Have you ever felt that your well-crafted plastic product was ruined by hidden forces? High injection pressure might be to blame.
High pressure in plastic molding leads to problems like flying edges, stream marks, burn marks, very high internal stress and cavities inside. These problems ruin the product’s look and weaken its strength. High pressure increases production costs and causes more waste.
I think back to my time in the field and recall feeling frustrated when lovely parts were spoiled by too much pressure. It felt like seeing a cake fall after stirring the batter too much. These defects need attention, not blame. We learn to stop them early. In the next parts, I will explore where each defect starts. I will share ideas on stopping these problems early. Designs should be as nice in reality as on paper. Designs should match the vision.
Flying edge occurs due to high injection pressure.True
High injection pressure causes plastic melt overflow, forming fringes.
Burn marks are caused by low injection pressure.False
Burn marks result from excessive frictional heat, not low pressure.
What Appearance Defects Are Caused by High Injection Pressure?
I recall my first experience with injection molding defects. The plastic parts seemed to have a mind of their own.
High injection pressure results in problems like flying edges, stream marks and burn marks. These flaws affect how the product looks and need expensive repairs. The plastic melt behaves differently under too much pressure. This impacts the final product’s appearance and quality.
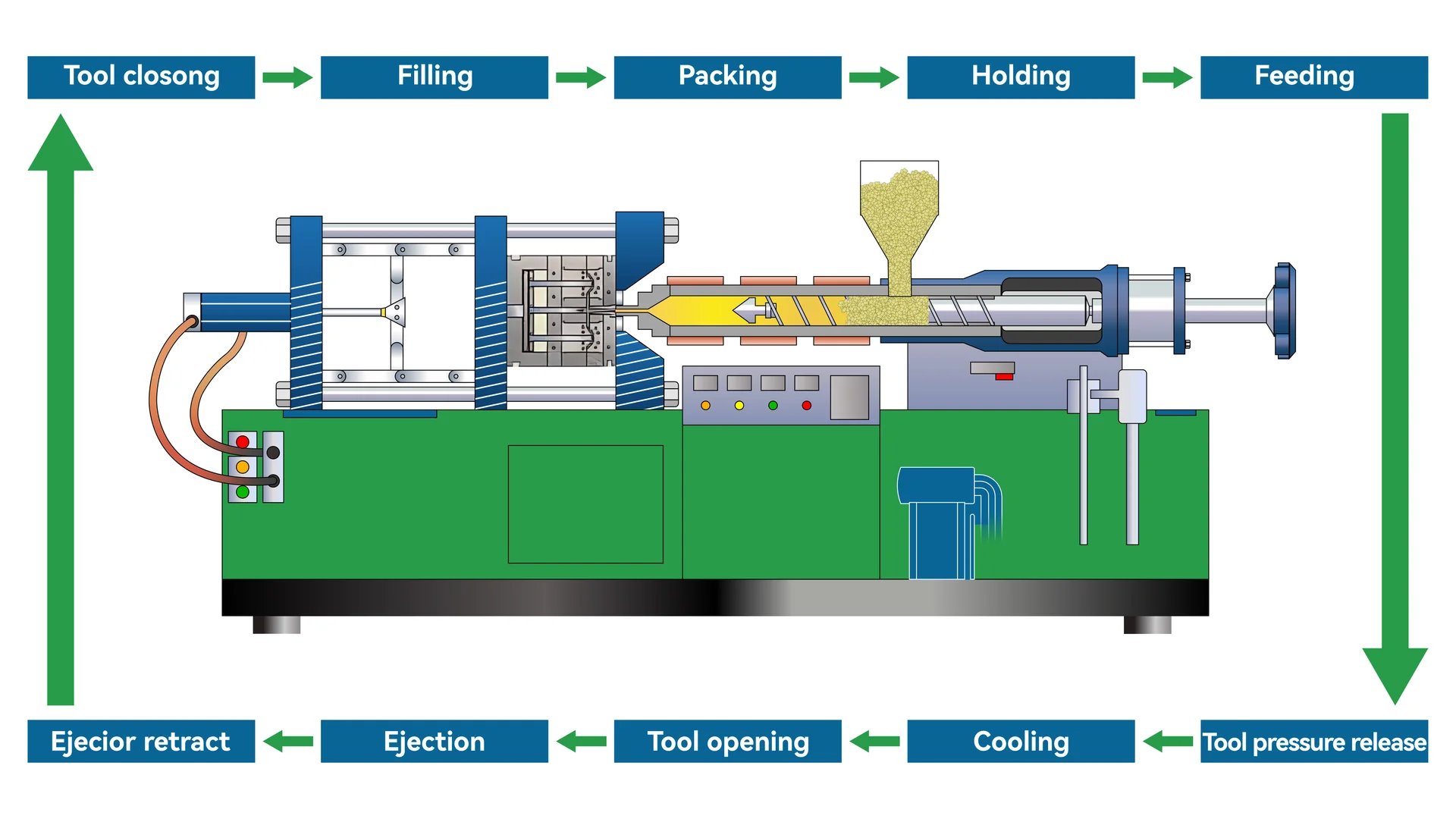
Flying Edges
When I began working with plastic parts, I felt surprised by how something tiny, like injection pressure, created many issues. Pressure seems to have its own character, deciding when to act nicely and when to cause trouble.
I remember seeing a small plastic part grow wings—not actually, but those edges seemed ready to fly. High pressure forces the melted plastic to spill out from the mold, creating these annoying edges. Handling them demands extra cutting, which is just as thrilling as it sounds. It feels like cleaning up after a messy roommate all the time. Really all the time.
Defect Type | Cause | Impact |
---|---|---|
Flying Edges | Overflow from mold surfaces | Requires trimming, raises costs |
Stream Marks and Silver Streaks
Next came the strange wavy lines—stream marks—that ruined a shiny surface. These lines appeared unexpectedly, much like guests at a party who missed the dress code. Fast-flowing plastic traps air, leading to silver streaks—very unwanted silver streaks resemble undesirable hair highlights.
Excessive pressure causes the melt to flow rapidly, leading to wavy flow marks on the surface. This issue is detrimental for items demanding high gloss or transparency like lenses1. Moreover, air entrapment during rapid flow creates silver streaks or mottling on the product2.
Defect Type | Cause | Impact |
---|---|---|
Stream Marks | Unstable melt front | Affects appearance in glossy items |
Burn Marks
Burn marks remind me of burn spots on my favorite shirt after ironing wrong. High injection pressure generates frictional heat, leaving scorch marks on the product. With sensitive plastics like PVC, it’s easy for things to go from good to damaged.
High injection pressure generates excessive frictional heat particularly near gates or narrow runners leading to burn marks. This defect is prevalent in heat-sensitive plastics like PVC where it causes discoloration and a burnt odor.
These problems taught me a lot about managing injection molding successfully. Knowing them reduces surprises; more understanding means more calm moments.
Defect Type | Cause | Impact |
---|---|---|
Burn Marks | Excessive frictional heat | Discoloration and potential scrap |
High injection pressure causes flying edges.True
Excessive pressure leads to plastic overflow at mold gaps, forming fringes.
Burn marks are unrelated to injection pressure.False
High pressure generates frictional heat, causing scorching and burn marks.
How Do Flash Affect Product Quality?
Flash in injection molding surprised me with how much they could really harm product quality. This was an important lesson in precision. Precision matters a lot.
Flash in injection molding often result in visible defects like fringes and flow marks. These edges also lead to hidden issues such as stress and cavities. Proper control of injection pressure helps reduce these flaws. This approach results in better product quality. Product quality really depends on managing pressure well.
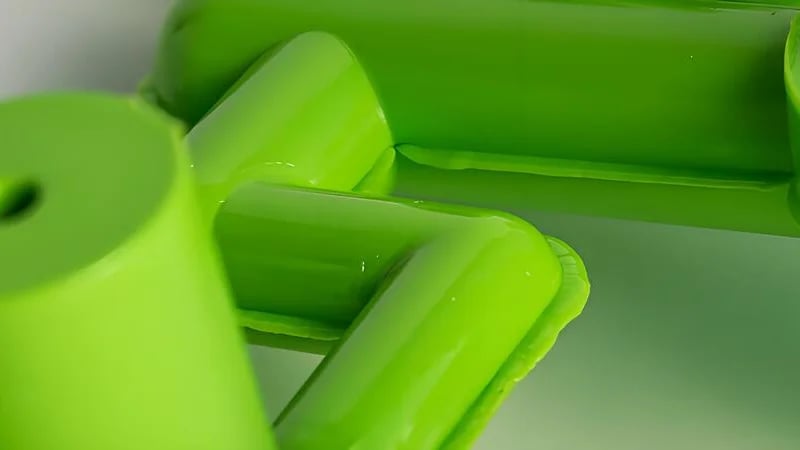
Appearance Flaws Due to Flash
Think of creating a nice vase. You pull it from the mold and find an ugly fringe on the edge. This happens with flying edges in plastic items when too much plastic spills over the mold because of high injection pressure3. I remember seeing this first on a small plastic gadget. Extra material stuck to the edges, needing trimming, which took more time and increased costs.
Table: Common Appearance Defects
Defect Type | Description |
---|---|
Flash | Excess plastic forms fringes at edges |
Flow Marks | Wavy traces on surfaces due to unstable melt front |
Silver Streaks | Air involvement causing streaks or mottling |
Flow marks are another issue. They look like tiny waves on the product’s surface, not great if you want a smooth, shiny finish like plastic lenses. I learned quickly that managing pressure is very important to keep these marks away.
Silver streaks also appear if air and speed don’t mix well in molding. I worked once on a shiny project and saw these streaks. They looked like someone painted a silver line over our work. It was really annoying!
Internal Issues from Too Much Pressure
More than just looks, Flash can cause big problems inside. High injection pressure creates serious internal stress4 inside products, causing them to warp or crack. I saw this with big containers, where stress cracked the walls.
Internal cavities or uneven density are also problems. In thick products, high pressure makes a honeycomb pattern inside, weakening them. I remember one project where a solid piece was filled with these holes.
Managing Injection Pressure
How do we fix it? Mastering the pressure is key. Keeping it steady lets the melted plastic spread smoothly, reducing flying edges and their annoying flaws. Adjusting the molding process5 helps improve product quality and cuts down on extra work after.
Knowing these effects has greatly helped me design better and improve product strength. This useful knowledge benefits anyone interested in mold design and manufacturing.
Flying edges increase production costs due to trimming needs.True
Excess plastic on edges requires removal, raising production expenses.
Internal voids are caused by low injection pressure.False
High pressure creates localized vacuums during cooling, forming voids.
Why Do Stream Marks and Silver Streaks Occur?
Have you ever seen those annoying streaks on your favorite plastic gadget? Let’s explore why these streaks appear and discover ways to fix them.
Stream marks and silver streaks appear from high injection pressure during plastic molding. This pressure causes uneven flow of melted plastic and tiny air pockets. Mold temperature and pressure settings need adjusting to prevent these problems.
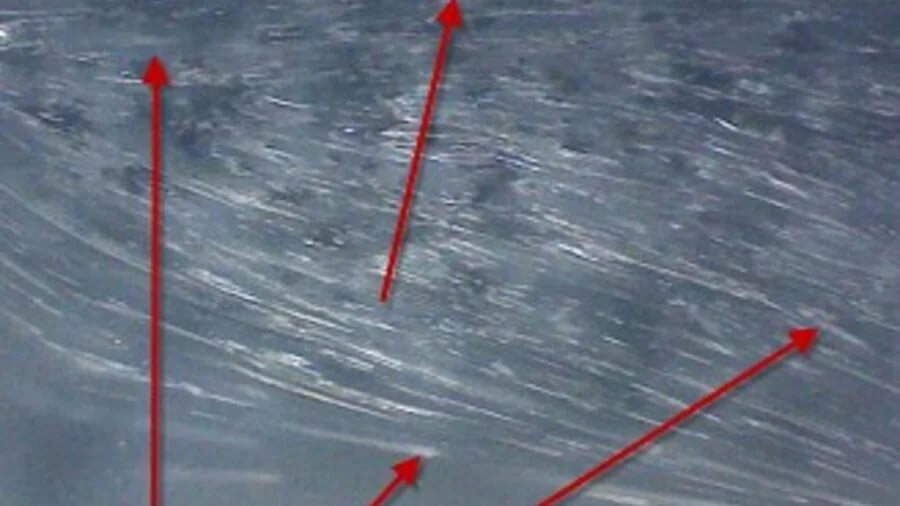
Causes of Stream Marks and Silver Streaks
The first time I saw stream marks, it confused me. I had finished working on a shiny gadget case and those wavy lines showed up. They were not part of the plan. These lines often appear because of high injection pressure6. Melt flows too fast and leaves ugly marks behind.
-
Stream Marks: Imagine ripples in a pond after you throw a stone. Stream marks look like that on plastic surfaces. They are annoying when you want a glossy, perfect finish.
-
Silver Streaks: Then there are silver streaks. They remind me of a ghost moving across your product. This is not welcome. They happen when the fast melt traps air, making streaks that ruin the look.
How Injection Pressure Affects Appearance
Table: Effects of Injection Pressure on Plastic Molding
Pressure Level | Potential Defects |
---|---|
High | Stream marks, silver streaks, burn marks |
Low | Short shots, sink marks |
Learning about pressure control was like finding a secret in a game. Too much pressure can mess up the appearance. It can also stress the plastic so much that it changes shape later.
- For clear parts like lenses, control of mold temperature7 and pressure is very important.
Practical Solutions to Mitigate These Defects
I spent many hours changing settings to fix these issues. But some practical steps can help:
- Optimize Mold Design: Even cooling and proper venting help avoid air pockets.
- Adjust Pressure Settings: Find the right injection pressure for smooth flow.
- Monitor Mold Temperature: Keeping a steady temperature helps prevent silver streaks.
After managing these factors, creating perfect plastic products8 becomes possible, not just a dream.
Flying edge is caused by low injection pressure.False
Flying edge results from excessive injection pressure, not low pressure.
Stream marks affect the appearance of plastic lenses.True
Stream marks can form on products with high gloss requirements, like lenses.
What Leads to Burn Marks During Injection Molding?
Ever spotted those ugly burn marks on molded products and wondered why they appear repeatedly? Many people in manufacturing have encountered this mystery.
Burn marks in injection molding happen because too much heat comes from high pressure. This heat causes the plastic to scorch. Narrow runners or gates usually show these burn signs. Managing pressure well is important. Mold design also plays a big role. These measures prevent defects.
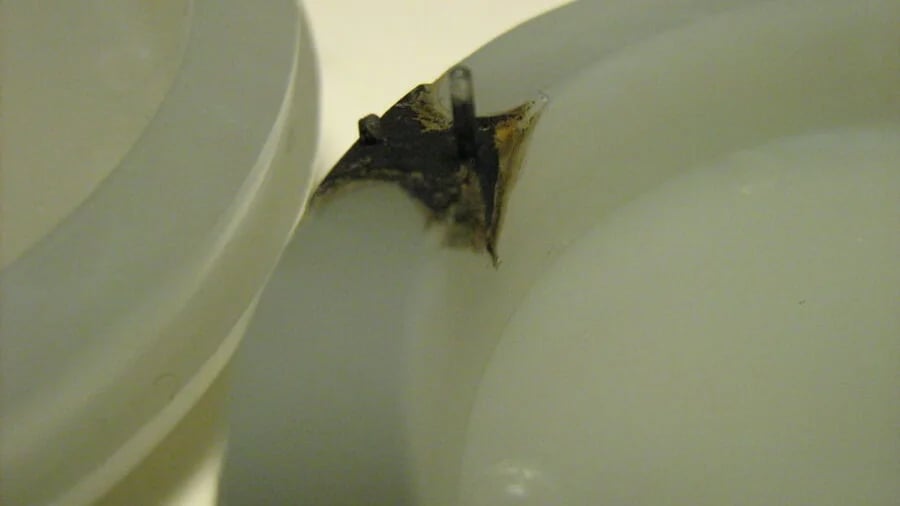
Key Factors Causing Burn Marks
Too Much Injection Pressure
Imagine trying to squeeze more toothpaste from an almost empty tube. Pressure builds up and suddenly, too much toothpaste bursts out. In injection molding, high pressure causes excess heat from friction as plastic moves through the mold. This happened when I pushed too hard to meet a tight deadline. High resistance areas, like near gates or narrow runners9, are heat hotspots, especially with plastics like PVC.
Factor | Impact |
---|---|
High injection pressure | Increased frictional heat and potential scorching |
Narrow runner design | Greater resistance, raising localized temperatures |
Moisture in the Material
I once skipped drying the materials, thinking it wasn’t that important. Big mistake! Moisture turned to steam in the mold, causing burn marks. Now, I always dry materials like nylon and ABS10 before use.
Consideration | Solution |
---|---|
Moisture content | Ensure thorough drying of materials |
Trapped Air and Gases
Imagine shaking a soda can and opening it. The air rushes out quickly, making a mess. In molds, trapped air compresses during injection, causing burn marks. Realized the need for good venting systems to let air escape easily.
Consideration | Solution |
---|---|
Air entrapment | Implement efficient venting systems |
Material Characteristics
Different plastics act differently under heat and pressure. Understanding how they behave is key to setting the right conditions and avoiding burn marks.
Understanding these factors changed everything for me and others in making top-quality plastic parts. Setting molding conditions based on material traits and having good mold designs leads to great product looks. These experiences shaped my way of working and my promise to deliver the best to my clients.
Excessive pressure causes flying edges in injection molding.True
High pressure causes plastic to overflow, forming fringes at edges.
Burn marks are caused by low injection pressure.False
Burn marks result from excessive frictional heat due to high pressure.
How Does Excessive Internal Stress Impact Product Durability?
Ever felt like you were close to exhaustion? Products, too, often experience similar strain!
Too much internal stress affects product strength. It causes flaws such as bending, cracking and inside gaps. High injection pressure during production is often the reason. The structure becomes weak. The structure is less reliable.
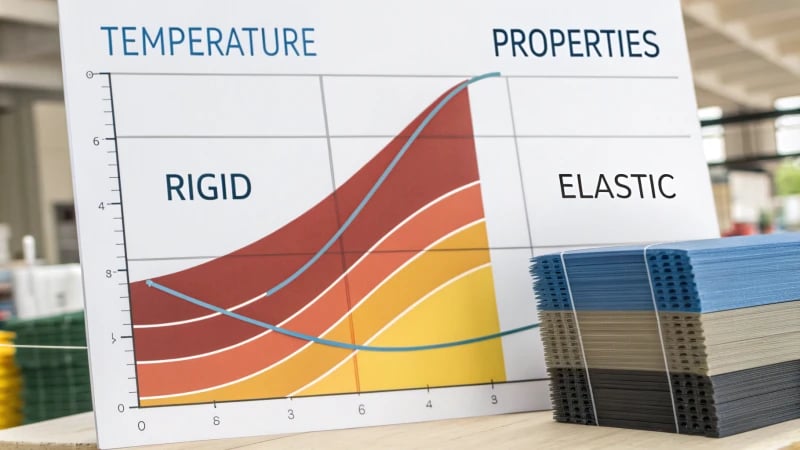
Understanding Internal Stress in Manufacturing
When I first started learning about plastic manufacturing11, the term "internal stress" appeared more often than I expected. I found out quickly that in this field, internal stress is not only a human feeling – it affects materials too. High pressures, used for filling molds correctly, often bring unwanted internal stress.
Types of Defects
Defect Type | Cause | Impact on Durability |
---|---|---|
Deformation | Molecular chain orientation | Warping during use |
Cracking | Excessive compression | Weak points fracture |
Cavities | Localized vacuum | Reduced structural integrity |
The Role of Injection Pressure
Now, here’s the tricky part: injection pressure acts as both a friend and an enemy. It helps to fill molds properly, but too much pressure causes problems. Think of trying to fit into tight clothes after eating too much – that’s what happens to molecular chains under excessive pressure. They become too organized, creating stress that remains as the product cools. This stress is like a hidden threat, ready to cause deformation12 at any time.
Picture this: you’re making big containers and the walls suddenly bend or crack due to internal stress. Transportation or storage suddenly becomes a huge problem.
Appearance Defects and Their Consequences
Then there are appearance defects. High injection pressures can cause flying edges, stream marks, and burn marks. They not only reduce the product’s attractiveness but also suggest deeper issues inside.
For example:
- Flying edge happens when extra material spills over, needing more cutting.
- Stream marks indicate unstable flow, a major issue for clear products.
- Burn marks come from heat created by friction, especially bad for plastics sensitive to heat.
These problems mean more work and higher production costs and they might also shorten the product’s lifetime.
Reducing Internal Stress
Luckily, designers have some strategies! By improving mold design and changing process settings, stress can be reduced. Methods like stress-relieving processes13 spread out stress, increasing strength.
Additionally, using process control measures and advanced simulation tools may help predict and lessen stress-related problems, keeping products reliable over time.
Excessive injection pressure causes burn marks.True
High pressure generates frictional heat, leading to scorching.
Stream marks improve the appearance of plastic products.False
Stream marks create wavy traces, degrading appearance quality.
Conclusion
High injection pressure in plastic molding leads to defects like flying edges, stream marks, and burn marks, compromising product appearance and strength while increasing production costs.
-
Understand why flying edges occur with high pressure, aiding in prevention. ↩
-
Learn about the formation of silver streaks to improve product quality. ↩
-
Exploring injection pressure effects provides insights into preventing common defects like flying edges. ↩
-
Understanding internal stress effects helps in preventing structural weaknesses in products. ↩
-
Learning best practices aids in optimizing molding processes to reduce defects. ↩
-
Learn about the impact of injection pressure on defects like stream marks for better molding outcomes. ↩
-
Explore why consistent mold temperature is crucial to prevent defects like silver streaks. ↩
-
Discover strategies to enhance the quality and appearance of plastic products through effective molding techniques. ↩
-
Learn how high pressure affects plastic flow and causes defects. ↩
-
Discover why proper drying of plastics like nylon or ABS is crucial. ↩
-
Learn about internal stress in plastic manufacturing and its impact on product quality and performance. ↩
-
Discover how excessive internal stress leads to deformation in manufactured products. ↩
-
Explore effective stress-relieving techniques that enhance product durability and reduce defects. ↩