Do you ever think about what creates the gadgets we use every day to be so trustworthy and well-designed?
A cooling system in injection molding optimizes performance by reducing cycle times, enhancing product quality, minimizing deformation, and extending mold lifespan through effective temperature control.
These are just the basics. Picture your favorite gadget. Maybe it’s your phone or a clever kitchen tool. Think about how a great cooling system speeds up production. It saves money too. Quality stays the same. It’s like having a secret weapon. It gives you a competitive edge. Your products become better, quicker and more economical. Whether you seek improved designs or want to reduce expenses, understanding this aspect truly changes the game.
Cooling systems reduce injection mold cycle times.True
Cooling systems speed up the cooling process, reducing cycle times.
A cooling system increases mold surface defects.False
Cooling systems minimize surface defects by controlling temperature.
What Are the Key Components of a Mold Cooling System?
Have you ever thought about how mold cooling systems work?
The main parts of a mold cooling system are cooling channels, temperature control units and heat exchangers. These parts efficiently remove heat from the mold. Rapid cooling happens because of this. Product quality improves.
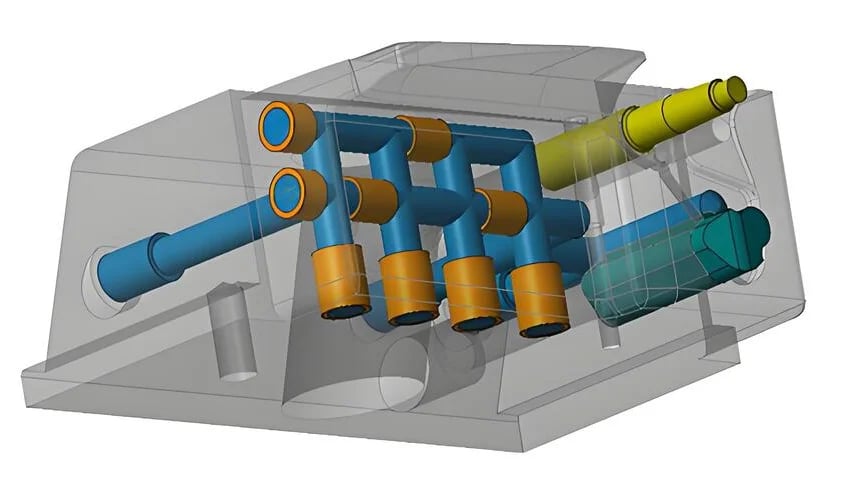
Cooling Channels
I remember the first time cooling channels showed their importance. It felt like discovering a secret to productivity. These channels function like the mold’s veins. They carry a cooling medium, often water or oil, throughout. The medium absorbs and removes heat from the plastic melt. Precise design in these channels is really crucial.
Design Considerations:
- Channel Layout: Even cooling is key. It prevents bothersome product deformations. I once faced a project with an uneven layout. The result was warped products. That experience taught me layout is everything.
- Uniform distribution of cooling channels helps in achieving even cooling1 across the mold, reducing the risk of product deformation.
- Channel Size: Larger channels allow better flow; however, they must balance to not weaken mold.
- Larger channels can facilitate better flow but may require more material removal, impacting mold strength.
Temperature Control Units (TCUs)
TCUs are very important. They keep the cooling medium at the right temperature. The units adjust through heating or chilling as needed. TCUs are like thermostats for your mold. Every batch gets consistent quality.
Component | Function |
---|---|
Heater | Increases medium temperature when needed |
Chiller | Reduces medium temperature |
Proper calibration of TCUs is really crucial. Once, a batch failed because of slight miscalibration. That taught me an important lesson.
Heat Exchangers
In complex molds needing rapid heat removal, heat exchangers are amazing. They transfer heat from the mold to the cooling medium.
- Efficiency: They probably increase system efficiency by maximizing heat transfer rates.
- Design: Their compact form fits snugly into tight spaces, making them ideal for complex molds.
Additional Elements
- Flow Regulators: Adjusting flow rate is vital for fine-tuning cooling efficiency. A small change can prevent many headaches later and can be essential for fine-tuning cooling efficiency2.
- Pressure Sensors: Sensors watch pressure levels to prevent damage and keep operations smooth by monitoring and maintaining optimal pressure levels within the system.
Reflecting on experiences, a balanced cooling system shortens molding cycles and increases productivity while extending mold life—essential in any efficient production line. These components working together transform challenges into smooth operations.
Cooling channels are crucial for mold cooling systems.True
Cooling channels circulate a medium to absorb and remove heat from the mold.
Temperature control units only cool the medium.False
TCUs can both heat and cool the medium to maintain desired temperatures.
How Does Cooling Time Impact Production Efficiency?
Cooling time greatly affects production efficiency. It helps a lot. This time period determines how fast and smooth products are made. Shorter cooling might speed up work, but it could harm quality. Quality matters. Longer cooling often means better product quality. However, it might slow down production. Balancing cooling time is tricky but very important. Effects on efficiency are probably significant. Hence, understanding cooling time benefits production processes.
Cooling time influences production effectiveness by affecting cycle duration, product quality and mold lifespan. Optimizing cooling systems very likely reduces cycle times. Improved product quality and longer mold life also probably result from this optimization. Efficiency really increases.
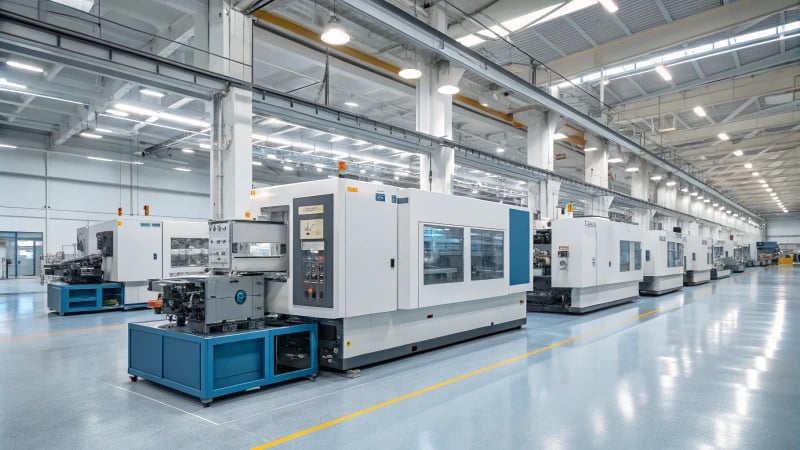
The Role of Cooling Time in Production Efficiency
I recall the first time I observed an injection molding machine3. Watching molten plastic turn into a solid shape was fascinating. What really stayed with me was realizing how important cooling time is in this process. Cooling time is not just waiting; it’s a key element that determines the efficiency of production.
In injection molding, cooling time takes up a large portion of the total cycle time. Understanding this was like a light bulb moment for me. Reducing that cooling time isn’t only about speeding things up. It transforms the entire manufacturing process. Imagine cutting cooling times from 30-60 seconds to 10-20 seconds for products with 3-5mm thickness. That’s a major improvement.
Aspect | Without Efficient Cooling | With Efficient Cooling |
---|---|---|
Cooling Time | 30-60 seconds | 10-20 seconds |
Production Output | Lower | Higher |
Improving Product Quality
Optimizing cooling affects both speed and quality. I worked on a project where a large flat plastic panel warped due to uneven cooling. We had to rethink everything to achieve consistent cooling throughout. With an equally distributed cooling system4, we reduced warping and improved dimensional accuracy.
Proper cooling also enhances the physical properties of plastics like polyamide (PA). It strengthens the plastic by allowing a uniform crystalline structure to form during cooling, enhancing strength, hardness, and toughness. Stronger, more reliable products result from this careful attention.
Extending Mold Life
I learned early that molds are precious in injection molding. Keeping them in excellent condition is crucial. High temperatures can wear down mold materials quickly, causing costly repairs or replacements. An effective cooling system5 maintains optimal mold temperatures, preserving mold integrity.
Benefit | Description |
---|---|
Reduced Temperature | Preserves mold material properties |
Less Wear | Minimizes abrasion and adhesion issues |
Effective cooling reduces friction and thermal expansion effects, meaning less maintenance and longer-lasting molds. It’s not just about saving money; it’s about ensuring smooth, uninterrupted production cycles.
Understanding these aspects allows me to significantly increase production efficiency through cooling time optimization. This improvement is not just about reducing time; it’s about enhancing quality, lowering costs, and achieving stable operations. By focusing on these aspects, I’ve seen firsthand how they drive success in injection molding processes.
Efficient cooling reduces cycle time by 50%.True
Efficient cooling systems can halve cooling times from 30-60 to 10-20 seconds.
Uneven cooling increases product deformation risk.True
Uniform cooling reduces warping and deformation, ensuring product stability.
How Does Uniform Cooling Affect Product Quality?
Ever wonder why some plastic products look perfect while others appear damaged? The cooling process in injection molding is the key. It’s very important!
Uniform cooling in injection molding plays a key role in keeping product quality high. It helps maintain an even temperature distribution. This uniformity stops deformation. Surface quality improves with good temperature distribution. Physical properties become better. Consistent product standards remain achievable with uniform cooling.
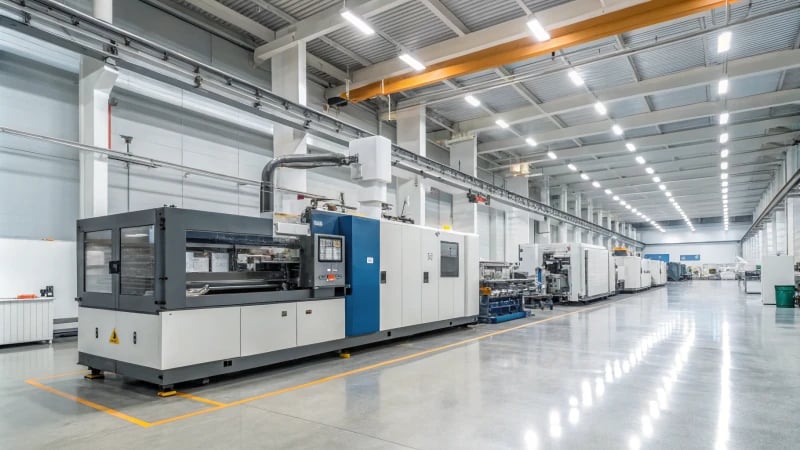
The Importance of Even Cooling
Even cooling is crucial in the injection molding6 process as it directly impacts the dimensional stability of the product. Uneven cooling can lead to warping or bending, which affects the final product’s quality.
Example Scenario:
I remember my first major project as a product designer. I worked late nights to perfect a big flat plastic part. The excitement of seeing the prototype quickly vanished when I saw it had warped. That frustration led me to understand even cooling better.
Consider a large flat piece that warps because one side cooled faster than the other. By designing a cooling system with evenly spread coolant, manufacturers can prevent these mishaps and ensure both sides cool at the same rate.
Parameter | Effect on Product Quality |
---|---|
Even Cooling | Prevents Warping |
Uneven Cooling | Causes Deformation |
Influence on Surface Quality
Surface quality is also significantly affected by even cooling. A well-designed cooling system controls the cooling speed, avoiding common flaws like shrink marks or flow lines.
Case Study:
I recall working on plastic covers for electronic devices where achieving a sleek finish was essential. An effective cooling system avoids defects such as indentations from fast cooling or visible marks from slow cooling, thus optimizing surface aesthetics.
Improving Physical Properties
When using crystalline plastics like polyamide (PA), even cooling influences more than just appearance; it affects strength and toughness too.
Technical Insight:
Consistent temperature ensures a uniform crystalline structure within the material, enhancing its mechanical properties7.
Economic Advantages
Economic benefits are also significant with effective even cooling systems. Shortening the molding cycle by speeding up cooling greatly increases productivity and reduces costs.
- Cooling Time Reduction:
- Without effective cooling: 30-60 seconds
- With effective cooling: 10-20 seconds
Cycle Time Reduction | Benefit |
---|---|
Shortened Cycle | Higher Productivity |
Increased Output | Lower Costs |
In summary, even cooling is not just about keeping products cool; it ensures product quality and manufacturing efficiency through improved systems like conformal cooling.
Uniform cooling prevents warping in injection molding.True
Uniform cooling ensures even temperature distribution, preventing deformation.
Uneven cooling improves surface quality of molded products.False
Uneven cooling causes defects like shrink marks and flow lines.
How Do Cooling Systems Enhance Injection Mold Longevity?
You know that happy feeling when everything fits perfectly? Cooling systems really help keep your injection molds in top condition.
Cooling systems increase the lifespan of injection molds. They control temperatures in an efficient way. This reduces wear, tear and thermal fatigue. Molds keep their material properties. Their performance improves and they really last longer.
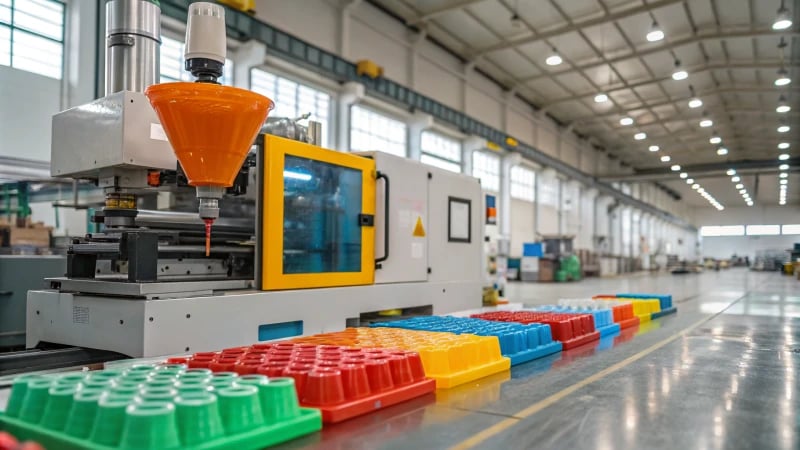
The Role of Cooling Systems in Mold Longevity
Cooling systems play a vital role in extending the life of injection molds by effectively managing mold temperatures. During the injection molding process, high-temperature plastic melt transfers heat to the mold. Without adequate cooling, this can lead to excessive heat buildup, reducing the hardness of mold materials and increasing thermal fatigue.
Benefits of Proper Cooling
-
Temperature Control
- Reducing mold temperature keeps its material properties intact. It maintains hardness and prevents thermal fatigue.
-
Reduced Wear and Tear
- Temperature stabilization decreases friction between mold parts due to thermal expansion.
- It also reduces plastic sticking8 to the mold surface.
Benefit | Description |
---|---|
Reduced Mold Temperature | Maintains material hardness, preventing thermal fatigue. |
Lower Friction | Reduces wear caused by expansion and contraction. |
Less Cleaning | Prevents adhesion, minimizing cleaning frequency. |
Example of Effective Cooling
Consider molds made from hot work steel like H13. These molds crack from heat if used in high-heat areas for too long. A good cooling system reduces this risk by efficiently dissipating heat, ensuring longevity and reducing maintenance costs.
Moreover, when dealing with glass-filled plastics, the cooling system minimizes abrasion on the mold surface, thus extending its operational life.
To understand how these systems affect injection molds, explore mold maintenance techniques9 for more tips on optimizing cooling setups and improving manufacturing efficiency.
Cooling systems prevent thermal fatigue in molds.True
Proper cooling maintains material hardness, reducing thermal fatigue.
High mold temperatures increase the lifespan of injection molds.False
High temperatures cause wear and reduce mold material hardness.
Conclusion
Cooling systems in injection molding enhance performance by reducing cycle times, improving product quality, and extending mold life through efficient temperature control and uniform cooling.
-
Learn how uniform channel distribution minimizes product defects like warping or shrinkage. ↩
-
Explore how flow regulators optimize cooling by adjusting medium flow rates for precise control. ↩
-
Explore the basics of injection molding to understand how cooling time fits into the overall process. ↩
-
Discover how uniform cooling designs prevent product deformation in injection molding. ↩
-
Understand how optimizing mold cooling systems enhances longevity and efficiency. ↩
-
Explore how uniform cooling impacts the injection molding process, including benefits for dimensional stability and defect prevention. ↩
-
Learn about how controlling crystallinity through uniform cooling can enhance material strength and toughness. ↩
-
Understanding how cooling systems prevent adhesion can help enhance mold maintenance strategies. ↩
-
Discovering maintenance techniques can improve mold lifespan and optimize production processes. ↩