Ever stood in front of your project, wondering which mold material can handle the heat without cracking under pressure?
Ideal materials for high-temperature injection molding include H13 and HMAX die steels, stainless steel, hard alloy, and Ultracur3D® RG3280, offering excellent heat resistance, strength, and durability under extreme conditions.
I remember the first time I had to choose a mold material for a project under tight deadlines. It felt like staring at a vast menu with no idea what to order. Knowing the basics of these materials is crucial, but understanding their specific applications can make all the difference. Let’s dive into each one, so you can confidently pick the best fit for your molding projects.
H13 steel is ideal for high-temp injection molding.True
H13 steel offers excellent heat resistance and durability.
Ultracur3D® RG3280 lacks heat resistance for molding.False
Ultracur3D® RG3280 is known for its heat resistance.
- 1. What Makes H13 Hot-Working Die Steel Stand Out?
- 2. How Does Stainless Steel Perform Under High-Temperature Conditions?
- 3. Why Are Hard Alloys Considered for High-Performance Molding?
- 4. What Makes Special High Temperature Materials Stand Out?
- 5. How to Choose the Right Mold Material for Your Specific Application?
- 6. Conclusion
What Makes H13 Hot-Working Die Steel Stand Out?
Imagine working with a material that stands strong under pressure and heat, like a trusted ally in the workshop. That’s H13 steel for you.
H13 hot-working die steel excels due to its superior wear resistance, high-temperature strength, and robustness, ideal for precision molds and die-casting. It effectively manages high pressure and thermal stress, making it a reliable choice for demanding applications.
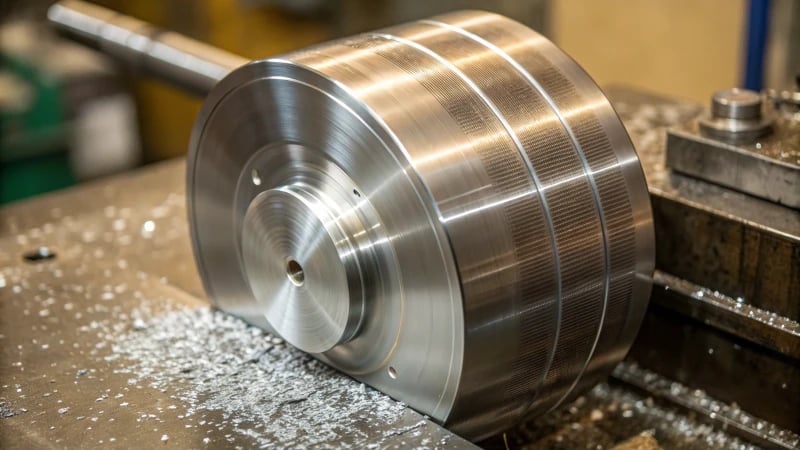
Getting to Know H13 Hot-Working Die Steel
Let me take you on a journey through the world of H13 steel—a staple in the manufacturing industry1. Picture yourself in my shoes, designing high-precision plastic and die-casting molds, where every detail matters. The ability of H13 to maintain its strength and toughness at high temperatures is like having a steadfast partner that never lets you down.
Key Characteristics:
- Wear Resistance: Imagine repeatedly handling stress without a scratch. That’s what H13 offers, enduring the relentless demands of injection molding.
- High-Temperature Strength: It’s like a superhero cape, keeping its form under extreme heat, promising durability and reliability.
- Toughness: Think of it as the steel that won’t buckle under pressure, perfect for those high-stakes industrial settings.
How Does It Compare with Other Mold Materials?
Material | Key Properties | Ideal Use |
---|---|---|
H13 Steel | Wear & Temperature Resistant | High-precision molds |
Stainless Steel | Corrosion & Temperature Resistant | Food & medical molds |
Hard Alloy | High Hardness & Wear Resistance | Precision injection molds |
The HMAX series, particularly HMAX-4, provides medium-carbon ultra-high strength with air-cooled hardening. It’s my go-to when performance needs to be at its peak in extreme mold scenarios2.
Diving into Application Insights
When I’m crafting automotive parts or electronic housings, H13 is my go-to. Its resilience against thermal stress and pressure is like having peace of mind that it won’t fail me when it matters most. This reliability makes it an essential material3 for designers like me, who are always pushing the limits in large-scale production.
What’s Next in Mold Materials?
The future is exciting with materials like Ultracur3D® RG3280 resin, which are paving the way towards innovative composites with remarkable heat resistance and speedy manufacturing capabilities. They’re increasingly significant for anyone aiming to cut down production times4 without compromising quality—something I’m always striving for.
H13 steel is corrosion resistant.False
H13 is known for wear resistance and high-temperature strength, not corrosion.
H13 steel can withstand high-pressure conditions.True
H13's toughness allows it to endure high-pressure without deforming.
How Does Stainless Steel Perform Under High-Temperature Conditions?
Ever wondered if stainless steel can stand the heat? Let’s dive into its fiery capabilities and see how it holds up when things get scorching hot!
Stainless steel excels in high-temperature conditions due to its oxidation resistance and structural integrity. Different grades have varying temperature limits and applications, underscoring the importance of selecting the appropriate grade for optimal performance.

Properties of Stainless Steel at High Temperatures
In my years of designing molds, I’ve learned that choosing the right material is like picking the right partner; it needs to handle the pressure, keep its cool, and stay reliable through thick and thin. Stainless steel5 often fits this role perfectly in high-temperature environments due to its remarkable ability to resist both heat and corrosion. Imagine working in a kitchen where all your tools withstand the sizzle without breaking a sweat—that’s stainless steel for you!
Oxidation Resistance
One memorable project involved creating components for a chemical plant. The key challenge? Ensuring longevity despite constant high heat exposure. Stainless steel’s oxidation resistance was a game-changer, preserving the surface finish and preventing scale formation that could otherwise shorten the lifespan of materials.
High-Temperature Grades
-
Austenitic Stainless Steels
- Grades like 304 and 316 often became my go-to for their solid high-temp strength and resistance to rust. Whether crafting food-grade containers or chemical processing gear, these materials felt like trusty friends who could always be counted on.
- They usually manage temperatures up to 870°C (1600°F).
-
Ferritic Stainless Steels
- Known for their excellent oxidation resistance, I found them perfect for automotive exhaust systems and industrial furnaces—areas where you need steadfast endurance.
- These steels comfortably handle temperatures up to 750°C (1382°F).
-
Martensitic Stainless Steels
- When working on turbine blades or high-strength shafts, I appreciated their moderate corrosion resistance paired with enhanced heat resilience.
- They typically max out around 650°C (1202°F).
Applications in High-Temperature Environments
Stainless steel’s versatility in high-temperature scenarios spans several industries, proving invaluable in many projects over the years:
Industry | Application |
---|---|
Power Generation | Heat exchangers, boiler tubes |
Aerospace | Jet engine components |
Automotive | Exhaust systems |
Chemical Processing | Reactors, heat-resistant conveyors |
The trick lies in matching the right grade with the specific conditions it will face, just like finding the right tool for a particular task.
Challenges at Elevated Temperatures
Though stainless steel excels in many ways, I’ve encountered a few hurdles along the way. Prolonged heat exposure can lead to issues like carbide precipitation—resulting in corrosion resistance loss—and phase changes that may cause embrittlement. I’ve learned that using grades with stabilizing elements such as titanium or niobium can mitigate these risks.
Comparing with Other Materials
When comparing mold materials for high-temperature injection molding, stainless steel frequently rivals other options like:
- Hot-working Die Steel (e.g., H13)
- Hard Alloys
- Special High-Temperature Materials
Each has its perks. While stainless steel6 stands out for corrosion resistance, alternatives like hot-working die steel might offer superior wear resistance or thermal conductivity. I found that weighing these factors according to specific project needs was crucial for success.
Austenitic stainless steels withstand up to 870°C.True
Grades like 304 and 316 can handle temperatures up to 870°C.
Martensitic steels are used in food-grade containers.False
Martensitic steels are used in turbine blades, not food containers.
Why Are Hard Alloys Considered for High-Performance Molding?
Ever wondered why some molds last longer and perform better under pressure? The secret lies in the materials they’re made from.
Hard alloys are ideal for high-performance molding due to their wear resistance and toughness, enhancing mold lifespan and precision, crucial for aerospace and electronics.
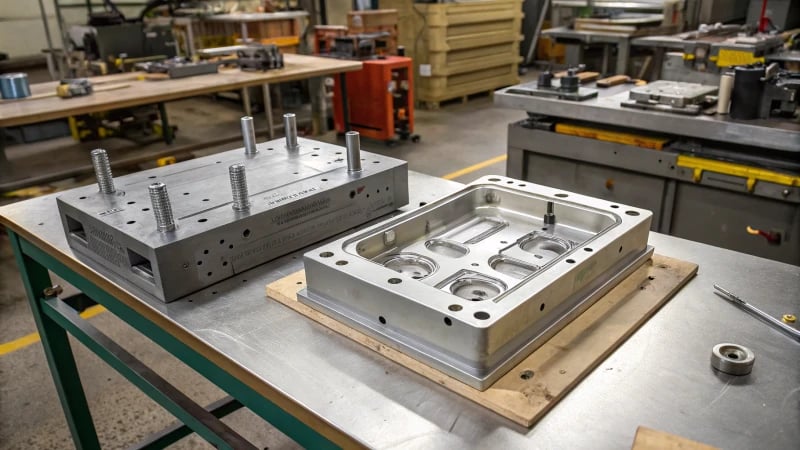
I remember the first time I came across hard alloys in my mold design work. It was like finding a hidden gem in the world of materials. Hard alloys, with their mix of metals like tungsten and cobalt, are a powerhouse when it comes to durability and precision. I’ve found their wear resistance invaluable, especially in high-temperature conditions where maintaining precision is non-negotiable.
Superior Material Properties
Hard alloys, comprising metals like tungsten and cobalt mixed with binders, exhibit unparalleled wear resistance7 and hardness. These properties ensure longevity and precision in molds, especially under high-temperature conditions. This makes them ideal for precision injection8 molds used in demanding industries such as aerospace.
Property | Benefit |
---|---|
Wear Resistance | Extends mold life |
High Hardness | Maintains precision |
Toughness | Withstands stress |
Imagine crafting molds that withstand the test of time and temperature. Hard alloys do just that. They ensure that, even in challenging environments, the molds remain as precise as they were on day one. This is crucial for industries like aerospace, where every detail matters.
Applications in High-Performance Molding
In my experience, the aerospace sector relies heavily on these materials because every component’s precision can’t be compromised. They ensure that molds retain their shape and efficiency, even under repeated thermal cycles. The electronics industry9 also leverages these alloys for creating intricate components that require exact specifications to function correctly.
Cost versus Performance
Initially, investing in hard alloys might seem steep, but from what I’ve seen, the payoff is substantial. The long-term benefits10 often justify the cost. Their durability leads to fewer replacements and lower maintenance costs over time, proving to be a savvy investment.
Alternative Materials for Comparison
When considering alternatives like H13 steel or stainless steel, I’ve noticed they offer certain perks but lack the extreme hardness of hard alloys. For instance, stainless steel11 is great for resisting corrosion but doesn’t quite match the wear resistance needed for some high-performance applications.
By embracing hard alloys in high-performance molding processes, I’ve witnessed significant improvements in efficiency and product reliability. This is particularly evident when molds face high-stress environments, ensuring consistency and quality throughout production cycles.
Jacky, a fellow designer from Canada, would appreciate how these insights align with optimizing large-scale production without skimping on quality or performance. It’s all about making informed decisions that balance cost with long-term benefits.
Hard alloys are ideal for aerospace molds.True
Their wear resistance and hardness ensure precision under thermal cycles.
Stainless steel matches the hardness of hard alloys.False
Stainless steel is less hard, focusing on corrosion resistance over wear resistance.
What Makes Special High Temperature Materials Stand Out?
Ever wondered why some materials can withstand the blistering heat of industrial applications without breaking a sweat?
Special high temperature materials like H13 steel and hard alloys stand out for their ability to retain shape, strength, resist wear and corrosion, and withstand intense heat, making them essential in industrial applications.
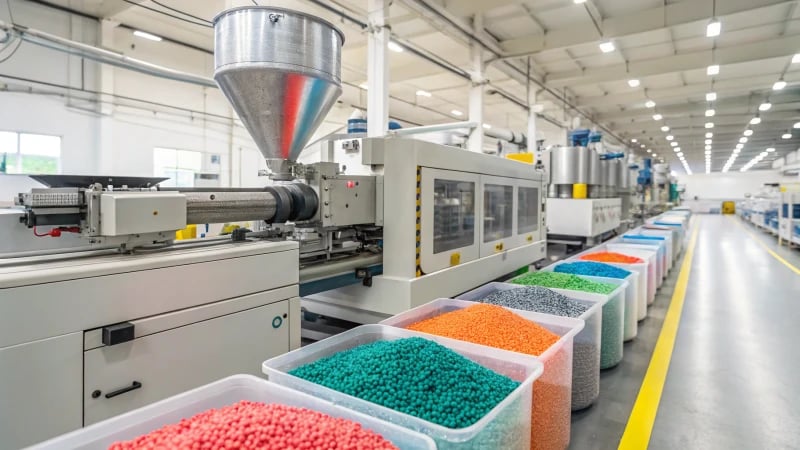
Exceptional Thermal Stability
I remember the first time I encountered H13 steel during a project that involved die-casting molds. I was amazed at how it retained its form even when subjected to intense heat. This material is like the unsung hero in manufacturing, quietly ensuring that molds maintain their consistency in shape and strength under high temperatures. Special high temperature materials, like H13 steel, are renowned for their ability to maintain structural integrity12 even at elevated temperatures.
Superior Wear Resistance
Have you ever watched a blacksmith at work, repeatedly hammering metal into shape? That’s the kind of wear resistance the HMAX series offers. These materials are like the heavy lifters of the industrial world, built to withstand the repeated stress of hot forging or extrusion. Exploring more about these materials reveals why they’re indispensable in high-demand industries. Materials such as the HMAX series offer exceptional wear resistance. This property is crucial in scenarios involving repeated mechanical stress, such as hot forging or extrusion.
Material | Application | Properties |
---|---|---|
H13 Steel | Die-casting, Plastic molds | Good wear resistance, High temperature strength |
HMAX Series | Hot forging, Extrusion | High thermal strength, Red hardness |
Stainless Steel | Injection molds, Rubber molds | Corrosion resistance, High temperature stability |
Corrosion Resistance
I’ve always been fascinated by how stainless steel can weather harsh environments without a hint of rust. It’s often my go-to choice when I need both heat and corrosion resistance, especially in fields like food and medical manufacturing where hygiene is non-negotiable. Stainless steel is frequently utilized in environments that demand both high temperature and corrosion resistance. In fields such as food and medical13 manufacturing, this dual capability is invaluable.
Advanced Compositions and Applications
Then there’s Ultracur3D® RG3280, a ceramic filled resin with incredible stiffness and heat resistance. Imagine being able to print 3D molds that can handle temperatures over 280℃! This material is a game-changer for rapid prototyping, slashing production time and cost while meeting high standards for strength and heat deformation. Its ability to withstand temperatures over 280℃ makes it stand out in rapid prototyping.
Lastly, let’s talk about hard alloy. Formed by mixing metal powders like tungsten and cobalt, this material is a powerhouse of toughness at high temperatures. It’s essential for precision injection molds in sectors like aerospace and electronics—areas where every detail counts. Choosing the right material isn’t just about meeting current needs; it’s about anticipating future demands and ensuring longevity and efficiency in mold performance.
Understanding these properties allows engineers like me to select materials that not only meet but exceed performance expectations in challenging environments.
H13 steel maintains integrity at high temperatures.True
H13 steel is known for its structural integrity at elevated temperatures.
Ultracur3D® RG3280 withstands temperatures over 300℃.False
Ultracur3D® RG3280 withstands temperatures over 280℃, not 300℃.
How to Choose the Right Mold Material for Your Specific Application?
Ever found yourself puzzling over which mold material to pick for a project? It’s a choice that can make or break your product’s success.
Choose mold material based on application needs like temperature, corrosion, and wear resistance. Options include die steels, stainless steel, alloys, and resins, optimizing durability and cost efficiency.
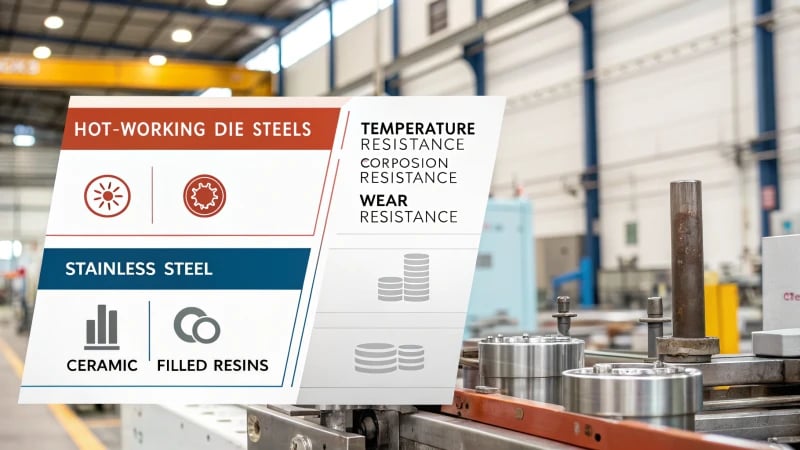
Evaluating Application Requirements
When selecting a mold material, first consider the specific requirements of your application. For instance, if your process involves high-temperature injection molding14, materials like H13 steel or the HMAX series are ideal due to their exceptional thermal stability and wear resistance.
Material | Characteristics | Applications |
---|---|---|
H13 Steel | High temperature & wear resistance | Automotive parts, electronic product housings |
HMAX Series | Ultra-high strength, air-cooled hardening | Copper alloy die casting, hot forging |
Corrosion Resistance Needs
In industries such as food, medical, or chemicals where corrosion is a concern, stainless steel15 is an excellent choice. Its durability in corrosive environments makes it suitable for molds in these demanding sectors.
Wear Resistance and Durability
For applications requiring high wear resistance and hardness, consider using hard alloys. These materials are costly but provide unmatched durability and performance, especially in aerospace or high-end electronics.
Specialized High-Temperature Solutions
If rapid turnover and specific mold characteristics are necessary, Ultracur3D® RG3280, a ceramic-filled resin, offers high stiffness and heat resistance, making it suitable for quick manufacturing cycles.
Cost vs. Performance Considerations
Finally, balancing cost with performance is crucial. While hard alloy materials16 offer superior durability, they come at a higher price. Consider your production volume and budget constraints to make an informed choice.
By understanding these factors and aligning them with your application’s demands, you can select the most suitable mold material that meets both technical and economic requirements efficiently. Explore further resources to deepen your knowledge on this topic and refine your decision-making process in mold material selection.
H13 steel is ideal for high-temperature applications.True
H13 steel offers exceptional thermal stability and wear resistance.
Stainless steel is unsuitable for corrosive environments.False
Stainless steel is highly durable in corrosive environments.
Conclusion
High-temperature injection molding requires materials like H13 steel, HMAX series, stainless steel, hard alloys, and Ultracur3D® RG3280 for durability, wear resistance, and thermal stability in demanding applications.
-
Gain insights into various applications of H13 steel in the manufacturing industry. ↩
-
Understand the properties that distinguish the HMAX series from other die steels. ↩
-
Discover why H13 is critical in the production of high-demand molds. ↩
-
Explore how new materials are transforming mold manufacturing processes. ↩
-
This link delves into the intrinsic properties of stainless steel that contribute to its high-temperature performance, offering valuable insights. ↩
-
This comparison highlights the advantages and drawbacks of using stainless steel versus other high-temperature mold materials. ↩
-
Explore how hard alloys’ wear resistance extends mold life and enhances production efficiency. ↩
-
Learn why precision is critical in aerospace applications and how hard alloys contribute. ↩
-
Understand how hard alloys support complex designs in the electronics sector. ↩
-
Discover how investing in hard alloys can reduce long-term costs despite high upfront expenses. ↩
-
Compare stainless steel with hard alloys to identify suitable applications for each material. ↩
-
Discover how these materials maintain their shape under extreme heat conditions. ↩
-
Explore the dual benefits of stainless steel in resistant environments. ↩
-
Explore high-temperature injection molding to understand material requirements for thermal stability and wear resistance. ↩
-
Learn why stainless steel is preferred in environments requiring corrosion resistance. ↩
-
Discover the benefits of using hard alloy materials for enhanced durability and performance. ↩