Navigating the world of injection molding can feel overwhelming, but understanding its core principles is vital for success.
To achieve high-quality injection molding, focus on selecting superior raw materials, designing precise molds, controlling the molding process parameters, and implementing rigorous quality inspection. These steps ensure product consistency, durability, and visual appeal.
As we delve deeper into each step, you’ll uncover valuable insights and expert techniques that can elevate your injection molding game.
High-quality resin ensures better injection molding results.True
Using pure, stable resins improves strength and appearance.
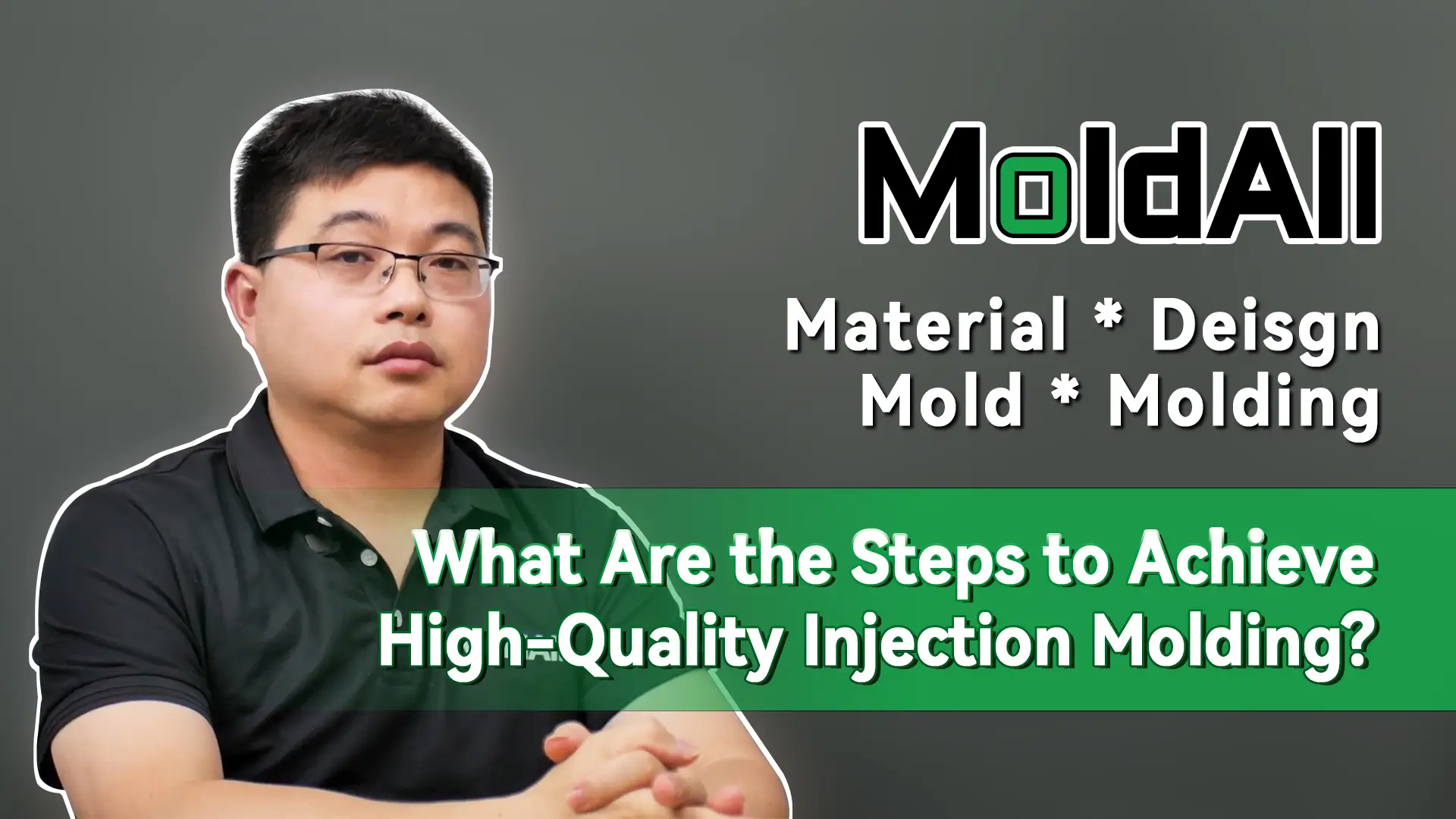
How Do You Select the Right Raw Materials for Injection Molding?
Selecting the right raw materials is a pivotal step in injection molding, influencing product quality and performance.
To choose the right raw materials for injection molding, assess the specific requirements of your product, select high-quality resins, and add suitable additives to enhance performance. Consider material purity and stability to ensure optimal part quality.
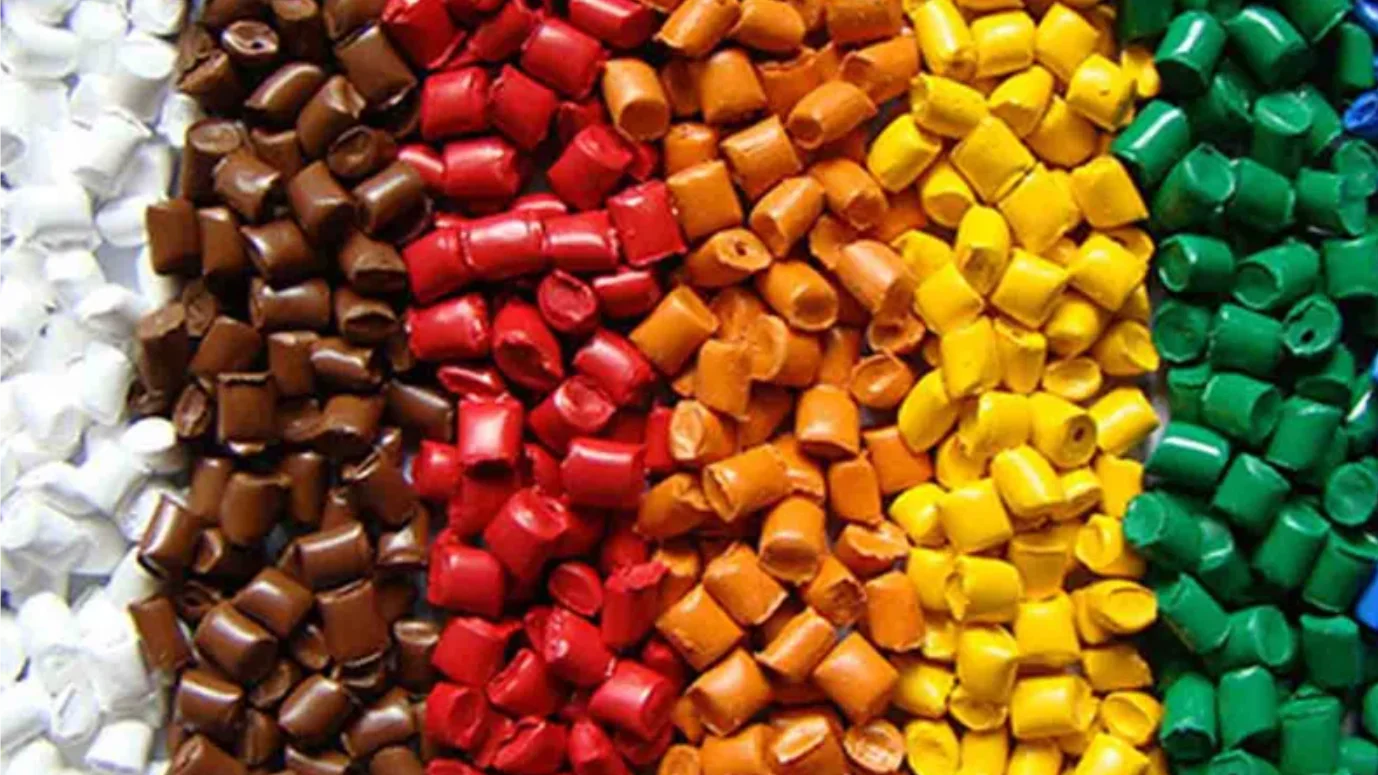
Understanding Material Requirements
When selecting raw materials for injection molding, the first step is understanding the specific requirements of your product1. Are you aiming for high strength, excellent surface finish, or perhaps resistance to heat and chemicals? Knowing the primary function and environment of the part will guide your material choice.
For instance, if your product requires high mechanical strength, high-performance engineering plastics like polycarbonate or nylon may be ideal. Alternatively, for products needing a sleek finish, materials with inherent gloss like ABS could be more suitable.
Choosing High-Quality Resins
The resin forms the backbone of any injection molded part. Selecting a resin that aligns with your product’s specifications is crucial. High-performance resins can dramatically impact the strength and durability of the final product. Ensure that your chosen resin offers the necessary properties such as tensile strength, elongation, and modulus of elasticity.
Moreover, ensure that the resin is free from impurities or degradation products which can compromise both performance and aesthetics. Using a degraded or impure resin can lead to defects such as warping or discoloration in the final product.
Role of Additives in Material Performance
Additives play a significant role in modifying and enhancing the properties of base resins. Based on the desired characteristics of your injection molded parts, you might incorporate different additives:
- Plasticizers: Improve flexibility and processability.
- Stabilizers: Enhance heat resistance and weatherability.
- Lubricants: Aid in smoother processing by reducing friction.
When incorporating additives, it’s vital to balance their quantity carefully. Overuse can lead to adverse effects, such as reduced mechanical properties or unwanted chemical reactions during processing.
Ensuring Material Purity and Stability
Material purity and stability are paramount in ensuring that the end product meets quality standards. Contaminants in raw materials can lead to defects like splay marks or reduced mechanical integrity.
To mitigate these risks, source your raw materials from reputable suppliers who provide detailed material data sheets outlining purity levels and stability under specified conditions.
Practical Insights from Industry Experts
Industry experts emphasize that meticulous selection and preparation of raw materials are foundational to successful injection molding. A proactive approach in vetting material quality not only improves product performance but also optimizes production efficiency by reducing waste and rework.
By thoroughly understanding the requirements, selecting appropriate resins, judiciously adding performance-enhancing additives, and ensuring material purity, you lay a solid foundation for producing superior injection molded parts.
High-performance resins enhance product durability.True
High-performance resins increase strength and durability.
Additives reduce the mechanical properties of resins.False
Additives enhance resin properties if used correctly.
What Are the Key Considerations in Mold Design and Manufacturing?
Mold design and manufacturing play a pivotal role in the injection molding process, impacting product quality and production efficiency.
Key considerations in mold design include ensuring a reasonable mold structure and precision manufacturing. These factors affect the dimensional accuracy, appearance, and durability of injection molded parts.
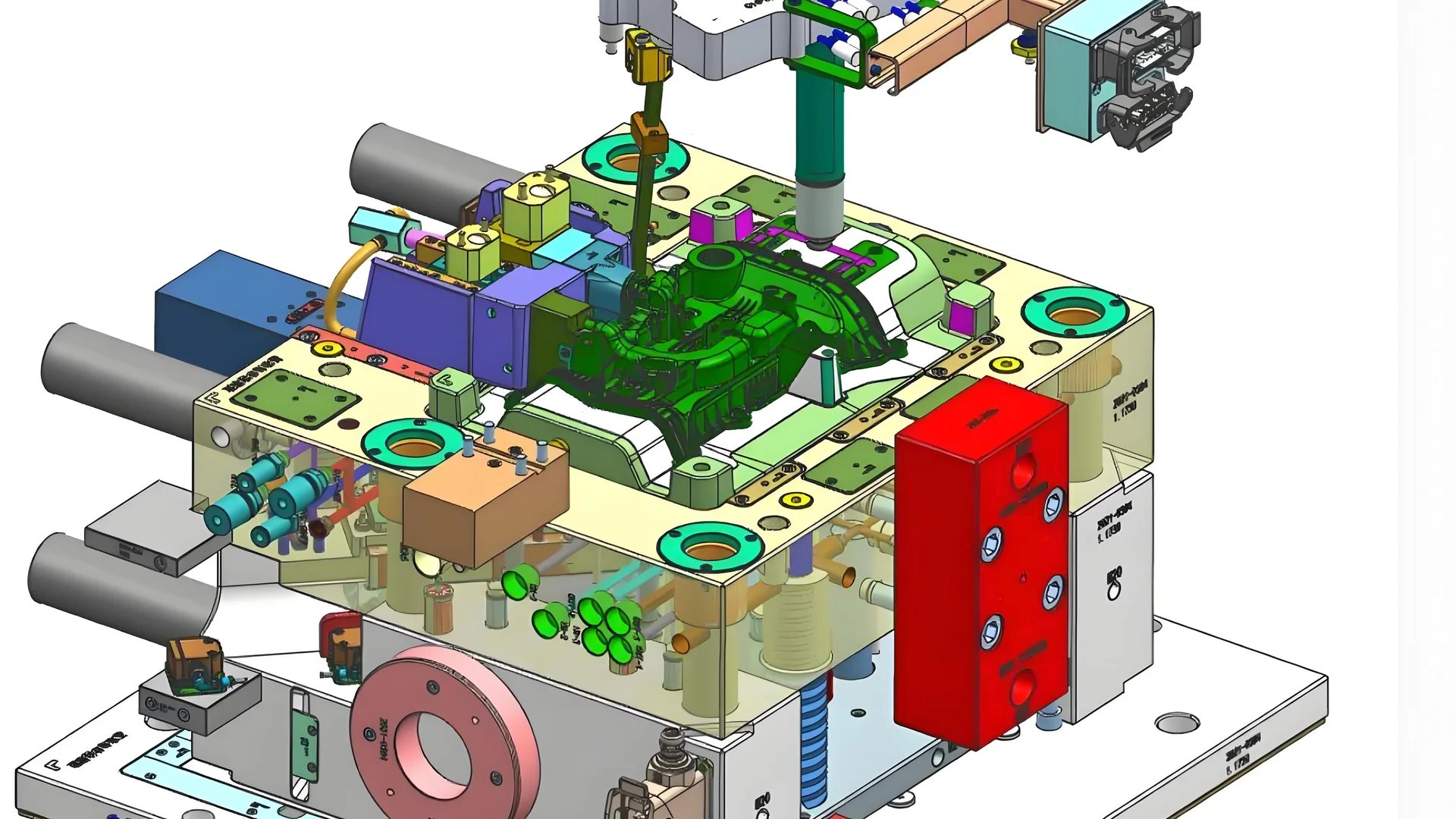
Understanding Mold Structure
A well-designed mold structure is fundamental to producing high-quality injection molded parts. When conceptualizing a mold, consider factors such as the shape, size, and wall thickness of the component. These aspects are crucial for determining how the mold will fill with molten plastic and subsequently cool.
-
Shape and Size: The mold must accurately reflect the intended shape and dimensions of the final product. This includes not only the external dimensions but also any internal features or undercuts that may be required.
-
Wall Thickness: Uniform wall thickness helps in avoiding potential issues such as warping or sink marks. It also ensures consistent cooling and solidification of the part.
-
Gate Design: Optimizing the gate position, size, and number is essential to ensure even flow of plastic melt into the cavity. Improper gating can lead to defects like air traps or incomplete filling.
Achieving Precision in Mold Manufacturing
The precision of mold manufacturing directly influences the quality of the injection molded parts. Utilizing advanced processing equipment and techniques can significantly enhance mold accuracy.
-
Advanced Machining: Techniques such as CNC machining ensure that molds are produced with high precision, reducing dimensional errors.
-
Surface Treatments: Processes like heat treatment enhance mold hardness and wear resistance, prolonging mold life. Surface treatments can also improve corrosion resistance, vital for maintaining mold integrity over multiple cycles.
Consideration | Benefits | Potential Issues Without It |
---|---|---|
Precision | Ensures dimensional accuracy | Inconsistent part dimensions |
Gate Design | Promotes even material flow | Defects like air traps |
Wall Thickness | Avoids warping and sink marks | Uneven cooling, leading to defects |
Integrating Technology for Enhanced Outcomes
Incorporating technology like computer-aided design (CAD) and simulation tools can further refine mold design and manufacturing.
-
Simulation Tools: These tools help in predicting flow patterns, cooling rates, and potential defect areas before actual production begins. This proactive approach enables adjustments to be made early in the design process.
-
Computer-Aided Design (CAD): CAD software allows for precise modeling and testing of molds before fabrication, ensuring all specifications are met accurately.
By focusing on these key considerations—structure, precision, and technology integration—you can achieve superior results in mold design and manufacturing. Explore more about advanced CNC machining techniques2 for precision manufacturing and how simulation tools optimize mold design3.
Uniform wall thickness prevents warping in molds.True
Uniform wall thickness ensures consistent cooling, reducing warping.
Gate design has no effect on injection molding defects.False
Improper gate design can cause defects like air traps or incomplete filling.
How Can You Optimize Injection Molding Process Parameters?
Optimizing injection molding process parameters is key to enhancing product quality and production efficiency. Learn how to fine-tune temperature, pressure, and speed for superior results.
To optimize injection molding process parameters, focus on precise control of temperature, pressure, speed, and time settings. Tailor these parameters to the specific resin and part design to ensure optimal performance and minimize defects.
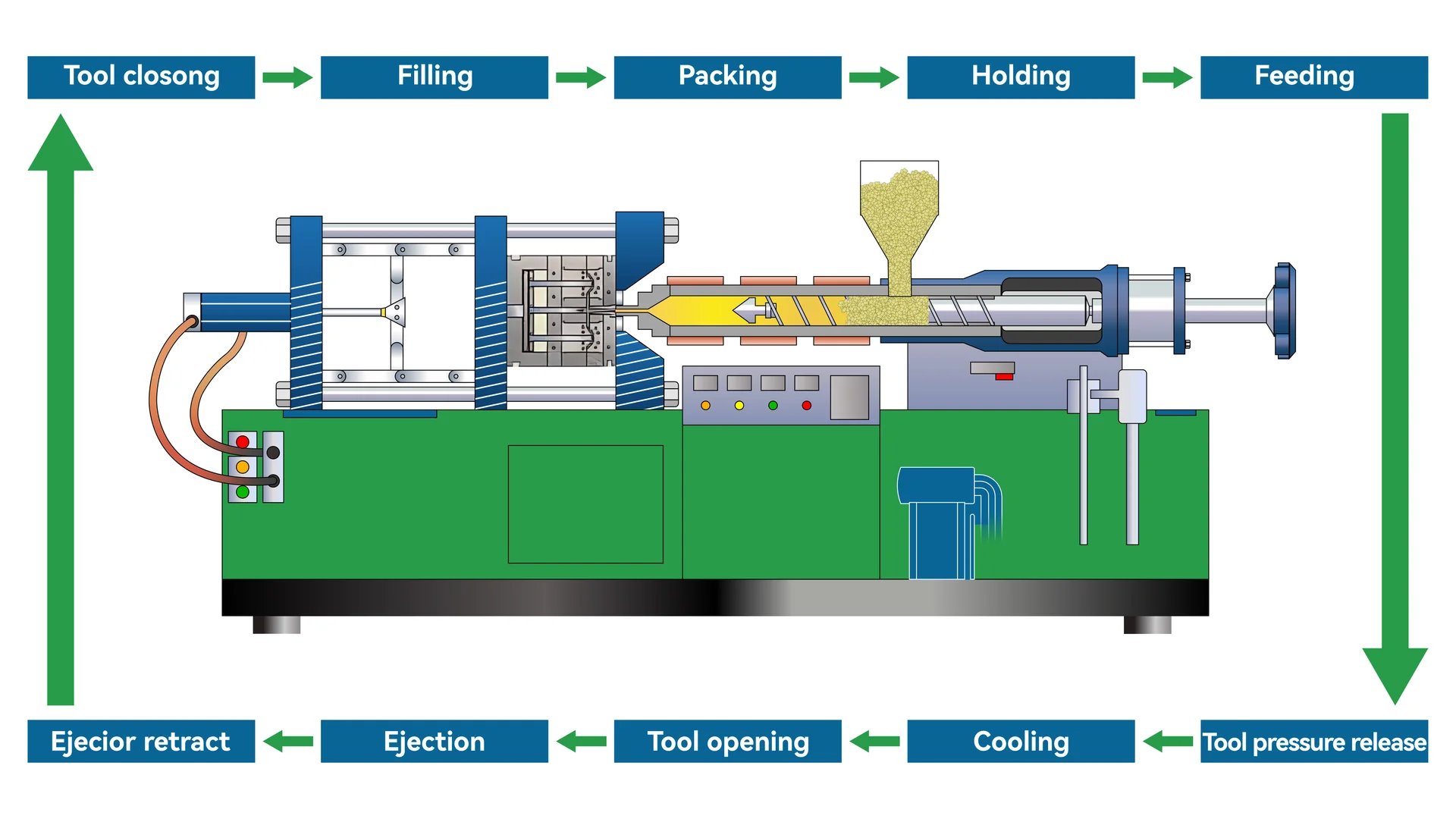
Understanding the Critical Process Parameters
Injection molding involves several critical process parameters, including temperature, pressure, speed, and time. Each of these parameters plays a pivotal role in determining the quality of the final product. A deep understanding of these factors can help reduce defects such as warping, sink marks, or poor surface finish.
Temperature Control
The barrel, nozzle, and mold temperatures must be meticulously controlled to prevent material degradation and ensure proper flow. Different resin materials require specific temperature ranges, which need adjustment according to the part’s complexity and the desired properties.
- Barrel Temperature: This affects the melting and homogenization of the plastic resin. A consistent temperature profile is crucial to avoid partial melting or burning.
- Mold Temperature: Influences the cooling rate of the molded part. Higher mold temperatures generally improve surface finish but can increase cycle time.
Explore more about temperature control strategies4 to enhance molding precision.
Pressure Control
Injection pressure and holding pressure are vital for filling the mold cavity and maintaining the shape of the part. Adjustments in pressure can directly influence the density and mechanical properties of the part.
- Injection Pressure: Must be set high enough to fill the mold but not so high that it causes flashing or other defects.
- Holding Pressure: Maintains material in the mold as it cools and solidifies, preventing shrinkage and voids.
Learn techniques for optimizing pressure settings5 to ensure dimensional accuracy.
Speed Control
The speed of injection impacts the flow pattern of the molten resin. Fast speeds can cause flow lines or jetting, while slow speeds may lead to short shots or incomplete fills.
- Injection Speed: Should be tailored to the geometry of the mold. Gradual speed profiles can help achieve even filling without defects.
- Screw Speed: Influences plasticization and mixing efficiency. It should be optimized for consistent material quality.
Delve into speed optimization methods6 for improved part quality.
Time Control
Time parameters, including injection time, cooling time, and cycle time, are crucial for balancing production efficiency and product quality.
- Cooling Time: Affects dimensional stability and surface finish. Optimizing this can reduce cycle time without compromising quality.
- Cycle Time: Efficient management leads to higher throughput while maintaining quality standards.
Explore strategies for time management7 in the injection molding process.
Monitoring and Adjustments
Continuous monitoring with sensors and cameras enables real-time adjustments to maintain process stability. Implementing an automated system can significantly enhance precision and reduce human error.
By understanding and controlling these parameters, manufacturers can achieve superior product quality, improve production efficiency, and reduce waste. The integration of advanced monitoring technologies further supports these efforts by providing data-driven insights into process improvements.
Higher mold temperatures reduce cycle time.False
Higher mold temperatures generally increase cycle time, not reduce it.
Injection speed affects flow pattern of resin.True
The speed of injection impacts the flow pattern and filling quality.
Why Is Quality Inspection Essential in Injection Molding?
Ensuring top-notch quality in injection molding is critical for maintaining product standards and customer satisfaction. Quality inspection plays a pivotal role in this process.
Quality inspection in injection molding ensures that products meet design specifications and function as intended. It involves real-time monitoring, sampling, and traceability to identify defects early, preventing costly recalls and ensuring consistency.
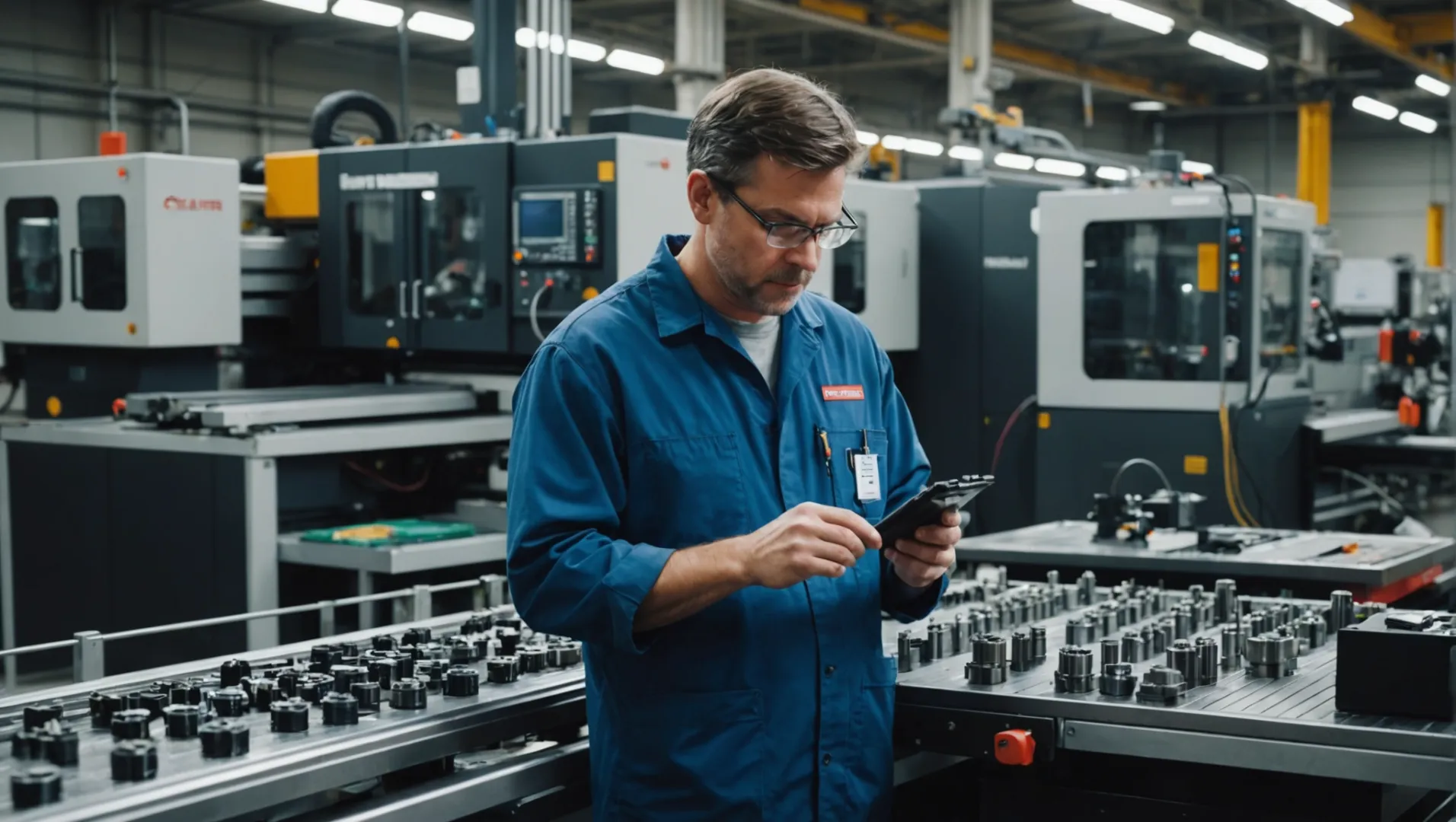
The Role of Online Inspection
Online inspection utilizes advanced technologies like sensors and cameras to continuously monitor the production line. This real-time analysis helps in detecting deviations in size, appearance, and weight8 of injection molded parts. If a defect is spotted, adjustments can be made promptly to avoid further production of faulty items.
Sampling Inspection Techniques
Sampling inspection acts as a safety net by selecting random samples for thorough testing. This includes measuring dimensions, assessing mechanical properties, and conducting visual checks. For instance, if a batch of parts is produced with varying tensile strength, sampling can identify this inconsistency, allowing for corrective actions.
Inspection Type | Purpose | Tools Used |
---|---|---|
Online Inspection | Real-time defect detection | Sensors, Cameras |
Sampling Inspection | Verifying batch quality | Calipers, Micrometers |
Importance of Quality Traceability
A robust quality traceability system records each part’s production details. This data becomes invaluable when tracing back any defects to their source, whether it’s a material issue or a process parameter deviation. Such traceability not only aids in solving current issues but also in refining future production strategies.
Benefits of Rigorous Quality Inspection
Implementing rigorous quality inspection protocols ensures that the final products not only meet but exceed customer expectations. It reduces the risk of defective products reaching the market9, which could lead to recalls or damage to brand reputation.
Quality inspection is a cornerstone of the injection molding process, safeguarding against errors and enhancing product reliability. By integrating comprehensive inspection methods, manufacturers can maintain high standards and deliver superior products consistently.
Online inspection detects defects in real-time.True
Real-time monitoring helps identify defects immediately, allowing quick adjustments.
Sampling inspection checks every single product for defects.False
Sampling inspection tests random samples, not each product, for quality control.
Conclusion
By mastering each stage of injection molding—from material selection to process control—you can produce superior parts that meet stringent quality standards.
-
Helps grasp how product requirements influence material choices.: Understanding how materials respond to certain environmental conditions is crucial for ensuring the longevity and functionality of a product. ↩
-
Learn how CNC machining enhances mold precision.: Precision machining technology allows machine shops to create parts with tight tolerances that are highly complex and require intricate geometries. ↩
-
Discover how simulation tools improve mold design efficiency.: Incorporating simulation of the cooling stage of the injection molding process can help to make a tool as efficient as possible. ↩
-
Discover advanced methods for precise temperature management.: The mold’s temperature should be controlled at 60 degrees Celsius to prevent stress cracking in plastics with good fluidity such as PE, PP, HIPS … ↩
-
Learn effective techniques for achieving accurate pressure control.: Here are the 8 key parameters in injection molding that you need to align in order to produce consistent, high quality plastic parts. ↩
-
Uncover strategies to enhance speed settings for better quality.: 1. Temperature Control: · 2. Injection Speed: · 3. Cooling Time: · 4. Plastic Material Selection: · 5. Screw Speed and Back Pressure: · 6. Injection … ↩
-
Find ways to balance cycle time with product quality.: Utilize machines with parallel actions. For example, get machines with simultaneous ejection and injection to save time during each cycle. ↩
-
Explore how real-time monitoring enhances defect detection during production.: We specialize in real-time production monitoring for the plastics industry, primarily injection molding machines. Book a free demo with us. ↩
-
Learn why preventing defects is crucial for maintaining product quality.: Strategies for Reducing Defects in Manufacturing · 1. Proper Quality Management · 2. Maintain a Positive Work Environment · 3. Aim For Continuous Improvement. ↩