When it comes to injection molding, selecting the right gate type can feel overwhelming, yet it’s a pivotal decision that can change everything.
Gate types in injection molds, such as direct, point, and side gates, each offer unique advantages and challenges. Selecting the right one depends on factors like part size, wall thickness, material, and appearance requirements.
Understanding each gate type’s characteristics is just the beginning. The real challenge lies in balancing technical knowledge with practical application. Let’s dive deeper into these gate types and uncover how they can shape your molding process.
Direct gates minimize pressure loss in injection molding.True
Direct gates allow plastic melt to flow directly, minimizing pressure loss.
What Are the Advantages and Disadvantages of Direct Gates?
Direct gates play a pivotal role in injection molding, offering unique benefits and challenges.
Direct gates allow plastic melt to flow directly into the mold cavity, minimizing pressure loss and speeding up the molding process. However, they can leave noticeable gate marks and create large internal stresses, leading to potential defects.
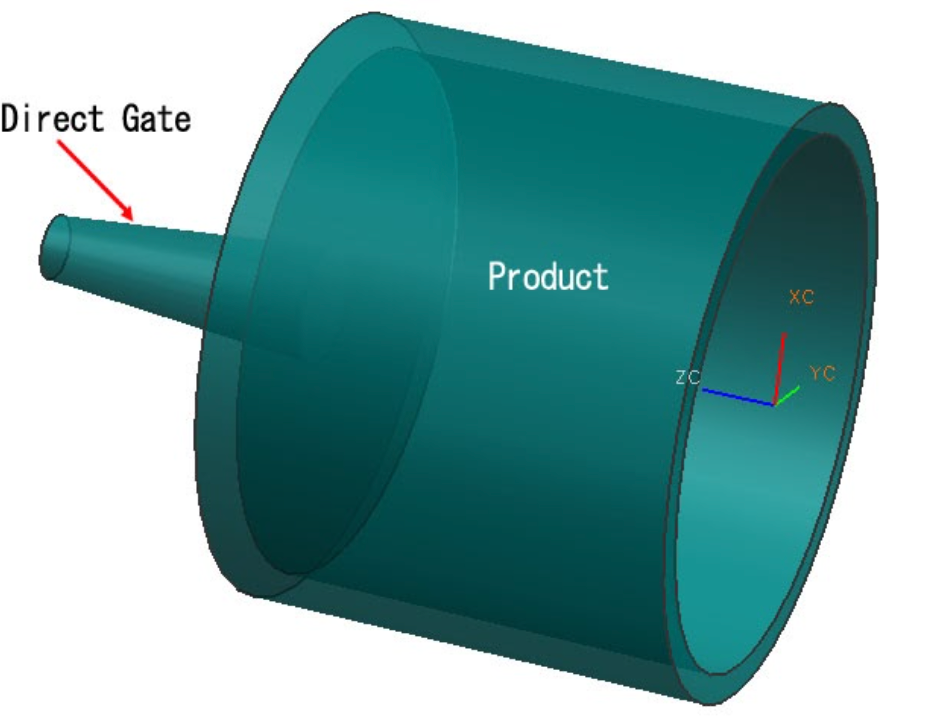
Understanding Direct Gates
Direct gates, also known as sprue gates, are a common choice in the injection molding process1 due to their simplicity and effectiveness. The plastic melt flows directly into the cavity, allowing for minimal pressure loss and faster cycle times. This makes direct gates particularly suitable for producing large or thick-walled plastic parts.
Advantages of Direct Gates
-
Efficient Flow: The design of direct gates ensures that the plastic melt reaches the cavity with minimal resistance. This efficient flow reduces the risk of material degradation and maintains the quality of the final product.
-
Pressure Transmission: With strong pressure holding capabilities, direct gates facilitate effective shrinkage compensation. This characteristic is crucial when molding thick-walled parts where uniform density is required.
-
Simple Mold Structure: The straightforward design of direct gates translates to easier manufacturing and maintenance of molds. This simplicity often results in reduced tooling costs and quicker production setups.
Disadvantages of Direct Gates
-
Gate Removal Challenges: One of the primary drawbacks is the difficulty in removing the gate from the finished part. This can lead to noticeable gate marks, which may not be acceptable for high-appearance products.
-
Heat Concentration: The area near the gate tends to retain heat longer, which can cause slow cooling and result in internal stresses. These stresses might lead to defects such as shrinkage pits or surface concave issues.
Applications and Considerations
When choosing direct gates, it’s important to weigh their advantages against their potential drawbacks. They are best suited for applications where appearance is not a critical factor, but structural integrity is essential.
Advantages | Disadvantages |
---|---|
Efficient flow | Difficult gate removal |
Strong pressure hold | Heat concentration |
Simple mold structure | Visible gate marks |
In conclusion, while direct gates offer significant benefits in terms of efficiency and cost-effectiveness, their application should be carefully considered in scenarios where cosmetic appearance is paramount. For detailed guidance on selecting the right gate type for your project, consider exploring gate type selection criteria2.
Direct gates minimize pressure loss in molding.True
Direct gates allow plastic to flow directly, reducing pressure loss.
Heat concentration in direct gates leads to faster cooling.False
Heat near direct gates causes slower cooling, not faster.
How Do Point Gates Influence Product Appearance and Automation?
Discover how point gates enhance both the aesthetic and automated aspects of injection-molded products.
Point gates improve product appearance by minimizing gate marks and support automation through automatic gate removal. They are ideal for complex molds requiring aesthetic precision and efficient production.
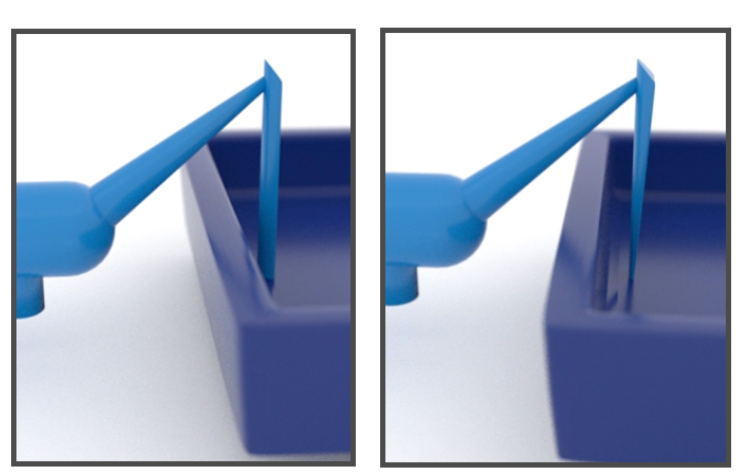
The Role of Point Gates in Product Appearance
Point gates are renowned for their ability to minimize visible marks3 on plastic products. Unlike direct gates, where gate removal leaves noticeable blemishes, point gates leave minimal traces due to their small size and strategic placement. This is crucial for products where appearance is paramount, such as consumer electronics or automotive parts.
The strategic placement of point gates at the edges or less visible areas ensures that the product’s surface remains smooth and aesthetically pleasing. This attribute makes them particularly advantageous for products with complex geometries or intricate designs, where maintaining a flawless finish is essential.
Enhancing Automation with Point Gates
In the realm of automation, point gates offer significant benefits by integrating seamlessly with automated systems. The design allows the gate to be automatically removed when the mold opens, which not only saves time but also reduces manual labor costs. This feature is especially beneficial in high-volume production environments where efficiency and speed are critical.
Moreover, their compatibility with automated systems means less human intervention is required, thereby reducing the potential for human error and increasing overall productivity. For instance, in industries producing small, delicate components, such as medical devices, the precision and consistency offered by point gates can drastically improve operational workflows.
Practical Applications and Limitations
Despite their advantages, point gates do come with certain limitations. The necessity for a three-plate mold structure can complicate the mold design and increase manufacturing costs. Additionally, they experience larger pressure loss compared to some other gate types, which could affect the fill rate and final product integrity if not carefully managed.
To mitigate these challenges, engineers must carefully balance design complexity with production efficiency. For instance, when producing barrel-shaped products4, multiple point gates can be employed to ensure even filling without compromising structural integrity. Likewise, when dealing with thin-walled items, adjusting wall thickness around the gate area can prevent cracking and maintain product durability.
Point gates minimize visible marks on molded products.True
Point gates are strategically placed to leave minimal traces.
Point gates increase manual labor costs in production.False
Point gates reduce labor costs by enabling automatic gate removal.
Why Choose a Side Gate for Multi-Cavity Molds?
Side gates are popular in injection molding for their flexibility and efficiency, especially in multi-cavity molds.
Side gates, known for their simple design and precise processing, are ideal for two-plate multi-cavity molds due to their flexible positioning and easy gate removal. This makes them suitable for improving filling conditions while maintaining cost-effectiveness in manufacturing processes.
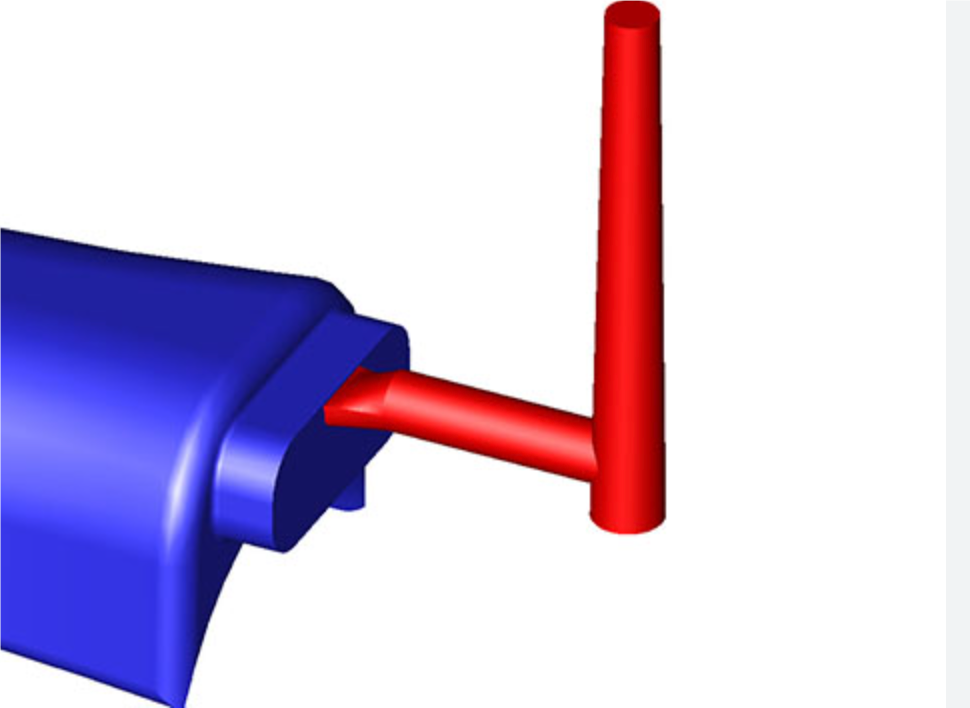
Understanding the Side Gate’s Versatility
The side gate, often referred to as the edge gate, is widely favored in multi-cavity mold designs5 for its versatility and ease of use. Its simple cross-section shape allows for precise processing, which is crucial when dealing with multi-cavity molds that require consistency across multiple parts. The flexibility in gate positioning further enhances its appeal, allowing manufacturers to optimize the filling process by strategically placing the gate to ensure even distribution of plastic melt.
Benefits of Using Side Gates
1. Flexible Positioning:
One of the primary benefits of side gates is their flexible positioning, which is particularly advantageous in multi-cavity molds. By positioning the gate on the side of the cavity, manufacturers can easily adjust the filling pattern to avoid common issues like weld lines and air traps. This flexibility is not only beneficial for product quality but also for optimizing cycle times.
2. Ease of Gate Removal:
In contrast to other gate types that may leave noticeable marks or require complex post-processing, side gates allow for easy removal with minimal trace. This feature is vital in high-volume production settings where efficiency and appearance are paramount.
3. Ideal for Two-Plate Molds:
Side gates are particularly well-suited for two-plate molds, a common setup in multi-cavity injection molding6. Their compatibility with this mold type simplifies the manufacturing process, reducing the need for complex mechanisms and enhancing production speed.
Considerations When Choosing Side Gates
While side gates offer numerous advantages, they are not without limitations. Issues such as weld marks or depressions can occur if not properly managed. Additionally, the injection pressure loss is typically larger compared to other gate types, necessitating careful planning and execution.
Here’s a quick comparison table summarizing side gates against other common gate types:
Gate Type | Advantages | Disadvantages |
---|---|---|
Side Gate | Simple design, flexible positioning, easy removal | Possible weld marks, large pressure loss |
Direct Gate | Fast feeding speed, strong pressure holding | Difficult gate removal, obvious marks |
Point Gate | Small residual traces, supports automation | Large pressure loss, complex mold needed |
By carefully weighing these factors and consulting with experienced mold designers, manufacturers can make informed decisions about using side gates to enhance their production processes.
Side gates are ideal for two-plate molds.True
Side gates simplify manufacturing in two-plate molds, enhancing speed.
Side gates leave noticeable marks on molded parts.False
Side gates allow easy removal with minimal trace, unlike other types.
What Factors Should Guide Your Gate Type Selection?
Choosing the right gate type is crucial for achieving optimal injection mold performance.
Factors such as plastic part size, material, wall thickness, and production needs guide gate type selection. Consideration of these factors ensures compatibility with molding requirements and desired product quality.
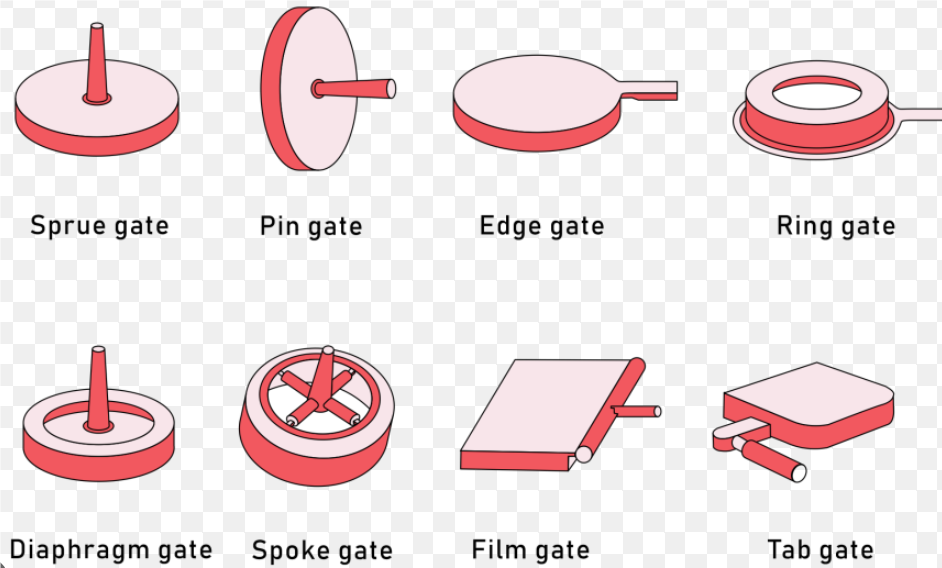
Understanding Part Specifications
When selecting a gate type for injection molds, the specifications of the plastic part are paramount. For instance, large or thick-walled parts benefit from using a direct gate7 due to its efficient pressure transmission and molding ease. Conversely, thin-walled or intricate parts might require a point gate8, which offers minimal impact on appearance due to smaller residual marks.
Material Considerations
Different plastics exhibit varied flow behaviors and cooling characteristics. Tough materials like PA (polyamide) may not fare well with latent gates9 due to cutting difficulties, whereas brittle materials like PS (polystyrene) can crack easily. The choice of gate must accommodate these material properties to prevent defects such as shrinkage or warping.
Material | Recommended Gate Type | Key Considerations |
---|---|---|
PA | Direct Gate | Avoid latent gates due to cutting issues |
PS | Side Gate | Prevent cracking and ensure uniform fill |
Production Batch and Cost Efficiency
High-volume production may favor gates that facilitate automation, like side gates10, due to their easy removal and minimal trace marks. Cost considerations also play a role; simpler gate designs like direct or fan gates might reduce manufacturing expenses.
Aesthetic and Structural Requirements
For parts where appearance is critical, such as consumer products, using a latent gate11 helps maintain a clean finish. Structural requirements also dictate gate choice; for example, spoke gates can enhance core stability in cylindrical parts.
Mold Structure Compatibility
The complexity of the mold structure is another factor. A three-plate mold structure12 is typically necessary for point gates, adding to mold complexity and cost. On the other hand, two-plate molds are compatible with side or direct gates, simplifying the mold design.
In conclusion, selecting the appropriate gate type involves balancing technical considerations with practical application needs. By evaluating these factors, manufacturers can optimize their molding processes to achieve superior product quality and efficiency.
Direct gates improve pressure transmission efficiency.True
Direct gates transmit pressure effectively, aiding in molding ease.
Latent gates are ideal for tough materials like PA.False
Latent gates pose cutting difficulties for tough materials like PA.
Conclusion
Choosing the right gate type enhances production efficiency and product quality. Take time to evaluate your design needs carefully.
-
Learn why direct gates are popular in injection molding.: This reduces labor costs, especially across higher part volumes, and ensures more consistent cycle times. The automatic shearing of excess gate … ↩
-
Discover criteria for choosing the best gate type.: Edge gates do not require a specific resin wither type, making them an ideal choice if you can simplify your design for injection molding. ↩
-
Learn how point gates reduce gate marks for better product aesthetics.: It allows the molten plastic to flow into the cavity from the bottom, which can help to reduce the visible gate marks on the part. ↩
-
Explore methods to use point gates effectively in barrel-shaped items.: An injection molding gate is a critical component in the mold design, serving as the point of entry for molten plastic into the mold cavity. … ↩
-
Learn how flexible positioning enhances mold efficiency.: Designing symmetrical parts like a left- and right-hand side into a single mold can reduce piece-part costs. ↩
-
Discover why two-plate molds suit side gates well.: Two-plate molds are often less expensive to build than multi-plate molds, and they also require less money to maintain. These advantages contribute to their … ↩
-
Learn how direct gates improve pressure transmission and molding ease.: Injection molding gates are openings in molds that allow molten plastic to enter the cavity while controlling the direction and volume of flow. ↩
-
Discover how point gates minimize residual marks on products.: It helps control the flow of joining plastic, ensuring correct filling of mold cavities and minimizing the occurrence of defects such as gaps, … ↩
-
Understand why latent gates may not suit tough or brittle materials.: The challenge is that, once the part is ejected from the mold, the sprue, runner, or small lump of plastic that remains attached to the gate must be trimmed … ↩
-
Explore the automation advantages of side gates in manufacturing.: All our wooden gates can be made suitable to be installed as an automated/electric sliding gate, however they are still made and supplied as a pair of gates. ↩
-
Find out how latent gates help achieve a clean product finish.: This paper compares the perspectives of product attributes and consumer behaviour through discussing two theoretical models (behavioural … ↩
-
Learn about the role of three-plate molds with point gates.: When the part is too large for a two-plate mold, or when many injection locations are required, a three-plate mold is used. … plate mold injection molding … ↩