Ever wondered how the right design can transform manufacturing? Let me tell you about my journey with Design for Manufacturability (DFM) and its impact on injection molding.
Design for Manufacturability (DFM) improves injection molding by incorporating manufacturing processes into the design phase, ensuring mold feasibility, reducing costs, and enhancing production efficiency and quality.
Reflecting on my early days in the field, I recall struggling to balance design creativity with manufacturing practicality. It wasn’t until I embraced DFM principles that things started clicking. By focusing on aspects like product structure, mold design, and material selection, I learned that each choice influences the end product’s success. For instance, designing with uniform wall thickness can prevent pesky issues like shrinkage or warping. Similarly, thoughtful rib and draft angle designs can add strength without adding unnecessary weight or material costs.
In mold design, I’ve found that positioning the parting line and gate correctly can be game changers. A well-placed parting line simplifies the mold structure while a strategically chosen gate enhances melt flow. And let’s not forget the ejector mechanism—it’s crucial for ensuring parts exit molds smoothly.
Material selection also plays a vital role. Early in my career, I once chose a material based solely on cost, only to face performance failures later on. Now, I balance cost with properties like strength and compatibility to avoid such pitfalls.
Embracing DFM has been a journey of discovery and growth, opening doors to innovation and efficiency in my projects. Let’s explore these DFM elements further so you can experience the same benefits in your work.
DFM reduces injection molding production costs by 30%.False
While DFM can reduce costs, the exact percentage varies widely based on specific projects and implementations.
DFM considers mold feasibility in the design phase.True
DFM integrates mold feasibility early to ensure designs are manufacturable and cost-effective.
- 1. What Are the Key Principles of DFM in Injection Molding?
- 2. How Does Wall Thickness Influence Injection Molding Quality?
- 3. Why Is Proper Mold Design Essential for DFM?
- 4. How Important is Material Selection in Design for Manufacturability?
- 5. How Can DFM Reduce Costs in Injection Molding Projects?
- 6. Conclusion
What Are the Key Principles of DFM in Injection Molding?
Ever wonder what really makes a product design click in manufacturing? It’s all about Design for Manufacturability (DFM) in injection molding.
DFM in injection molding emphasizes optimizing design and mold creation for efficient, quality, cost-effective production by ensuring consistent wall thickness, selecting appropriate materials, and implementing strategic mold designs.
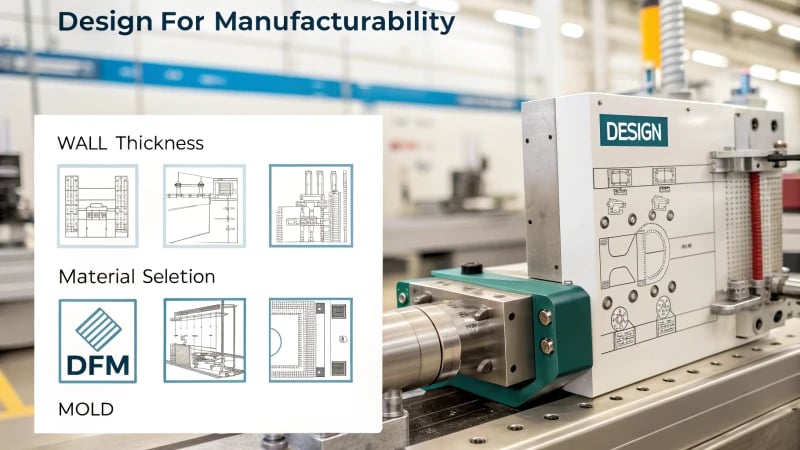
I remember the first time I dove into the world of injection molding; it was like cracking open a puzzle box full of engineering challenges and creative opportunities. The principles of DFM were my guiding stars, ensuring that every product I designed could be manufactured smoothly and economically.
Product Structure Design
Wall Thickness Design
I’ve learned that uniform wall thickness is the unsung hero of a quality injection-molded part. In my early projects, I underestimated its importance, leading to warped prototypes. By keeping wall thickness between 1-3mm, and smoothing out transitions, I saw a remarkable decrease in defects.
Wall Thickness | Importance |
---|---|
Uniform | Prevents uneven shrinkage |
Transition | Reduces stress concentration |
Rib Design
Adding ribs was a revelation. They boost strength without bulking up weight. I found that keeping ribs at 60% or less of the wall thickness, and ensuring a draft angle of at least 0.5°, made demolding a breeze. Rib Design Guide1
Mold Design
Parting Line Design
Strategically placing parting lines was like playing chess; it simplified mold construction and kept costs down. I always aim for placements that are out of sight but keep the product’s look intact.
Gate Design
Choosing the right gate location felt like an art form. A well-placed gate ensures smooth plastic flow, reducing defects like weld marks. Gate Design Techniques2
Material Selection
Material Performance Matching
Material choice can make or break a product. I often weigh mechanical, thermal, and chemical properties to match the product’s needs. Polycarbonate, for instance, is my go-to for strength and toughness.
Material Type | Recommended Use Cases |
---|---|
Polycarbonate | High-strength requirements |
Polypropylene | Cost-effective applications |
Cost and Supply Stability
Balancing performance with cost is crucial. For projects with flexible requirements, I lean towards common plastics like polypropylene for their affordability and availability. Material Selection Tips3
Ejector Mechanism Design
I’ve found that a well-chosen ejection method—be it push plate or ejector pin—ensures smooth part removal, especially for complex designs.
By weaving these principles into my work, I’ve been able to cut costs and enhance product quality consistently. For anyone involved in injection molding design, these strategies are not just helpful—they’re essential.
Uniform wall thickness prevents warping in injection molding.True
Uniform thickness ensures even cooling and shrinkage, preventing warping.
Ribs should be 80% of wall thickness for optimal strength.False
Ribs should be no more than 60% of wall thickness to avoid stress.
How Does Wall Thickness Influence Injection Molding Quality?
When I first started in the world of injection molding, I quickly learned that wall thickness wasn’t just a number; it was the heartbeat of the process.
Uniform wall thickness in injection molding prevents defects such as warping and sink marks. Proper transitions and rib structures enhance structural integrity, ensuring high-quality outcomes.
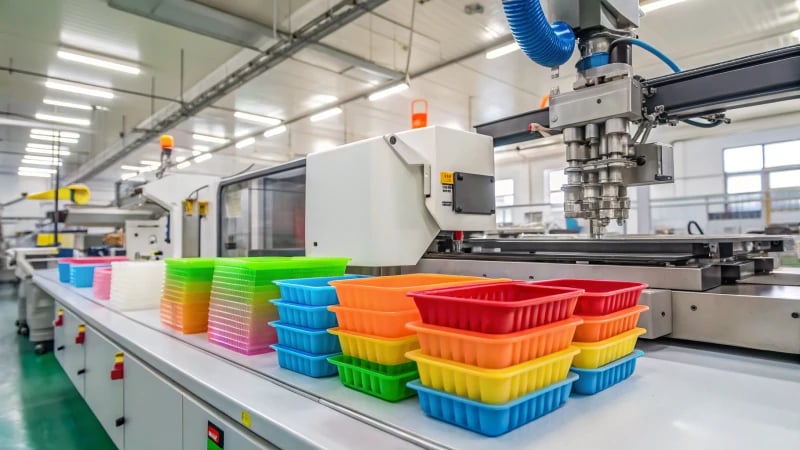
The Importance of Uniform Wall Thickness
I remember the first time I encountered a part with inconsistent wall thickness—it was a mess! Thicker sections cooled slower than the thinner ones, leading to nasty warping. This taught me the importance of uniformity in wall thickness. By keeping it consistent, I can avoid stress concentrations and ensure even cooling, reducing risks of defects like cracks or distortions.
Imagine designing a product only to see it warp due to uneven shrinkage. This can ruin dimensional accuracy and appearance. But with careful design, such nightmares are avoidable.
Best Practices for Wall Thickness Design
- Maintain Consistency: Keep adjacent wall thickness differences within 25% to minimize quality issues. I’ve found this simple rule can make a world of difference.
- Smooth Transitions: Gradual changes like slopes or arcs in thickness improve flow and reduce stress. In my designs, this has been crucial for maintaining structural integrity.
Wall Thickness | Recommended Range |
---|---|
Small Parts | 1 – 3 mm |
Large Parts | 2 – 4 mm |
Following these guidelines has been vital for me as an injection molding4 expert, ensuring high-quality production every time.
Enhancing Strength with Rib Design
Integrating ribs into my designs has been a game-changer. They increase strength without adding much weight or cost. For me, ensuring rib thickness is no more than 60% of the main wall thickness is a golden rule.
- Draft Angle: A minimum of 0.5° draft angle makes demolding smooth—a lesson I learned the hard way!
- Height Considerations: Avoid overly tall ribs; they complicate ejection.
Effective rib design5 is key to preventing deformation and maintaining integrity under stress.
Transition Techniques and Stress Concentration
Transition areas between varying wall thicknesses need careful attention. Using arcs instead of sharp corners reduces stress concentration significantly. This ensures smooth plastic melt6 flow within the mold cavity, preventing weak spots.
Understanding these aspects of wall thickness has improved my injection molding outcomes, achieving both aesthetic and functional excellence in products. These practices also align with Design for Manufacturability (DFM) principles, optimizing from design to final delivery.
Uniform wall thickness reduces warping in injection molding.True
Even cooling and solidification prevent defects like warping.
Rib thickness should be 80% of the main wall thickness.False
Rib thickness should be 50% or less of the main wall thickness.
Why Is Proper Mold Design Essential for DFM?
Ever wondered why the intricacies of mold design are such a big deal in manufacturing? Let me take you through it.
Proper mold design is essential for DFM as it ensures product quality, reduces costs, and enhances efficiency by optimizing parting lines, gates, and ejection systems to meet manufacturability and quality standards.
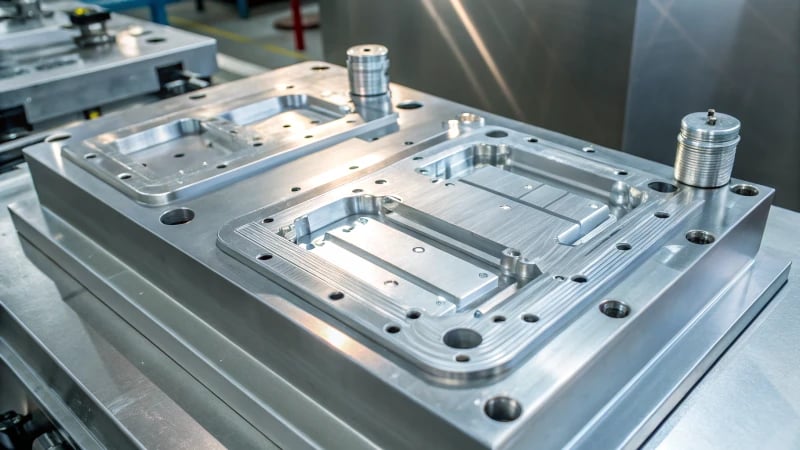
Understanding Design for Manufacturability (DFM)
So, what exactly is Design for Manufacturability (DFM)? Picture this: you’re designing a gadget from scratch, aiming to get the best bang for your buck while ensuring top-notch quality. DFM is like your behind-the-scenes partner, making sure every piece of the puzzle—from materials to mold—is just right from the get-go. It’s about marrying design with production in a way that’s efficient and cost-effective.
DFM Considerations | Key Aspects |
---|---|
Wall Thickness | Uniformity |
Rib Design | Strength |
Gate Design | Efficiency |
Product Structure Design
Wall Thickness Design: Imagine you’re baking a cake. If one side’s too thick, you risk uneven baking. In molding, uniform wall thickness prevents warping and other defects. Aim for a gradual transition, like gently sloping icing on a cake.
Rib Design: Ribs are like the backbone of your design. They add strength without weighing down the product. Think of them as reinforcing beams that keep everything stable without adding bulk.
Mold Design: Parting Line and Gate
Parting Line Design: The secret to an easy-to-use mold is a cleverly placed parting line—think of it as a hidden seam in a well-tailored suit. It keeps things simple and cost-effective.
Gate Design: The gate is where everything flows smoothly—or not! Proper positioning can make or break your product quality, much like choosing the right nozzle for icing a cake.
Ejector Mechanism and Material Selection
Ejector Mechanism Design: The magic of demolding without damage lies in selecting the right ejection method, akin to gently removing a cake from its pan without crumbling.
Material Performance Matching: Picking the right materials is like choosing ingredients for a recipe. Nylon, for instance, offers strength when you need it most.
The Role of Mold Design in DFM
Ultimately, mold design isn’t just about shaping plastic; it’s about shaping success. By aligning with DFM principles, mold design ensures products that aren’t just functional but also affordable and high-quality. It’s a delicate dance of creativity and practicality, ensuring each product is more than just a piece of molded plastic—it’s a testament to thoughtful engineering.
Uniform wall thickness prevents warping in molded parts.True
Uniform wall thickness minimizes stress and ensures even cooling, reducing warping.
Ribs should exceed 60% of wall thickness for strength.False
Ribs should not exceed 60% of wall thickness to avoid defects.
How Important is Material Selection in Design for Manufacturability?
Ever wondered how the materials you pick can make or break your product’s success? Let me share a little insight from my experience.
In Design for Manufacturability, selecting the right material is crucial for product performance, enhancing durability, reducing costs, and improving processing efficiency.
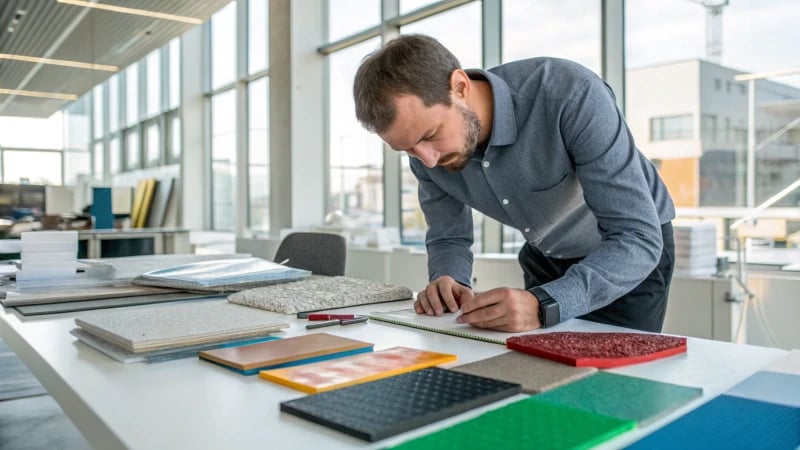
Understanding Material Performance
Material performance is a primary consideration in DFM. Selecting materials with the appropriate mechanical, thermal, and chemical properties ensures that the product meets its use requirements. For instance, engineering plastics like nylon (PA) or polycarbonate (PC) are ideal for products that need to withstand significant external forces.
To match material performance with product requirements, designers must consider the mechanical properties7 such as strength and toughness, as well as thermal properties like melting point. This detailed assessment helps maintain product integrity during usage.
Cost-Effectiveness and Supply Stability
Balancing performance with cost is a vital aspect of material selection. Choosing materials that are both affordable and readily available can significantly reduce production expenses. For example, general plastics like polypropylene (PP) are cost-effective for products without stringent performance needs.
Material | Cost | Availability |
---|---|---|
Nylon | High | Moderate |
PP | Low | High |
Ensuring a stable supply also mitigates risks of production delays and cost fluctuations, which is vital for maintaining a competitive edge.
Compatibility in Multi-Material Products
In products involving multiple materials, compatibility is key to preventing issues such as delamination. It’s crucial to ensure different materials can be combined effectively. This aspect of material selection often requires compatibility testing8 to verify that materials will bond without compromising structural integrity.
When considering multi-material designs, it’s essential to analyze both physical and chemical interactions between materials to avoid potential failures.
Environmental and Sustainability Considerations
Sustainability is becoming increasingly important in DFM. Material selection can contribute to eco-friendly design by using recyclable or biodegradable materials. This shift not only benefits the environment but can also improve the brand image.
Designers are encouraged to explore sustainable options9, balancing environmental impact with performance needs to create products that are both efficient and responsible.
Each of these factors highlights the integral role material selection plays in DFM, emphasizing its impact on product success from design through to manufacturing.
Nylon is cost-effective for high-performance needs.False
Nylon has high performance but is not cost-effective, with high costs.
PP is highly available and low-cost.True
Polypropylene (PP) is both affordable and readily available.
How Can DFM Reduce Costs in Injection Molding Projects?
Ever wondered how a simple tweak in design can save big bucks in injection molding?
DFM helps reduce costs in injection molding by optimizing product design, mold complexity, and material choices. This approach streamlines production, cuts down defects, and saves time and resources.
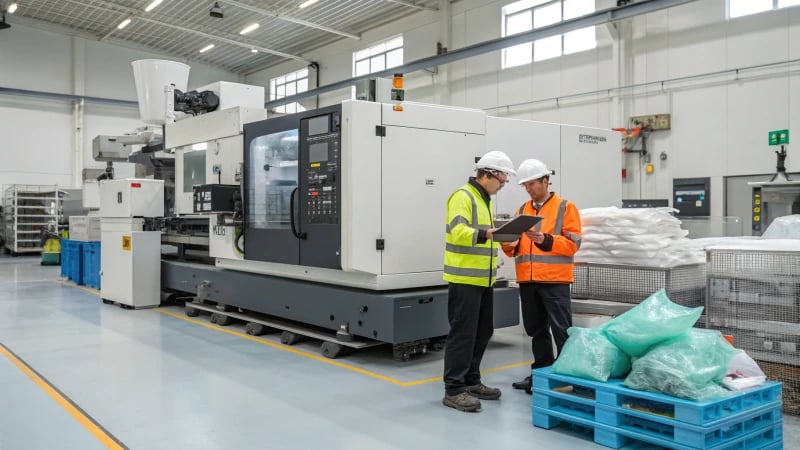
When I first dove into the world of injection molding, I was blown away by how much the design phase could influence costs. It’s like discovering that the secret to great cooking is not just the ingredients but how you prepare them.
Product Structure Design
Imagine this: designing a plastic part with the perfect wall thickness is like making the perfect pancake. Too thick, and it takes forever to cook; too thin, and it falls apart. In injection molding, maintaining wall thickness between 1-3mm with less than 25% variation avoids uneven shrinkage and ensures smooth production. Gradual transitions in thickness, using slopes or arcs, are key to avoiding stress points—much like flipping that pancake just right to keep it from sticking.
Table: Wall Thickness Guidelines
Parameter | Recommended Value |
---|---|
Overall Thickness | 1-3mm |
Variation | <25% |
Then there’s rib design. It’s all about adding strength without heft—like a good pair of hiking boots that are sturdy yet light. Ribs should be 60% of the wall thickness with a gentle draft angle of at least 0.5° to ensure easy removal from molds. Properly placed ribs prevent deformities, just as those boots help you tackle uneven trails.
Undercut and snap design simplifies assembly, much like clever packing makes travel a breeze. The size and shape should allow for smooth demolding and strong assembly, akin to packing cubes that fit perfectly into your suitcase.
Mold Design
Parting lines in molds are like seams in clothing—they need to be strategically placed to enhance both function and aesthetics. I learned that placing parting lines where they won’t mar the product’s appearance is crucial.
Gate design is another vital element. It’s like finding the right spot for a plant in your garden, ensuring it gets even sunlight. Positioning gates correctly ensures even melt flow, preventing defects like weld marks.
Material Selection
Choosing materials is akin to picking ingredients for a recipe—it’s all about balance. For high-strength needs, engineering plastics like nylon are go-to options. It’s like choosing whole wheat over white bread for a sandwich when you need that extra fiber.
Material cost and supply stability are also pivotal. Opting for affordable yet reliable materials like polypropylene can significantly cut costs without sacrificing quality.
Table: Material Recommendations
Material | Recommended Use |
---|---|
Nylon | High-strength applications |
Polypropylene | General injection molding |
Process Optimization
Implementing DFM principles is akin to meal prepping for the week: planning ahead to save time and stress later. By anticipating potential production challenges during design, we can streamline operations, reduce errors, and lower costs effectively.
For more insights on how DFM can further enhance efficiency in production10, consider exploring additional resources on this topic.
Uniform wall thickness prevents injection molding defects.True
Consistent wall thickness avoids shrinkage and stress, reducing defects.
Rib height should exceed 60% of wall thickness for strength.False
Ribs should be 60% of the wall thickness to prevent demolding issues.
Conclusion
Design for Manufacturability (DFM) optimizes injection molding by enhancing product design, mold feasibility, and material selection, leading to improved efficiency, quality, and cost-effectiveness in manufacturing processes.
-
Explore best practices in rib design to enhance product strength and rigidity without adding excess weight or cost. ↩
-
Learn effective gate positioning techniques to ensure quality and minimize defects in molded products. ↩
-
Discover tips on selecting materials that offer a balance of performance, cost, and supply stability. ↩
-
Explores fundamental concepts of injection molding, offering insights into processes that ensure part quality. ↩
-
Learn how rib design enhances structural integrity without compromising demoldability. ↩
-
Understand how plastic melt flow impacts the formation and quality of molded parts. ↩
-
Explore how engineering plastics like nylon offer superior mechanical properties beneficial for demanding applications. ↩
-
Learn about testing methods that ensure different materials bond effectively without structural issues. ↩
-
Discover eco-friendly materials that can be used in injection molding to enhance sustainability. ↩
-
Explore how DFM principles lead to streamlined manufacturing processes. ↩