Remember the first time you got lost in how things work? Injection molding is one of those fascinating processes that hooks you with its precision and complexity.
An injection molding machine heats plastic to a molten state, then injects it into a mold to cool and form. Its structure comprises an injection unit, mold, clamping unit, and control system.
When I first stepped into the world of plastic design, I was amazed by how these machines transform tiny pellets into the gadgets we use daily. Breaking down each component helped me see how essential they are to creating flawless designs. From the precise injection unit to the robust clamping system, understanding these parts can save you time and headaches in production.
As a designer, having this knowledge isn’t just about technical know-how—it’s about envisioning your design’s journey from a concept to a tangible product. It’s like watching your ideas take shape, bit by bit, until they become something you can hold. So, let’s dive deeper into how each part contributes to this incredible process.
Injection molding machines can only produce simple shapes.False
They can produce complex shapes with precision, not just simple ones.
The injection unit is a key component of the machine's structure.True
The injection unit is essential for heating and injecting molten plastic.
- 1. What Are the Main Components of an Injection Molding Machine?
- 2. How Does the Injection Process Work Step by Step?
- 3. What Materials Are Commonly Used in Injection Molding?
- 4. What Are the Advantages of Using Injection Molding for Production?
- 5. How Can Designers Optimize Products for Injection Molding?
- 6. Conclusion
What Are the Main Components of an Injection Molding Machine?
Peering inside an injection molding machine feels like unraveling a complex puzzle of innovation and precision.
An injection molding machine consists of three main components: the injection unit, the mold, and the clamping unit, which work together to shape raw materials into finished products.
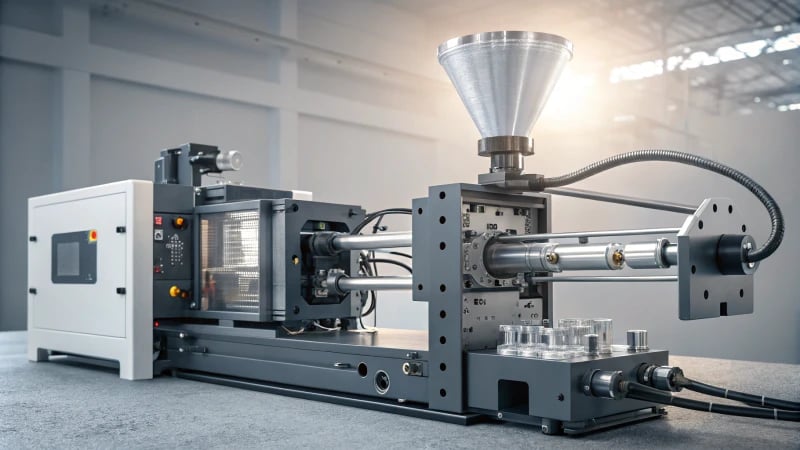
The Injection Unit
When I first stepped into a bustling manufacturing floor, the hum of machinery was a melody of modern engineering. One of the most fascinating aspects was the injection unit. This part is the heart of the operation, melting and injecting materials with such precision that it feels almost magical. The injection unit includes the hopper, barrel, reciprocating screw, and nozzle.
I remember watching as pellets cascaded from the hopper1 like tiny soldiers ready for duty. They were then fed into the heated barrel, where the real transformation happens. The rotating screw inside the barrel generates friction and heat, melting the material into a malleable state. This meticulous process always reminds me of how important each component is in shaping our everyday items.
Component | Function |
---|---|
Hopper | Stores raw material |
Barrel | Melts material |
Screw | Moves and mixes material |
Nozzle | Injects material into the mold |
The Mold
The mold is where creativity and engineering truly merge. It’s in these custom-designed cavities that molten plastic takes on its final form. As a designer, I’ve often marveled at how these molds, with their two halves—the core and cavity—work together to create both intricate details and smooth surfaces. Each project feels like crafting a new masterpiece.
Mold design2 is an art form in itself, demanding precision to achieve high-quality products. I’ve spent countless hours ensuring every contour and feature aligns perfectly, knowing that even the smallest oversight can impact the end product.
The Clamping Unit
The clamping unit has always fascinated me with its sheer power and precision. It holds mold halves together during the injection process and controls the cooling phase with unwavering force. This unit comprises a platen, toggle mechanism, or hydraulic cylinders that apply pressure, ensuring everything stays in perfect alignment.
Witnessing a clamping unit in action is like watching a well-rehearsed dance where every movement is calculated to perfection. It opens and closes the mold effortlessly, releasing finished products ready for the world.
Component | Function |
---|---|
Platen | Supports mold halves |
Toggle Mechanism | Provides mechanical force |
Hydraulic Cylinders | Apply pressure and control mold movements |
Understanding these components has not only enriched my career but also deepened my appreciation for the intricate dance of technology and design. It’s this knowledge that allows us to push the boundaries of what’s possible, optimizing injection molding processes3 for greater efficiency and unmatched quality.
The hopper injects material into the mold.False
The hopper stores raw material; the nozzle injects it.
The clamping unit opens and closes the mold.True
The clamping unit holds, opens, and closes the mold during production.
How Does the Injection Process Work Step by Step?
Ever wondered what happens to that little pile of plastic granules before it becomes your favorite gadget? Let me take you on a fascinating journey through the injection process.
The injection process involves preparing materials, injecting them into molds, cooling, and ejecting to create durable plastic products, ensuring high-quality manufacturing through precise execution of each step.
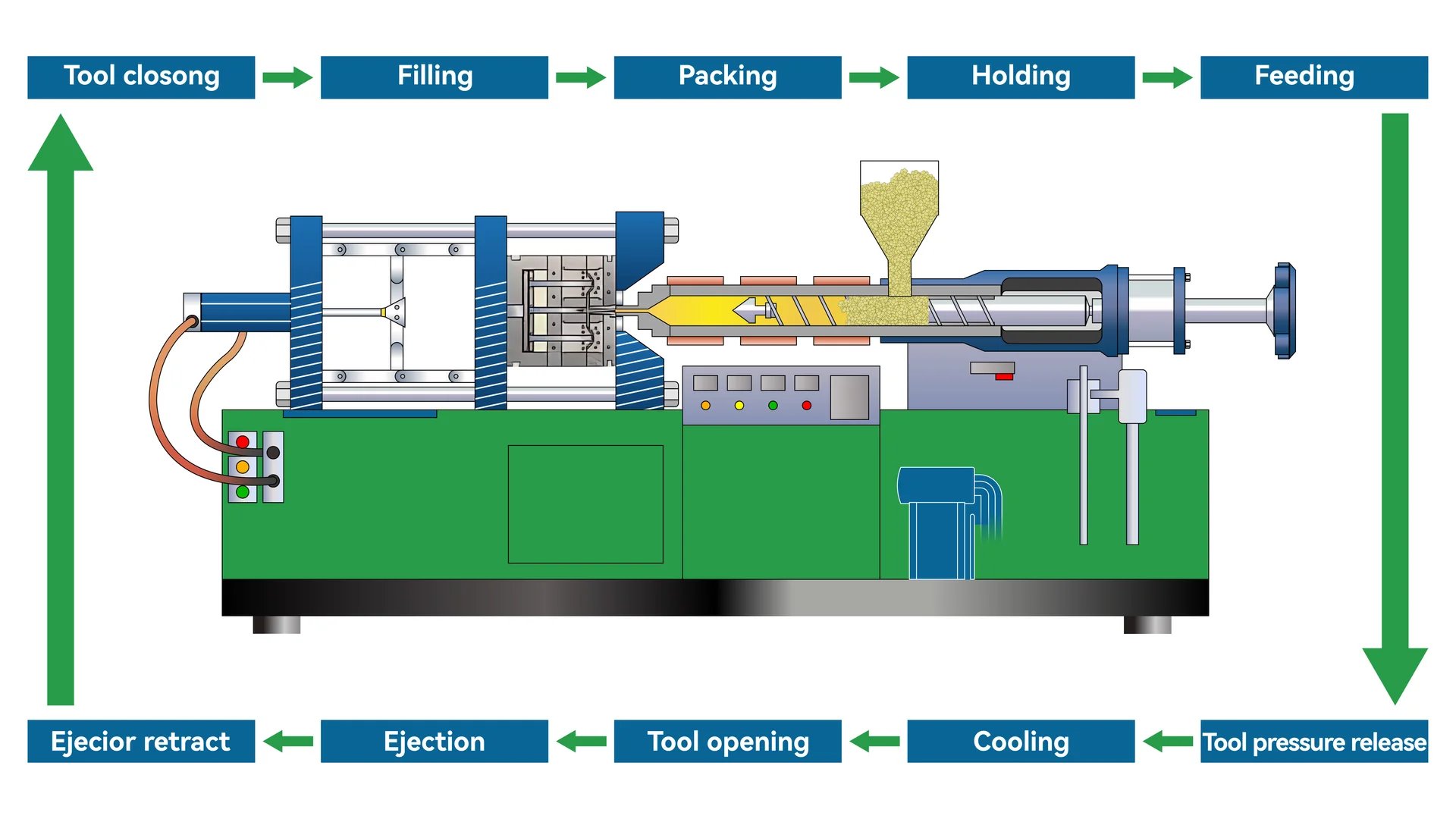
Material Preparation
I remember my first day at the mold factory; I was amazed by the meticulousness required just to prepare the material. We begin by selecting the right plastic granules and feeding them into the hopper. The granules are dried to remove moisture, ensuring the quality of molded parts4 isn’t compromised. It’s like getting the ingredients ready before baking a cake—precision is key!
Injection
Once dried, these granules are funneled into the injection molding machine’s barrel. I still recall the first time I saw the transformation—it was mesmerizing! The granules were heated to their melting point through heaters and shear forces, turning into molten plastic ready to be injected into a mold.
Step | Description |
---|---|
1 | Heat granules to melting point. |
2 | Inject molten plastic into mold. |
It’s fascinating how something solid and rigid can become so pliable.
Cooling
Cooling is a game of patience and precision. Once the molten plastic fills the mold, it starts to cool and solidify. Depending on material type and part thickness, cooling times vary. Effective cooling prevents defects and ensures each piece meets our stringent standards of dimensional accuracy.
Ejection
Finally, after cooling, the mold opens with a satisfying click, and ejector pins push the solidified part out. I still get a thrill every time I see a perfectly formed part emerge, ready for any finishing touches like trimming or surface treatments5. Each of these steps must be finely tuned to balance speed, quality, and efficiency.
Adjustments might be necessary depending on material properties6 or specific design needs. And every time we tweak a process or solve a problem, it feels like a small victory. This is what makes this job so rewarding—seeing raw materials transform into something useful and beautiful.
Plastic granules are dried to remove moisture before injection.True
Drying removes moisture, preventing defects and ensuring quality.
The cooling phase occurs after the mold is opened.False
Cooling happens while the mold is closed to solidify the part.
What Materials Are Commonly Used in Injection Molding?
I remember my first deep dive into injection molding; it felt like exploring a whole new world of possibilities.
Injection molding commonly uses thermoplastics like ABS, polycarbonate, and nylon for their distinct properties such as strength, flexibility, and resistance, making them suitable for various applications.
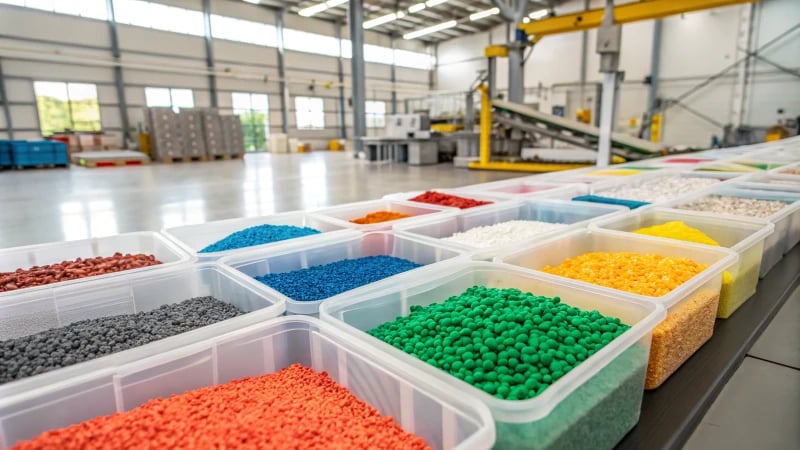
Understanding Thermoplastics
I still recall my early days in the field, experimenting with different thermoplastics and being amazed by their versatility. These materials, which soften when heated and harden when cooled, can be reused multiple times—making them both practical and eco-friendly.
Material | Properties | Applications |
---|---|---|
ABS | Toughness, impact-resistant | Automotive components |
Polycarbonate | Transparency, high impact strength | Eyewear line |
Take ABS7, for instance. I once worked on a project involving automotive components where ABS’s toughness was crucial. And then there’s polycarbonate8. Its transparency and impact strength were perfect for the eyewear line I helped design.
Exploring Other Material Options
Beyond thermoplastics, I’ve also dabbled with thermosetting plastics and elastomers. Each of these offers unique benefits that cater to specific needs:
- Thermosetting Plastics: These are like the steadfast warriors of the material world—once set, they don’t soften on reheating. Ideal for things like electrical insulators.
- Elastomers: Their elasticity reminds me of rubber bands. They’re fantastic for seals and hoses.
Lately, I’ve noticed a trend towards biodegradable materials9, which not only help in reducing environmental impact but also resonate with our collective responsibility towards sustainability.
Factors Influencing Material Choice
Choosing the right material feels a bit like matchmaking—it involves weighing multiple factors:
- Mechanical Properties: Strength, flexibility, and durability can’t be compromised.
- Cost: Balancing budget with performance is an art in itself.
- Environmental Impact: Opting for sustainable materials is increasingly becoming the norm.
One example I remember is when I opted for recycled plastics10 for a project. It was not only cost-effective but also aligned with our sustainability goals.
By delving into these factors and materials, designers like me strive to optimize products for performance and efficiency. With the latest research11 continually expanding our horizons, we can create innovative designs that keep pace with the demands of various industries.
ABS is used in automotive parts due to its glossiness.False
ABS is used for its toughness and impact resistance, not glossiness.
Thermosetting plastics are recyclable like thermoplastics.False
Thermosetting plastics cannot be remelted or reshaped, unlike thermoplastics.
What Are the Advantages of Using Injection Molding for Production?
Ever wondered why injection molding is a game-changer in manufacturing? Let me take you on a journey through its incredible benefits, from cost savings to design flexibility.
Injection molding offers high precision, repeatability, and cost-effectiveness for large-scale production. It supports complex designs and provides material flexibility, making it ideal for manufacturing intricate parts.
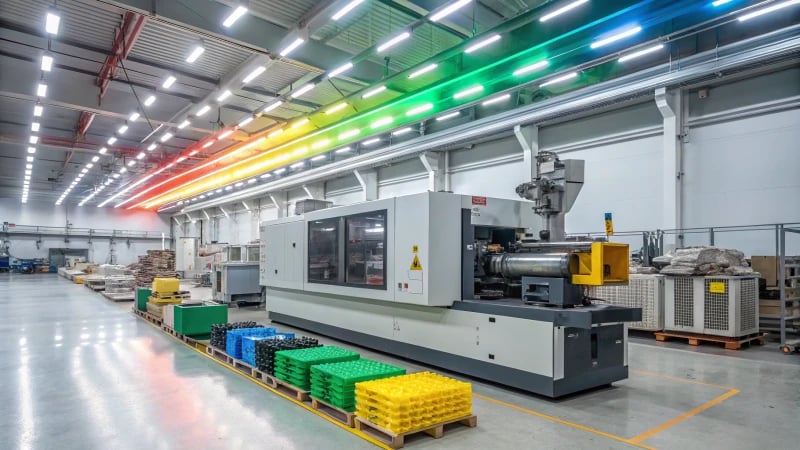
Precision and Repeatability
Imagine crafting a complex jigsaw puzzle. Each piece must fit perfectly; even the slightest deviation could ruin the entire set. Injection molding is like that master puzzle-maker, consistently delivering pieces with precise tolerances. I remember the first time I saw a perfectly molded plastic part in action, and I was amazed by the consistency across thousands of units. This precision not only ensures quality but also reduces waste.
Cost-Efficiency
I vividly recall a project where we needed thousands of units for a product launch. At first, the upfront cost of creating molds felt like a hurdle, but as production scaled up, the costs per unit plummeted. It’s like buying bulk at a grocery store—the more you buy, the less you pay per item. This efficiency is a game-changer for any large-scale production plan, helping manufacturers optimize their budget12 while keeping standards high.
Material Versatility
Choosing the right material feels like picking the perfect outfit for an event—it has to be just right for the occasion. Injection molding caters to this need by supporting a variety of materials, from thermoplastics to thermosetting polymers. This flexibility allows me and other designers to select materials that best meet the product’s needs.
Material Type | Applications |
---|---|
Thermoplastics | Consumer electronics, automotive |
Thermosets | Electrical components |
Design Flexibility
Picture this: You’re tasked with creating a revolutionary gadget that requires intricate designs and innovative features. With injection molding, these seemingly impossible designs become achievable. The process allows for complex geometries, like undercuts and threads, which can be tricky with other methods. It’s as if the design possibilities are endless.
Efficiency in Production
Speed is often of the essence. I once worked on a project where time was critical. Injection molding’s short cycle times were a lifesaver, significantly boosting productivity. Plus, automation further elevates efficiency and cuts labor costs. It’s like having a highly skilled team working round-the-clock to ensure high-volume projects are completed swiftly13, all while maintaining impeccable quality.
By leveraging these advantages, manufacturers can produce high-quality products efficiently. For those weighing injection molding against other methods, these insights are crucial in making informed decisions and planning successful projects.
Injection molding ensures consistent quality in large volumes.True
The process maintains precise tolerances, reducing waste and ensuring uniformity.
Thermosetting polymers are unsuitable for injection molding.False
Injection molding supports both thermoplastics and thermosetting polymers.
How Can Designers Optimize Products for Injection Molding?
Ever struggled to get your design just right for injection molding? Let’s explore some key strategies that can transform your product into a masterpiece.
To optimize products for injection molding, ensure consistent wall thickness, appropriate draft angles, effective rib design, and suitable material selection to enhance production speed, minimize defects, and increase product durability.
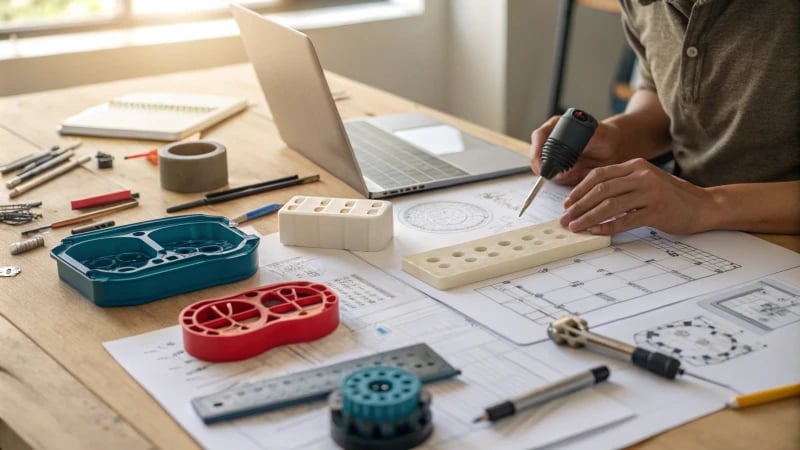
Consistent Wall Thickness
Maintaining consistent wall thickness is crucial in injection molding. Variations can lead to defects such as warping or incomplete filling. A uniform thickness ensures smoother material flow14 and reduces stress.
Aspect | Recommendation |
---|---|
Wall Thickness | 2-4 mm for most plastics |
Variance | Less than 10% of thickness |
Effective Draft Angles
Draft angles are essential for easy ejection of the part from the mold. Without proper draft, parts may stick to the mold, causing damage.
- General Rule: 1 to 2 degrees per side
- Polished Surfaces: At least 3 degrees
Draft angles facilitate better mold release15, which increases the lifespan of both the mold and the finished product.
Strategic Rib Design
Ribs enhance part strength without adding excessive material. However, improper rib design can cause issues such as sink marks.
- Height: Less than 3 times wall thickness
- Thickness: 50-60% of wall thickness
By incorporating optimal ribbing16, designers can improve structural integrity while maintaining aesthetic appeal.
Thoughtful Material Selection
Selecting the right material is pivotal. Consider factors such as strength, flexibility, and thermal resistance.
- Polypropylene: Versatile and cost-effective
- ABS: High impact resistance
Choosing the appropriate material ensures that the final product meets the required specifications17 without unnecessary complications during molding.
Designers must also evaluate environmental impacts and sustainability when selecting materials for their projects. Understanding the nuances of different materials will help optimize the production process.
By applying these strategies, designers can enhance their product designs, ensuring successful outcomes in injection molding processes. These insights not only improve efficiency but also support innovative approaches in design engineering.
Consistent wall thickness prevents warping.True
Uniform wall thickness ensures smooth material flow, reducing defects.
Draft angles are unnecessary for polished surfaces.False
Polished surfaces require at least 3 degrees draft for easy mold release.
Conclusion
Injection molding machines heat plastic, inject it into molds, and cool it to create precise parts. Key components include the injection unit, mold, and clamping unit for efficient production.
-
Learn about how hoppers contribute to efficient material feeding in injection molding. ↩
-
Discover how precise mold design impacts product quality and manufacturing efficiency. ↩
-
Explore strategies for enhancing the efficiency and quality of injection molding operations. ↩
-
Learn about how material preparation impacts final product quality and what best practices to follow. ↩
-
Explore various surface treatment techniques that enhance the durability and appearance of plastic parts. ↩
-
Discover how different materials affect the injection molding process and what adjustments may be necessary. ↩
-
Discover why ABS is a preferred choice in injection molding due to its robustness and versatility. ↩
-
Learn about polycarbonate’s applications and why it’s valued for its strength and clarity. ↩
-
Explore biodegradable materials for sustainable injection molding practices. ↩
-
Find out how using recycled plastics can cut costs and support sustainability. ↩
-
Stay updated with cutting-edge research that could transform injection molding processes. ↩
-
This link offers insights on cost savings achieved through injection molding, essential for budget-conscious manufacturing. ↩
-
Discover strategies to enhance production speed using injection molding, crucial for meeting tight deadlines efficiently. ↩
-
Explore why consistent wall thickness is critical to prevent defects like warping and ensure smooth material flow. ↩
-
Learn how proper draft angles facilitate easier ejection and increase mold lifespan. ↩
-
Discover how strategic ribbing enhances structural integrity without compromising aesthetics. ↩
-
Understand how choosing the right material affects product quality and manufacturing ease. ↩