Facing challenges with shrinkage defects in injection molded parts? You’re not alone! Let’s dive into how you can identify these pesky issues and make improvements that really matter.
To identify shrinkage defects in injection molded parts, look for dimensional changes, surface depressions, and deformations. Improving these issues involves selecting appropriate materials, optimizing mold design, and adjusting process parameters to ensure quality production.
While recognizing shrinkage defects is the first step, implementing effective improvements is crucial to preventing future occurrences. Continue reading to explore comprehensive strategies and expert insights that will enhance your injection molding processes.
Material selection impacts shrinkage rates in injection molding.True
Different materials exhibit varying shrinkage characteristics, affecting defect rates.
What Are the Common Causes of Shrinkage Defects?
Shrinkage defects in injection molding can lead to significant production challenges and are influenced by several factors.
Shrinkage defects commonly arise from material selection, mold design issues, and improper process parameters. These factors affect the cooling and solidification of the plastic, leading to dimensional inconsistencies, surface depressions, and deformations.
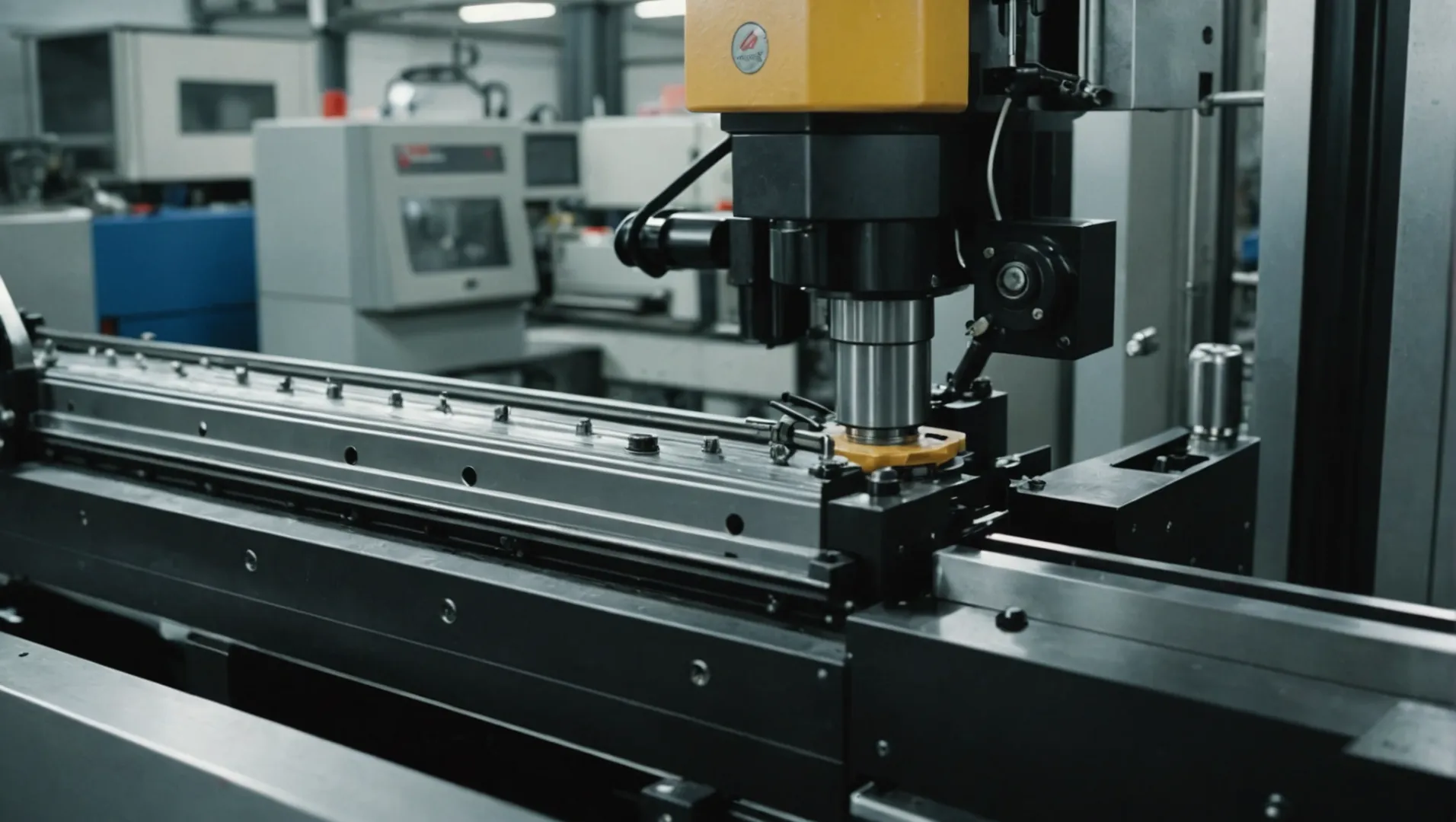
Understanding Shrinkage Defects in Injection Molding
Shrinkage defects are a major concern in the injection molding industry due to their potential impact on both the appearance and performance of molded parts. Understanding the common causes of these defects is essential for optimizing production processes and ensuring high-quality outcomes.
Material Selection
The choice of material significantly influences shrinkage rates. Different plastics exhibit varying shrinkage characteristics during the cooling phase. Thermoplastics like polyethylene and polypropylene have higher shrinkage rates compared to materials such as polycarbonate or ABS.
To mitigate shrinkage:
- Opt for materials with lower shrinkage properties.
- Consider adding fillers or reinforcing agents to reduce shrinkage.
Mold Design Considerations
The design of the mold itself plays a crucial role in controlling shrinkage. Poorly designed molds can lead to uneven cooling and filling, resulting in defects.
Key design elements include:
- Gate Location and Number: Proper placement ensures even filling and reduces localized shrinkage.
- Wall Thickness: Uniform wall thickness minimizes differential cooling rates, reducing shrinkage.
- Temperature Control: Ensure even temperature distribution across the mold to avoid hotspots that can exacerbate shrinkage issues.
Process Parameter Adjustments
The parameters set during the injection molding process can significantly affect shrinkage outcomes.
Important adjustments include:
- Injection Pressure and Holding Time: Increasing these can improve packing efficiency, reducing voids and shrinkage.
- Cooling Time: Adequate cooling time ensures proper solidification, minimizing shrinkage-related deformation.
- Injection Temperature: Proper temperature settings enhance material flow and reduce shrinkage potential.
By carefully managing these aspects, manufacturers can effectively address shrinkage defects, enhancing both the quality and consistency of injection molded parts. For further insights into how each factor influences outcomes, consider exploring material selection for injection molding1 and mold design techniques2.
Polyethylene has a higher shrinkage rate than polycarbonate.True
Polyethylene's thermoplastic nature results in higher shrinkage compared to polycarbonate.
Increasing cooling time reduces shrinkage-related deformation.True
Adequate cooling time ensures proper solidification, minimizing deformations.
How Does Material Selection Influence Shrinkage Rates?
Choosing the right material is crucial in managing shrinkage rates in injection molding, impacting the final product’s dimensions and surface quality.
Material selection directly impacts shrinkage rates due to inherent properties of plastics. Materials with lower shrinkage rates, or modified with fillers, can reduce defects like warping and surface depressions.
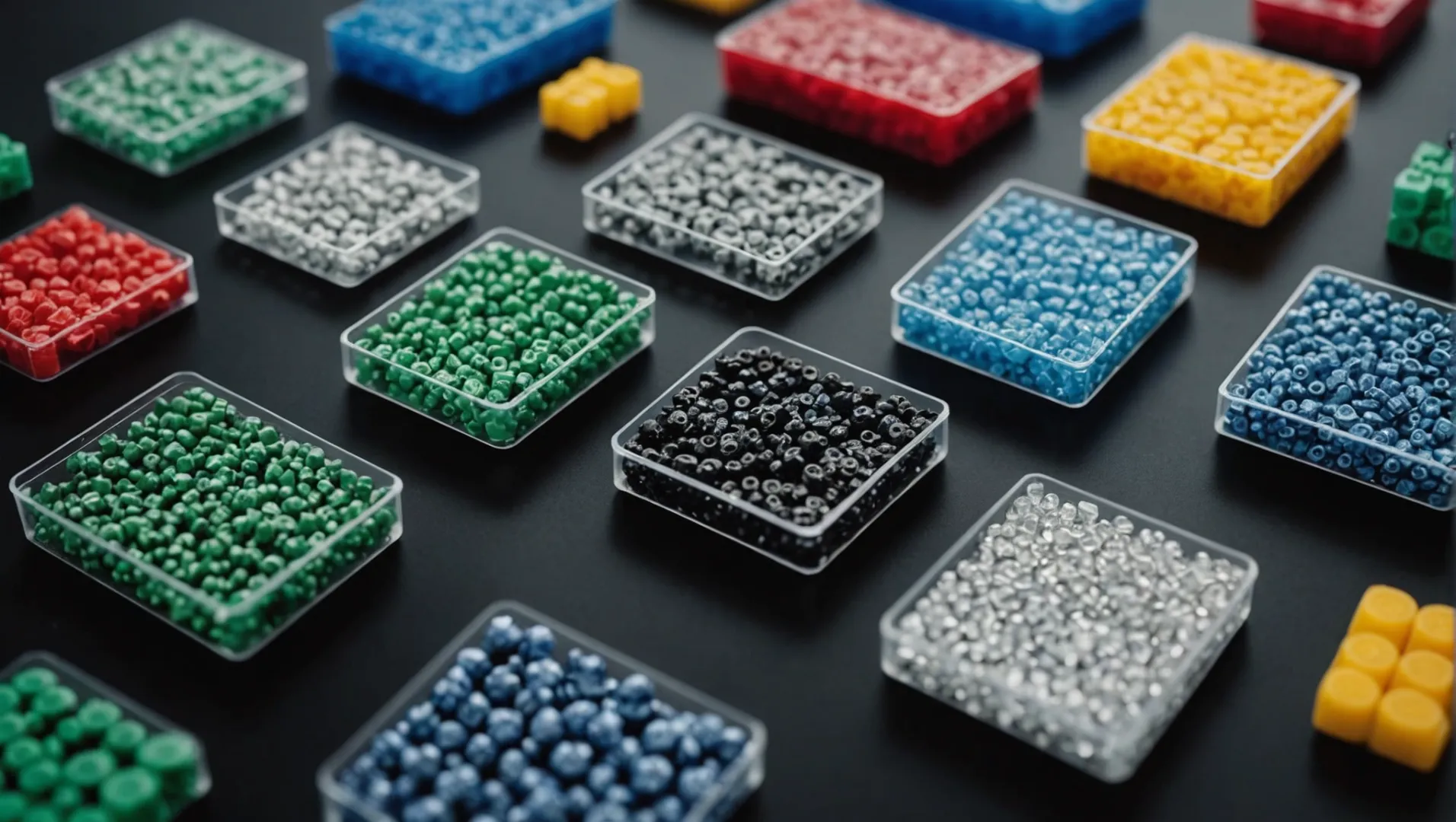
The Impact of Material Properties on Shrinkage
Understanding the characteristics of different plastics3 is essential for predicting shrinkage rates. Plastics vary in their thermal expansion and contraction behaviors, directly affecting the degree of shrinkage post-molding. For instance, crystalline polymers typically exhibit higher shrinkage compared to amorphous polymers due to their structured molecular alignment during cooling.
Amorphous vs. Crystalline Polymers
- Amorphous Polymers: These plastics, like ABS and polycarbonate, generally have lower and more predictable shrinkage rates because their random molecular structure doesn’t change significantly upon cooling.
- Crystalline Polymers: Materials such as polypropylene and polyethylene have higher shrinkage due to ordered molecular structures that expand during heating and contract upon cooling.
Modifying Material Composition
Selecting materials with built-in properties that counteract shrinkage is beneficial. However, when working with inherently high-shrinkage materials, modifications can be made:
- Adding Fillers: Incorporating materials such as glass fibers can significantly reduce shrinkage by limiting the polymer’s ability to contract.
- Reinforcing Agents: These materials enhance structural integrity and reduce warping by distributing stresses more evenly throughout the polymer matrix.
A simple comparison of materials and their typical shrinkage rates is shown below:
Material Type | Typical Shrinkage Rate (%) |
---|---|
Polypropylene | 1.0 – 2.5 |
ABS | 0.5 – 0.7 |
Polycarbonate | 0.5 – 0.8 |
Nylon | 0.7 – 1.0 |
Considerations for Material Selection
To mitigate shrinkage effectively, consider the following during material selection:
- Compatibility with Design Requirements: Ensure that the material’s shrinkage properties align with the desired part dimensions and tolerances.
- Cost vs. Performance: Balancing material costs with performance requirements can impact the choice, especially when selecting between unmodified and filled polymers.
- Environmental Conditions: Factor in how environmental conditions during use (temperature, humidity) will affect the material’s stability and dimensional integrity.
By evaluating these factors4, manufacturers can make informed decisions that enhance product quality and reduce defect rates.
Crystalline polymers have higher shrinkage rates than amorphous ones.True
Crystalline polymers expand and contract more due to ordered structures.
Adding fillers increases the shrinkage rate of polymers.False
Fillers reduce shrinkage by limiting polymer contraction.
What Role Does Mold Design Play in Reducing Shrinkage?
Mold design is pivotal in minimizing shrinkage in injection molded parts, affecting their precision and integrity.
Mold design influences shrinkage through gate placement, temperature control, and wall thickness management. Optimizing these aspects can significantly reduce shrinkage defects, ensuring better quality and dimensional accuracy in injection molded parts.
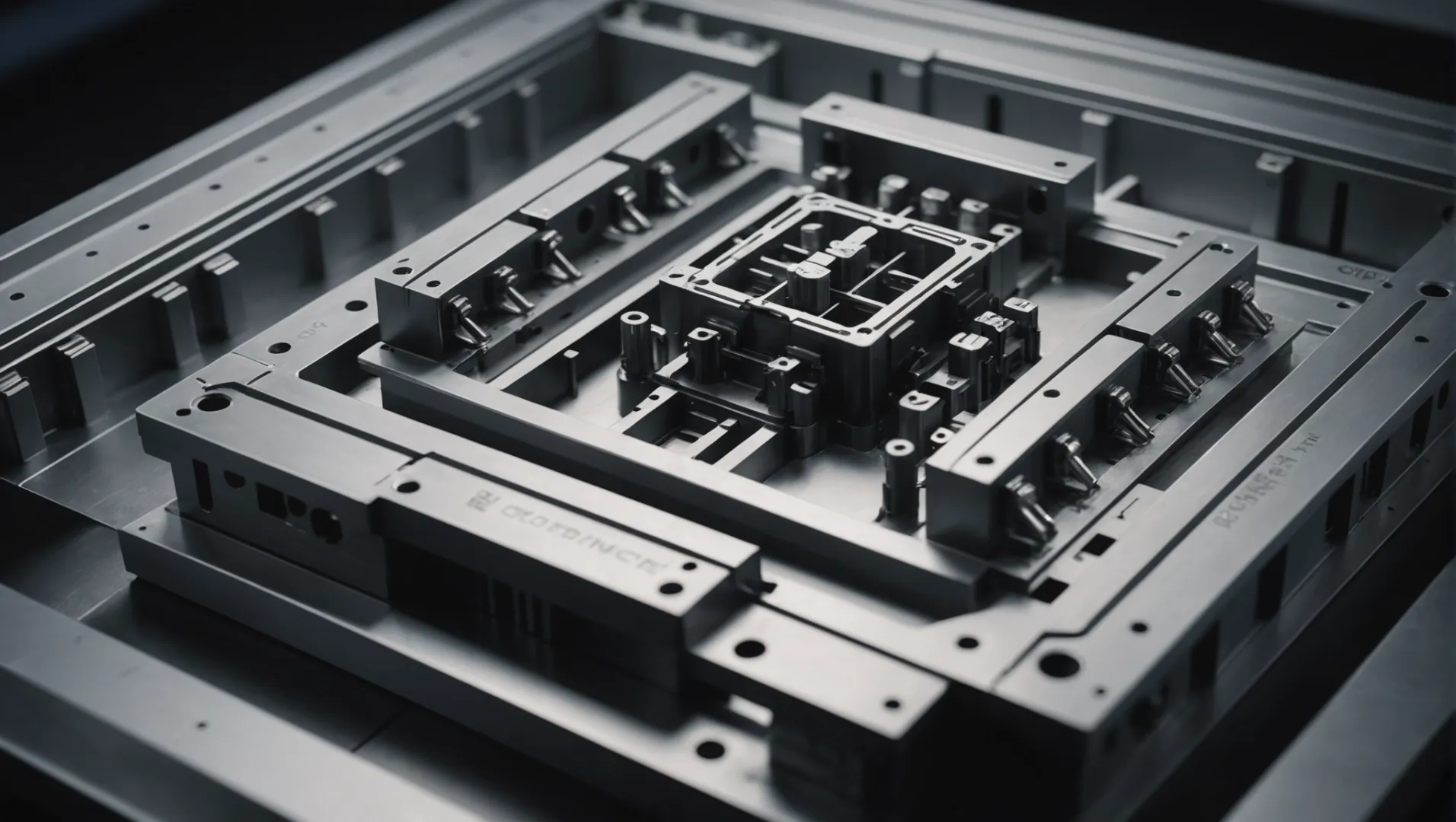
The Significance of Gate Placement
Gate placement is a crucial element in mold design that directly impacts the filling and cooling of the plastic material. Properly positioned gates ensure an even distribution of molten plastic within the mold cavity, thereby minimizing localized shrinkage.
- Optimizing Gate Location: Strategically placing gates at points where the material can flow uniformly reduces the risk of surface depressions and dimensional changes.
- Increasing Gate Number: In some designs, adding more gates can enhance the filling process, especially for larger or more complex parts.
Temperature Control Systems
Managing mold temperature is essential to prevent uneven cooling, which can lead to shrinkage and warping.
- Uniform Temperature Distribution: Utilize heating rods and cooling channels to maintain a consistent temperature throughout the mold.
- Avoiding Hot Spots: Ensure there are no areas within the mold that are significantly hotter or cooler than others, as this can cause differential shrinkage.
Wall Thickness Considerations
Wall thickness is another critical factor in controlling shrinkage. Uneven or excessively thick walls can lead to increased shrinkage.
- Designing Uniform Walls: Strive for a uniform wall thickness throughout the part to reduce differential shrinkage and deformation.
- Incorporating Reinforcing Ribs: Adding ribs can support thinner walls, reducing the likelihood of shrinkage without compromising structural integrity.
These elements of mold design, when carefully considered and implemented, play a vital role in reducing shrinkage. By focusing on gate placement5, temperature control6, and wall thickness7, manufacturers can achieve more precise and reliable injection molded parts.
Gate placement affects shrinkage in injection molding.True
Proper gate placement ensures even material flow, reducing shrinkage.
Thicker walls increase shrinkage in molded parts.True
Uneven or thick walls lead to differential shrinkage, causing defects.
How Can Process Parameters Be Adjusted to Minimize Defects?
Mastering process parameters is crucial for reducing defects in injection molding, enhancing product quality and consistency.
To minimize defects, adjust injection pressure, temperature, and cooling time according to the material’s characteristics and mold design. These adjustments ensure even filling, proper solidification, and reduced shrinkage in the final product.
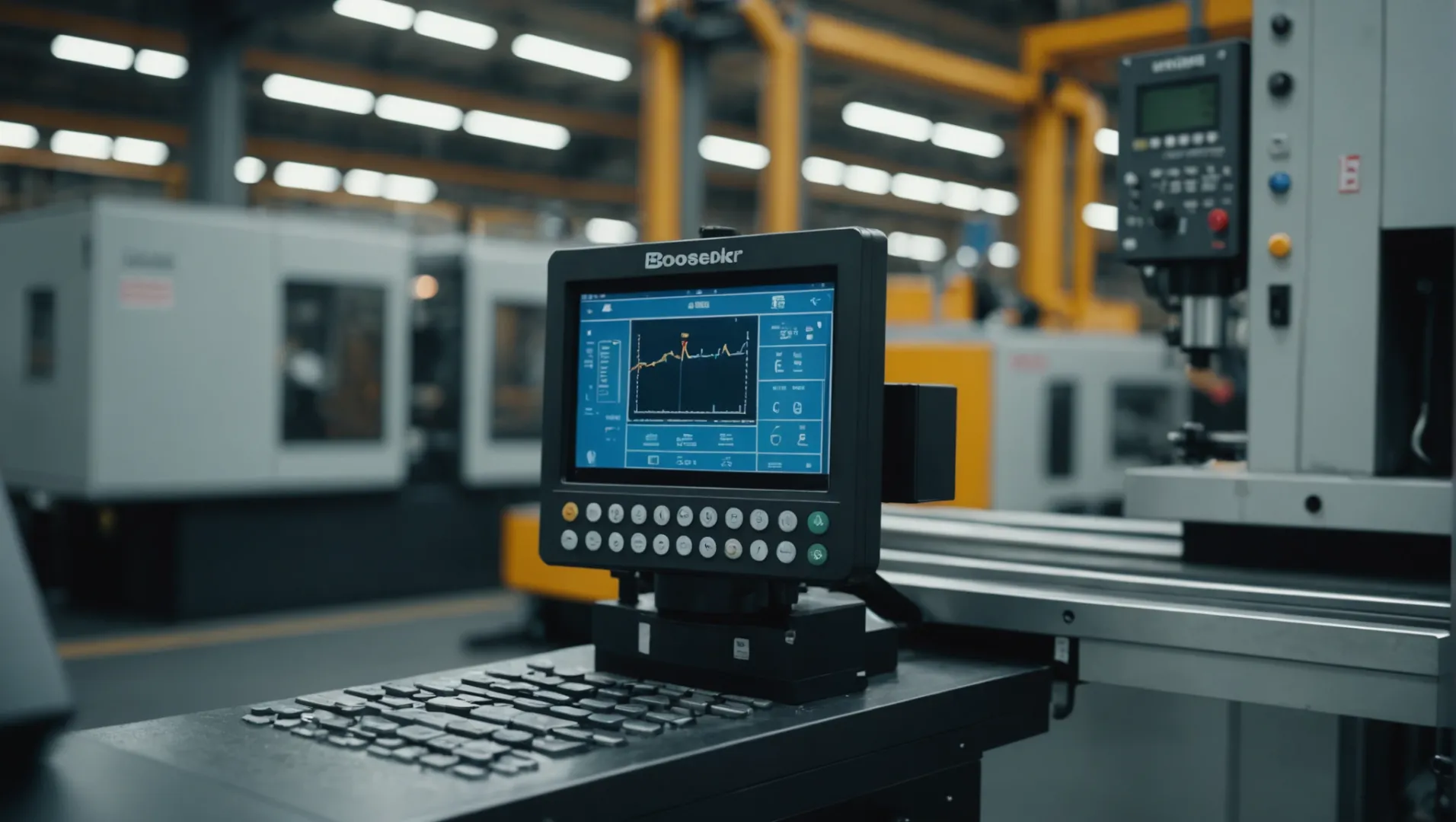
Importance of Injection Pressure and Holding Pressure
Adjusting injection pressure is vital to ensure that the plastic material fills the mold cavity completely and evenly. High injection pressure helps overcome resistance as the molten plastic flows into complex geometries. However, excessive pressure can lead to flashing issues8, so it’s crucial to balance it with the mold’s capability.
Holding pressure is equally important as it maintains the material within the mold until it begins to solidify. By extending the holding time, manufacturers can reduce shrinkage as the material cools uniformly under pressure.
Parameter | Effect on Shrinkage |
---|---|
Injection Pressure | Higher pressure reduces shrinkage |
Holding Pressure | Maintains shape during cooling |
Optimizing Injection Temperature
The temperature at which plastic is injected into the mold affects its viscosity. If the injection temperature is too high, it may cause excessive shrinkage and degrade the material. Conversely, a low temperature might not allow the material to flow adequately, leading to incomplete parts or defects like voids.
Selecting an appropriate temperature depends on the specific material’s properties9 and the desired flow characteristics. Proper temperature control ensures that the material fills all mold cavities effectively, minimizing potential defects.
Controlling Cooling Time
Cooling time is a critical parameter that affects shrinkage and warping. If the plastic is ejected from the mold before it has adequately cooled, it may continue to shrink outside the mold, resulting in deformities. Longer cooling times allow for uniform solidification but can reduce cycle efficiency.
Striking a balance between sufficient cooling and production speed is essential. Adjustments should be based on part thickness and material type, as these factors influence how heat dissipates.
Comprehensive Approach to Parameter Adjustment
Incorporating a holistic approach means continuously monitoring and adjusting all relevant parameters. Employing advanced monitoring systems can provide real-time data, enabling proactive adjustments10 to maintain quality standards.
Combining technological solutions with expert insights ensures that adjustments are precise and effective, ultimately minimizing defects in injection molded parts.
Higher injection pressure reduces shrinkage.True
Higher pressure ensures complete mold filling, reducing material shrinkage.
Longer cooling times increase production speed.False
Longer cooling times ensure uniform solidification but slow down production.
Conclusion
By identifying and addressing shrinkage defects effectively, manufacturers can ensure high-quality injection molded parts. Implementing these expert strategies not only enhances product reliability but also optimizes production efficiency. Take action now to refine your processes and achieve superior results.
-
Discover how choosing the right material reduces shrinkage defects.: The shrinkage of molded plastic parts can be as much as 20% by volume when measured at the processing and ambient temperature. ↩
-
Explore mold design strategies to minimize shrinkage issues.: Common techniques include adding draft angles, designing uniform wall thicknesses, and using ribs for structural stability. ↩
-
Learn how plastic characteristics influence their shrinkage rates.: Polymers filled with long glass fibers shrink less along the direction in which fibers align. The shrinkage occurs in the flow direction compared to the … ↩
-
Discover methods for assessing materials to reduce defects.: Learn about material properties to quantitatively analyze parts before selecting a thermoplastic resin · Comparing Injection Molding Materials · The Standard … ↩
-
Explore gate placement strategies to enhance material flow and reduce shrinkage.: Wrong gate placement leads to molding defects, such as injection molding flash, weak spots, fractures, uneven thickness, etc. Determining the … ↩
-
Learn how uniform temperature distribution prevents shrinkage and warping.: CTM-W series standard water temperature controllers are designed to heat molds while maintaining a constant temperature. ↩
-
Understand how uniform wall thickness minimizes differential shrinkage.: This under-packing can cause higher shrinkage, potentially leading to part sink and/or warp. Cooling Rate. Deviations in injection molding uniform wall … ↩
-
Learn about the impact of injection pressure on flashing issues.: Insufficient Clamping Pressure Clamping pressure, a measurement of the force needed to hold the mold closed during injection, is related to flash formation. … ↩
-
Discover how material properties influence optimal injection temperatures.: Impact on Mechanical Properties (Internal Stress). Low mold temperature makes weld lines obvious, reducing product strength. For crystalline … ↩
-
Explore advanced systems for proactive parameter adjustments.: SmartMOLD is a cloud-based software platform dedicated to the plastics industry providing real-time data to drive injection molding innovation. ↩