Accurate estimation of the injection molding cycle can transform your manufacturing efficiency and slash costs.
To estimate the injection molding cycle accurately, consider key factors like cooling time, injection time, and mold operations. Cooling time is crucial and can be calculated using the formula t = (6s)×(δ²/χ²). Injection time depends on product volume and speed, while holding time compensates for shrinkage.
While these formulas provide a foundation, fully grasping the estimation process involves integrating multiple variables like mold complexity and machine specifications. Let’s dive deeper into these factors.
Cooling time is calculated as t = (6s)×(δ²/χ²).True
Cooling time depends on wall thickness and thermal diffusion.
What Role Does Cooling Time Play in Cycle Estimation?
Cooling time is a pivotal element in cycle estimation for injection molding, influencing both efficiency and product quality.
Cooling time in cycle estimation is vital as it affects the overall cycle duration and the quality of the molded part. Calculated using the formula t = (6s)×(δ²/χ²), where s is wall thickness and χ is thermal diffusion coefficient, it considers factors like mold temperature and plastic type.
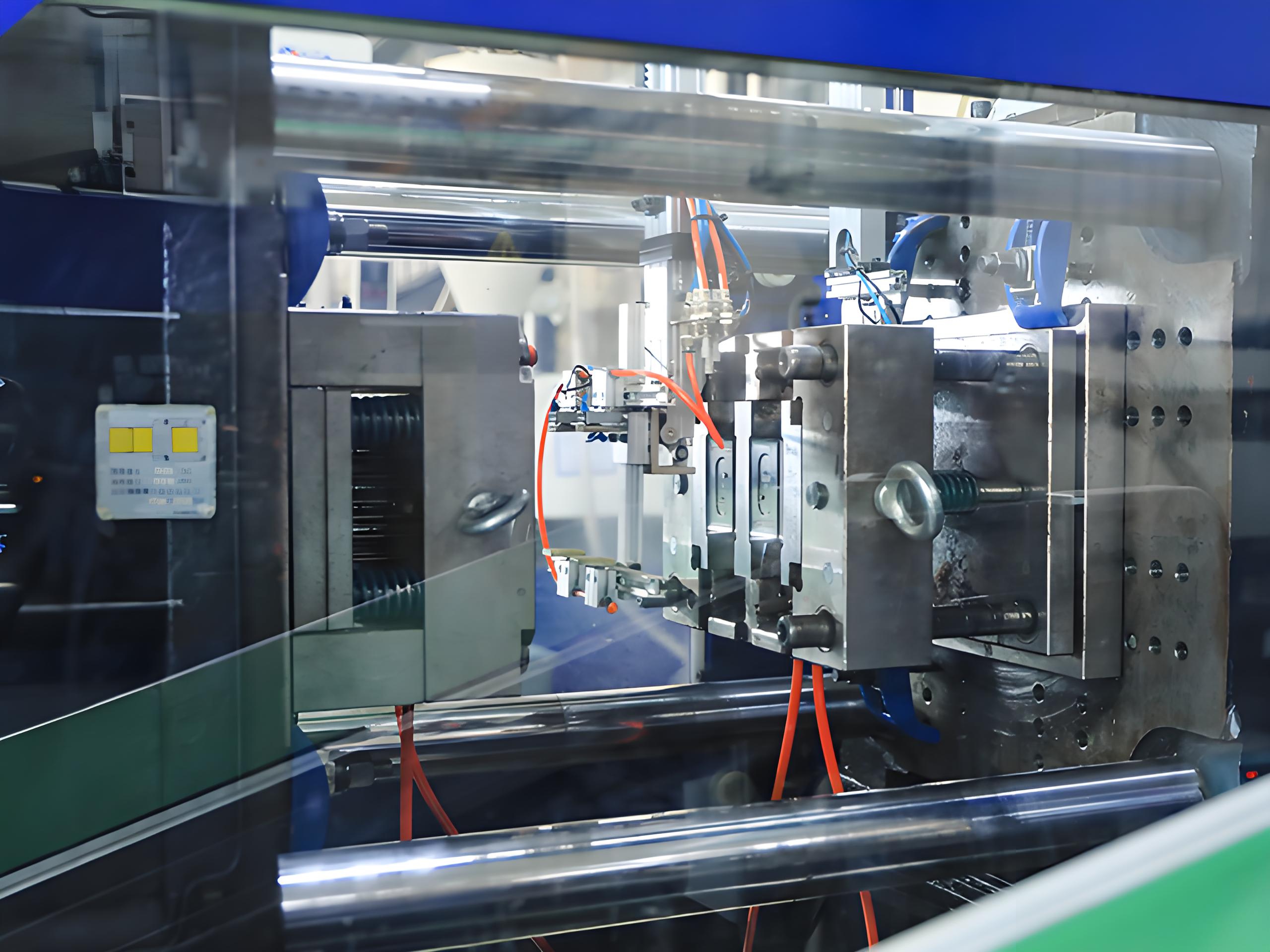
Understanding the Importance of Cooling Time
In the context of injection molding, cooling time is not merely a phase; it’s a crucial determinant of both efficiency and product quality. This period allows the molten plastic to solidify within the mold, forming the final product’s shape and structural integrity. The cooling time can be precisely calculated using:
[ t = (6s)×(δ²/χ²) ]
Where:
- t represents cooling time in seconds.
- s is the wall thickness of the product in millimeters.
- χ is the thermal diffusion coefficient of the plastic in mm²/s.
This formula underscores how varying wall thickness and material properties can significantly alter the cooling time, hence affecting the entire cycle estimation.
Factors Influencing Cooling Time
-
Mold Temperature: Lower mold temperatures typically reduce cooling times but may also affect product quality. A balance must be struck to ensure rapid cooling without compromising on strength or appearance.
-
Thermal Conductivity of the Plastic: Plastics with higher thermal conductivity will cool faster. This property should be considered when selecting materials for specific applications.
-
Shape and Size of the Product: More complex or larger products might require extended cooling periods to ensure uniform solidification, reducing the risk of defects such as warping or surface imperfections.
Practical Tips for Optimizing Cooling Time
-
Material Selection: Choose materials with suitable thermal properties that align with your production goals.
-
Mold Design Adjustments: Consider mold design enhancements like adding cooling channels to expedite heat dissipation.
-
Process Monitoring: Implement sensors to continuously monitor mold temperature and cooling rates to adjust parameters dynamically.
By focusing on these factors, manufacturers can optimize their injection molding cycle strategies1 for enhanced efficiency and product quality.
Cooling time affects injection molding product quality.True
Proper cooling ensures structural integrity and surface finish.
Higher thermal conductivity plastics cool slower.False
Plastics with higher thermal conductivity cool faster.
How Does Injection Time Affect Overall Efficiency?
Injection time is a crucial parameter in the injection molding process that significantly impacts overall efficiency and product quality.
Injection time affects overall efficiency by influencing cycle time and energy consumption. A precise injection time ensures optimal filling of the mold, reducing waste and defects. It is calculated using the formula t_injection = V/S×60, where V is volume and S is speed.
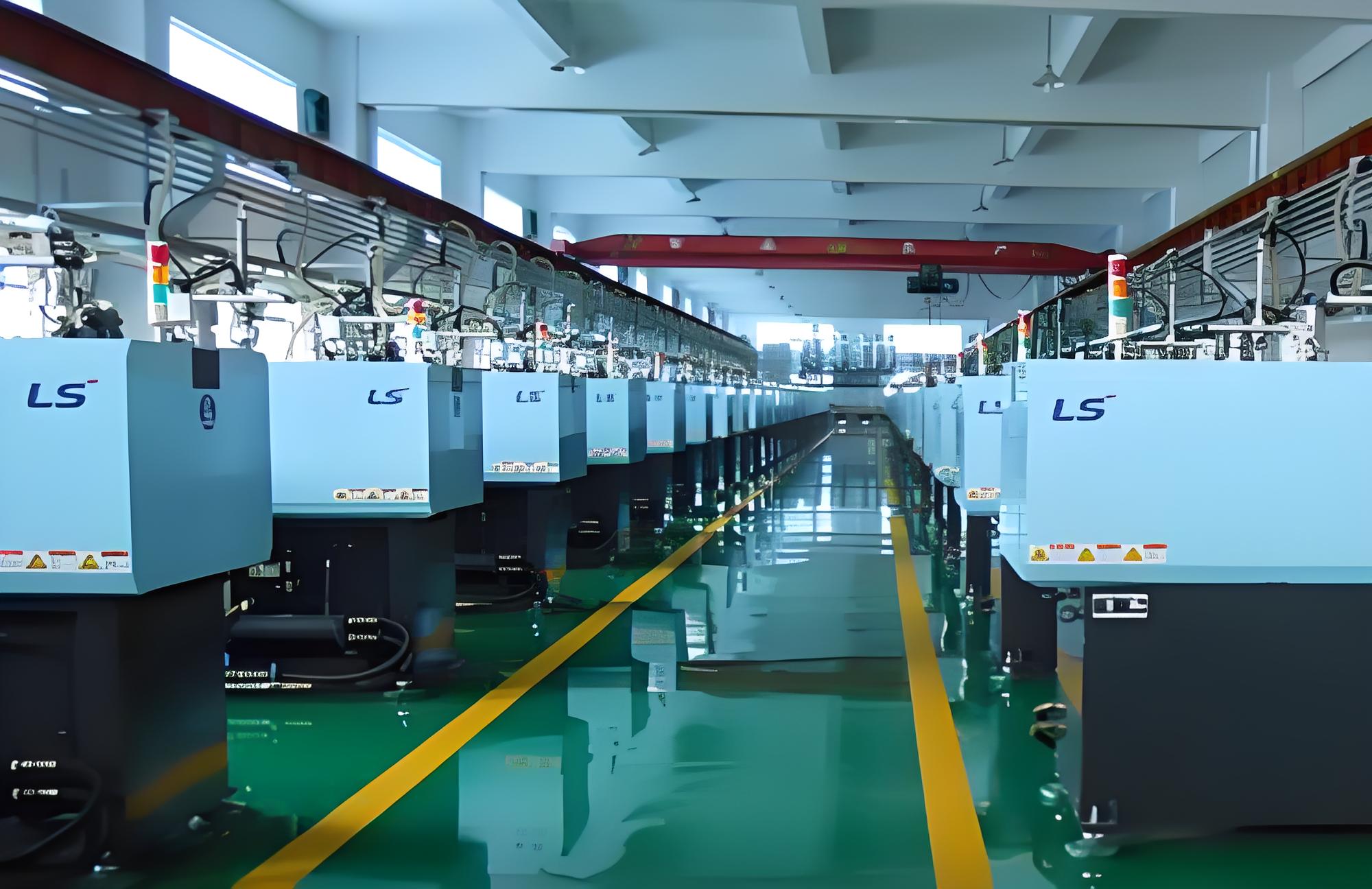
Understanding Injection Time
Injection time refers to the duration required to fill the mold cavity with molten plastic. It is determined by the injection speed and the volume2 of the product, playing a pivotal role in defining the cycle time of the injection molding process.
Formula for Injection Time
The formula used to calculate injection time is:
$$t_{injection} = \frac{V}{S} \times 60$$
- V: Product volume in cubic centimeters.
- S: Injection speed in cubic centimeters per second.
Impact on Efficiency
Cycle Time
Reducing injection time without compromising product quality can significantly decrease cycle time, allowing for more units to be produced in a given timeframe. This reduction directly boosts manufacturing efficiency.
Energy Consumption
Shorter injection times often lead to lower energy consumption, as machines operate less per cycle. This reduction not only decreases operational costs but also contributes to more sustainable production practices.
Factors Influencing Injection Time
- Product Complexity: Complex shapes may require longer injection times to ensure proper filling and avoid defects.
- Material Properties: Viscosity and thermal properties of plastics can alter the required injection speed.
- Machine Specifications: The capabilities of the injection molding machine, such as maximum injection pressure and speed, are critical.
Strategies for Optimization
- Balancing Speed and Pressure: Adjusting these parameters can help achieve efficient mold filling without introducing defects like flashing or incomplete filling.
- Monitoring and Adjustment: Continuously monitoring process variables and adjusting them based on real-time data can enhance consistency.
Conclusion
Understanding and optimizing injection time is essential for improving overall efficiency in injection molding operations. By carefully considering factors such as material properties and machine specifications, manufacturers can enhance both productivity and product quality.
Shorter injection times reduce energy consumption.True
Shorter times mean machines operate less, lowering energy use.
Injection time does not affect cycle time in molding.False
Injection time directly impacts cycle time by influencing mold filling speed.
Why Is Holding Time Essential in the Molding Process?
Discover the pivotal role holding time plays in ensuring the quality and accuracy of molded products.
Holding time is vital in the molding process as it compensates for the volume shrinkage of plastic during cooling. It is typically 1/3 to 2/3 of the injection time, depending on factors like product size, shape, and material shrinkage rate. Precise holding time ensures dimensional stability and minimizes defects.

Understanding Holding Time in Injection Molding
Holding time in injection molding is crucial for managing the shrinkage that occurs when plastic cools from a liquid to a solid state. As the plastic inside the mold begins to cool, it shrinks, potentially leading to defects such as sink marks or voids.
To counteract this, holding pressure is applied after the initial injection phase, maintaining pressure on the melted plastic until it solidifies sufficiently. This process is crucial for ensuring that the finished product retains its intended dimensions and structural integrity.
Factors Influencing Holding Time
-
Material Shrinkage Rate: Different plastics have varying shrinkage rates. For instance, crystalline materials like polyethylene might require longer holding times compared to amorphous materials like polystyrene due to their higher shrinkage rates.
-
Product Size and Shape: Larger or more complex products often necessitate extended holding times to ensure even pressure distribution and consistent cooling throughout the product.
-
Injection Time Ratio: Typically, holding time is calculated as a fraction (1/3 to 2/3) of the injection time. However, this ratio can vary based on specific material characteristics and product requirements.
Factor | Impact on Holding Time |
---|---|
Material Shrinkage | High shrinkage requires longer holding time |
Product Complexity | Complex shapes may need extended holding |
Injection Time Ratio | Generally 1/3 to 2/3 of injection time |
Optimizing Holding Time for Quality Products
To optimize holding time, consider conducting trial molding sessions3 to identify the ideal pressure and duration for your specific product and material. Adjustments can be made by closely monitoring any defects or variations in product dimensions.
Moreover, using a scientific molding approach4 can help refine parameters based on data-driven insights, allowing for precision and consistency in production.
Ensuring the correct holding time not only maintains dimensional accuracy but also enhances overall product quality by minimizing defects associated with improper cooling and shrinkage.
Holding time is 1/3 to 2/3 of injection time.True
Holding time usually ranges from 1/3 to 2/3 of the injection time.
Amorphous materials need longer holding times.False
Crystalline materials require longer holding times due to higher shrinkage.
What Are the Key Considerations for Mold Operations?
Mold operations are pivotal in the injection molding process, influencing both efficiency and product quality.
Key considerations for mold operations include cooling time, injection speed, and the design of demolding mechanisms. Each aspect plays a vital role in determining cycle time and product integrity.
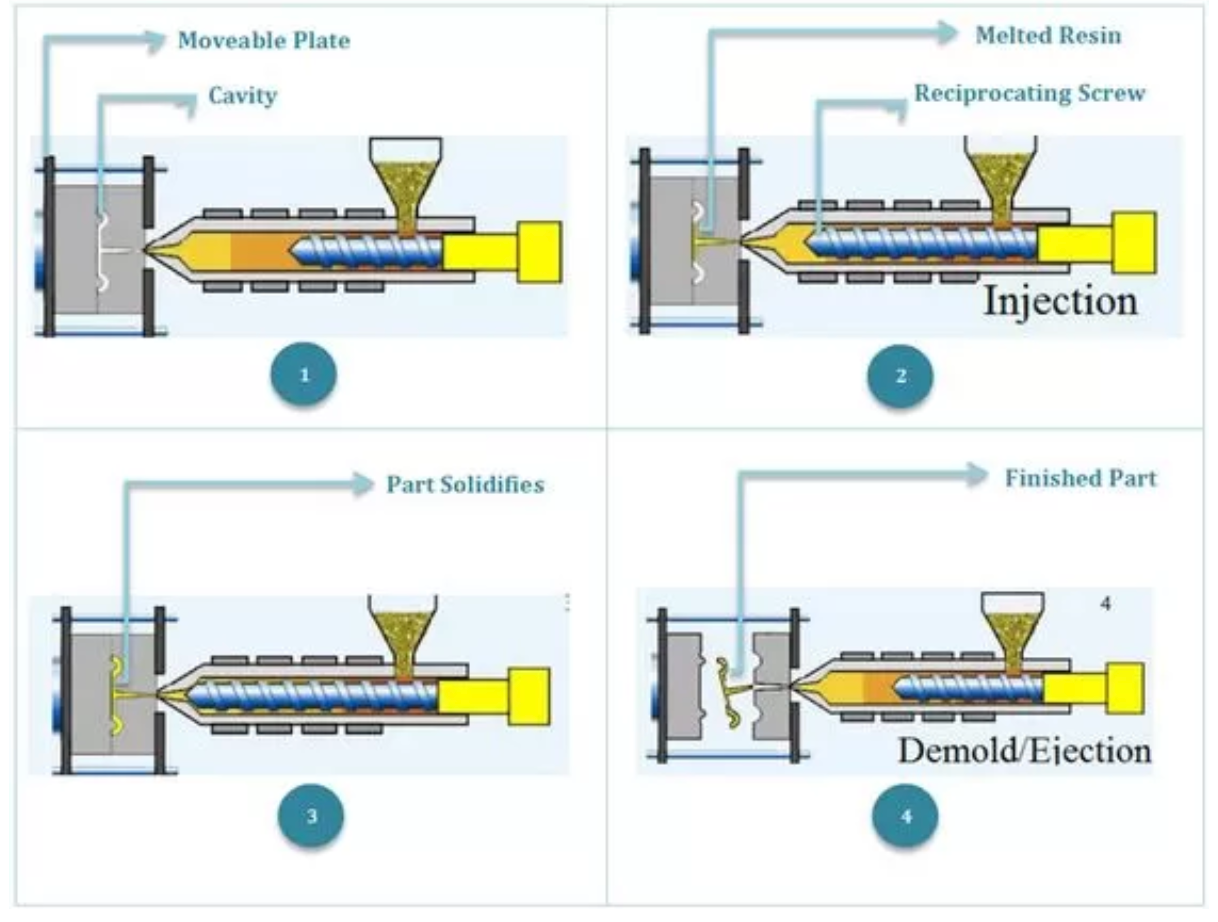
Cooling Time: A Critical Component
Cooling time is the largest segment of the injection molding cycle, significantly impacting efficiency. The cooling time can be calculated using the formula:
t = (6s)×(δ²/χ²),
where t is the cooling time, s is the wall thickness, and χ is the thermal diffusion coefficient. Faster cooling can be achieved by optimizing factors like mold temperature and thermal conductivity.
Example: For a product with a wall thickness of 2mm and a thermal diffusion coefficient of 0.2 mm²/s, the cooling time would be approximately 120 seconds.
Injection Time: Influencing Cycle Speed
Injection time depends on both the speed and volume of the plastic being molded. It can be estimated as follows:
t_injection = V/S×60,
where V is the product volume and S is the injection speed. Faster injection speeds can reduce cycle times but may require more advanced equipment.
Holding Time: Ensuring Product Quality
Holding time compensates for plastic shrinkage during cooling, often ranging from one-third to two-thirds of the injection time. It’s crucial for maintaining product dimensions and preventing defects.
Consideration: For larger products or those with high shrinkage rates, extending holding time can be beneficial.
Mold Operations: Opening, Demolding, Closing
- Mold Opening Time: Dependent on mold complexity and machine speed. Simple designs open faster.
- Demolding Time: Affected by product shape; intricate designs may need longer demolding times.
- Closing Time: Similar to opening, influenced by mold complexity and machine capabilities.
These elements collectively influence cycle efficiency and product quality. Adjustments to these parameters can optimize performance, necessitating a careful balance of all factors involved.
Explore cooling time estimation5 Learn about injection speed6
Cooling time is the shortest part of molding cycle.False
Cooling time is the longest segment of the injection molding cycle.
Faster injection speeds can reduce cycle times.True
Increasing injection speeds decreases the time needed for molding.
Conclusion
Mastering the estimation of the injection molding cycle can significantly enhance your production efficiency and product quality. Embrace these insights to elevate your manufacturing practices.
-
Discover advanced techniques for enhancing cooling efficiency.: Optimizing Cooling Time · Minimizing Filling Time · Appropriate Pause Time · Time Optimization in the Injection Stage · Reducing Excess Movements. ↩
-
Explore how injection speed influences mold filling efficiency.: Generally, at the same injection speed, higher injection pressure improves the plastic’s flow capability, enhancing the dimensional precision … ↩
-
Learn how trial molding can refine holding time for better results.: The mold trial process is a critical step in ensuring that a mold can produce qualified products, operate under normal production conditions, and meet the … ↩
-
Discover how scientific molding optimizes production processes.: Scientific molding is a systematic approach to injection molding that’s based largely on the tenets of the scientific method (developing and testing a … ↩
-
Gain insights into precise cooling time calculations.: A good rule of thumb is adding 20% to the cooling timer to account for variation on incoming material and slight shifts in machine performance. ↩
-
Understand how injection speed impacts cycle efficiency.: Increasing injection speed shortens the injection time, resulting in the production of high-quality products at significantly lower mold … ↩