Have you ever thought about how a little change in gate location changes your injection-molded items?
Gate location and number in injection molding crucially affect product aesthetics, strength, and quality by reducing visible marks, weld lines, and internal stresses, facilitating easier filling and ejection for higher-quality outcomes.
I remember the first time I chose where to put gates for a project. It felt like solving a hard puzzle. Every decision either improved the product’s appearance or left visible marks. Understanding these details really brought better designs. It also increased my confidence in creating quality products. Now, let’s explore how smart choices about gate positions and numbers achieve great results in injection molding.
Gate location affects product appearance in injection molding.True
Proper gate placement minimizes visible marks and weld lines.
More gates always improve injection molded product quality.False
Excessive gates can increase complexity and internal stresses.
How Do Gate Marks Affect Product Appearance?
Ever wondered why some products have those annoying little marks that look like flaws? These marks are called gate marks. They often impact a product’s appearance. Gate marks might even ruin the look of the product.
Gate marks are marks left at the spot where material enters molded items. Their location and visibility very much impact how products look. This is especially true in consumer electronics. The appearance of these products is very important.
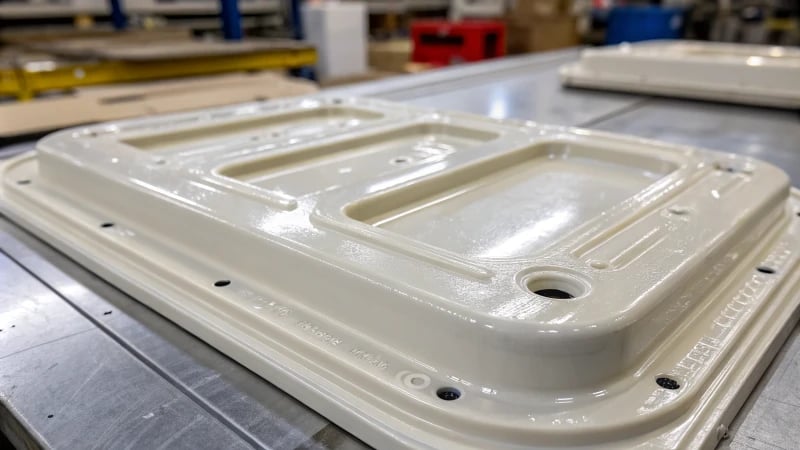
Influence of Gate Position on Product Looks
I remember the first time I realized the importance of gate mark position. I was working on a sleek new gadget design. We had a glaring gate mark right in the middle of the front panel. It was like a pimple on a perfect face. It struck me then – the gate mark location could either improve or ruin the visual appeal.
If placed prominently, such as at the center front, gate marks become glaring. A hidden gate placement, like on the side or bottom, minimizes this impact1.
Gate Position | Visibility Impact |
---|---|
Front Center | High |
Side | Low |
Bottom | Minimal |
Using multiple gates brings problems – more gates create more marks. I’ve learned this from many small devices needing to stay sleek.
Weld Marks and Their Effect
Weld marks appear where melted plastic joins inside the mold. Improper gate positioning or excess gates can result in these unsightly marks. Wild gate placements, especially near complex shapes like ribs or holes, create unsightly marks.
- Complex Structures: Avoid placing gates near tricky parts to stay away from weld marks2.
- Number of Gates: Keep it low for a smooth melt flow.
Additional Considerations
It’s not just about appearance. Optimizing for looks also affects other aspects:
- Residual Stress: Gate positions alter stress distribution inside, affecting durability.
- Demolding: Choose carefully so the gate doesn’t hinder demolding3, affecting integrity.
Understanding these details helps designers find a balance between looks and function in molded products.
Gate marks on the front center are highly visible.True
Gate marks at the front center of a product are highly noticeable.
Multiple gates simplify product design aesthetics.False
Multiple gates complicate design, affecting aesthetics negatively.
How Does Gate Placement Influence Weld Mark Formation?
Have you ever thought about how tiny details, like where you put a gate, really affect product design? Let me share some ideas.
Gate placement in injection molding influences where weld marks appear. It directs the flow routes of the plastic melt inside the mold. Smart positioning of the gate reduces weld marks. It really improves how the product looks. It also strengthens the product.
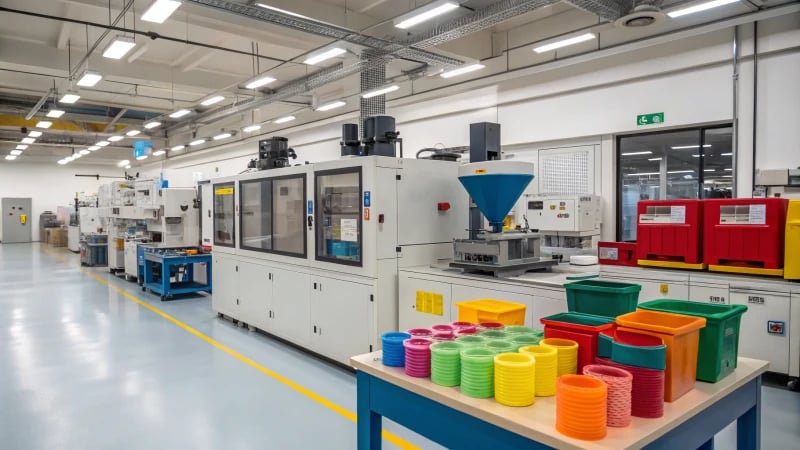
Understanding Weld Marks in Injection Molding
Picture this: you examine a glossy new phone case you designed, and there they are—those annoying weld marks. These marks form when different streams of molten plastic come together inside the mold. They often appear more clearly on transparent or glossy surfaces. I found this out early in my designing journey and learned to make those seams nearly invisible.
Factors | Impact on Weld Marks |
---|---|
Number of Gates | More gates can increase flow front intersections. |
Gate Location | Affects flow path; improper location leads to marks. |
Influence of Gate Position
Imagine this: I once placed a gate in a high-visibility area. The result was noticeable marks that spoiled the look, showing me how important gate placement is. It is best to position gates away from complex features like holes or ribs, allowing smoother melt flow and reducing visible weld lines.
Case Study: Transparent Components
I worked on transparent plastic decorations once. The first gate placement left visible marks and reduced clarity. We moved the gate to a less obvious area, like the bottom or side, preserving transparency and improving the visual appeal4.
Mechanical Properties and Weld Marks
Weld marks do more than look bad; they can weaken your product. Stress on these marks creates weak spots. I recall a product with a gate at the edge where stress concentrated at the center where melt fronts met. Adjusting gate placement distributed stress more evenly, reducing potential weak points.
Consider a case where the gate is located at the edge of a product:
- This setup can cause stress concentration at the center where melt fronts converge, potentially weakening under stress.
Optimizing Gate Placement for Mold Filling
Gate placement is crucial for filling the mold without leaving weld marks. I faced a challenging design once; careful gate positioning prevented short shots in thin-walled areas, resulting in a flawless finish.
-
Example Layout: A table comparing different gate placements and their effects on fill quality:
Gate Placement Filling Effect Weld Mark Formation Center Uneven distribution, high risk High Edge Better distribution, lower risk Medium Multiple (Balanced) Optimized distribution, minimal Low
Understanding the link between gate placement, flow paths, and product design reduces weld marks significantly while maintaining both structural strength and visual quality—an approach very valuable for creating complex or visually demanding applications5.
More gates increase weld mark risk.True
More gates lead to more flow front intersections, increasing weld mark formation.
Center gate placement reduces weld marks.False
Center placement causes uneven distribution, increasing weld mark risk.
How Do Gate Locations Influence Mechanical Properties?
Find out how a minor adjustment in gate position transforms both the durability and look of molded items. Small changes have a big impact.
Gate locations directly affect mechanical properties. They shape stress distribution, material flow and molecular orientation. Correct placement gives uniform strength. It reduces defects. This really helps product quality. Quality is very important.
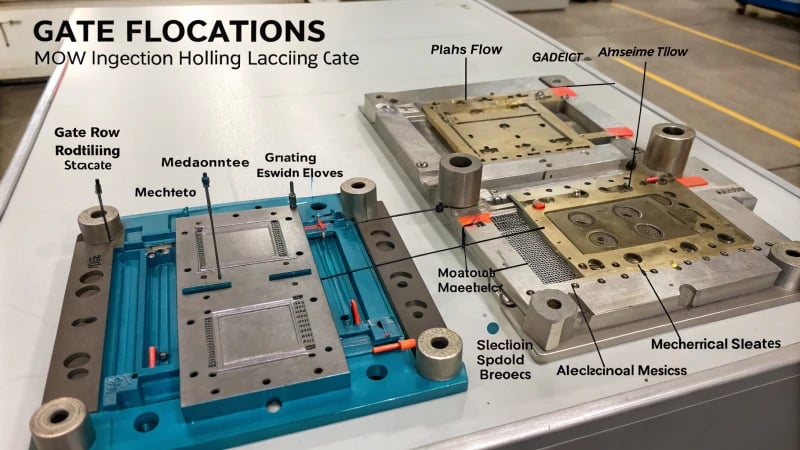
Gate Locations and Internal Residual Stress
When I started using injection molds, I realized gate position is very important for internal residual stress. Imagine placing the gate at the mold’s edge. The molten material fills inward, often causing stress at the center. I overlooked this once, leading to cracks under pressure. It was a tough lesson. By placing gates carefully, we distribute stress evenly. This avoids possible structural problems6.
Molecular Orientation and Mechanical Strength
The gate’s location affects how molten plastic flows and aligns molecules. Picture a long piece with a gate at one end. Molecules align along the length. This increases tensile strength in that direction but might weaken the other direction. I once adjusted gate placement in a project to balance forces and achieve desired strength properties7.
Influence on Crystallinity
For crystalline plastics, gate location is essential to control crystallization during cooling. I worked on a decorative plastic piece once where poor gate placement caused uneven cooling, affecting its density and toughness. Proper gate locations provided uniform crystallinity, resulting in consistent mechanical properties8.
Tables for Gate Effect Analysis
Aspect | Effect of Gate Location |
---|---|
Stress Distribution | Can create or reduce stress concentration areas |
Molecular Orientation | Affects alignment, altering tensile strength |
Crystallinity | Influences cooling rates, affecting material hardness |
Careful gate placement is key in injection molding. Understanding these effects helped improve design choices and product quality got better with this knowledge.
Gate location affects residual stress distribution.True
Gate placement influences how stress is distributed, impacting structural integrity.
Gate position does not affect molecular orientation.False
Gate location dictates flow, affecting molecular alignment and tensile strength.
How Can Gate Number Impact Product Molding Performance?
Do you ever think about how the number of gates in a mold changes your product’s final appearance and durability?
Gates in a mold affect how a product looks and how strong it is. More gates help melt fill the mold better. This reduces chances of short shots. However, adding more gates really complicates the design. These extra gates maybe cause visual flaws. These flaws can hurt both looks and strength.
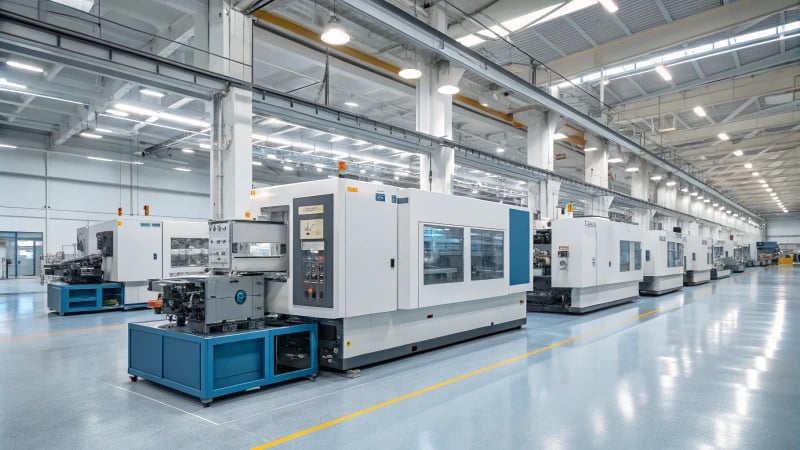
Influence on Product Appearance
I remember my first major project with a clear plastic decoration. I was very excited to see how it would turn out. When it came out of the mold, there was a big mark right in the center. The clear, shiny finish was ruined. This taught me why gate positioning is important for how products look. Placing gates in less visible areas, like the side or bottom, helps reduce these marks and keeps the product’s beauty intact.
Additionally, multiple gates can be tricky too; they might leave several ugly marks where the melt flows converge. Balancing design complexity with appearance is crucial to mitigate these visual imperfections.
Influence on Mechanical Properties
Once, I designed a casing for an electronic device. We put the gates at the edges for simplicity, but it caused stress in the center, weakening the product. This showed me how gate placement affects stress distribution and strength.
For certain plastics, gate position also changes molecular orientation and crystallinity, affecting tensile strength and toughness. Proper gate placement allows even cooling and crystallization, improving mechanical qualities.
Influence on Molding Performance
Aspect | Impact of Gate Number |
---|---|
Filling Effect | Using more gates can enhance melt flow into intricate areas, reducing short shots. However, too many gates can cause uneven flow and increase mold complexity. |
Demolding Process | Poorly positioned gates may hinder demolding, especially if undercuts are present. The number of gates affects structural integrity during demolding without damage risks. |
Working on large or complex products taught me about using more gates to fill cavities efficiently. But it’s a real balancing act as too many gates can increase mold costs and complicate design.
Using hidden gates9 has been very helpful as they allow easier demolding without damage while keeping the product whole.
Practical Considerations for Designers
When I design, I think hard about making something both beautiful and functional while keeping manufacturing costs low. Leveraging advanced CAD tools10 has been very helpful; these tools simulate different designs to find the best solution.
The aim is always to create a product that looks good and works well without high costs.
Gate position affects product appearance.True
Gate placement influences visual marks and blemishes on molded products.
Multiple gates reduce weld marks.False
Multiple gates increase the likelihood of weld marks where flows meet.
Conclusion
Gate location and number significantly impact the appearance, strength, and quality of injection-molded products by influencing weld marks, stress distribution, and overall design aesthetics.
-
Learn how strategic gate placement can minimize visible marks and improve product aesthetics. ↩
-
Explore techniques for minimizing weld marks through optimal gate placement. ↩
-
Discover how gate position affects ease of demolding and product integrity. ↩
-
Learn methods to enhance transparency and reduce defects in molded products. ↩
-
Discover real-world applications where strategic gate placement improves quality. ↩
-
Learn how different gate placements influence internal stress distribution and potential defect risks. ↩
-
Understand how gate positioning impacts molecular alignment and overall material strength. ↩
-
Explore how gate positioning affects crystallization, impacting density and toughness. ↩
-
This link provides techniques to minimize visible gate marks, enhancing product aesthetics. ↩
-
Discover CAD tools that help simulate injection molding processes, optimizing gate design and placement. ↩