Color consistency in injection molded products is a game-changer for brand loyalty and product quality.
To ensure color consistency in injection molded products, focus on controlling raw materials, optimizing the injection molding process, maintaining molds, and implementing robust color management practices. These strategies help achieve uniformity across batches and enhance product quality.
But there’s so much more beneath the surface! Let’s explore these elements in depth and uncover the secrets to achieving flawless color consistency.
Temperature control affects color consistency in injection molding.True
Stable temperatures ensure uniform material flow and color distribution.
What Are the Common Causes of Color Inconsistency in Injection Molding?
Color inconsistency in injection molding can lead to significant quality issues and customer dissatisfaction.
Color inconsistency in injection molding is primarily caused by fluctuations in raw material quality, variations in processing parameters, and inadequate mold design and maintenance. Addressing these elements through stringent controls and regular monitoring can greatly enhance color uniformity.
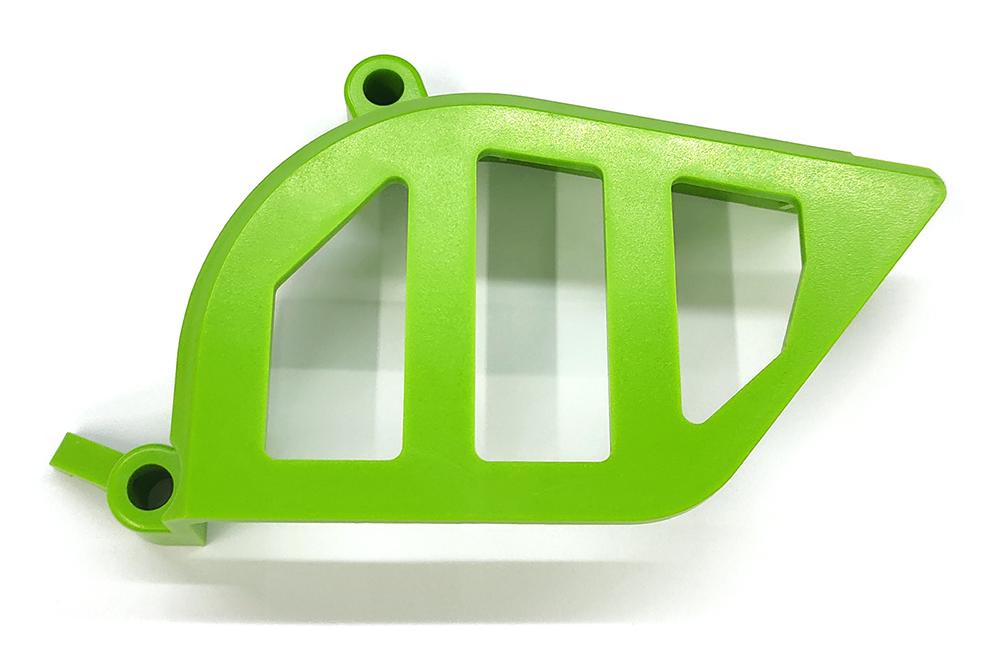
Raw Material Variability
One of the primary causes of color inconsistency in injection molding is the variability in raw materials. It is crucial to source from reliable suppliers1 who provide consistent masterbatches and pigments. Ensuring a stable supply chain reduces color variation risks significantly.
Incoming Inspection Protocols
Implementing strict incoming inspection protocols is essential. Utilizing tools like colorimeters can help in detecting even slight variations in raw material color. Raw materials should meet predefined standards before being accepted for production.
Injection Molding Process Parameters
Temperature Control
Fluctuations in temperature during the injection molding process can severely impact color consistency. Stable barrel, nozzle, and mold temperatures are critical to ensuring uniform color dispersion. Using advanced temperature control systems, such as thermocouples, can mitigate these fluctuations.
Pressure and Speed Management
Inconsistent injection pressure or speed can lead to uneven color distribution. It’s necessary to adjust these parameters according to the specific product requirements to maintain uniformity. By optimizing these settings, manufacturers can ensure the plastic fills the mold evenly, preventing local color discrepancies.
Parameter | Impact on Color Consistency |
---|---|
Temperature | Affects fluidity and color dispersion |
Pressure | Influences plastic density and color depth |
Speed | Impacts flow pattern and surface finish |
Mold Design and Maintenance
Mold design plays a pivotal role in achieving color uniformity. Designing appropriate gate positions and sizes ensures even filling of the mold. Additionally, regular mold maintenance2 prevents residue buildup, which can alter the final product’s appearance.
Maintenance Best Practices
Routine cleaning and inspection of molds are essential. Replacing worn parts and maintaining precise mold dimensions help avoid unexpected color changes during production.
Effective Color Management Practices
A comprehensive color management system is vital for sustaining consistency across batches. Establishing clear color standards and tolerances, coupled with regular monitoring, allows for timely adjustments in process parameters or raw material formulations when deviations occur.
Recording and Traceability
Recording every aspect of the production process, from raw material batches to processing conditions, allows for effective tracing of any issues that arise. This systematic approach enables manufacturers to pinpoint causes of inconsistencies quickly and implement corrective actions effectively.
Raw material variability is the main cause of color inconsistency.True
Variability in raw materials affects color consistency significantly.
Temperature fluctuations have no impact on color consistency.False
Temperature changes affect fluidity and color dispersion during molding.
How Does Mold Design Influence Color Uniformity?
Mold design plays a pivotal role in achieving uniform color in injection molded products, ensuring aesthetic appeal and product quality.
Mold design influences color uniformity by ensuring even material distribution, controlling air entrapment, and reducing friction between the mold and material. Proper gate placement, exhaust systems, and surface treatments are crucial design elements that maintain consistent color across the product.
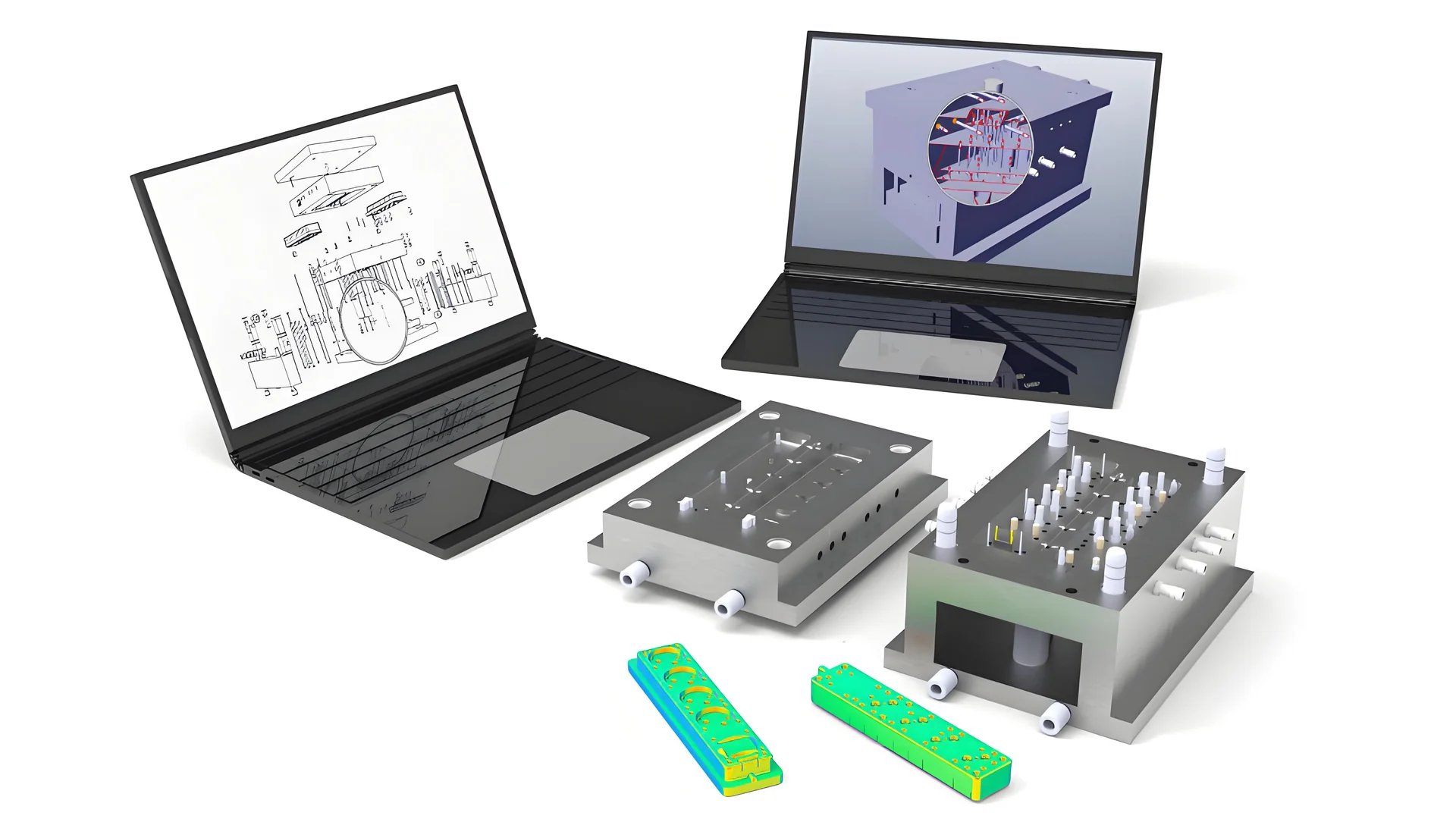
The Importance of Gate Design
Gate design is fundamental to achieving color uniformity. Proper placement and sizing of gates ensure that molten plastic fills the mold evenly, preventing local color variations. A poorly designed gate can lead to uneven flow, resulting in regions of varying color intensity.
Example: Practical Gate Placement
Consider a mold for a flat plastic panel. If the gate is placed too far from one edge, the fill pattern may cause a visible color gradient. By positioning the gate centrally or using multiple gates, the flow can be more uniform, minimizing color discrepancies.
Exhaust Systems and Air Entrapment
Air entrapment during injection molding can cause color defects such as streaks or spots. Implementing an effective exhaust system allows trapped air to escape, thereby maintaining the desired color consistency.
- Types of Exhaust Systems: Venting grooves and vacuum systems are commonly used to facilitate air removal.
- Impact on Color: Without proper exhausts, trapped air can result in oxidation, altering the intended color of the product.
Mold Material and Surface Treatment
The choice of mold material and its surface treatment can significantly affect color uniformity. Using high-quality materials reduces wear and tear, which could lead to inconsistent texture and color.
- Material Selection: Stainless steel or aluminum with high thermal conductivity helps maintain consistent temperature and smooth surface finishes.
- Surface Treatments: Polishing or applying a coating to the mold surface reduces friction and wear, ensuring a stable interface between the plastic and the mold.
Regular Maintenance Practices
Consistent maintenance of molds prevents residues and contaminants from affecting color consistency. Regular cleaning schedules and inspections help keep molds in optimal condition.
- Cleaning Protocols: Use non-abrasive cleaners to avoid scratching the mold surface.
- Wear Inspection: Regularly check for signs of wear and replace worn parts promptly to prevent defects.
By integrating these mold design practices3, manufacturers can significantly enhance the color uniformity of injection molded products.
Gate design affects color uniformity in molding.True
Proper gate placement ensures even flow, reducing color variations.
Air entrapment has no impact on color consistency.False
Trapped air causes streaks or spots, affecting color uniformity.
What Role Does Temperature Control Play in Color Consistency?
Temperature control is a pivotal factor in ensuring color consistency in injection molding, impacting fluidity and dispersion.
Temperature control is crucial in maintaining color consistency during injection molding. It affects the fluidity and dispersion of materials, ensuring uniform color distribution. Precise temperature regulation prevents color variations, making it essential for consistent product quality.
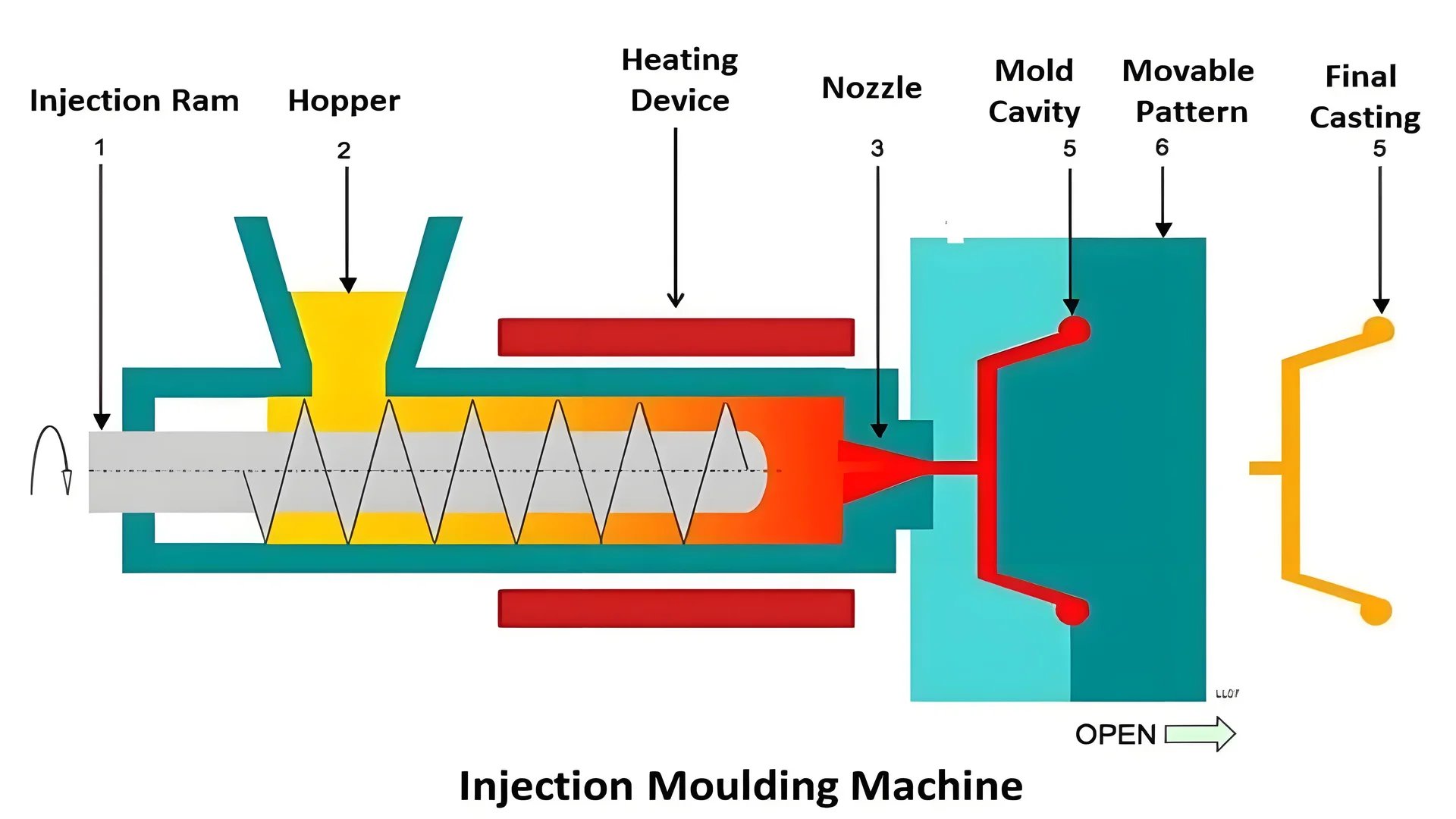
The Importance of Temperature Stability
Temperature fluctuations during the injection molding process4 can lead to noticeable color variations. Stable temperature management ensures that the plastic material flows evenly within the mold, reducing the risk of streaks or spots.
-
Barrel Temperature: Maintaining a consistent barrel temperature is vital as it directly impacts the melting and flow characteristics of the plastic. Deviations can result in uneven color distribution.
-
Nozzle Temperature: Anomalies in nozzle temperature can cause differential cooling rates, affecting the final product’s hue and saturation.
-
Mold Temperature: Proper mold temperature ensures uniform cooling and solidification of the plastic, critical for achieving consistent coloration.
Tools for Effective Temperature Control
Employing precise instruments such as thermocouples and thermostats can aid in maintaining optimal temperature conditions:
- Thermocouples: These devices measure the temperature at various points of the molding machine, providing real-time data to prevent deviations.
- Thermostats: Used to regulate the heating elements, thermostats maintain consistent temperatures throughout the process.
Case Study: Effects of Temperature Variation
A manufacturer observed inconsistent colors in their products despite using high-quality pigments. Investigation revealed that their injection molding machine experienced frequent temperature fluctuations due to worn-out thermostats. By replacing these components, they achieved a 95% reduction in color variance, underscoring the significance of precise temperature control.
Best Practices for Temperature Control
Implementing stringent temperature control practices can significantly enhance color consistency:
- Regular Calibration: Routinely calibrate thermocouples and thermostats to ensure accurate readings.
- Monitor Equipment Wear: Regular maintenance of heating elements and cooling channels prevents unexpected temperature changes.
- Data Logging: Keeping detailed records of temperature settings and variations aids in troubleshooting and process optimization.
Conclusion
While temperature control is not the only factor affecting color consistency, it plays a substantial role in achieving a uniform appearance across injection molded products. By investing in reliable equipment and implementing robust monitoring practices, manufacturers can ensure high-quality outputs with consistent coloration.
Temperature control prevents color variations in injection molding.True
Precise temperature regulation ensures uniform color distribution.
Nozzle temperature has no impact on product hue.False
Nozzle temperature affects cooling rates, influencing hue and saturation.
How Can Effective Supplier Relationships Improve Color Stability?
Establishing strong supplier relationships is key to enhancing color stability in injection molded products, ensuring consistent quality and reducing variations.
Effective supplier relationships enhance color stability by ensuring consistent raw material quality, facilitating better communication for troubleshooting, and fostering long-term collaboration for continuous improvement.
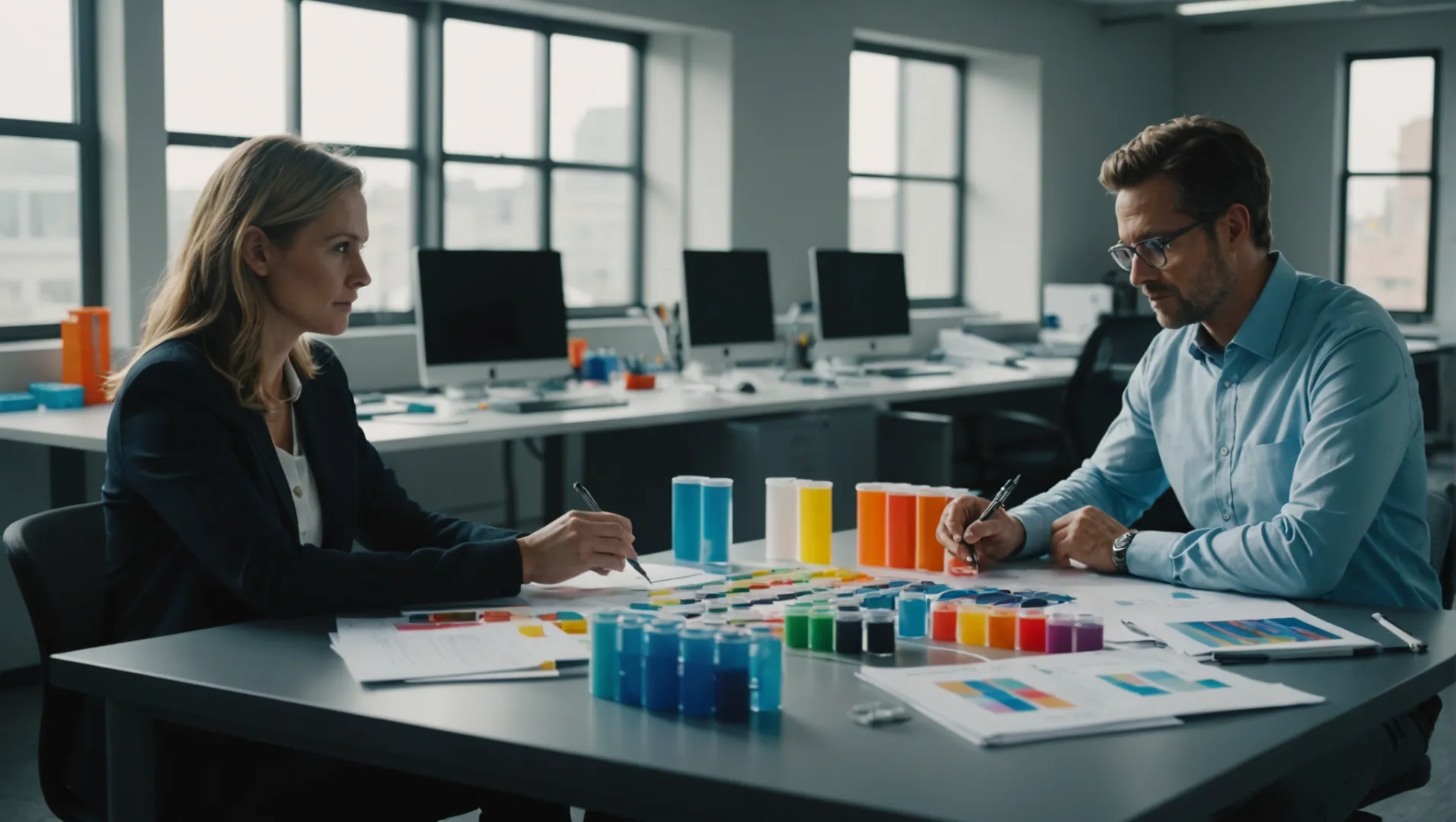
Building Trust with Reliable Suppliers
Choosing a reliable supplier forms the backbone of color stability in injection molding. A trustworthy supplier provides raw materials with minimal color variation between batches, crucial for maintaining consistent product appearance. Establishing a long-term partnership5 with such suppliers not only ensures stability but also opens channels for effective communication when addressing color issues.
Implementing Rigorous Quality Control Measures
Suppliers with robust quality control systems are invaluable. They offer masterbatches and pigments that align with stringent color standards, minimizing deviations. Regular audits and inspections of incoming raw materials are pivotal. Using tools like colorimeters ensures that only materials meeting specific standards are utilized in production.
Quality Control Measures | Benefits |
---|---|
Colorimeter Use | Precise color measurement |
Regular Audits | Ensures adherence to standards |
Facilitating Open Communication
Effective supplier relationships are built on open lines of communication. This openness allows for immediate feedback and rapid resolution of any issues related to color stability. Suppliers can provide insights into potential improvements or changes in raw material formulations that might affect color consistency.
Collaborating for Continuous Improvement
Long-term supplier relationships enable collaborative efforts towards innovation and process improvement. By working closely, both parties can develop new solutions and methodologies to further enhance color stability. Suppliers may also offer technical support or training on new technologies that can improve production processes.
Leveraging Supplier Expertise
Many suppliers bring extensive expertise in material science and technology. By tapping into this knowledge, manufacturers can optimize their processes, ensuring that the interaction between raw materials and production parameters results in stable, uniform colors. This collaboration can lead to innovations that enhance overall product quality.
In conclusion, while selecting the right suppliers is crucial, nurturing these relationships over time leads to significant benefits in maintaining color stability in injection molded products.
Strong supplier ties reduce color variation in products.True
Reliable suppliers provide consistent raw materials, minimizing color differences.
Supplier expertise is irrelevant to color stability improvement.False
Suppliers offer insights into material science, aiding color consistency.
Conclusion
Mastering color consistency is a journey of meticulous attention to detail across various stages of production. Start today, and watch your product quality soar!
-
Find tips on selecting suppliers ensuring consistent material quality.: Learn how to select the right material for your injection molding design with this technical overview of thermoplastic resins. ↩
-
Discover essential maintenance practices to ensure mold longevity.: Shop floor control software allows you to easily schedule regular mold maintenance rounds and verify that they have been completed. ↩
-
Discover detailed insights into optimizing mold design for better product outcomes.: The quality and make of the mold allows injection molders to ensure high tolerance, identify defects, maintain precision, choose the right raw materials, as … ↩
-
Explore detailed insights into temperature’s impact on injection molding.: Higher mold temperatures can promote better color development and uniformity, while lower temperatures may result in color fading or unevenness. ↩
-
Discover how sustained supplier partnerships enhance quality and efficiency.: Relationships with trusted suppliers can enable organisations to outsource non critical activities, allowing buyers to harness specific industry … ↩