Have you ever stopped to think about how the plastic products around you come to life?
Plastic molding engineering involves converting plastic raw materials into products with desired shapes and properties through techniques like injection, extrusion, blow, and compression molding.
To truly grasp the intricacies of this engineering marvel, it’s essential to delve deeper into the processes, materials, and equipment that define plastic molding engineering. Discover how this field impacts various industries and explore its future trends.
Injection molding is ideal for producing hollow plastic products.False
Blow molding, not injection molding, is used for hollow products like bottles.
What Are the Key Steps in Plastic Material Selection?
Choosing the right plastic material is crucial for product performance and durability. This selection process involves understanding the unique properties of various plastics and aligning them with product requirements.
The key steps in plastic material selection include evaluating mechanical properties, processing characteristics, and environmental impact. Consideration of application-specific needs ensures optimal material choice for performance and sustainability.
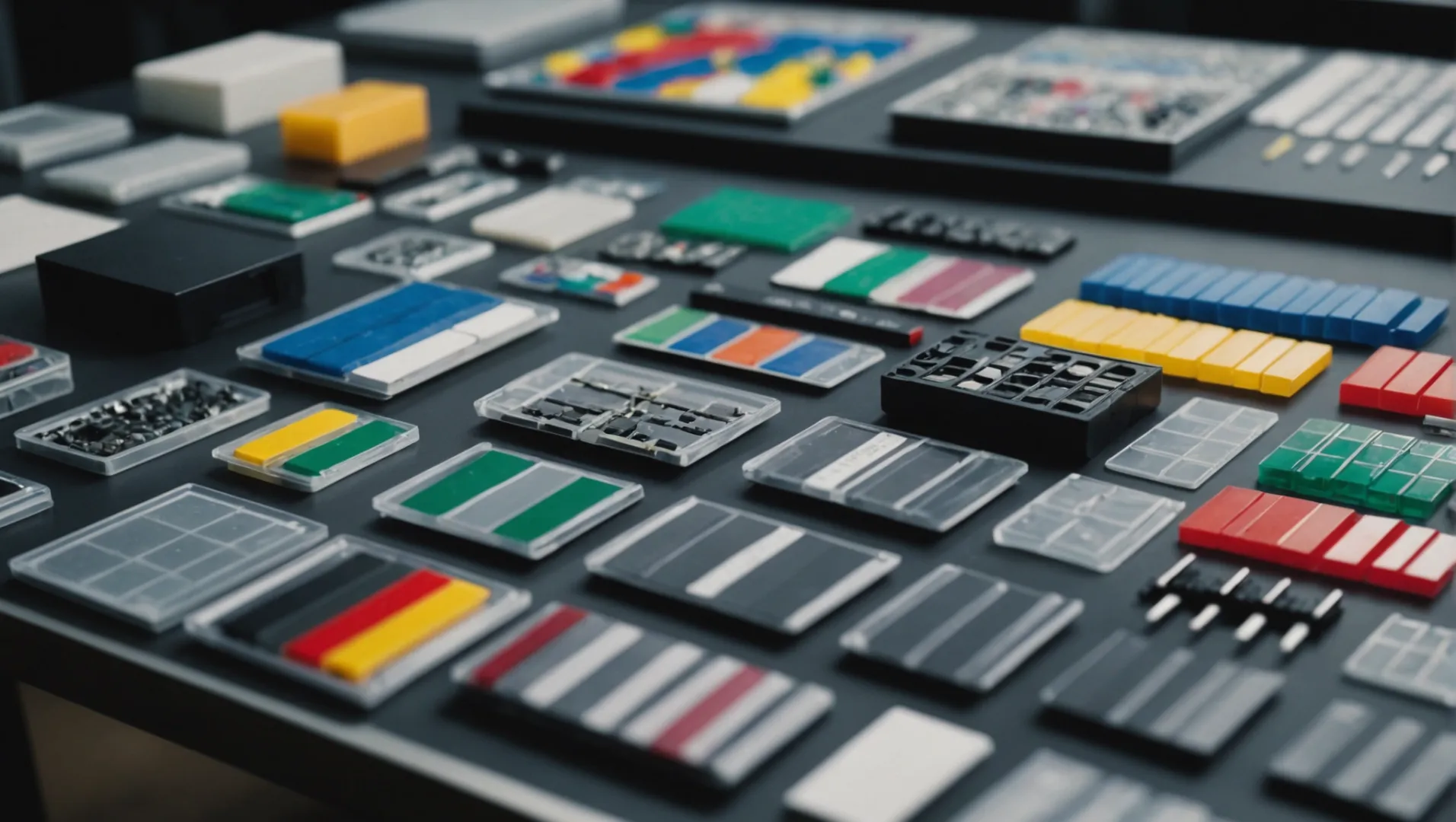
Evaluating Mechanical Properties
When selecting a plastic material, it’s vital to start by evaluating its mechanical properties. Different plastics like polyethylene, polypropylene, polystyrene, and polyvinyl chloride offer varied strengths, heat resistances, and transparencies. For instance, polyethylene is known for its excellent impact resistance, while polyvinyl chloride provides superior durability and resistance to environmental degradation. Choosing the right material ensures the product can withstand the intended stressors and conditions.
Processing Characteristics
Understanding the processing characteristics of a plastic is just as important as its mechanical properties. This includes examining fluidity, shrinkage, and thermal stability. These factors influence the ease of manufacturing and the final quality of the product. For example, a plastic with high shrinkage might not be suitable for precision parts that require tight tolerances. By considering these characteristics, manufacturers can optimize their processes to improve efficiency and product quality.
Environmental Considerations
As environmental concerns grow, the sustainability of plastic materials becomes increasingly important. Opting for biodegradable plastics or those that can be easily recycled can significantly reduce the ecological footprint of a product. Additionally, understanding the lifecycle of the plastic—such as its energy consumption during production and potential for recycling—can guide more environmentally responsible decisions.
Application-Specific Needs
The end-use application of the plastic product plays a decisive role in material selection. For example, products used in high-temperature environments require materials with excellent heat resistance. Similarly, plastics for food packaging need to meet stringent safety standards. Manufacturers must align material characteristics with specific application requirements to ensure functionality and compliance.
By following these steps, manufacturers can ensure they choose the right plastic material for their products, balancing performance, cost, and environmental impact. To learn more about different types of plastics and their applications, check out this detailed guide on plastic properties1.
Polyethylene offers excellent impact resistance.True
Polyethylene is known for its high impact resistance, making it suitable for durable products.
Biodegradable plastics increase the ecological footprint.False
Biodegradable plastics reduce the ecological footprint by breaking down naturally.
How Does Each Molding Process Differ in Technique and Application?
In the realm of plastic manufacturing, various molding techniques cater to different product requirements. Each process offers unique advantages, influencing both the technique and the applications.
Different molding processes like injection, extrusion, blow, and compression molding vary in technique and applications. Injection molding is ideal for intricate designs; extrusion is used for continuous profiles; blow molding creates hollow items, and compression molding is fit for large, thick-walled products.
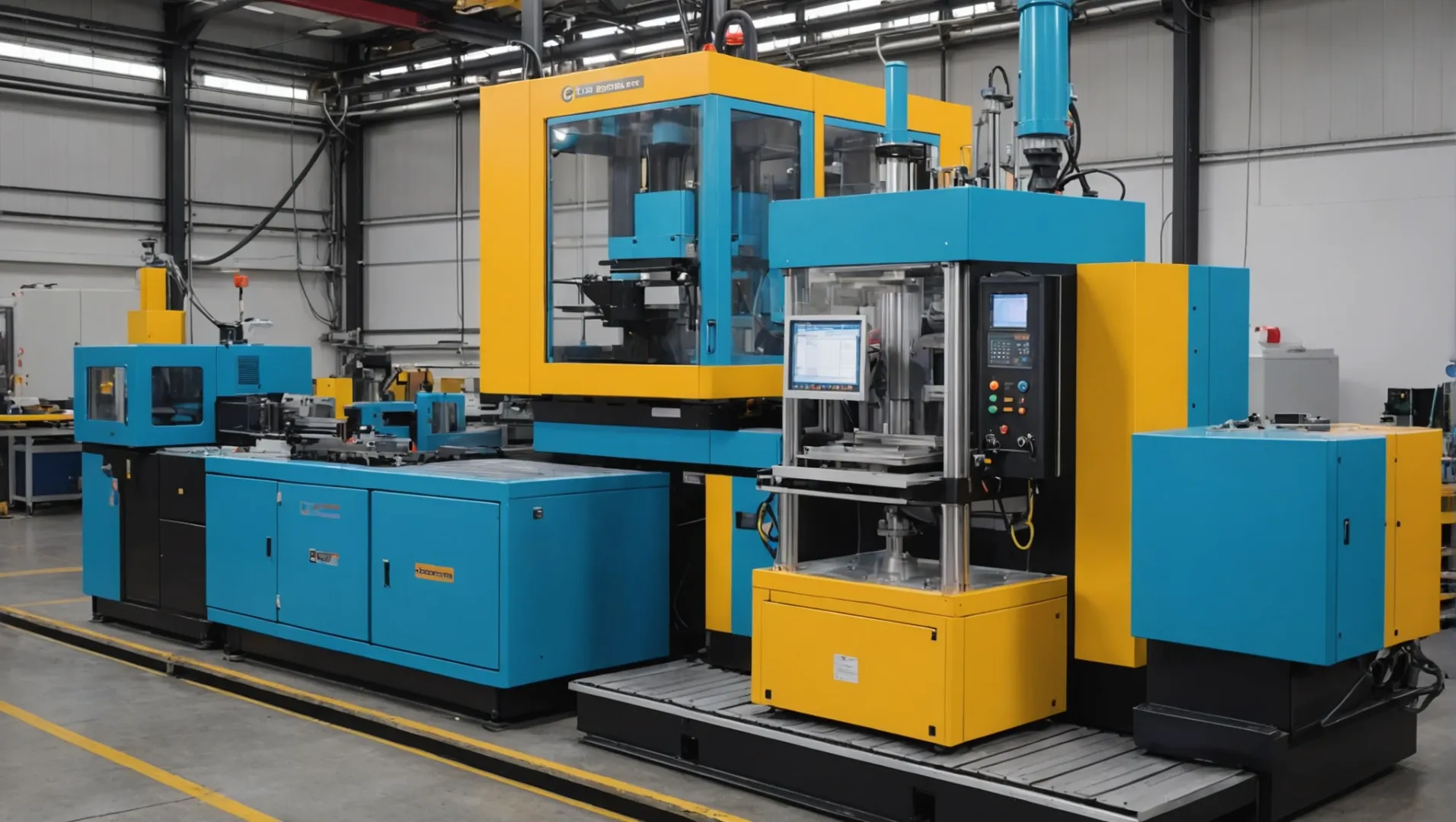
Injection Molding: Precision and Complexity
Injection molding stands out for its ability to produce highly complex and precise plastic components. This process involves injecting molten plastic into a mold cavity, where it cools and solidifies into the desired shape. Injection molding is exceptionally suited for industries like automotive2 and electronics, where accuracy and intricate designs are paramount. Its application ranges from car bumpers to mobile phone cases.
Extrusion Molding: Efficiency and Continuity
Extrusion molding focuses on producing continuous plastic profiles by melting plastic materials and forcing them through a die. This technique is renowned for its efficiency and low cost, making it perfect for creating pipes, sheets, and films. The construction industry benefits significantly from extrusion molding through products like plastic pipes3 and window frames.
Blow Molding: Creating Hollow Products
Blow molding is primarily used for manufacturing hollow plastic products. It begins with heating a plastic parison in a mold, which is then shaped by compressed air. This method is prevalent in the packaging industry for producing items like bottles and barrels. Its application ensures lightweight and durable packaging solutions across various sectors.
Compression Molding: Strength and Thickness
Compression molding involves placing raw plastic material into a heated mold, then applying pressure to shape it. This process excels in creating large, thick-walled products with significant strength. The automotive industry often employs compression molding for components requiring durability, such as engine covers4 and certain structural parts.
Each of these molding processes comes with distinct technical nuances, allowing manufacturers to select the best method based on product specifications, required precision, and cost considerations. As technology advances, these techniques continue to evolve, offering enhanced capabilities across diverse applications.
Injection molding is best for hollow products.False
Injection molding is suited for intricate designs, not hollow items.
Extrusion molding is used for continuous profiles.True
Extrusion molding creates continuous plastic profiles efficiently.
Why Is Mold Design Critical in Plastic Molding Engineering?
In the realm of plastic molding engineering, mold design is not merely a step—it’s the blueprint for success.
Mold design is crucial in plastic molding engineering as it determines the final product’s quality, dimensional accuracy, and production efficiency. By considering factors such as material properties, product shape, and manufacturing constraints, mold design ensures optimal performance and longevity of the mold.
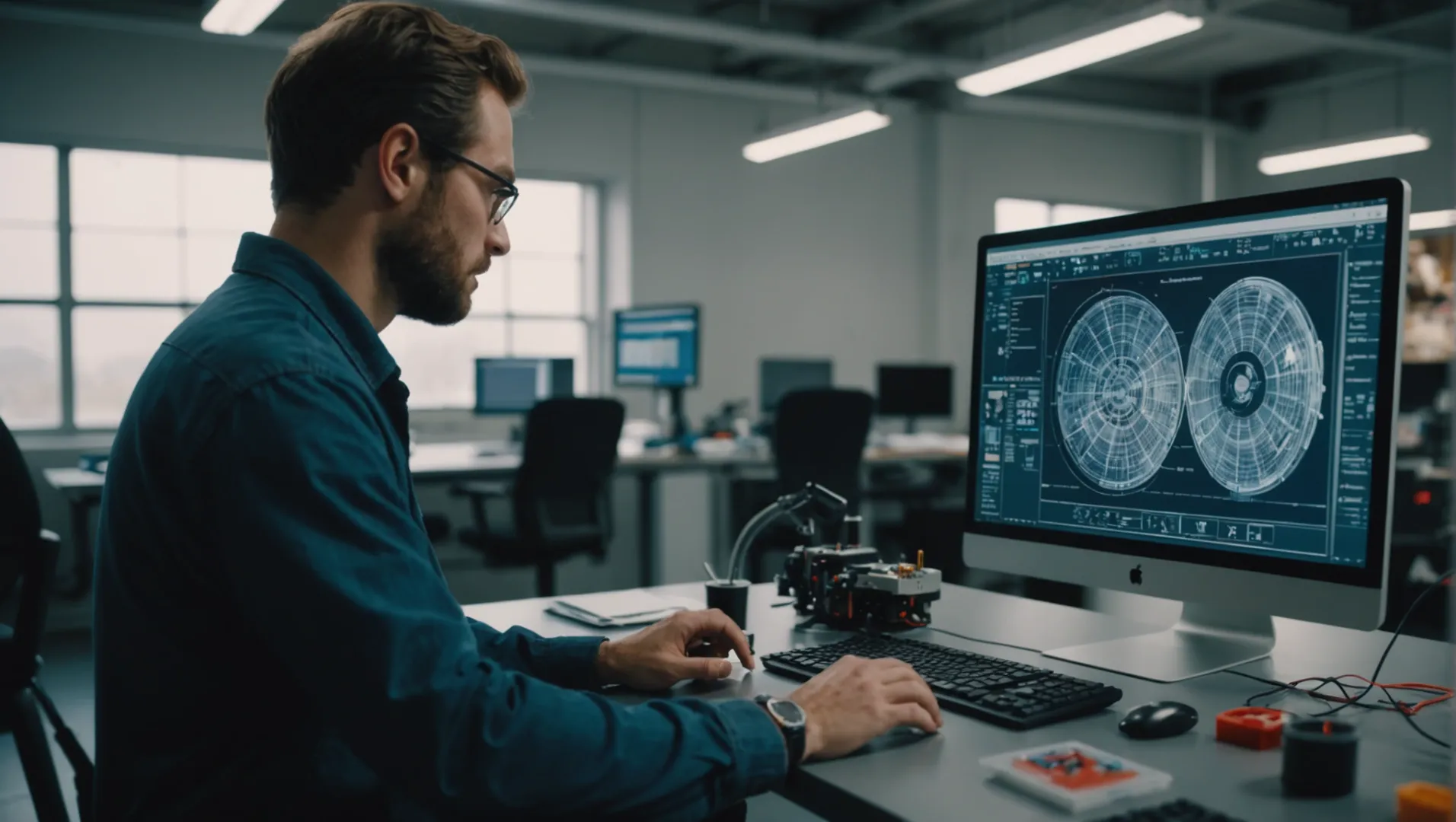
Understanding Mold Design in Plastic Molding
In the complex world of plastic molding engineering5, mold design stands as a pivotal factor influencing both the quality and efficiency of production. The mold essentially acts as a precise cavity that shapes the molten plastic into the desired form, making its design fundamental to achieving the end product’s specifications.
Key Considerations in Mold Design
-
Material Compatibility: Selecting suitable materials for the mold is vital. The chosen materials must withstand high temperatures and pressures during processes like injection molding.
-
Product Specifications: Each mold is custom-designed to meet specific product requirements. This includes considerations of shape, size, and precision.
-
Demolding Process: Efficient demolding is essential to ensure products can be removed without damage, reducing waste and improving cycle times.
Impact on Production Efficiency
A well-designed mold minimizes cycle time by optimizing the cooling process. Rapid cooling not only accelerates production but also maintains dimensional accuracy. Furthermore, molds designed for easy maintenance and adjustment can significantly reduce downtime.
Technological Integration in Mold Design
Recent advancements in technology have further underscored the importance of mold design. Techniques such as CNC machining6 and EDM7 (Electrical Discharge Machining) allow for intricate designs and high precision. Additionally, software tools enable engineers to simulate and test mold designs before physical production, reducing errors and costs.
Challenges and Solutions in Mold Design
Designing a mold that balances all these aspects is challenging. Engineers must predict how different materials behave under stress and how complex geometries affect flow dynamics.
-
Solution Through Simulation: Advanced simulation tools help predict potential issues such as warping or sink marks, allowing adjustments before manufacturing begins.
-
Collaborative Design Process: Engaging cross-functional teams early in the design process can lead to innovative solutions that address multiple challenges simultaneously.
In conclusion, while mold design is just one element of plastic molding engineering, its critical role cannot be overstated. By investing in thoughtful design, manufacturers can ensure quality products and efficient production processes.
Mold design impacts plastic product quality.True
Mold design determines the final product's quality and accuracy.
EDM is irrelevant in mold manufacturing.False
EDM enhances precision, crucial for intricate mold designs.
What Role Does Quality Control Play in Plastic Product Manufacturing?
Quality control is pivotal in ensuring plastic products meet stringent standards, affecting their performance and durability.
In plastic product manufacturing, quality control ensures dimensional accuracy, appearance quality, and physical properties meet industry standards. Advanced testing equipment and methods are employed to detect and rectify quality issues promptly, maintaining product integrity.
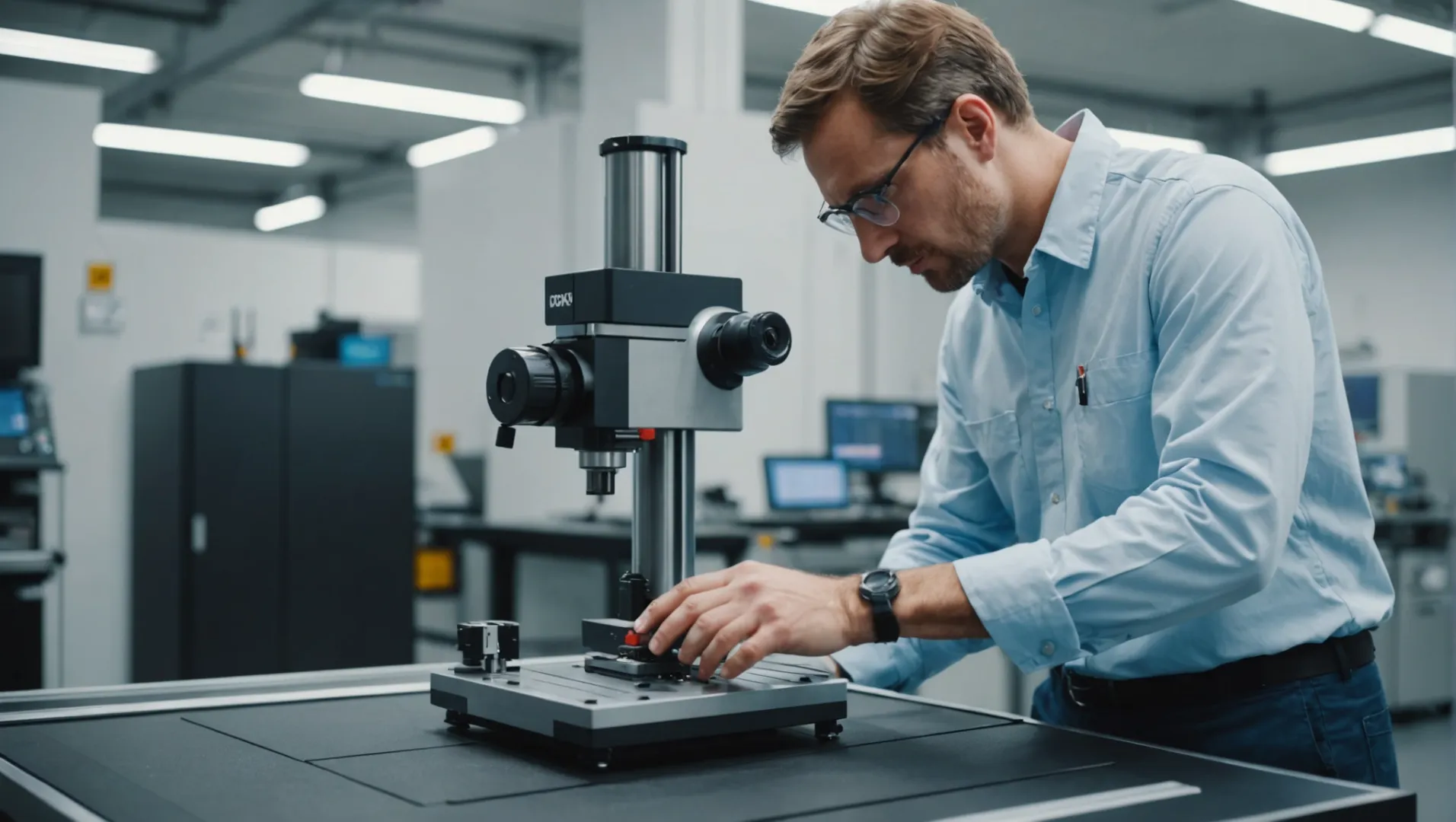
Ensuring Dimensional Accuracy
Dimensional accuracy is a fundamental aspect of quality control in plastic manufacturing. Products must conform to precise measurements to ensure compatibility and functionality. Deviations can lead to assembly issues or product failure. Tools such as coordinate measuring machines and laser scanners are employed to verify dimensions against design specifications.
- Injection Molding Precision: Techniques like injection molding demand high accuracy due to the complexity of shapes produced. Regular checks help maintain this precision.
- Tolerance Levels: Specific tolerance levels are established, beyond which products are rejected or reworked.
Maintaining Appearance Quality
The appearance of plastic products often reflects their quality and impacts consumer perception. Surface defects such as scratches, discoloration, or blemishes can diminish product appeal.
- Visual Inspection: This involves checking for color consistency and surface finish. Automated systems can enhance the speed and accuracy of inspections.
- Advanced Microscopy: Optical microscopes are used to scrutinize surface integrity at a micro level, identifying imperfections not visible to the naked eye.
Evaluating Physical Properties
Physical properties such as strength, flexibility, and resistance to environmental factors are crucial for the intended use of plastic products.
- Mechanical Testing: Methods like tensile testing assess material strength and elasticity. These tests ensure products can withstand intended loads and stressors.
- Environmental Testing: Products are exposed to various conditions to simulate real-world environments, evaluating their durability against elements like UV radiation or moisture.
Implementing Advanced Testing Methods
To uphold quality, advanced testing methods are integrated into the production line. These methods provide data-driven insights that inform quality control decisions.
- Non-Destructive Testing (NDT): Techniques such as X-ray and ultrasound allow for internal inspection without damaging the product. Explore more about NDT techniques8.
- Statistical Process Control (SPC): SPC tools track production metrics in real-time, identifying trends and anomalies that could indicate quality issues. This proactive approach reduces defect rates and enhances efficiency.
Quality control in plastic product manufacturing is not just a final check but a continuous process that begins with raw material selection and extends through every stage of production. By employing rigorous quality control measures, manufacturers can deliver reliable, high-quality plastic products across various industries.
Quality control ensures plastic products meet industry standards.True
Quality control is crucial for meeting dimensional and physical standards.
Non-destructive testing damages plastic products during inspection.False
Non-destructive testing inspects without causing product damage.
Conclusion
Plastic molding engineering is pivotal in modern manufacturing, offering versatile solutions across industries. Its continual evolution towards sustainability and efficiency promises exciting innovations ahead.
-
Explore detailed descriptions of various plastics and their unique properties.: 7 Different Types of Plastic · 1. Acrylic or Polymethyl Methacrylate (PMMA) · 2. Polycarbonate (PC) · 3. Polyethylene (PE) · 4. Polypropylene (PP) · 5. Polyethylene … ↩
-
Explore how injection molding benefits automotive design intricacies.: Automotive injection molding lets designers produce plastic parts for EVs, PHEVs, and cars, trucks, and motorcycles that use ICE engines. ↩
-
Discover extrusion’s role in building sustainable infrastructure.: Extrusion moulding is used to form plastic or metal materials into a pre-defined shape. During the process, the material is melted and pushed through an. ↩
-
Learn about compression molding’s impact on durable auto parts.: Compression molding provides excellent control over part dimensions and tolerances. The process allows for consistent quality and precision in the manufactured … ↩
-
Learn why effective mold design is vital for high-quality plastic products.: Mike Baranoski, a Design Engineer at Rodon, discusses how his role and having a solid design are critical to the plastic injection molding process. ↩
-
Explore how CNC machining revolutionizes precision in mold design.: CNC machining is the leading production style for mold making. Molds are most commonly machined out of tool steel and stainless steel, but aluminum is also … ↩
-
Discover how EDM enhances mold manufacturing precision.: Wire electrical discharge machining (EDM) is widely used by injection mold builders to create intricately detailed workpieces. Wire EDM cutting is extremely … ↩
-
Learn how non-destructive testing ensures product integrity without damage.: It can be applied contact-free and is a non-destructive testing (NDT) method. In comparison, testing with ultrasound waves usually requires a coupling medium … ↩