Choosing the right runner system in injection molding can feel daunting. It’s like picking the right partner for a dance—each has its unique rhythm and advantages!
Hot runners keep plastic molten within the runner system using heating elements, leading to faster cycles and less waste. Cold runners solidify plastic, requiring removal of excess material, which can extend cycle times but reduce initial costs.
Let’s dive deeper into these systems, explore their structures, and uncover the best applications for each. Trust me; it’s worth it!
Hot runners reduce cycle times by over 20% compared to cold runners.True
Hot runners keep plastic molten, eliminating cooling time, thus speeding cycles.
How Do Hot Runners Improve Production Efficiency?
Hot runners revolutionize production efficiency by minimizing waste and reducing cycle times in injection molding.
Hot runners maintain the plastic in a molten state within the runner, enabling continuous cycles without solidifying the material, which significantly shortens molding cycles and reduces waste, enhancing overall production efficiency.
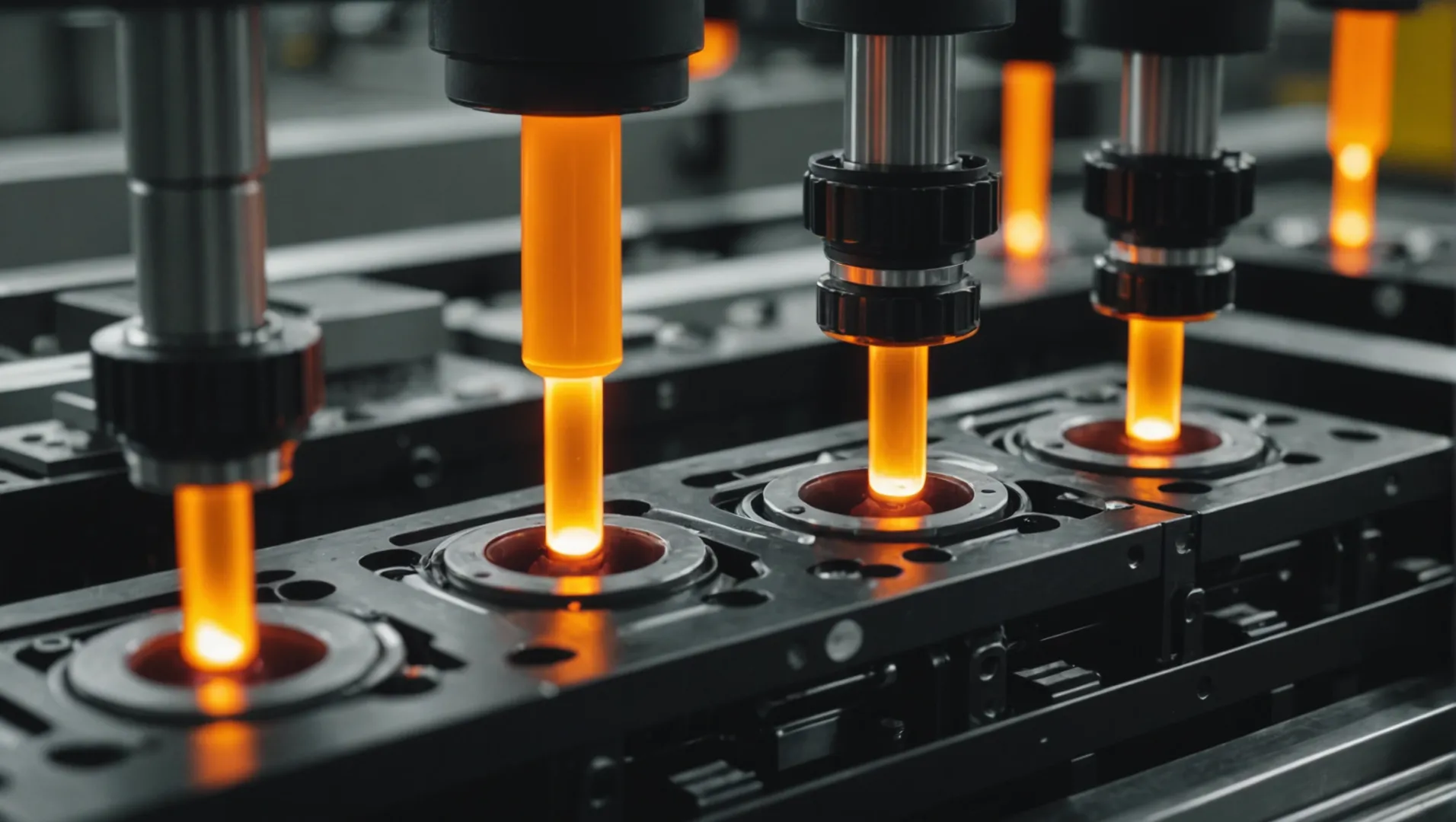
Understanding the Hot Runner System
Hot runner systems are designed to keep the plastic in the runner and gate molten, thanks to integrated heating elements like rods and rings. This allows for immediate re-use of the material when switching between cycles, eliminating the downtime typically required for cooling and reheating seen in cold runners1.
Reduced Cycle Times
The primary advantage of using hot runners is the reduction in molding cycle time. Since the plastic is maintained in a flowable state throughout the process, it eliminates the need for cooling time within the runner. Compared to cold runners, hot runner systems can decrease cycle times by over 20%, leading to significant improvements in manufacturing output.
Feature | Hot Runner | Cold Runner |
---|---|---|
Cycle Time | Shortened by 20%+ | Longer due to cooling |
Material State | Always molten | Solidifies after each cycle |
Minimization of Waste
With no runner waste generated, hot runners contribute to a more sustainable production process. By continuously reusing materials without the need for recycling, companies can significantly lower their raw material costs. This not only reduces waste but also improves long-term cost-efficiency2 and environmental sustainability.
Enhanced Product Quality
Hot runner systems also allow for precise control over temperature and fluidity of the plastic. This results in improved uniformity and dimensional accuracy of products, which is crucial for high-precision industries such as automotive and electronics manufacturing.
Application in Complex Designs
Due to their ability to manage complex flow paths and maintain consistent material conditions, hot runners enable the creation of intricate product designs. This capability is particularly beneficial when manufacturing parts that require high precision and reduced defect rates such as weld marks or bubbles.
In conclusion, while the initial investment in hot runner systems is higher, their ability to boost production efficiency, reduce waste, and enhance product quality makes them an attractive option for manufacturers aiming to optimize their processes.
Hot runners reduce cycle time by over 20%.True
Hot runners maintain plastic molten, eliminating cooling, thus reducing cycle time.
Hot runners generate more waste than cold runners.False
Hot runners minimize waste by reusing material without solidifying it.
What Are the Long-term Cost Implications of Each System?
Understanding the long-term cost implications of hot and cold runners is crucial for optimizing injection molding operations.
Hot runners, though initially costly, offer long-term savings by reducing material waste and enhancing production efficiency. Cold runners, while cheaper to start, incur higher operational costs due to increased material waste and energy consumption.
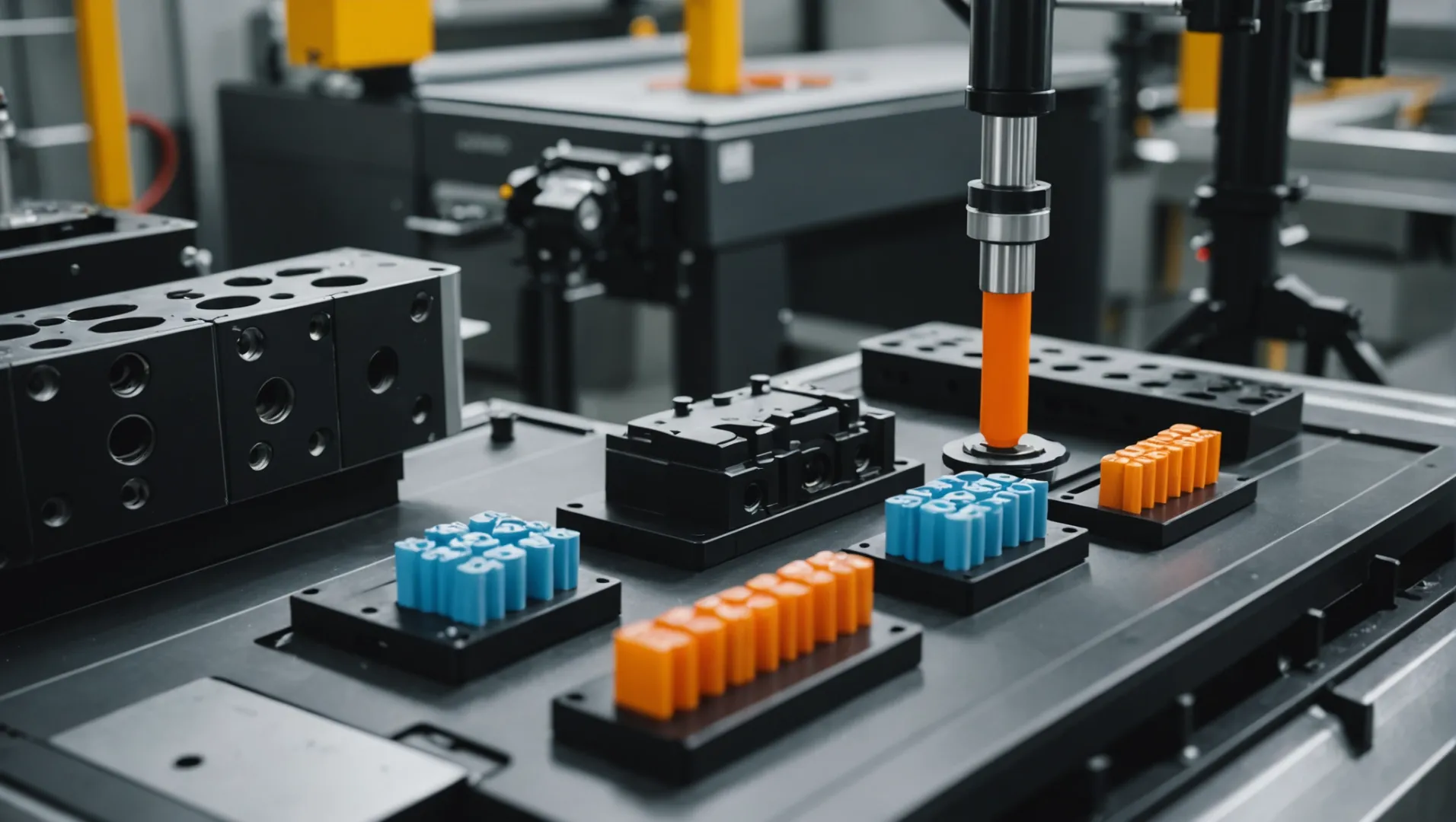
Initial Investment Costs
When considering injection molding, the initial cost is a significant factor. Hot runner systems demand a higher upfront investment due to their complex structures, requiring heating elements and precise temperature controls. For instance, a medium-level hot runner nozzle can cost several thousand yuan, and a complete system might be multiple times the cost of a basic cold runner mold.
In contrast, cold runner systems are more economical initially. They have simpler structures and do not require additional heating devices, making them attractive for projects with limited budgets or smaller production volumes.
Operating Costs Over Time
The decision between hot and cold runner systems also affects long-term operational costs. Hot runners excel in reducing material waste since they don’t produce runner condensate. This efficiency not only saves on raw material costs but also minimizes machine operating time and energy consumption due to faster production cycles.
Conversely, cold runners generate substantial runner waste. While some of this waste can be recycled, the process requires extra equipment and labor, potentially degrading the material’s performance. Additionally, longer cooling times lead to increased machine operation time and energy use.
Cost Aspect | Hot Runners | Cold Runners |
---|---|---|
Initial Investment | High due to complexity | Low due to simplicity |
Material Waste | Minimal | Significant, with recycling needs |
Energy Consumption | Reduced | Increased |
Balancing Short-term Savings with Long-term Benefits
When deciding between these systems, it’s essential to weigh short-term financial constraints against potential long-term savings. While hot runners might seem expensive initially, their ability to boost efficiency and reduce waste often results in overall cost savings over time.
For manufacturers considering smaller batches3 or those with limited initial funds, cold runners may be a viable option. However, they should be prepared for ongoing costs related to waste management and energy usage.
Understanding these factors helps manufacturers choose the most cost-effective system tailored to their specific needs and production goals.
Hot runners reduce material waste in injection molding.True
Hot runners eliminate runner condensate, minimizing material waste.
Cold runners have lower initial costs than hot runners.True
Cold runners are simpler and cheaper initially due to no heating elements.
How Do Runner Systems Impact Product Quality?
The quality of injection-molded products is heavily influenced by the choice of runner system, whether hot or cold.
Hot runners enhance product quality through precise temperature control, reducing defects and allowing complex designs. Cold runners may result in uneven cooling, leading to defects like warping.
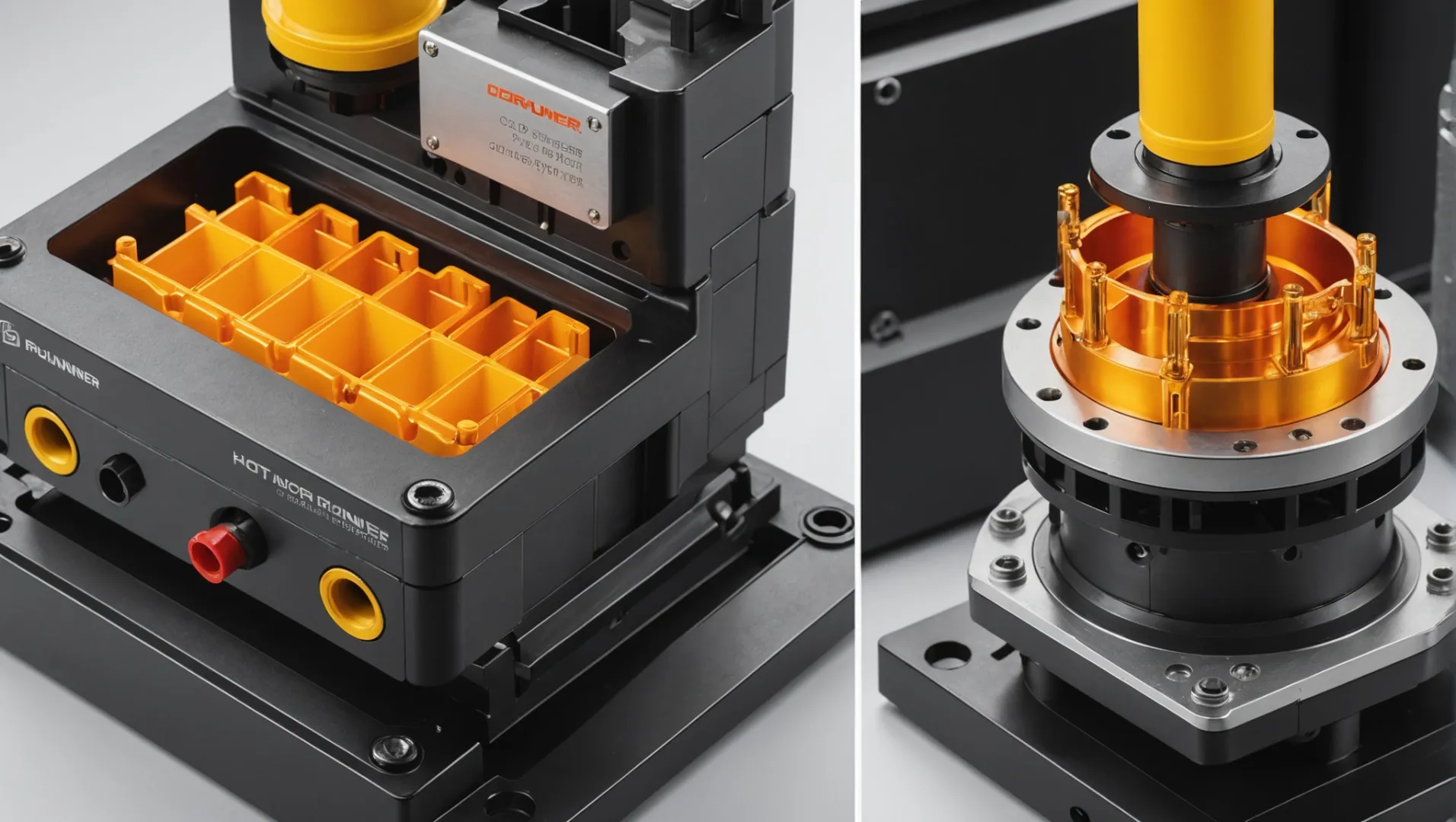
Understanding the Influence of Temperature Control
In injection molding4, the runner system’s ability to manage temperature is pivotal to product quality. Hot runners excel in this area by maintaining a consistent molten state throughout the process. This precision in temperature control allows for uniform melt flow, which is crucial for maintaining dimensional accuracy and stability. Consequently, defects such as weld lines, which occur when two flow fronts meet and fail to bond properly, are significantly reduced.
Cold runners, on the other hand, rely on ambient cooling to solidify the plastic. This can lead to uneven cooling, potentially causing issues like stress concentration and warping. These defects often require additional processing or even result in product rejection, impacting overall quality.
Material Flow and Complexity of Design
The fluidity managed by hot runners supports intricate designs. The system’s ability to consistently heat plastic ensures that it remains flowable, allowing manufacturers to create complex shapes without compromising on structural integrity. This feature is particularly advantageous for products requiring high precision or those with detailed features.
With cold runners, the design is limited by the need for thicker gates to manage the flow of material. This limitation can impact the aesthetic and functional attributes of the final product. Moreover, any adjustments to gate size or position might affect the end product’s appearance or performance negatively.
Comparing Defect Rates
Runner System | Common Defects | Impact on Quality |
---|---|---|
Hot Runner | Minimal weld lines, reduced bubbles | High dimensional accuracy and stability |
Cold Runner | Stress concentration, warping | Potential for increased defects and quality issues |
Understanding these differences is crucial for selecting the appropriate runner system based on desired product quality outcomes. Evaluating your specific manufacturing needs against these considerations can guide you toward the most suitable choice.
Hot runners improve product quality by reducing defects.True
Hot runners maintain consistent temperature, reducing defects like weld lines.
Cold runners enhance complex design capabilities in molding.False
Cold runners limit design complexity due to uneven cooling and thicker gates.
Which Runner System is Best for Your Manufacturing Needs?
Choosing the optimal runner system is crucial for efficient and cost-effective manufacturing.
Selecting between hot and cold runner systems depends on factors such as production volume, product quality requirements, and material type. Hot runners are ideal for high-volume, high-precision needs, while cold runners suit small batches and budget constraints.
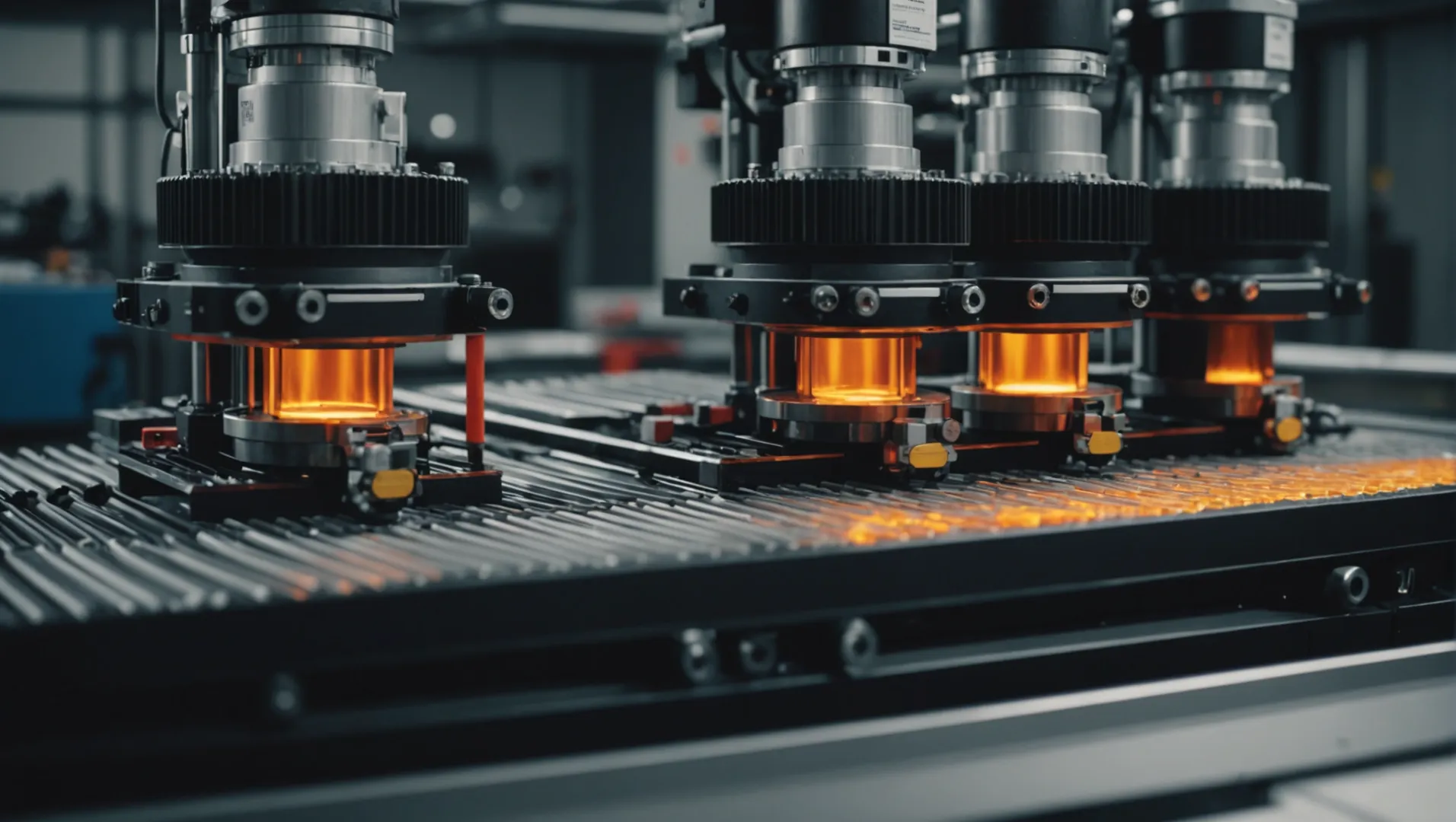
Assessing Production Volume and Cost Considerations
One of the primary factors in deciding between a hot runner5 and a cold runner system is the production volume. Hot runners, with their ability to maintain plastic in a molten state, significantly reduce cycle times, making them ideal for high-volume production. This results in greater efficiency and reduced operational costs over time. However, the initial investment is substantially higher due to the complexity and cost of heating elements and controls.
In contrast, cold runners present a lower upfront cost, making them suitable for smaller production batches or projects where budget constraints are critical. However, they incur higher operational costs over time due to waste material generation and longer cycle times.
Factor | Hot Runner | Cold Runner |
---|---|---|
Initial Cost | High | Low |
Long-term Savings | High | Low |
Cycle Time | Short | Long |
Evaluating Product Quality and Complexity
The choice of runner system also affects product quality and design complexity. Hot runners offer precise control over plastic temperature and flow, enhancing product quality by minimizing defects such as weld lines and warping. This makes them suitable for products requiring high dimensional accuracy and complex geometries.
Cold runners may pose limitations on gate positioning and size, affecting the final product’s appearance and performance. These systems are better suited for less complex products where minor quality imperfections are acceptable.
Material Compatibility and Application Scenarios
Material type is another critical consideration. Hot runners excel with high-melting-point plastics like PC or PA, ensuring consistent melt flow without cooling interruptions. However, they may struggle with materials reinforced with glass fibers due to potential blockages.
Cold runners accommodate a broader range of common plastics like polypropylene or polyethylene, making them versatile for various applications. Yet, they may falter with materials sensitive to temperature changes.
Ultimately, the decision hinges on your specific manufacturing requirements. For high precision and volume, invest in a hot runner system despite its initial cost. For cost-sensitive projects with simpler design needs, a cold runner may be more appropriate.
Hot runners reduce cycle times significantly.True
Hot runners keep plastic molten, reducing cycle times in production.
Cold runners are ideal for high-volume production.False
Cold runners suit small batches due to higher cycle times and waste.
Conclusion
Deciding between hot and cold runners involves evaluating efficiency, costs, and product requirements. This choice can dramatically enhance your manufacturing process.
-
Discover detailed distinctions between hot and cold runner systems.: Hot Runner System Advantages · Reduced cycle time: One main difference between a hot runner and cold runner injection molding is the cycle time. ↩
-
Explore how hot runners save costs over time.: Using a hot runner system saves on the cost of the unusable material. You can use our sprue cost calculator to calculate how much material costs could be saved. ↩
-
Explore why cold runners might suit smaller batch production.: In terms of their initial cost, cold runner molds are usually less expensive because they’re simpler in design and don’t require secondary equipment from a … ↩
-
Understand how temperature management influences product quality in molding.: A too hot mold causes the part to warp or blister the plastic. This leads to raised sections on the surface. Inappropriate temperature levels … ↩
-
Explore detailed advantages of hot runner systems in manufacturing.: Also, with hot runner systems, lower injection pressures can generally be used, which will reduce mold and platen deflection and keep flash … ↩