Designing plastic molded parts is both an art and a science, demanding precision and foresight.
The key steps to designing plastic molded parts involve clarifying design requirements, selecting appropriate materials, executing structural design, collaborating with mold manufacturers, and conducting thorough testing and optimization. Each step ensures the production of high-quality molded parts.
While the initial overview provides a framework, delving deeper into each step reveals critical insights and best practices that are crucial for both beginners and seasoned professionals. Let’s explore these steps in detail to enhance your plastic part design skills.
Selecting the right plastic material is crucial for design success.True
Material choice affects functionality, cost, and processing performance.
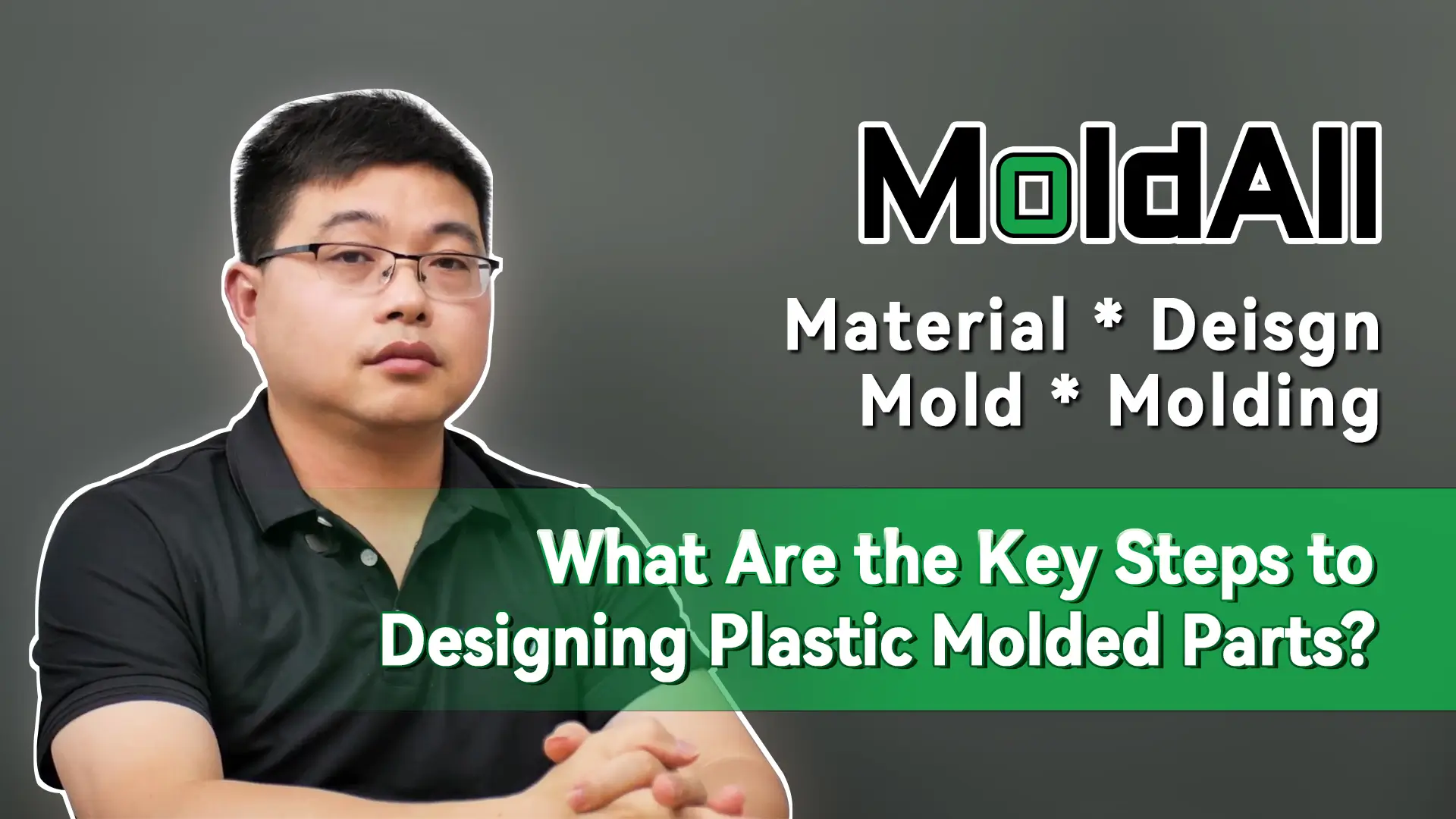
What Are the Common Challenges in Plastic Mold Design?
Designing plastic molds is complex, with challenges that can impact functionality and manufacturability.
Common challenges in plastic mold design include balancing functional requirements with material selection, addressing environmental factors, ensuring manufacturability, and maintaining cost-effectiveness. Each challenge requires strategic planning and collaboration with mold manufacturers to achieve optimal results.
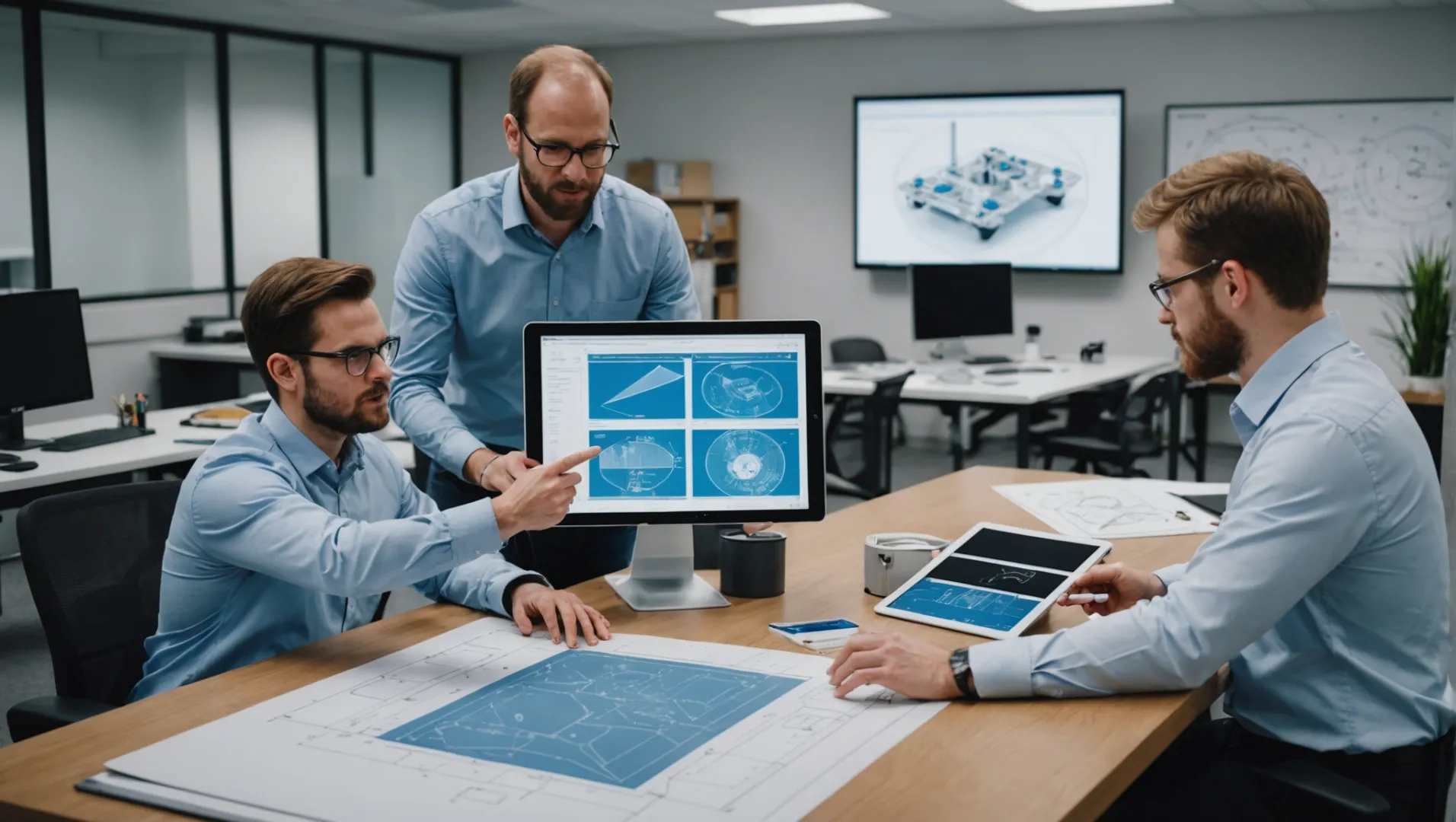
Balancing Functional Requirements with Material Selection
One of the primary challenges in plastic mold design is aligning the functional needs of the product with the right materials. Designers must consider functional requirements1 like structural support or aesthetic appeal, which directly influence the choice of material. For example, a part requiring high strength may necessitate a different material than one designed for decorative purposes.
Further complicating this process is the need to account for the use environment. Molded parts may encounter varying temperatures, humidity levels, or exposure to chemicals. Thus, selecting materials that offer suitable resistance to these conditions is crucial.
Addressing Environmental Factors
Environmental conditions play a significant role in plastic mold design. Parts used outdoors need materials that can withstand UV radiation and weather changes. This involves not just choosing UV-resistant plastics but also considering their longevity and performance under such exposure.
Additionally, the manufacturing process itself must take into account environmental factors such as temperature and humidity, which can affect both the material’s behavior and the mold’s performance.
Ensuring Manufacturability
Designs that look good on paper may not always be feasible in practice. Ensuring manufacturability involves considering the mold’s ability to produce the desired shape efficiently and consistently. This includes designing for ease of demolding, optimizing wall thickness, and incorporating features like ribs to enhance strength without adding bulk.
To prevent defects like warping or stress concentrations, it’s essential to maintain uniform wall thickness. Moreover, designs should avoid unnecessary complexity in shapes, which could lead to increased production costs and reduced mold life.
Maintaining Cost-Effectiveness
Balancing cost while meeting design and functional requirements is another challenge. Material selection impacts not only performance but also cost. Opting for high-performance materials may increase expenses but can be justified if they significantly enhance product lifespan or functionality.
Moreover, the design phase must consider cost-saving measures like minimizing waste during production and selecting materials that are recyclable to align with sustainability goals.
Collaborating with Mold Manufacturers
Successful plastic mold design demands close collaboration with mold manufacturers. Providing detailed design specifications and participating in reviews ensures the final product meets expectations. Regular communication helps address potential issues early on and facilitates the optimization of both design and manufacturing processes.
Engaging manufacturers early in the process can also lead to innovative solutions that designers alone might overlook, ultimately improving product quality and reducing time-to-market.
Material selection impacts cost-effectiveness in mold design.True
Choosing materials influences both performance and cost of molds.
Environmental factors rarely affect plastic mold designs.False
Environmental conditions significantly impact material behavior and design.
How to Choose the Right Plastic Material for Your Design?
Choosing the right plastic material is critical for the success of your design, balancing functionality and cost.
To select the appropriate plastic material, consider functional requirements, environmental conditions, appearance, material properties, cost factors, and processing performance. Evaluating these aspects ensures that the material meets both design and sustainability goals.
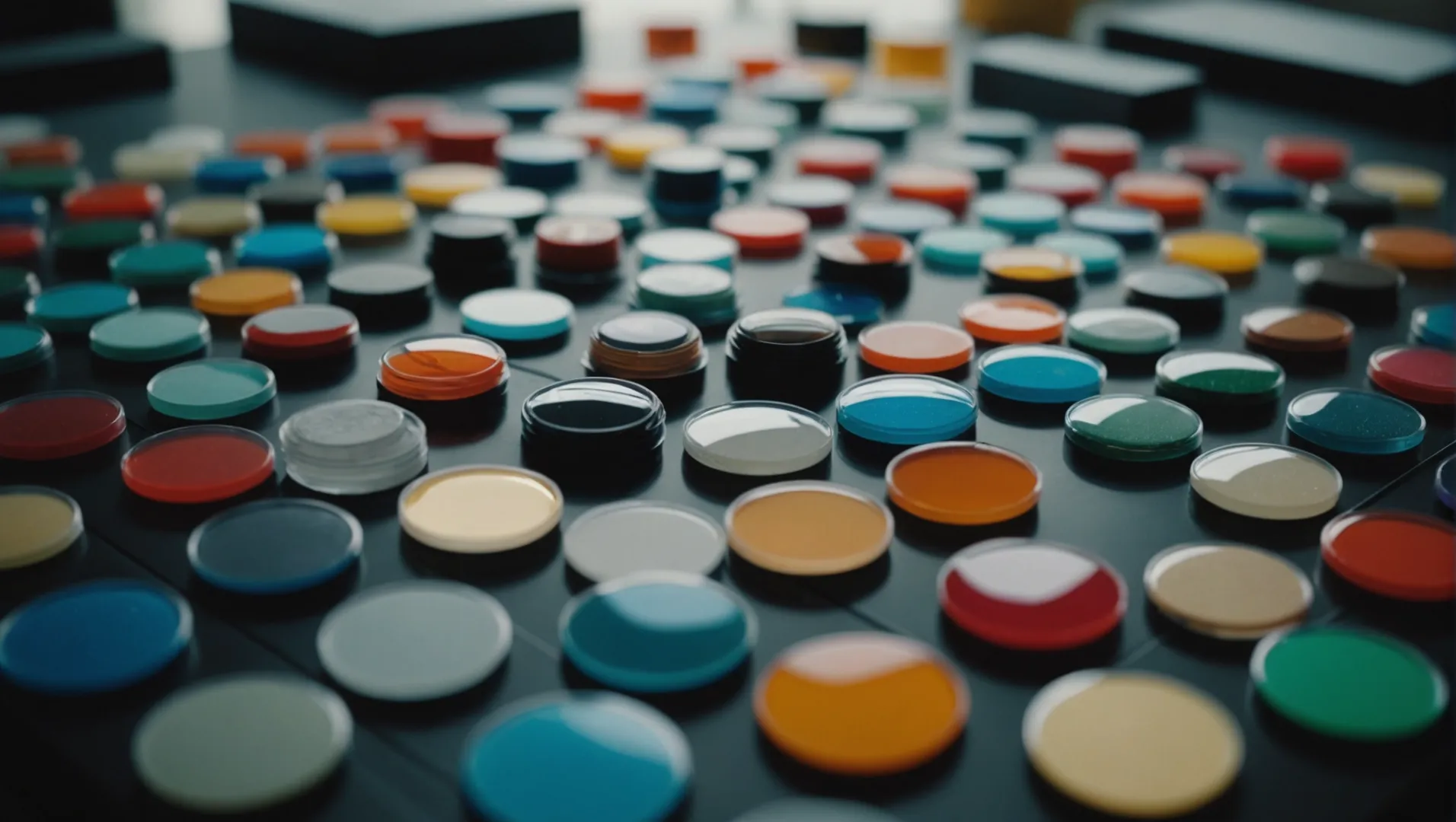
Understanding Design Requirements
Before choosing a plastic material, it’s essential to understand the design requirements2. Determine the function of the part within the product—is it for structural support, decoration, or sealing? This will affect its shape and mechanical performance needs. Additionally, consider how it will interact with other components to ensure proper fit and function.
Evaluating Environmental Conditions
The environment in which the plastic part will be used significantly influences material choice. Analyze factors like temperature, humidity, and potential exposure to chemicals. For outdoor applications, select plastics that offer UV resistance and aging durability.
Assessing Appearance Needs
Appearance can be as crucial as functionality. Decide on surface quality elements such as finish, color, and transparency. These factors will guide decisions on surface treatment and processing techniques. If special textures or patterns are needed, they should be planned early in the design phase.
Factor | Considerations |
---|---|
Functional Requirements | Structural support, decoration, sealing |
Environmental Conditions | Temperature, humidity, chemical exposure |
Appearance Needs | Finish, color, transparency |
Material Properties and Cost
Selecting plastic materials involves a deep dive into their properties such as strength, heat resistance, and chemical resistance. Compare these against your design requirements using technical data from suppliers. Cost is another critical factor—opt for materials that meet your needs at a reasonable price while considering recyclability and sustainability aspects.
Processing Performance
Understand how your chosen material behaves during processing. Factors like fluidity and thermal stability can impact mold design and process selection. For challenging materials, specialized molds or processes might be necessary.
By thoroughly evaluating these aspects, you can choose a plastic material that not only fulfills your design specifications but also aligns with sustainability goals.
UV resistance is crucial for outdoor plastic parts.True
Outdoor applications require UV resistance to prevent material degradation.
Cost is not a factor when selecting plastic materials.False
Cost is a critical factor in selecting materials, balancing budget with needs.
What Role Does Structural Design Play in Molded Parts?
Structural design is pivotal in ensuring molded parts meet their functional and aesthetic goals.
Structural design in molded parts defines their functionality, durability, and manufacturability, impacting factors like material choice, wall thickness, and mold complexity.
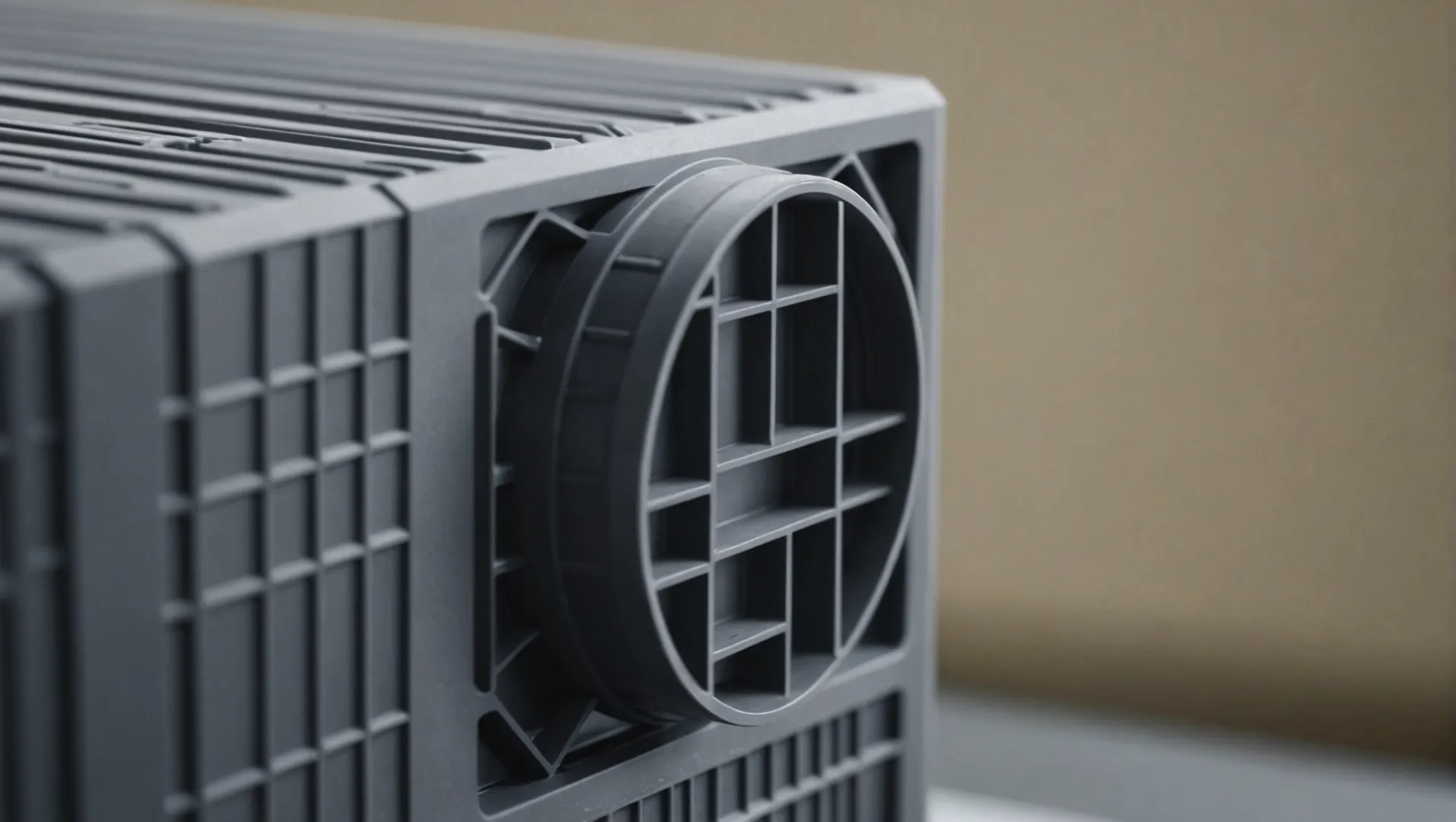
The Foundation of Functionality
The structural design of molded parts is integral to their functionality. By identifying the part’s intended use—whether for structural support, sealing, or decoration—designers can determine the necessary shape, dimensions, and mechanical properties. This foundation is essential for ensuring parts fulfill their role effectively within a product.
Material Selection and Environmental Considerations
Structural design also dictates material selection by assessing the environment where the part will be used. For instance, parts exposed to high temperatures or chemical corrosion require materials with specific heat or chemical resistance properties. This ensures the part’s durability and longevity in its operating conditions.
Wall Thickness and Weight Management
A crucial element of structural design is determining the wall thickness of molded parts. Uniform wall thickness prevents stress concentrations and warping, enhancing part stability. Moreover, avoiding excessive wall thickness helps reduce material usage and weight, which is beneficial for cost management and ease of production.
Feature | Purpose | Considerations |
---|---|---|
Rib Design | Increase strength and rigidity | Avoid stress concentration; maintain symmetry |
Hole & Slot Design | Accommodate functional components | Minimize complexity; use inserts for larger openings |
Simplifying Complexity with Symmetry
Using simple and symmetrical shapes in structural design minimizes manufacturing complexity and cost. Avoiding intricate curves and sharp angles extends mold life and improves part quality. Additionally, considering demolding aspects like slope and parting surfaces in the design phase ensures smooth ejection from molds.
Collaboration with Mold Manufacturers
Structural design isn’t solely an internal process. Communicating detailed design requirements with mold manufacturers is crucial. Providing comprehensive drawings and participating in mold reviews allows for effective problem-solving, ensuring the final product meets all design specifications and quality standards. Learn more about mold manufacturing collaboration3.
These aspects underline the significance of structural design in molded parts, influencing everything from material choice to manufacturing efficiency. It’s a holistic process that requires careful consideration and collaboration at every step.
Structural design affects molded parts' material choice.True
Material choice is influenced by the design to meet functional needs.
Complex mold designs reduce manufacturing costs.False
Simple, symmetrical designs minimize complexity and cost.
Why Is Communication with Mold Manufacturers Essential?
Effective communication with mold manufacturers is crucial for successful plastic part production.
Communication with mold manufacturers ensures that design requirements are met, potential issues are identified early, and cost-effective solutions are implemented. This collaboration leads to efficient mold production and high-quality plastic parts.
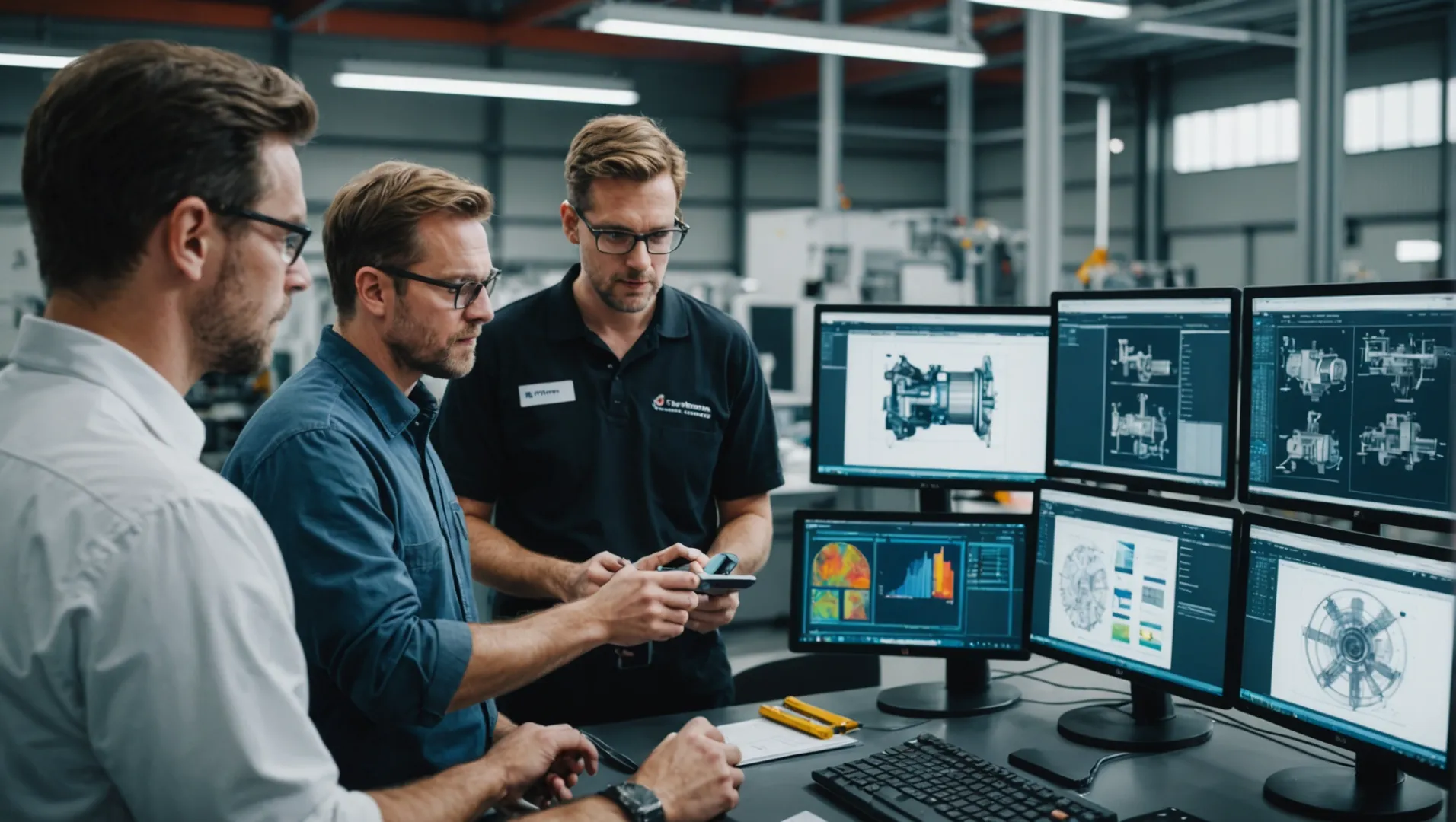
Understanding Design Requirements
Effective communication starts with conveying detailed design requirements to the mold manufacturer4. This involves sharing comprehensive drawings, including 3D models and 2D engineering drawings that encapsulate dimensional tolerances and surface quality needs.
This level of detail helps manufacturers understand the functional role of the part, such as structural support or decorative use, and tailor their approach accordingly. Ensuring clarity in these requirements is critical to avoid misunderstandings that could lead to costly revisions later.
Involvement in the Mold Design Process
Engaging in the mold design process is another key aspect of effective communication. By maintaining a continuous dialogue throughout the design and manufacturing stages, potential problems can be addressed promptly. Participating in mold reviews and trials allows for real-time feedback, ensuring that the final product aligns with initial design intents.
Providing samples and test data can further assist manufacturers in optimizing both mold design and the molding process itself. This collaboration not only speeds up production but also enhances the overall quality of the final product.
Addressing Technical Challenges
Communicating technical challenges and receiving expert insights from manufacturers can significantly improve part design. For instance, discussing environmental factors like temperature or humidity can influence material selection, ensuring the product withstands its intended conditions.
Similarly, sharing concerns about mechanical performance or appearance can lead to suggestions for alternative materials or processes that better meet the project’s objectives.
Testing and Optimization
Finally, communication plays a pivotal role during testing and optimization phases. Once a mold is produced, sample tests are crucial for verifying dimensional accuracy and mechanical properties.
Close interaction with manufacturers during these tests allows for immediate adjustments based on test results, facilitating quicker transitions to mass production. This proactive communication can lead to continuous improvements in molding processes and enhance overall production efficiency.
In conclusion, maintaining open and detailed communication with mold manufacturers ensures that the entire design-to-production cycle runs smoothly. This collaboration not only mitigates risks but also paves the way for innovative solutions and high-quality outcomes.
Communication prevents costly mold revisions.True
Clear communication avoids misunderstandings, reducing the need for expensive mold corrections.
Ignoring design requirements speeds up production.False
Overlooking design details can lead to errors, delaying production instead.
Conclusion
By meticulously following these steps, you can ensure the production of robust and reliable plastic molded parts. Reflect on each phase to continuously refine your design process.
-
Explores how functional needs influence material choices.: The engineer should optimize the part design to ensure optimal functionality. They should consider factors such as part geometry, wall thickness … ↩
-
Gain insights into aligning material choice with specific design needs.: Proper wall thickness is one of the most fundamental requirements in designing a part for plastic injection molding. Plastic shrinks as it cools which can … ↩
-
Explore strategies to enhance collaboration for better mold design outcomes.: Inexpensive Production Costs · Consistent and Quality Products · Better Communication and Understanding of One Another. ↩
-
Learn how effective communication enhances mold design and production efficiency.: Effective communication and collaboration are crucial components of success for mold development teams. The development of molds requires a high level of … ↩