Have you ever wondered how a simple dash of color can transform plastic into something truly remarkable?
Colorants and pigments in injection molding affect plastic properties such as flexibility and durability, enhance visual appeal, and are crucial for optimal performance in manufacturing.
I remember the first time I saw a batch of our products come off the line with a vibrancy that was almost palpable. It wasn’t just about looking good; it was about making sure they performed well too. The subtleties of how each pigment interacts with various polymers can make or break a project. I’ve learned that understanding these nuances is crucial for optimizing the injection molding process. So, let’s dive deeper into how selecting the right colors can elevate your product to new heights.
Colorants can alter plastic flexibility in injection molding.True
Colorants affect physical properties, including flexibility, during molding.
All colorants enhance durability of plastic components.False
Not all colorants improve durability; some may reduce it.
- 1. How Do Different Colorants Affect Plastic Properties?
- 2. What Are the Challenges of Using Pigments in Injection Molding?
- 3. How do I choose the right colorant for my plastic product?
- 4. How Do Colorants Influence Production Efficiency?
- 5. How Do I Perfectly Mix Colorants in Molding?
- 6. How Do Colorants Influence Product Aesthetics and Durability?
- 7. Conclusion
How Do Different Colorants Affect Plastic Properties?
Have you ever stopped to think about how the color of a plastic product can change its performance?
Colorants in plastics alter properties such as thermal stability, UV resistance, and mechanical strength. Selecting appropriate colorant types and concentrations is crucial to optimize plastic performance for specific uses.
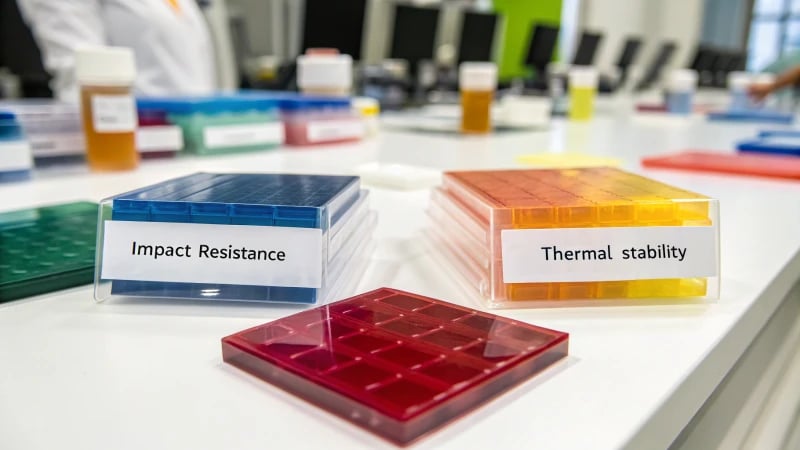
The Science Behind Colorants in Plastics
Colorants, whether pigments or dyes, aren’t just about making things pretty. They can fundamentally change how a plastic behaves depending on how they interact with the polymer matrix1. It’s a bit like adding spice to a dish—it can elevate or completely alter the final taste.
Impact on Mechanical Strength
One of my more seasoned colleagues once shared a story of how carbon black saved the day by reinforcing the tensile strength of a critical component we were developing. It’s fascinating how some pigments, especially those packed with metals, can boost strength. But there’s a flip side—use too much, and you might end up with brittleness instead of toughness.
Colorant | Impact on Strength |
---|---|
Carbon Black | Increases tensile strength |
Titanium Dioxide | May cause brittleness |
Imagine using titanium dioxide; it’s great for certain properties but can lead to brittle plastics if overused.
Thermal Stability Considerations
I’ve learned that choosing the right colorant also means considering how your product will behave under heat. Some pigments like titanium dioxide can help increase thermal stability, which is crucial if your product is going to be exposed to high temperatures. However, others might degrade when things heat up, making it vital to select wisely to keep your designs intact.
UV Resistance and Aging
Have you ever left something plastic outside, only to find it faded and brittle after a few months? That’s where UV resistance comes into play. Some colorants offer inherent UV protection; for example, carbon black is effective in absorbing UV radiation, thereby extending the life of your plastic products2 significantly. It’s amazing how the right choice can protect against aging.
Environmental and Health Considerations
We all want to do our part for the planet, right? That means thinking about the environmental and health impacts of the colorants we use. While heavy metal-based pigments might offer some benefits, they can be toxic. I prefer eco-friendly alternatives whenever possible, especially for products that end up in homes or around food packaging3.
So, when you’re picking colorants for your next project, remember it’s not just about aesthetics—each choice brings its own set of advantages and challenges that must align with your design’s intended application and safety standards.
Carbon black increases tensile strength in plastics.True
Carbon black enhances durability and tensile strength in polymers.
Titanium dioxide reduces UV resistance in plastics.False
Titanium dioxide can increase thermal stability, not reduce UV resistance.
What Are the Challenges of Using Pigments in Injection Molding?
Have you ever wrestled with the nuances of injection molding pigments? It’s a journey filled with color dreams and practical challenges.
Challenges of using pigments in injection molding include color inconsistency, resin compatibility issues, and moisture troubles. Overcoming these ensures visually appealing and high-quality plastic products.
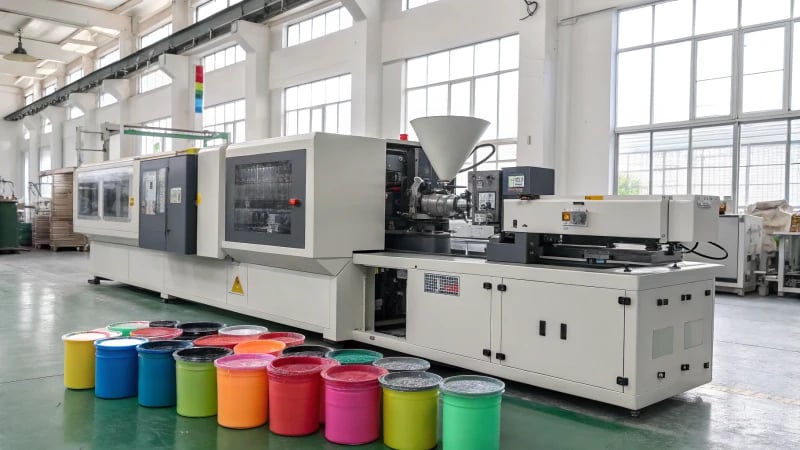
Color Consistency
I remember my first major project where color consistency became a real headache. We were crafting a set of vibrant plastic cases, and let’s just say, achieving that perfect shade was no walk in the park. Variations in pigment distribution left us with everything from neon to dull pastel, all from the same batch! It taught me the value of investing in advanced mixing techniques and equipment4. These tools are lifesavers, ensuring every piece is the color of your dreams.
Resin Compatibility
Oh, the trials of resin compatibility! There was this one time we discovered mid-production that our chosen pigments didn’t quite jive with the resin’s chemistry. The strength and flexibility of our parts took a nosedive. That’s when I learned the hard way that pre-production testing5 isn’t just a formality; it’s an absolute must. Testing ensures that your pigment-resin combo won’t let you down when it matters most.
Moisture Sensitivity
Ah, moisture—the sneaky culprit behind many of my sleepless nights. I recall battling streaks and bubbles that seemed to appear out of nowhere in our products. It was like fighting an invisible enemy! The solution? A controlled environment with desiccant systems6. It’s a game-changer for keeping those pesky moisture-induced defects at bay.
Production Efficiency
Introducing pigments into the mix can feel like adding a twist to a well-practiced routine. It often complicates things, lengthening cycle times and boosting defect rates. Through trial, error, and perhaps a few too many cups of coffee, I’ve found that optimizing machine settings and using automated monitoring systems7 can save the day. It’s all about working smarter, not harder.
Challenge | Solution |
---|---|
Color Consistency | Advanced mixing and dispersion techniques |
Resin Compatibility | Pre-production testing of pigment-resin combinations |
Moisture Sensitivity | Controlled environment with desiccant systems |
Production Efficiency | Optimized settings and automated monitoring |
Exploring Further
Diving deeper into the world of pigments, I’ve found that staying updated with the latest advancements is key. Exploring how new pigment technologies can be applied to injection molding8 has been an eye-opener, offering innovative solutions to these age-old challenges. It’s an ongoing journey but one that ensures we’re always creating products that not only meet but exceed expectations.
Pigments always ensure color consistency in injection molding.False
Achieving uniform color is challenging due to pigment distribution issues.
Moisture can cause defects in pigment-injected plastic parts.True
Moisture absorption by pigments can lead to streaks or bubbles.
How do I choose the right colorant for my plastic product?
Choosing the right colorant for your plastic product can feel like finding the perfect shade of paint for your living room. It’s not just about looks—it’s about durability and compatibility, too.
Choose a colorant for your plastic product by considering compatibility with the base polymer, desired aesthetics, and environmental factors like UV exposure and heat stability to ensure performance and appeal.
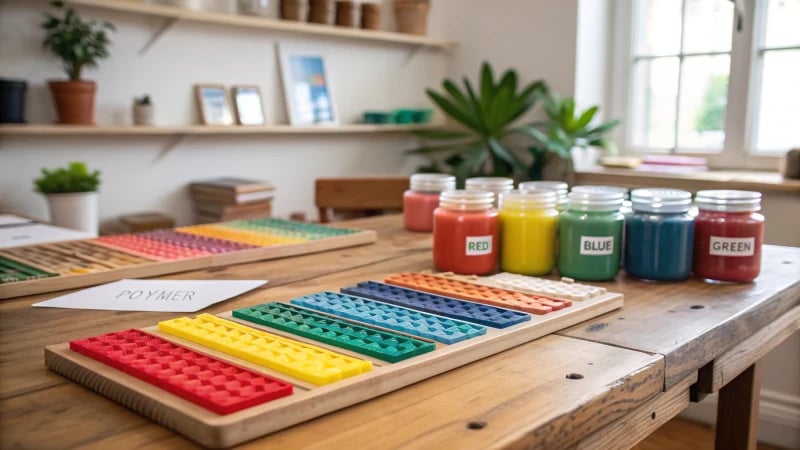
Understanding Colorant Compatibility
I remember the first time I had to choose a colorant for a polyethylene product. I was overwhelmed with the choices but soon realized that compatibility was key. If the colorant doesn’t get along with the base polymer, it’s like trying to mix oil and water—discoloration and even structural issues can arise.
- Polyethylene (PE): Use polyolefin-compatible pigments to avoid issues.
- Polypropylene (PP): Go for heat-stable pigments to maintain strength.
- Polyvinyl Chloride (PVC): Choose non-migratory dyes to prevent plasticizer migration.
Polymer Type | Recommended Colorant | Potential Issues |
---|---|---|
PE | Polyolefin-compatible | Discoloration |
PP | Heat-stable pigments | Loss of mechanical strength |
PVC | Non-migratory dyes | Plasticizer migration |
Aesthetic Considerations
I vividly recall a project where we needed to nail the visual appeal. The client was particular about everything from gloss levels to color consistency. We had to decide between a matte or glossy finish and ensure the color was uniform across all batches. It was challenging but incredibly satisfying when it all came together.
- Opacity vs. Transparency: Your design might require one over the other.
- Gloss Level: Match it to your brand’s aesthetic.
- Color Consistency: Conduct color matching tests9 to ensure uniformity.
Environmental Factors
Once, a client called us about a product that faded after just a few months in the sun. That’s when I learned the hard way about the importance of UV-resistant pigments. Depending on where your product will live, you’ll need to consider:
- UV Resistance: Prevent fading with UV-stabilized pigments.
- Heat Stability: For high-temperature uses, pick heat-resistant colorants.
- Chemical Resistance: Opt for colorants that won’t succumb to corrosive chemicals.
Creating a checklist before you choose a plastic colorant10 can save you from headaches down the road, ensuring longevity and quality.
Cost vs. Quality Balance
I’ve often found myself in discussions about whether to splurge on premium pigments or stick to standard colorants. It’s like deciding between buying a luxury car or a reliable sedan—it all depends on your budget and needs.
A table comparison may help in weighing options:
Aspect | Premium Pigments | Standard Colorants |
---|---|---|
Cost | Higher initial investment | Lower upfront cost |
Longevity | Long-lasting performance | May degrade over time |
Aesthetic | Superior visual effects | Basic color results |
By analyzing these factors, I’ve been able to make choices that align with both my design objectives11 and budget constraints, setting the stage for successful projects every time.
Incompatible colorants can cause discoloration in PE products.True
Using colorants not compatible with polyethylene can lead to discoloration.
PVC requires heat-stable pigments to prevent degradation.False
PVC needs non-migratory dyes, not heat-stable pigments, for stability.
How Do Colorants Influence Production Efficiency?
Ever thought about how the colors in our daily products come to life? It’s more complex than you might think!
Colorants affect production efficiency by influencing material behavior, processing times, and product quality, thereby streamlining production, reducing waste, and enhancing sustainability.
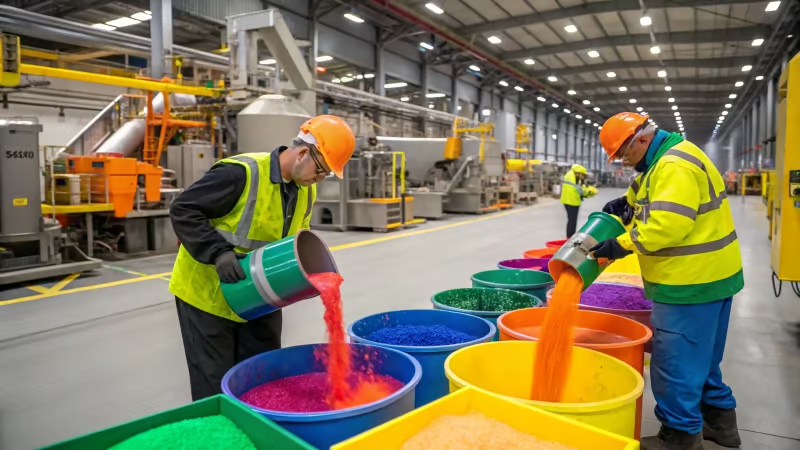
The Role of Colorants in Manufacturing
I remember my first deep dive into the world of colorants. It was like opening a door to a hidden universe of colors that were not just about aesthetics but a crucial cog in the production wheel. In manufacturing, especially in plastic injection molding, the choice of appropriate colorants12 can be a game-changer. The right one can make materials flow like butter, speeding up the process and cutting costs.
Not all colorants are created equal, though. I learned this the hard way when a project went sideways because the colorant wasn’t compatible with our materials, leading to costly downtime. That experience taught me the importance of considering factors like thermal stability and environmental impact when choosing colorants.
Types of Colorants and Their Effects
When I first started working with dyes, pigments, and masterbatches, I felt like a kid in a candy store. Each type brings its own unique flavor to the table:
Type | Advantages | Challenges |
---|---|---|
Dyes | Easy to disperse, cost-effective | Limited heat resistance |
Pigments | Excellent color stability | Can affect material flow |
Masterbatches | Versatile, reduces contamination risk | Higher initial cost |
Navigating these options helped me tailor solutions to fit specific manufacturing needs, ensuring we always hit our production efficiency targets.
Environmental Considerations
Sustainability wasn’t always on my radar until I realized the environmental footprint of our processes. Eco-friendly options such as biodegradable colorants13 have emerged as fantastic choices for reducing impact without sacrificing quality. Embracing these alternatives has not only improved our brand’s image but also opened doors to eco-friendly certifications.
Practical Examples in Industry
I recall working with a forward-thinking consumer electronics company that made the bold move to switch to eco-friendly colorants. This pivot didn’t just polish their green credentials; it also cut down on production waste, saving them a tidy sum.
Another time, a packaging manufacturer I consulted opted for a masterbatch perfectly suited to their thermal requirements. This smart choice significantly reduced their energy consumption14.
These stories illustrate that thoughtful selection of colorants is more than a technical decision—it’s a strategic move that can transform production efficiency across industries.
Eco-friendly colorants reduce production downtime.True
Eco-friendly colorants streamline operations, reducing environmental impact and downtime.
Masterbatches are the cheapest colorant option.False
Masterbatches have a higher initial cost compared to dyes and pigments.
How Do I Perfectly Mix Colorants in Molding?
I remember my first molding project with colorants; it felt like trying to master a vibrant symphony. It’s a dance of precision and creativity, where every step counts.
To perfectly mix colorants in molding, use precise measurements, maintain consistent temperatures, and test small batches to prevent streaks and ensure uniform color.
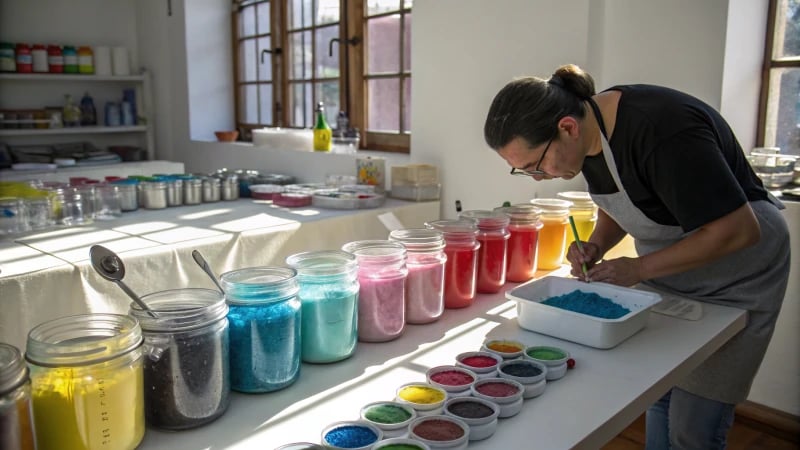
Precision is Key in Colorant Mixing
I can’t stress enough the importance of precision when it comes to mixing colorants in molding. My first attempt taught me this lesson the hard way—my color was off, and it cost me a lot of time and resources. Now, I rely on digital scales to get those weight ratios just right, minimizing any room for error.
Keeping Temperature Consistent
I’ve learned that keeping a steady temperature during mixing can be a game-changer. Once, when the temperature fluctuated, I ended up with streaks in my product—a mistake I’ve since avoided by investing in temperature-controlled15 environments. It’s these little tweaks that make a world of difference.
Testing with Small Batches
Before diving headfirst into full-scale production, I always test with small batches. This practice saved me once when I discovered an issue with my colorant ratios before it became a costly mistake. Conducting batch testing16 is not just about saving materials—it’s about ensuring that quality is never compromised.
Structuring a Colorant Mixing Table
To keep track of everything, I’ve found that creating a mixing table is invaluable. Here’s an example setup:
Component | Weight (g) | Temperature (°C) | Notes |
---|---|---|---|
Resin | 500 | 180 | Base resin |
Colorant | 25 | 180 | Red pigment |
Additives | 10 | 180 | UV stabilizer |
By maintaining such records, replicating successful mixtures becomes straightforward, and spotting discrepancies is much easier.
Specialized Equipment to the Rescue
When I first started, I used basic tools, but upgrading to high-shear mixers transformed my workflow. These mixers ensure the colorants blend seamlessly with the base materials, reducing any risk of separation.
For anyone looking to deepen their understanding, exploring mixing technologies17 available today could open up new possibilities.
Embracing these best practices has not only enhanced the visual appeal of my projects but also boosted the overall quality and durability of the products. Keeping these tips in mind helps me streamline processes efficiently, much like how Jacky would in his design endeavors.
Using a digital scale minimizes colorant waste.True
Digital scales provide accurate measurements, reducing errors and waste.
High-shear mixers increase color separation risk.False
High-shear mixers enhance blending, reducing the risk of color separation.
How Do Colorants Influence Product Aesthetics and Durability?
Ever wondered how the colors in our everyday products can make or break their appeal and lifespan?
Colorants enhance product aesthetics with vibrant hues and impact durability by affecting material stability and environmental resistance. The right colorant choice ensures both visual appeal and functional strength.
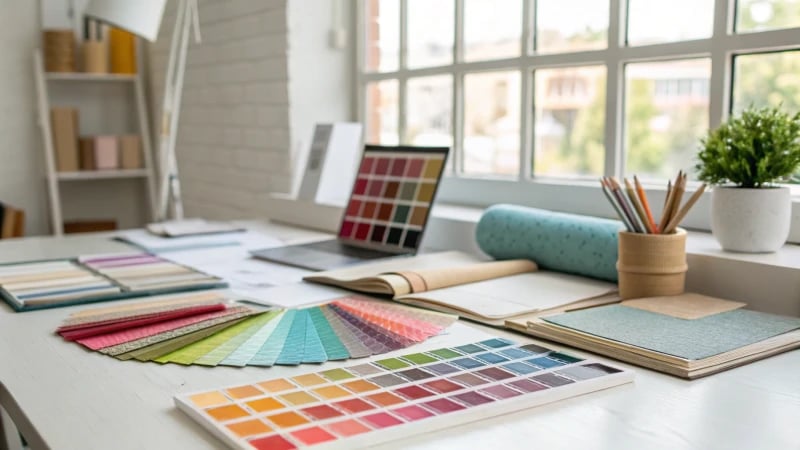
The Role of Colorants in Product Aesthetics
When I think back to the first time I worked on a design project that required choosing the right color, I remember feeling like a kid in a candy store. The spectrum of hues available was mesmerizing, each telling a different story. Colorants are not just about making a product look good—they’re about creating a connection. They help align products with brand identity and consumer preferences, much like how I choose colors that reflect my own personality when I’m redecorating my home.
Colorant Type | Aesthetic Effect |
---|---|
Organic | Bright, vibrant colors |
Inorganic | Earthy, muted tones |
Special Effect | Iridescent, metallic sheen |
Strategically incorporating these colors can enhance marketability, making products more appealing to specific demographics. It’s like when I found the perfect shade of red for a client’s electronics line; it was bold, eye-catching, and exactly what was needed to stand out in a crowded market.
Impact on Product Durability
While aesthetics are crucial, I’ve learned that durability is equally important. A product can look stunning but if it fades or cracks too soon, it fails its purpose. Colorants play a big role here. For instance, inorganic pigments often provide greater stability against UV degradation, which is a lifesaver for outdoor products. Imagine a patio chair that keeps its vibrant color season after season—it’s those thoughtful choices in materials that make it happen.
Factor | Consideration |
---|---|
UV Resistance | Inorganic pigments for longevity |
Chemical Stability | Additives to prevent reactions |
Moisture Resistance | Sealing techniques |
Strategic Colorant Selection
For designers like me, selecting the right colorant is all about balance. It’s about marrying aesthetic goals with functional needs—a bit like choosing between a stylish yet comfortable pair of shoes for a long day at work. The choice should consider the intended use of the product and its environmental exposure.
Diving deep into exploring colorants18 shows how this seemingly simple choice affects not just appearance but the entire lifecycle of a product. Every decision has layers of implications, much like when I pick out fabric for a new sofa; I want something that looks great but also withstands the wear and tear of daily life.
Ultimately, navigating the intersection between aesthetics and durability with colorants requires understanding their properties and implications. For more insights on leveraging colorants effectively, keeping up with industry trends and technological advancements is key for any designer aiming to create standout products.
Organic colorants provide bright, vibrant colors.True
Organic colorants are known for their ability to produce vivid hues.
Inorganic pigments degrade quickly under UV light.False
Inorganic pigments are stable and resist UV degradation, enhancing durability.
Conclusion
Colorants and pigments significantly influence the injection molding process, affecting plastic properties like durability, flexibility, and aesthetics while ensuring optimal performance in manufacturing.
-
Explore this link to understand the fundamental interactions between colorants and polymer matrices, crucial for optimizing material performance. ↩
-
Learn why carbon black is effective for UV protection, crucial for extending the lifespan of outdoor plastic products. ↩
-
Discover safer pigment options for use in consumer goods and packaging applications, prioritizing health and environmental safety. ↩
-
Discover how cutting-edge equipment can improve pigment distribution and enhance color consistency in molded products. ↩
-
Learn about testing procedures for ensuring pigments are compatible with resins to maintain product quality. ↩
-
Explore how desiccant systems help manage moisture levels, preventing defects in injection molded parts. ↩
-
Find out how automation can improve efficiency and reduce errors in the injection molding process. ↩
-
Investigate new developments in pigment technology to overcome challenges in injection molding. ↩
-
Discover techniques for ensuring color consistency across multiple production batches. ↩
-
Explore various plastic colorants available and their ideal applications for better decision-making. ↩
-
Understand how aligning colorant choices with design objectives enhances overall product success. ↩
-
Learn how specific colorants improve flow and processing time in injection molding. ↩
-
Discover the environmental advantages of using biodegradable colorants. ↩
-
See how the right colorant selection can lead to energy savings. ↩
-
Understand how maintaining consistent temperatures can prevent color variations. ↩
-
Discover how small batch testing can optimize your mixing process and save costs. ↩
-
Explore advanced equipment options that ensure better mixing results for high-quality products. ↩
-
Explore comprehensive strategies for selecting colorants that optimize both aesthetics and durability in product design. ↩