Have you ever thought about how the perfect heat changes plastic into art?
The processing temperature of materials depends on factors like crystallinity, molecular structure, additives, product design and equipment performance. Crystalline materials have clear melting points. Non-crystalline materials soften slowly. Additives change how fluid a material is. Product shape and equipment details affect conditions. Temperature really varies because of these things.
I remember the first time I worked on creating a complex mold for a new gadget. The details of managing temperature were truly surprising. Crystalline plastics like polypropylene need exact temperatures to melt correctly. Non-crystalline ones like polycarbonate soften gently over a range. Additives act like secret ingredients; a plasticizer magically lowers the processing temperature for smoother operation.
The product’s shape matters a lot. Thin walls require higher heat for the plastic to flow smoothly into every corner. Thicker designs need less heat because they cool more slowly. The equipment cannot be forgotten – my old injection molding machine had its own peculiarities. Knowing its heating system and screw design was crucial. It was really the key to achieving that perfect melt.
Crystalline materials have defined melting points.True
Crystalline materials transition sharply from solid to liquid at specific temperatures.
Additives like plasticizers increase material crystallinity.False
Plasticizers enhance fluidity by reducing intermolecular forces, not crystallinity.
- 1. How does chemical structure determine processing temperature?
- 2. How Do Additives Change Plastic Processing Temperatures?
- 3. How Does Product Design Affect Processing Temperatures?
- 4. How Does Equipment Performance Impact Material Processing?
- 5. What are the common challenges in managing processing temperature?
- 6. Conclusion
How does chemical structure determine processing temperature?
Have you ever thought about how a material’s molecules choose its processing temperature?
The chemical structure of a material sets its processing temperature. It influences melting point, flow and thermal stability. Important elements include crystallinity, length of molecular chains and additives. These aspects are vital in the process.
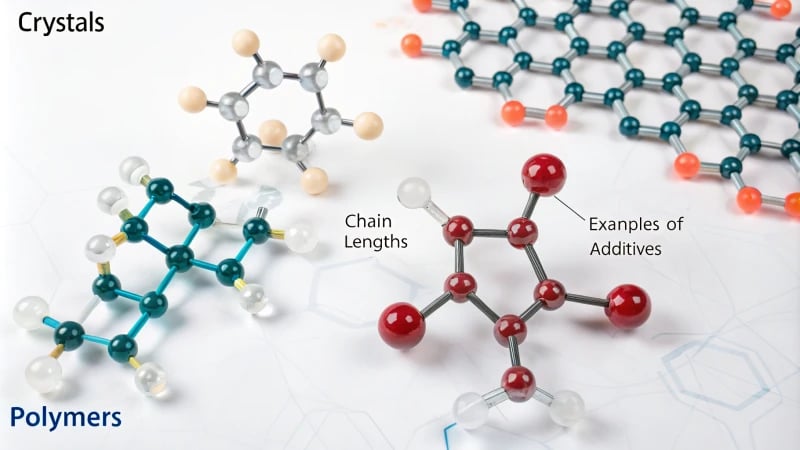
Understanding Crystallinity and Processing Temperature
The crystallinity of a material often affects its processing temperature. Crystalline plastics, such as polyethylene, have a specific melting point. They require higher temperatures to mold properly. Non-crystalline plastics, like polycarbonate, soften over a range of temperatures. This offers flexibility but also requires precise control of temperature.
Material Type | Characteristics | Processing Temperature |
---|---|---|
Crystalline | Specific melting point | Higher |
Non-Crystalline | Softens over a range | Wider range |
Influence of Molecular Chain Structure
I once worked with low-density polyethylene (LDPE). Its short molecular chains and few branches allowed it to flow well at lower temperatures. Materials like polyamides are different; these have polar groups that form strong intermolecular forces, meaning higher temperatures are needed to separate them.
Effect of Additives on Temperature
Plasticizers
In my projects, plasticizers really impressed me by lowering processing temperatures. Adding something like dioctyl phthalate to PVC reduces the temperature significantly.
Stabilizers and Fillers
Heat stabilizers in PVC help prevent breakdown during processing, allowing slightly higher temperatures. Fillers, such as glass fibers, increase viscosity; thus, higher temperatures are often necessary to maintain smooth flow.
Product Design and Temperature Changes
A product’s shape and needs always surprise me. Thin-walled products, for example, need higher temperatures to stay fluid before cooling. Complex designs require optimal temperatures for the melt to travel through detailed channels and fill molds well.
Equipment Performance Importance
Injection molding machines perform critical roles with their heating systems distributing temperature evenly while cooling systems control mold temperature—both affecting fluidity and quality.
Understanding these elements feels like discovering a secret recipe that improves production efficiency and product quality—crucial aspects in my work. Maybe explore more on injection molding machine performance1 to understand their impact on processing materials.
Crystalline materials have a distinct melting point.True
Crystalline plastics like polyethylene have a clear melting point.
Additives increase the processing temperature of all plastics.False
Some additives, like plasticizers, lower processing temperatures.
How Do Additives Change Plastic Processing Temperatures?
Additives might seem unimportant, but they are the secret heroes in creating the ideal plastic item.
Additives such as plasticizers and stabilizers change how hot plastics need to be during processing. Plasticizers really help the plastic flow easily and reduce the heat needed. Stabilizers strengthen the plastic’s ability to withstand heat. This allows work at higher temperatures. These adjustments improve how plastics perform when they are being made.
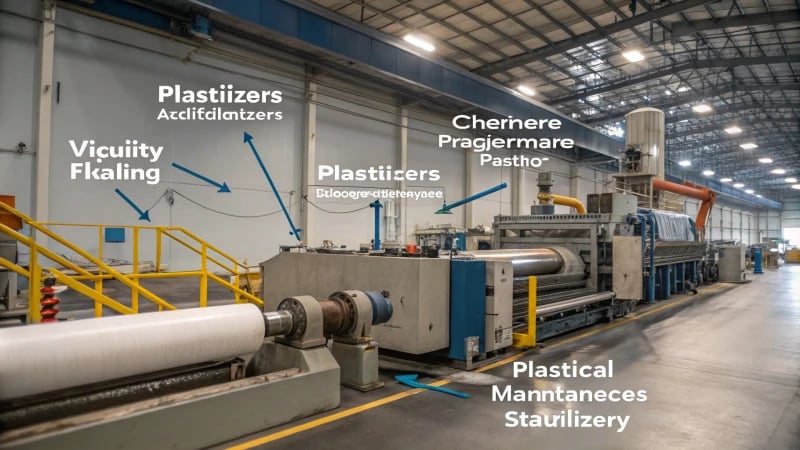
Influence of Chemical Structure
Plastics rely on their chemical makeup just as much as on additives. I remember a project with crystalline plastics like polyethylene2. These need careful heating due to their unique melting points. It’s very interesting how these materials, unlike non-crystalline ones like polycarbonate, require careful temperature control to change smoothly from solid to liquid.
Plastic Type | Melting Behavior |
---|---|
Crystalline | Distinct melting point |
Non-Crystalline | Gradual softening |
Polar groups in the molecular chains lead to higher temperature needs to break strong bonds. The process resembles guiding them delicately until they flow easily.
Role of Plasticizers
Plasticizers ease tension, much like friendly guests at a gathering. Once, with soft PVC, adding dioctyl phthalate3 felt transformative; processing temperatures surprisingly dropped by up to 40℃. This shift simplifies getting the right flexibility without needing too much heat.
Additive | Effect on Temperature |
---|---|
Plasticizer | Lowers |
Effect of Stabilizers
Stabilizers prevent plastic breakdown when it heats up. I recall using lead salt stabilizers in PVC. They kept the material intact even in soaring temperatures. The stability of our products remained constant, which was comforting.
Fillers and Reinforcing Agents
My first encounter with glass fiber fillers4 surprised me with how much they raised the viscosity. We had to adjust processing temperatures to maintain flow, like steering a ship through rough waters. Thankfully, surface changes sometimes ease this, keeping flow manageable.
Impact of Product Shape
Product design always intrigues me. Thin-walled items need higher heat for fluidity, whereas thick ones handle slower temperature settings. It’s similar to cooking: some meals need quick, intense heat; others slow cooking.
Processing Equipment Performance
Good equipment is crucial for smooth production. I remember adjusting our molding machines for even temperature distribution. The heating systems and screw designs interplay; it’s not just about achieving the right temperature but maintaining it to ensure quality and consistency.
Reflecting on these experiences highlights how every part of production – from additives to equipment – works together to create the perfect product. Chemistry and physics combine in a dance that always fascinates me.
Crystalline plastics require lower processing temperatures.False
Crystalline plastics need higher temperatures due to their distinct melting points.
Plasticizers reduce the glass transition temperature of PVC.True
Plasticizers enhance fluidity by lowering the glass transition temperature, reducing processing temperatures.
How Does Product Design Affect Processing Temperatures?
Picture this꞉ you have created the ideal product design and suddenly you discover the temperatures are incorrect. This situation really troubles designers. Grasping the details can truly solve the problem.
Product design affects processing temperatures through material choice, shape and how it functions. Crystallinity and additives are important parts that decide the temperature range needed for efficient processing. These factors are crucial for success.
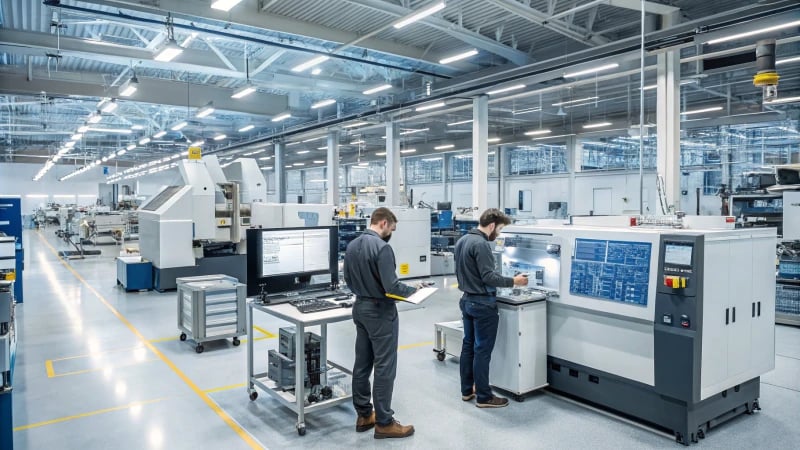
Material Characteristics and Processing Temperatures
One project involved picking materials for eco-friendly water bottles. Choosing polyethylene, which has a crystalline structure, meant hitting certain melting points for proper flow. These choices affected the production and taught me how important it is to know material properties.
Material Type | Characteristics | Processing Temperature |
---|---|---|
Crystalline | Clear melting point | Higher |
Non-Crystalline | Gradual softening | Wide range |
For more on optimizing product design with processing conditions, check guidelines from experts5.
Influence of Molecular Structure
Once, a colleague and I discussed low-density versus high-density polyethylene for a task. It was interesting to see how shorter molecular chains in low-density polyethylene required lower processing temperatures. This saved time and energy. Little changes in molecular structure really matter.
Additives and Their Impact
Experimented with additives like plasticizers in PVC. These lowered processing temperatures significantly. It felt like magic watching the material change with small adjustments. Stabilizers also allowed us to safely push materials a bit further.
Product Shape and Complexity
A product’s shape is very important. Worked on a thin-walled electronic casing that needed the right melt fluidity. Increased temperature made the material fill the mold entirely, especially during quick cooling.
Equipment Performance Considerations
Equipment performance is extremely crucial. The success depended on injection molding machines, especially their heating and cooling parts. Learned that good heating systems heat materials evenly, which is really important for good processing.
Understanding these details has helped in designing for efficiency and quality in manufacturing. By looking into these aspects, product performance improves for safe and effective production environments.
Crystalline materials require higher processing temperatures.True
Crystalline materials have clear melting points, necessitating higher temperatures.
Additives always increase processing temperatures.False
Additives like plasticizers can lower processing temperatures by reducing viscosity.
How Does Equipment Performance Impact Material Processing?
Have you ever thought about why certain materials act differently during production? The reason is all in the equipment. Equipment really matters.
Equipment performance is very important in material processing. It controls temperature, affects flow and impacts efficiency. Better equipment means higher material quality and fewer defects. Productivity is likely to increase in manufacturing with optimal equipment.
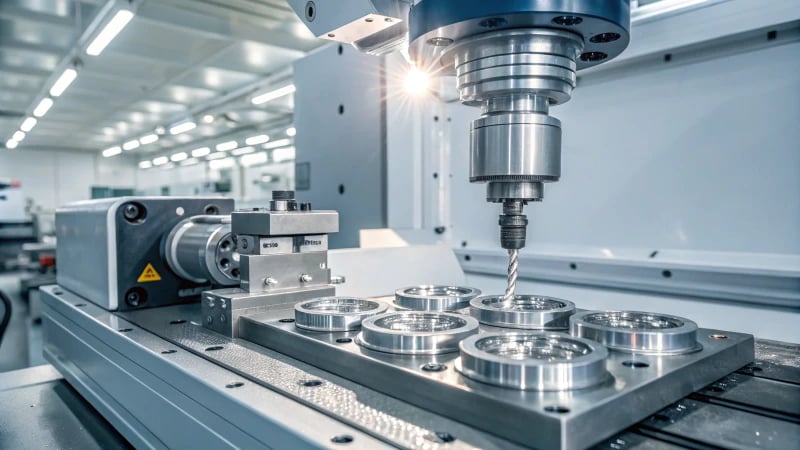
The Role of Heating and Cooling Systems
I recall standing in front of an injection molding machine’s heating system6 at my previous job. The need for even heating impressed me when I saw how crystalline plastics melted perfectly. It looked like pure magic. Uniform heating matters a lot, especially for plastics with a specific melting point, like polyethylene and polypropylene. These need exact temperature control.
Cooling systems play an unsung hero role. They handle mold temperature, which affects the final product’s quality. I learned this the hard way when a cooling system breakdown caused defects in our products. A reliable cooling system keeps everything steady during cooling.
Screw Design: Aspect Ratio and Speed
Screw design is an engineer’s puzzle! The right screw, with a large aspect ratio7 and correct compression, changes material processing. It feels like adjusting gears on a bike; too much or too little creates problems. These adjustments help plastics reach the right melt temperature.
Screw rotation speed influences friction heat, affecting processing efficiency. It’s like finding the perfect balance on a bike ride.
Influence of Material Additives
On one project, the choice of additives changed everything. Adding plasticizers, like dioctyl phthalate to PVC, lowers processing temperatures greatly. I remember the relief when we realized it improved fluidity at lower temperatures8, saving time and energy.
Stabilizers stop decomposition at high temperatures, giving more thermal stability. It’s amazing how fillers and reinforcing agents, like glass fiber, require equipment settings tweaks to keep viscosity.
Additive | Effect on Processing |
---|---|
Plasticizer | Lowers processing temp |
Stabilizer | Prevents decomposition |
Filler | Affects viscosity |
Product Shape and Equipment Adjustment
Designing thin-walled products taught me the value of precise control over temperature and pressure9. Seeing those thin walls form without issues was very rewarding. Meanwhile, complex designs need higher melt fluidity, testing equipment limits while keeping material integrity.
Understanding these complex relationships helps manufacturers optimize processes for better efficiency and product quality. Experienced professionals or newcomers alike benefit from recognizing these connections as they probably make a big difference in production outcomes.
Uniform heating is crucial for crystalline plastics.True
Uniform heating ensures crystalline plastics melt adequately for optimal fluidity.
Screw speed does not affect material processing efficiency.False
Screw speed generates friction heat, impacting processing efficiency.
What are the common challenges in managing processing temperature?
Understanding the complex details of controlling temperature in factories is similar to learning a dance – it’s all about accuracy and timing.
Controlling processing temperature requires solving problems like changes in material properties, effects from additives and limits of equipment. Each issue needs careful attention for best results. Attention is really needed for best results.
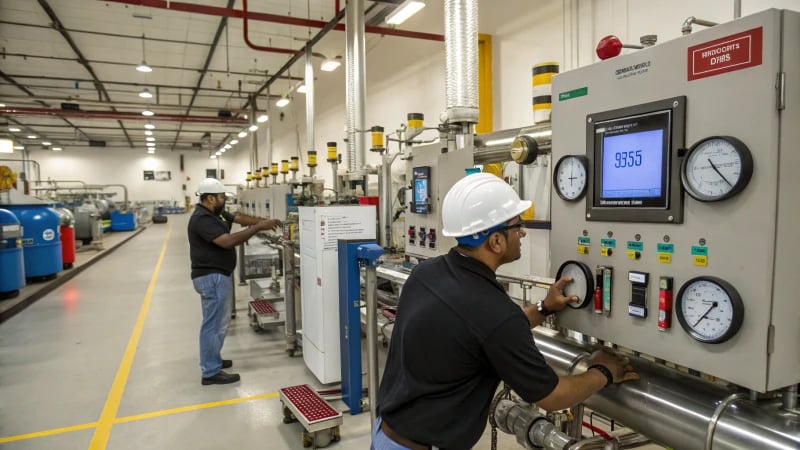
Understanding Material Properties
Materials act differently when heated. Plastics, for example, have special traits. Their chemical structure10 decides how they change with heat. Crystalline plastics like polyethylene turn from solid to liquid when heated enough, like ice cream melting perfectly. Non-crystalline ones soften slowly, offering more temperature options to work with.
Material Type | Characteristics |
---|---|
Crystalline | Clear melting point |
Non-crystalline | Gradual softening over temperature range |
Molecular chains11 matter, too. Short chains with few branches flow easily, while polar groups need more heat because of strong pull between molecules. It’s like urging a shy friend to dance.
Influence of Additives
Additives change materials in amazing ways. I worked on a project adding plasticizers to polyvinyl chloride, which made processing much easier at lower temperatures. Plasticizers lower glass transition temperatures and make the material flow better.
Additive Type | Impact on Processing Temperature |
---|---|
Plasticizer | Reduces temperature |
Stabilizer | Increases upper temperature range |
Stabilizers help materials stay strong at high temperatures. Fillers might slow flow but can be adjusted to behave better, like balancing creaminess and firmness in cooking.
Product Design Considerations
Designing a product feels like solving a puzzle. Shape and needs decide everything. Thin products need high heat to stay fluid before cooling. Once, designing electronic casings with complex paths required exact control of flow and heat.
Product complexity also influences temperature control. Intricate designs demand better fluidity to ensure the melt navigates complex channels efficiently.
Equipment Performance Factors
Now, equipment excites me the most. Good heating systems are crucial. They help materials work well without burning.
When using injection molding machines, I got obsessed with screw design. Proper size and compression improve heat creation while keeping materials safe.
Equipment Feature | Effect on Processing Temperature |
---|---|
Heating System | Influences material performance |
Screw Design | Affects plasticization and heat generation |
Understanding all this helps deal with temperature challenges wisely.
Crystalline plastics have a clear melting point.True
Crystalline plastics like polyethylene exhibit a clear melting point.
Plasticizers increase processing temperatures.False
Plasticizers reduce glass transition temperatures, enhancing fluidity.
Conclusion
Processing temperature of materials is influenced by crystallinity, molecular structure, additives, product design, and equipment performance, crucial for achieving optimal fluidity and quality in manufacturing.
-
Understand how machine heating systems influence material processing temperatures. ↩
-
Exploring crystallinity will provide insights into how different plastics behave under heat, helping you choose the right material for your needs. ↩
-
Understanding dioctyl phthalate’s role will guide you in selecting suitable plasticizers to optimize your product’s manufacturing process. ↩
-
Learning about glass fiber’s effects on plastics will assist in making informed decisions on using fillers for your designs. ↩
-
Learn how different materials impact the necessary processing temperatures for manufacturing efficiency. ↩
-
Explore how advanced heating systems improve precision in material processing. ↩
-
Learn about how screw design impacts material plasticization. ↩
-
Understand how plasticizers alter processing temperatures. ↩
-
Discover why precise temperature control is essential for complex molds. ↩
-
Learn how different chemical structures affect processing temperatures, helping to choose materials wisely. ↩
-
Understand how molecular structures influence material fluidity and processing temperatures for better material selection. ↩