Choosing the right hot runner system can feel overwhelming, but it doesn’t have to be!
To choose the right hot runner system, consider the product’s material type, size, and precision requirements, as well as mold design and production demands. This ensures efficient production and high-quality output tailored to specific manufacturing needs.
This guide will walk you through each critical factor, providing insights from industry experts that could transform your manufacturing process.
Mold design affects hot runner selection.True
Mold design dictates the structural type, cavity layout, and cooling needs.
What Are the Key Product Characteristics to Consider?
Understanding the characteristics of your product is crucial when selecting a hot runner system. Factors such as material type, size, and precision needs play a pivotal role in ensuring efficient production and top-notch quality.
Key product characteristics to consider include plastic material properties, product size and weight, and accuracy requirements. These factors determine the appropriate hot runner system needed to ensure optimal manufacturing performance and quality outcomes.
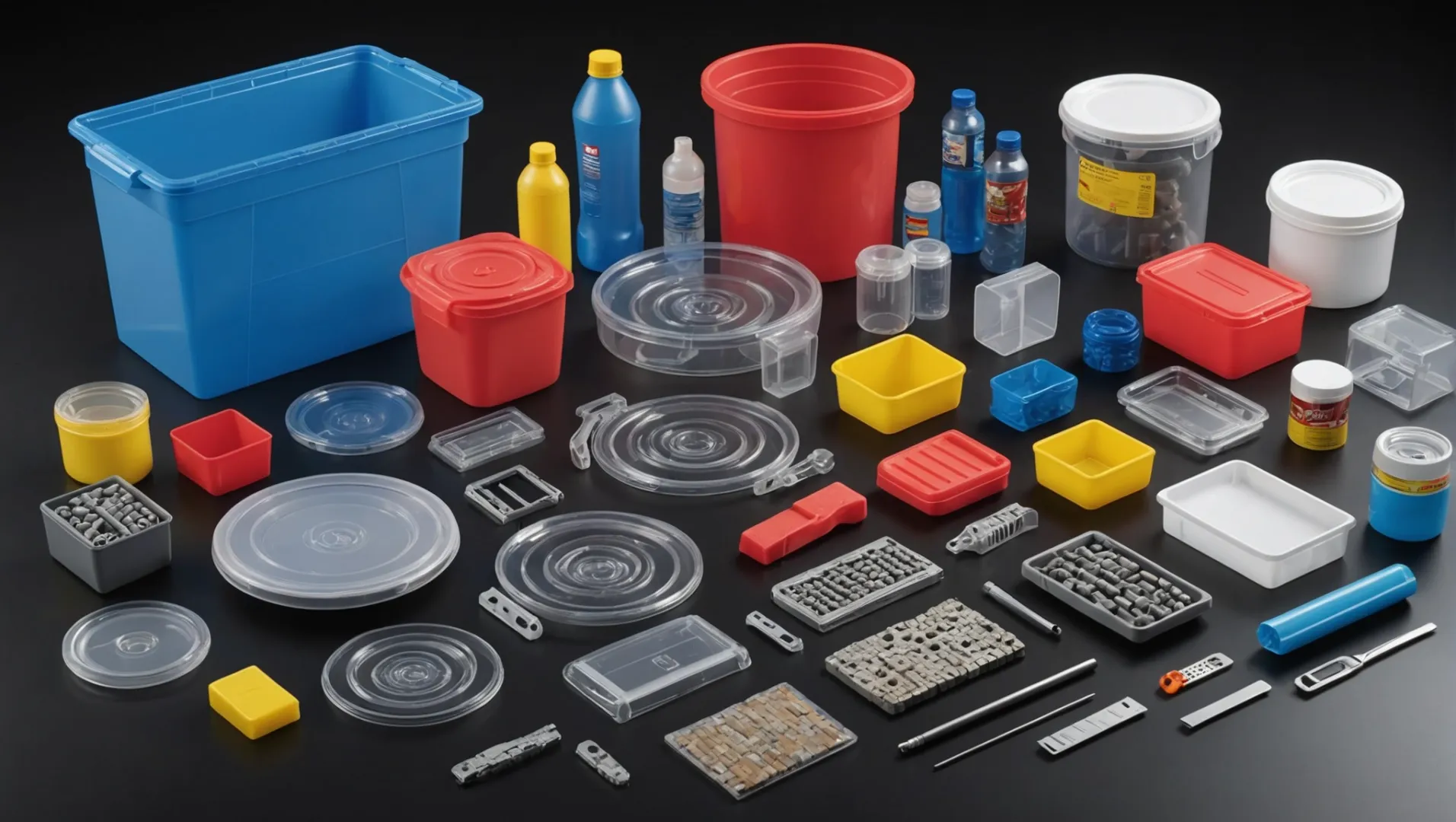
Evaluating Plastic Material Properties
The choice of plastic material significantly influences the selection of a hot runner system. Different plastics exhibit varying fluidity, thermal sensitivity, and processing temperature ranges. For instance, engineering plastics with poor fluidity may necessitate a hot runner system with larger gate sizes and higher injection pressures to achieve smooth mold cavity filling. In contrast, heat-sensitive materials like polycarbonate (PC) require precise temperature control to prevent material degradation.
Additionally, understanding the shrinkage rate of the plastic is vital, as it affects dimensional accuracy. Some advanced hot runner systems can adjust temperature and pressure to compensate for plastic shrinkage, thereby enhancing product quality.
Considering Product Size and Weight
The size and weight of the product determine the injection volume and the number of gates required in a hot runner system. Large products often need multiple gates and larger nozzles to ensure even mold cavity filling. Conversely, smaller products benefit from smaller systems that reduce costs and increase efficiency.
Wall thickness is another critical factor. Thin-walled products demand a hot runner system with fast response times and precise temperature control to avoid defects like short shots or flow marks.
Meeting Product Accuracy Requirements
For products with high demands for dimensional accuracy and surface quality, selecting a hot runner system with high-precision temperature control is essential. Systems capable of maintaining temperature control accuracy within ±0.5℃ ensure consistent product stability and appearance.
Special appearance requirements, such as transparency or high gloss, necessitate hot runner systems that minimize defects like flow marks or air marks. These characteristics are especially important in industries where aesthetics play a significant role in product value.
In summary, understanding these key product characteristics1 helps in choosing a suitable hot runner system that aligns with manufacturing goals and product specifications. Each factor—from material properties to product dimensions—plays a role in ensuring successful production outcomes.
Engineering plastics need larger gate sizes.True
Due to poor fluidity, engineering plastics require larger gates for smooth mold filling.
Thin-walled products require slower response times.False
Thin-walled products need fast response times to avoid defects like short shots.
How Does Mold Design Influence Hot Runner Selection?
The design of a mold plays a pivotal role in selecting the right hot runner system. It impacts efficiency, product quality, and cost.
Mold design affects hot runner selection by determining structural type, cavity layout, size, weight, and cooling requirements. Each aspect influences the choice to ensure optimal performance and compatibility with production needs.
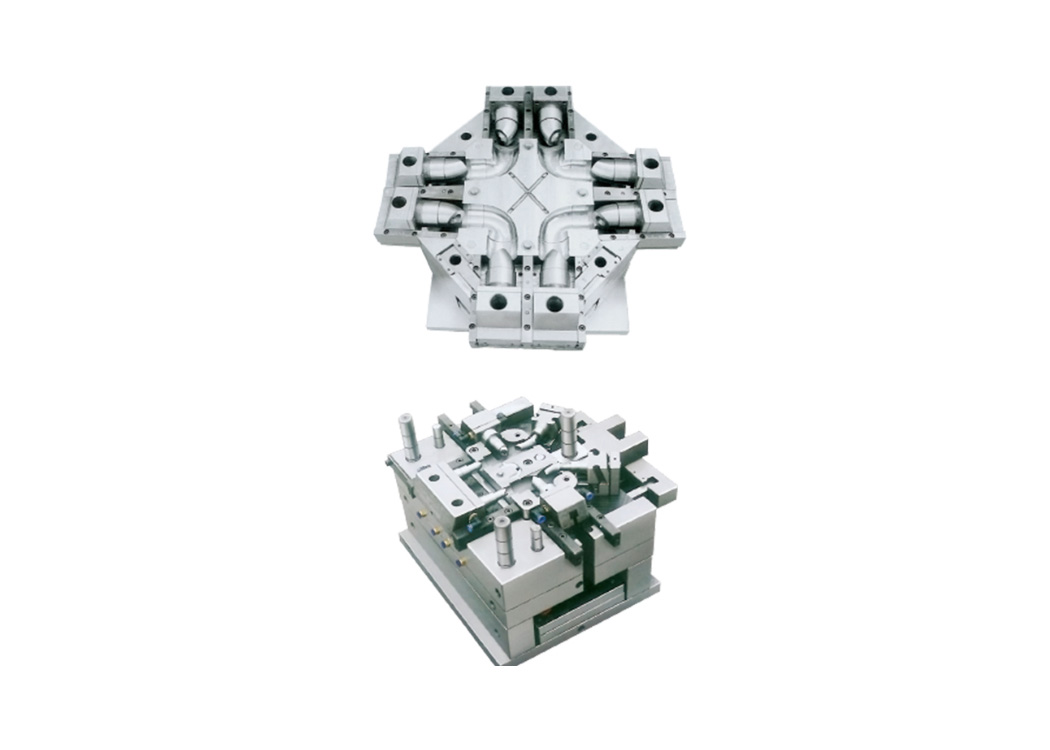
Understanding Mold Structure’s Impact
The mold structure2 is a primary factor in hot runner selection. For instance, a two-plate mold might suit a simple hot runner system, while a three-plate mold often requires a needle valve system to facilitate automatic gate cutting. This avoids leaving gate marks on the product surface, crucial for aesthetic finishes.
Moreover, the cavity layout significantly influences system design. A mold with many cavities or uneven distribution may demand a multi-point hot runner system to ensure even filling. This is particularly important for maintaining consistency across products and reducing material waste.
The Role of Mold Size and Weight
Mold size and weight are other critical considerations. Larger molds need robust hot runner systems that provide sufficient injection pressure and flow. They must also account for the weight of the hot runner system itself, as it impacts the mold’s operational stability and safety.
Example Table: Mold Characteristics vs. Hot Runner Requirements
Mold Feature | Hot Runner Requirement |
---|---|
Large Size | High pressure system |
Heavy Weight | Reinforced stability |
Multiple Cavities | Multi-point system |
Integrating Cooling Systems
Compatibility with the mold’s cooling system is essential for efficient production. The hot runner must work in tandem with cooling elements to ensure uniform plastic cooling within the cavity. Advanced systems incorporate heat insulation plates and heating rods to minimize heat transfer to the mold, enhancing cooling efficiency.
Considering these aspects ensures the selected hot runner system optimally supports the mold design, contributing to higher production efficiency and better product quality.
Two-plate molds suit simple hot runner systems.True
Two-plate molds often use simpler systems due to fewer components.
Large molds require low-pressure hot runner systems.False
Large molds need high pressure for adequate material flow.
Why Are Production Requirements Crucial in Your Decision?
Understanding production requirements is essential when selecting a hot runner system, as it directly influences efficiency, costs, and product quality.
Production requirements are crucial because they determine the hot runner system’s reliability, speed, and automation level needed for efficient manufacturing. These requirements guide the selection of systems that meet specific batch sizes, cycle times, and automation needs, ensuring seamless integration into existing workflows.
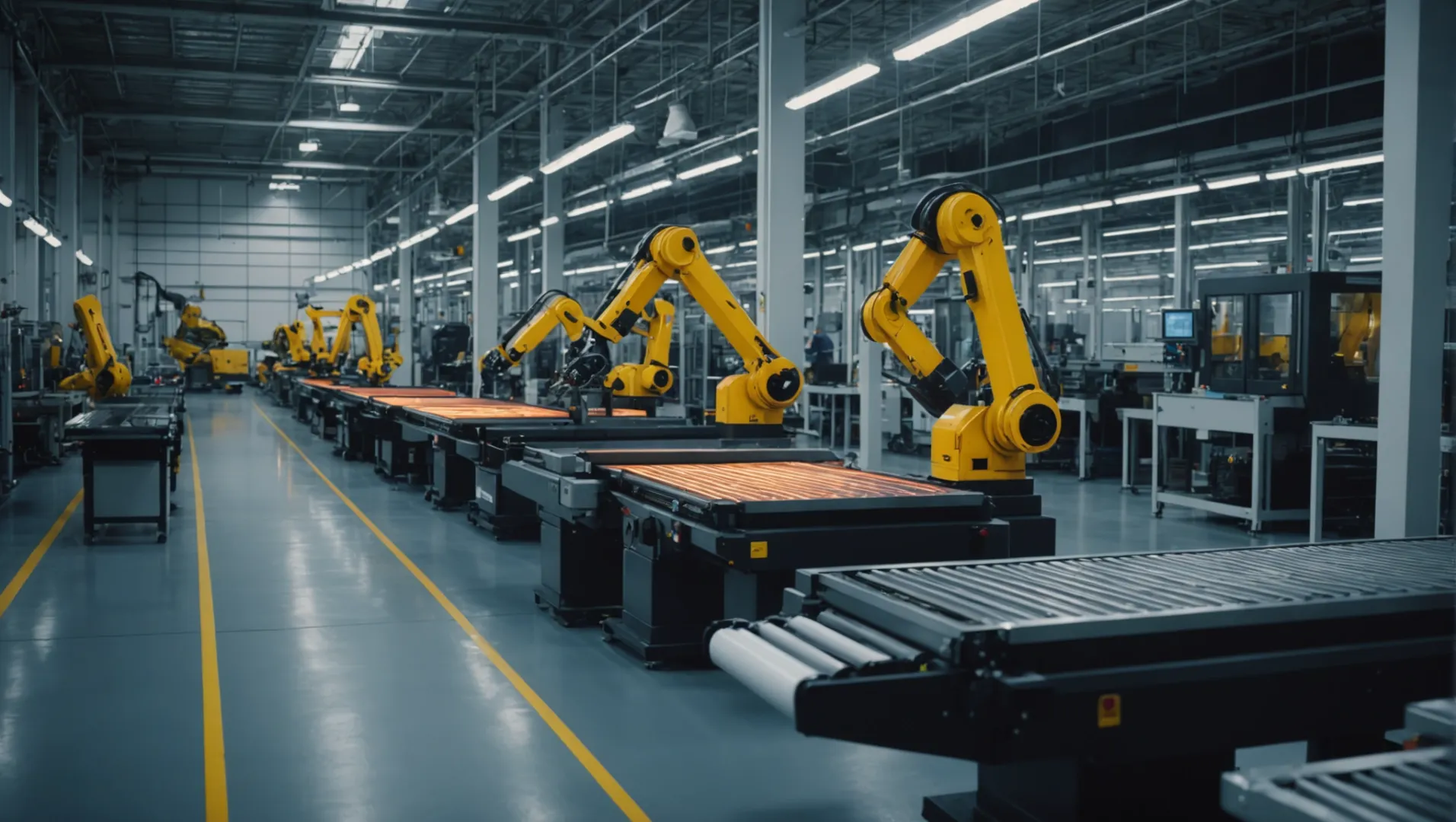
Analyzing Production Batch Size and System Reliability
The size of your production batch can significantly impact the choice of a hot runner system. For large-scale productions, a system with high reliability and low maintenance costs becomes essential. High-end systems often offer long-term continuous operation capabilities, reducing downtime and enhancing production efficiency3. Conversely, for smaller batches, a more cost-effective system might suffice, allowing you to balance quality and budget effectively.
Understanding the Production Cycle Time
When dealing with short production cycles, the speed of the hot runner system is pivotal. Systems with quick response times and rapid color changes can drastically reduce cycle times. Advanced models can switch colors in mere minutes, thus boosting throughput. It’s also vital to factor in heating and cooling times to ensure the system matches the desired cycle pace.
Considering the Degree of Automation
A highly automated production process demands a compatible hot runner system. Many modern systems can integrate seamlessly with automated equipment through sensors and controllers for temperature control and process monitoring. This level of integration not only enhances productivity but also minimizes human intervention, thus reducing errors and improving consistency4.
Balancing Costs with Performance
While cost is always a consideration, it should not overshadow performance and quality. Evaluating the total cost of ownership, including maintenance and operation expenses, can provide a clearer picture of the system’s value over time. Opt for systems offering the best cost-performance ratio5 to ensure long-term benefits without compromising on quality or reliability.
Hot runner systems reduce production cycle times.True
Advanced hot runner systems can switch colors quickly, boosting throughput.
Automation decreases errors in hot runner systems.True
Automated systems minimize human intervention, reducing errors and improving consistency.
What Should You Look for in a Hot Runner Supplier?
Choosing the right hot runner supplier is vital to ensuring quality, efficiency, and reliability in your manufacturing processes. Here’s what to consider.
When selecting a hot runner supplier, prioritize reputation, experience, technical support, and cost-effectiveness. These factors ensure reliable performance and strong after-sales service, ultimately leading to smoother production operations and enhanced product quality.
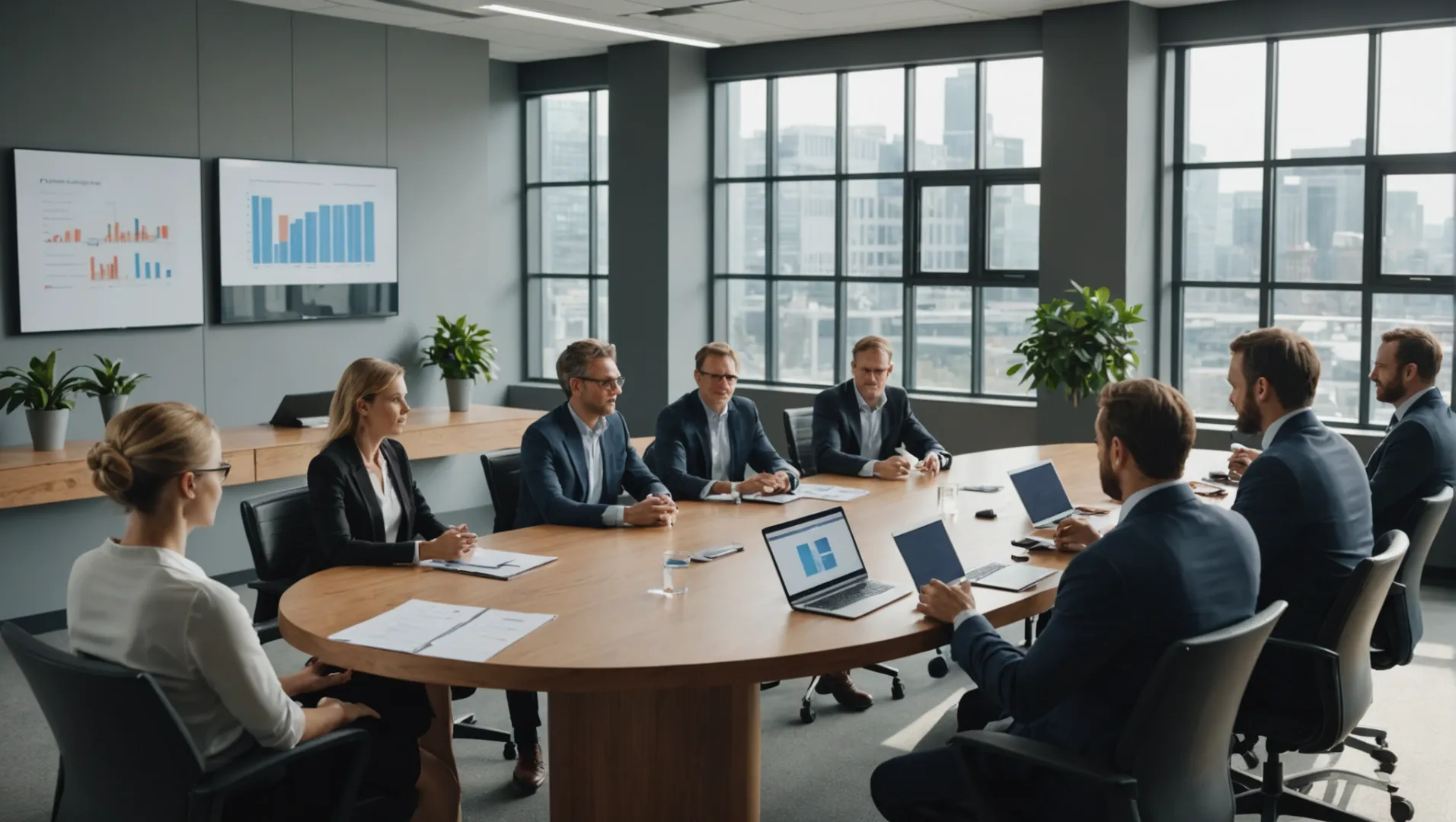
Evaluating Supplier Reputation and Experience
A supplier’s reputation and experience6 are paramount when selecting a hot runner system. Renowned suppliers often have a history of delivering quality products and reliable systems. To gauge this:
- Check Qualifications: Look for industry certifications and qualifications that attest to their expertise.
- Customer Reviews: Analyze feedback from other users to understand the supplier’s reliability.
Importance of Technical Support and After-Sales Service
Technical support is essential for addressing issues that arise during the hot runner system’s operation. A good supplier should offer:
- Timely Responses: Ensure they have a dedicated team for prompt troubleshooting.
- Comprehensive Maintenance: Look into their maintenance services to minimize downtime.
- Training and Guidance: Opt for suppliers who provide training sessions to help your team utilize the system efficiently.
Assessing Price and Cost-Effectiveness
While cost is a significant factor, it should not overshadow quality. Balancing price with performance7 is crucial:
- Quality vs. Cost: High-quality systems might have a higher upfront cost but save money in the long run through reduced maintenance needs.
- Cost Performance Ratio: Consider the overall performance benefits versus the price to ensure value for money.
Supplier’s Innovation and Adaptability
In a fast-evolving industry, a supplier’s ability to innovate and adapt is invaluable:
- Research & Development: Choose suppliers investing in R&D for more advanced, efficient systems.
- Customization Options: Seek suppliers offering systems that can be tailored to specific production requirements.
Considering these aspects will guide you in selecting a supplier who not only meets your current needs but also supports your future growth and innovation ambitions.
Reputation is key in selecting a hot runner supplier.True
A supplier's reputation indicates their history of delivering quality systems.
Cost should be prioritized over quality in hot runner systems.False
Balancing cost with quality ensures long-term savings and reliability.
Conclusion
Taking the time to select a hot runner system that meets your specific needs can greatly enhance your production efficiency and product quality. Reflect on these key factors to make a choice that aligns with your goals.
-
Explores how product traits influence hot runner system choice.: The type, size, and weight of plastic molded parts produced by hot runners are wider, which is more conducive to optimizing the plastic moulding in Bangalore … ↩
-
Understand how different mold structures affect hot runner choices.: Hot runner molds consist of two plates that are heated with a manifold system. The manifold helps maintain a consistent temperature by keeping the molten … ↩
-
Explore strategies to enhance efficiency in manufacturing processes.: High production efficiency can lead to significant cost savings and improved profitability. Manufacturers who master it not only optimize their … ↩
-
Discover methods to ensure consistent output in manufacturing.: How to Improve Manufacturing Efficiency · 1. Don’t Waste Material · 2. Improve Training · 3. Quantify Everything · 4. Organize Everything · 5. ↩
-
Learn how to assess cost versus performance in manufacturing systems.: The price–performance ratio is often written as cost–performance, cost–benefit or capability/price (C/P), refers to a product’s ability to deliver performance. ↩
-
Learn methods to assess a supplier’s reputation effectively.: Previous Experiences – you will always hear both horror stories and stories of stellar performance about any given hot runner supplier. Often … ↩
-
Understand why balancing cost and quality is crucial.: Material savings, reduced production costs, and improved efficiency lead to significant cost savings over the lifecycle of a project. ↩