In the world of injection molding, precision and quality are paramount.
Holding time in injection molding is the period during which pressure is maintained after injection to compact the melt and compensate for shrinkage, directly impacting product quality by ensuring dimensional accuracy and preventing defects.
While holding time is just one aspect of the injection molding process, its impact on quality cannot be overstated. This article delves into the nuances of how holding time affects product characteristics and offers insights into optimizing it for better results.
Holding time prevents shrinkage marks in molded parts.True
By maintaining pressure, holding time compensates for shrinkage, reducing marks.
What is Holding Time in Injection Molding?
Delve into the pivotal role of holding time in shaping quality injection-molded products.
In injection molding, holding time is the period after injection when pressure is maintained to compact the melt and compensate for shrinkage, ensuring product quality by preventing defects.
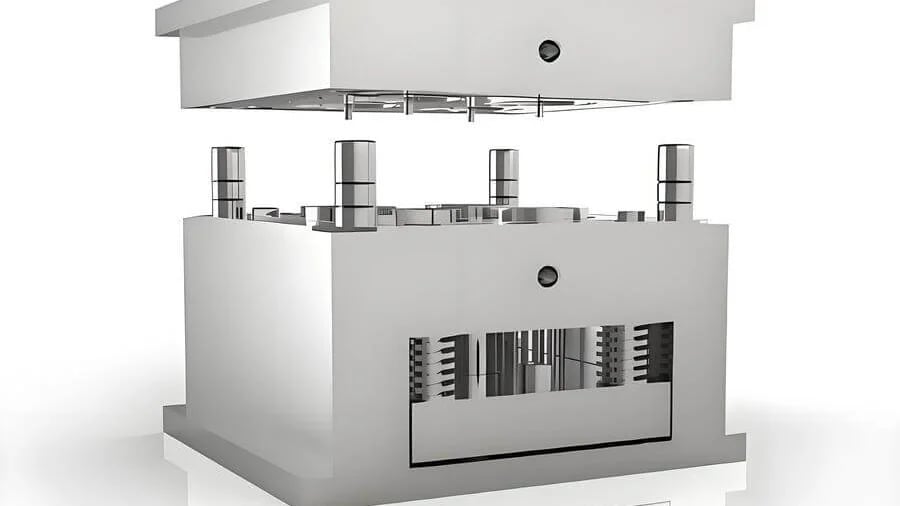
Understanding Holding Time in Injection Molding
Injection molding is a complex process where each phase significantly influences the final product quality. Holding time refers to the duration during which the injection molding machine maintains a specific pressure after the initial injection phase. This stage is critical for ensuring that the molten material in the mold cavity is properly compacted and any shrinkage during cooling is compensated.
Functions of Holding Time
1. Compensation for Shrinkage:
During cooling, the plastic melt tends to shrink, which can lead to defects like shrinkage marks or holes. By maintaining pressure during the holding phase, these defects can be minimized as the material remains compacted. Compensation mechanisms1 are crucial for ensuring the integrity of the final product.
2. Enhancement of Product Quality:
The right holding time ensures dimensional accuracy and improves surface quality. This occurs as the pressure reduces internal voids and stress concentrations within the plastic parts. This compaction leads to more robust and reliable components, vital in industries where precision is paramount.
3. Process Stabilization:
By correctly setting the holding time, manufacturers can stabilize their production processes. A consistent holding time reduces scrap rates and enhances production efficiency by minimizing variability in product outcomes.
Factors Affecting Holding Time
Several factors influence how long the holding time should be set:
- Material Properties: Plastics with different fluidities require varying holding times.
- Part Design: Larger or more complex parts often need longer holding periods.
- Mold Temperature: The temperature can alter how quickly the material cools and solidifies.
- Injection Pressure: Higher pressures may reduce the required holding time.
For instance, plastics with high shrinkage rates may demand longer holding times to compensate for their tendency to contract during cooling. Conversely, materials with excellent fluidity may not need as long a duration under pressure.
In practice, determining the optimal holding time2 requires experimentation and adjustments based on specific production conditions. Manufacturing teams often use trial-and-error methods to fine-tune this parameter, achieving a balance between efficiency and product integrity.
Holding time compensates for plastic shrinkage.True
Holding time maintains pressure to compact melt, minimizing shrinkage.
Higher injection pressure increases holding time needed.False
Higher pressures may reduce the required holding time.
Why is Shrinkage Compensation Crucial in Injection Molding?
Understanding shrinkage compensation is vital for achieving precision in injection molding.
Shrinkage compensation in injection molding ensures products maintain their intended dimensions and quality by addressing the natural reduction in volume that occurs as plastic cools and solidifies.
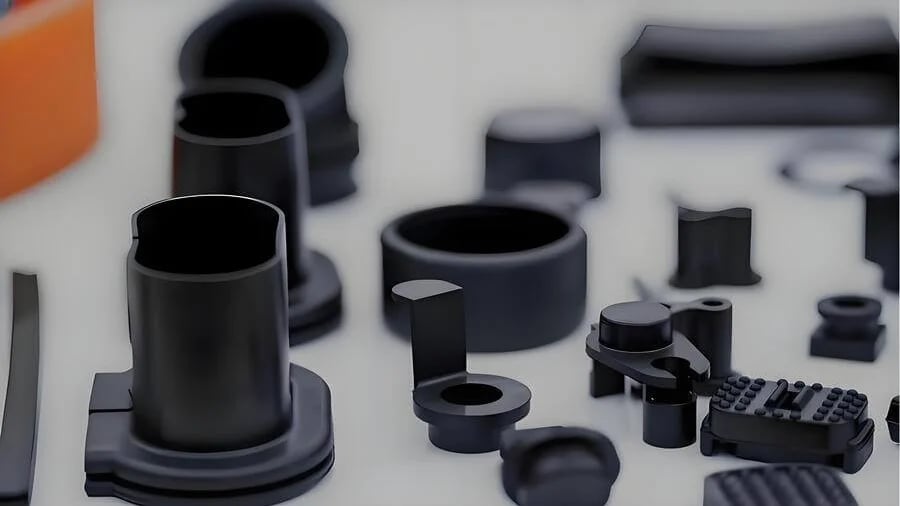
Understanding Shrinkage in Injection Molding
During the injection molding process, molten plastic is injected into a mold cavity. As it cools, the plastic undergoes a natural reduction in volume, known as shrinkage. This phenomenon can lead to defects such as shrinkage marks and voids if not properly managed. Shrinkage management3 becomes crucial to maintain the integrity of the final product.
The Role of Holding Time
Holding time is the duration for which pressure is applied after the initial injection. It plays a pivotal role in shrinkage compensation by allowing additional material to fill any voids created by cooling shrinkage. This step ensures that the final product maintains its intended shape and dimensional accuracy.
Benefits of Proper Shrinkage Compensation
- Prevention of Defects: By compensating for shrinkage, manufacturers can prevent common defects such as sink marks and voids, which affect both aesthetics and functionality.
- Improved Dimensional Accuracy: Proper shrinkage compensation contributes to maintaining the tight tolerances required in many precision applications.
- Enhanced Surface Quality: Ensuring uniform pressure during holding time can lead to smoother surfaces and better overall quality of the plastic parts.
Factors Affecting Shrinkage Compensation
Several factors influence how effectively shrinkage can be compensated:
- Material Properties: Different plastics exhibit varying shrinkage rates. Materials with higher shrinkage require more careful management.
- Part Geometry: Complex shapes may need adjusted holding times to ensure even pressure distribution.
- Mold Temperature: Higher mold temperatures can influence the cooling rate and thus affect shrinkage dynamics.
To optimize shrinkage compensation4, manufacturers must carefully balance these variables through rigorous testing and precise adjustments in their production processes. This ensures consistency and quality across batches, making it an essential aspect of high-quality injection molding.
Holding time reduces shrinkage in injection molding.True
Holding time allows extra material to fill voids from cooling shrinkage.
Shrinkage compensation is unnecessary for dimensional accuracy.False
Proper compensation is crucial to maintain tight tolerances and accuracy.
How Does Holding Time Affect Dimensional Accuracy?
Precision in injection molding hinges on understanding factors like holding time, which affects dimensional accuracy.
Holding time impacts dimensional accuracy by maintaining pressure to counteract shrinkage and voids in molded parts.

The Role of Holding Time in Dimensional Accuracy
In injection molding, holding time is crucial for maintaining the pressure required to ensure the plastic melt compensates for shrinkage as it cools. This pressure compaction is essential for achieving high dimensional accuracy5 in the final product. Without adequate holding time, the material may contract unevenly, leading to defects such as shrinkage marks or voids that detract from precision.
How Shrinkage Affects Accuracy
Shrinkage is an inherent part of the cooling process for plastic materials. As the melt cools, it contracts, which can cause variations in the final dimensions if not properly managed. By applying the correct holding time, manufacturers can compensate for this shrinkage, ensuring the dimensions remain consistent with design specifications.
Balancing Pressure and Time
Finding the right balance between pressure and holding time is critical. Too little time can result in incomplete compaction, while excessive time may lead to other issues like increased cycle times or potential material degradation. The optimal balance ensures dimensional stability without unnecessary delays or material compromise.
Factor | Influence on Holding Time |
---|---|
Plastic Material Type | Plastics with high shrinkage require longer holding times. |
Part Size | Larger parts typically need extended holding times to ensure full compaction. |
Mold Temperature | Higher mold temperatures can reduce necessary holding time. |
Testing for Optimal Holding Time
Determining the ideal holding time often requires experimentation. Manufacturers may need to conduct trials, adjusting variables like pressure, temperature, and time to achieve the desired dimensional accuracy. This iterative process helps refine production settings for consistent quality outputs.
By carefully analyzing these factors and their interplay, manufacturers can enhance precision and minimize defects, thereby optimizing the injection molding process for superior product quality6.
Longer holding time reduces shrinkage in molded parts.True
Longer holding time maintains pressure, compensating for shrinkage during cooling.
Excessive holding time always improves dimensional accuracy.False
Excessive holding time can lead to increased cycle times and material issues.
What Factors Influence the Optimal Holding Time?
In injection molding, determining the ideal holding time is crucial to producing high-quality plastic parts.
Optimal holding time in injection molding is determined by factors like material properties, part size, mold temperature, and injection pressure, which collectively ensure efficient shrinkage compensation and product integrity.
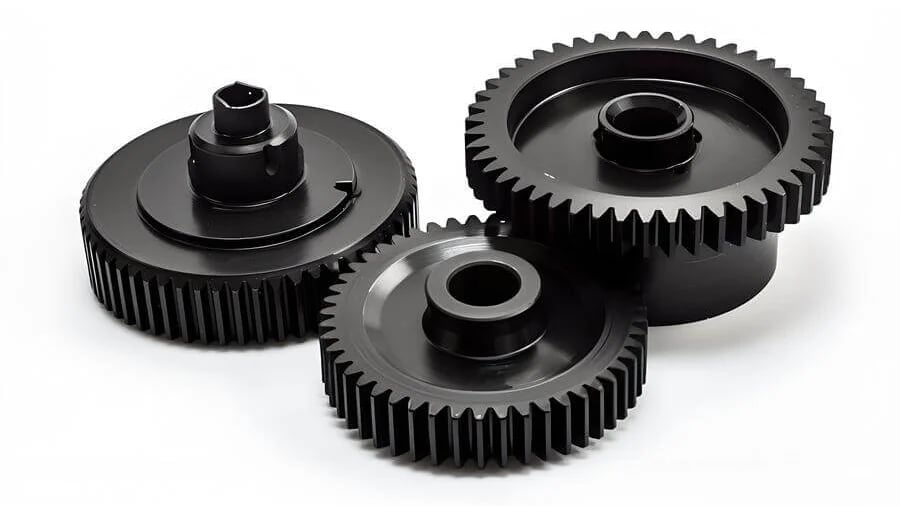
Understanding Material Properties
The properties of the plastic material play a pivotal role in determining the holding time. Plastics with high fluidity require shorter holding times because they can easily fill the mold cavity. Conversely, materials prone to shrinkage, such as those with crystalline structures, necessitate longer holding times to adequately compensate for shrinkage during cooling.
Influence of Part Size and Shape
Larger and more complex parts generally require extended holding times. This is due to the increased volume of material that needs adequate pressure for proper compaction and shrinkage compensation. For example, a large panel might need a different holding time compared to a small gear, due to its size and shape variations.
Impact of Mold Temperature
The temperature of the mold can significantly affect the optimal holding time. Higher mold temperatures may require adjustments in holding time to ensure proper solidification and compaction of the plastic melt. Balancing mold temperature with holding time is essential for maintaining the dimensional accuracy and surface finish of the final product.
Role of Injection Pressure
The initial injection pressure influences the subsequent holding phase. High injection pressures can lead to shorter holding times as the pressure aids in filling and compacting the melt efficiently. However, excessive pressure without adequate holding can cause defects like flash or warping.
Experimentation and Adjustment
Achieving optimal holding time often involves experimentation. Adjusting the variables based on specific production conditions can refine the process. Implementing trial runs and analyzing results allow manufacturers to tailor the holding time for each unique application, leading to improved product quality and reduced defect rates.
For further exploration on optimizing injection molding processes, refer to advanced molding techniques7 which offer insights into balancing these factors for enhanced efficiency.
High fluidity plastics need shorter holding times.True
Plastics with high fluidity fill molds easily, requiring less time.
Higher mold temperatures always increase holding time.False
Higher temperatures may reduce holding time by aiding solidification.
Conclusion
Optimizing holding time in injection molding is key to improving product quality and efficiency. Adjusting this parameter leads to better accuracy and reduced defects.
-
Learn how compensation mechanisms enhance product quality.: Industrial global compensation is a method to apply the average shrinkage value of the injected part to compensate the product dimension. This … ↩
-
Discover methods for determining optimal holding times.: Holding pressure is less than injection pressure. Holding time is the duration that ensures the product gate is completely frozen, preventing backflow. ↩
-
Explore techniques to manage shrinkage effectively for better product quality.: It indicates the extent to which the size of the plastic component is reduced after it is removed from the mold and allowed to cool. Plastic kinds, molding … ↩
-
Learn strategies to optimize shrinkage compensation for precision parts.: Demoulding improvements to prevent ejection deformation: balance the jacking force, carefully polish the new side, increase the demoulding angle … ↩
-
Understand why precision is critical in molded parts.: Manufacturing Precision of Mold Dimensions: The precision with which the mold is manufactured is a key factor in determining the dimensional accuracy of the … ↩
-
Explore strategies to enhance molded product quality.: Steps to INJECTION MOLDING Process Optimization · 1. Tool functionality examination · 2. Short shot testing · 3. Gate seal studies · 4. Sample parts evaluation/data … ↩
-
Discover innovative strategies to optimize injection molding processes.: Owned and managed by engineers, we specialize in technical applications of fluid path, critical shutoffs, and disciplined manufacturing. ↩