Navigating the landscape of injection-molded plastics can feel overwhelming, but it’s essential for crafting durable products that stand the test of time.
Polycarbonate (PC) is generally regarded as the strongest injection-molded plastic, known for its high tensile strength, excellent toughness, and strong weather resistance.
While polycarbonate takes the crown for strength, exploring other high-strength plastics can significantly enrich your material selection journey.
Polycarbonate is the strongest injection-molded plastic.True
Polycarbonate is known for its high tensile strength, toughness, and weather resistance.
What Makes Polycarbonate So Strong?
Polycarbonate (PC) stands out in the realm of injection-molded plastics due to its robust properties.
Polycarbonate’s strength is attributed to its high tensile strength, remarkable toughness, and superior weather resistance.
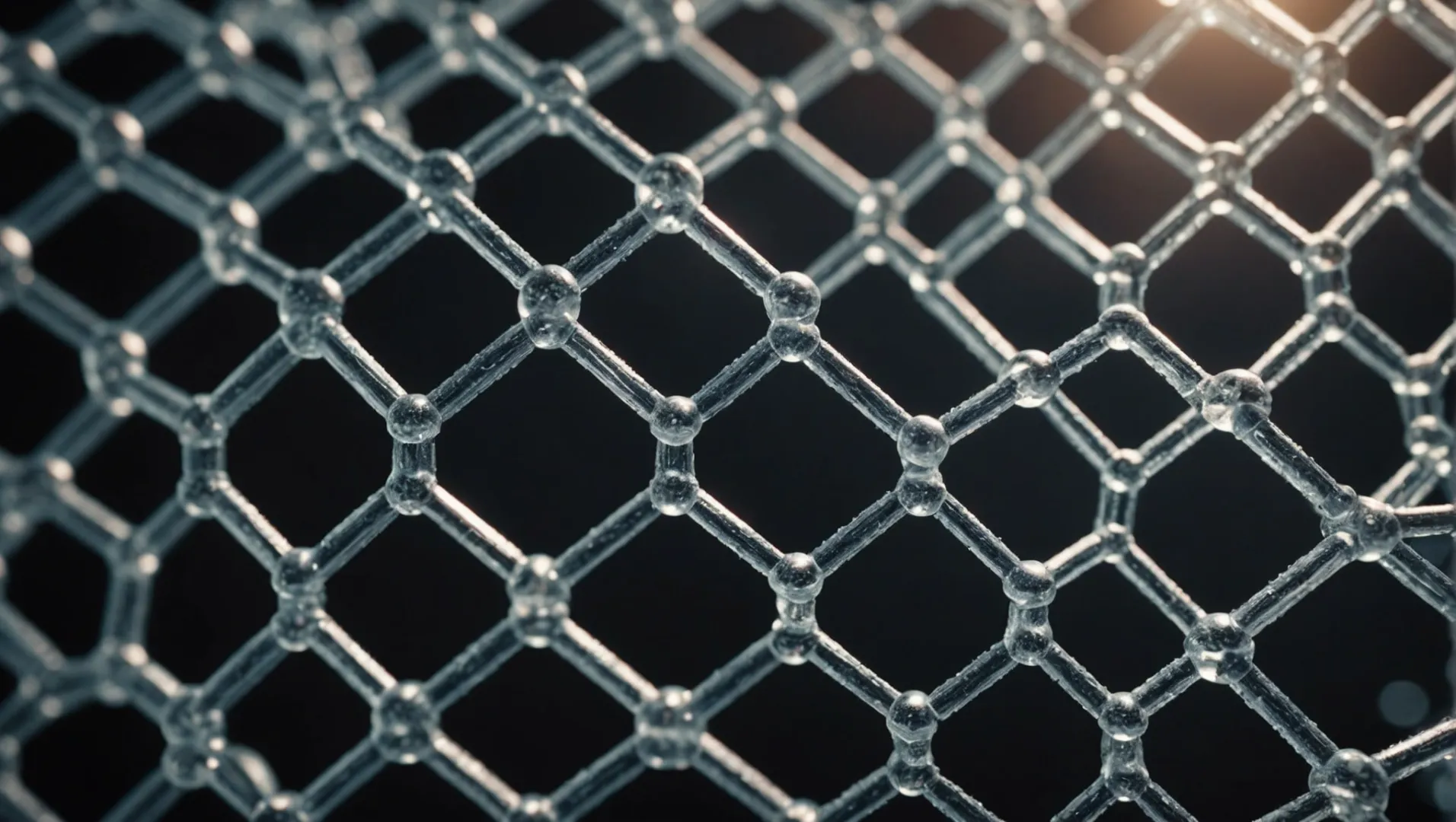
Understanding Polycarbonate’s Composition
Polycarbonate is a synthetic polymer renowned for its unique combination of strength and versatility. Its chemical structure consists of carbonate groups, which provide the foundation for its notable mechanical properties.
High Strength Attributes
One of the key reasons behind polycarbonate’s strength is its high tensile strength, which allows it to endure significant stretching and pulling forces without breaking. This makes it an ideal choice for applications requiring durable materials that can withstand stress.
Additionally, polycarbonate exhibits impressive bending strength, enabling it to resist deformation when subjected to bending forces. This property is particularly beneficial in applications where structural integrity is paramount.
Property | Benefit |
---|---|
High Tensile Strength | Resists stretching and pulling forces effectively |
Bending Strength | Maintains shape under bending stress |
Exceptional Toughness
Polycarbonate’s toughness is another critical factor contributing to its strength. It can absorb energy upon impact, reducing the likelihood of brittle fracture. This characteristic is crucial in industries such as automotive and construction, where materials must endure dynamic loads without failing.
Dimensional Stability
In environments with fluctuating temperature and humidity, polycarbonate maintains excellent dimensional stability. Its ability to retain shape and size under varying conditions ensures that components remain accurate and reliable over time. For detailed applications where precision is essential, such as optical lenses, this property is invaluable.
Weather Resistance and Transparency
Polycarbonate’s strong weather resistance shields it from UV rays, oxidation, and chemical corrosion, prolonging its lifespan even in harsh outdoor environments. Furthermore, its high transparency allows for the creation of clear products without sacrificing mechanical strength.
While polycarbonate stands out for these qualities, it’s important to compare it with other materials like glass fiber reinforced nylon1 or polyphenylene sulfide2 to determine the best fit for specific applications. Each material has unique attributes that cater to different industry needs.
Polycarbonate has high tensile strength.True
Polycarbonate can endure stretching and pulling forces effectively.
Polycarbonate is not weather resistant.False
Polycarbonate resists UV rays, oxidation, and chemical corrosion.
How Does Glass Fiber Reinforced Nylon Compare in Strength?
Glass fiber reinforced nylon is gaining attention for its impressive strength and versatile applications.
Glass fiber reinforced nylon (PA+GF) combines the toughness of nylon with the added strength of glass fibers, making it a robust alternative to other materials like polycarbonate (PC). This blend enhances its tensile strength, impact resistance, and dimensional stability, making it suitable for demanding environments.
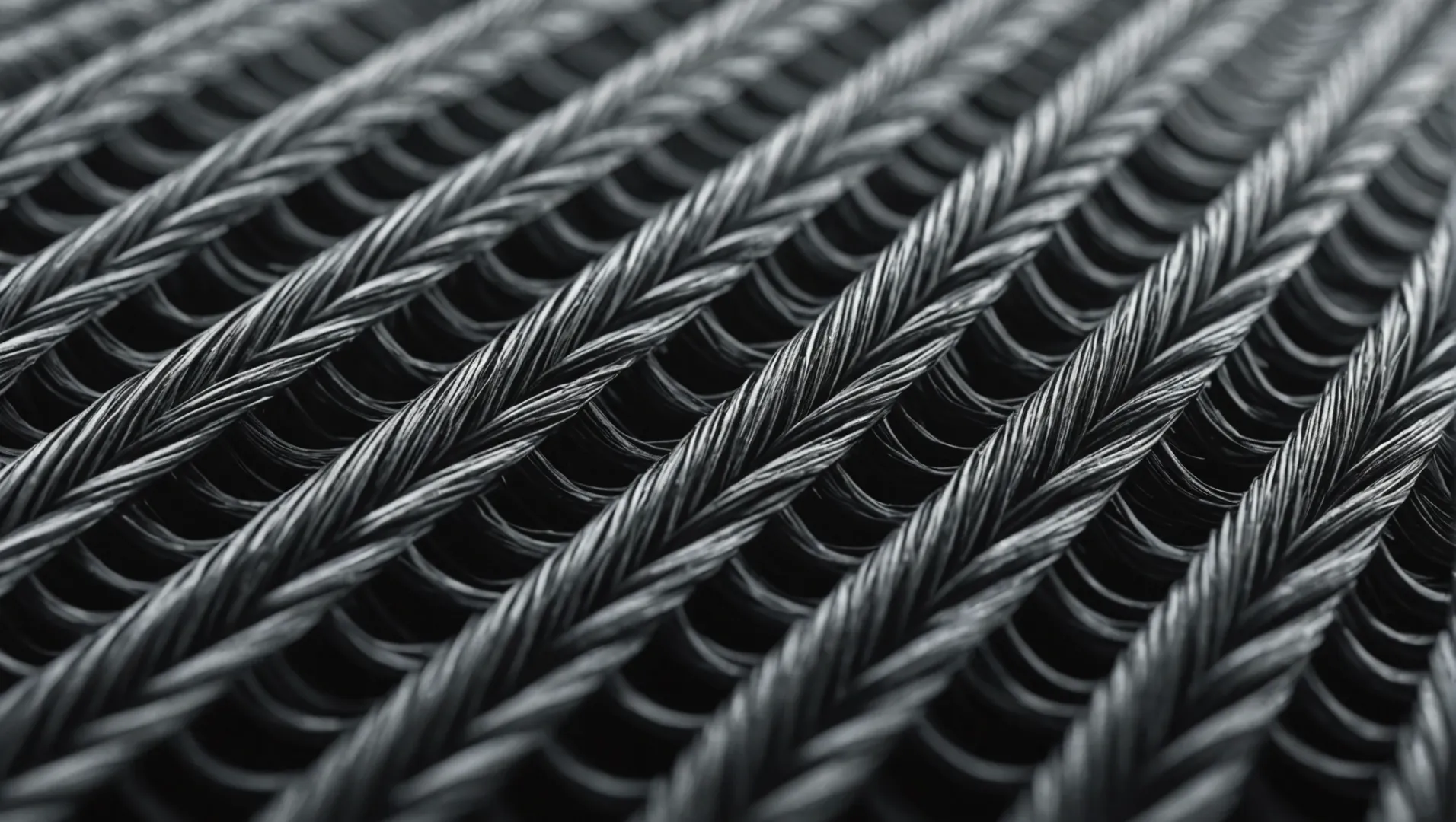
Understanding Glass Fiber Reinforced Nylon
Glass fiber reinforced nylon is a composite material formed by blending nylon, typically nylon 6 or nylon 66, with glass fibers. This combination leverages the benefits of both components to produce a material that excels in various mechanical properties.
-
Tensile Strength: The inclusion of glass fibers significantly enhances the tensile strength of nylon. This improvement allows glass fiber reinforced nylon to withstand higher loads without deformation, making it ideal for high-stress applications such as automotive components and industrial machinery.
-
Impact Resistance: While traditional nylon already offers good toughness, the addition of glass fibers improves its ability to absorb impact energy. This characteristic is crucial in applications where sudden forces are encountered, ensuring the material maintains integrity and performance.
-
Dimensional Stability: One of the notable features of glass fiber reinforced nylon is its stability under varying environmental conditions. It exhibits low thermal expansion and moisture absorption, which contributes to maintaining consistent dimensions over time. This property makes it suitable for precision parts where dimensional accuracy is critical.
Comparing with Polycarbonate
While polycarbonate3 is renowned for its high strength and versatility, glass fiber reinforced nylon presents a compelling alternative in specific contexts:
-
Weight Considerations: Glass fiber reinforced nylon typically offers a better strength-to-weight ratio compared to polycarbonate, which can be advantageous in applications where weight reduction is essential.
-
Cost Efficiency: Generally, glass fiber reinforced nylon can be more cost-effective than polycarbonate, especially when considering long-term durability and performance in specific scenarios.
-
Heat Resistance: While polycarbonate can withstand considerable heat, glass fiber reinforced nylon offers better performance in higher temperature ranges, making it preferable in certain high-heat environments.
Application Insights
The choice between these materials often hinges on specific application needs. For instance:
- Automotive industry prefers glass fiber reinforced nylon for parts like engine covers due to its thermal stability.
- Electronics often utilize polycarbonate for transparent components that also require electrical insulation properties.
By evaluating these aspects, engineers and designers can make informed decisions tailored to their project requirements.
Glass fiber reinforced nylon is stronger than polycarbonate.True
The glass fibers enhance tensile strength, surpassing polycarbonate.
Polycarbonate has better heat resistance than glass fiber nylon.False
Glass fiber reinforced nylon performs better in high temperatures.
Are There Alternatives to Polycarbonate for High-Strength Applications?
Polycarbonate stands out in high-strength applications, but are there viable alternatives?
Yes, there are alternatives to polycarbonate, such as glass fiber reinforced nylon and polyphenylene sulfide, which also offer high strength and durability.
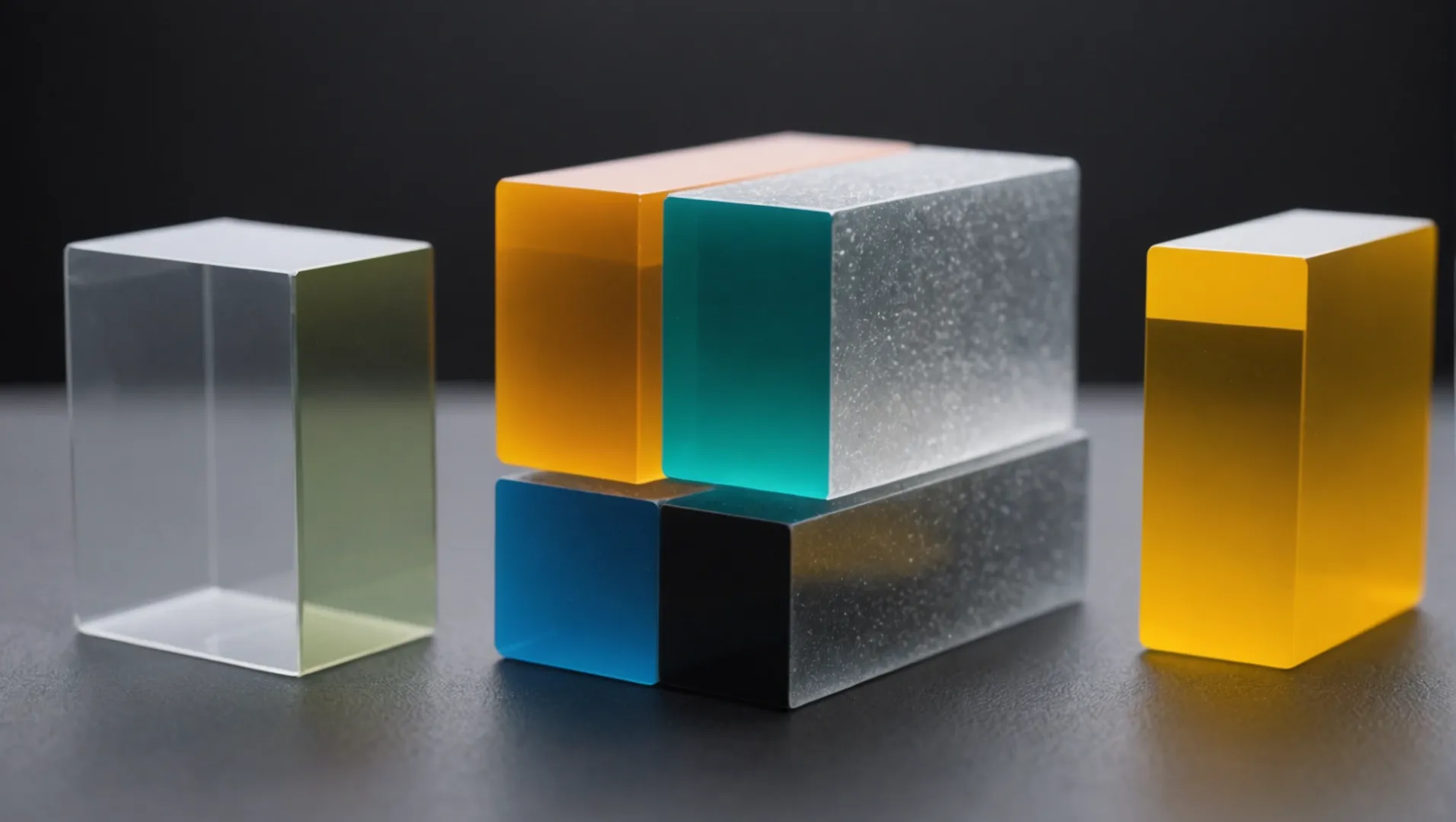
Understanding the Need for Alternatives
While polycarbonate4 is celebrated for its exceptional properties, the demand for alternative materials often arises due to cost considerations, specific application requirements, or environmental factors.
Exploring Glass Fiber Reinforced Nylon
Glass fiber reinforced nylon (PA+GF) emerges as a strong contender when looking for alternatives. This composite material combines the flexibility of nylon with the added strength of glass fibers, offering enhanced mechanical properties. The high tensile strength and impact resistance make it suitable for automotive parts and industrial machinery components.
Property | Polycarbonate (PC) | Glass Fiber Reinforced Nylon (PA+GF) |
---|---|---|
Tensile Strength | High | High |
Impact Resistance | Excellent | Excellent |
Weather Resistance | Strong | Moderate |
Analyzing Polyphenylene Sulfide (PPS)
Polyphenylene sulfide (PPS) is another remarkable alternative known for its outstanding thermal stability and chemical resistance. PPS is often used in high-temperature environments, such as electrical housings and automotive components. Its dimensional stability under stress further enhances its appeal in precision engineering applications.
Choosing the Right Material
Selecting an appropriate alternative to polycarbonate involves assessing various factors such as mechanical requirements, environmental conditions, and cost constraints. Material testing5 and prototyping can provide valuable insights into which material will best meet your project’s needs.
Each of these alternatives presents unique benefits and limitations. Ultimately, the choice depends on aligning the material’s properties with the specific demands of your application.
Glass fiber reinforced nylon has higher tensile strength than PC.False
Both materials have high tensile strength, but not higher than PC.
PPS is used in high-temperature environments.True
PPS is known for its thermal stability, suitable for such uses.
What Factors Should Be Considered When Selecting Injection Molded Plastics?
Selecting the right injection molded plastic involves balancing performance, cost, and application requirements.
Key factors in choosing injection molded plastics include application needs, mechanical properties, cost, and processing technology.
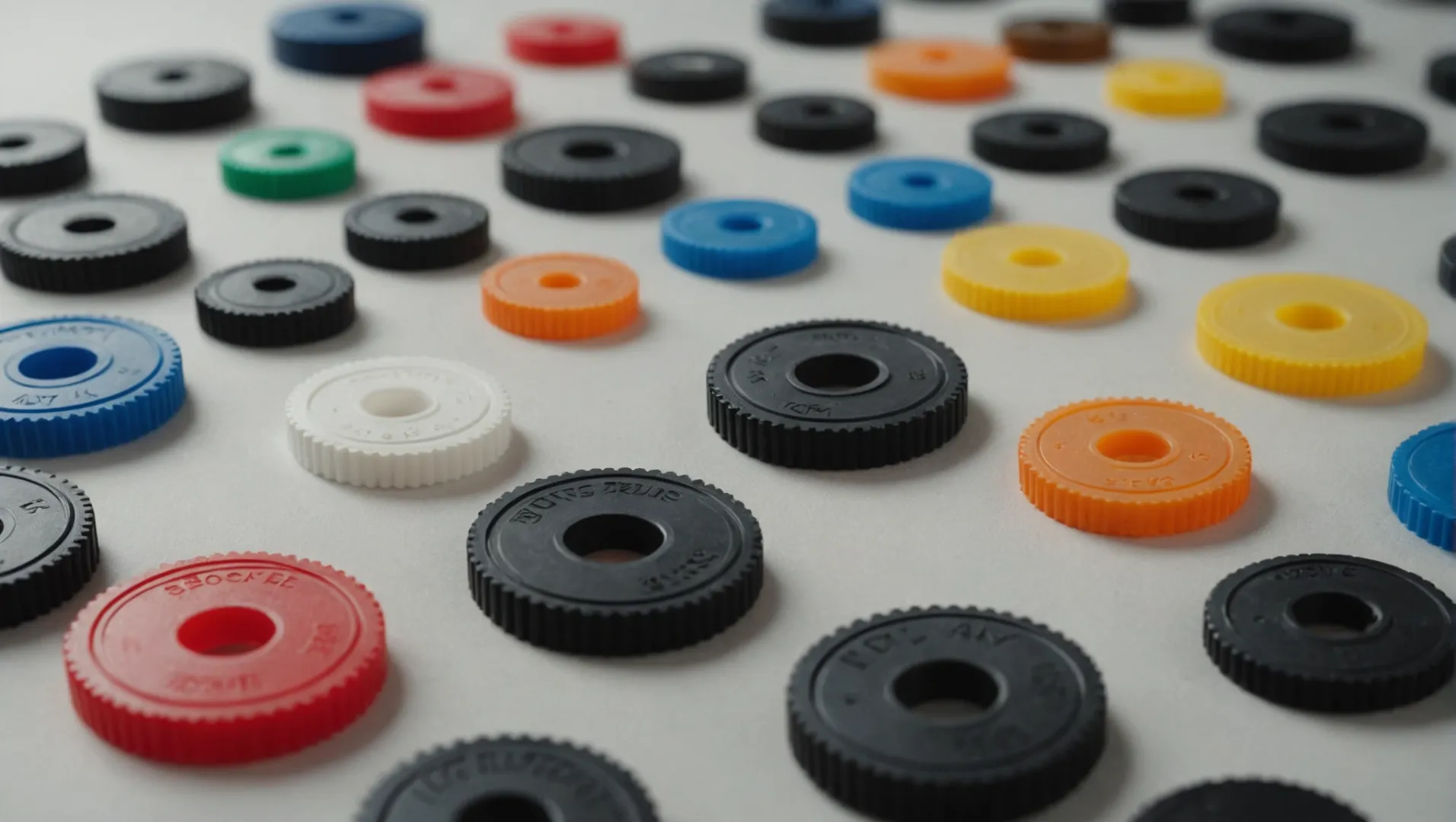
Understanding Application Requirements
Every project has unique demands, and understanding these is crucial for selecting the right plastic. Consider the environment in which the product will be used—factors like temperature, humidity, and exposure to chemicals can impact material choice. For example, if high transparency is necessary alongside mechanical strength, polycarbonate could be an optimal choice due to its excellent optical clarity and durability.
Evaluating Mechanical Properties
Mechanical properties such as tensile strength, impact resistance, and toughness are vital considerations. For applications requiring high strength and toughness, materials like polycarbonate6 or glass fiber reinforced nylon may be suitable. Polycarbonate offers high tensile and impact strength, making it ideal for products subjected to significant stress.
Considering Cost and Efficiency
Cost is often a limiting factor. Balancing cost with performance can be challenging but is essential for maintaining project budgets. Consider not only the material cost but also how processing technology might affect overall expenses. Glass fiber reinforced nylon, for instance, can offer a cost-effective solution for certain high-strength applications.
Processing Technology and Feasibility
The processing technology available can influence material selection. Some materials require specialized equipment or conditions, affecting feasibility and cost-effectiveness. For instance, polyphenylene sulfide (PPS) might be chosen for its thermal stability, but it requires precise control during molding processes.
Exploring Alternatives
While polycarbonate is renowned for its strength, exploring alternatives like polyphenylene sulfide or glass fiber reinforced materials can unveil other benefits specific to your application. Each material brings unique properties that might better align with certain product goals.
Factor | Example Material | Key Property |
---|---|---|
Strength | Polycarbonate | High tensile strength and toughness |
Cost | Glass Fiber Nylon | Cost-effective for high-strength needs |
Processing | Polyphenylene Sulfide | Requires precise molding conditions |
Understanding these factors enables informed decision-making when selecting injection molded plastics, ensuring optimal performance and efficiency in final products.
Polycarbonate is ideal for high transparency needs.True
Polycarbonate offers excellent optical clarity, suitable for transparent applications.
Glass fiber reinforced nylon is expensive for all uses.False
It is cost-effective for high-strength applications, not expensive for all uses.
Conclusion
Polycarbonate shines in strength among injection-molded plastics, but assessing application-specific needs is vital for optimal material selection.
-
Compare nylon’s performance attributes to polycarbonate’s for informed material choice.: Polycarbonate offers high toughness and heat resistance ideal for durable and high-impact applications, while Nylon provides lightweight, wear-resistant, and … ↩
-
Discover PPS benefits in specialized applications compared to polycarbonate.: Mechanical Properties PPS has high strength, high rigidity and low degradation characteristics even in high temperature conditions. It also … ↩
-
Explore why polycarbonate stands out in plastic applications.: Lightweight – Polycarbonate is relatively lightweight when compared to glass and other plastic materials making it easier for transportation and installation … ↩
-
Discover more about polycarbonate’s distinct mechanical properties.: Polycarbonate (PC) is a transparent thermoplastic. Its high strength makes it resistant to impact and fracture. It is lightweight so an excellent … ↩
-
Learn why material testing is crucial in selecting the right plastic.: It helps engineers and scientists understand material properties, optimize designs, and develop innovative solutions to various challenges. ↩
-
Learn more about polycarbonate’s exceptional mechanical strengths.: Ball Indentation Hardness, 95.0 – 120 MPa, 13800 – 17400 psi ; Tensile Strength, Ultimate, 28.0 – 75.0 MPa, 4060 – 10900 psi ; Tensile Strength, Yield, 39.0 – 120 … ↩