In the fast-paced world of manufacturing, where every second counts, finding ways to optimize efficiency and product quality is paramount. That’s where hot runner systems in injection molding come into play—a technology that has truly transformed production processes.
Hot runner systems in injection molding are used to maintain plastic material in a molten state, significantly improving production efficiency and product quality. They are particularly beneficial for multi-cavity molds, large parts, and complex shapes.
But there’s so much more beneath the surface! Let’s dive deeper into the specific applications and advantages that make hot runner systems indispensable in industries such as automotive and consumer goods.
Hot runner systems reduce plastic waste in molding.True
Hot runners eliminate cold runner scraps, minimizing waste significantly.
How Do Hot Runner Systems Compare to Cold Runner Systems?
Choosing between hot and cold runner systems can significantly affect the efficiency and quality of injection molding.
Hot runner systems keep plastic material molten, reducing waste and improving efficiency, while cold runner systems cool and recycle material, leading to higher waste but lower initial cost.
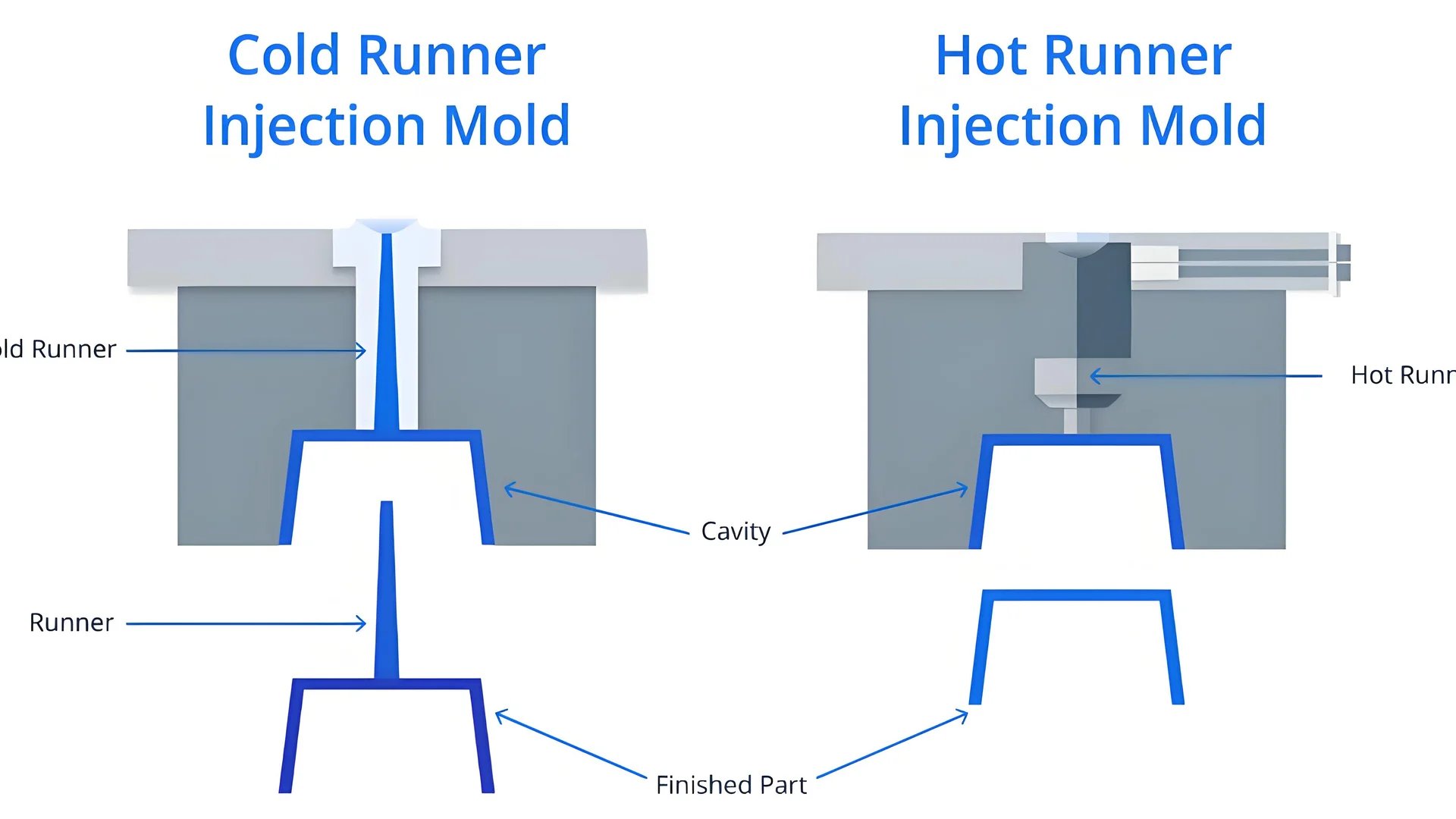
Understanding the Basics of Runner Systems
Injection molding relies on efficient runner systems to distribute molten plastic into mold cavities. These systems can be broadly categorized into hot runners and cold runners.
-
Hot Runner Systems: Designed to keep the plastic material in a molten state throughout the entire process, hot runner systems eliminate the need for runners to cool and solidify. This not only increases efficiency by reducing cycle times but also minimizes material waste.
-
Cold Runner Systems: Traditional in nature, cold runner systems allow the plastic to cool and solidify within the runner channels. Post molding, these solidified runners are ejected along with the final product and need to be trimmed and recycled if possible.
Efficiency and Cost Considerations
Aspect | Hot Runner System | Cold Runner System |
---|---|---|
Material Waste | Minimal | Higher due to solidification |
Cycle Time | Reduced | Longer due to cooling requirement |
Initial Investment | Higher | Lower |
Maintenance Cost | Moderate to high | Low |
The initial cost of implementing a hot runner system1 is generally higher due to its complex design and technology. However, it compensates by reducing material waste and shortening cycle times, which can lead to lower operational costs over time.
Quality of the Final Product
The quality of products manufactured using hot runners is often superior. They enable precise control over the temperature and flow of the plastic, leading to better filling uniformity and reduced defects such as weld lines and shrinkage marks. Cold runners, while effective, may result in inconsistencies due to cooling and solidification processes.
Suitability for Different Applications
-
Hot Runners: Ideal for multi-cavity molds, large parts like automotive components, and intricate designs where consistency and quality are paramount. They support high-volume production with minimal waste.
-
Cold Runners: Often used for smaller production runs or where the initial cost is a concern. These systems are simpler and easier to maintain, making them suitable for less complex molds.
Choosing between these systems depends on the specific needs of the production line, weighing factors like cost, efficiency, and the quality requirements of the final product.
For more insights on selecting the appropriate system for your needs, explore the benefits and drawbacks of each approach further.
Hot runner systems reduce material waste significantly.True
Hot runner systems keep material molten, eliminating solid waste.
Cold runner systems have a higher initial cost than hot runners.False
Cold runner systems have a lower initial cost due to simpler design.
What Are the Environmental Benefits of Using Hot Runner Systems?
As industries strive for sustainability, hot runner systems offer a greener alternative in injection molding, minimizing waste and conserving resources.
Hot runner systems reduce plastic waste by eliminating cold runner scraps, enhance raw material efficiency, and lower energy consumption during injection molding, contributing significantly to environmental sustainability.
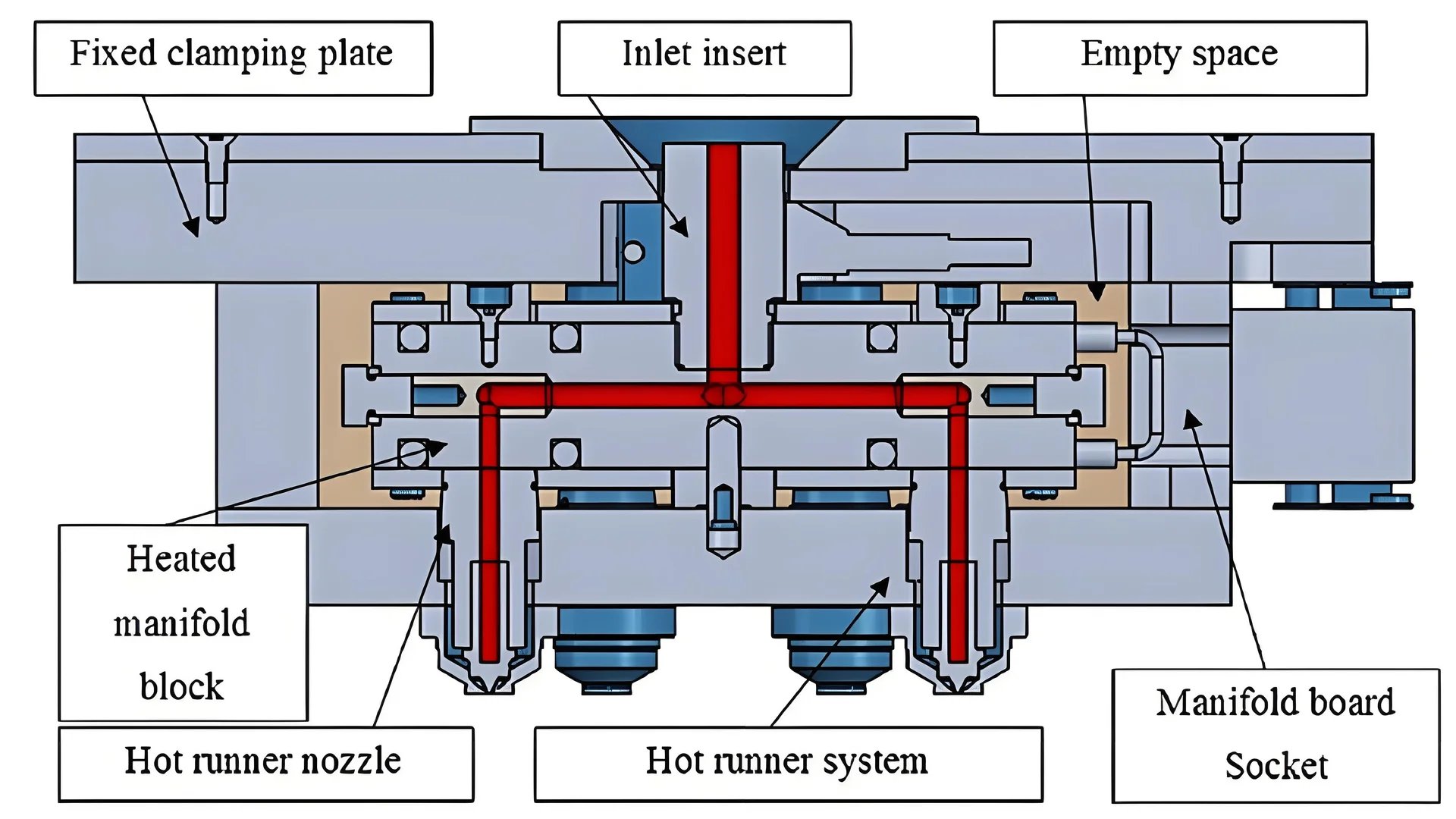
Minimizing Plastic Waste
One of the standout environmental benefits of hot runner systems is their ability to significantly reduce plastic waste. In traditional cold runner systems, excess material is often left behind in the runner after molding, which must be trimmed and discarded. This not only results in additional waste but also requires extra processing steps to manage the scraps. By maintaining the plastic in a molten state, hot runner systems eliminate the need for cold runner channels, thus preventing the generation of plastic waste entirely.
Enhanced Raw Material Utilization
Hot runner systems optimize the use of raw materials by ensuring that nearly 100% of the plastic is converted into finished products. This high level of efficiency is particularly beneficial when dealing with expensive or specialized plastics, as it reduces material costs and helps conserve resources. Additionally, since there is no excess material to recycle or dispose of, this approach reduces the carbon footprint associated with waste management processes.
Energy Efficiency and Reduced Emissions
Another environmental advantage of hot runner systems is their potential to lower energy consumption. By maintaining the melt at an optimal temperature throughout the molding process, these systems require less energy for reheating compared to traditional methods. This reduction in energy demand not only decreases operational costs but also lowers greenhouse gas emissions associated with energy production. Furthermore, by shortening the molding cycle time, hot runner systems contribute to increased production efficiency, which can lead to further energy savings.
Supporting Sustainable Manufacturing Practices
Hot runner technology supports the broader goals of sustainable manufacturing by promoting resource efficiency and reducing environmental impact. Industries focusing on sustainability initiatives are increasingly adopting hot runner systems as part of their efforts to align with green manufacturing standards. For instance, sectors like automotive and consumer electronics, which face pressure to reduce their environmental footprints, find hot runner systems invaluable for producing high-quality components while adhering to eco-friendly practices.
With such compelling environmental benefits, it’s clear why more manufacturers are turning to hot runner technology2 as a part of their sustainable production strategies. Whether it’s through waste minimization, enhanced raw material efficiency, or reduced energy usage, hot runner systems offer a viable path towards greener manufacturing solutions.
Hot runner systems eliminate cold runner scraps.True
Hot runners keep plastic molten, removing the need for cold runner channels.
Hot runner systems increase energy consumption.False
They reduce energy use by maintaining optimal melt temperature, lowering reheating needs.
How Can Hot Runner Systems Enhance Production Automation?
In the ever-evolving landscape of manufacturing, achieving seamless automation is the holy grail. Hot runner systems play a pivotal role in this quest.
Hot runner systems streamline production by eliminating waste, reducing cycle times, and enhancing quality control, making them ideal for automated manufacturing.
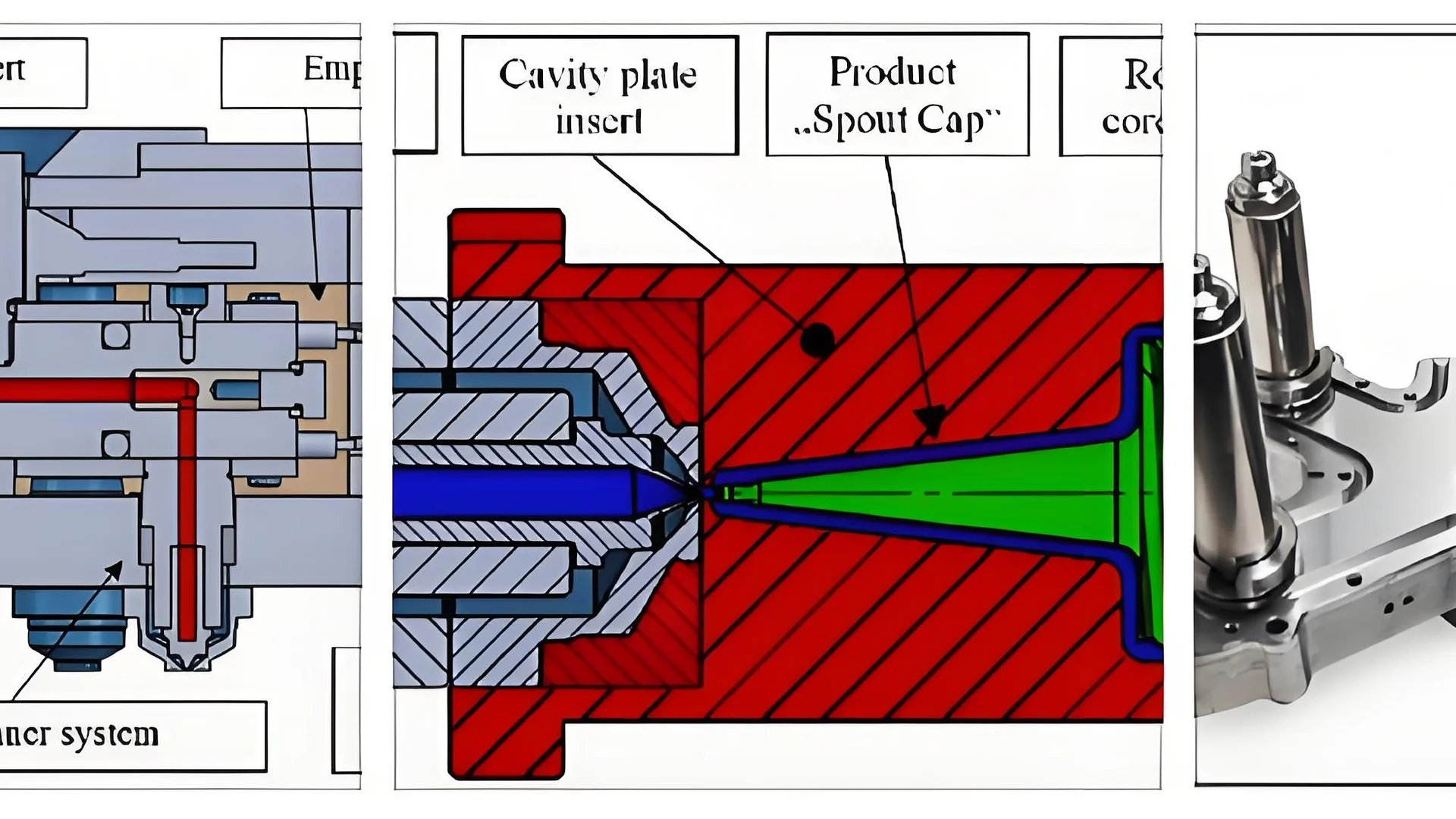
Streamlining Production Processes
Incorporating hot runner systems into automated production lines3 can significantly enhance efficiency. By maintaining the plastic in a molten state, these systems remove the need for cooling and reheating between cycles, thus shortening the overall production time. This characteristic is particularly beneficial in high-speed manufacturing environments where every second counts.
Moreover, hot runner systems eliminate the waste associated with cold runners, which not only reduces the need for manual handling of excess material but also minimizes interruptions in automated lines. This leads to smoother operations and less downtime.
Enhancing Quality Control
Hot runner systems offer precise temperature control, ensuring uniform melt flow and reducing defects such as shrinkage or weld lines. This uniformity is crucial in automated quality assurance processes4, where consistent product quality can be monitored and maintained without manual intervention. The enhanced control translates into fewer rejects and less need for human oversight.
Additionally, the improved flow characteristics mean that parts can be designed with more complex geometries without compromising on quality, opening up new possibilities for automation in design and manufacturing.
Facilitating Easy Integration with Robotics
The use of hot runner systems facilitates easier integration with robotic systems. As finished products emerge without needing trimming or additional post-processing, robotic arms can seamlessly handle these parts for further assembly or packaging. This integration is essential for smart factories5 aiming to maximize throughput and efficiency.
In multi-cavity mold applications, robots can swiftly sort and manage parts, ensuring that the production line remains uninterrupted and efficiently organized.
Reducing Energy Consumption
Hot runner systems contribute to a more sustainable production process by reducing energy consumption. Without the need to re-melt solidified runners, the energy usage is drastically reduced, aligning with the goals of energy-efficient manufacturing6. This reduction not only cuts operational costs but also supports environmental sustainability initiatives within automated facilities.
Hot runner systems reduce cycle times in manufacturing.True
They eliminate cooling and reheating, speeding up production.
Hot runner systems increase waste in automated processes.False
They reduce waste by eliminating cold runners, minimizing excess material.
What Challenges Might Arise with Hot Runner System Implementation?
Implementing hot runner systems can transform production efficiency, yet it comes with its own set of challenges.
Hot runner system implementation challenges include high initial costs, complex maintenance, and technical expertise requirements. These systems demand precise temperature control and can be difficult to retrofit into existing molds.
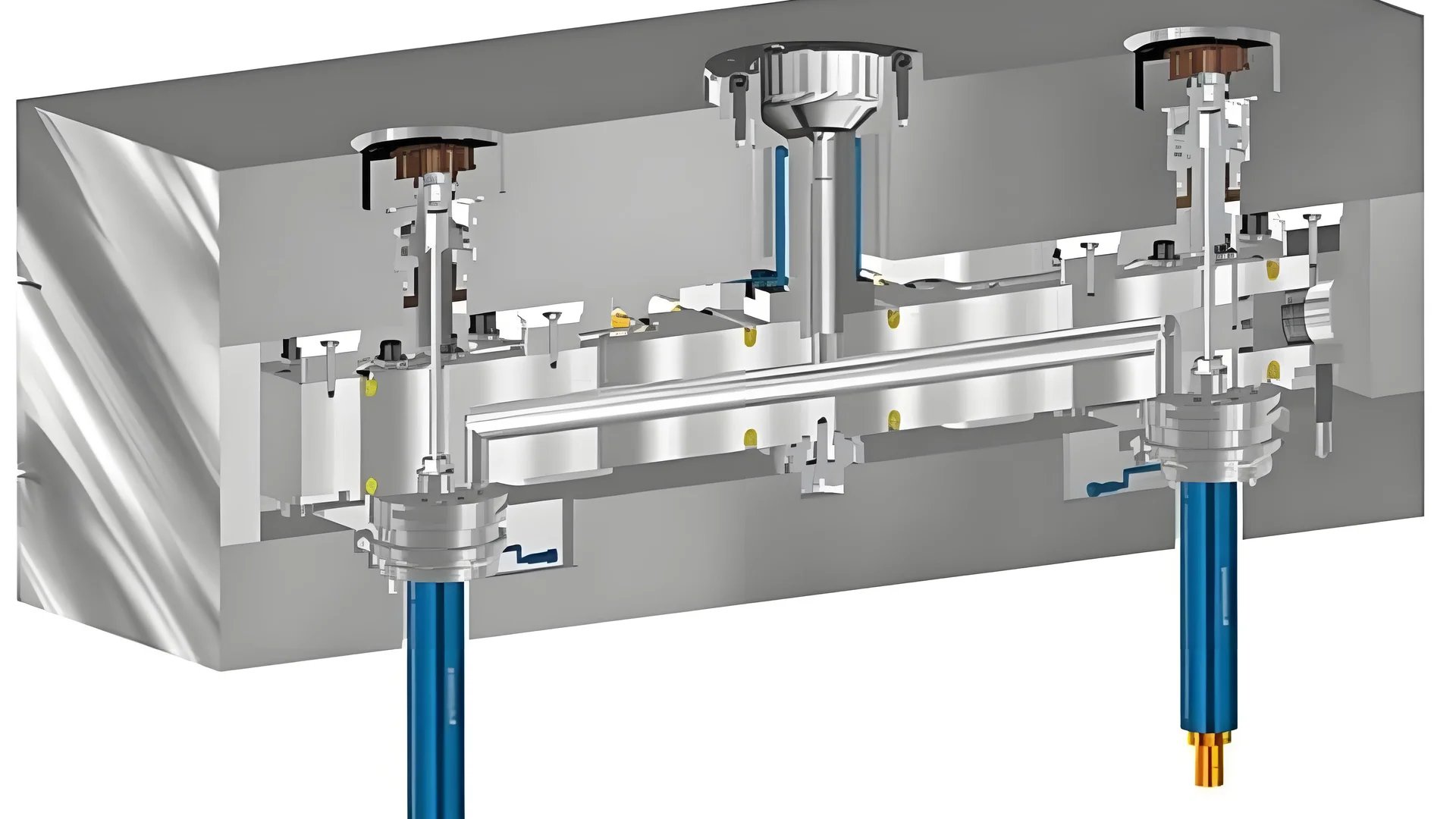
High Initial Investment
One of the primary challenges faced by manufacturers is the high initial cost associated with hot runner system implementation7. The design and components such as temperature controllers, manifolds, and nozzles are costly. This investment can be daunting for small to medium enterprises that may not have substantial capital reserves.
Complex Maintenance Needs
Maintenance of hot runner systems is more intricate compared to traditional cold runners. These systems require regular monitoring to ensure optimal performance and to prevent issues such as leaks or blockages. Any failure in components could lead to significant production downtime, impacting efficiency and increasing costs.
To maintain these systems, technicians need specialized training, which can be an additional cost burden. Regularly scheduled maintenance and the need for specialized skills can deter companies from adopting this technology.
Technical Expertise Required
Implementing a hot runner system isn’t just about installing new equipment; it involves a comprehensive understanding of the technology. Skilled personnel are required to manage the system’s operation effectively. This includes adjusting settings for precise temperature control, managing the melt flow, and troubleshooting any issues that arise.
The complexity increases further when integrating these systems into existing manufacturing setups, as retrofitting might require substantial redesigns or modifications to the mold structure.
Precision Temperature Control Challenges
One of the pivotal advantages of hot runner systems is precise temperature control, which ensures uniformity in product quality. However, achieving and maintaining this precision can be challenging. Fluctuations in temperature can lead to defects such as warping or incomplete filling. Thus, consistent monitoring and fine-tuning are essential to meet the desired outcomes.
Implementing hot runner systems poses several challenges, including cost and technical demands. While they offer remarkable benefits in terms of efficiency and product quality, addressing these challenges requires careful planning and investment in skilled personnel and equipment.
By weighing these factors, companies can better prepare for successful hot runner system integration8.
High initial costs deter small manufacturers.True
Small manufacturers often lack the capital for expensive hot runner systems.
Hot runner systems require no maintenance.False
These systems demand regular monitoring and maintenance to function properly.
Conclusion
In conclusion, embracing hot runner systems can lead to transformative improvements in manufacturing processes, fostering innovation and sustainability.
-
Explore a detailed comparison between hot and cold runner systems.: Internally heated systems offer better flow control. The hot runner process eliminates runners entirely, so recycling and regrind (which can only be done with … ↩
-
Explore how hot runners minimize waste and improve sustainability.: By embracing hot runner technology, manufacturers can reduce waste, conserve resources, and minimize their environmental footprint while … ↩
-
Discover how hot runners enhance efficiency in high-speed manufacturing.: While both hot runner and cold runner systems have their benefits, for design flexibility as well as reduced cycle times and costs, hot runner … ↩
-
Learn about maintaining consistent quality with automated processes.: A research project is exploring new avenues for AI-assisted automated optical quality assurance during the injection molding process. ↩
-
Explore how robotics and hot runners work together seamlessly.: A robot can lift a moulded part out of one injection moulding machine and place it into another for the over-moulding process. This reduces labour and assembly … ↩
-
Understand how hot runners contribute to energy savings.: We use innovative hot runner technologies to develop modern, thermally insulated gate point systems. Our hot runners achieve highly efficient runner injection … ↩
-
Discover the financial implications before investing in hot runner systems.: The initial cost of hot runner systems is high, which can make them uneconomical for small-batch production. However, for mass production, hot … ↩
-
Learn strategies for overcoming common implementation hurdles.: A proper hot runner design is the key element to successfully produce a good quality plastic injection molding part with minimized cost. ↩