Have you ever felt the thrill of turning complex designs into functional art?
For effective overmolding in multi-step processes, select compatible materials, optimize mold designs, and ensure strong bonding. These practices enhance product functionality and aesthetics while managing costs.
I remember the first time I tackled a multi-step overmolding project; it was like piecing together a puzzle, where every choice mattered. Beyond just understanding the basics, diving deep into these processes can transform how your products perform and stay within budget. Let’s explore some advanced techniques that could change the way you design and produce.
Compatible materials are crucial in overmolding.True
Using compatible materials ensures strong bonding and product integrity.
Overmolding increases manufacturing costs significantly.False
Proper design in overmolding can maintain cost-efficiency.

- 1. Why Does Material Selection Matter in Overmolding?
- 2. What should I consider when designing for multi-step overmolding?
- 3. How Can You Optimize Mold Design for Precision and Efficiency?
- 4. How Can You Ensure Strong Layer Bonding in Overmolding?
- 5. How Does Overmolding Compare with Insert Molding?
- 6. What Are Common Challenges in Overmolding and How to Overcome Them?
- 7. Conclusion
Why Does Material Selection Matter in Overmolding?
Imagine the thrill of crafting a product that not only meets but exceeds both performance and aesthetic expectations.
Material selection in overmolding is crucial for ensuring a strong bond and optimal product performance by choosing materials with compatible thermal properties and shrinkage rates.
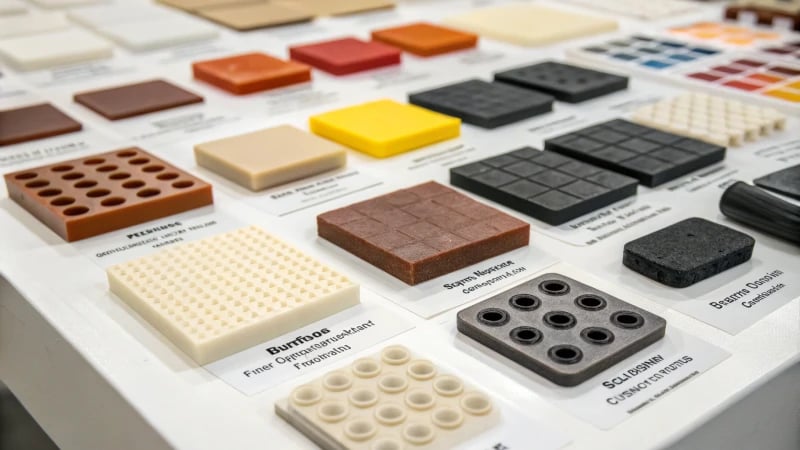
A little bit of text that will be used as a placeholder in the content area of the page. This is just some random text that is being used to fill up space and show how a paragraph will look when it is rendered on the screen. The quick brown fox jumps over the lazy dog.
Material compatibility affects overmolding success.True
Compatible materials ensure strong bonds and product durability.
Testing is unnecessary before full-scale production.False
Prototyping helps identify issues, ensuring better overmolding outcomes.
What should I consider when designing for multi-step overmolding?
Remember that time you marveled at a complex, multi-colored gadget and wondered how it came to life?
Consider material compatibility, mold design, part geometry, and process parameters for successful multi-step overmolding, ensuring strong adhesion, durability, and appealing aesthetics.
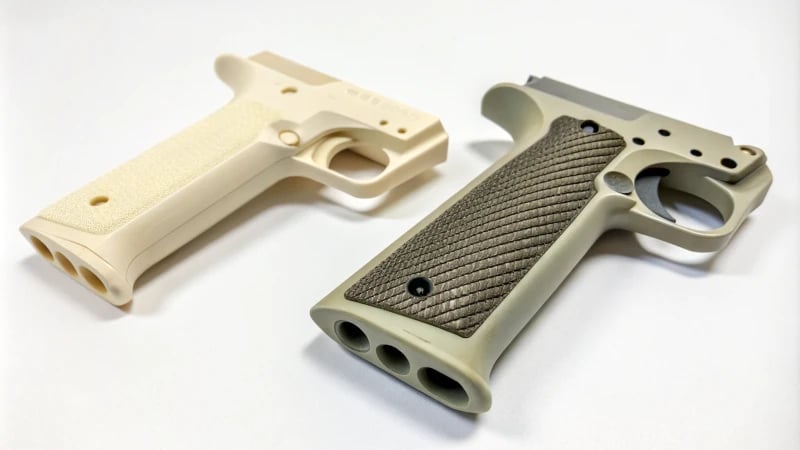
That’s the magic of multi-step overmolding—a technique that’s become second nature to me in my years designing for consumer electronics. Let’s unravel the secrets behind creating these durable and visually striking products.
Material Compatibility
I once had a project where the materials didn’t quite play well together. This hiccup was a turning point for me. Ensuring compatibility between the substrate and overmold materials is non-negotiable. Different materials expand and contract differently under heat, affecting how well they bond. Using a compatibility chart1 early in the design phase has saved me countless headaches.
Mold Design
Mold design can make or break the outcome. I’ve learned that features like gating and venting are crucial. They help maintain a consistent flow and prevent defects that can arise from trapped air. Precision in temperature control is another lesson learned the hard way—it’s vital for ensuring each material layer sticks just right.
Feature | Consideration |
---|---|
Gating | Uniform flow to avoid weak spots |
Venting | Prevents air entrapment |
Temperature | Optimal adhesion between layers |
Part Geometry
Geometry isn’t just about looks; it’s about strength too. I remember an early design of mine that had sharp corners—it looked sleek but was prone to cracking under stress. By utilizing design software2, I now simulate and tweak designs to find that sweet spot where form meets function.
Process Parameters
Fine-tuning process parameters like injection speed, pressure, and cooling rates is akin to being a maestro conducting an orchestra. These settings need to be just right for each specific material, ensuring not only optimal adhesion but a flawless surface finish too.
Adhesion Techniques
Exploring different adhesion techniques has been a game-changer in my work. Techniques like surface treatments or primers can work wonders on materials that naturally resist sticking together.
- Surface Treatments: Improve adhesion by modifying surface energy.
- Primers: Create a binding layer between dissimilar materials.
By honing in on these design considerations, I’ve been able to elevate the performance and aesthetic appeal of multi-step overmolded components in my projects. Leveraging industry insights3 keeps me ahead of the curve, ensuring my designs meet the specific needs of each project while pushing the envelope of what’s possible.
Material compatibility affects overmolding adhesion.True
Different materials have varying properties, impacting adhesion stability.
Gating design is irrelevant in multi-step overmolding.False
Proper gating ensures uniform flow and prevents weak spots in the material.
How Can You Optimize Mold Design for Precision and Efficiency?
Ever felt like your mold design process could use a bit of a boost? Let me walk you through some proven strategies that have truly transformed my approach, bringing precision and efficiency to the forefront.
Optimize mold design by selecting suitable materials, incorporating efficient cooling systems, and using advanced CAD software. Regular design reviews and continuous testing enhance precision and manufacturing efficiency.
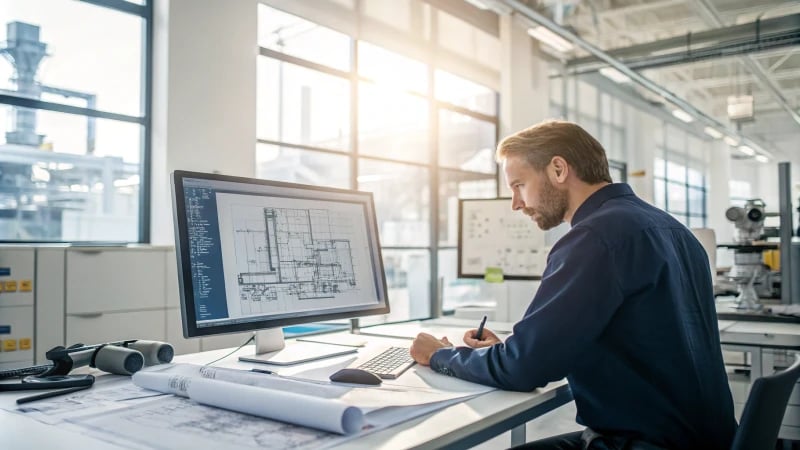
Material Selection: The Foundation of Precision
Imagine this: you’re in the middle of a project, and suddenly, everything seems to click because you chose the right material. It was like finding the perfect pair of shoes that fit just right! Different materials4 can dramatically affect your design’s durability and performance. High-grade steel or aluminum alloys, for instance, have been my go-to for their wear resistance and heat distribution.
Material Type | Benefits | Considerations |
---|---|---|
Steel | Durable, precise | Cost, weight |
Aluminum | Lightweight, fast | Lower strength |
Cooling Systems: Enhancing Efficiency
Picture yourself in the thick of a summer day without air conditioning. That’s what it’s like designing molds without an efficient cooling system. Implementing conformal cooling channels has slashed my cycle times and upped product consistency5. Advanced CFD (Computational Fluid Dynamics) software is my secret weapon for designing these systems.
CAD Software: A Designer’s Best Friend
When I first started using cutting-edge CAD software, it felt like I had upgraded from a bicycle to a high-speed train. With simulation features, I could foresee and fix potential issues before they caused any real trouble. Keeping my CAD tools updated means I’m always at the cutting edge of design technology.
Design Reviews and Testing: Ensuring Precision
In my experience, regular design reviews are like having a second pair of eyes on everything—absolutely invaluable! They catch potential mistakes early on. Thorough design audits6 coupled with prototypes have saved me from many headaches. Continuous testing throughout the production cycle helps maintain high standards of precision and efficiency.
By focusing on these core areas, I’ve been able to significantly improve mold designs, which in turn has led to superior product quality and more streamlined manufacturing processes. Embracing these strategies has not only kept me competitive but also passionate about the evolving field of mold design.
High-grade steel is ideal for mold durability.True
High-grade steel offers excellent wear resistance and precision in molds.
Aluminum molds are stronger than steel molds.False
Aluminum is lightweight and fast but has lower strength compared to steel.
How Can You Ensure Strong Layer Bonding in Overmolding?
Ever wondered how overmolding keeps everything from your toothbrush to your smartphone looking sleek and functioning perfectly?
Ensure strong layer bonding in overmolding by focusing on surface preparation, material compatibility, and process optimization. Use techniques like plasma treatment, compatible polymers, and optimized mold design for durable bonds.
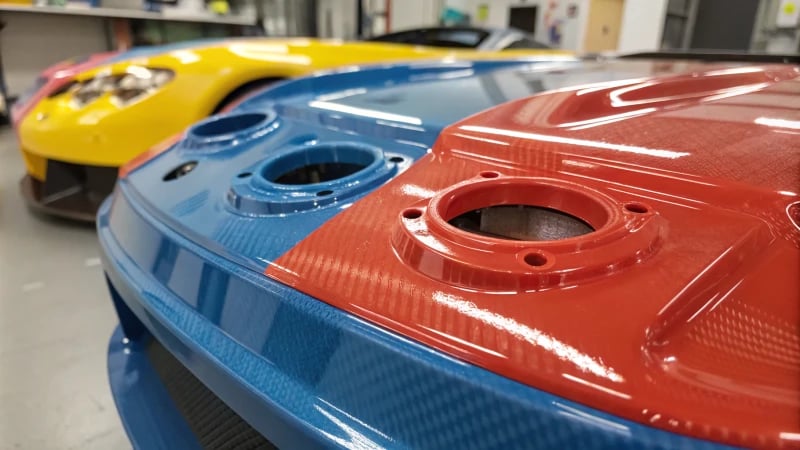
Understanding Overmolding Dynamics
Overmolding feels like a magic trick sometimes—combining different materials to create something that’s not only useful but also a pleasure to use. When I first started working with overmolding, the most fascinating part was how the layers came together, almost like they were meant to be. The secret sauce? Achieving a robust bond between those layers. Let’s dive into the techniques that can make or break that perfect bond.
Surface Preparation
I remember back when I was a rookie in this field, I underestimated how important surface preparation was. Think of it as prepping a wall before painting; if you skip this step, nothing sticks! Techniques like plasma treatment or corona discharge are game-changers—they boost the surface energy, making the layers practically cling to each other.
Technique | Description |
---|---|
Plasma Treatment | Cleans and activates surfaces for better adhesion |
Corona Discharge | Increases surface energy to enhance bonding |
Material Compatibility
Picking the right materials is like choosing dance partners. They need to move seamlessly together, or else someone’s toes get stepped on. Incompatible materials can lead to issues like poor adhesion or even delamination. I learned this the hard way once when mismatched polymers led to a product failure. Now, I always consider both the chemical and thermal properties of the materials involved.
For instance, using polymers with similar coefficient of thermal expansion (CTE) can minimize stress at the interface during thermal cycling.
Process Parameters Optimization
Once, I got too eager and cranked up the heat during a trial run—big mistake! It’s crucial to tweak parameters such as temperature, pressure, and time. Too much heat can ruin materials, while too little pressure leaves layers barely holding hands instead of embracing tightly.
Parameter | Effect on Bonding |
---|---|
Temperature | Affects material flow and bond strength |
Pressure | Ensures intimate contact between layers |
Time | Allows sufficient reaction or curing for adhesive layers |
Mold Design Considerations
Mold design isn’t just about creating a pretty shape; it’s about ensuring everything fits together perfectly. Features like vents and gates need careful planning to avoid air pockets or incomplete fills that can weaken bonds. I’ve had designs where neglecting these details meant going back to the drawing board.
Moreover, accommodating thermal expansion and contraction is crucial to prevent stress points that might cause failure.
Designing molds with appropriate draft angles also aids in reducing ejection forces that might damage bonds during demolding.
Implementing Adhesion Promoters
Adhesion promoters are like matchmakers for incompatible materials. They help create a bond where none seemed possible. However, selecting the right promoter is vital—one wrong choice could lead to more problems than solutions.
While useful, they should be selected carefully to prevent chemical incompatibilities.
For further exploration of overmolding techniques, consider checking7 additional resources that discuss innovative approaches and challenges in overmolding.
Plasma treatment increases surface energy for better adhesion.True
Plasma treatment cleans and activates surfaces, enhancing adhesion.
Incompatible materials improve layer bonding in overmolding.False
Incompatible materials lead to poor adhesion or delamination.
How Does Overmolding Compare with Insert Molding?
Picture this: you’re a designer faced with the choice between overmolding and insert molding, each promising unique advantages. Which path do you take?
Overmolding adds material over a substrate; insert molding places inserts in the mold first. Both techniques are essential for making complex multi-material products.
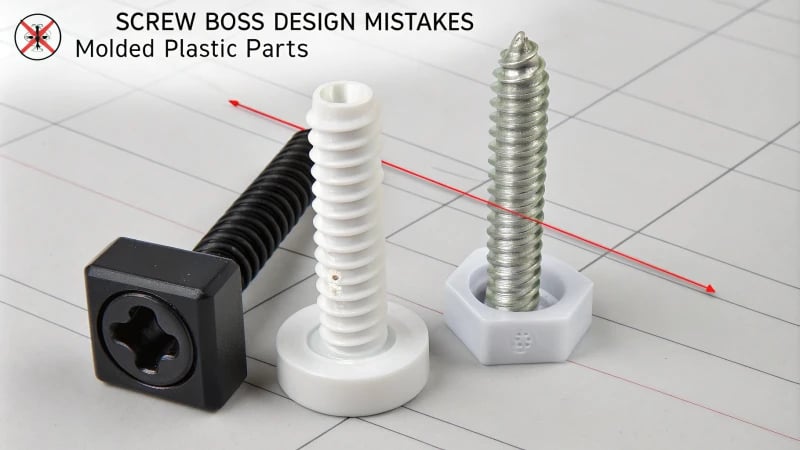
The Basics: Overmolding vs. Insert Molding
I remember the first time I had to decide between overmolding and insert molding for a project. It felt like standing at a crossroads in design, each path offering a different set of possibilities. Overmolding is like adding that final flourish to a painting, molding a second material over a pre-existing part to enhance its look or feel. It’s the technique behind those comfortable grips on your favorite tools or the sleek finish on your electronic gadgets.
In contrast, insert molding is more about the nuts and bolts—quite literally. It’s the process of embedding metal parts within plastic components to create something robust and integrated. This is the go-to method when you’re aiming for something that screams durability and strength, like engine components in cars or intricate aerospace parts.
Technique | Primary Function | Common Materials |
---|---|---|
Overmolding | Adds layers for grip, aesthetics, or insulation | Thermoplastics, elastomers |
Insert Molding | Combines metal and plastic for functional parts | Metals, engineering resins |
Advantages and Applications
Over the years, I’ve come to appreciate the flexibility that overmolding brings to the table. It’s like having a magic wand to add functionality and flair to products. Think of those fancy tool handles that fit perfectly in your hand or the rugged cases that protect your tech from life’s little mishaps. Overmolding can even make products more durable by adding layers that absorb shocks.
Then there’s insert molding, the unsung hero of manufacturing when it comes to creating parts with high structural integrity. The automotive and aerospace industries love it for good reason. It’s all about seamlessly marrying metal with plastic to form components that need to be strong yet precise. When you want to cut down on post-processing steps and still achieve complex designs, insert molding is your best friend.
Challenges and Considerations
Every time I embark on an overmolding project, I remind myself to consider material compatibility8 between materials and the potential heat-related challenges. It’s vital to ensure that the original part can handle the heat without warping—a lesson I learned the hard way on one of my early projects.
Insert molding has its quirks too. Getting those inserts just right in the mold is crucial to avoid issues like misalignment—a bit like assembling a jigsaw puzzle where every piece needs to fit perfectly while accounting for thermal expansion properties of both materials involved.
Key Factors in Decision-Making
Choosing between these two techniques often boils down to what you want from your final product. If it’s all about ergonomics or aesthetics, overmolding might be the way to go. But if precision and mechanical strength are non-negotiable, then insert molding should be your pick.
For anyone in the thick of decision-making—like me during those critical project phases—it helps to dive deep into resources on process optimization . They offer invaluable insights for achieving top-notch results with both techniques.
Overmolding involves adding layers for grip or aesthetics.True
Overmolding is used to add ergonomic grips, seals, or aesthetic layers.
Insert molding is unsuitable for automotive applications.False
Insert molding is widely used in the automotive industry for robust components.
What Are Common Challenges in Overmolding and How to Overcome Them?
Overmolding might seem like a magical process that combines materials for a perfect product, but it’s more like a complicated dance requiring finesse and strategy.
Overmolding challenges include material compatibility, adhesion, and complex mold design. Overcome these by choosing compatible materials, optimizing processing conditions, and designing precise molds.
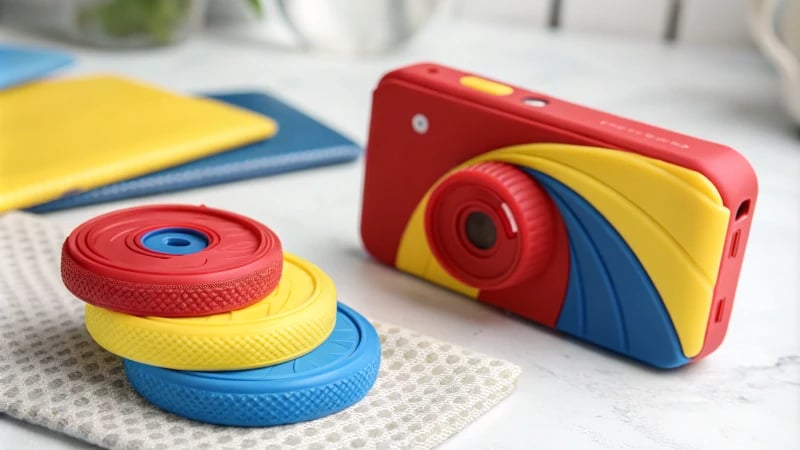
I remember my first experience with overmolding vividly. It was like trying to blend two colors of Play-Doh without ending up with an unsightly mess. As a designer, the joy comes from seeing two materials come together seamlessly, but the challenges can be daunting.
Material Compatibility
One of the first hurdles I faced was ensuring the materials actually liked each other. Imagine trying to make two people who don’t get along work together—it’s similar when dealing with materials that have different thermal expansion rates or chemical resistance. Testing smaller samples became my go-to strategy to avoid unpleasant surprises like warping or poor adhesion.
Material A | Material B | Compatibility | Notes |
---|---|---|---|
ABS | TPU | High | Excellent for flexible grips |
PC | PVC | Moderate | Needs careful temperature control |
Adhesion Problems
Adhesion is like the glue in a relationship; without it, things fall apart. Some materials just don’t want to stick together naturally. I learned early on that using techniques like plasma treatment or corona discharge could significantly improve surface energy, boosting adhesion between layers9. Adjusting process parameters such as pressure and temperature was another vital step.
Mold Design Complexities
Designing molds felt akin to solving a puzzle with too many pieces. The complexity comes from having to accommodate different materials while ensuring they bond well and maintain the product’s integrity. I found that using advanced CAD software10 allowed me to predict how materials would behave, considering factors like shrinkage and heat distribution.
Process Optimization
Fine-tuning is the name of the game here. It’s like adjusting the knobs on an old radio to find the perfect station. Monitoring systems became my best friend in ensuring parameters such as temperature, pressure, and cycle time were just right.
Parameter | Ideal Range | Impact on Product |
---|---|---|
Temperature | 180°C – 250°C | Affects material flow |
Pressure | 1500 – 2500 psi | Ensures proper filling |
Navigating through these complexities has taught me that overmolding is as much about patience and precision as it is about technical knowledge. With each project, I learn something new that helps refine my approach and enhance the quality of my work.
Material compatibility affects overmolding success.True
Incompatible materials can cause warping or poor adhesion.
Advanced CAD software complicates mold design.False
Advanced CAD software aids in creating precise mold designs.
Conclusion
This article outlines best practices for designing overmolding in multi-step processes, emphasizing material compatibility, mold design, and process optimization to enhance product performance and aesthetics.
-
Learn which materials work best together to avoid adhesion issues. ↩
-
Find tools that help visualize and optimize complex geometries effectively. ↩
-
Gain expert perspectives on optimizing overmolding processes. ↩
-
Discover different materials used in mold making and their benefits to choose the best option for your designs. ↩
-
Explore how conformal cooling can enhance efficiency and consistency in injection molding processes. ↩
-
Learn about the role of design audits in ensuring precision and preventing costly errors. ↩
-
Learn about the latest advancements and challenges faced in the field of overmolding. ↩
-
Discover crucial factors in selecting compatible materials for successful overmolding and insert molding processes. ↩
-
Clicking this link offers insights into methods for enhancing adhesion between layers, including surface treatment techniques. ↩
-
Explore this link to discover top CAD software options that facilitate precise mold design, crucial for complex overmolding projects. ↩