Getting the rib-to-wall ratio right in injection molding can turn a challenging project into a success story.
The ideal rib-to-wall ratio for injection molding is whith in 0.5 times the wall thickness, minimizing sink marks and maintaining structural integrity.
But let’s not stop there—this is just the tip of the iceberg. Think of it like baking a cake; you need the right ingredients in the right amounts, but also the right techniques to make it perfect. Factors like the choice of material, the intended function of the part, and specific mold design considerations can fine-tune your process for even better results. As someone who’s seen both triumphs and trials in this field, I know how crucial these details can be. Let’s dive deeper into these elements so you can achieve that flawless finish every time.
The ideal rib-to-wall ratio is within 0.5 times the wall thickness.True
This ratio minimizes defects like sink marks and maintains strength.
Material choice does not affect the rib-to-wall ratio.False
Material properties influence design considerations, including ratios.
- 1. Why is Rib-to-Wall Ratio Important in Injection Molding?
- 2. How Does Material Choice Affect Rib Design?
- 3. What are Common Mistakes in Rib Design?
- 4. How Do You Determine the Best Rib Dimensions?
- 5. What Tools Can Assist in Designing Ideal Ribs?
- 6. How Do Ribs Impact the Aesthetic of Molded Parts?
- 7. Conclusion
Why is Rib-to-Wall Ratio Important in Injection Molding?
I once learned the hard way that a small oversight in design can lead to big issues down the line.
The rib-to-wall ratio is vital in injection molding for maintaining structural integrity, preventing warping or sink marks, and ensuring optimal performance and appearance.
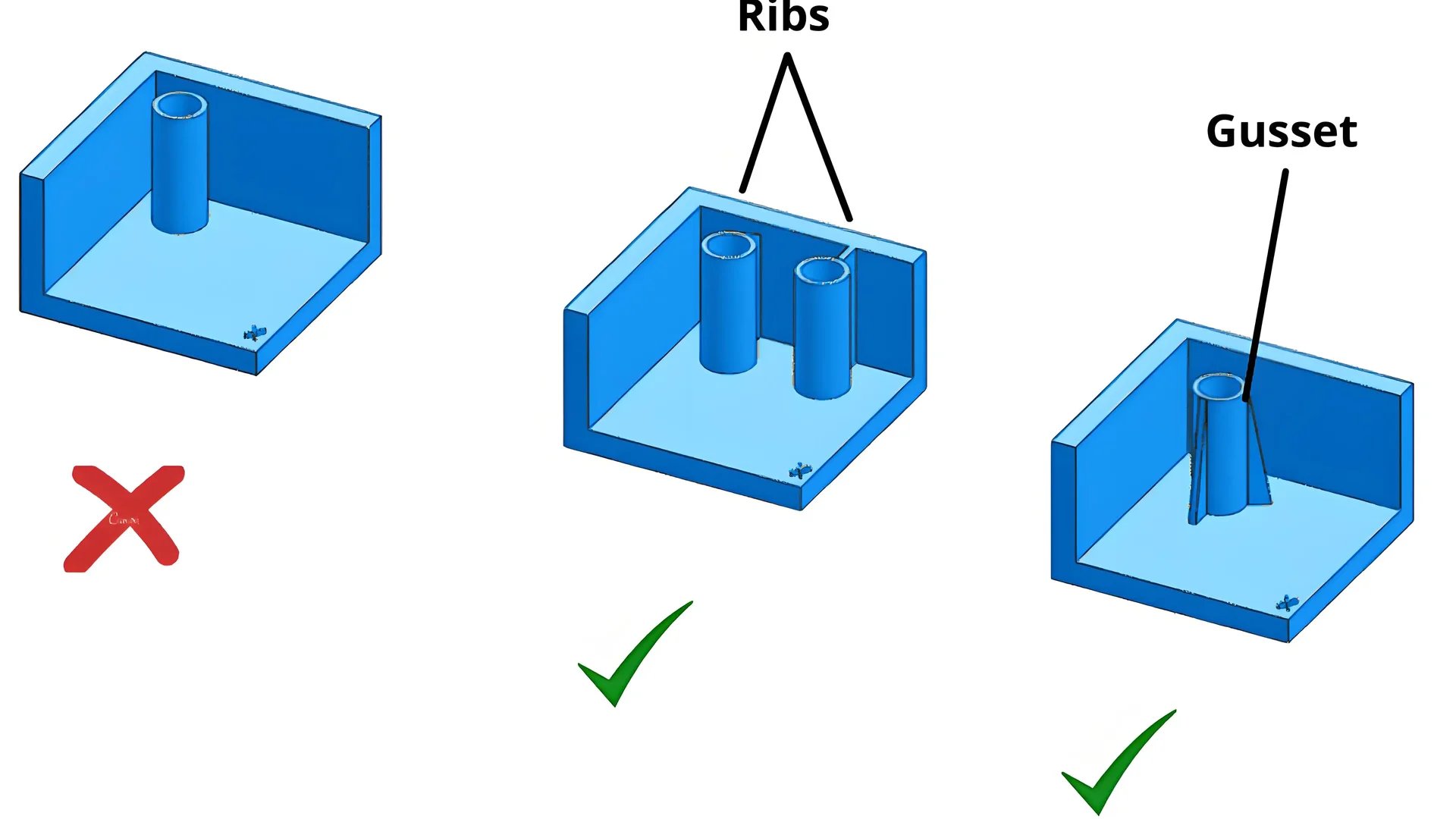
Understanding Rib-to-Wall Ratio
Let me take you back to a project I worked on where I underestimated the importance of the rib-to-wall ratio. It was a lesson learned the hard way! This ratio is vital because it influences how well a part can withstand mechanical stresses. Ribs are like the unsung heroes in plastic parts—they add strength without much extra weight. But if you don’t get the ratio right, you’re looking at a host of manufacturing issues1.
Common Defects Due to Improper Ratios
Imagine this: you’ve just wrapped up a design for a sleek new gadget, only to find out during testing that your prototype warps like a plastic spoon in hot soup! That’s what happens when ribs are too thick—they cool at different rates, causing warping.
- Warping: Too-thick ribs lead to uneven cooling, resulting in warping.
- Sink Marks: Thick ribs can pull material inward during cooling.
- Stress Concentration: If ribs are too thin, stress might concentrate, reducing durability.
To avoid these defects, it’s crucial to follow guidelines on rib design:
Rib Thickness | Wall Thickness | Ratio |
---|---|---|
0.5 mm | 2 mm | 0.25 |
1 mm | 4 mm | 0.25 |
2 mm | 8 mm | 0.25 |
Best Practices for Rib Design
- Tapered Ribs: Slightly tapering the ribs from base to tip helps—think of it as giving them a subtle waistline.
- Rounded Corners: Avoid sharp corners; they’re stress magnets!
- Spacing Between Ribs: Space them out enough to keep stress fields from overlapping.
Case Study: Electronics Housing Design
Picture this: You’re designing an electronics housing where ribs play a crucial role in reinforcement. You must calculate the rib-to-wall ratio carefully to avoid any embarrassing warping or those pesky sink marks.
Designers like me often turn to simulation software to foresee any hiccups before production kicks off. It’s like having a crystal ball for rib designs and wall thicknesses. If you’re interested in diving into simulation techniques, check out this related resource2.
Thick ribs cause warping in molded parts.True
Thick ribs lead to differential cooling, causing warping.
Rib-to-wall ratio of 0.5 is recommended.False
The recommended rib-to-wall ratio is typically 0.25.
How Does Material Choice Affect Rib Design?
Ever wonder how the choice of material can make or break a rib design? I’ve seen firsthand how picking the right one can transform a project.
Choosing the right material is crucial in rib design, affecting thickness, height, and spacing. Materials differ in tensile strength and flexibility, shaping these design elements.
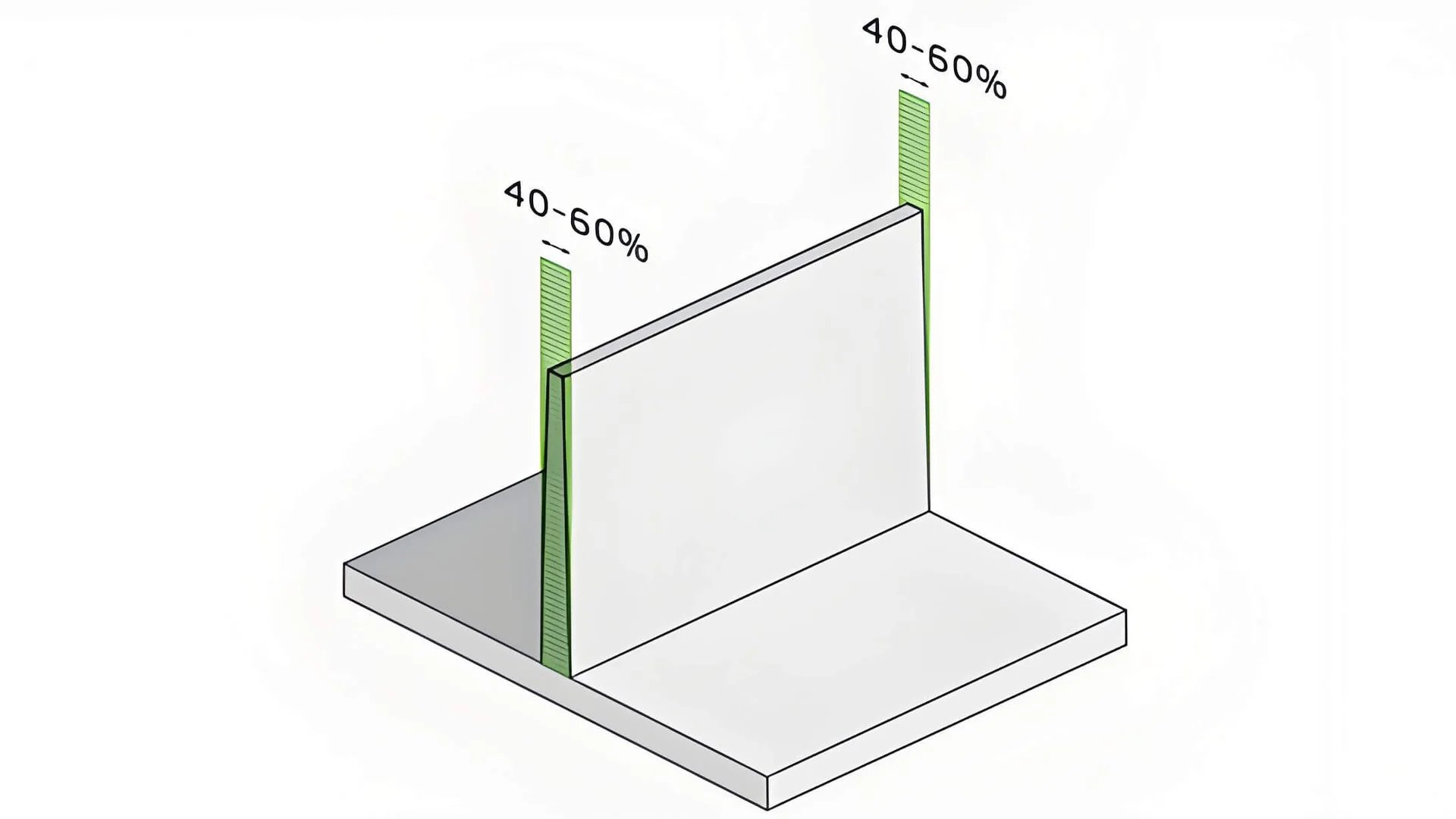
Understanding Material Properties
Every material tells its own story in design. I remember when I first discovered how ABS3 offered both strength and impact resistance. It was like a light bulb went off. For projects where flexibility is key, polypropylene became my go-to because of its excellent chemical resistance.
Influence on Rib Thickness
I’ve learned through trial and error that rib thickness can really make or break a design. Using polycarbonate, I was amazed at how much strength could be maintained even with thinner ribs. But when working with more flexible materials, going thicker is sometimes unavoidable to keep things rigid.
Material | Typical Rib Thickness |
---|---|
Polycarbonate | 0.5 – 1.0 mm |
ABS | 1.0 – 2.0 mm |
Polypropylene | 2.0 – 3.0 mm |
Effect on Rib Height and Spacing
I once had a project where the choice of nylon, with its high strength-to-weight ratio, allowed for ribs that were taller and spaced further apart—an elegant solution that reduced material usage without sacrificing strength. With polyethylene, though, it was a different story; we had to opt for shorter, closely spaced ribs for adequate support.
- Nylon: Allows for taller ribs due to its high strength-to-weight ratio.
- Polyethylene: Might require shorter, closely spaced ribs for sufficient support.
Thermal Considerations
Thermal properties are like the unsung heroes of rib design. I’ve had moments where neglecting them led to unexpected warping. Now, I always make it a point to consider materials that can withstand high temperatures without deforming, ensuring the parts hold up over time.
Understanding how different materials respond to thermal stress has been pivotal in predicting how rib designs will perform across various applications.
Practical Examples and Guidelines
In one of my projects focused on consumer electronics, using ABS4 with well-thought-out rib geometry truly enhanced durability while keeping the weight in check. It’s those little tweaks that make a big difference.
I’ve found that leveraging simulation tools to model rib designs under different conditions has been invaluable. It’s like having a crystal ball to foresee real-world performance before making any commitments.
By delving into these details, I aim to craft components that seamlessly balance function and aesthetics, ensuring they meet all requirements efficiently.
Polycarbonate ribs can be thinner than polypropylene ribs.True
Polycarbonate's strength allows for thinner ribs compared to flexible materials like polypropylene.
ABS requires the thickest ribs among common plastics.False
Polypropylene, not ABS, typically requires thicker ribs due to its flexibility.
What are Common Mistakes in Rib Design?
Ever wonder why some products just seem to fall apart? It might come down to rib design.
Common rib design mistakes include incorrect thickness, poor placement, neglecting draft angles, and ignoring material flow, leading to structural integrity issues, warping, or aesthetic flaws.
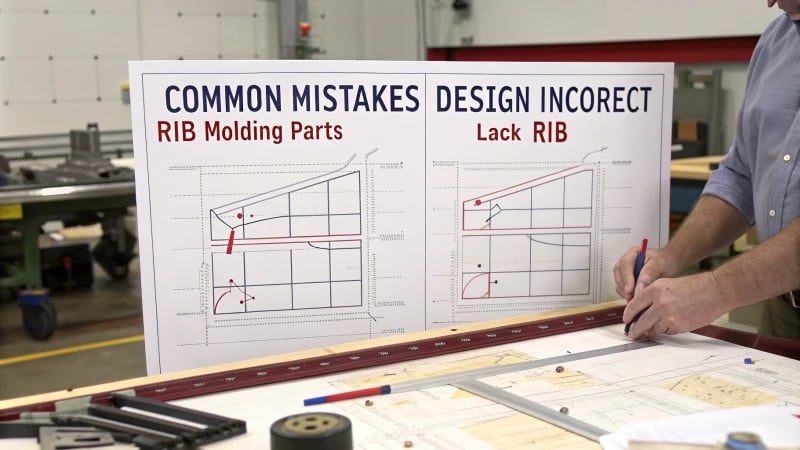
Rib Thickness Errors
I remember the first time I made a blunder with rib thickness. I was working on a sleek new gadget case, and I thought, "Hey, thicker ribs will make it stronger, right?" Wrong! When the parts came out of the mold, they were marred with unsightly sink marks5, like dimples on a golf ball. To avoid this, the rule of thumb is to keep rib thickness under 50% of the nominal wall thickness.
Rib Thickness | Impact |
---|---|
Too Thick | Sink Marks, Warping |
Too Thin | Insufficient Strength |
Incorrect Rib Placement
Placement is key—trust me, I’ve learned the hard way. During one project, I placed ribs too close together, thinking it would reinforce the product. Instead, it choked off material flow6 and left me with incomplete fills. Just like how crowding your plants can stunt their growth, ribs need space to ensure even distribution and strength.
Lack of Draft Angles
Draft angles might seem like an afterthought, but without them, you’re setting yourself up for a disaster during ejection. Imagine trying to yank a tight boot off your foot—it’s not easy, right? Parts can get stuck or damaged without at least a 0.5° draft angle.
Overlooking Material Flow
Understanding material flow is like being a detective of plastic pathways. Once, I ignored how materials would travel through my design, leading to warped pieces that looked more like modern art than consumer electronics due to uneven shrinkage7. Running simulations with CAD software can save you from these headaches by predicting how your design will behave in reality.
- Simulation Software: This has become my go-to tool for catching potential issues before they happen.
- Material Selection: Just as important as the design itself—picking the right materials prevents brittleness or unwanted flexibility.
By learning from these errors, I’ve honed my skills and now approach rib design with a mix of caution and creativity. It’s about balancing aesthetics with functionality to create products that don’t just look good but also stand the test of time.
Ribs should not exceed 60% of wall thickness.True
Exceeding this thickness can cause sink marks and warping.
Draft angles are unnecessary in rib design.False
Draft angles prevent ejection issues and reduce mold wear.
How Do You Determine the Best Rib Dimensions?
Ever found yourself lost in the world of rib dimensions, wondering how to get them just right?
To determine optimal rib dimensions, consider material properties, load distribution, and design constraints. Utilize engineering formulas or design software to ensure robust and visually appealing designs.
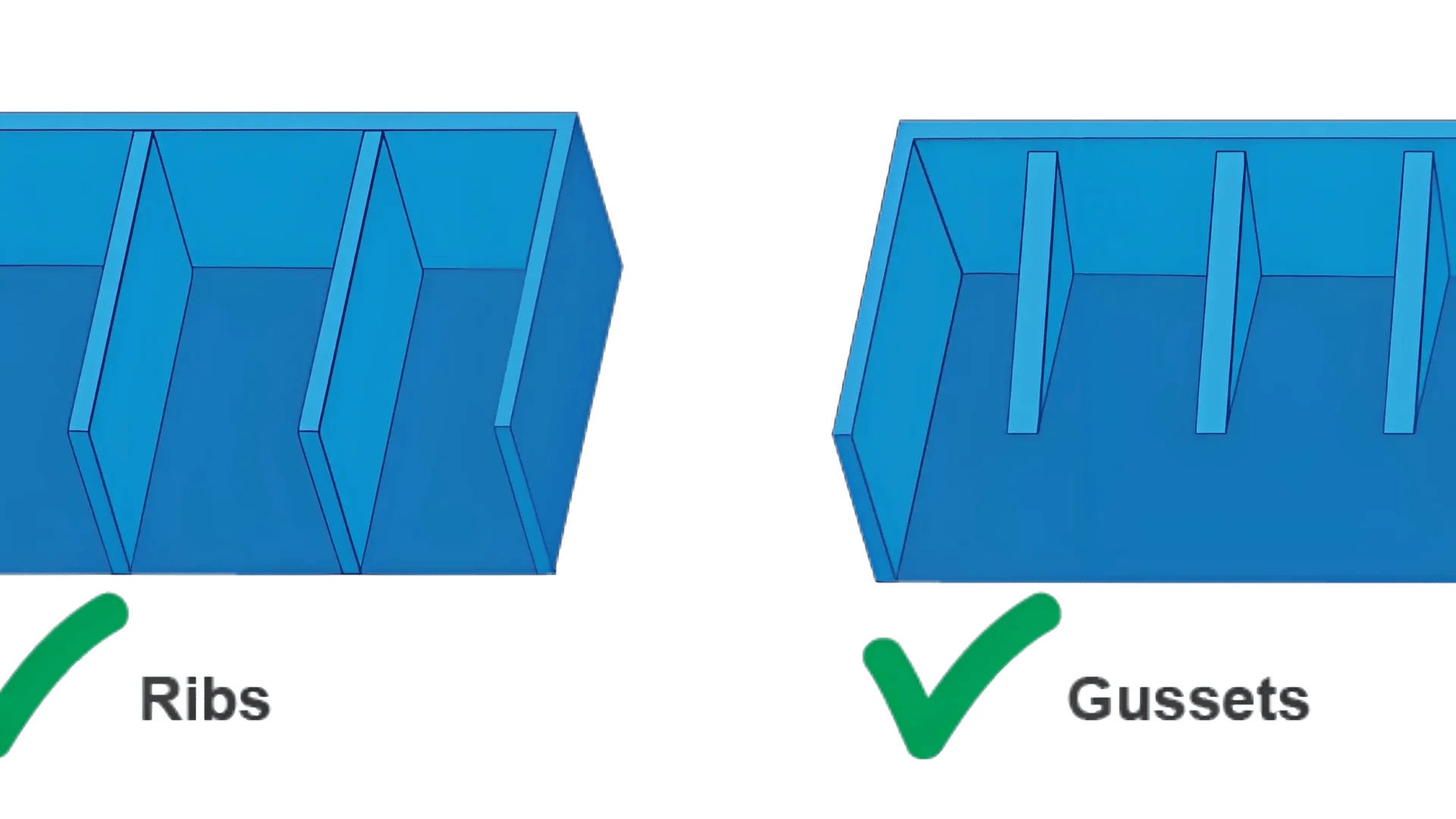
Understanding Rib Functions
Ribs serve as critical components in various fields, from textile design to engineering structures. In textiles, ribs add elasticity and texture, while in engineering, they provide reinforcement. Understanding the purpose of your ribs helps in choosing appropriate materials8.
When I first started in the field, I was baffled by the importance of ribs. Over time, I realized that understanding what role your ribs play is key to picking the right materials. For example, a friend of mine once chose a plastic material for ribs, thinking it would be lighter but soon realized that the flexibility required thicker ribs than anticipated.
Key Factors Influencing Rib Dimensions
-
Material Properties: Different materials have varied strength and elasticity. For instance, plastics may require thicker ribs than metals due to their inherent flexibility. I remember working on a project where I underestimated how much thicker plastic ribs needed to be compared to metal ones.
-
Load Distribution: Analyze how loads are distributed across the rib structure — it’s like planning a road trip; you need to know where the weight is going to sit. This will help determine the necessary thickness and spacing.
-
Design Constraints: Consider any aesthetic or functional limitations your design might impose. Sometimes aesthetics rule; for example, visible ribs might need to adhere to specific dimensions for uniformity.
Calculating Rib Thickness
A general formula for rib thickness in engineering is within 0.5 times the wall thickness of the part it’s supporting. In textiles, it’s more about feel — how much stretch do you want? Use the following table as a guide:
Material Type | Recommended Rib Thickness (as % of wall thickness) |
---|---|
Plastic | within 50% |
Metal | 30-50% |
Fabric | Based on stretch requirements |
Leveraging Software for Precision
For complex designs, leveraging software like CAD can aid in precise calculations. These tools allow for simulation and testing under different conditions, ensuring that your ribs meet both structural and aesthetic criteria.
I can’t count how many times CAD tools have saved my designs from becoming engineering disasters.
Real-World Examples and Case Studies
Consider case studies where optimized rib dimensions have led to significant improvements in product performance. For instance, in automotive design, proper ribbing9 can reduce weight without compromising strength.
I love diving into case studies where rib optimization led to breakthroughs; these stories provide inspiration and cautionary tales for my own projects.
By examining different scenarios, we can gain insights into practical applications and potential pitfalls to avoid in our own projects.
Ribs in textiles add elasticity and texture.True
Textile ribs enhance stretch and texture, serving functional roles.
Metal ribs require thicker dimensions than plastic.False
Plastic requires thicker ribs due to its flexibility compared to metal.
What Tools Can Assist in Designing Ideal Ribs?
Ever stared at a plastic component and wondered how those tiny ribs make such a big difference? I have, and I’ve found the right tools to make rib designing a breeze.
Tools like CAD software, simulation programs, and design guides assist in designing ideal plastic ribs by optimizing their dimensions, placement, and integrity for efficient manufacturing and performance.
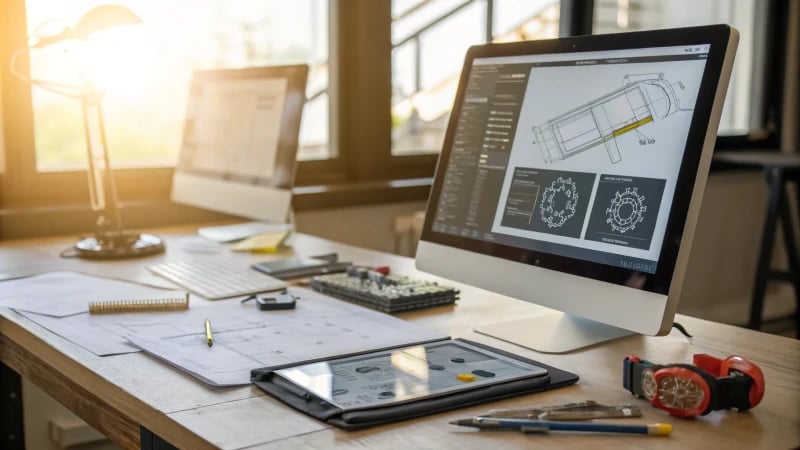
The Role of CAD Software
Let me take you back to my first encounter with CAD software10. It was like discovering a new language—one that spoke in dimensions and shapes. Tools like SolidWorks and AutoCAD became my go-to translators, helping me visualize complex rib designs with precision. They allow me to simulate different structures, showing how stress moves across them and helping me refine shapes for aesthetics and functionality.
Key Features of CAD Tools:
Feature | Benefit |
---|---|
3D Modeling | Visualize complex rib designs accurately |
Simulation | Test rib strength under various conditions |
Parametric Design | Quickly modify dimensions for optimization |
Importance of Simulation Programs
I’ll never forget the time I underestimated the stress load on a rib design. Thankfully, simulation tools like ANSYS caught my oversight before it became an expensive mistake. They are like my safety net, allowing me to test how ribs will behave in real-world conditions and tweak materials to optimize performance.
Benefits of Simulation:
- Identify potential failure points
- Optimize material usage
- Predict product lifespan
Design Guides and Standards
When I was starting out, design guides were my best friends. Resources like the "Injection Molding Handbook" provided insights that saved me from countless rookie errors. They taught me about essential principles like rib-to-wall thickness ratios and how to avoid common pitfalls like sink marks.
Reference Guides11 often include:
- Recommended rib-to-wall thickness ratios
- Suggestions for rib spacing and orientation
- Tips on minimizing sink marks and other defects
By using these tools12, I’ve learned to create rib designs that are not only functional but also efficient for manufacturing processes. Leveraging CAD software, simulation programs, and comprehensive design guides has enhanced my workflow significantly.
Balancing Aesthetic and Functional Requirements
In my experience, balancing aesthetics with functionality is like walking a tightrope. Advanced rendering capabilities in CAD tools help me evaluate the visual impact while ensuring structural integrity. By incorporating these techniques, I’ve been able to craft innovative solutions that meet both consumer expectations and production constraints. These resources have helped me stay ahead in the competitive landscape of product design.
CAD software allows for precise rib design modeling.True
CAD software provides tools for accurate 3D modeling and visualization.
Simulation programs cannot predict rib failure points.False
Simulation tools like ANSYS can identify potential failure points.
How Do Ribs Impact the Aesthetic of Molded Parts?
When I first started designing molded parts, I was amazed at how something as simple as a rib could transform both the look and feel of a product.
Ribs enhance the aesthetic of molded parts by influencing surface finish, thickness, and design complexity. They offer structural support but need careful design to avoid visual defects.
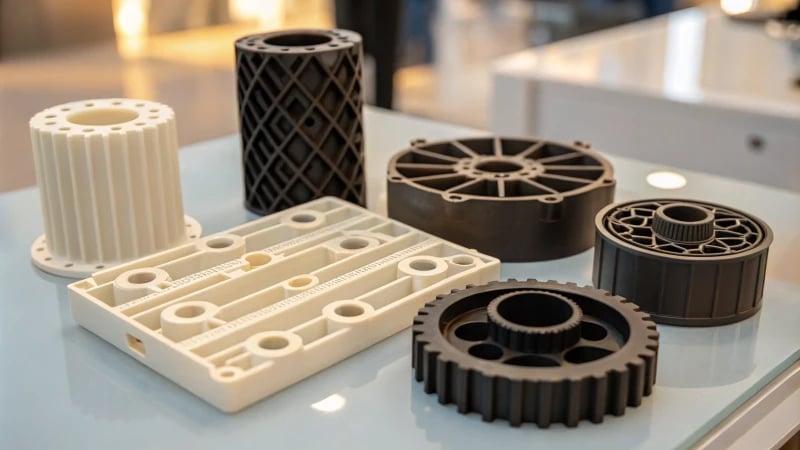
Surface Finish and Appearance
I remember the first time I saw "sink marks" on a product; it was a wake-up call. These visible blemishes can mar an otherwise sleek design, often occurring when the material cools unevenly around ribs. Over the years, I’ve learned that by optimizing rib dimensions and placement, we can significantly enhance the surface finish13. This became second nature, like remembering to put on a seatbelt.
Another crucial lesson was maintaining a uniform wall thickness. Think of it like baking a cake—you wouldn’t want one side to rise higher than the other. A good rule of thumb is to keep rib thickness under 60% of the adjacent wall. This approach not only smooths the exterior but also keeps structural integrity intact.
Visual Complexity and Design Considerations
Incorporating ribs is like choosing a frame for a photograph—it can either enhance the picture or distract from it. I’ve found that an intricate rib pattern can add sophistication, but overdoing it leads to a cluttered look. The key is finding that sweet spot between simplicity and functional complexity.
Thank goodness for CAD software14, which lets me play around with designs before they ever hit production. This way, I can experiment with rib patterns and see how they impact aesthetics without any real-world consequences.
Table: Rib Design Guidelines
Design Aspect | Guideline |
---|---|
Rib Thickness | Less than 50% of the adjacent wall thickness |
Rib Height | Generally up to three times the wall thickness |
Draft Angle | Include a minimum draft angle for easy release |
Influence on Part Thickness
Ribs are often my go-to solution for when I need to reduce wall thickness without losing strength. They’re like those reinforcements in bridges that you don’t really see, but you know they’re doing their job. However, they need to be designed with care to avoid visible warping or uneven cooling patterns. A comprehensive analysis15 is my trusty companion in finding optimal rib design practices.
Understanding these elements has been crucial in helping me enhance both the functional and aesthetic aspects of molded parts. It’s all about ensuring the final product not only meets specifications but also delights the end users. In fields like consumer electronics, where both form and function are paramount, getting this balance right is key.
Rib thickness should be less than 60% of wall thickness.True
This guideline helps minimize sink marks and maintain structural integrity.
Excessive rib complexity always enhances visual appeal.False
Too much complexity can clutter the design, reducing aesthetic value.
Conclusion
The ideal rib-to-wall ratio in injection molding is within 0.5 times the wall thickness, crucial for minimizing defects and ensuring structural integrity in plastic components.
-
Explore common defects like warping and sink marks linked to rib-to-wall ratios in injection molding. ↩
-
Learn about simulation techniques that predict defects and optimize rib designs in injection molding. ↩
-
Discover why ABS is favored in rib design for its balance of strength and weight. ↩
-
Discover why ABS is favored in rib design for its balance of strength and weight. ↩
-
Learn why sink marks occur and how to prevent them in molded parts. ↩
-
Understand the impact of rib placement on material distribution in molds. ↩
-
Explore factors leading to uneven shrinkage and strategies to mitigate it. ↩
-
This link provides insights into how different materials impact rib design choices and their effectiveness. ↩
-
Explore how optimized ribbing enhances performance and efficiency in automotive engineering. ↩
-
Discover leading CAD software options tailored for detailed rib design to improve precision and efficiency in your projects. ↩
-
Access comprehensive PDF guides on rib design to gain insights into industry standards and best practices. ↩
-
Explore various tools and resources that can help optimize rib design for enhanced performance and cost-efficiency. ↩
-
Learn techniques to reduce sink marks, enhancing surface quality and aesthetics. ↩
-
Explore top CAD tools that assist in visualizing and optimizing rib designs. ↩
-
Discover strategies for designing ribs that maintain strength without aesthetic compromise. ↩