Have you ever marveled at how some plastic parts can be incredibly thin yet remarkably strong?
The common technical difficulties in ultra-thin injection molding include flowability control, precise mold design, and stringent product quality management. These challenges arise from the need for high fluidity materials, meticulous cavity design, and avoiding defects like warping and shrinkage.
While understanding these issues is crucial, finding solutions to overcome them is equally important. The following sections will explore each difficulty in detail, providing insights into how manufacturers can optimize their processes for better outcomes.
High fluidity materials may reduce product strength.True
High fluidity aids cavity filling but often compromises mechanical strength.
- 1. How Does Material Selection Impact Ultra-Thin Injection Molding?
- 2. What Role Does Mold Design Play in Successful Ultra-Thin Injection Molding?
- 3. How Can Warping Deformation Be Prevented in Ultra-Thin Products?
- 4. What Are Effective Strategies for Controlling Shrinkage and Improving Product Strength?
- 5. Conclusion
How Does Material Selection Impact Ultra-Thin Injection Molding?
Material selection is pivotal in ultra-thin injection molding, impacting fluidity, strength, and process parameters.
Choosing the right material for ultra-thin injection molding is crucial due to its significant impact on flowability, strength, and compatibility with process parameters. High-fluidity materials are preferred, but they often require trade-offs with other properties such as heat resistance. Precise adjustments in processing techniques are essential to accommodate specific material characteristics.
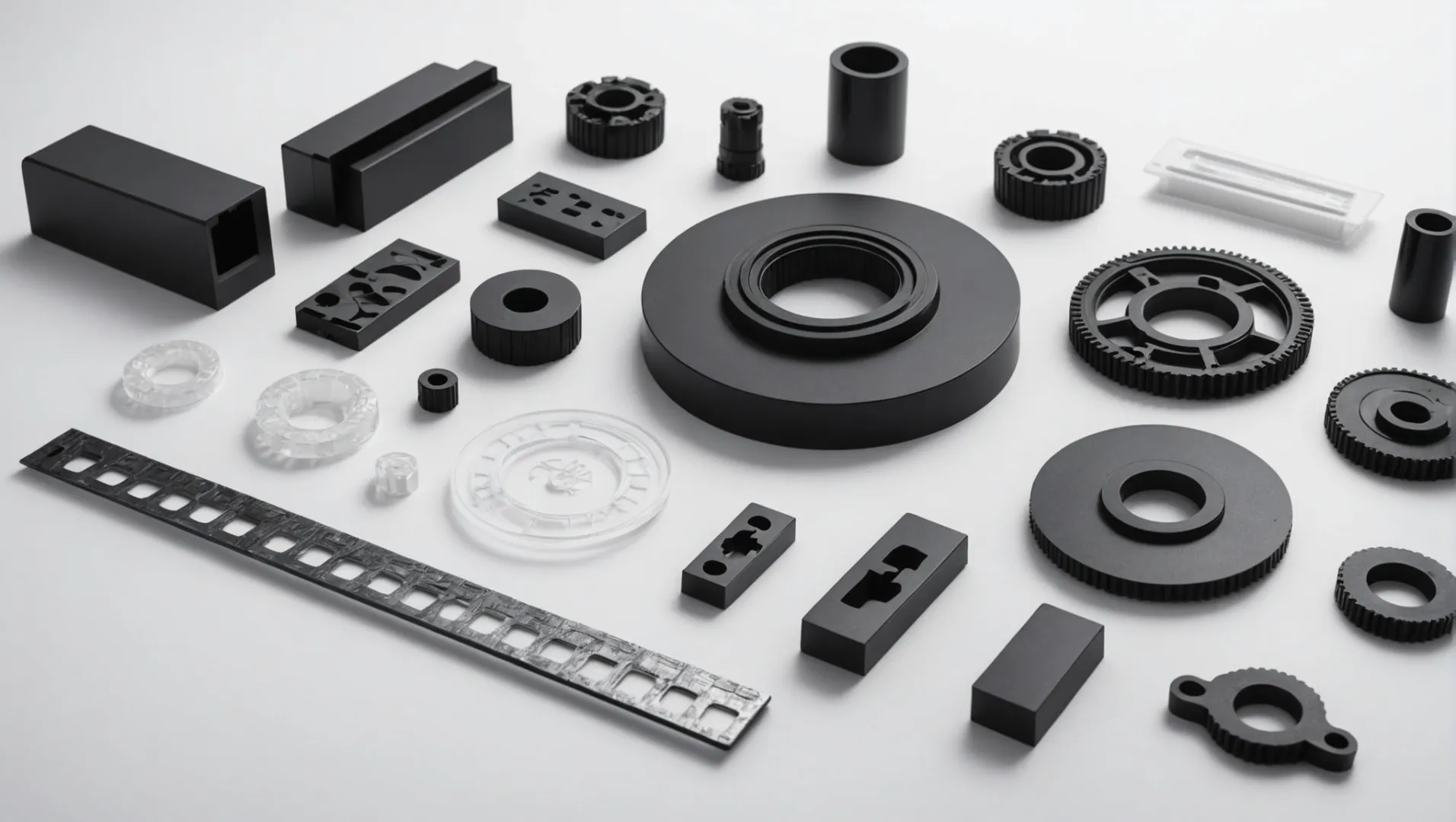
Importance of Material Flowability
One of the primary challenges in ultra-thin injection molding1 is managing the flowability of plastic materials. High fluidity is essential for filling the ultra-thin cavities efficiently. However, materials with the necessary flow properties may have drawbacks, such as reduced mechanical strength or lower heat resistance. For instance, choosing a polycarbonate with excellent fluidity might mean compromising on its ability to withstand high temperatures. This necessitates a delicate balance and selection based on the intended application of the molded part.
Balancing Material Properties
In material selection2 for ultra-thin injection molding, achieving the right balance between fluidity and other material properties like strength and thermal stability is critical. For example, a material that flows easily at lower temperatures may not provide the structural integrity required for certain applications. Engineers must consider how these materials will interact with process parameters and adjust accordingly. This might include altering injection speeds or pressure settings to optimize performance while minimizing defects.
Influence on Process Parameters
The selected material significantly affects the injection molding process parameters3. Each material has unique requirements for melt temperature, injection pressure, and cooling rates. Materials that decompose or discolor at higher temperatures may necessitate precise temperature control systems to maintain optimal flow without degradation. Likewise, materials requiring higher pressures for adequate cavity filling might lead to increased wear on molds, thus impacting longevity and maintenance costs.
Case Study: Trade-offs in Material Choice
A practical example of these trade-offs can be seen in the use of acrylonitrile butadiene styrene (ABS) versus polypropylene (PP) in ultra-thin applications. ABS offers superior strength and surface finish but requires careful handling to prevent overheating during the molding process. In contrast, PP provides better flow at lower pressures but may not offer the same level of structural support or surface quality. Understanding these material-specific characteristics helps manufacturers tailor their approach to meet specific design and performance criteria while avoiding potential pitfalls like warping or shrinkage.
High-fluidity materials reduce injection molding defects.False
High fluidity aids flow but can lead to defects like warping.
ABS offers superior surface finish in ultra-thin molding.True
ABS provides excellent surface quality, crucial for thin applications.
What Role Does Mold Design Play in Successful Ultra-Thin Injection Molding?
Mold design is the cornerstone of successful ultra-thin injection molding, influencing product quality and manufacturing efficiency.
In ultra-thin injection molding, mold design is crucial. It ensures precise cavity dimensions, effective temperature control, and high manufacturing accuracy, directly impacting the quality of the final product.

Importance of Cavity Design
The cavity design is pivotal in determining the success of ultra-thin injection molding. The cavity’s structure and dimensions4 must be meticulously planned to withstand the high pressures involved while maintaining ultra-thin wall sections. A well-designed cavity minimizes potential deformations or defects in the final product.
- Shape and Size: The shape and size of the cavity can influence the flow of the plastic melt. Complex shapes may require strategic gating systems to ensure uniform flow and prevent defects.
- Wall Thickness: Ultra-thin walls must be precisely defined to avoid structural weaknesses. Optimal thickness ensures the product maintains its integrity without excessive material use.
Precision in Mold Manufacturing
High precision in mold manufacturing is non-negotiable when aiming for ultra-thin injection molded products. The precision of the core and cavity components needs to be at the micron level to ensure dimensional accuracy and high-quality finishes.
Component | Required Precision |
---|---|
Core | Micron level |
Cavity | Micron level |
Any deviation can lead to mismatches, affecting both the appearance and functionality of the product. Therefore, employing advanced machining technologies and rigorous quality checks is essential.
Mold Temperature Control
Effective temperature control within molds significantly influences both the production process and final product quality. In ultra-thin injection molding, rapid heat transfer due to thin walls demands precise temperature management. This is achieved through advanced heating and cooling systems, ensuring the mold remains at an optimal temperature throughout the process.
- Heating Systems: These are used to bring molds to the required temperature quickly.
- Cooling Systems: Rapid cooling helps in maintaining production efficiency while preventing warping and shrinkage.
The role of mold design in ultra-thin injection molding is multifaceted, impacting material flow, product integrity, and manufacturing efficiency. Each aspect must be carefully considered and executed to produce high-quality, defect-free ultra-thin products.
Mold design affects product quality in ultra-thin molding.True
A well-designed mold ensures precise dimensions and effective temperature control.
Ultra-thin walls require less precision in mold manufacturing.False
High precision is crucial to maintain dimensional accuracy and product integrity.
How Can Warping Deformation Be Prevented in Ultra-Thin Products?
Warping deformation is a significant challenge in the production of ultra-thin injection molded products. To ensure product quality, manufacturers must address this issue effectively.
Preventing warping deformation in ultra-thin products requires precise control of injection parameters, optimal mold design, and strategic material selection. Adjustments in temperature, pressure, and speed during the molding process, along with a well-designed cavity, help reduce warping risks.
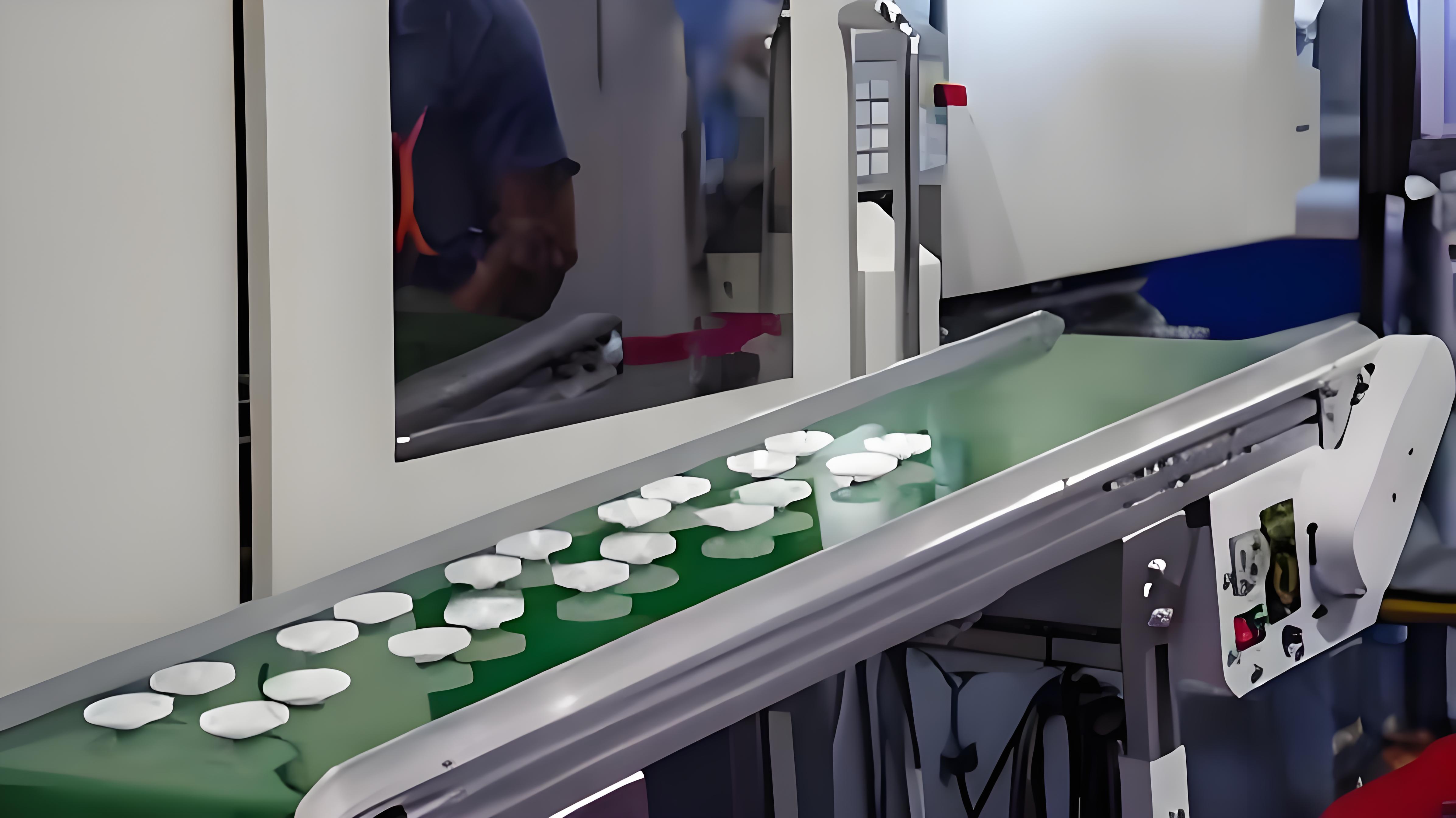
Importance of Material Selection
The selection of plastic materials plays a pivotal role in minimizing warping deformation. For ultra-thin products, plastics with high fluidity are preferred to ensure smooth filling of the cavity. However, these materials might compromise on strength or heat resistance, leading to potential complications5. Balancing these properties requires careful assessment and testing to determine the most suitable material for specific product requirements.
Optimizing Mold Design
Mold design is critical in preventing warping deformation. The design must accommodate the thin walls of the product while maintaining structural integrity. Key aspects include:
- Cavity Structure: The shape and size of the cavity must be meticulously planned to avoid stress concentrations.
- Temperature Control: Implementing an efficient heating and cooling system within the mold helps maintain consistent temperature distribution, reducing thermal gradients that cause warping.
- Precision Engineering: The mold’s core and cavity require micron-level precision to ensure accurate product dimensions.
Injection Molding Process Adjustments
Proper control of injection pressure and speed is essential for preventing warping. Excessive pressure can lead to internal stresses that distort the product post-cooling. Conversely, insufficient pressure may result in incomplete filling or lack of material, also causing deformation. Therefore, achieving a balance is crucial. Employing advanced sensors and control systems can help maintain optimal conditions throughout the injection cycle.
Role of Product Design
Finally, the product’s structural design should consider potential deformation issues. Uniform wall thickness and strategic reinforcement areas can mitigate warping tendencies. Incorporating features that distribute stress evenly across the product can also be beneficial.
By addressing these factors—material selection, mold design, injection parameters, and product design—manufacturers can significantly reduce the risk of warping deformation in ultra-thin products.
High fluidity plastics prevent warping in ultra-thin products.True
High fluidity ensures smooth cavity filling, reducing stress and warping.
Excessive injection pressure reduces warping risks.False
Excessive pressure increases internal stresses, leading to warping.
What Are Effective Strategies for Controlling Shrinkage and Improving Product Strength?
Ultra-thin injection molding faces unique challenges with shrinkage and product strength, demanding innovative solutions to maintain quality.
To control shrinkage and enhance product strength in ultra-thin injection molding, optimize material selection, adjust injection parameters, and refine cooling processes. Implementing these strategies can reduce defects and improve the mechanical properties of the final product.
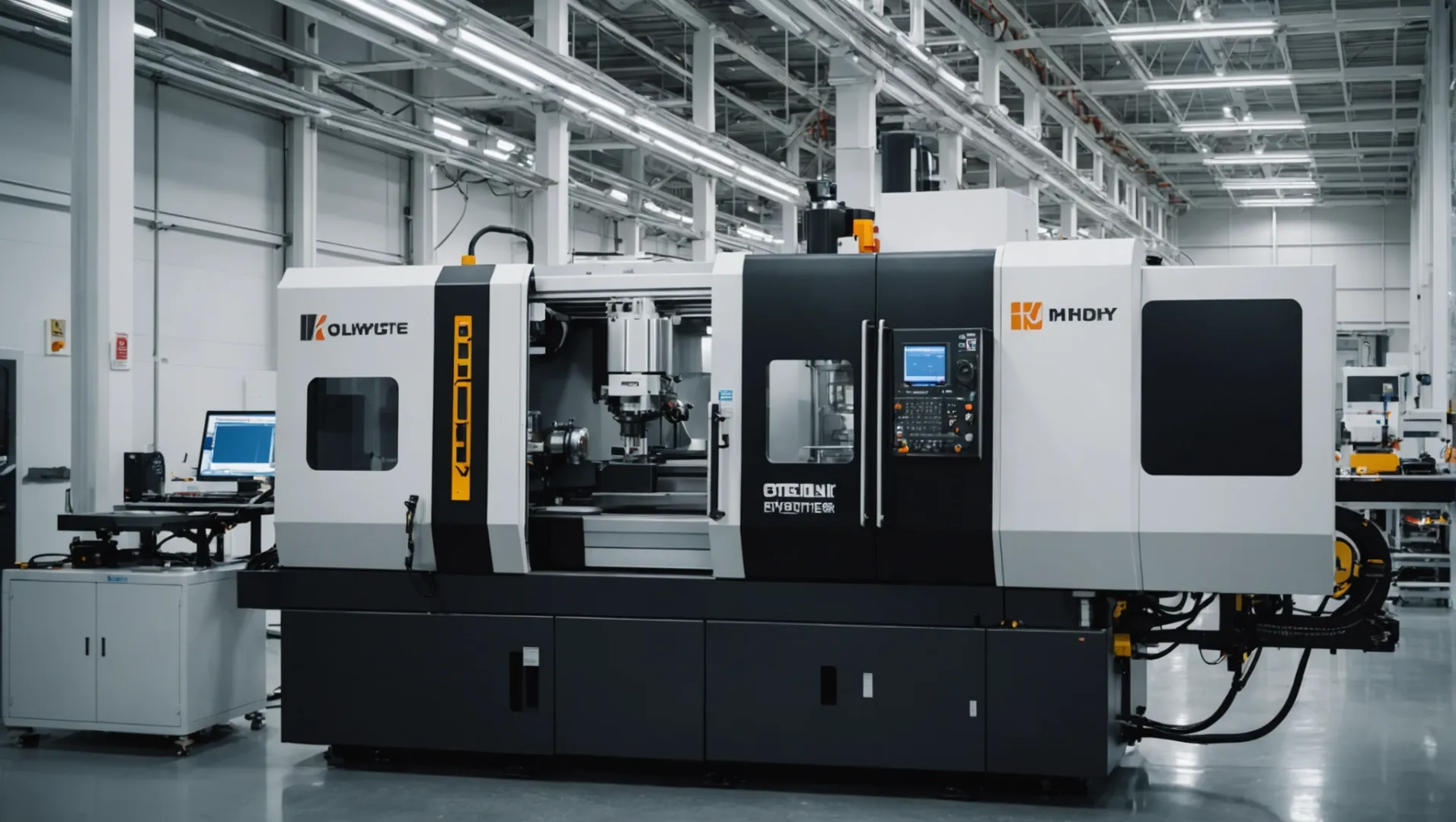
Understanding Shrinkage in Ultra-Thin Injection Molding
Shrinkage is a common issue in injection molding that can compromise the dimensional accuracy and appearance of the final product. In ultra-thin injection molding, this problem is exacerbated due to the thin wall sections, which can cool unevenly, leading to warping and shrinkage. To manage shrinkage effectively, it’s crucial to understand the role of material properties and processing conditions.
Material Selection: Choosing the right material is pivotal. High-fluidity plastics are essential for filling ultra-thin cavities, but they often come with trade-offs in terms of strength and heat resistance. To balance these properties, manufacturers might consider blending different polymers or adding fillers to enhance strength without compromising fluidity. For instance, incorporating glass fibers can increase tensile strength but requires careful consideration of the resultant impact on flowability.
Optimizing Injection Parameters
The parameters set during the injection molding process greatly influence shrinkage and product strength. Here are some key considerations:
-
Injection Pressure and Speed: High pressure and speed are necessary to fill thin cavities swiftly, but excessive force can lead to increased mold wear and internal stress. Precise control is needed to ensure adequate filling while minimizing stress-induced defects.
-
Melt Temperature: The melt temperature must be finely tuned; too high can cause degradation, while too low can hinder flowability. Using advanced temperature control technologies ensures the plastic remains at an optimal temperature for consistent quality.
Enhancing Product Strength
Improving the strength of ultra-thin molded products involves a multi-faceted approach:
-
Reinforcing Materials: Adding reinforcing agents like carbon or glass fibers can significantly boost product strength. However, these materials can affect the flow and final appearance of the product, so their inclusion needs careful calibration.
-
Cooling Rate Control: Managing the cooling rate is crucial as it affects crystallinity and thus the mechanical properties of the final product. Rapid cooling might cause thermal stresses and warping, whereas slow cooling could lead to sink marks or inconsistent shrinkage.
Strategy | Impact on Shrinkage | Impact on Strength |
---|---|---|
Material Blending | Reduces inconsistent shrinkage | Enhances uniformity and tensile strength |
Precise Pressure Control | Minimizes internal stress | Prevents warping and defects |
Reinforcing Agents | Limits shrinkage variability | Increases durability and rigidity |
Conclusion: Toward Optimized Manufacturing
While these strategies address many common issues in ultra-thin injection molding, ongoing research and technological advancements continue to offer new solutions. Manufacturers should remain adaptable, incorporating emerging techniques and materials to consistently improve product quality while minimizing defects like shrinkage.
Material blending reduces inconsistent shrinkage.True
Blending materials can balance properties, reducing uneven shrinkage.
High injection pressure always improves product strength.False
Excessive pressure can cause mold wear and stress-induced defects.
Conclusion
By addressing technical difficulties in ultra-thin injection molding, manufacturers can significantly enhance product quality and efficiency.
-
Discover essential flowability properties for ultra-thin cavity filling.: A 0.5mm wall thickness has a 0.2mm thick cured layer, leaving a 0.1mm thick flow path. When the filling is not completed and the flow channel … ↩
-
Learn how to achieve the ideal balance in material properties.: The accepted ground rule for balancing melt flow in multi-cavity injection molds is to achieve equal flow distance from the injection point … ↩
-
Understand how materials influence critical process settings.: The selection of materials in injection molding significantly impacts the setting of process parameters. Each material has unique properties … ↩
-
Understand how cavity design impacts flow and structural integrity.: Since the mold cavity is incredibly narrow in thin wall plastic injection molding, avoiding sharp corners and edges is even more critical to … ↩
-
Discover top plastics that balance fluidity with strength for your projects.: Try ABS. ABS works for many, many applications. It’s reasonably priced, strong, relatively tough, has a decent appearance and is forgiving even if you don’t … ↩