As I delve into the world of sustainable packaging, I’ve discovered how vital injection molding machines are in shaping our eco-friendly future.
Injection molding machines can produce PET or PLA cups by heating and melting pellets of these materials, injecting them into molds, and cooling them to form cups. Each material’s unique properties require specific adjustments in the molding process to ensure quality.
But there’s so much more to it than just melting and molding! Let’s explore the fascinating characteristics of PET and PLA that influence their production.
PET cups require higher molding temperatures than PLA.True
PET has a higher melting point than PLA, requiring more heat for molding.
What Are the Material Properties of PET and PLA?
Exploring PET and PLA can reveal why they’re pivotal in eco-friendly packaging solutions.
PET and PLA, both thermoplastics, exhibit distinct properties that make them suitable for various applications. PET is known for its strength and transparency, while PLA is valued for its biodegradability and biocompatibility. Understanding these properties helps tailor the injection molding process to optimize the production of cups and containers.
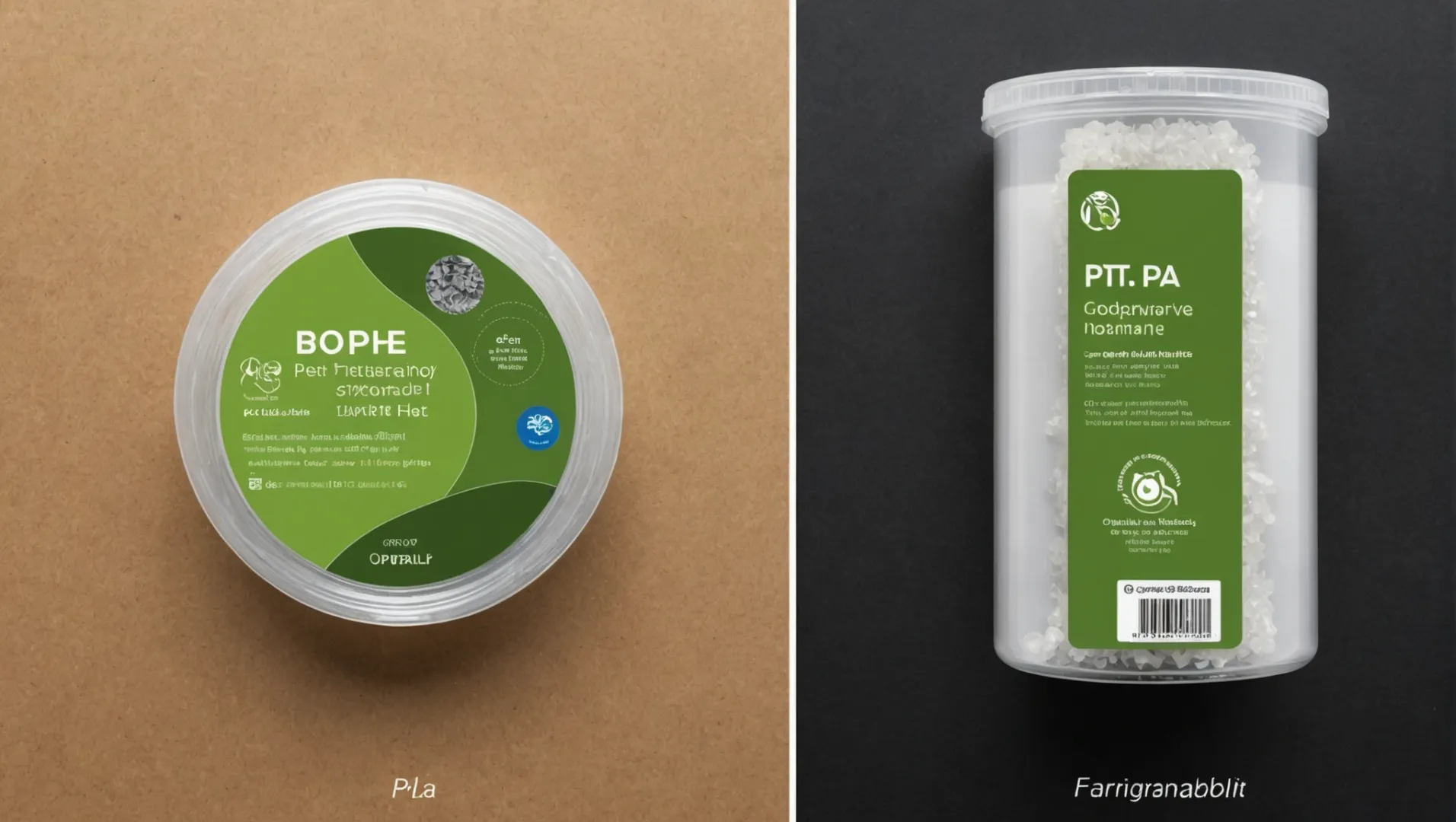
Understanding the Basics of PET and PLA
Polyethylene Terephthalate (PET) is a widely used thermoplastic polyester. It boasts excellent transparency, robust strength, and notable heat resistance. These properties make it ideal for creating products like beverage bottles and food packaging. Its ability to withstand heat without warping also enhances its utility in various applications.
Polylactic Acid (PLA), on the other hand, is a biodegradable plastic derived from renewable resources such as corn starch. Its key attributes include good biocompatibility and degradability. However, it has a lower melting point compared to PET, which influences its processing conditions.
Comparing Physical Properties
Property | PET | PLA |
---|---|---|
Transparency | High | Moderate |
Strength | High tensile strength | Lower than PET |
Heat Resistance | Good thermal stability | Lower melting point |
Biodegradability | Non-biodegradable | Biodegradable in industrial settings |
How Material Properties Affect Injection Molding
The material properties of PET and PLA significantly impact their processing in injection molding.
-
PET requires precise control of parameters such as temperature and pressure due to its higher melting point. Its fluidity when melted allows for more intricate designs in molds, yet care must be taken to avoid defects like bubbles through adequate drying prior to molding.
-
PLA‘s lower melting point necessitates a cooler molding environment. Its poor fluidity can be challenging during the molding process, requiring adjustments in speed and pressure to ensure quality. Despite these challenges, its biodegradability makes it an attractive option for environmentally conscious manufacturers.
Practical Applications and Environmental Impact
Understanding the properties of PET and PLA1 is crucial for making informed decisions about their use in various applications. The choice between these materials often hinges on factors like the desired product life span, environmental considerations, and cost-effectiveness.
-
PET, with its robustness and clarity, continues to dominate in areas where durability is paramount.
-
PLA finds favor in sectors prioritizing sustainability, offering a compostable alternative albeit with a limited shelf life.
These material properties not only influence product design but also impact the sustainability of manufacturing practices.
PET has a higher melting point than PLA.True
PET's higher melting point requires precise temperature control in molding.
PLA is non-biodegradable in industrial settings.False
PLA is biodegradable in industrial settings, unlike PET.
How Does the Injection Molding Process Differ for PET and PLA?
Understanding the differences in injection molding processes for PET and PLA is key to successful production.
The injection molding process for PET and PLA differs primarily in temperature, pressure, and material handling. PET requires higher temperatures and precise drying, whereas PLA, being biodegradable, needs lower temperatures and specific flow adjustments. These distinctions ensure optimal product quality and efficiency.
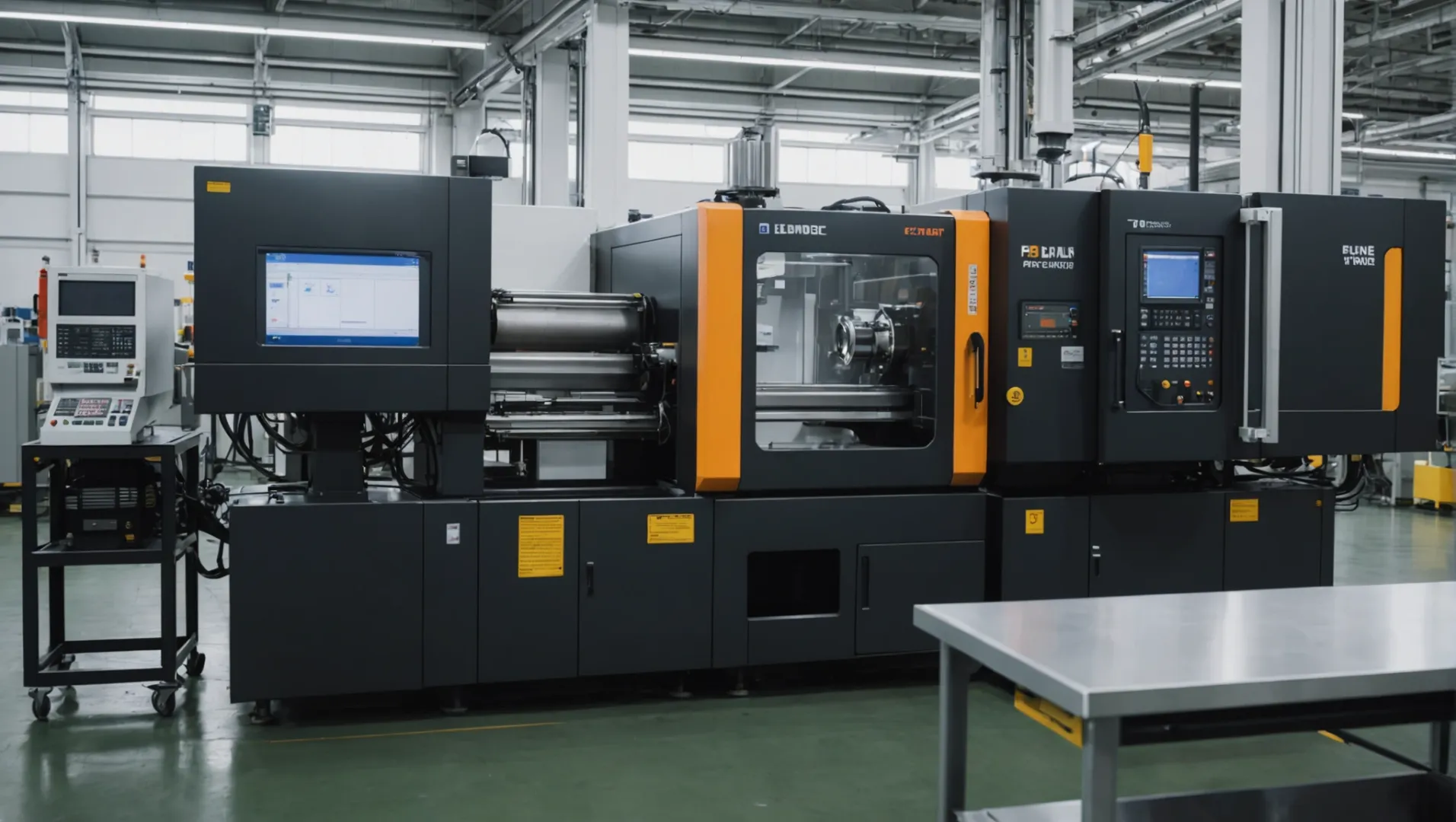
Material Properties and Implications
PET, or polyethylene terephthalate, is a thermoplastic polyester known for its strength, transparency, and heat resistance. Its application spans across beverage bottles and food packaging. In contrast, PLA, or polylactic acid, is derived from biomass materials such as corn and starch. It is biodegradable, making it a preferred choice for environmentally conscious packaging solutions.
Differences in Injection Molding Temperatures
One of the most critical differences between PET and PLA in injection molding lies in their melting temperatures. PET requires a higher melting point, necessitating more heat during processing. The temperature2 must be closely monitored to avoid degradation and ensure clarity and strength in the finished product.
PLA, however, melts at lower temperatures. This property not only reduces energy consumption but also calls for precise control to manage its poor fluidity. The lower temperature helps maintain PLA‘s biodegradability but requires careful adjustments to prevent defects in the molding process.
Adjustments in Injection Speed and Pressure
For PET, the injection speed and pressure must be meticulously calibrated to avoid issues like warping or incomplete mold filling. The pressure must be sufficient to ensure the material fills the mold cavity completely while avoiding stress marks or other imperfections.
PLA‘s poor fluidity demands slower injection speeds and sometimes higher pressures to fill the mold uniformly. This adjustment ensures that the biodegradable material forms correctly without compromising its structural integrity.
Importance of Material Drying
Both PET and PLA pellets must be dried before injection molding to remove moisture that could cause defects such as bubbles or silver streaks on the final product. However, drying PET is particularly crucial due to its hygroscopic nature, which can lead to hydrolytic degradation if not properly managed.
Influence of Mold Design
A well-designed mold is essential for both PET and PLA products. The mold must accommodate the shrinkage characteristics of each material—PET generally shrinks less than PLA, which can affect the final dimensions of the product. Proper mold design ensures dimensional accuracy and reduces waste during production.
In summary, while both materials utilize similar foundational processes in injection molding, understanding their unique properties allows for tailored adjustments that enhance product quality and production efficiency.
PET requires higher temperatures than PLA in molding.True
PET needs higher temperatures to prevent degradation and ensure clarity.
PLA has better fluidity than PET during injection molding.False
PLA has poor fluidity, requiring slower speeds and adjustments.
What Role Does Mold Design Play in Quality Control?
Mold design is a pivotal element in maintaining the quality of products created through injection molding.
Mold design ensures product quality by accommodating material properties, controlling dimensional accuracy, and preventing defects. It requires adjusting for factors like shrinkage rates and material fluidity, essential for producing consistent, high-quality PET and PLA cups.
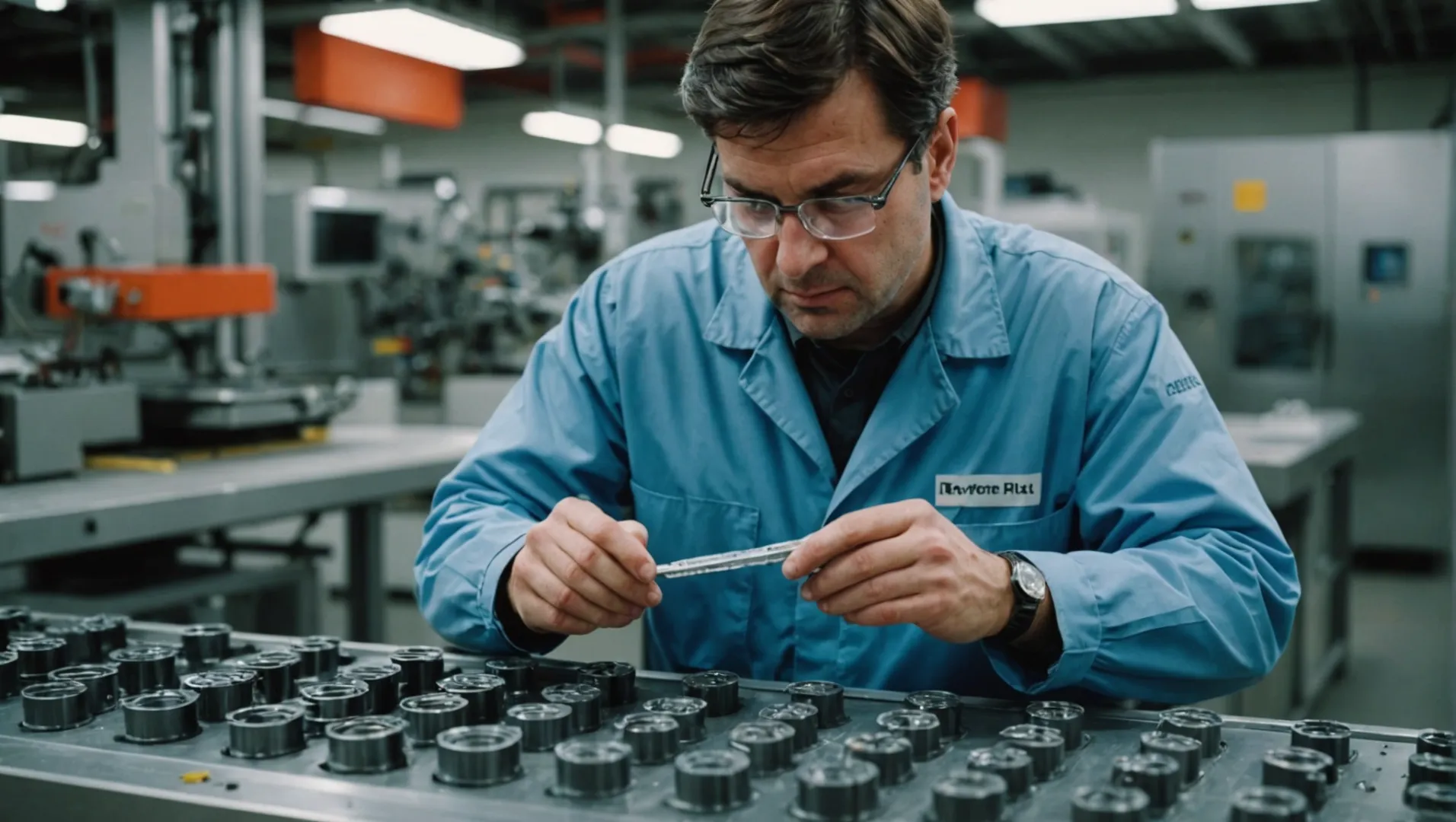
Understanding Material Properties and Mold Design
The properties of materials like PET and PLA significantly influence mold design. PET, being a thermoplastic polyester, boasts good transparency, strength, and heat resistance. These characteristics require a mold that can withstand high temperatures and pressures while ensuring clarity in the final product. Conversely, PLA is biodegradable with excellent biocompatibility, but its low melting point and poor fluidity demand precise adjustments in the mold design process.
Importance of Dimensional Accuracy
Dimensional accuracy is crucial for quality control. A well-designed mold accounts for the shrinkage rates of PET and PLA during the cooling phase. By doing so, it ensures that the final product maintains its intended dimensions and structural integrity. This accuracy is particularly important for applications such as beverage bottles and food packaging3, where fitting and seal integrity are vital.
Defect Prevention Strategies
Defects such as bubbles and silver streaks can compromise product quality. A mold tailored to the specific properties of PET or PLA can mitigate these issues by providing uniform heat distribution and optimal cooling paths. For instance, drying treatments for pellets before injection help prevent moisture-induced defects.
Additionally, maintaining a clean production environment prevents impurities from mixing into the material, which could otherwise lead to defects or a diminished appearance.
Adapting to Material Characteristics
The unique characteristics of PET and PLA require specific mold adaptations. For PET, higher temperatures necessitate robust molds with efficient cooling systems to prevent warping or distortion. On the other hand, PLA‘s poor fluidity means that molds must be designed to ensure smooth flow and fill without excessive pressure that could cause material degradation.
Regular Mold Maintenance
Regular maintenance of molds is indispensable for quality assurance. Over time, wear and tear can affect the precision of a mold. Regular inspection and servicing can identify issues before they affect production, ensuring the continuous production of high-quality items.
In summary, mold design is not just about creating a form but involves a comprehensive approach that considers material characteristics, production requirements, and defect prevention strategies. By focusing on these elements, manufacturers can consistently produce high-quality PET and PLA cups.
Mold design affects product dimensional accuracy.True
Proper mold design compensates for material shrinkage, ensuring accurate dimensions.
PLA has a higher melting point than PET.False
PLA has a lower melting point than PET, affecting mold design requirements.
How Can Equipment Maintenance Affect Production Efficiency?
Neglecting equipment maintenance can lead to reduced efficiency, increased downtime, and lower product quality.
Regular maintenance of injection molding machines minimizes breakdowns, enhances production efficiency, and maintains product quality. Well-maintained equipment operates smoothly, reducing the risk of defects and ensuring consistent output.

Importance of Regular Maintenance
In manufacturing environments, especially those involving injection molding machines, regular maintenance ensures operational efficiency. These machines are complex systems requiring precise operation to produce high-quality PET and PLA cups. A well-maintained machine minimizes unexpected breakdowns, ensuring a steady production flow.
Components Requiring Attention
-
Heating Elements:
Both PET and PLA require specific temperatures for effective molding. Malfunctioning heaters can lead to improper melting, resulting in defects. Routine checks help maintain temperature precision.
-
Mold Cavity:
Over time, wear and tear can affect mold accuracy. Regular inspection prevents issues such as flash (excess material) or incomplete fillings, maintaining product integrity.
-
Hydraulic Systems:
The hydraulic system powers the injection process. Leaks or pressure inconsistencies can lead to inefficient molding cycles. Maintenance of seals and regular oil changes ensure smooth operations.
-
Electrical Systems:
Proper functioning of the machine’s electrical system is critical for automation and control. Regular inspections reduce the risk of electrical failures, which can halt production.
Benefits of a Proactive Approach
Adopting a proactive maintenance schedule boosts production efficiency by:
- Reducing Downtime: Fewer unexpected breakdowns mean more continuous production hours.
- Improving Product Quality: Consistent operations reduce the likelihood of producing defective cups.
- Extending Equipment Lifespan: Regular checks and part replacements help prolong the life of machinery.
Real-World Example: Impact on Injection Molding
Consider a facility producing PLA cups. Poor maintenance could lead to inadequate drying of PLA pellets before molding, introducing moisture into the process and resulting in bubbles or other defects in the final product.
Emphasizing Preventive Measures
Implementing preventive maintenance strategies4 not only enhances efficiency but also fosters a culture of responsibility and foresight among staff. Training personnel to recognize early signs of wear can be invaluable.
By maintaining equipment meticulously, manufacturers ensure the reliability of their injection molding processes, ultimately leading to improved production efficiency and higher-quality PET and PLA cups.
Regular maintenance reduces unexpected equipment breakdowns.True
Proactive maintenance prevents failures, ensuring continuous production.
Neglecting mold cavity inspections can enhance product quality.False
Ignoring mold wear leads to defects, reducing product quality.
Conclusion
Understanding material properties and optimizing the injection molding process are key to producing high-quality PET and PLA cups. By focusing on mold design, drying treatments, and equipment maintenance, we can create sustainable packaging solutions that resonate with our eco-conscious values.
-
Learn how PET and PLA differ in their applications and environmental impact.: In terms of mechanical properties, PETG is fairly strong and durable. A typical PETG filament has a tensile strength of around 50 MPa, which is … ↩
-
Explore why precise temperature control is vital for PET molding.: Inappropriate temperature levels during the molding process can mar the desired outcome in no small measure. This is why it is crucial to … ↩
-
Learn how dimensional accuracy affects product quality and functionality.: Manufacturing Precision of Mold Dimensions: The precision with which the mold is manufactured is a key factor in determining the dimensional accuracy of the … ↩
-
Learn how preventive maintenance boosts efficiency and reduces downtime.: Lengthen asset lifespan · Lower risk of breakdowns · Increase efficiency · Decrease unplanned downtime · Promote health and safety · Boost customer satisfaction … ↩