I still remember the first time I had to pick a material for a mold. It felt like searching for the best shoes to run a very long race.
Picking the best mold material for precision injection molding relies on batch size, accuracy demands and surroundings. P20, H13 and S136 steel provide unique benefits. These materials resist wear and remain stable under heat. This is crucial for precise and long-lasting products. The choice of material is very important.
Choosing the right mold material often seems confusing. It takes me back to my early mold design days, juggling many choices. Start by considering your production batch size. P20 steel suits smaller batches because it’s cheap yet dependable. Next, think about precision꞉ I once worked on a product needing tight tolerance and I relied on S136 steel for its great stability.
Understanding these materials well helps you decide smartly. For example, H13 steel survives the tough needs of large-scale production. When strength matters, it’s a lifesaver. Focusing on these points improves accuracy and streamlines your process.
P20 steel is ideal for small batch mold production.True
P20 steel is cost-effective and pre-hardened, suitable for small batches.
H13 steel is unsuitable for high-temperature environments.False
H13 steel has high thermal stability, making it suitable for high temperatures.
What Should You Consider When Choosing Mold Materials?
Picking the best mold material feels like finding the ideal tool for a stunning creation. It influences all aspects!
When choosing mold materials, consider the production batch size. Think about how precise the product needs to be. Assess the working environment. Look for materials that are easy to process. Cost matters, too. These factors lead to very high-quality manufacturing. These choices help in efficient production.
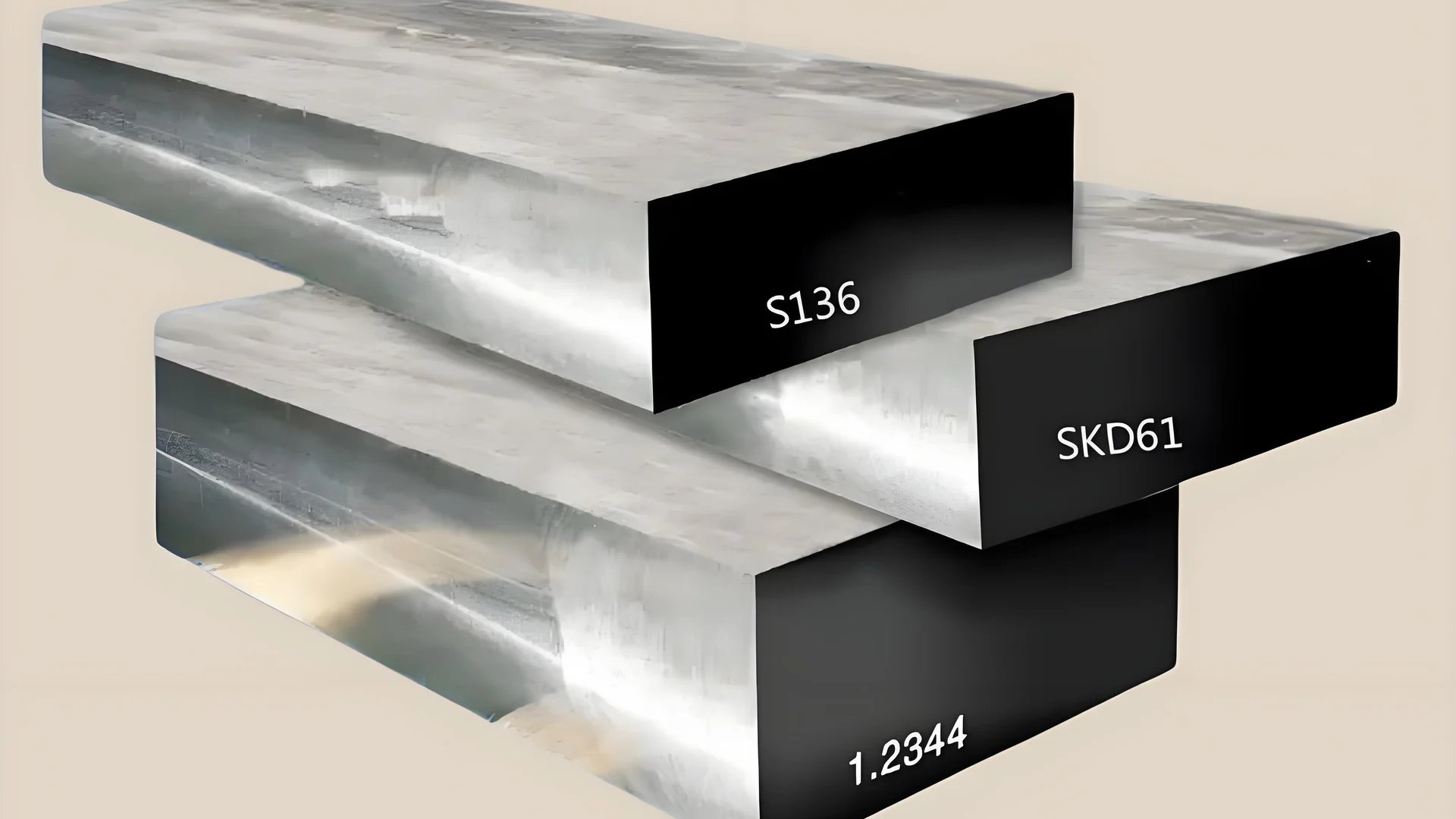
Understanding Production Batch Needs
When I started learning about mold design, I learned quickly that the size of production strongly affects which material to use. For small batches, like a few hundred pieces, P20 steel1 works well. It’s like picking a trusty old car that’s cheap but reliable. This steel is pre-hardened and easy to shape, which suits small runs. But for large-scale productions, H13 steel2 is better. Its strength and resistance make it last through long runs.
Production Batch | Recommended Material | Key Properties |
---|---|---|
Small (hundreds) | P20 Steel | Cost-effective, Pre-hardened |
Mass (thousands) | H13 Steel | Wear-resistant, Durable |
Precision and Material Selection
Precision was always my main focus in design. I worked on projects requiring tiny parts to fit together like puzzles. S136 steel3 was valuable in such cases. Its low thermal expansion ensures molds don’t warp under heat. This is essential when high accuracy is needed.
- Example: For products that need very precise dimensions of ±0.05mm, S136 supports smooth surfaces with roughness as low as 0.01μm.
Considering the Work Environment
I saw how the environment changes material decisions. High-temperature materials like polycarbonate need a special choice, like beryllium bronze alloy, which improved our cooling and product accuracy, much like turning on a fan in a hot room.
Environment | Material Recommendation | Benefits |
---|---|---|
High Temperature | Beryllium Bronze Alloy | Thermal stability, Improved cooling |
Performance in Processing Mold Materials
At the factory, I learned processing performance is crucial. P20 steel’s4 excellent cutting performance allowed tougher cuts on CNC machines without losing quality. This gave machinists confidence. However, using very hard steels like cemented carbide needed patience and precision tools, similar to creating delicate art.
- Heat Treatment: Correct heat treatment enhances material properties. For H13 steel, quenching and tempering increase hardness, showing controlled heating and cooling’s importance.
Considering Material Costs
Cost was always significant, especially with limited budgets. Balancing performance and cost was like tightrope walking. For simple projects, domestic 45 steel was cheap yet adequate. But for critical precision projects, high-grade imported steels like PX88 were worth the investment.
- Cost Evaluation: Comparing high-grade materials against budget limits helps allocate resources wisely.
By looking at all these factors, I selected the right mold materials to improve production outcomes. Understanding each factor ensured our molds met quality and budget standards.
P20 steel is ideal for mass production molds.False
P20 steel is suitable for small batch production due to its cost-effectiveness.
H13 steel maintains high precision in long-term use.True
H13 steel's wear resistance and toughness help maintain mold cavity accuracy.
How does the size of a production batch affect mold material choice?
Have you ever thought about how the size of a production batch decides your choice of mold material? This aspect is crucial. Batch size really affects material selection. Smaller batches might require different materials from larger ones.
Selecting materials for molds depends on how many items you plan to produce. Small groups benefit from cheaper choices such as P20 steel. Large groups need strong materials like H13 steel for excellent wear resistance.
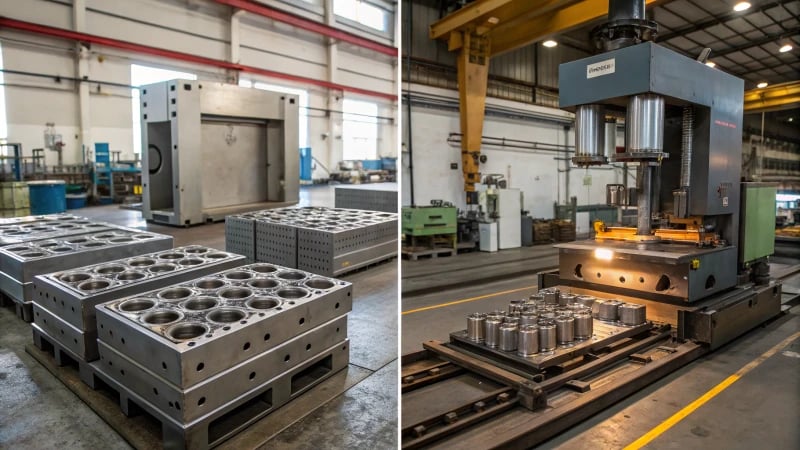
Understanding Production Batches
Batch size truly matters. At the start, I learned the hard way that selecting the wrong material wastes time and money. Small batches, maybe just a few hundred pieces, require balancing cost and function. That’s where P20 steel shines. It’s cheap and effective without emptying your wallet.
Batch Type | Material Choice |
---|---|
Small Batch | P20 Steel |
Large Batch | H13 Steel |
Material Requirements for Mass Production
Producing tens of thousands of pieces? That’s a whole different challenge. A material must endure wear and tear. H13 steel is my choice because it stays strong under pressure, keeping its shape and precision. I remember my first big project; mold wear worried me, but using H13 steel made a huge difference.
Precision Needs in Mold Making
High-tech gadgets demand precision. Even a slight error can cause failure. For this, I use S136 steel. It remains stable under heat changes, ensuring the precision required.
Mold Material Selection by Working Environment
Consider the working environment:
- High temperatures? Use beryllium bronze alloy for its thermal stability.
- Corrosive conditions? Corrosion-resistant materials5 like stainless steel 420 are ideal.
It’s like choosing the right outfit for the weather – one must match material to conditions.
Processing Performance of Mold Materials
Processing performance matters too. P20 steel works quickly and efficiently on CNC machines with higher cutting speeds (machining performance6). Tougher materials like carbide slow down the process and need specialized tools.
Cost Considerations
Budgeting is crucial:
- Sometimes, simple and affordable options like domestic 45 steel suit basic molds.
- However, high-stake projects may benefit from investing in premium materials like PX88 steel by analyzing the product’s value7 and potential profits.
Ultimately, selecting the correct mold material involves more than just science; it’s about strategy, experience, and sometimes trusting your instincts.
P20 steel is suitable for mass production molds.False
P20 steel is used for small batch production due to its cost-effectiveness.
S136 steel ensures high precision in plastic products.True
S136 steel's low thermal expansion and high surface quality ensure precision.
Why Are Material Processing Performances Critical in Mold Design?
Have you ever thought about how picking the right materials changes the design of a mold and really affects the outcome of your project?
Material processing tasks, such as cutting and heat treatment, play a key role in mold design. They directly impact accuracy, strength and cost. Picking the right materials is vital for keeping molds working well over time. Very important.
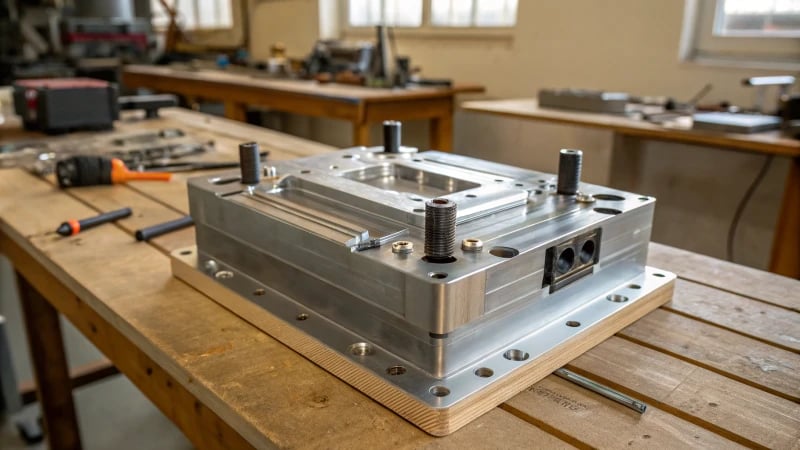
Cutting Performance
One lesson I learned was about cutting performance. Imagine working with P20 steel; it allows high speeds on CNC machines8. Smoother finishes and precise dimensions follow. Every designer appreciates this.
In contrast, there’s cemented carbide. Its wear resistance excels, yet machining it feels like taming a wild horse. Special tools and patience are needed.
Material Type | Cutting Speed (m/min) | Feed Rate (mm/r) |
---|---|---|
P20 Steel | 100 – 200 | 0.05 – 0.2 |
Carbide | Special Tools Needed | Lower Parameters |
Heat Treatment
Heat treatment is another important factor. I remember a project where using H13 steel was essential. Quenching and tempering processes were like guiding a ship through stormy seas. Every degree of temperature required precision.
Quenching from 1020°C to 1050°C and tempering between 550°C to 650°C kept molds stable. This stability was vital for mold accuracy9 over time.
Cost vs. Performance
Choosing materials often feels like balancing cost and performance. For simpler molds, 45 steel works well without costing too much.
For high-performance needs, pricier options like PX88 prove their worth. The choice often depends on the balance between product value and profit margins, ensuring cost-effectiveness10.
Production and Product Precision
Finally, matching material choice to production needs is key:
- For small batches, P20 steel is suitable due to easy machining.
- When production scales up, H13 steel’s wear resistance is invaluable.
- For precision products, S136 steel’s low thermal expansion ensures excellent surface quality despite temperature changes.
Understanding these details helps me optimize mold design11 for any production requirement.
P20 steel is ideal for small batch mold production.True
P20 steel is cost-effective and meets accuracy requirements for small batches.
H13 steel has poor wear resistance for mass production.False
H13 steel is known for high hardness and wear resistance, suitable for mass production.
How Do Environmental Conditions Affect Mold Material Choices?
I once believed choosing mold materials was only about finding the least expensive one. Now I know it’s a complete science. Balancing environmental problems with performance needs really defines this field.
Temperature, humidity and contact with harmful substances greatly influence the choice of mold material. Materials need to withstand such challenges. It is crucial for materials to keep their structure strong.
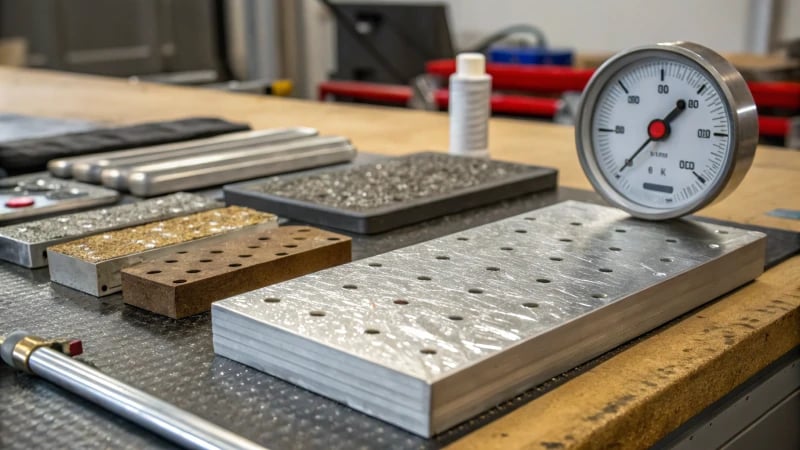
Navigating Temperature Challenges
I remember my first project where temperature played a big role. Using high-temperature plastics12, I discovered that some materials couldn’t take the heat. Beryllium bronze alloy helped with its ability to handle heat. It was very useful.
Material | Temperature Range | Key Property |
---|---|---|
Beryllium Bronze | 280-320°C | High thermal conductivity |
Humidity and Corrosion: The Hidden Dangers
Once, I didn’t realize how bad humidity could be until a batch returned with problems because of corrosion. Since that time, I have used stainless steel 42013. It has the resistance needed to keep things accurate. It’s my reliable choice.
Production Insights
Balancing Batch Size and Cost
I found out through experience that the cost isn’t just about the initial price of materials. P20 steel works really well for smaller batches because it’s both affordable and precise. But when I produce on a large scale, I trust H13 steel since it’s very durable.
Production Type | Material Choice | Reason |
---|---|---|
Small Batch | P20 Steel | Low cost, good machining |
Mass Production | H13 Steel | High hardness, durability |
Precision in Every Detail
Precise projects need materials that survive temperature changes without changing shape. S136 steel14 has saved me in projects needing strict tolerances. It truly meets tough demands.
Processing Performance: Efficiency is Key
Choosing the right material affects how efficient the process is. P20 steel, with its great cutting ability, helps me meet deadlines while keeping top quality. It’s important.
In my mold design journey, I learned that knowing how environment impacts material choice is crucial for project success. Looking at these areas together helps me choose the best material for every mold.
P20 steel is ideal for high-precision mold production.False
P20 steel is suitable for small batch production, not high-precision molds.
H13 steel maintains mold accuracy in mass production.True
H13 steel's hardness and toughness ensure dimensional accuracy in mass production.
Conclusion
Choosing the right mold material, like P20, H13, or S136 steel, is crucial for precision injection molding based on production batch size, accuracy needs, and environmental conditions.
-
Learn why P20 steel is preferred for small batch productions due to its cost-effectiveness and machining capabilities. ↩
-
Discover how S136 steel ensures high precision in products by maintaining dimensional stability across temperatures. ↩
-
Explore P20 steel’s cutting performance advantages in CNC machining for enhanced surface accuracy. ↩
-
Gain comprehensive insights into selecting appropriate mold materials for optimal manufacturing efficiency. ↩
-
Explore why corrosion-resistant materials are essential in environments with acidic additives. ↩
-
Learn why P20 steel’s machining performance is preferred for small batches due to its pre-hardened nature. ↩
-
Understand how to balance mold material costs with product value and profitability. ↩
-
Explore how CNC machining enhances precision in mold making with high-speed capabilities. ↩
-
Learn how controlled heat treatment improves mold material properties for better accuracy. ↩
-
Discover strategies to balance cost with performance in mold material selection. ↩
-
Find insights into optimizing mold designs for specific production requirements. ↩
-
Exploring this link will help you understand the specific high-temperature plastics suited for injection molding processes. ↩
-
This link provides insights into why stainless steel 420 is ideal for environments requiring corrosion resistance. ↩
-
Discover more about S136 steel’s thermal properties and its suitability for precision components. ↩