Dealing with cracks in injection molded products feels like navigating a minefield. I have experienced this situation and it is a challenge. This issue really affects quality and costs. Let us explore ways to solve this problem together.
Prevent cracks in injection molded products by optimizing design, controlling molding parameters, maintaining mold quality, ensuring proper wall thickness, avoiding sharp corners, and properly managing cooling for enhanced strength and efficiency.
In my experience, understanding the details of product design really matters. The complex injection molding process is significant. Mold maintenance is very important too. These aspects probably change everything. I recall a project where we optimized wall thickness. This move saved us from potential disasters. Suddenly, our products did very well. They thrived! Prioritizing these steps in your designs is crucial.
We now explore effective strategies to minimize cracks. I’ll share insights and practical tips from my experiences. These tips have improved production outcomes. Our designs should not just meet expectations. They must really exceed them.
Optimizing product design can prevent cracks in molded products.True
A well-thought-out design reduces stress concentrations, minimizing the risk of cracks during the injection molding process.
Sharp corners in designs lead to fewer cracks in injection molding.False
Contrary to this claim, sharp corners increase stress and crack likelihood; rounded corners are recommended for better results.
How Does Product Design Influence Crack Prevention?
Have you ever thought about how the design of a product influences its strength? Let’s explore the interesting field of product design. Thoughtful choices really help to stop cracks in plastic items.
Product design aids crack prevention by optimizing wall thickness, reducing sharp corners, and employing effective demolding techniques, enhancing durability and reliability.
Product Design Optimization
Reasonable Wall Thickness Design
When designing plastic items, I quickly saw that wall thickness is much more important than I thought. A consistent wall thickness is essential to reduce stress points that cause cracks. Once, I found that replacing sharp corner connections with smooth curves made products much more durable. This simple change not only improved appearance but also significantly lowered stress areas. Typically, I keep the ratio of adjacent wall thicknesses under 1.5:1. Small detail, big impact.
Avoiding Sharp Inner Corners
I avoid sharp corners. Rounded inner corners distribute stress evenly. On a project designing plastic brackets, I used a proper fillet radius. This not only looked better but also greatly reduced cracking. Usually, I maintain a radius of at least 0.5 times the wall thickness. Simple change, impressive results.
Consideration of Demoulding Structure
Demoulding is tricky. I faced many obstacles here. A reasonable demoulding slope, often between 0.5° and 3°, is second nature now. This minimizes friction and prevents cracks during mold removal. Taller items need a bigger slope. It’s about making it easy for both the product and me!
Injection Molding Process Optimization
Temperature Control
Controlling temperature in injection molding is like finding the perfect baking temperature. If too hot or too cold, bad things happen quickly. I carefully set temperatures in different barrel areas following material characteristics. For polypropylene, I follow these ranges:
Correct temperatures allow complete plasticization and avoid issues with overheating or underheating.
Mold Temperature
Raising mold temperatures has been a game changer for me. It helps plastic flow smoothly and cool evenly. For crystalline plastics like nylon, I use a mold temperature of 80-100°C. This keeps everything consistent and lowers internal stress.
Pressure and Speed Adjustment
Managing injection pressure and speed is very important. For very thin products, lower injection speeds help fill smoothly without causing high-speed impacts that crack. It’s about patience and accuracy.
Cooling Control
Cooling needs balance. Too fast creates deformities, too slow lowers production efficiency. Thoughtfully designed cooling channels allow uniform cooling across the product’s surface. I learned this lesson the hard way.
Mold Design and Maintenance
Good Exhaust Design
In my view, a good mold design is key for quality. Enough exhaust features let out trapped gases during injection, lowering internal pressure and preventing cracking. I find exhaust groove depths between 0.02-0.04mm effective, with a width of 3-5mm.
Surface Quality and Precision
A smooth mold surface helps plastic flow better and lowers stress. Regular maintenance is routine for me now. Molds must remain in top condition to perform flawlessly.
Reasonable Ejection System
Lastly, the ejection system should be well planned to prevent cracks during demolding. Even distribution of push rods matters for thin-walled products. It ensures ejection forces stay within safe limits.
Explore more on designing durable products: product design techniques and injection molding best practices.
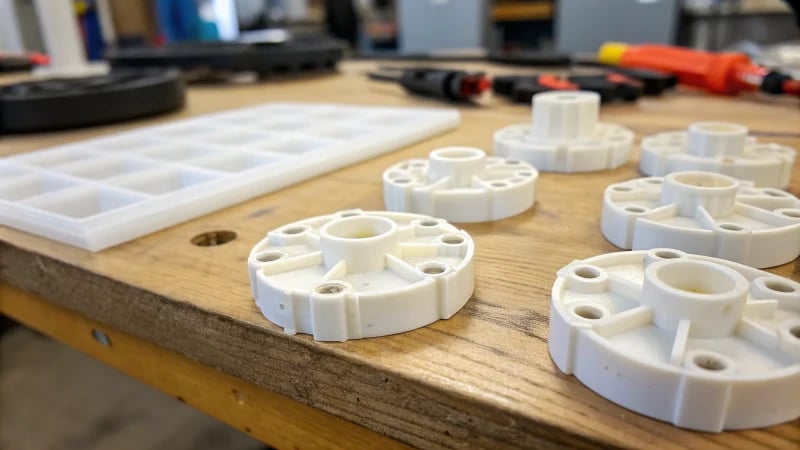
Product Design Insights
Product design combines aesthetics with durability, emphasizing longevity. Through late-night design refinements, the focus is on creating visually appealing, long-lasting products. Key insights reveal strategies in design to prevent cracks, ensuring strength and attractiveness.
Reasonable Wall Thickness Design
The wall thickness of a product plays a critical role in its overall durability. A uniform wall thickness minimizes the risk of stress concentration, which is a leading cause of cracks. To achieve this, designers should avoid abrupt transitions and instead opt for gradual changes.
For example, when designing a plastic container, connecting the bottom and side walls with an arc instead of a right-angle transition helps reduce stress concentrations. Ideally, the ratio of adjacent wall thicknesses should not exceed 1.5:1 to effectively mitigate crack risks.
Avoiding Sharp Inner Corners
In product design, inner corners should be rounded rather than sharp. Sharp corners can lead to stress points that are prone to cracking. The fillet radius should be appropriately sized; generally, it’s recommended to be at least 0.5 times the wall thickness.
For instance, in injection-molded plastic brackets, employing an appropriately sized fillet can help distribute stress more evenly and reduce the likelihood of cracks.
Consideration of Demoulding Structure
The design phase should also include considerations for demoulding. A reasonable demoulding slope (typically between 0.5° and 3°) is essential to minimize friction and cracking during the demoulding process.
For higher injection-molded products, a steeper slope may be necessary to ensure smooth removal and prevent damage from excessive forces.
Injection Molding Process Optimization
1. Temperature Control
Temperature management in injection molding is crucial for avoiding cracks. Each section of the barrel must be set according to the material characteristics.
Material Type | Front Temp (°C) | Middle Temp (°C) | Rear Temp (°C) |
---|---|---|---|
Polypropylene | 180-200 | 200-220 | 160-180 |
Properly setting these temperatures ensures complete plasticization and prevents issues related to overheating or underheating.
Mold Temperature
Increasing mold temperature aids in smoother plastic flow and even cooling. For crystalline plastics like nylon, maintaining a mold temperature around 80-100°C can help reduce internal stress.
Pressure and Speed Adjustment
Injection pressure and speed must be controlled carefully to avoid excessive force that can lead to cracking. For thin-walled products, using lower injection speeds allows for a smoother fill without causing high-speed impacts that may create cracks.
Cooling Control
Cooling must also be optimized. Too rapid cooling can lead to deformities, while too slow cooling can affect production efficiency. A well-designed cooling channel ensures uniform cooling across the product’s surface.
Mold Design and Maintenance
1. Good Exhaust Design
Mold design should incorporate sufficient exhaust features to release trapped gases during injection. This reduces internal pressure that could lead to cracking. The depth of exhaust grooves typically ranges from 0.02-0.04mm, with a width of 3-5mm.
Surface Quality and Precision
High-quality surfaces in molds facilitate smoother plastic flow, reducing stress concentrations due to flow obstructions. Regular maintenance of molds is vital for ensuring they meet quality standards.
Reasonable Ejection System
The ejection system must be carefully designed to prevent cracks during demolding. Employing evenly distributed push rods for thin-walled products can ensure that ejection forces do not exceed safe limits.
To explore more about optimizing product designs for durability, check out these resources: product design techniques1 and injection molding best practices2.
Uniform wall thickness reduces crack risk in products.True
A uniform wall thickness minimizes stress concentrations, significantly lowering the chances of cracks in product design.
Sharp inner corners enhance product durability.False
Sharp inner corners create stress points that increase the likelihood of cracking, hence should be avoided in product design.
How Does Temperature Control Impact Defect Reduction in Manufacturing?
Have you ever thought about why controlling temperature matters so much in manufacturing? I have! It seems that having the right temperature can really mean the difference between creating a perfect product or a faulty one. A minor change in temperature maybe leads to defects.
Effective temperature control in manufacturing minimizes defects, such as cracks and deformations, by optimizing processing conditions. Proper management of barrel and mold temperatures enhances product quality and ensures operational consistency.
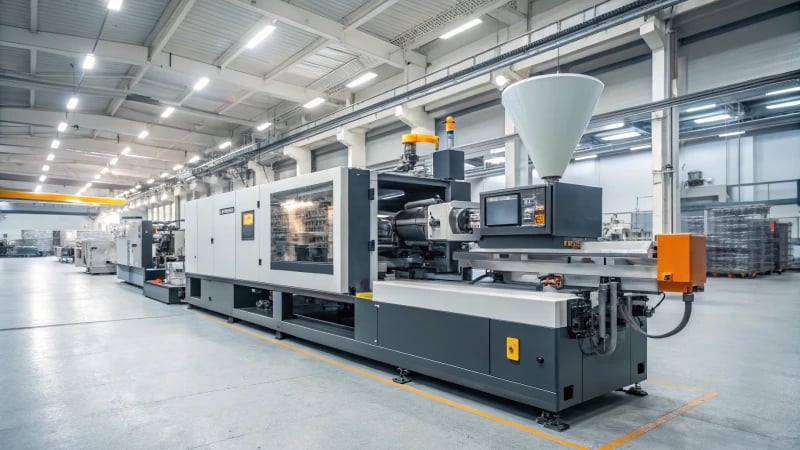
Understanding Temperature Control in Manufacturing
Temperature control is not just a simple tool; it is the heart of quality in manufacturing, especially in injection molding. Managing barrel and mold temperatures reduces defects like cracks and deformations. Product quality improves greatly, delivering better results to our customers.
For example, setting the right barrel temperature is essential. Different plastics have specific processing temperature ranges. For instance, polypropylene (PP) should have a barrel temperature of around:
Section | Temperature (°C) |
---|---|
Front | 180 – 200 |
Middle | 200 – 220 |
Rear | 160 – 180 |
Using these temperature settings ensures the plastic is fully plasticized, which is crucial to avoid decomposition or incomplete plasticization that can lead to defects. Learn more about barrel temperature settings3.
Mold Temperature: A Key to Quality
Mold temperature is another key factor. Proper mold temperature allows melted plastic to flow and cool correctly. I worked with nylon (PA) and kept the mold temperature between 80-100°C. This helped in achieving even crystallization, reducing internal stress and cracks.
This balance is critical; too high a temperature can lead to excessive flow and poor detail reproduction, while too low can lead to incomplete filling and defects. Explore the impact of mold temperature4.
The Influence of Cooling Control
Cooling is important in temperature management. Uneven and fast cooling can lead to internal stresses. Designing optimized cooling channels has transformed the process. Layered cooling channels promote even cooling, improving production efficiency.
A common practice is to optimize the cooling channel design in molds. For large injection products, consider adopting a layered cooling channel approach5.
The Role of Pressure and Speed Adjustments
Pressure and speed adjustments are crucial alongside temperature. Lower injection pressure protects mold walls from too much force, reducing cracks. Slow injection speeds benefit thin-walled products by easing material stress.
Furthermore, managing holding pressure and timing is important to avoid internal stresses. Achieving the right balance through trials creates stable, crack-free products that resonate with our clients. Discover more on pressure adjustments6.
Together, these elements create a process that exceeds quality expectations. Focusing on temperature control, smart design and process optimization allows us to achieve outstanding results.
Optimal barrel temperature prevents plastic decomposition.True
Maintaining the correct barrel temperature during injection molding avoids decomposition of plastics, ensuring higher quality products with fewer defects.
Cooling speed affects the risk of internal stresses.True
Controlling cooling speed is crucial to prevent uneven solidification, which can lead to internal stresses and product defects after demolding.
Why is Mold Maintenance Critical for Quality Assurance?
When I began my job in manufacturing, I didn’t understand the crucial role of mold maintenance. Later, I discovered its vital impact on our product quality. Mold maintenance is essential. Why does it matter so much?
Mold maintenance is crucial for quality assurance as it prevents defects, ensures product consistency, and reduces production costs by maintaining uniformity and minimizing flaws.
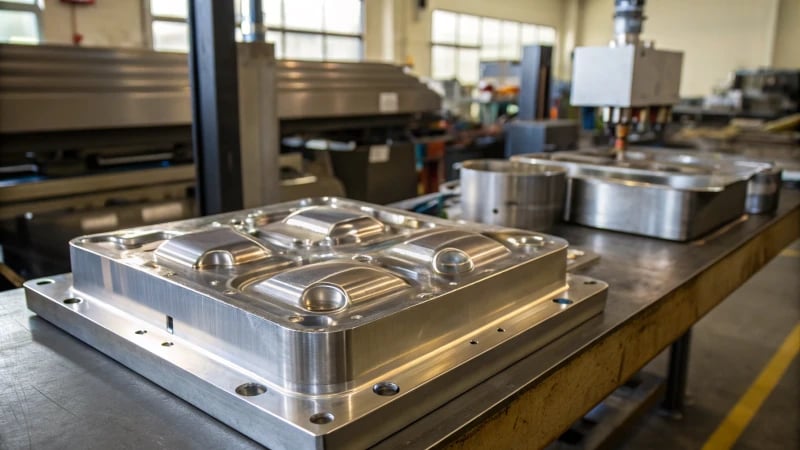
Understanding Mold Maintenance in Quality Assurance
Mold maintenance is important for quality assurance. It stops defects, improves product consistency and saves costs in production. I have witnessed how keeping a mold in good condition elevates product quality from average to very good.
Regular maintenance can significantly impact product consistency and defect rates. When molds are maintained properly, they produce more uniform parts, which minimizes variations that can lead to defects.
Preventing Defects Through Regular Maintenance
Regular inspections are crucial for preventing defects. Problems like:
- Wear on mold surfaces
- Cooling channel blockages
- Ejection system misalignment
These issues can cause a mess. I once saw a production batch ruined because a cooling channel was blocked, leading to warped products. It was a really costly mistake! Therefore, having a detailed maintenance schedule7 is essential for any manufacturing operation.
Improving Product Consistency
I care deeply about product consistency. Consistent production quality is paramount in any manufacturing process. I remember projects where we couldn’t meet specifications due to poor mold maintenance. Regular attention to molds results in parts that meet specifications more reliably. This keeps everything on track.
Maintenance Task | Frequency | Importance |
---|---|---|
Surface inspections | Weekly | Identifies wear early |
Cooling channel checks | Before each run | Prevents defects |
Ejection system review | Monthly | Ensures smooth demolding |
Cost Efficiency in the Long Run
Time and resources in mold maintenance always save money for me. Investing time and resources into mold maintenance can save costs associated with production delays due to defects. Repairs on faulty molds are often far more expensive than preventive maintenance. Additionally, costs from defective products can exceed maintenance expenses.
Maintaining molds well helps avoid:
- Production halts
- High scrap rates
- Customer dissatisfaction due to quality issues
Conclusion: Strategic Importance of Mold Maintenance
In my experience, mold maintenance has strategic importance. It improves production efficiency and product quality assurance. For those who seek to understand best practices, looking into industry guidelines8 can offer important insights, helping you avoid mistakes I have made.
Mold maintenance prevents defects in manufactured products.True
Regular mold maintenance identifies issues that can lead to defects, ensuring product quality and consistency.
Neglecting mold maintenance increases production costs.True
Failing to maintain molds often results in defects and production delays, raising overall manufacturing expenses.
What Common Mistakes Should I Avoid in Injection Molding?
Navigating injection molding often feels daunting. Experience shows that common pitfalls waste time and money. Recognizing these can save both. Let’s explore key mistakes and avoid them together!
Avoid common injection molding mistakes by ensuring uniform wall thickness, controlling processing temperatures, maintaining molds properly, and regularly checking ejection systems.
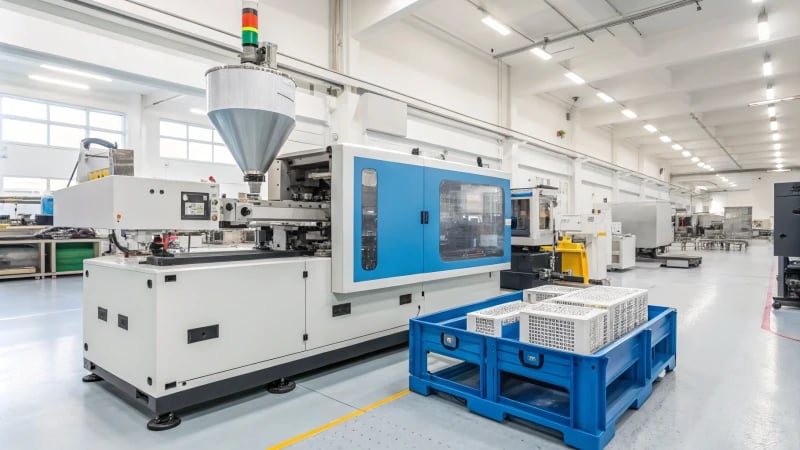
Product Design Optimization
Understanding common mistakes in injection molding is crucial for designers and manufacturers. Focusing on key areas helps avoid costly errors.
One of the first areas to focus on is product design optimization. It’s essential to ensure that the wall thickness of your injection molded part is as uniform as possible.
Reasonable Wall Thickness Design
A sudden change in wall thickness can lead to defects. When designing, try to keep the ratio of adjacent wall thicknesses below 1.5:1. For example, consider a plastic container where the bottom and side walls meet: transitioning with an arc rather than a right angle reduces stress concentration.
Wall Thickness Ratio | Recommended Action |
---|---|
1:1 – 1.5:1 | Maintain uniformity |
> 1.5:1 | Optimize design to reduce risk of cracks |
Avoid Sharp Inner Corners
Designing sharp inner corners can also lead to increased stress points. Instead, use rounded corners, ensuring the radius is at least 0.5 times the wall thickness. For instance, in an injection-molded bracket, a fillet can distribute stress more evenly, minimizing the risk of cracking.
Consider the Demoulding Structure
The convenience of demoulding is crucial. Implement a demoulding slope between 0.5° and 3° based on the product’s shape and material. For higher products, increasing this slope can prevent cracks from excessive demoulding force.
Injection Molding Process Optimization
Next, let’s examine injection molding process optimization, focusing on temperature control and pressure adjustments.
Temperature Control
Proper temperature settings are vital for the plastic’s characteristics:
- Barrel Temperature: Different plastics require different settings. For instance, polypropylene (PP) should have a barrel temperature between 180-200℃ in the front section.
- Mold Temperature: Increasing mold temperature allows smoother flow of plastic and reduces internal stress. For nylon (PA), maintain mold temperature between 80-100℃.
Pressure and Speed Adjustment
Controlling injection pressure and speed is another critical factor:
- Injection Pressure: Should be determined based on the product’s shape and size; lower pressures can help avoid cracks.
- Holding Pressure and Time: Excessive holding pressure may create internal stress leading to cracks. Finding the right balance through testing can ensure stable dimensions post-demolding.
Mold Design and Maintenance
Finally, mold design and maintenance play a pivotal role in avoiding common mistakes.
Good Exhaust Design
Ensure that molds have adequate exhaust grooves or holes to allow gases to escape smoothly during injection. Poor exhaust can trap gases, increasing internal pressure and leading to cracks.
Exhaust Groove Specifications | Recommended Depth | Recommended Width |
---|---|---|
General Use | 0.02-0.04mm | 3-5mm |
Surface Quality and Precision
Mold surfaces should be smooth and well-finished to prevent melt flow obstruction. Regular inspections and repairs will ensure longevity and quality in production.
Reasonable Ejection System
Design an effective ejection system tailored to the product’s shape to avoid improper ejection that could cause cracks. For thin-walled products, consider using multi-point ejection methods with controlled speeds.
By addressing these issues in injection molding—from design to process and mold maintenance—my product quality very much improved while reducing defects.
Uniform wall thickness prevents defects in injection molding.True
Maintaining uniform wall thickness below a 1.5:1 ratio reduces stress and avoids cracking during the injection molding process.
Sharp inner corners improve injection mold strength.False
Using sharp inner corners increases stress concentration, leading to potential cracks; rounded corners are recommended for better distribution of stress.
Conclusion
Learn how to prevent cracks in injection molded products through optimized design, temperature control, and proper mold maintenance for improved durability and production efficiency.
-
This link offers in-depth insights into advanced product design techniques that minimize cracking risks. ↩
-
Learn about best practices in injection molding that enhance product durability against cracking. ↩
-
Discover how temperature management can enhance product quality and minimize defects in your manufacturing process. ↩
-
Learn about best practices in temperature settings to optimize your production process. ↩
-
Understand the significance of cooling control in reducing defects during manufacturing. ↩
-
Explore effective strategies for pressure and speed adjustments to minimize defects. ↩
-
Clicking this link will provide you with comprehensive guidelines on effective mold maintenance practices that can enhance product quality. ↩
-
This resource will offer detailed insights into how mold conditions affect product quality, making it essential for understanding your processes. ↩