Have you ever wondered how those everyday plastic items are made? Let’s dive into the fascinating world of injection molding!
Injection molding is a fundamental process in manufacturing, and understanding its components is vital for precision and efficiency.
But wait! There’s so much more to discover about how these components work together. Let’s take a deeper look into each part and see their significance in creating high-quality molded products.
The main runner controls the flow of plastic melt.True
The main runner directs molten plastic from the nozzle to the mold cavity.
What Are the Key Components of an Injection Mold?
Understanding the key components of an injection mold is crucial for optimizing manufacturing processes and ensuring product quality.
Injection molds consist of several essential components: casting system, molding parts, demolding mechanism, guide mechanism, cooling system, and exhaust system. Each part plays a crucial role in shaping and producing plastic parts efficiently and accurately.
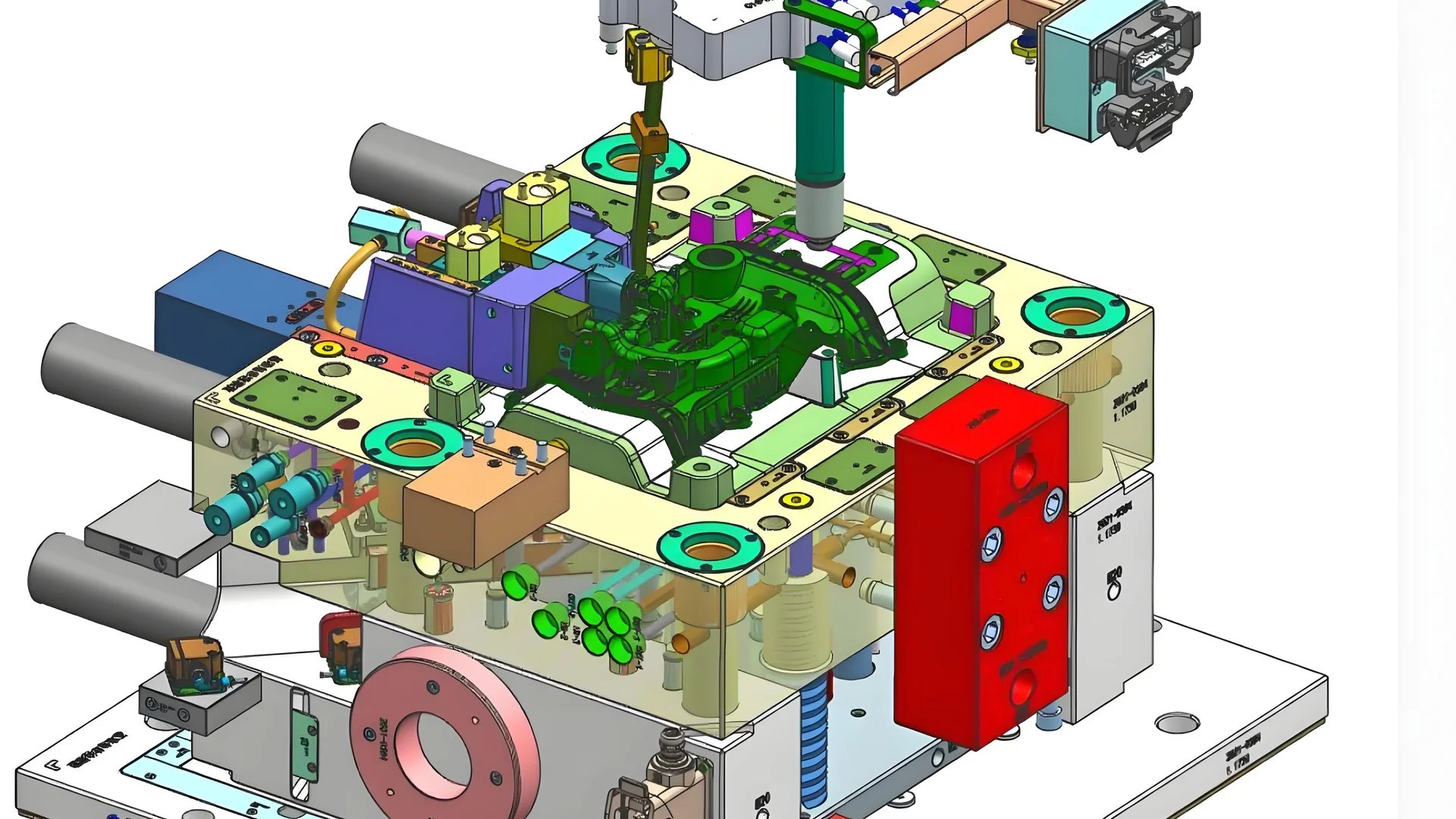
Casting System
The casting system is the gateway for molten plastic to enter the mold cavity. It includes the main runner, branch runner, and gate.
-
Main Runner: Acts as the primary conduit between the injection molding machine nozzle and the mold. It is vital for controlling the flow of plastic melt into the mold.
-
Branch Runner: Distributes the molten plastic evenly across various cavities, ensuring simultaneous filling.
-
Gate: Regulates the entry of plastic melt into the cavity, controlling flow rate and preventing overflow.
Molding Parts
These components determine the shape of the final product by forming both inner and outer surfaces.
-
Punch (Core): Responsible for shaping the inner surface of the plastic part. Installed on the movable side of the mold, it works in tandem with the concave mold.
-
Concave Mold (Cavity): Shapes the outer surface. Positioned on the fixed mold side, it complements the punch to create the desired shape.
Demolding Mechanism
This mechanism ensures that finished parts are efficiently ejected from the mold.
-
Ejector: Facilitates removal of molded parts from the punch by pushing them out.
-
Push Plate: Works with the ejector to completely eject parts from the mold cavity.
Guide Mechanism
Essential for maintaining alignment and accuracy during mold opening and closing.
-
Guide Pillar: Aligns the movable and fixed molds, ensuring precision in movement.
-
Guide Sleeve: Works with the guide pillar to maintain movement accuracy.
Cooling System
Regulates temperature within the mold to enhance quality and efficiency.
- Cooling Water Channel: Circulates water to cool down the plastic melt, crucial for solidification and mold performance.
Exhaust System
Prevents defects by removing air and volatiles from the mold cavity.
- Exhaust Groove: Located at strategic points such as parting surfaces to allow air escape, preventing weld marks and voids in molded parts.
Understanding these components reveals how each plays a critical role in manufacturing precision plastic parts. To further explore how they interact, check out this detailed breakdown of injection mold components1.
The main runner controls plastic flow into the mold.True
The main runner is crucial for controlling the flow of plastic melt.
Exhaust grooves are part of the cooling system.False
Exhaust grooves are part of the exhaust system, not cooling.
How Does the Casting System Influence Molding Efficiency?
The casting system is pivotal in the injection molding process, directly affecting the efficiency and quality of molded products.
The casting system, consisting of the main runner, branch runner, and gate, significantly influences molding efficiency by ensuring optimal flow and distribution of molten plastic.

Understanding the Casting System’s Components
The casting system is integral to injection molding, comprising several key components that ensure the efficient flow and distribution of molten plastic. These components include the main runner, branch runner, and gate, each playing a crucial role in maintaining molding efficiency.
-
Main Runner: The primary channel connecting the injection molding machine’s nozzle to the branch runner. It introduces the molten plastic into the mold cavity. The main runner’s design significantly impacts the flow and filling of the plastic melt, making it essential for achieving uniformity across multiple cavities.
-
Branch Runner: Once the plastic melt travels through the main runner, it is distributed via the branch runner. This component ensures even distribution of the melt into each cavity, allowing simultaneous filling. Its design affects the balance and timing of filling across cavities, which is vital for maintaining quality and reducing cycle times.
-
Gate: The gate links the branch runner to the cavity, controlling the flow rate and timing of the molten plastic. Proper gate design prevents backflow and overflow, influencing both the structural integrity and aesthetic quality of the final product.
Impact on Efficiency and Quality
The efficiency of the casting system is paramount to both production speed and product quality. By ensuring precise control over the flow of molten plastic, these components minimize defects such as voids or weld lines. Efficient designs of runners and gates reduce waste and energy consumption while optimizing cycle times.
Design Considerations for Optimal Molding
To maximize efficiency, designers must consider:
- Geometry and Size: The shape and size of runners and gates must support adequate flow without causing excessive pressure or shear stress.
- Material Flow Characteristics: Understanding how different plastics behave when melted can guide optimal design choices.
- Temperature Management: Effective temperature control within the casting system helps maintain consistent melt viscosity, crucial for high-quality molding.
For further exploration on optimizing casting systems, check out resources on runner system design2 and gate optimization techniques3. These insights can enhance understanding of how design tweaks can boost efficiency.
By examining these components’ roles and influences, manufacturers can better tailor their systems to produce superior molded products with enhanced efficiency and reduced defects.
Main runner design affects plastic flow uniformity.True
The main runner's design is crucial for uniform flow in molding.
Gates prevent backflow and overflow in molding.True
Proper gate design controls flow, preventing backflow and overflow.
What Role Do Molding Parts Play in Shaping Plastic Products?
Molding parts are crucial in defining the dimensions, surface finish, and structural integrity of plastic products.
Molding parts, including the punch and concave mold, are essential in forming the inner and outer shapes of plastic products. These components ensure precise detailing and consistency across production batches, impacting the quality and functionality of the final product.

Understanding the Key Molding Parts
Molding parts are integral to the injection molding process, primarily responsible for shaping the molten plastic into a predefined form. These components work in harmony to deliver precise and consistent plastic products. Let’s delve into two main components: the punch and the concave mold.
Punch: Forming the Inner Surface
The punch, often referred to as the core, is vital in crafting the internal features of a plastic part. Typically installed on the movable mold side, it engages with the concave mold during the injection process to shape the inner surfaces.
Functionality:
- Defines cavities and hollows within a plastic product.
- Provides structural integrity by ensuring uniform wall thickness.
- Works with the concave mold to control dimensional accuracy.
For instance, in the manufacturing of a plastic bottle, the punch determines the bottle’s internal volume and neck design.
Concave Mold: Shaping the Outer Surface
The concave mold, or cavity, is tasked with creating the external profile of a plastic product. Mounted on the fixed mold side, it complements the punch to complete the shape formation process.
Functionality:
- Establishes the outer dimensions and aesthetic features.
- Influences surface finish quality through texture patterns and precision.
- Coordinates with cooling systems to facilitate efficient solidification.
Consider a smartphone case; the concave mold defines its outer contours and texture, ensuring protective strength and tactile appeal.
The Interplay Between Punch and Concave Mold
Together, these molding parts must work seamlessly to avoid defects such as warping or misalignment. Ensuring both components are meticulously designed and aligned is crucial for achieving high-quality outputs.
Advances in Molding Technology
Modern innovations have introduced enhanced materials and precision engineering techniques to further refine molding part efficacy. For more detailed insights into recent advancements, explore advancements in injection molding technology4.
Practical Applications and Case Studies
Understanding real-world applications of molding parts can provide deeper insights into their significance. Learn how industries implement these components for superior product quality through real-world molding applications5.
Through these detailed insights, it becomes evident that molding parts are not just functional components but pivotal elements in shaping products that meet exacting industry standards.
The punch forms the outer surface of plastic products.False
The punch shapes the inner surface, not the outer.
Concave molds influence the external features of plastics.True
Concave molds define outer dimensions and aesthetics.
Why Is the Cooling System Vital for Mold Performance?
The cooling system is crucial in injection molding, directly affecting the quality and efficiency of the process.
The cooling system in injection molding ensures rapid solidification of molten plastic, maintaining precision and reducing cycle times. It regulates mold temperature, preventing defects and enhancing production efficiency.
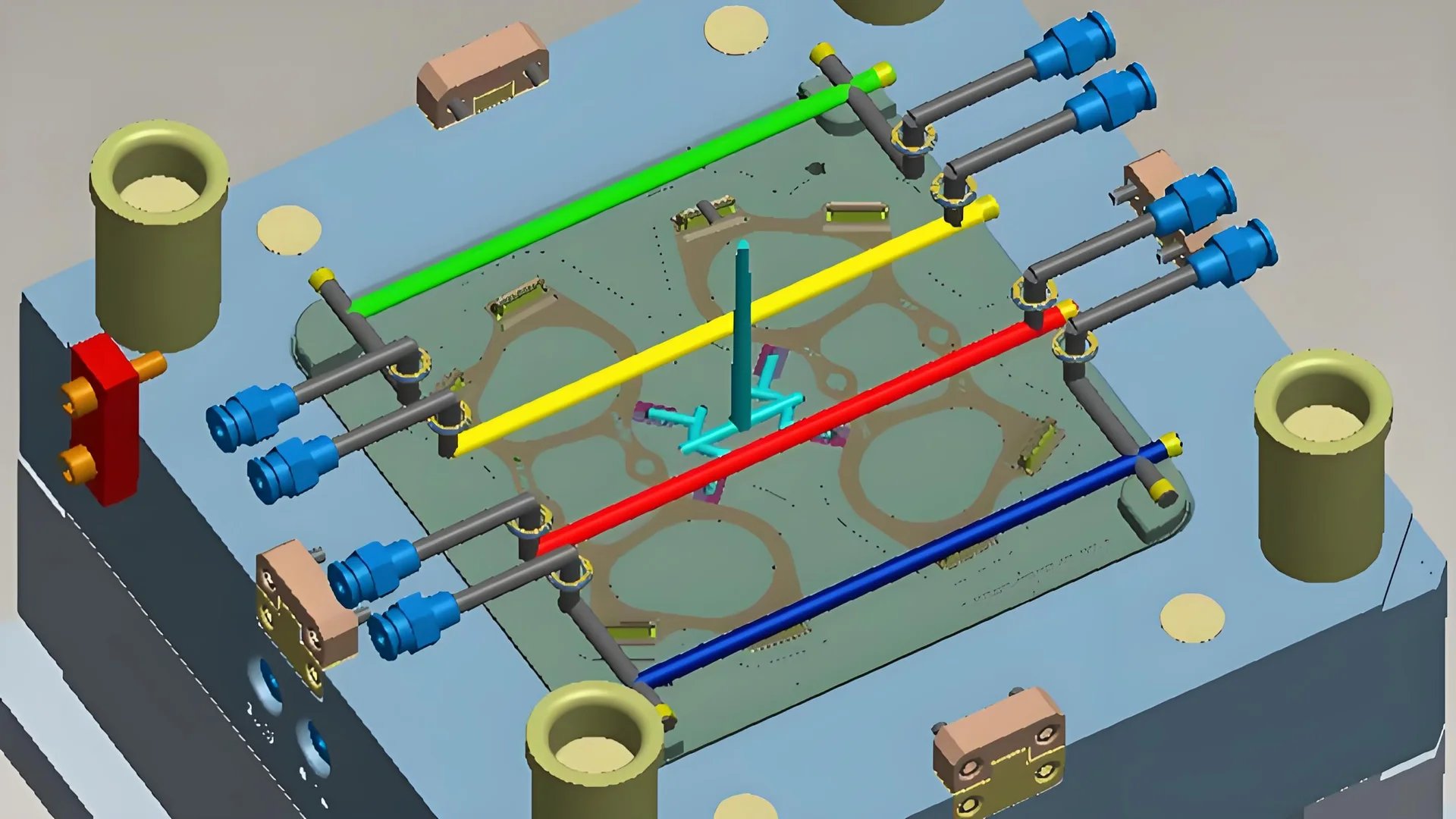
The Role of Cooling Systems in Injection Molding
In injection molding, the cooling system’s primary function is to remove heat from the molten plastic as quickly and efficiently as possible. This process is crucial because:
-
Rapid Solidification: By swiftly cooling the molten plastic, the cooling system ensures that parts solidify quickly, maintaining their shape and dimensions. This rapid solidification helps in achieving precise dimensions and reduces the chances of warping or deformities.
-
Cycle Time Reduction: Efficient cooling shortens the cycle time—the duration needed to produce a single part—which is vital for high-volume production. A well-optimized cooling system can significantly enhance productivity.
-
Quality Enhancement: Proper cooling helps prevent common defects such as sink marks, voids, and warpage. Maintaining an even temperature throughout the mold ensures uniform part quality.
Components of the Cooling System
-
Cooling Water Channels: These channels are strategically placed around the mold cavity and core to facilitate uniform cooling. The design and placement of these channels directly impact cooling efficiency and part quality.
-
Temperature Control Units: These units regulate the flow and temperature of the cooling medium (usually water). By adjusting these parameters, manufacturers can optimize the cooling rate to suit specific material properties and product requirements.
-
Baffles and Bubbler Systems: For complex molds with intricate shapes, baffles and bubblers help direct the coolant closer to critical areas, ensuring effective heat removal.
Impact on Mold Performance
-
Temperature Uniformity: A well-designed cooling system maintains consistent temperature across the mold surfaces, crucial for dimensional accuracy and structural integrity of molded parts.
-
Mold Longevity: Efficient heat removal prevents overheating and thermal stress on the mold, prolonging its lifespan and reducing maintenance needs.
-
Energy Efficiency: By optimizing the cooling process, manufacturers can reduce energy consumption, thereby lowering operational costs.
A deep understanding of cooling water channel design6 and its implications can lead to significant improvements in mold performance. Additionally, exploring temperature control techniques7 offers insights into achieving optimal cycle times and product quality.
Cooling systems reduce cycle times in injection molding.True
Efficient cooling leads to faster solidification, shortening production cycles.
Mold longevity is unaffected by cooling system efficiency.False
Proper cooling prevents thermal stress, extending mold lifespan.
Conclusion
By exploring these components, I’ve gained a newfound respect for the intricate dance of engineering that produces everyday items.
-
Discover how each component contributes to efficient molding.: An injection mold is a tool comprised of a series of parts that allows molten plastic to be formed and cooled in such a way as to create a discrete part shape. ↩
-
Learn about advanced runner designs for improved flow efficiency.: Mold design: The runner system should be designed to minimize pressure drop and ensure that the material flows evenly throughout the mold cavity. There are … ↩
-
Discover methods to enhance gate performance and reduce defects.: In this guide, we will explore the fundamentals of injection molded gates and provide valuable insights to help you make informed decisions in your injection … ↩
-
Discover cutting-edge innovations enhancing molding precision and efficiency.: A great innovation for injection molding is structural foam molding. This process combines injection molding and gas-assisted injection molding … ↩
-
Explore practical examples showcasing molding part effectiveness.: 3. Legos and Toys. Toys for children are also among the most common injection molded plastic parts for several reasons. First, you can expect … ↩
-
Learn about efficient designs to enhance mold cooling performance.: Injection Mold Cooling System Design · Confirm that cooling channels are as close as possible to the thickest part of the mold cavity (i.e., the … ↩
-
Discover methods for optimizing mold temperature control.: Control of the temperature of the medium. This method is used most frequently. · Control of the mould temperature. A temperature probe is installed for this. ↩