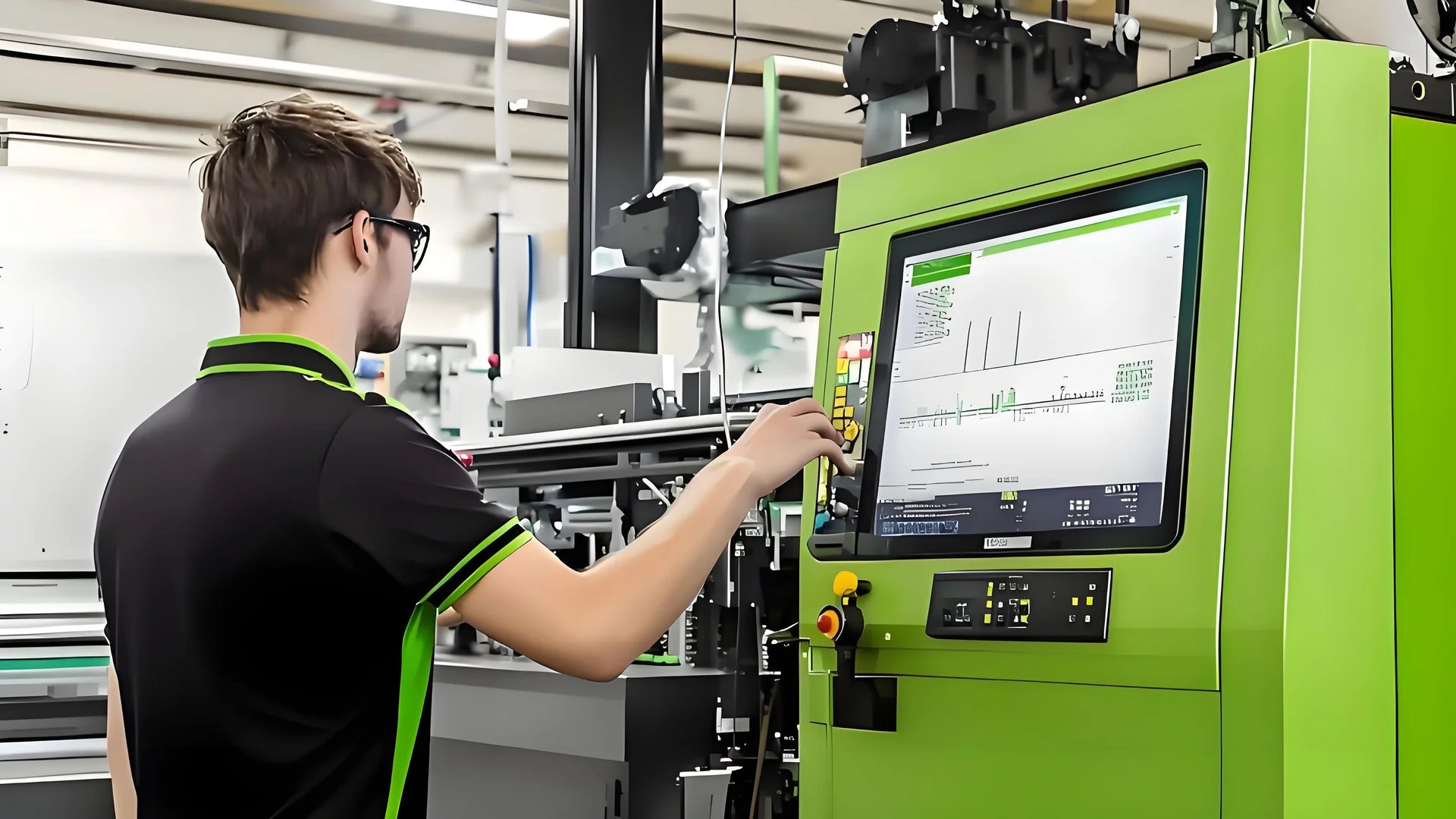
Adjust Mold Temperature
In my early days at the factory, everything seemed to go wrong with our plastic brackets. Incomplete fills and fragile areas kept appearing. All of it traced back to low injection pressure. I learned that warming the mold a bit more helped the plastic flow better. It was like magic – suddenly, everything fit perfectly. This minor change solved issues like insufficient strength11 and dimensional errors. Simple but important.
Increase Injection Speed
I remember working on a project with thick-walled components. Increasing the injection speed changed everything. At first, we worried about defects like jetting. But once balanced, it beautifully compensated for low pressure. Incredible! Shrink marks decreased and the surface quality got much better very quickly. This was an unexpected surprise.
Factor | Potential Effect |
---|---|
Injection Speed | Enhanced filling |
Mold Temperature | Improved melt flow |
Optimize Gate Design
Another breakthrough was optimizing the gate design. On a project with plastic toys, I adjusted the gate size. By making it larger and positioning it well, we achieved even filling and reduced issues like uneven shrinkage. It felt like solving a complex puzzle—puzzling, but rewarding.
Enhance Material Properties
Improving material properties changes everything. Using materials that flow better or adding flow helpers made processes smoother. It was amazing to see how small changes improved results even at low pressure—small adjustments, big impact.
Low injection pressure needs a unique fix for each situation. Each product and process requires special attention by analyzing each factor separately and together; production outcomes really prosper.
Low injection pressure reduces product strength.True
Insufficient pressure leads to incomplete filling, reducing structural integrity.
High injection pressure improves product toughness.False
Excessive pressure can lead to material degradation, reducing toughness.
Conclusion
Low injection pressure in molding leads to incomplete fills, reducing strength, toughness, and dimensional stability while causing surface defects that compromise product quality and sealing performance.
-
Explore advanced mold filling techniques to improve injection molding outcomes. ↩
-
Understand strategies to prevent defects in injection molding for better product quality. ↩
-
Explore how insufficient injection pressure affects the mechanical properties of molded parts. ↩
-
Learn about strategies to optimize mold design for better dimensional stability. ↩
-
Learn about how inadequate filling leads to structural weaknesses in molded products. ↩
-
Explore how insufficient pressure causes dimensional deviations in molded parts. ↩
-
Discover techniques to enhance surface quality by maintaining optimal injection pressure. ↩
-
Explore how insufficient pressure leads to incomplete molding of bottle caps, causing leakage issues. ↩
-
Learn why shrink marks are more than just aesthetic issues; they impact product functionality. ↩
-
Discover techniques to better control injection pressure for optimal product quality. ↩
-
Understanding how mold temperature impacts injection molding helps in achieving better product quality by optimizing filling and reducing defects. ↩