Selecting the correct mold processing method often seems like a challenging puzzle. However, it’s vital for high-quality production.
When choosing mold processing technology, I look at design complexity, material qualities, production quantity, equipment abilities, worker expertise and budget limits. Design complexity really matters. Material qualities also play a crucial role. Production quantity is important too. Equipment abilities shouldn’t be ignored. Worker expertise really affects the outcome. Budget limits need attention. These factors are very important.
I think about my own experiences. Knowing these factors is very important. For example, with complex designs, choosing high-speed milling or EDM is vital for precision. Expertise of my team really influences our process. Cost and quality need balance, which is tricky but necessary for success. Sharing these ideas might help others with mold challenges.
High-speed milling is needed for complex mold surfaces.True
Complex mold surfaces require precise machining, which high-speed milling provides.
Ordinary milling is sufficient for molds with free-form surfaces.False
Free-form surfaces require advanced processes like EDM or CNC for accuracy.
- 1. How Does Design Complexity Influence Mold Processing Choices?
- 2. How Do Material Characteristics Affect Mold Processing Technology?
- 3. Why Is Production Volume Important in Selecting Mold Processing Methods?
- 4. How Do Equipment Capabilities Determine Mold Processing Options?
- 5. How Do Technician Skills Impact Mold Processing Technology Selection?
- 6. How Do Cost Constraints Affect Mold Processing Technology Choices?
- 7. Conclusion
How Does Design Complexity Influence Mold Processing Choices?
Did you ever see a mold design and wonder why it matters so much in manufacturing? I once believed it was simple until I explored the world of molds myself.
Design complexity affects mold processing choices by needing special techniques for detailed designs. Very intricate structures require high-precision methods like HSM or EDM. Simpler designs probably use basic milling techniques. Very simple.
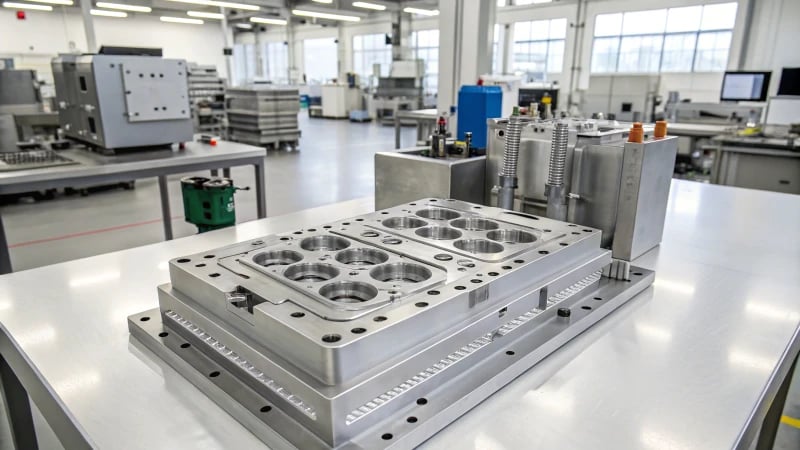
Influence of Design Demands
Design demands significantly impact mold processing choices, particularly concerning shape and structural complexity. For simple shapes, ordinary milling suffices. However, molds with intricate designs, such as automotive interiors, require high-speed milling1 or EDM for precise machining.
Design Aspect | Processing Technique |
---|---|
Simple Shapes | Ordinary Milling |
Complex Free-form | High-Speed Milling (HSM) |
Undercut Structures | Electrical Discharge Machining (EDM) |
Dimensional accuracy surprised me. High-precision molds needed techniques for tight tolerances and I had to learn them fast. Techniques like precision grinding are used to achieve tolerances as tight as ±0.001mm. Everything fits right because of them.
Surface quality also matters. High-gloss surfaces may need extra polishing post-machining, whereas textured surfaces might use laser etching. Details are important for a good final product.
Mold Material Impact
The characteristics of mold materials, such as hardness, influence processing techniques. Choosing tools for hard materials like H13 was tough early on. Balancing hardness and toughness allows smooth processing.
Material Property | Processing Approach |
---|---|
High Hardness | Carbide Tools |
Lower Hardness | High-Speed Steel Tools |
For these strong materials, carbide tools have become crucial, especially for precision.
Thermal stability and wear resistance are important too. Wear-resistant materials demand durable tools to ensure accuracy over time.
Production and Efficiency Choices
Production scale affects processing choices. Mass production needs durable processes to maintain quality and reduce costs, often leveraging advanced CNC machining centers that have really changed the game by speeding up and sharpening results.
For small batch production, flexibility helps a lot in finding the balance between cost and quality sometimes needs a mix of basic milling and minimal EDM.
Equipment and Resources Availability
Available equipment in a shop decides a lot about what can be done internally versus what needs outsourcing due to limits in capability; however, advanced CNC setups provide more choices.
Technical knowledge matters too; skillful use of CAD/CAM software often makes a big difference in handling advanced processes effectively.
Budget Limits
Balancing cost and precision is difficult but necessary; advanced processes like CNC and EDM have higher costs but are vital for precision work where budget-friendly options2 might suffice for simpler designs without compromising on essential quality aspects.
Maintenance costs should also be considered when selecting processing technologies to avoid unexpected expenses related to mold upkeep and part replacement later on.
Understanding how design complexity intersects with these factors helps in making smart choices that balance cost efficiency while achieving excellent mold production results.
High-precision molds require ±0.001mm tolerance.True
Precision molds like optical lens molds need high dimensional accuracy.
Ordinary milling is suitable for complex free-form surfaces.False
Complex surfaces require advanced methods like HSM or EDM.
How Do Material Characteristics Affect Mold Processing Technology?
Have you ever thought about how the materials we select change the world of mold processing? It’s really interesting to watch how every detail holds an important role.
Material traits such as hardness, toughness, thermal stability and wear resistance greatly impact mold processing technology. These traits guide the choice of tools, set machining parameters and affect process efficiency. They play a major role in achieving top mold quality and performance.
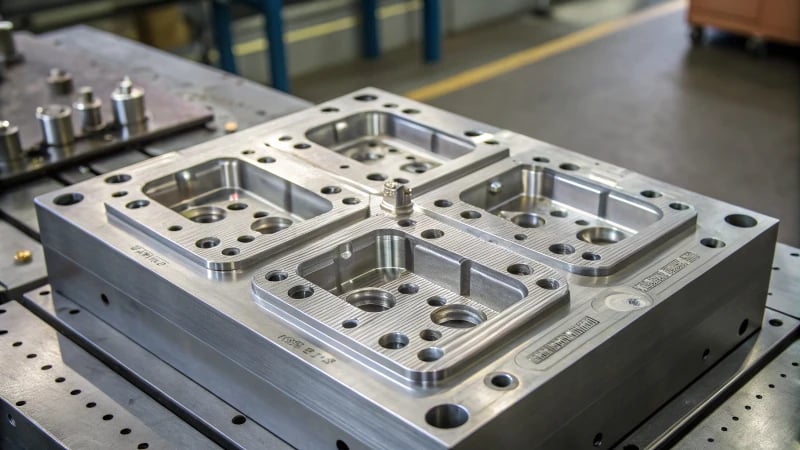
Hardness Affects Tool Choice
When I first started working with mold processing, I quickly discovered that materials control the whole process. Imagine sculpting a masterpiece with marble instead of butter – each requires a different method.
Material hardness is a primary factor affecting tool selection during mold processing. Thinking back to my early days, I remember struggling with very tough materials like H13 and S136. We needed carbide tools and adjusted our settings to tackle the high cutting force. It felt like choosing the right chisel for stone sculpting – accuracy mattered. Softer aluminum alloys were easy but needed attention to avoid sticking.
Toughness and Ductility Require Adaptation
Toughness and ductility taught me about care and adaptability. These properties needed special tools to prevent sticking. We used coated tools with great ability to reduce friction and changed how we used cutting fluids3. Very ductile materials, especially for thin walls, required lower cutting depths and slower feeds to stop bending.
Thermal Stability and Wear Resistance: A Double Challenge
Thermal stability seemed perfect – less heat meant less worry about getting too hot. But high wear resistance brought new challenges. We needed tools that could resist wear and regular checks for tool damage. This reminded me of old carpentry days, where keeping tools sharp was as crucial as the wood.
Material Characteristic | Effect on Mold Processing |
---|---|
Hardness | Influences tool choice; requires specific cutting parameters |
Toughness & Ductility | Demands adapted tools and technology; considers fluid use |
Thermal Stability | Low heat effect but increased tool wear concerns |
Wear Resistance | Requires constant tool monitoring and replacement |
Matching Process with Production Needs
Production size – whether large or small batches – guides mold processing choices. Large-scale production needs very precise CNC machining for strength and effectiveness. In small batches, we have some room to focus on saving costs while keeping quality high.
Understanding these material characteristics enables manufacturers to optimize mold processing technologies effectively, aligning them with specific production requirements and quality goals.
High-hardness materials require carbide tools for processing.True
Carbide tools are necessary for high-hardness materials to ensure efficient cutting.
Ordinary milling is suitable for high-gloss surface molds.False
High-gloss surfaces need polishing or electrochemical polishing, not just milling.
Why Is Production Volume Important in Selecting Mold Processing Methods?
Have you ever thought about how much we produce changes our choice in mold processing methods? Production quantity very often influences decision-making. High production volumes often require specific methods. Different techniques are really needed for small and large batches. Production levels dictate processing methods. They always have.
Production quantity plays a big role in choosing mold processing methods. It affects costs, equipment options and how well the process works. Large quantities need strong molds. Small quantities find value in flexible and cheap methods. It is very important.
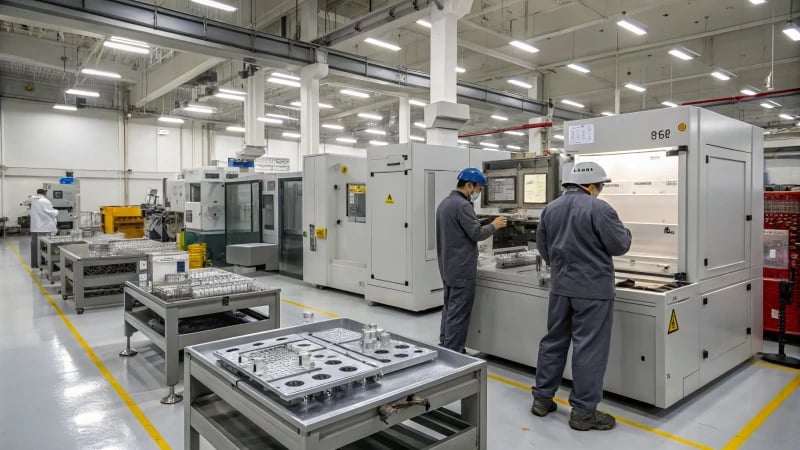
How Production Volume Affects Mold Processing
When I began learning about mold processing, I quickly saw how important production volume is in choosing the right method. High-volume production needs molds that can handle constant use, just like my shoes needed to last when I trained for a marathon. For busy processes, methods like precise CNC machining are critical to keep quality steady through thousands of uses. This is very important.
High-Volume vs. Low-Volume Thoughts
Thinking about my experiences, I compare high-volume manufacturing to cooking for a big family event – everything must be perfect. Techniques like fast milling4 and EDM are key here. They help molds fit exact size and surface needs, like making sure every dish is seasoned well. On the other hand, small projects feel like making a simple meal for friends. This allows for more creativity and choices, using cheaper methods like basic milling but still doing well.
Economic Effects of Production Volume
Production Volume | Processing Method | Cost Implications |
---|---|---|
High | Advanced CNC, EDM | Higher upfront costs |
Low | Basic Milling | Lower initial expenses |
The money side reminds me of planning for a long trip versus a short weekend. Spending more on top processes for a lot of production saves money in the long run, while small volumes gain from lower starting costs and quick setups. It’s a big difference.
Design Needs and Efficiency
Designs for large production must be simple and repeatable like a favorite recipe. This needs precise tools and special machines such as advanced equipment5. But, for low volume work, it feels like trying a new recipe – there is room to try new things without much worry about cost.
Equipment and Skill Level Thoughts
Picking the correct method depends on machines and worker skills. Like when I upgraded my kitchen tools; suddenly, hard recipes were doable. Companies with advanced CNC tools deal with complex molds easier than those limited to basic machinery. Worker skill level is vital – like having a great chef in your kitchen – so training is very important in high-volume settings.
Choosing mold processing relies on production volume. Matching methods with production needs helps save money and keep quality consistent across multiple cycles like this6. It’s probably crucial to know these aspects to pick the best mold methods that fit both business goals and production demands.
High-speed milling is necessary for complex mold shapes.True
Complex molds require precise machining, achievable through high-speed milling.
Ordinary milling suffices for high-gloss mold surfaces.False
High-gloss surfaces need polishing, not just ordinary milling.
How Do Equipment Capabilities Determine Mold Processing Options?
Do you ever think about how your machines change the way you process molds?
Equipment abilities shape mold processing choices. They guide the selection of machining methods, tools and techniques. Design complexity matters a lot. Material traits also impact decisions. Production needs play a crucial role in the process.
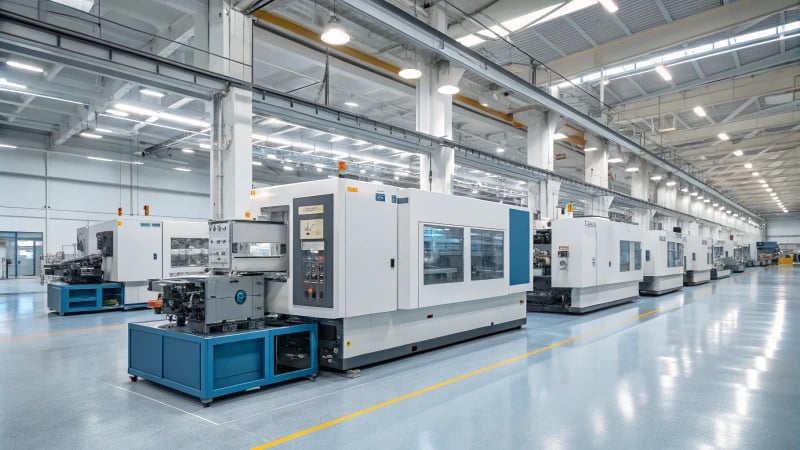
Design Complexity and Equipment Capabilities
Whenever I explore designs for molds7, I first assess if my equipment can manage those complex shapes. It’s like solving a puzzle with the right pieces. Simple shapes often need ordinary milling, but intricate, free-form surfaces demand high-speed milling (HSM) or electrical discharge machining (EDM).
Table: Equipment vs. Design Complexity
Design Complexity | Required Equipment |
---|---|
Simple Shapes | Ordinary Milling |
Complex Free-form | HSM, EDM |
Take automotive interior molds, for instance. Their complexity definitely requires equipment capable of handling detailed textures and surfaces with ease.
Material Characteristics Impact
Material characteristics greatly affect processing choices. Hard materials require carbide tools and more power in cutting. Softer materials might let me use high-speed steel tools, but these sometimes cause sticking due to their toughness.
- Hardness: Carbide tools are essential for hard materials.
- Toughness: Needs tools with good lubrication and cutting fluids.
Production Batch Size and Efficiency
Batch size often determines equipment needs. Large production calls for precise equipment to maintain smooth efficiency, while smaller batches allow flexibility, offering cheaper processing options. Advanced CNC machining centers revolutionize efficiency and durability, especially in big projects.
- Mass Production: Needs durable, efficient processes.
- Small Batch: Uses cost-effective technology with basic quality.
Technical Resources and Equipment Availability
Availability of machines like CNC centers or EDM impacts mold processing choices significantly. Limited to basic milling? Outsourcing complex tasks may be necessary.
Equipment Availability | Processing Flexibility |
---|---|
Basic Equipment | Limited Processing Options |
Advanced CNC, EDM | Broad Range of Process Options |
Plus, technician skill levels impact technology decisions. Good CAD/CAM knowledge opens many possibilities.
Balancing Cost Considerations
Processing costs matter and vary with chosen technology. High-precision CNC processes cost more than regular milling. Special surface treatments may also increase maintenance expenses.
When choosing methods, consider both immediate costs and future maintenance to balance long-term viability and efficiency without compromising quality. Aligning equipment capabilities with mold requirements optimizes strategies effectively.
Recognizing these dynamics is key for well-informed decisions that raise productivity and ensure exceptional product quality.
High-speed milling is essential for complex mold shapes.True
Complex molds require precise machining, achievable with high-speed milling.
Ordinary milling suffices for all mold types.False
Complex molds need advanced processes beyond ordinary milling for accuracy.
How Do Technician Skills Impact Mold Processing Technology Selection?
Picture yourself in a busy workshop, the sound of machinery filling the air. A talented technician adjusts the processes that shape our daily lives.
Technician skills are crucial in selecting mold processing technology. They affect programming, operation and maintenance. Skilled technicians handle tasks with precision. Technicians really enhance production processes. They adopt advanced technologies with ease. This leads to better results. Outcomes improve significantly.
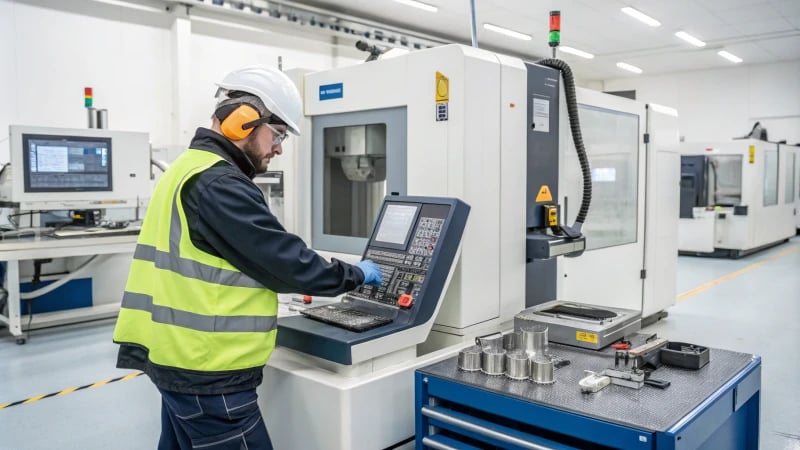
How Technicians Impact Process Choices
Technicians play a critical role in selecting mold processing technologies8 by leveraging their knowledge and experience to align technology with project requirements.
Skills in Programming and Operating
I recall a tough mold project with complex shapes. Technicians, skilled in CAD/CAM software, tackled it directly. They knew how to use complex machines to perform CNC machining tasks perfectly. This skill was vital for reaching the accuracy required for complicated designs.
Technician Skills | Impact on Process Selection |
---|---|
CAD/CAM Proficiency | Enables advanced CNC processes |
High-Precision Operation | Ensures dimensional accuracy |
Keeping Up with New Technology
As mold technologies9 evolve, keeping up becomes very important. I saw technicians who regularly updated their skills to use new methods like HSM and EDM. Our molds met complex design needs and also performed really well.
Troubleshooting and Maintenance
During an important project phase, a machine broke suddenly. The technician solved the problem quickly. Their maintenance skills keep machines running well, which stops interruptions and keeps mold production steady.
Moreover, skilled technicians can identify potential issues early, preventing costly repairs or replacements.
Technician Skills and Using Resources Well
Our technicians’ skills help us use resources smartly. One technician’s deep knowledge of EDM equipment10 let us use it very effectively. This sort of expertise really guides decisions on what technology fits best.
In summary, technician skills are not just useful – they’re essential for choosing the best mold processing techniques. From programming to maintenance, skilled technicians ensure top-level mold production.
High-speed milling is needed for complex mold shapes.True
Complex molds require high-speed milling for precision.
Ordinary milling is sufficient for all mold types.False
Complex molds need advanced techniques beyond ordinary milling.
How Do Cost Constraints Affect Mold Processing Technology Choices?
Navigating cost constraints in mold processing feels like solving a puzzle. Workers need to find that sweet spot between budget and technology without lowering quality. Balancing these factors is very important. Quality remains vital and should never be compromised.
Cost limits often decide the choice of mold processing methods by reducing options to cheaper techniques. Basic quality remains important. Processing, maintenance and replacement costs are key factors.
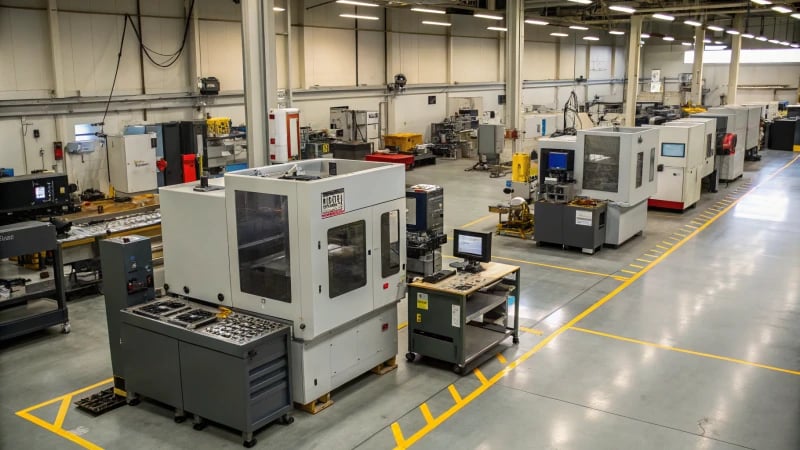
Simple Design and Budget Planning
In mold design, cost and accuracy often clash for me. Picture working on a mold project with very detailed surfaces. High-speed machines suit this task but are expensive. Simpler designs let us use regular milling, saving money.
Design Aspect | High-Cost Technology | Low-Cost Alternative |
---|---|---|
Complex Shapes | High-speed milling | Conventional milling |
High Surface Quality | Electrochemical polishing | Basic polishing |
Material Choice and Expenses
Picking mold material is like choosing clothes for an event. Hard materials need costly tools and careful handling, which raise expenses. If I use aluminum alloys11, costs drop, but I must be careful to meet durability needs.
- High Hardness: Needs pricy tools.
- Lower Hardness: Permits cheaper tools.
Production Quantity Thoughts
Production scale really affects my choices. For mass production, buying advanced machines seems smart because they are tough and fast. For smaller batches, I use cheaper methods that still keep quality high.
Production Type | Preferred Technology | Justification |
---|---|---|
Mass Production | Advanced CNC Machining | Ensures durability and speed |
Small Batch or Trials | Ordinary Milling + Some EDM | Cost-effective with flexibility |
Tools and Skill Importance
Having top equipment really helps. I have worked with great CNC machines, handling tough projects easily. Skilled workers are also vital; their knowledge decides if we use complex machines successfully.
Budget Consideration
Balancing money and technology is an art I’ve learned. Using fancy machines like EDM is tempting, but checking upkeep costs is vital. Finding a balance helps keep costs low and functions high in mold making.
- Processing Expenses: Weigh money against tech needs.
- Upkeep Costs: Check future spending for mold care.
Navigating these points mixes planning ahead with real-life experience. Quality mold production needs cost-wise choices without losing quality.
High-precision molds require EDM for complex surfaces.True
EDM is essential for high-precision molds with complex shapes due to its accuracy.
Ordinary milling suffices for automotive interior molds.False
Automotive interior molds often need high-speed milling due to complexity.
Conclusion
Choosing mold processing technology involves considering design complexity, material properties, production volume, equipment capabilities, technician skills, and budget constraints to ensure quality and efficiency in manufacturing.
- Explore this link to understand the differences between high-speed milling and EDM, and how they apply to complex mold designs. ↩
- Discover budget-friendly processing technologies suitable for simpler mold designs without compromising quality. ↩
- Learn about the role of cutting fluids in managing tool lubrication and cooling when processing tough materials. ↩
- Learn about the advantages of high-speed milling in enhancing mold precision. ↩
- Discover the role of advanced equipment in achieving precise mold designs. ↩
- Explore how durability and efficiency are prioritized in high-volume mold processing. ↩
- Explore more about design requirements that influence equipment choice for mold processing. ↩
- This link offers insights into why technician skills are crucial for selecting appropriate mold processing technologies. ↩
- Discover recent innovations in mold processing technologies that require skilled technicians for effective implementation. ↩
- Explore the specific capabilities of EDM equipment in mold processing and why technician expertise is vital. ↩
- Discover why aluminum alloys are a cost-effective choice for certain mold applications. ↩