Picture a world where each plastic piece matches perfectly, like parts of a puzzle. Really sounds ideal, right?
Injection pressure holds great importance for keeping plastic products stable in size. High pressure might lead to rebound and warping. Low pressure could cause parts to fill incompletely or inconsistently. Striking the perfect balance is key for accuracy. Stability really matters.
When I first started with injection molding, I learned that controlling injection pressure is like tuning a guitar. Pressure must be right to create harmony. For example, too much pressure once caused my design to shrink a little, ruining the fit for precise parts. This taught me patience and accuracy.
What if you mess up? Too much pressure might shrink your product after taking it out of the mold. Too little pressure might not fill the mold fully, resulting in a faulty product. I have seen how frustrating this is in important projects.
These details help us improve processes. Each piece must meet high standards of accuracy and performance. Maybe you are a beginner or just polishing skills. Mastering injection pressure is very important for perfect results.
Excessive injection pressure causes plastic deformation.True
High pressure can lead to material rebound, altering product shape.
Low injection pressure always ensures complete mold filling.False
Insufficient pressure may result in incomplete filling and defects.
What Happens When Injection Pressure is Too High?
Have you ever thought about what occurs when you increase the injection pressure too much? It feels like forcing a square peg into a round hole. Chaos follows, especially in the world of plastic molding.
High injection pressure in plastic molding causes product shrinkage. It also affects mold shape and leads to instability because of stress inside. Proper pressure is very important for quality. It is crucial for accuracy.
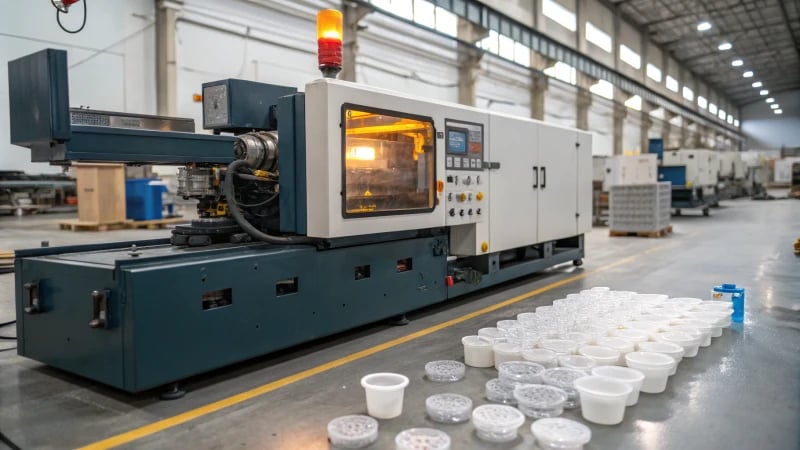
Effects of Excessive Injection Pressure
Pushing injection pressure too far is like releasing a monster inside the mold. The plastic melt becomes very stressed and starts pushing out with intense force. Once, while working on a precise part, after removing it from the mold, it shrank by 0.1mm. Every millimeter really matters in precision work.
Table: Problems with High Injection Pressure
Issue | Description |
---|---|
Rebound & Dimensional Change | Shrinkage post-demoulding due to internal stress release. |
Mold Deformation | Long-term use causes mold cavity deformation, affecting product consistency. |
Dimensional Instability | Residual stresses lead to size changes over time, especially in varying environments. |
Molecular chains in the plastic are pressed so hard that when released, they want to return to their natural form quickly. Over time, this really causes small deformations in the mold cavity, affecting size stability during production.
Concerns About Long-term Dimensional Stability
Residual stresses cause trouble long after molding. At first, they may seem small but expose the product to heat or humidity and changes happen slowly, like watching a slow-motion disaster. In high temperatures, I’ve noticed changes increase by 20-30%. Chaos for part compatibility follows.
Understanding these dynamics is essential for maintaining quality and consistency in plastic products. If unchecked, such issues may lead to significant discrepancies between design intentions and actual outcomes.
Balancing Injection Pressure for Best Results
Finding the right balance is key – neither too high nor too low. It’s about adjusting process parameters for harmony. I spent many hours fine-tuning settings to guarantee our designs looked good and remained strong during production. Checking for mold deformation1 and other things during calibration is crucial.
Being watchful and tweaking settings can prevent future issues, helping products meet specs and last longer in production cycles. By understanding injection pressure well, we design molds and pick materials that withstand forces effectively.
Table: Comparing High vs. Low Injection Pressure Effects
Parameter | High Pressure Effects | Low Pressure Effects |
---|---|---|
Filling Quality | Overfilled molds, potential flashing | Incomplete filling, short shots |
Dimensional Accuracy | Shrinkage due to rebound | Variability in product size |
Structural Integrity | Increased internal stresses | Weak spots due to uneven density |
Balancing these factors allows designers to perfect designs for functionality and manufacturing quality, reducing defects and improving performance. Grasping injection pressure intricacies really impacts the quality of molded components.
Explore resources on plastic injection molding techniques2 – they are treasure troves for mastering pressure management and achieving excellent results.
High injection pressure causes mold deformation over time.True
Excessive pressure leads to stress and deformation, affecting mold consistency.
Low injection pressure improves filling quality in molds.False
Low pressure can cause incomplete filling, leading to short shots.
Why Is Low Injection Pressure a Problem?
Do you sometimes feel like your car isn’t running smoothly? Low injection pressure could really be causing those unexpected problems.
Low injection pressure often results in molds not filling completely. This sometimes causes weak and inconsistent products. It really impacts plastic manufacturing. It also has a big effect on automotive engines. Incomplete mold filling is a major problem.
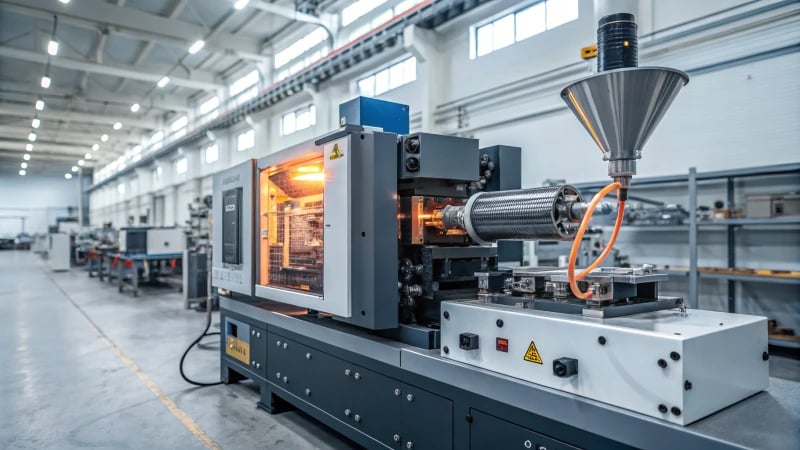
Incomplete Filling and Size Changes
Low injection pressure means the plastic melt lacks energy to completely fill the mold, causing a "short shot." Imagine creating a thick-walled plastic container but ending up with uneven walls due to low pressure – thinner in some areas than in others. It’s like baking a cake and realizing halfway through that the batter is insufficient.
Such issues are critical for industries3 where precision and consistency are paramount. In fields where precision is vital – like making car parts or electronics – this is a major problem. I once worked on a project where even a tiny mistake messed up the whole assembly line, causing issues with performance and fit.
Issue | Impact |
---|---|
Incomplete filling | Uneven product shapes and inconsistent sizes |
Dimensional accuracy | Varying sizes affecting interchangeability |
Size Precision and Uniformity
During mass production, I have seen how low pressure causes products to have different sizes. Each piece might differ slightly from the last. This variability can severely impact products that require strict interchangeability, like mechanical components. This is a big issue if parts must fit perfectly every time.
Furthermore, low pressure also results in uneven internal density. Picture a plastic part getting hot; it might start to bend or change size because its structure is weak. Such inconsistency can compromise the product’s resistance to external forces or environmental changes, such as temperature fluctuations. This is very concerning for automotive4 components, where strength is essential.
Keeping the right injection pressure is vital. It protects the strength and lifespan of parts in different uses. Understanding these ideas can cut down on mistakes and probably improve product quality in various industries.
Low injection pressure causes short shots in mold filling.True
Insufficient pressure prevents the plastic melt from fully filling the mold.
High injection pressure leads to dimensional inconsistencies.False
Dimensional inconsistencies are caused by low, not high, injection pressure.
How Does Injection Pressure Affect Long-Term Stability?
Have you ever thought about why some plastic parts last for years, yet others fall apart quickly?
Injection pressure plays a crucial role in keeping parts stable for a long time. It affects how accurate the dimensions are and controls stresses inside. The right pressure keeps molded parts strong. It stops them from bending. Quality stays high with the right pressure.
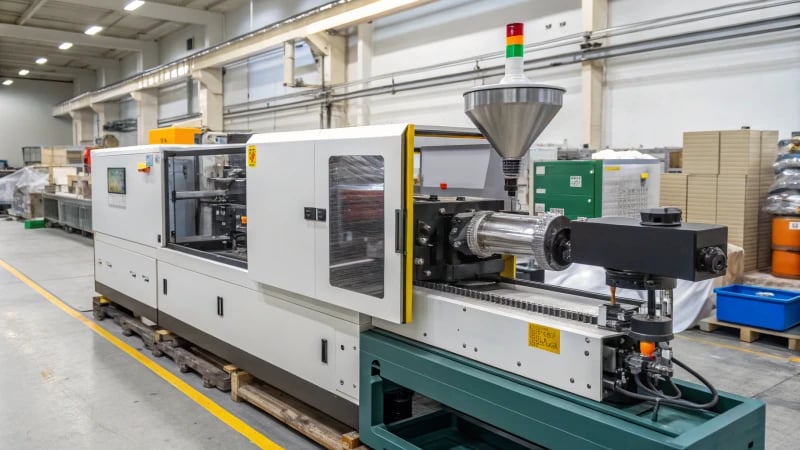
The Role of Injection Pressure
Injection pressure is a critical parameter in the molding process that dictates the dimensional accuracy5 and consistency of the final product. I recall when I first understood how important injection pressure is in molding. During a project where every tiny measurement was vital, I found that getting it right affects whether a product is consistent or not. Injection pressure decides the size and uniformity of each molded item. Too much pressure causes rebound effects; too little results in incomplete fills.
Impact of Excessive Injection Pressure
For a project involving precise instrument parts, I saw what happens with too much pressure. Parts mysteriously shrank by 0.1-0.3mm, causing chaos in a field needing exact precision. This shrinkage happens because high stress from too much pressure causes molecular chains to bounce back after demoulding.
This stress doesn’t disappear. Over time or when heated, it can warp parts more. I’ve seen how components misalign during hot summers, leading to mismatched pieces.
Condition | Impact on Product |
---|---|
High Injection Pressure | Rebound and shrinkage |
Environmental Changes | Increased deformation |
Consequences of Low Injection Pressure
On another occasion, I dealt with plastic containers that lacked uniform wall thickness due to low injection pressure causing short shots and uneven density. One fill was perfect, while the next warped under pressure, complicating mass production.
If a container’s bottom isn’t thick enough, it might bend when filled with liquid. I’ve seen this problem happen, frustrating our team.
Products with uneven density are more prone to changes under external forces or environmental conditions.
Balancing Injection Pressure for Stability
Finding the right balance is key. It took me years to learn that achieving the best injection pressure is both an art and a science. By understanding these factors, products perform better and last longer. Finding this balance helps products meet the high standards required in fields like ours.
Achieving optimal injection pressure is essential for ensuring both immediate and long-term stability of molded products by avoiding excessive stress and incomplete mold filling.
These insights into injection pressure taught me about solving today’s problems and preventing future ones. I always try to make sure our molded products not only look great but also last a very long time.
Excessive injection pressure causes product shrinkage.True
High pressure leads to stress, causing parts to shrink post-demoulding.
Low injection pressure ensures even density in molded parts.False
Insufficient pressure can cause uneven density, leading to defects.
How Can I Master Injection Pressure Management?
Did you ever think about how controlling injection pressure might greatly affect a manufacturing process? Let’s explore the best methods that help create perfect products.
Controlling injection pressure requires keeping a balance. Pressure should not be too high or too low. Regular checks help with this task. Understanding the materials matters a lot, too. Adjust machine settings for each production task.
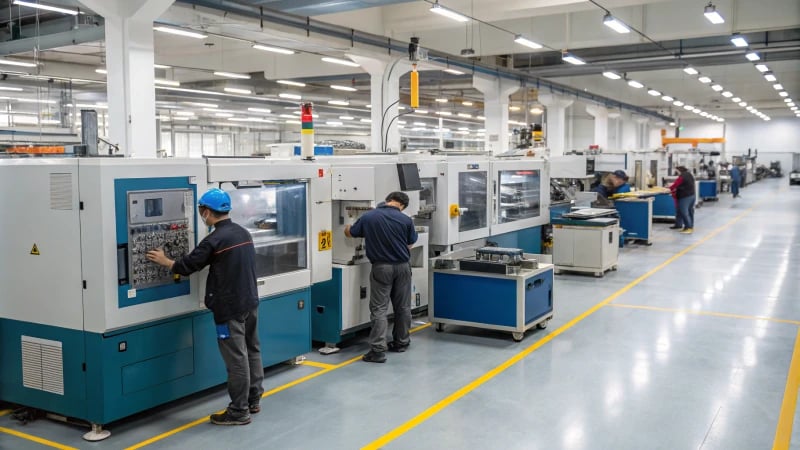
Understanding Injection Pressure
Injection pressure is very important for the quality of plastic items6. Imagine creating a part with great care, only to see it come out a bit smaller because of too much pressure. I’ve seen it happen. A small shrinkage like 0.1-0.3mm may not sound big, but industries needing perfect precision cannot accept it. Precision matters.
The Effects of Too Much Pressure
Excessive pressure shrinks parts and even forces them to change shape after coming out of the mold, altering the mold itself over time.
Issue | Effect |
---|---|
Shrinkage | Parts shrink after demoulding |
Mold Cavity Deform | Affects size consistency over time |
High pressure squeezes internal chains and builds stress inside, which leads to lasting changes.
The Effects of Low Pressure
On the other hand, too little pressure also causes problems. I’ve dealt with parts not fully filling, leading to short shots. These parts didn’t fit design needs, often having uneven density.
- Short Shots: Parts not fully formed.
- Unstable Thickness: Walls not even, hurting stability.
Keeping size accuracy in large-scale making is tough with low pressure. It’s like walking on a tightrope. Using too little pressure could harm part fits and how they work together in assemblies.
Good Ways to Handle Pressure
From my experience, regular checks and changes lead to good pressure control. I adjust settings based on material traits and specific needs.
Use Feedback Systems: Feedback systems revolutionized my work. They allow real-time changes and help keep product quality steady.
Material Knowledge: Different materials act differently under pressure. Knowing how each one behaves is key for the right settings.
For more info, check out material properties7 that are important for smart pressure control.
Using these ways supports smooth production and cuts down defects. Balancing injection pressure increases quality. It also makes production more cost-friendly and trustworthy.
Excessive injection pressure causes part rebound.True
Excessive pressure leads to shrinkage after demoulding, known as rebound.
Low injection pressure ensures dimensional accuracy.False
Insufficient pressure results in incomplete filling and dimensional deviations.
Conclusion
Injection pressure critically affects the dimensional stability of plastic products, with excessive pressure causing shrinkage and low pressure leading to incomplete fills, impacting overall quality and consistency.
-
Learn about how molds can deform under sustained high-pressure conditions. ↩
-
Explore different techniques in plastic injection molding to optimize processes. ↩
-
Learn about how low injection pressure affects manufacturing processes and product quality across different industries. ↩
-
Discover how low injection pressure can compromise the performance and efficiency of automotive engines. ↩
-
Explore how injection pressure influences the dimensional accuracy of molded parts, critical for ensuring high-quality production. ↩
-
Learn about how different levels of injection pressure affect the quality and dimensional stability of plastic products. ↩
-
Understand how specific material properties influence injection molding outcomes to optimize your manufacturing process. ↩