In the fast-paced world of manufacturing, perfection is the goal, but imperfections like knit lines can throw a wrench in your plans. Known as weld lines or flow lines, knit lines1 are those pesky visible seams that appear on injection-molded parts where two streams of molten plastic meet but don’t fully bond. These lines aren’t just cosmetic flaws—they can weaken your parts, especially in complex designs with holes, multiple gates, or tricky geometries. The good news? With smart strategies, you can minimize or even eliminate knit lines. Let’s dive into what knit lines are, why they happen, and how to keep them at bay with design tweaks, material choices, and process adjustments.
Knit lines can significantly reduce the strength of injection-molded parts.True
Studies show that knit lines can cut tensile strength by up to 50%, particularly in critical load-bearing areas.
- 1. What are Knit Lines in Injection Molding?
- 2. What Causes Knit Lines?
- 3. How to Prevent Knit Lines?
- 4. What are the Best Practices for Material Selection?
- 5. How to Adjust Process Parameters to Minimize Knit Lines?
- 6. What Design Strategies Help Avoid Knit Lines?
- 7. Are There Advanced Techniques to Eliminate Knit Lines?
- 8. Conclusion
What are Knit Lines in Injection Molding?
Knit lines form when two or more flow fronts of molten plastic converge in the mold cavity but fail to fuse completely. This leaves a visible seam on the part’s surface, which can compromise both its look and strength. You’ll often see them in parts with features that split the plastic flow—like holes, bosses, or multiple gates—making them a common headache in intricate designs.
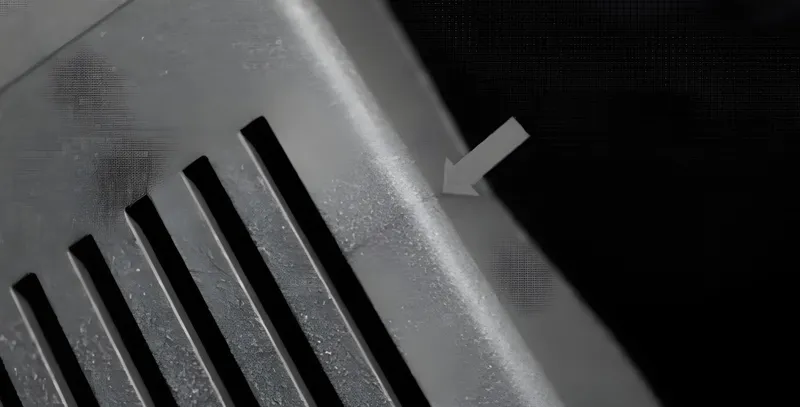
What Causes Knit Lines?
Knit lines don’t just appear out of nowhere. Here’s what sets the stage for them:
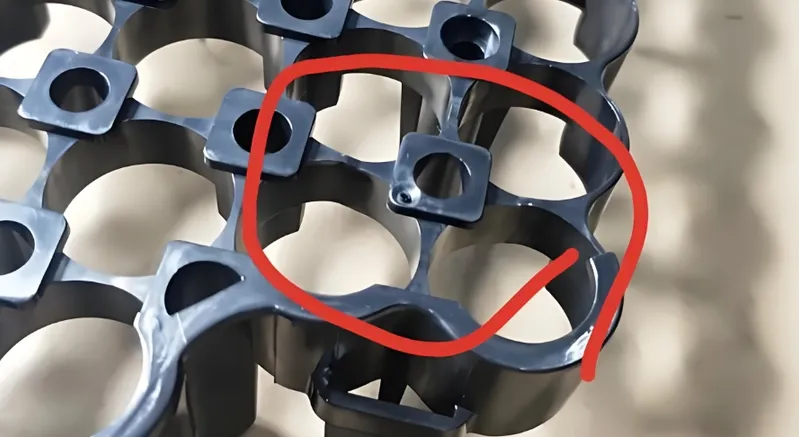
-
Multiple Gates2: When a mold has more than one entry point, plastic flows from each gate can collide, creating knit lines.
-
Obstacles in the Mold: Holes, inserts, or cores split the flow, forcing it to reconnect and form seams.
-
Low Injection Pressure or Speed3: If the plastic isn’t injected fast or hard enough, the flow fronts cool too soon to bond properly.
-
Low Mold or Material Temperature: Cooler conditions cause the plastic to solidify before it can fuse.
-
Poor Material Flow Properties: Some plastics, due to high viscosity or fast cooling, are more knit-line-prone.
Cause | Description |
---|---|
Multiple Gates | Flows from different gates meet, forming knit lines. |
Obstacles (holes, inserts) | Features split the flow, leading to reconvergence and seams. |
Low Injection Pressure/Speed | Slow or weak injection causes premature cooling. |
Low Temperatures | Cold mold or material solidifies too early. |
Material Properties4 | Poor flow or fast cooling increases knit line risk. |
How to Prevent Knit Lines?
Preventing knit lines takes a team effort—design, process, and materials all play a role. Here’s how to tackle them:
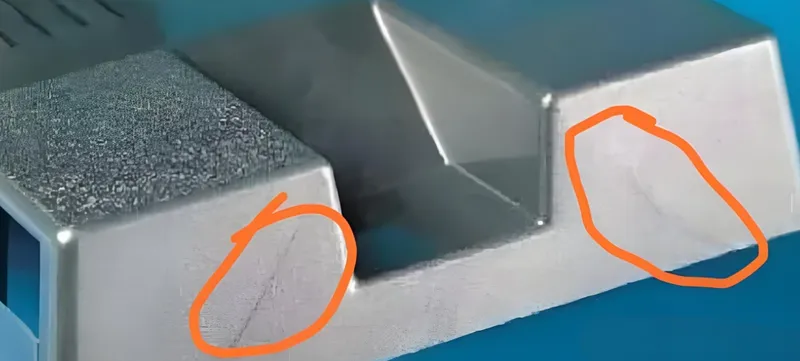
Optimize Part Design
-
Gate Placement: Position gates to steer flow away from critical areas or ensure seams form in less noticeable spots.
-
Wall Thickness: Keep it uniform to avoid flow disruptions from uneven cooling.
-
Feature Relocation: Shift holes or bosses to areas where knit lines won’t hurt strength or looks.
Adjust Process Parameters
-
Injection Speed5: Crank it up so flow fronts meet while still hot and fluid.
-
Injection Pressure: Boost pressure to force better fusion at the seam.
-
Temperature Control: Raise mold and material temps to delay cooling and enhance bonding.
Choose Appropriate Materials
- Pick plastics with good flow, like polypropylene, which hides knit lines better than ABS.
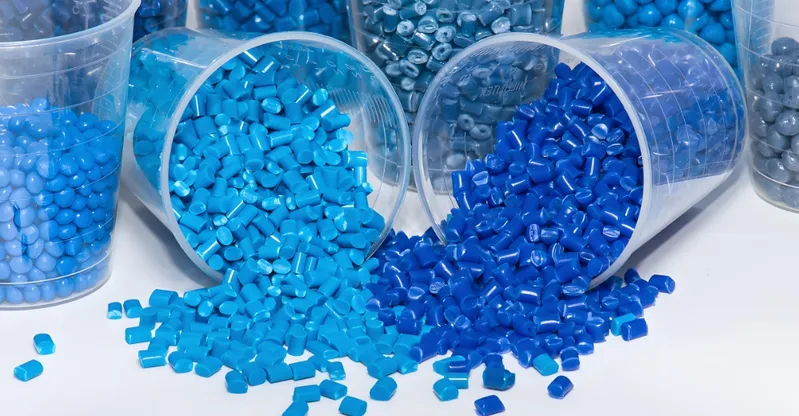
- Steer clear of additives that mess with flow or fusion.
Use Simulation Software
- Tools like Moldflow predict flow patterns, letting you tweak design or settings before molding starts.
Employ Advanced Techniques
-
Hot Runner Systems: Keep plastic hot and flowing consistently.
-
Valve Gates: Control flow timing to minimize seam formation.
Increasing injection speed can completely eliminate knit lines.False
Higher speed helps, but it won’t wipe out knit lines entirely, especially in complex parts with multiple flows.
What are the Best Practices for Material Selection?
Your material choice can make or break knit line prevention:
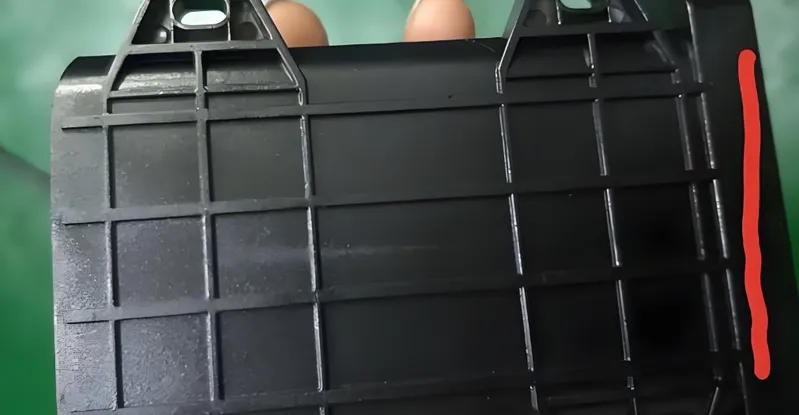
-
Unfilled Materials6: Flow better and fuse stronger (e.g., polypropylene).
-
Filled Materials: Fibers (like in glass-filled ABS) can weaken knit lines by disrupting fusion.
-
Additives: Flame retardants or lubricants might worsen seams by altering flow.
Material Type | Impact on Knit Lines | Example |
---|---|---|
Unfilled Thermoplastics | Stronger knit lines, better fusion | Polypropylene (PP) |
Filled with Short Fibers | Decent bonding, less weak than long fibers | Glass bead-filled PP |
Filled with Long Fibers | Weaker knit lines due to fiber misalignment | Glass fiber-filled ABS |
Additives (e.g., FR) | Can worsen knit lines | Flame-retardant ABS |
Polypropylene is less prone to knit lines than ABS.True
Thanks to its superior flow and slower cooling, polypropylene forms less visible knit lines.
How to Adjust Process Parameters to Minimize Knit Lines?
Tweaking your molding process can work wonders:
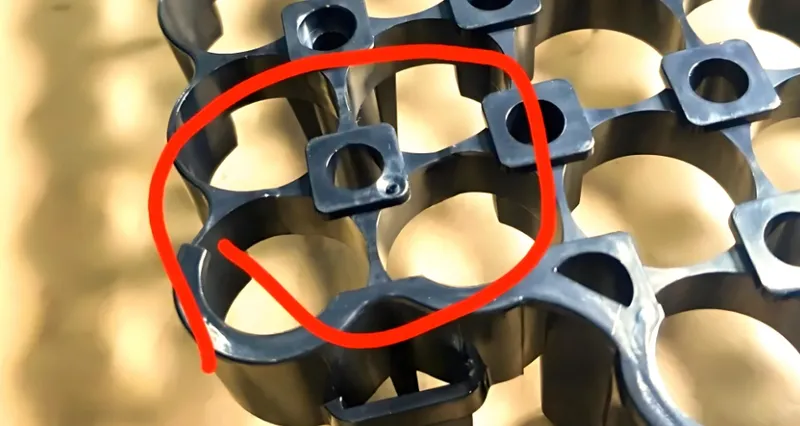
-
Injection Speed and Pressure: Higher values ensure flow fronts collide with enough heat and force to bond.
-
Mold Temperature7: Warmer molds slow cooling, giving plastic more time to fuse.
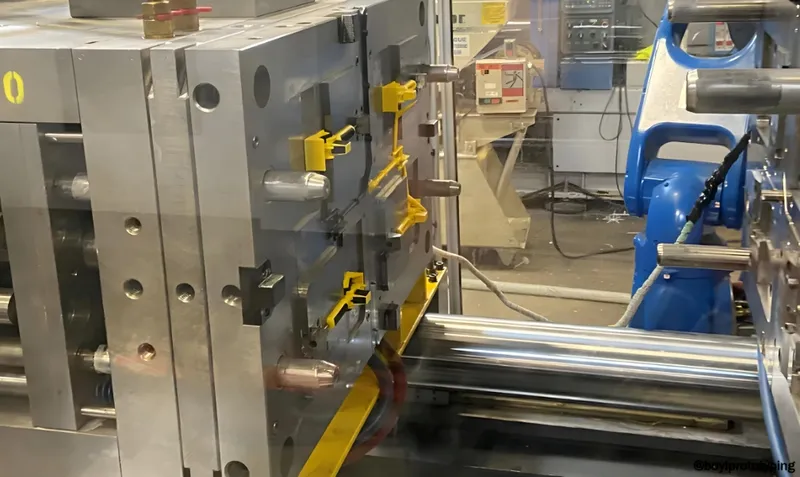
- Material Temperature: Hotter plastic stays molten longer, improving seam strength.
Parameter | Effect on Knit Lines | Recommended Action |
---|---|---|
Injection Speed | Faster speed improves fusion | Increase for better melding |
Injection Pressure8 | More pressure aids flow front bonding | Adjust to avoid overpacking |
Mold Temperature | Warmer molds delay cooling | Raise to enhance fusion |
Material Temperature | Hotter plastic flows better | Increase to keep it molten longer |
What Design Strategies Help Avoid Knit Lines?
Design smarter to sidestep knit lines:
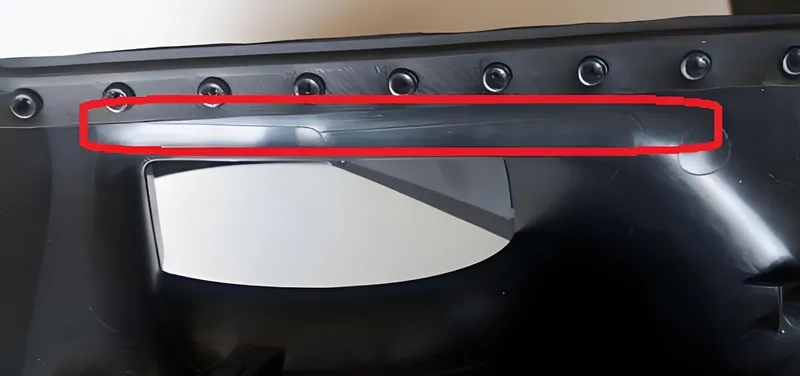
-
Minimize Gates: Fewer gates mean fewer flow collisions.
-
Gate Placement: Put gates where flows meet in non-critical zones.
-
Uniform Wall Thickness: Prevents fast-cooling thin spots that disrupt flow.
-
Smooth Transitions: Radii over sharp corners keep flow steady.
-
Relocate Features: Move flow-splitting elements like holes away from key areas.
Design Checklist:
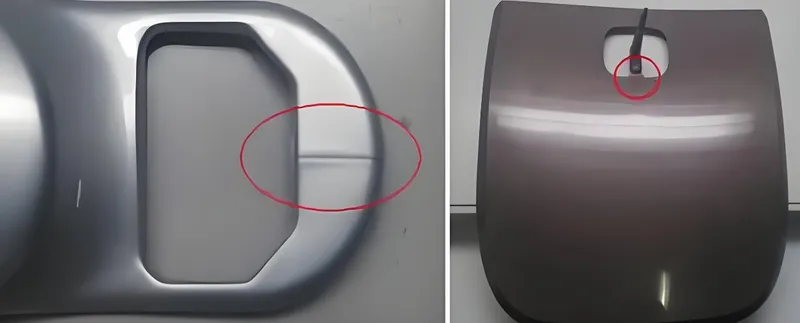
-
Use the fewest gates possible.
-
Maintain uniform wall thickness.
-
Add radii to avoid sharp corners.
-
Optimize gate locations.
-
Shift features causing flow splits.
Are There Advanced Techniques to Eliminate Knit Lines?
For tough cases, high-tech solutions shine:
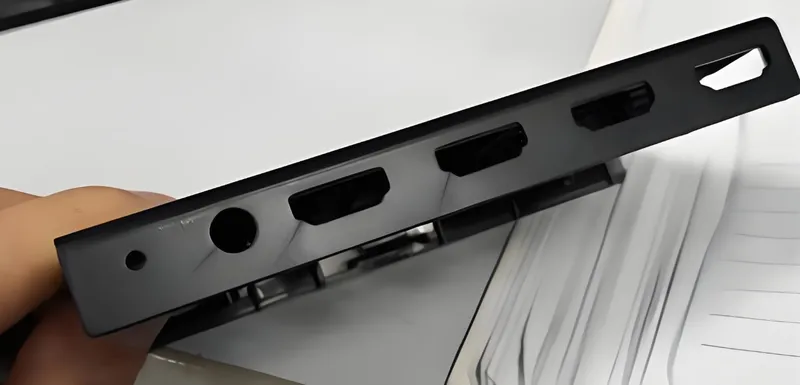
-
Simulation Software9: Autodesk Moldflow maps flow to fine-tune designs and settings.
-
Hot Runner Systems10: Keep plastic hot, reducing cooling-related seams.
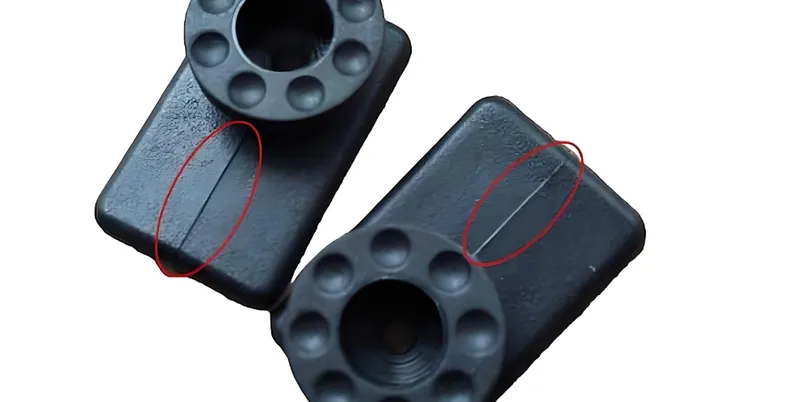
- Valve Gates11: Time the flow for seamless filling.
These tools cost more but pay off in precision parts.
Conclusion
Knit lines might be a thorn in your side, but they’re not unbeatable. By blending sharp design, savvy material picks, dialed-in process tweaks, and cutting-edge tech, you can slash their impact—or banish them entirely. It’s not always possible to erase every trace in complex parts, but these best practices will get you close, delivering stronger, better-looking products that stand up to scrutiny.
Simulation software is essential for preventing knit lines.False
It’s a great tool, but basic design and process fixes can often do the trick without it.
-
Understanding knit lines is crucial for improving product quality in manufacturing. Explore this link to learn effective strategies for minimizing them. ↩
-
Discover how multiple gates can lead to knit lines and learn design strategies to avoid them. This knowledge can enhance your manufacturing process. ↩
-
Explore the effects of injection pressure and speed on knit lines to optimize your injection molding process and improve part quality. ↩
-
Choosing the right materials is key to preventing knit lines. Discover which materials work best for your applications. ↩
-
Learn how adjusting injection speed can enhance fusion and reduce defects in molded parts. This resource provides valuable techniques. ↩
-
Learning about unfilled materials can help you choose the right plastics for better flow and fusion, enhancing your production efficiency. ↩
-
Exploring mold temperature effects can lead to better fusion and stronger products in your manufacturing process. ↩
-
Understanding injection pressure can significantly enhance your molding techniques and improve product quality. ↩
-
Explore how simulation software can enhance your design process and improve product quality. ↩
-
Learn how hot runner systems can optimize your injection molding and reduce defects. ↩
-
Discover the advantages of valve gates for achieving seamless filling in your molds. ↩