That feeling when all pieces fit? Like a cake baked just right or a project coming together smoothly? PET injection molding seeks that experience.
The optimal process conditions for PET injection molding include drying the resin at 120-150°C for 4-6 hours to achieve moisture content below 0.02%, setting the injection temperature between 260-280°C, and maintaining mold temperatures of 30-85°C depending on the desired crystallinity.
Imagine grasping every detail of your materials like reading a tricky recipe – it requires accuracy, patience and the proper environment. Dive deeper into how one might refine these factors for excellent outcomes.
Drying PET resin at 120-150°C for 4-6 hours is optimal.True
This range decreases moisture levels under 0.02%, stopping flaws.
How Does Drying Temperature Affect PET Injection Molding?
The drying heat is important in PET injection molding. It affects both product quality and efficiency.
Drying temperature directly influences the moisture content of PET resins, affecting their flowability and crystallization during injection molding. Proper drying ensures reduced defects and enhanced mechanical properties.
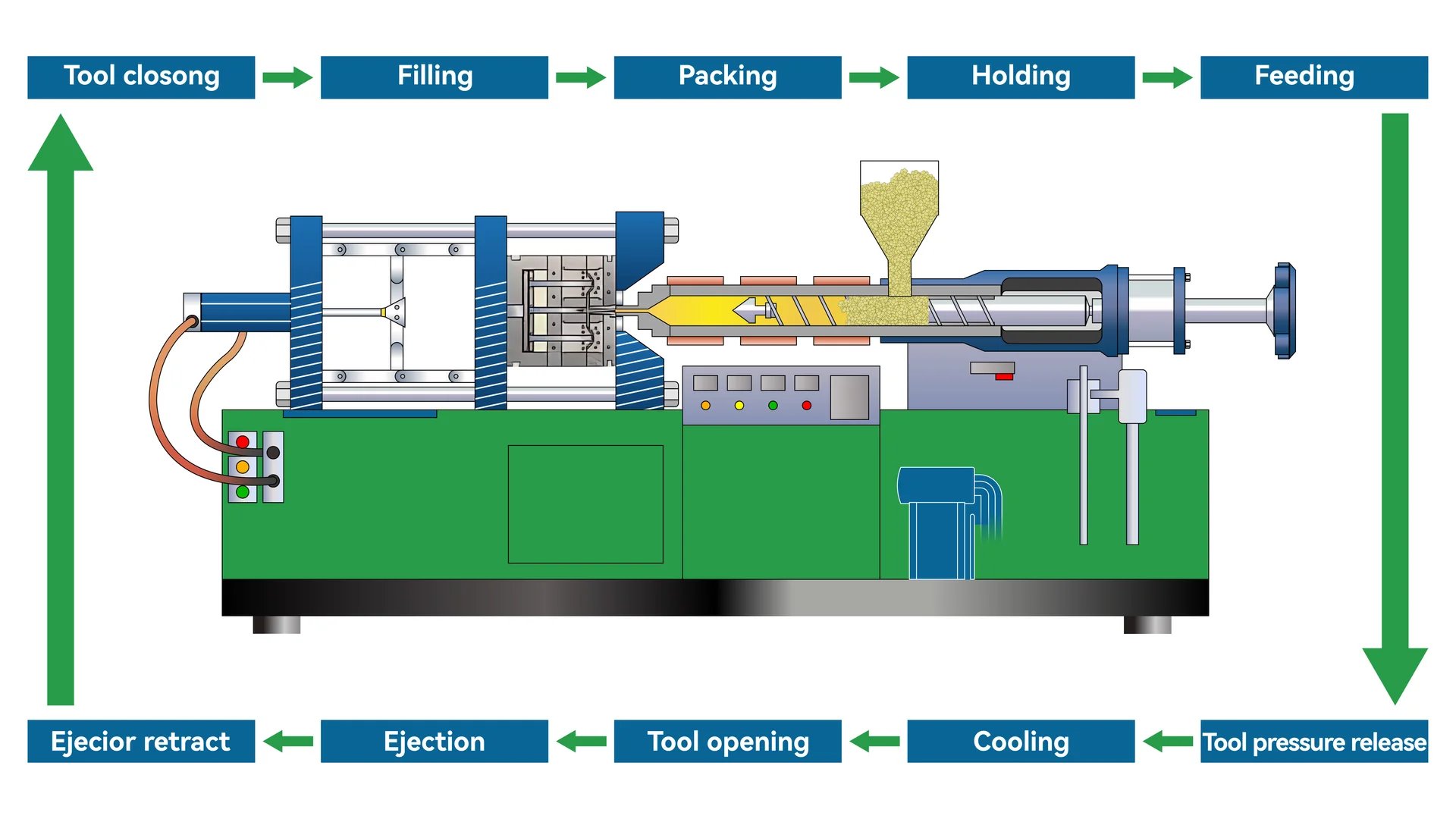
The Importance of Correct Drying Heat
Polyethylene terephthalate (PET), a kind of thermoplastic polyester1, feels the effects of moisture, which can really change its behavior during injection molding. PET takes in water from the air, which, if not removed well, causes hydrolysis when processing. This reaction can break the polymer chain, giving poor strength and bad surface.
The drying heat for PET usually lies between 120-150°C, with a drying time from 4 to 6 hours. This step lowers the moisture level to less than 0.02%, keeping the resin’s quality and bettering the flow during molding.
Impact on Molded Part Quality
Reaching the correct drying heat is key for keeping the shape stability and strength of the molded items. Not drying enough may cause:
- Brittleness: Water-driven hydrolysis can cause brittle materials, reducing the strength of the final product.
- Surface Flaws: High water content might create splay marks, bubbles or other surface issues.
- Uneven Crystallinity: Correct drying helps even crystallization, improving how PET products look and work.
Drying Heat | Drying Time (hours) | Water Content (%) |
---|---|---|
120°C | 4-6 | <0.02 |
135°C | 3-5 | <0.02 |
150°C | 2-4 | <0.02 |
Improving Process Efficiency
Managing the drying heat also betters the molding cycle time and energy use. Well-dried PET allows for quicker cycle times due to improved flow rates and reduced cooling needs. It also lowers waste by reducing defects that cause rejections.
Proper drying heat is vital, but also aligning other settings like mold heat and injection force with the material’s needs is very important for best outcomes. For more details on PET‘s mechanical properties2 and other processing details, keep reading our full guide.
Drying PET below 120°C increases brittleness.True
Not enough drying keeps moisture, which results in brittleness.
Optimal PET drying temperature is 100-120°C.False
The best temperature to dry PET is 120-150°C.
What Role Does Mold Design Play in PET Molding Efficiency?
The layout of the mold is crucial in increasing the efficiency and quality of PET molding.
Mold design significantly impacts PET molding efficiency by optimizing cooling systems, ensuring uniform material flow, and minimizing cycle times. Effective design results in better product quality, reduced waste, and enhanced production speed.
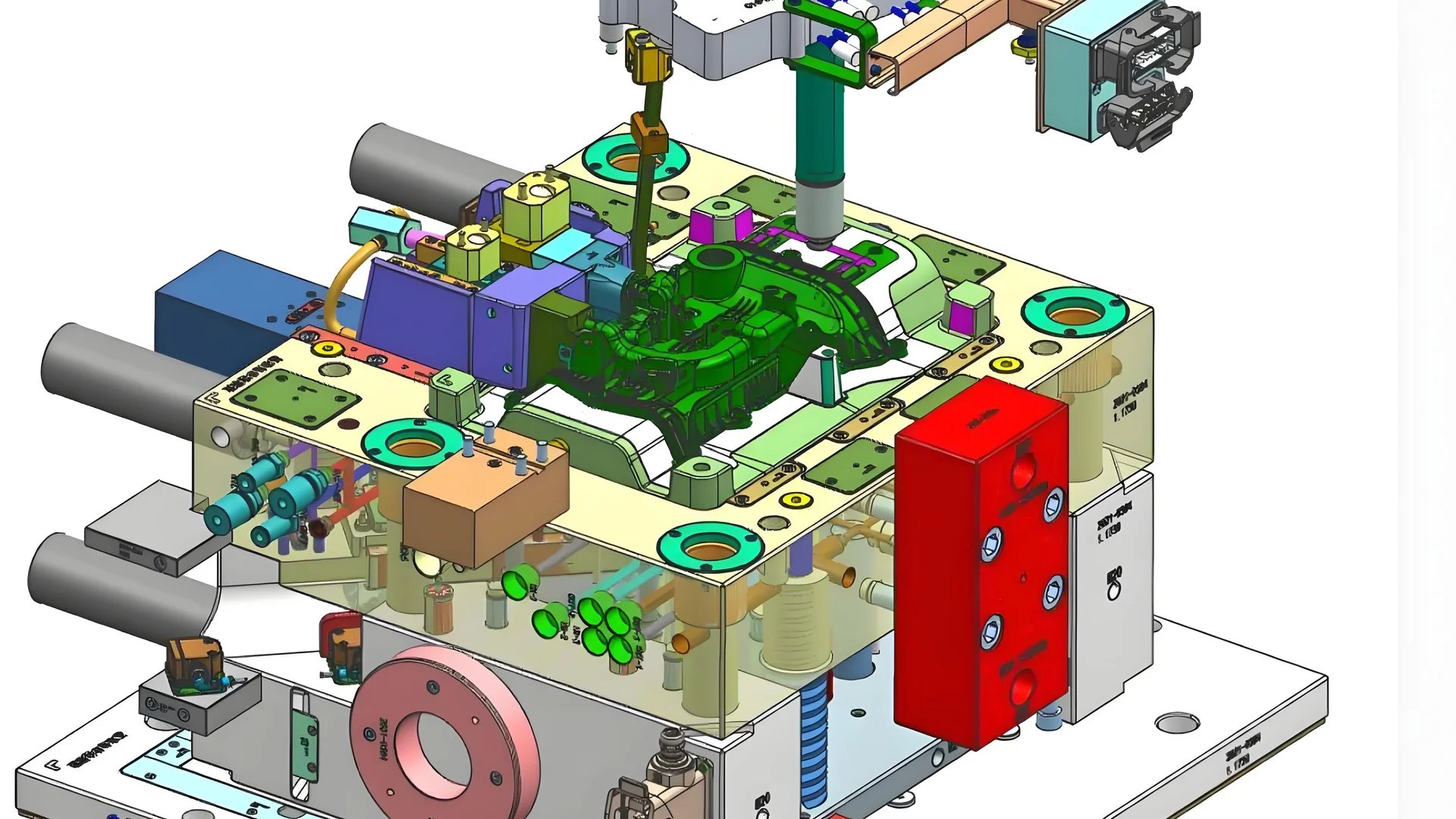
Importance of Cooling Systems
A key part of mold planning3 involves adding a good cooling system. PET materials become very hot during the molding process, needing strong cooling to keep the mold’s temperature steady and lower cycle times. Useful cooling methods, such as using water or air channels, help remove heat quickly. This directly affects how well production goes.
Material Flow Optimization
Even material movement within the mold is vital for the best PET products. Mold planning should allow smooth material flow to avoid issues like bending or uneven thickness. This needs smart placement of gates and runners to let molten PET reach all parts of the mold swiftly and evenly. Gate planning4, whether on the side or direct, affects the flow and must be carefully planned to keep product quality high.
Cycle Time Reduction
Good mold plans significantly lower cycle times, thus greatly improving production. By cutting the time for heating, filling, cooling, and removing the product, makers can reach higher output. For example, adding automatic ejector systems makes removing the mold faster, leading to quicker cycles.
Structural Integrity and Durability
Choosing the right mold materials is crucial for keeping structure strong through many cycles. High-quality alloy or pre-hardened steels often get picked for their resistance to wear and corrosion. These materials make the mold last longer, keeping its performance steady over time.
Considerations for PET-Specific Challenges
PET has special properties, like high glass transition temperatures and slow crystallization rates, which bring unique problems in mold design. Alterations like adding nucleating agents help with slow crystallization while reinforced glass fiber boosts stiffness and heat properties. By adapting mold plans for these traits, makers boost PET molding efficiency.
In conclusion, mold planning is more than shaping a cavity; it involves a full strategy to improve each part of the PET molding process for better efficiency and higher product quality.
Cooling systems stabilize mold temperature in PET molding.True
Cooling systems efficiently stabilize temperature, improving cycle times.
Gate design does not affect material flow in PET molds.False
Gate design is important for even material flow and good product quality.
How to Optimize Injection Temperature for PET?
Injection temperature holds a key position in how well PET molding processes work and the quality they achieve.
To optimize injection temperature for PET, maintain a range of 260-280°C. This ensures sufficient flow and crystallization while minimizing defects. Adjustments should be made based on material grade and mold design.
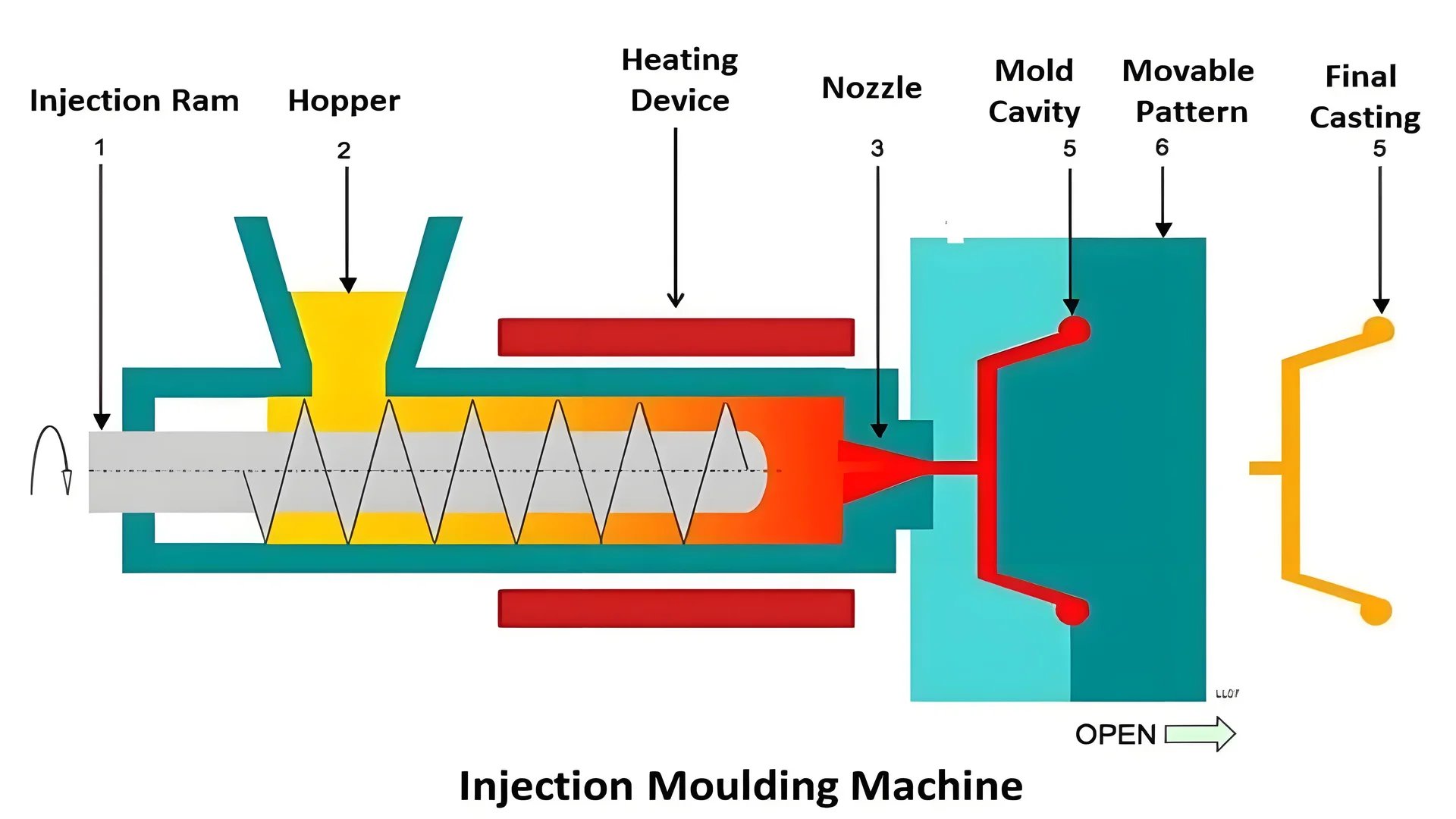
Basics of PET Injection Molding
Polyethylene terephthalate (PET) is a type of plastic with great strength and durability. Adjusting injection temperatures is important when trying to get good product quality5. Wrong temperatures result in problems like warping, bad filling, or poor surfaces.
Setting the Best Injection Temperature
The right temperature for PET most often falls between 260-280°C. This allows for proper melting and flow, filling up the mold evenly. Changes might be needed depending on the material or improvements added.
Injection Zone | Temperature (°C) |
---|---|
Nozzle | 280-295 |
Front Section | 270-275 |
Back Section | 250-270 |
Things That Change Temperature Settings
- Material Type: Special PET types with extra substances might need slight temperature adjustments to stop damage or burning.
- Mold Design: The mold’s shape and thickness might change temperature needs. Thicker molds could require higher temperatures to fill completely and avoid defects6.
- Surrounding Conditions: Room temperature and moisture in the air affect PET‘s performance, needing some changes in settings.
Watching and Changing During Production
Watching closely during injection is essential. Tools like sensors and data help find problems early. Quick changes keep the product good.
Advantages of Proper Temperature
Good temperature not only upgrades the final product but also speeds up production by cutting cycle times and lowering waste from errors. This means saving costs and raising productivity over time.
PET injection temperature should be 260-280°C.True
This range allows perfect flow and hardening, reducing flaws.
Higher ambient temperature doesn't affect PET molding.False
Environmental conditions such as temperature affect PET's behavior in shaping.
What are the Common Challenges in PET Injection Molding?
Moving through the PET injection molding process introduces special difficulties because of the material’s distinct characteristics.
Common challenges in PET injection molding include slow crystallization rates, high molding temperatures, and long production cycles. These factors can lead to poor dimensional stability and impact performance, necessitating precise control over processing conditions to ensure product quality.
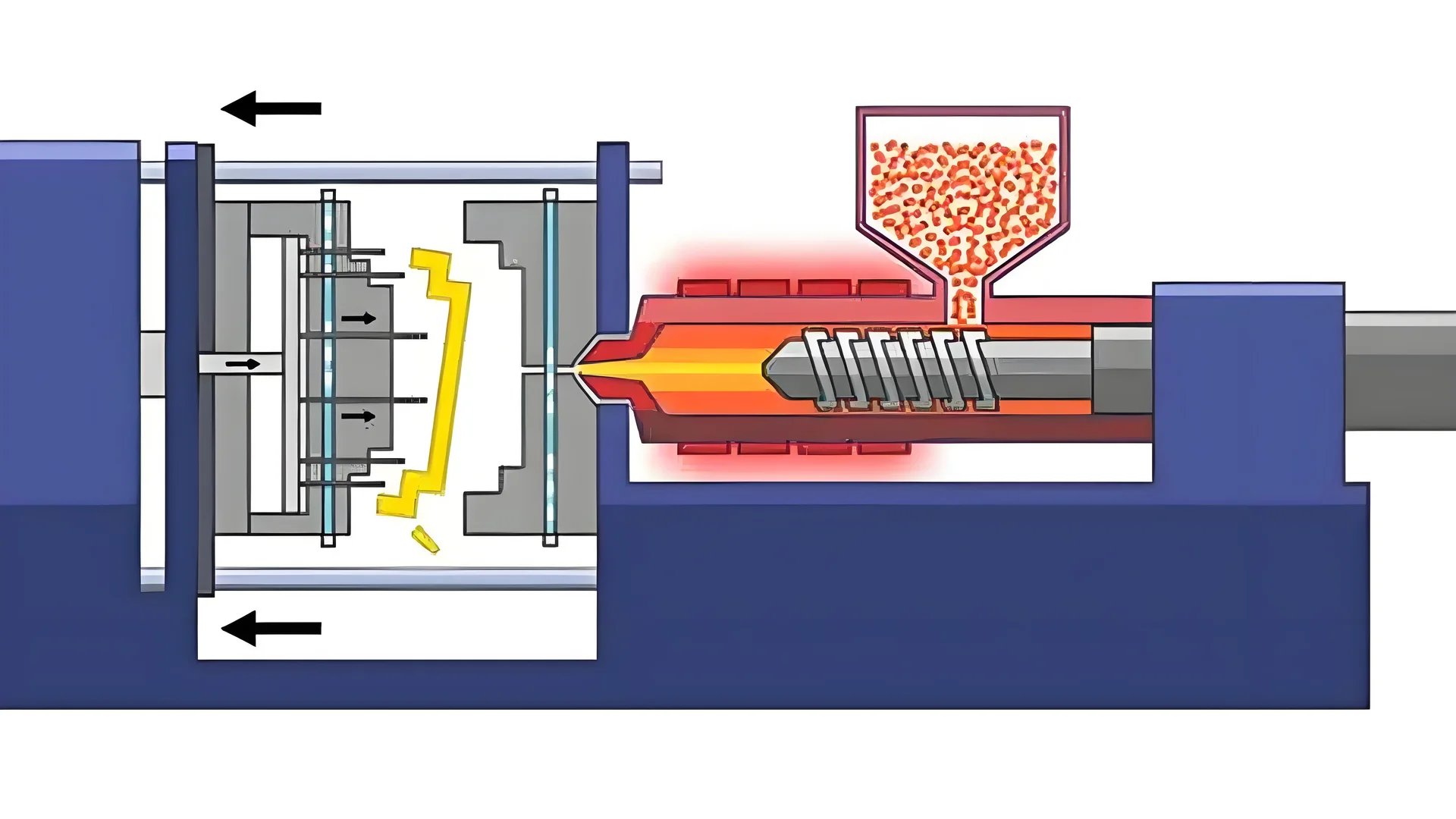
Understanding PET
PET or Polyethylene Terephthalate, is a strong plastic7 that resists many chemicals. It is tough but hard to shape.
Slow Crystallization: PET becomes solid slowly, which means shaping takes longer. This can make the finished object less stable and affect how well it works.
High Heat Needed: Shaping PET needs high heat, usually 260-280°C. This uses a lot of energy and might harm the mold over time. Keeping the right temperature is really important to avoid problems.
Long Production Times: Slow solidifying means longer production, which costs more and reduces work speed. Special additives might help PET solidify faster, but they must be chosen carefully to protect PET‘s quality.
Preparing and Handling Material
Good preparation8 is key to solving these issues. PET must be dried well to keep moisture very low before shaping. This stops the material from breaking down during shaping.
Mold Design
Good mold design9 helps speed up production and improve product quality. Adding good cooling systems and placing gates well helps manage the heat and flow inside the mold, resulting in better solidification and stronger products.
Control of Environment and Process
Managing surroundings like humidity and temperature in the shaping area is important for consistent results. Using advanced systems helps fix any changes in ideal conditions quickly.
These details show how complex PET shaping is and show why a well-rounded process is needed for better results.
PET's slow crystallization increases production cycle times.True
Gradual crystallization speeds extend molding times, impacting productivity.
High molding temperatures are unnecessary for PET.False
PET needs high heat (260-280°C) for proper shaping.
Conclusion
Learning about PET injection molding settings improves quality and productivity. Explore more detailed changes for the best outcomes. Want to raise your method up a level?
-
Understand the fundamental characteristics of thermoplastic polyesters like PET.: Polyesters are typically crystalline thermoplastics with excellent chemical resistance, relatively low water absorption, and excellent tensile and electrical … ↩
-
Learn more about PET’s mechanical strength and applications.: Hardness, Shore D · 71.4 – 87.0, 71.4 – 87.0 ; Ball Indentation Hardness, 117 – 194 MPa, 17000 – 28100 psi ; Tensile Strength, Ultimate, 22.0 – 830 MPa, 3190 – … ↩
-
Explore how cooling systems enhance efficiency in injection molding.: An improper injection mold cooling process, then, will almost always result in part defects that require rework or discard. The cooling process … ↩
-
Learn how gate design affects material distribution in molds.: The location of the injection gate is of great importance since it can influence the flow direction and melt solidification during and after filling [3]. ↩
-
Explore how precise temperature control affects product quality.: Temperature significantly impacts each step of the entire plastic injection molding process. This is why temperature control is crucial and … ↩
-
Understand typical issues caused by incorrect temperature settings.: 7 Common Injection Molding Defects and How to Avoid Them · 1. Flow Lines · 2. Sink Marks · 3. Surface Delamination · 4. Weld … ↩
-
Learn how PET’s crystallinity affects its molding process.: On the other hand, at temperatures below Tg, the mobility of the chains is restricted, leading to limited crystallization [50]. Other factors … ↩
-
Explore why drying PET resin is crucial before molding.: Water molecules bond strongly to the PET polymer chain. · Hot drying air loosens the bonds between moisture and the resin, allowing the molecules … ↩
-
Understand how mold design influences PET injection efficiency.: Injection moulding allows PET to be shaped into rigid packaging formats. PET initially comes in small pellet form. During the injection moulding … ↩