In the complex world of injection molding, a mold that does not fill correctly causes much frustration. Everyone has likely experienced this problem.
Analyze the injection speed, pressure and volume settings to understand if mold underfilling results from injection parameters or mold design. Examine gate position, runner design and venting conditions. This method finds the real root cause. It identifies targeted improvements.
I remember working on a tricky plastic cover once. The injection speed went from 30 cm/s to 60 cm/s. Suddenly, thin walls filled perfectly! A breakthrough occurred. Speed was very important.
But speed alone doesn’t solve everything. Sometimes, pressure needed more attention. Increasing injection pressure from 80MPa to 100MPa fixed a complicated piece. Really, adjusting the gate position also helped. It felt like solving a mystery each time.
Finding why a mold isn’t filling is not just technical. It’s both science and intuition. Each mold tells its own tale. Specific tests and observations teach us. These stories offer lessons. Let’s hear them.
Increasing injection speed improves filling.True
Increasing speed from 30 cm/s to 60 cm/s filled thin walls.
Gate size does not affect mold filling.False
Larger gate size improved filling in cantilever structures.
How Does Injection Speed Affect Mold Underfilling?
Injection speed is not just a number; it’s the key to successful mold filling. I learned this firsthand and it often determines whether a product is perfect or underfilled.
Injection speed plays a crucial role in filling a mold with molten material. Slow speed may cause the material to cool too soon. This might lead to underfilling. Adjusting the speed helps fill the mold completely, improving the quality of the product. Proper speed brings really good results. Complete filling is important.
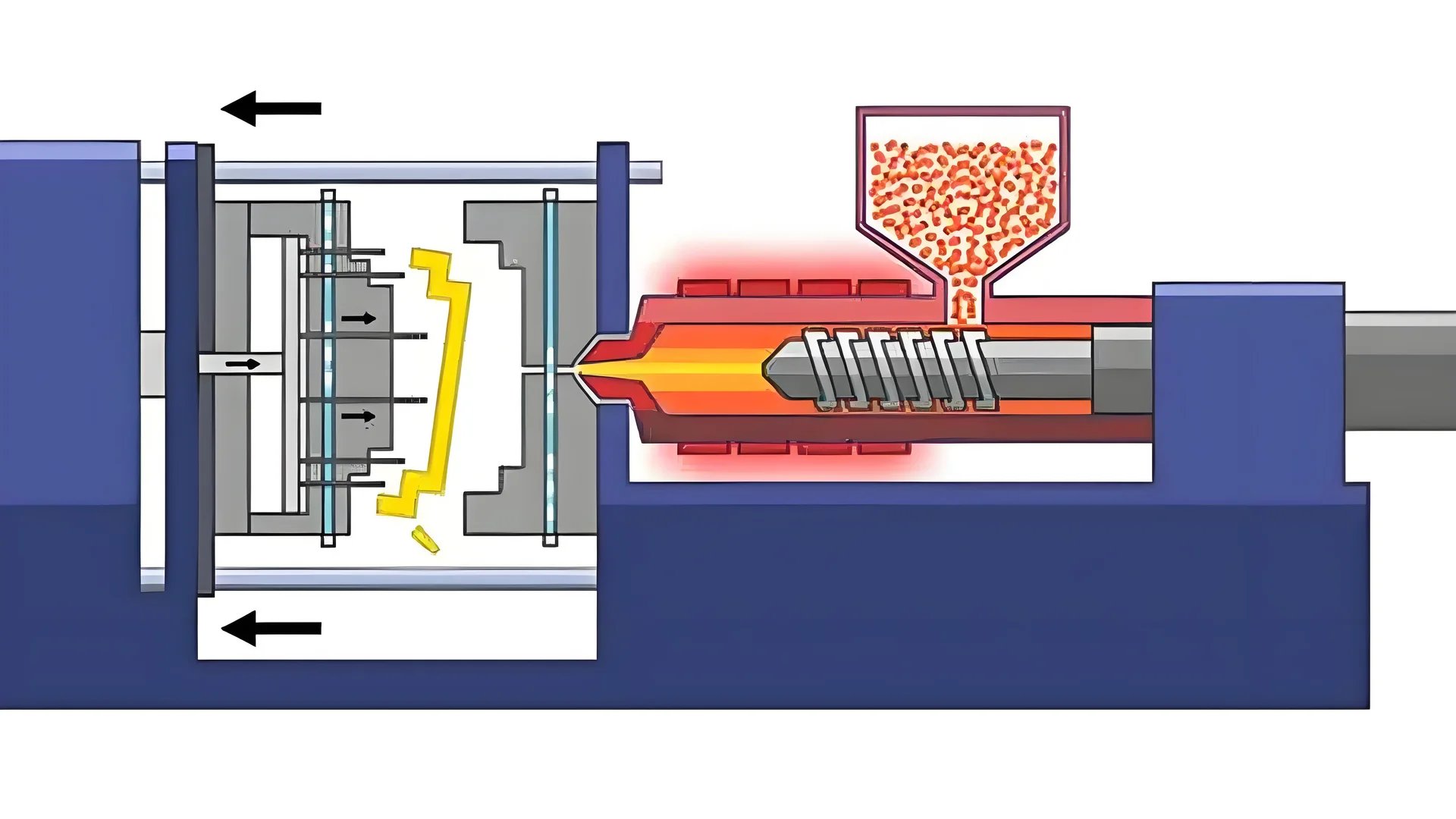
Understanding Injection Speed’s Impact
Injection speed determines how quickly molten material enters the mold. It affects how well the material fills the intricate spaces within the mold cavity. Optimizing injection speed1 ensures that the material reaches every part of the mold before it cools and solidifies.
In the beginning, I overlooked how important injection speed was. It’s not only about how quickly the hot material goes into the mold; it’s about filling every little space before it cools down. I remember a project where changing the speed solved everything. It felt magical when the parts turned out perfect. This lesson taught me that getting the right injection speed really is the secret to great molding.
Methods to Assess Injection Parameters
Injection Speed Test
Conducting an injection speed test involves gradually adjusting the speed. For instance, if increasing the speed from 30 cm/s to 60 cm/s resolves underfilling in thin-walled areas, it indicates that the initial speed was too low. This method helps determine if speed adjustments can solve underfilling issues.
Once, while working on plastic covers, I saw that increasing injection speed from 30 cm/s to 60 cm/s filled those tricky thin areas perfectly. This showed me that speed was indeed the problem.
Injection Pressure Monitoring
Monitoring pressure during injection provides insights into potential underfilling causes. If pressure does not reach its maximum and underfilling occurs, it may indicate insufficient pressure rather than speed. Gradual increases in pressure can clarify if pressure, rather than speed, is the culprit.
I remember changing pressure from 80MPa to 100MPa for a complex part, which greatly improved filling. It was a big realization that taught me to check pressure levels very carefully.
Parameter | Test Method | Indicator |
---|---|---|
Speed | Gradual Increase | Improved filling in thin areas |
Pressure | Monitor levels | Stops rising before max |
Injection Volume Check
Comparing set injection volume with actual required amounts helps identify if volume contributes to underfilling. If actual volume is below theoretical needs, it could point to issues beyond just speed, such as volume inadequacy.
Checking injection volume feels like double-checking my work. If I notice a difference between set and needed volumes, I know there’s more to explore. This has become a method I depend on.
Mold Design Factors Affecting Underfilling
Evaluation of Gate Position and Size
The gate’s position relative to unfilled areas can affect filling success. A gate too far from thin-walled sections may lead to underfilling. Adjusting gate size or location may improve filling efficiency.
Once, I worked on a long structure and found that moving the gate closer fixed filling problems. Changing gate size and position taught me to examine these aspects closely.
Runner System Check
A runner that’s too long or narrow increases melt flow resistance. Comparing runner designs with successful ones aids in identifying potential issues.
Earlier in my career, I found that a runner’s length and condition might stop flow. By comparing with successful designs, I’ve discovered that runner checks are vital to stop underfills.
Analysis of Venting Conditions
Proper venting is crucial for avoiding underfills, especially in deep cavities or blind spots. Adding exhaust slots may alleviate filling problems caused by inadequate venting.
Venting was tricky until I faced a big cavity mold that wouldn’t fill well. Adding exhaust slots solved it, showing the importance of proper venting.
For further reading on mold design checks2, exploring resources will provide more detailed insights into optimizing your injection molding process.
Increasing injection speed reduces underfilling.True
Higher injection speeds improve filling, as seen when thin-walled areas fill completely.
Gate size doesn't affect mold filling.False
Improper gate size can cause underfilling; increasing size improves filling.
How does injection pressure impact mold filling?
Picture trying to put paint into a small crack with a straw. Injection pressure works the same way with mold filling.
Injection pressure is the power that pushes melted material into every corner of a mold. Correct pressure fills the mold completely. This leads to very high-quality products without any defects.
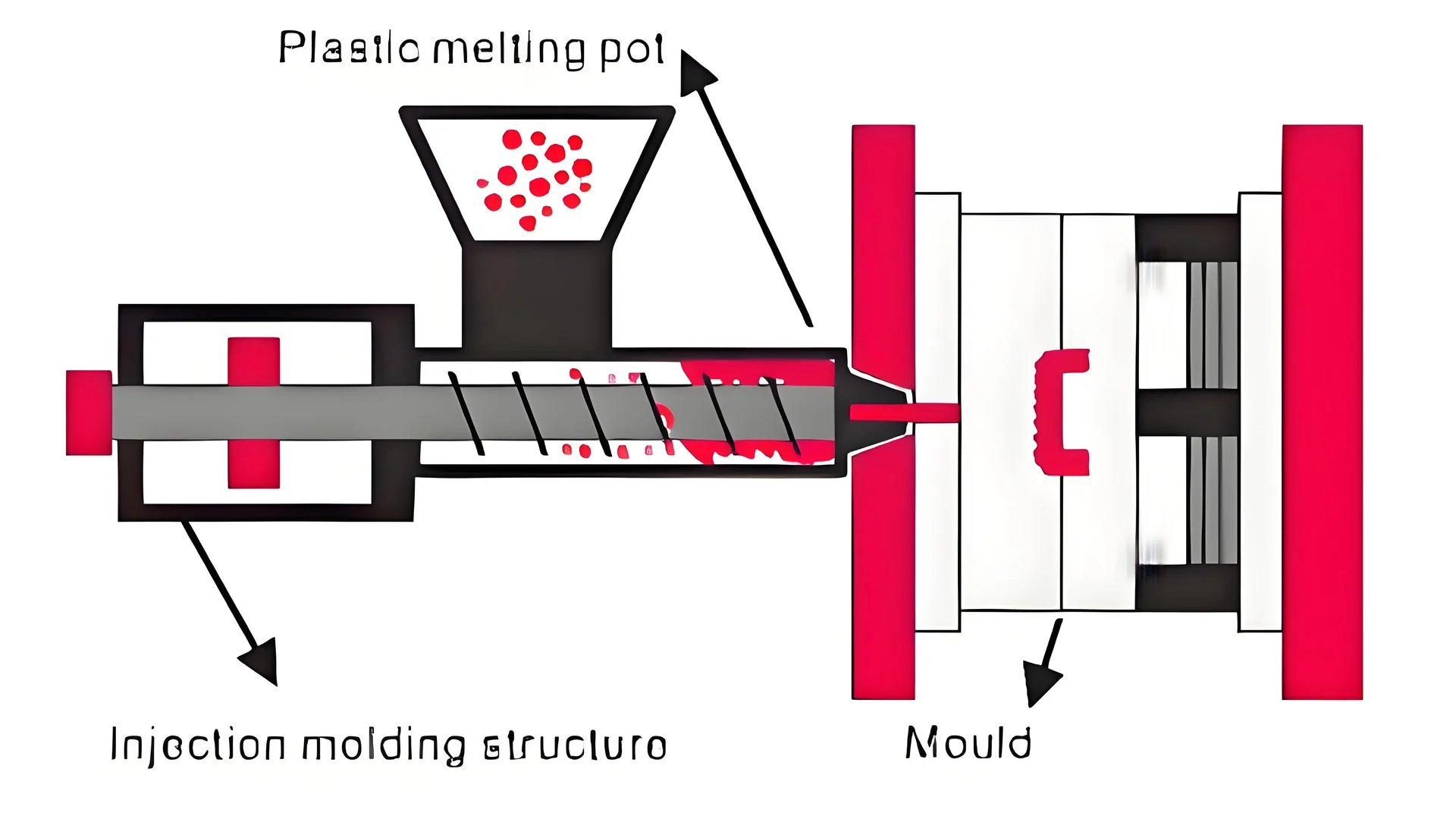
The Role of Injection Pressure in Mold Filling
When I started working in mold design, I really found that choosing the right injection pressure felt like cooking a perfect steak. Too little pressure leaves products underfilled3. Too much pressure leads to flaws like flashing or overpacking. The right amount depends on the material and the mold’s complexity.
Judging Injection Parameters
Injection Speed Test:
In my early projects, thin-walled areas weren’t filling properly. Increasing injection speed from 30 cm/s to 60 cm/s fixed the issue. It was like adjusting a car’s speed to find the perfect highway cruising pace.
Injection Pressure Monitoring:
I always watched pressure readings carefully. If pressure stopped increasing before the maximum and underfilling happened, increasing pressure helped. I had a tough case with a complex plastic piece. Raising pressure from 80MPa to 100MPa solved it completely.
Injection Volume Check:
Sometimes the problem wasn’t pressure or speed but volume. There was a project where injection volume was only 80% of what was needed. Correct volume is like having enough paint to cover an entire wall. It’s essential for a flawless finish.
Parameter | Adjustment Example | Result |
---|---|---|
Injection Speed | Increase from 30 cm/s to 60 cm/s | Improved fill in thin areas |
Injection Pressure | Increase from 80MPa to 100MPa | Better fill in complex parts |
Impact of Mold Design on Filling
Gate Position and Size:
Once, we faced an underfilling issue with a long structure. Moving the gate position closer and making it bigger solved the problem. It’s like adjusting a hose nozzle to water a garden evenly.
Runner System Check:
Long or thin runners increased melt flow resistance. It’s similar to untangling a hose for better water flow. Comparing with successful designs showed necessary changes to the runner.
Venting Conditions Analysis:
Poor venting is sneaky and causes underfilling in deep areas. Adding exhaust slots helped a lot, like opening a window for fresh air flow.
Understanding injection pressure’s role in mold filling is probably crucial for good manufacturing processes4. This knowledge is my toolbox for fixing and improving product quality in injection molding tasks.
Increasing injection speed can improve mold filling.True
Higher injection speeds help fill thin-walled areas effectively.
Gate size does not affect the filling of complex molds.False
Improper gate size can impede flow, leading to underfilling.
Why is injection volume critical in avoiding underfilling?
The smallest details in manufacturing decide if a product succeeds or fails. In injection molding, controlling the injection volume is essential to prevent underfilled parts.
Injection volume is very important. It fills the mold completely and stops any defects. Changing injection settings may fix underfilling problems. This really leads to better product quality.
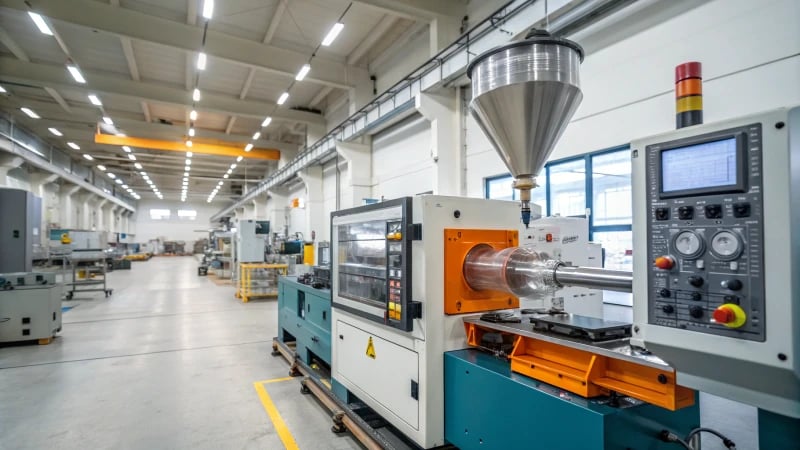
The Role of Injection Volume
Imagine cooking and pouring the perfect amount of pancake batter into the pan. Every edge fills nicely without spilling. Injection molding works similarly. If the volume isn’t exact, parts end up underfilled, which is undesirable.
Checking Injection Volume
Think of this as a quick check-up. By comparing the machine’s set volume with the needed volume, problems can be identified early and fixed. It’s like reviewing your shopping list before going to the store.
Parameter | Observation |
---|---|
Set Injection Volume | Check if it’s 100% of theoretical value |
Actual Injection Volume | Must match calculated requirement |
Injection Parameters and Their Influence
Testing Injection Speed
One project involved plastic housings. Increasing the injection speed from 30 cm/s to 60 cm/s changed everything. Thin-walled sections filled perfectly, like shifting from a stroll to a fast run.
Watching Injection Pressure
Similarly, I remember adjusting the pressure from 80MPa to 100MPa for a tricky mold. It was like adding the right amount of yeast to dough – it rose wonderfully.
Considerations for Mold Design
Position and Size of the Gate
One day, a stubborn cantilever structure caused frustration. Moving the gate closer made a big difference. Sometimes, changing perspectives helps.
Mold Feature | Recommendation |
---|---|
Gate Position | Should be near critical fill areas |
Gate Size | Large enough for adequate flow |
Analyzing Runner Systems
Runners are like highways for material. They must be smooth and direct. Even small rough areas can cause traffic jams or underfills.
Check against standard designs and previous successes to identify potential runner issues5.
Effects of Venting Conditions
Good venting is like having fresh air in a stuffy room. Adding vents where needed greatly improves filling, just like opening a window brightens a space.
Inspect molds for adequate venting, especially in deep cavities and blind holes.
Adding exhaust slots can improve airflow and filling.
These techniques always remind me how each manufacturing step links together closely. Finding the perfect balance leads to excellent product quality and efficiency.
Increasing injection speed can reduce underfilling issues.True
Higher injection speed improves filling, as seen in thin-walled areas.
Runner length has no effect on melt flow resistance.False
Longer runners increase resistance, potentially causing underfilling.
How Does Gate Design Affect Mold Filling?
Have you ever thought about why some plastic pieces look perfect, while others have many problems?
Gate design is very important in mold filling. It guides the flow and speed of molten material. This affects how well the mold fills. Incorrect gate size or placement leads to problems like underfilling or warping. These mistakes harm the product quality. It really affects the final product quality.
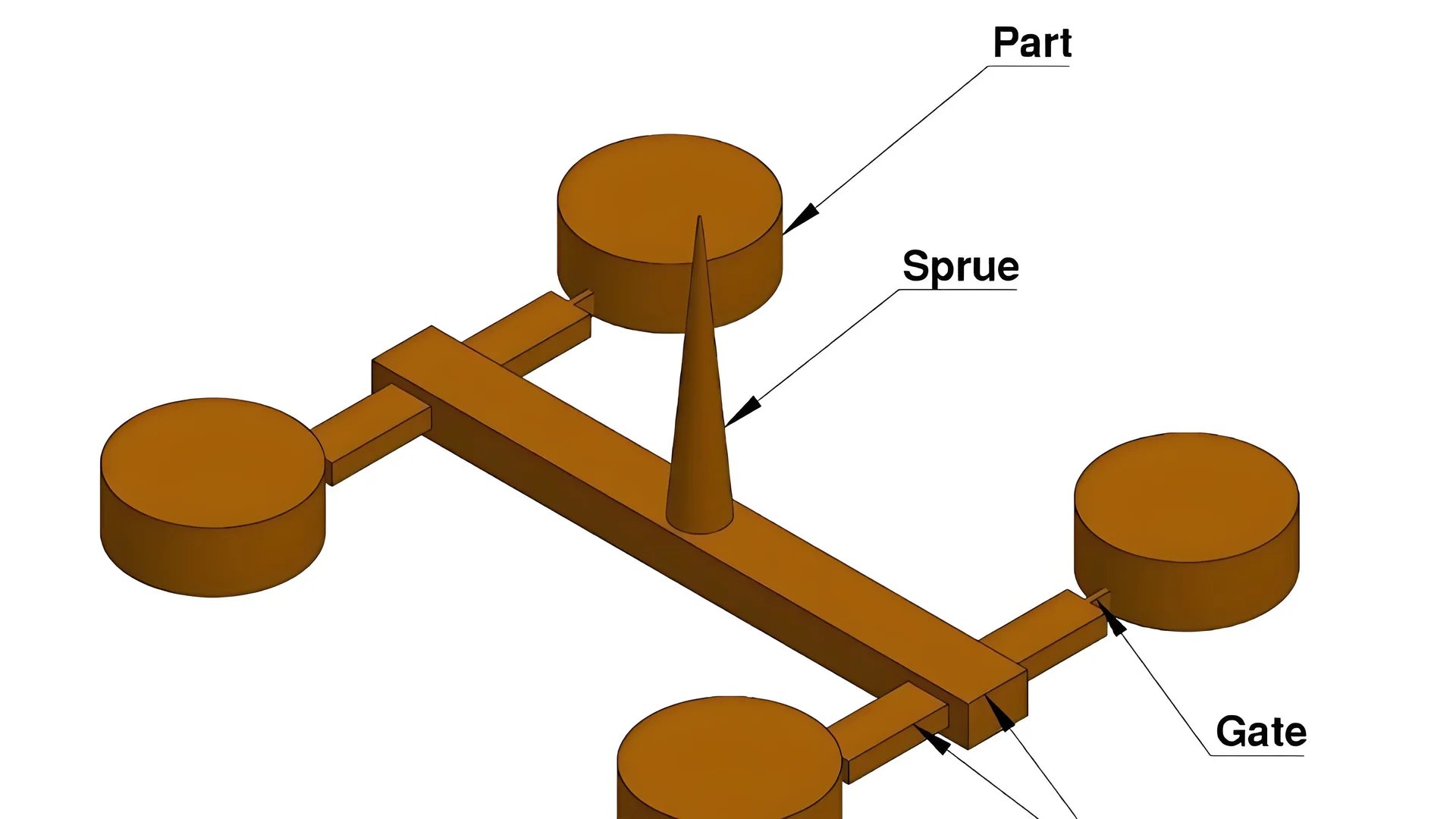
The Role of Gate Design in Mold Filling
When I began working in mold design, I didn’t understand the importance of gate design for the whole process. It’s similar to arranging dominoes perfectly; one wrong piece can spoil the entire setup. The gate’s size, shape, and position are vital for filling every part of the mold with molten plastic.
Design Element | Impact on Mold Filling |
---|---|
Gate Size | Influences flow rate and pressure distribution. Smaller gates may cause underfilling. |
Gate Position | Affects flow path; incorrect placement can result in incomplete filling of sections. |
Methods of Judging Mold Design
I recall a project with underfilling issues. By changing the gate’s position closer to the cantilever structure, we saw a big improvement. This felt like finding a hidden key for better results.
-
Gate Position and Size Evaluation
- If some parts remain unfilled far from the gate, it might signal a wrong gate location. For example, shifting the gate nearer to a cantilever can help with filling.
-
Runner System Check
- Examining runner dimensions is like spotting traffic jams. Long or narrow runners may increase resistance to melt flow, causing filling troubles6.
-
Venting Analysis
- Venting is also very important. I once added extra exhaust slots to a mold with deep cavities. This change stopped air traps and fixed underfilling issues.
Methods of Judging Injection Parameters
Injection parameters act like the hidden ingredient in mold filling. Changing these reveals a design’s true abilities.
-
Injection Speed Test
- I recall changing the injection speed during production. Thin-walled areas went from underfilled to perfect when speed increased.
-
Injection Pressure Monitoring
- Keeping an eye on pressure is very important. I’ve observed how raising pressure from 80MPa to 100MPa greatly improves fill quality.
-
Injection Volume Check
- Checking that the injection volume matches what is needed theoretically is crucial for effective mold filling7. Mistakes here often lead to underfilling.
Increasing injection speed improves filling in thin-walled areas.True
Higher injection speed enhances flow, filling thin-walled sections effectively.
Runner surface roughness does not affect melt flow resistance.False
Rough runner surfaces increase resistance, hindering melt flow.
What are the key considerations for runner system design?
Ever tried to make something perfect and ended up deep in changes? That’s runner system design! Let’s explore the important parts that keep it going.
Key points for designing a runner system include checking runner length, width and surface quality. Proper placement and size of gates are important. Watching injection settings and inspecting venting conditions really matter.
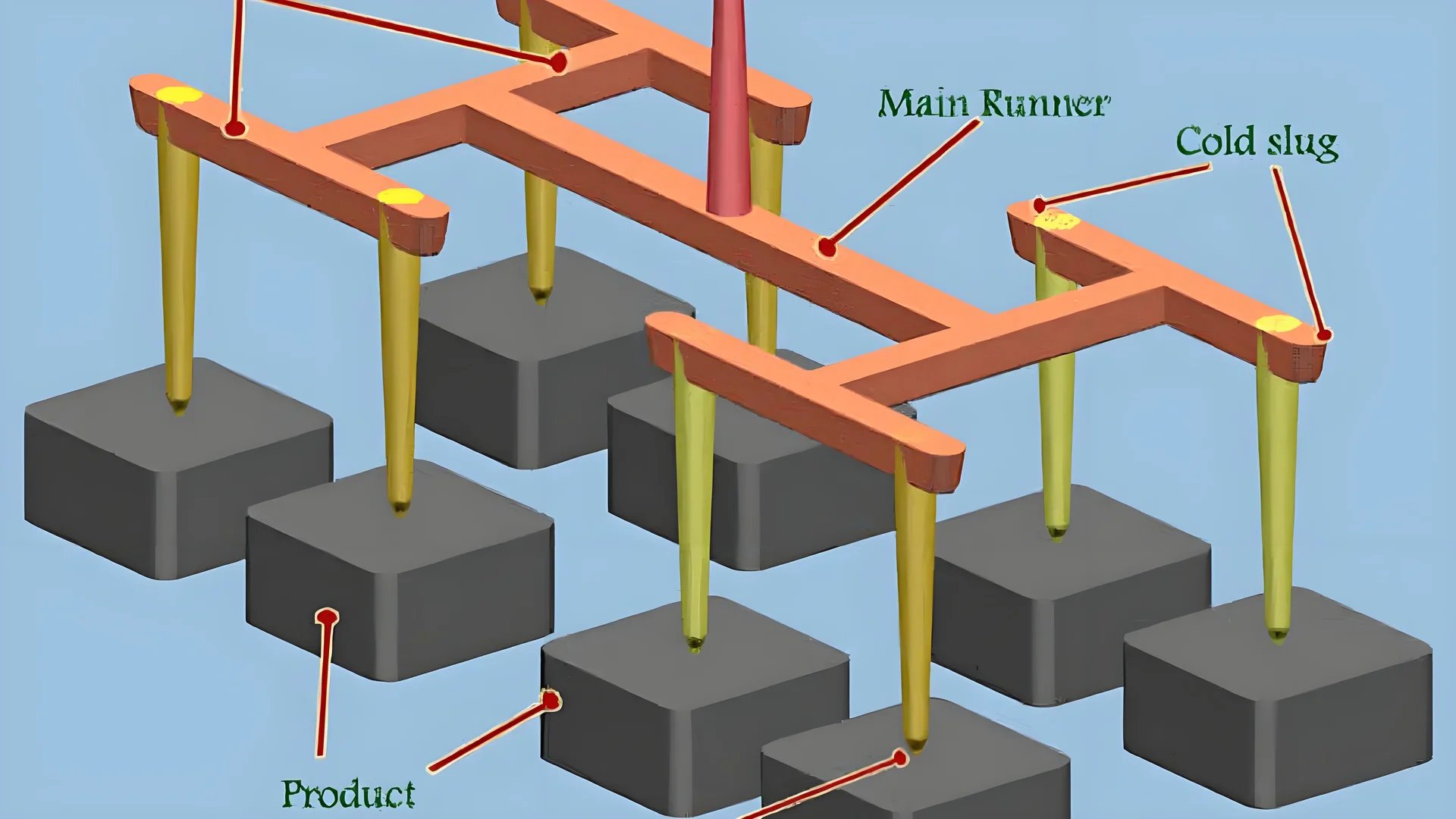
Evaluating Runner Length and Diameter
Running a long race feels tough with every extra step. A longer runner makes the flow in injection molding slow. One day, I cut the length of a runner in half and everything filled perfectly with less material waste. Changing the runner’s diameter is similar to adjusting water flow from a hose. It needs to be just right to keep the pressure steady.
Example: If a runner is twice as long as a successful previous design, evaluate if reducing length improves fill.
Surface Condition of the Runner
Rubbing your hand on a rough surface feels uncomfortable. A rough runner surface disrupts the melt flow in the same way. I compared a new mold with standard designs8, which felt like using a recipe that works well. Smooth surfaces reduce turbulence and even out distribution.
Tip: Regular checks and fixes act as your reliable partners. They help find small flaws before they become big problems.
Gate Position and Size
Choosing the correct window spot in a house brings in the right light. I worked on a tricky mold and found placing the gate closer to a complex section helped a lot. Suddenly, stubborn underfilled areas received enough material.
Case Study: Moving a gate nearer to a cantilever section improved fill, highlighting improper initial placement.
Monitoring Injection Parameters
Adjusting injection speed, pressure, and volume resembles tuning an old radio for a clear signal:
- Speed: In one project, increasing the injection speed from 30 cm/s to 60 cm/s improved thin-walled areas from poorly filled to well-formed structures.
- Pressure: Monitor and adjust injection pressure to address filling problems effectively.
- Volume: Ensure set volumes align with actual requirements to prevent short shots.
Parameter | Test | Impact |
---|---|---|
Speed | Gradual increase | Improves fill in thin areas |
Pressure | Incremental adjustment | Resolves complex fills |
Volume | Check against theoretical needs | Prevents short shots |
Assessing Venting Conditions
Cooking without opening a window keeps the air trapped and causes mistakes. Poor venting does this too. Cleaning vents is like opening a window, allowing everything to breathe and function smoothly.
Solution: Adding or cleaning vents can significantly improve mold fill efficiency by preventing air traps that cause defects.
By managing these factors, I noticed the process flows very smoothly. Small adjustments led to significant changes in quality and efficiency.
Increasing injection speed improves underfilling.True
Higher injection speeds can help fill thin-walled areas more effectively.
Long runners reduce resistance to melt flow.False
Long runners increase resistance, potentially leading to underfilling issues.
Conclusion
This article explores how to identify mold underfilling issues in injection molding by analyzing injection parameters and mold design factors, emphasizing the importance of speed, pressure, volume, and gate design.
-
Exploring optimization techniques will help understand how to prevent underfilling through speed adjustments. ↩
-
Understanding mold design considerations can aid in improving product quality by addressing underfilling. ↩
-
Explore the causes and effects of underfilled products to understand common issues in injection molding. ↩
-
Learn methods to enhance manufacturing efficiency, focusing on injection molding techniques. ↩
-
Identifying common runner design errors helps mitigate flow resistance and improve mold filling efficiency. ↩
-
Exploring the impact of runner systems can improve molding efficiency and product quality. ↩
-
Correct injection volume ensures complete filling, enhancing product integrity and reducing defects. ↩
-
Examining standard designs provides benchmarks for creating efficient runner systems. ↩