Ever wondered how those colorful LEGO bricks are made?
LEGO bricks are produced through injection molding, where molten plastic is shaped in precise molds, ensuring durability, consistency, and perfect fit for high-quality construction.
While injection molding is the core technique, there’s much more to LEGO’s production story. I remember the first time I walked into a mold factory; the precision and scale were awe-inspiring. It’s not just about shaping plastic; it’s about crafting perfect pieces that fit together seamlessly. From selecting top-grade materials to engineering molds with pinpoint accuracy, every step in LEGO’s process is a testament to their commitment to quality. Dive deeper with me into the fascinating blend of art and science that brings these beloved bricks to life.
LEGO bricks are made from recycled plastic.False
LEGO bricks are made from ABS plastic, not recycled materials.
Injection molding ensures LEGO brick precision.True
This process creates consistent shapes that fit perfectly together.
- 1. What Materials Are Used in LEGO Bricks?
- 2. Why Is Injection Molding Preferred for LEGO Production?
- 3. How Does LEGO Achieve Precision in Their Molds?
- 4. What Environmental Practices Does LEGO Follow?
- 5. How Can You Identify Injection Molded Products?
- 6. What Challenges Do LEGO Brick Manufacturers Face?
- 7. Conclusion
What Materials Are Used in LEGO Bricks?
Have you ever marveled at the vibrant, sturdy LEGO bricks that seem to withstand endless playtime without losing their charm?
LEGO bricks are made from Acrylonitrile Butadiene Styrene (ABS), a durable thermoplastic known for strength, longevity, and vibrant color retention, ensuring both safety and mechanical excellence.
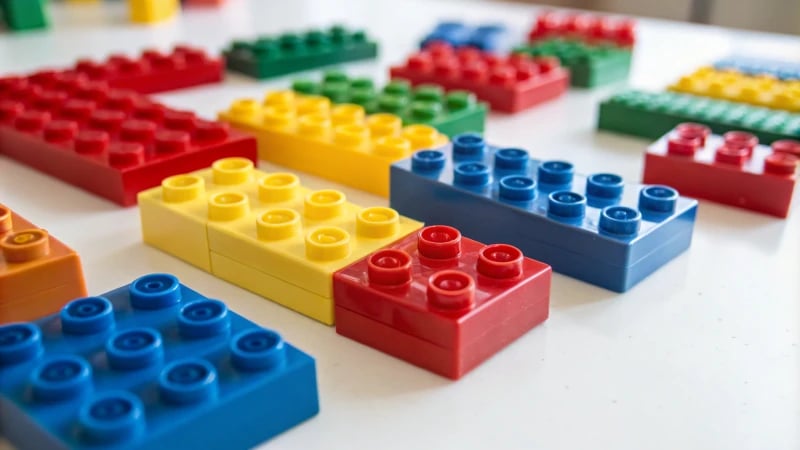
Exploring the Core Material: ABS
When I first learned about Acrylonitrile Butadiene Styrene, or ABS, I was amazed at how this thermoplastic polymer holds up under pressure, quite literally. As a kid, my LEGO creations took quite the beating—whether it was a giant tower crash or an epic spaceship battle—but they rarely broke. That’s thanks to ABS‘s incredible strength and rigidity1, which make it perfect for toys designed to endure years of imaginative play. Plus, ABS’s resistance to chemical interactions ensures that these beloved bricks maintain their form even after countless adventures.
The Role of Polycarbonate in LEGO
I remember the first time I built a LEGO set with transparent elements; it was a game-changer. Those crystal-clear windows and intricate designs were made possible by polycarbonate2. This material is known for its superior clarity and impact resistance, allowing us to see through our creations and imagine new worlds. Polycarbonate adds both beauty and functionality where see-through components are essential.
Environmental Considerations and Alternatives
It’s heartening to see LEGO making strides toward sustainability. Recently, they’ve started using bio-polyethylene, derived from sugarcane, in some newer sets. This shift not only reduces the carbon footprint but also aligns with a broader commitment to sustainability3 and protecting our planet. Seeing this change reminds me of when I started paying more attention to the environmental impact of my work; it’s a journey that transforms how you approach design and production.
Material | Usage | Properties |
---|---|---|
ABS | Most standard bricks | High strength, durable, colorful |
Polycarbonate | Transparent elements like windows | Clear, impact-resistant |
Bio-polyethylene | Select parts in newer eco-friendly sets | Renewable, lower carbon footprint |
Safety and Quality Standards
For me, safety is non-negotiable, especially when it comes to children’s toys. LEGO’s rigorous testing ensures each brick is non-toxic and safe for kids of all ages. Their stringent quality control processes4 mean that every set performs consistently, which is something I strive for in my own projects too.
Understanding these materials not only highlights LEGO’s engineering prowess but also reflects their evolving commitment to innovation and sustainability. As they continue exploring greener alternatives, I’m inspired to think about how I can incorporate similar practices into my own work. For those like me in product design and mold creation, diving deeper into these materials might just spark new ideas for our own projects. Exploring these materials further5 could open up new possibilities in design and environmental responsibility.
LEGO bricks are mainly made from polycarbonate.False
LEGO bricks are primarily made from ABS, not polycarbonate.
Bio-polyethylene is used in some newer LEGO sets.True
Bio-polyethylene, derived from sugarcane, is used in eco-friendly sets.
Why Is Injection Molding Preferred for LEGO Production?
Ever wondered why LEGO bricks always snap together so perfectly, no matter how many times you take them apart?
Injection molding is preferred for LEGO production due to its precision, consistency, and efficiency, enabling the mass production of durable, high-quality bricks that meet LEGO’s strict standards.
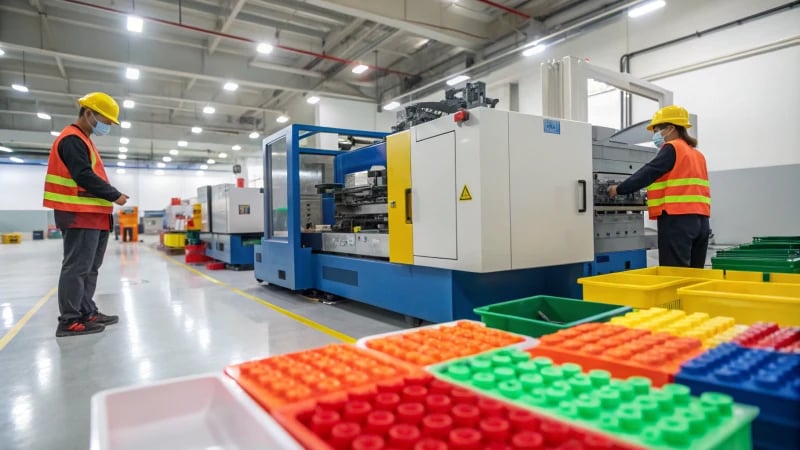
The Precision of Injection Molding
I remember the first time I set foot in a mold factory, the hum of machinery was like a symphony to my ears. Precision was everything there, just like it is for LEGO. Their bricks are famous for clicking together with satisfying accuracy, a testament to the precision of injection molding6. This method can achieve tolerances as fine as 0.005 mm, ensuring each piece fits perfectly, just like the time I meticulously crafted a prototype that needed to interlock seamlessly with existing parts.
Efficiency in Large-Scale Production
Back in my early days of manufacturing, I was awestruck by how fast we could churn out products. Similarly, LEGO uses injection molding to keep up with its staggering annual output of billions of bricks. With rapid production cycles and multi-cavity molds, they can produce multiple bricks in mere seconds—much like the time I marveled at a machine spitting out components faster than I could count!
Factor | Injection Molding Benefits |
---|---|
Precision | High tolerance manufacturing |
Production Speed | Rapid cycle times |
Consistency | Uniform quality |
Material Consistency and Strength
Remember that old toy you loved as a child that just wouldn’t break? LEGO’s use of ABS plastic7 through injection molding gives their bricks that same legendary durability. I’ve spent years working with different plastics, and ABS stands out for its toughness and smooth finish, making it ideal for the rough-and-tumble play of kids. The even distribution of material within each mold ensures every brick is as strong as it should be.
Cost-Effectiveness in the Long Run
While getting into injection molding initially might seem pricey—believe me, I’ve been there with custom molds and machines—it pays off. Over time, it becomes incredibly cost-effective. Producing large quantities quickly minimizes labor costs and reduces waste. Advances in mold design technologies8 have even trimmed cycle times further, making the process leaner and more efficient.
Adaptability to Complex Designs
As a designer, I love when creativity meets technology. LEGO’s increasingly intricate sets showcase how injection molding supports complex geometries thanks to advanced tooling and mold design techniques. It reminds me of projects where I had to push the boundaries of design while keeping production feasible.
Injection molding isn’t just a manufacturing choice; it’s a cornerstone of LEGO’s commitment to quality and innovation. It ensures every brick contributes to an exceptional play experience, just as my dedication to precision and efficiency has shaped my career.
LEGO bricks have a tolerance of 0.005 mm.True
Injection molding ensures precise interlocking by achieving tight tolerances.
ABS plastic is not used in LEGO production.False
ABS plastic is chosen for its durability and smooth finish in LEGO bricks.
How Does LEGO Achieve Precision in Their Molds?
Ever wondered how LEGO bricks always fit together seamlessly? It’s not magic, but a fascinating blend of technology and dedication. Join me as we explore how LEGO crafts such precise molds.
LEGO achieves mold precision with meticulous design, advanced CAD software, high-precision CNC machines, and rigorous quality checks, reaching tolerances as fine as 10 micrometers.
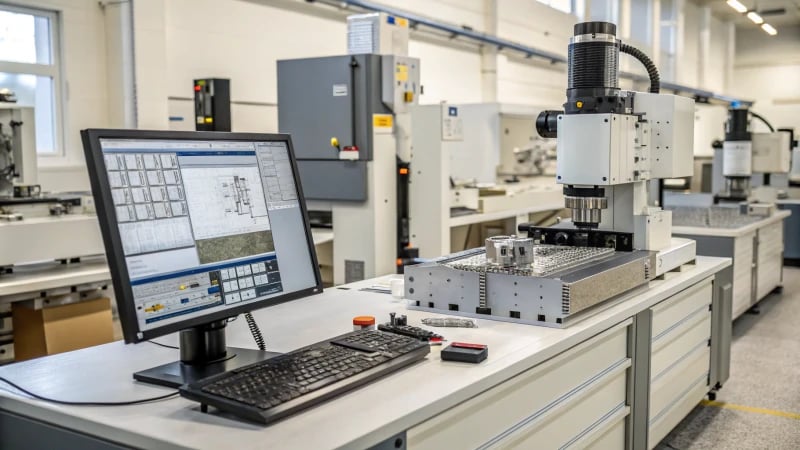
The Role of Advanced Design Tools
Imagine being an engineer tasked with designing a LEGO brick. It’s a journey that begins with advanced CAD software9. This software is like a digital playground where engineers craft every detail with precision. I remember the first time I watched an engineer bring a design to life on a computer screen; it was like watching a maestro compose music. Each click and drag was a note in the symphony of creation.
High-Precision CNC Machining
After the designs are finalized, they’re brought to life using CNC machines. These machines are the unsung heroes of precision, achieving tolerances as tight as 10 micrometers. Picture this: it’s akin to slicing a human hair into ten equal parts! When I first learned about CNC machining, it blew my mind just how precise these machines could be.
Quality Control Measures
Every mold is put through its paces with rigorous quality control. Think of it like a LEGO boot camp, ensuring each piece meets exacting standards.
Factor | Description |
---|---|
Dimensionality | Ensures molds maintain specified sizes |
Durability | Assesses wear resistance over time |
Surface Finish | Checks for smoothness and consistency |
These tests remind me of the countless times I’ve had to ensure my own projects were flawless before sending them off. It’s both nerve-wracking and exhilarating.
Continuous Innovation and Research
LEGO is constantly on the lookout for new materials and technologies to enhance their processes. This pursuit of innovation is something I deeply relate to, having seen firsthand how staying ahead of the curve can transform production efficiency and sustainability.
By integrating emerging manufacturing techniques10, LEGO not only maintains precision but also pushes the boundaries of what’s possible in manufacturing.
Collaboration with Industry Experts
Collaboration is at the heart of LEGO’s process. They partner with experts from various fields to refine their methods. This reminds me of the collaborative efforts in my career, where sharing knowledge has led to some of the most innovative solutions.
By combining technology, innovation, and expertise, LEGO remains a leader in crafting impeccably precise molds—a testament to their commitment to quality and excellence.
LEGO uses CAD software for mold design.True
LEGO employs advanced CAD software to create precise digital designs.
LEGO's CNC machines have a tolerance of 5 micrometers.False
LEGO's CNC machines achieve tolerances as tight as 10 micrometers.
What Environmental Practices Does LEGO Follow?
Ever wondered how LEGO keeps its magic alive while caring for our planet? Dive into their eco-friendly practices that promise a greener tomorrow!
LEGO adopts eco-friendly practices by using plant-based plastics, aiming for carbon-neutral production, investing in renewable energy, and minimizing waste through sustainable materials.
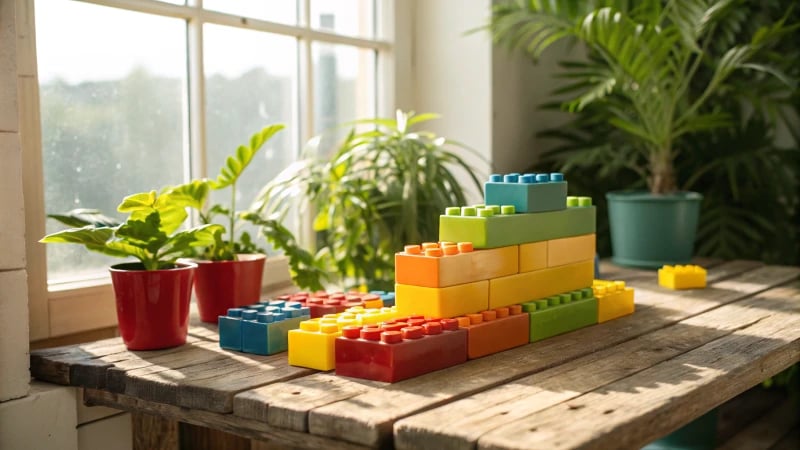
Sustainable Materials
I remember the first time I stepped on a LEGO brick in the middle of the night—painful, yes, but it got me thinking about what goes into making those iconic pieces. LEGO has taken a significant leap by switching to plant-based plastics11 made from sugarcane. Imagine that! By 2030, they aim to produce all their bricks from sustainable materials. It’s a giant step for tiny blocks!
Year | Sustainability Goal |
---|---|
2020 | Achieved 100% renewable energy capacity |
2025 | All packaging to be sustainable |
2030 | All products made from sustainable materials |
Energy Efficiency
When I think about energy efficiency, I’m reminded of my own journey to swap out every bulb in my house for LEDs—one small change at a time. Similarly, LEGO has committed to reducing its carbon footprint through renewable energy. In 2017, they reached their goal of balancing 100% of their energy use with renewable sources, thanks largely to wind power. It’s inspiring to see such dedication from a company of this scale.
Waste Reduction
Ever tried to minimize your own waste at home? It can be a challenge! Yet, LEGO factories manage to recycle over 93% of their waste. They’re constantly innovating to reduce production waste and improve recycling efforts. I find it encouraging to see such a large-scale operation putting in the effort to make every bit count.
Community and Innovation
LEGO’s commitment goes beyond bricks—they’re investing in community projects and innovations that foster sustainability. I recall joining a community clean-up event organized by LEGO, which was not only rewarding but also enlightening. The LEGO Foundation supports educational programs teaching kids about sustainability and environmental responsibility, which is crucial for building a better future.
While LEGO’s sustainability journey is ongoing, it’s clear they’re passionate about making a positive impact on our planet. If you’re curious about more detailed initiatives, checking out their annual sustainability reports12 offers a wealth of information.
LEGO uses oil-based plastics in all products.False
LEGO is shifting to plant-based plastics from sugarcane by 2030.
LEGO achieved 100% renewable energy capacity by 2020.True
LEGO reached this goal, focusing on wind power investments.
How Can You Identify Injection Molded Products?
Ever wondered how those plastic products in your life are made? Let me share a secret: many are injection molded! Here’s how you can tell.
Injection molded products are identified by parting lines, gate marks, ejector pin marks, uniform wall thickness, and consistent material, distinguishing them from other manufacturing methods.
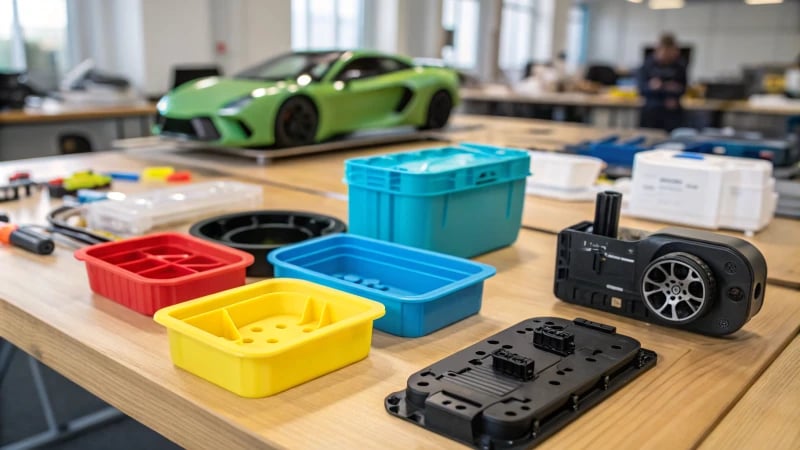
Key Characteristics of Injection Molded Products
Have you ever picked up a plastic gadget and wondered how it was made? I remember doing just that with my favorite kitchen spatula. As a designer, I’m always fascinated by the little clues that reveal the craftsmanship behind everyday objects. Injection molded products are no exception—they tell their own story through distinct features.
For instance, parting lines are like the seams on your favorite jeans. They appear where the two halves of the mold meet, providing a peek into the molding process13. Then there’s the gate mark, a small blemish akin to a birthmark on the plastic surface, showing where molten plastic first entered the mold. Depending on how polished the product is, these marks might be subtle but are usually present if you know where to look.
Ejector pin marks are another telltale sign—imagine little dimples left by pins pushing the product out of its mold home. These are typically hidden on the underside or in less conspicuous areas, almost like an artist’s signature tucked away in a corner.
Feature | Description |
---|---|
Parting Line | Line where two mold halves meet, often visible on the product. |
Gate Mark | Small blemish from where plastic enters the mold. |
Ejector Pin Marks | Circular marks from pins ejecting the product from the mold. |
Material Consistency and Wall Thickness
One thing I’ve learned over the years is that consistency is key—both in life and in injection molding! These products often boast uniform wall thickness, which adds to their durability and strength. If you’ve ever noticed a plastic item that’s warped or oddly shaped, it might be because its walls aren’t as consistent as they should be.
And let’s not forget about material consistency. Thanks to the high-pressure nature of injection molding, these items usually have a smooth finish and even color distribution. It’s like seeing a beautifully painted wall; this evenness tells you a lot about quality.
Applications in Various Industries
The versatility of injection molding never ceases to amaze me. It’s used in industries ranging from consumer electronics to automotive parts. Take electronics, for example—I once had a project designing plastic casings with intricate details that could only be achieved through injection molding techniques14. Or think about car dashboards and bumpers—those sleek surfaces are often results of this process.
By understanding these characteristics and observing your surroundings, you can start to appreciate the engineering behind everyday plastic products. This knowledge isn’t just interesting; it’s incredibly useful for product designers15 like me, as well as quality control professionals aiming to enhance manufacturing outcomes.
Parting lines are always visible on injection molded products.False
Parting lines can be polished away, making them less visible.
Injection molded products have uniform wall thickness.True
Uniform wall thickness is crucial for preventing warping and defects.
What Challenges Do LEGO Brick Manufacturers Face?
Have you ever marveled at the vibrant, perfectly interlocking LEGO bricks and wondered what it takes to create them? Behind each piece lies a world of intricate challenges.
LEGO brick manufacturers face challenges in precision mold design, consistent color production, and sustainability, necessitating innovative solutions to maintain LEGO’s high standards.
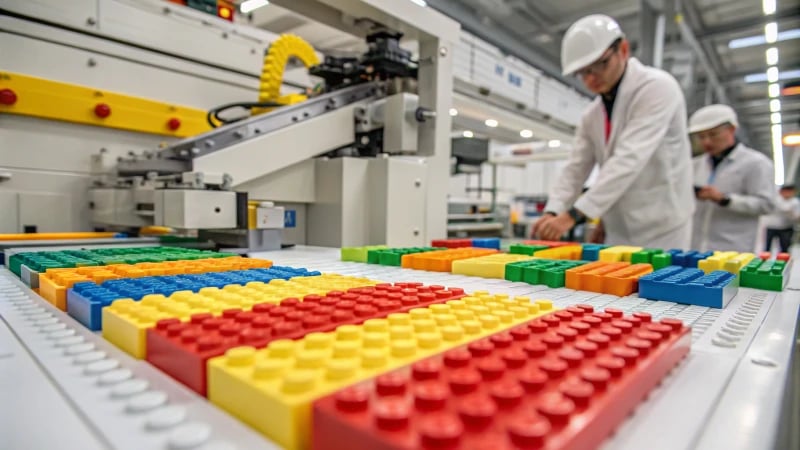
Ensuring Precision in Mold Design
I remember the first time I held a LEGO brick as a child, marveling at how perfectly each piece snapped together. Little did I know, achieving such precision is no small feat. Designing molds for LEGO requires accuracy that borders on perfection; even a slight mistake could ruin an entire set. It’s like trying to bake the perfect cake—every ingredient and step has to be just right. To accomplish this, LEGO uses highly advanced Computer-Aided Design (CAD) software and CNC machines that ensure each brick fits flawlessly.
Table: Factors Affecting Mold Precision
Factor | Impact on Precision |
---|---|
Material Quality | Consistency |
Machine Tolerances | Accuracy |
Environmental | Stability |
Color Consistency
The joy of opening a fresh box of LEGOs is like diving into a rainbow. But maintaining that vibrant spectrum isn’t easy. Imagine trying to paint the same picture over and over without any variation—that’s the challenge LEGO faces with color consistency. They have stringent quality control measures16 to ensure that every shade is exact, akin to the meticulous care a chef takes in replicating their signature dish.
Sustainability Concerns
In today’s world, we all think twice about sustainability. LEGO is no different, with a goal of moving away from petroleum-based plastics. It’s not just about swapping materials; it’s about finding ones that won’t compromise the iconic ‘click’ sound when two bricks snap together. It reminds me of the time I tried switching to eco-friendly coffee cups at my shop—not all of them held up to the test! LEGO’s ongoing research into sustainable materials17 is a testament to their commitment to innovation and environmental responsibility.
Scaling Production Without Sacrificing Quality
Producing billions of bricks annually is a staggering task. Think about preparing a massive feast while ensuring every dish tastes just as you envisioned. LEGO’s use of automated systems and real-time monitoring helps maintain their impeccable standards across vast production runs. It’s like having a kitchen filled with skilled chefs who never miss a beat.
Exploring LEGO’s manufacturing approach not only sheds light on their dedication to quality but also offers valuable lessons in balancing innovation with responsibility.
LEGO uses CNC machines for mold precision.True
CNC machines ensure high accuracy in mold design and production.
LEGO bricks are made from bio-polyethylene.False
LEGO is exploring bio-polyethylene but primarily uses ABS plastic.
Conclusion
LEGO bricks are primarily made through injection molding using ABS plastic, ensuring precision and durability while the company shifts towards sustainable materials for environmental responsibility.
-
Learn about the unique properties that make ABS plastic ideal for durable consumer products like LEGO. ↩
-
Discover how polycarbonate plastic is utilized in various industries for its strength and transparency. ↩
-
Explore LEGO’s efforts to adopt sustainable practices in their manufacturing process. ↩
-
Understand the rigorous quality control processes LEGO employs to ensure product safety and reliability. ↩
-
Gain insights into how material selection impacts product design, performance, and sustainability. ↩
-
Discover how injection molding achieves high precision, crucial for LEGO’s quality standards. ↩
-
Learn why ABS plastic is chosen for its strength and durability in LEGO products. ↩
-
Explore how new mold design technologies reduce costs and improve efficiency. ↩
-
Discover which CAD tools LEGO employs to achieve precision in their mold designs. ↩
-
Learn about the cutting-edge manufacturing methods LEGO is adopting to enhance precision. ↩
-
Explore LEGO’s use of plant-based plastics and how it contributes to reducing environmental impact. ↩
-
Review LEGO’s latest sustainability report for an in-depth understanding of their environmental strategies. ↩
-
Learn about parting lines to understand how they affect the final appearance of injection molded products. ↩
-
Explore how injection molding is applied in electronics to achieve precise and aesthetic designs. ↩
-
Discover why understanding injection molding is crucial for designers in creating functional and aesthetic products. ↩
-
Learn about the meticulous quality control measures LEGO implements to maintain its vibrant color palette. ↩
-
Explore the innovative materials LEGO is considering to replace traditional plastics and enhance sustainability. ↩