I remember the first time I held a piece of solid steel. It felt like holding the future of how things are made. I did not know then, but the toughness of mold materials really changed everything in our industry. It changed everything.
Hardness relates directly to how well mold materials resist wear. Higher hardness usually indicates better wear resistance. Strong atomic bonds reduce material loss when friction occurs. However, always remember to consider toughness and environmental conditions. These factors are very important.
When I started designing molds, I felt amazed by how a small change in hardness helped a mold last longer. But hardness alone doesn’t explain everything. Designing molds is like baking a cake; you need a good mix of ingredients. Toughness is important, too – just like a cake needs the right texture to stay strong. Once, I used high-carbon die steel that was hard but too fragile. It cracked under stress, which was frustrating. That experience taught me to look at every factor. Material structure and friction environment matter a lot. Each part has a special role in helping our molds last and work very well.
Higher hardness improves wear resistance in molds.True
High hardness materials resist wear by preventing atom transfer during friction.
Material toughness does not affect wear resistance.False
Poor toughness leads to cracks and spalling, reducing wear resistance.
- 1. How Does Material Toughness Affect Wear Resistance?
- 2. How Do Organizational Structure and Phase Composition Affect Wear Resistance?
- 3. How Does the Friction Environment Impact Wear Resistance?
- 4. Why Isn’t Hardness the Sole Determinant of Wear Resistance?
- 5. How Can Material Selection Improve Mold Durability?
- 6. Conclusion
How Does Material Toughness Affect Wear Resistance?
Have you ever thought about why some materials last a long time while others fall apart easily?
Material toughness greatly improves wear resistance by absorbing impact energy. Crack formation stops and structures stay strong during abrasion. It really helps maintain structural integrity.
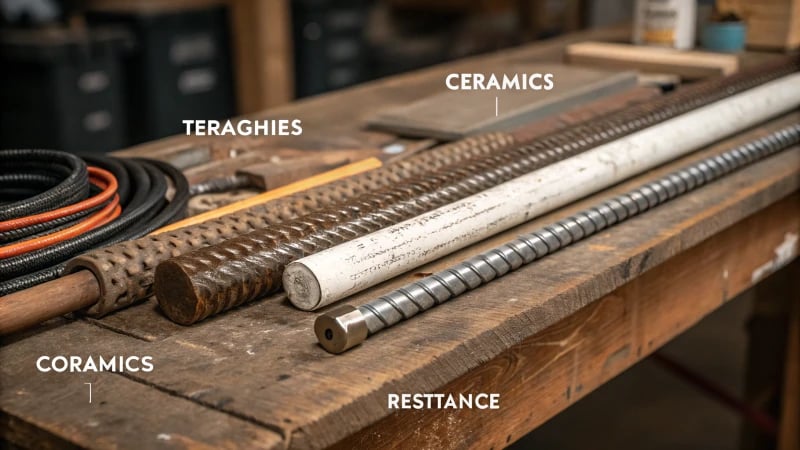
Understanding Material Toughness
Imagine a material that endures a lot and stays strong. Toughness is all about taking hits and changing shape without breaking. When I began creating molds, I quickly realized toughness is like an unacknowledged champion that prevents things from breaking down. In wear resistance1, this ability is very important for stopping materials from failing too soon.
The Interaction Between Toughness and Hardness
Hardness often gets all the attention, but I’ve seen how material toughness is key, especially in situations with lots of impacts or uneven friction. Tough materials absorb more energy without breaking, maintaining their wear resistance during difficult conditions.
Property | Influence on Wear Resistance |
---|---|
Hardness | Resists surface abrasion |
Toughness | Prevents crack formation |
Consider high-carbon steel2. It is very hard, but without enough toughness, it might chip at the edges under pressure. I’ve faced this issue with mold materials affected by dynamic forces. It taught me the importance of balancing these properties.
The Role of Microstructure
Microstructure acts like a hidden ingredient in enhancing toughness and wear resistance. Materials with finely spread carbides resist wearing out better. I’ve compared two equally hard materials – one with a martensitic structure and the other with scattered carbides. The latter often lasts longer because of its good microstructure.
Environmental Factors
The environment influences toughness. In rough settings, toughness helps the material withstand particle damage. In lubricated conditions, focusing on surface compatibility and roughness is important.
For designers, choosing materials becomes essential here. Just like Jacky must consider material selection3 to improve performance without reducing lifespan.
Practical Implications for Designers
Finding the right mix of hardness and toughness is crucial for designers like us to improve mold designs. Picking materials that are both tough and hard increases mold durability and product quality. I regularly use CAD tools to test these properties – it really simplifies the design process.
Recognizing the complete role of toughness in wear resistance enables us to make smart choices in selecting materials and planning design strategies. It’s like being a detective, gathering clues to build something strong and reliable.
Higher hardness improves wear resistance.True
High hardness materials resist wear better due to strong atomic bonds.
Material toughness does not affect wear resistance.False
Low toughness can lead to cracking, reducing wear resistance.
How Do Organizational Structure and Phase Composition Affect Wear Resistance?
Have you ever asked why certain materials remain intact for a long time, even when subjected to rubbing or scraping?
Organizational structure and phase composition strongly impact a material’s wear resistance. These factors dictate how effectively a material withstands friction and abrasion. This impacts both its durability and lifespan.
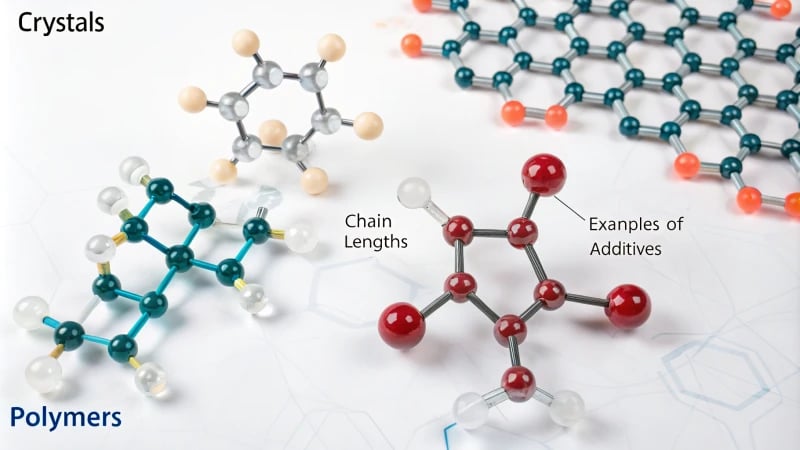
The Role of Organizational Structure in Wear Resistance
The organizational structure of a material refers to its internal arrangement, including grain size, shape, and distribution. In materials science, a refined microstructure with uniformly distributed phases can significantly enhance wear resistance. For instance, materials with fine carbide distribution4 act like a team of defenders that spread stress across the surface smoothly. This fine microstructure doesn’t just resist wear – it serves as armor, so the material resists friction and scratches better.
Material Type | Structure | Wear Resistance |
---|---|---|
Die Steel | Fine Carbides | High |
Martensitic | Coarse Grains | Low |
Materials with a uniform microstructure often have superior mechanical properties, which contribute to better wear performance. The presence of specific phases, like martensite or austenite, also plays a role in determining how a material responds to wear.
Phase Composition and Its Impact
Phase composition fascinates me. It describes the different phases present within a material, such as ferrite, pearlite, or cementite in steel. These phases determine hardness, toughness, and the overall wear resistance of the material. For example, high-entropy alloys5 are known for their complex phase structures that provide unique wear-resistant properties.
In some cases, adding hard phases like carbides or nitrides can dramatically improve the wear resistance of a material. These hard phases surprise me with their efficiency; they act as shields against abrasive particles—like guards at a club—keeping material loss low during frictional contact.
Interplay Between Structure and Environment
Understanding the link between organizational structure and phase composition is important for different environments. In abrasive settings where abrasive particles are present, materials that are very hard and finely structured stand out—it’s like wearing the best clothes for harsh weather. Conversely, in lubricated conditions? That’s a different story; compatibility between the lubricant and the material becomes more crucial than hardness alone.
Understanding these dynamics helps designers like me make informed decisions about material selection6 for specific applications. This knowledge is invaluable in ensuring optimal performance and longevity of products in diverse operating conditions.
Hardness is the sole factor in wear resistance.False
While hardness contributes, toughness and structure also affect wear resistance.
High hardness materials resist wear through elastic deformation.True
Elastic deformation helps high hardness materials reduce abrasive cutting depth.
How Does the Friction Environment Impact Wear Resistance?
Do you ever ask yourself how friction affects how long materials last?
Friction affects how materials resist wear by influencing how surfaces interact. Lubrication, abrasive particles and hardness are important. These factors decide how well a material endures wear. Hardness, in particular, really matters. Material strength also has a big impact.
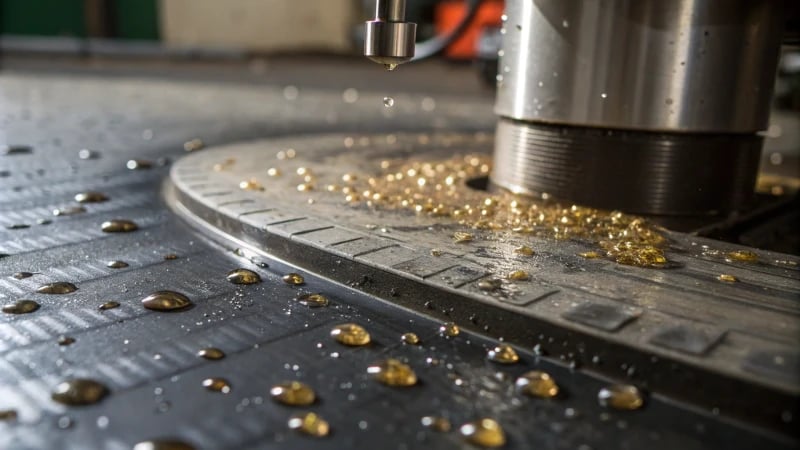
Grasping Friction Surroundings
When I began exploring mold design, understanding friction environments was like reaching a new level in a game. Friction involves more than just things rubbing together; it’s a whole world of conditions. Dry friction, lubricated friction, and abrasive settings each bring their own challenges. These affect how materials wear out over time.
Lubrication’s Impact
I remember discovering the magic of lubrication. It was like realizing how butter improves cooking! In lubricated situations, materials don’t scrape against each other as harshly. This decreases wear and tear, almost like giving materials extra years. If a material works well with lubricants7, it lasts longer. That’s pretty cool when creating something enduring.
Dry Friction and Wear
In dry settings, it’s totally different. I learned that materials encounter more direct contact. Here, the hardness of a material is critical, just like good hiking boots. Materials with high hardness, such as cemented carbide, resist wear due to their strong atomic bonds.
Battle with Abrasive Particles
Handling abrasive particles feels like constant fighting against grit. The material’s hardness serves as its shield. If particles are tougher, even the strongest materials might break. Good hardness-toughness balance8 becomes very necessary.
Friction Environment | Key Influences on Wear Resistance |
---|---|
Lubricated | Lubricant compatibility |
Dry | Material hardness |
Abrasive | Hardness-toughness balance |
Material Toughness in Various Environments
I’ve seen that toughness plays a crucial role. Materials that are both hard and tough stay strong, preventing cracks and chips even in harsh settings. That’s the real magic here.
Influence of Material Structure
The tiny details of materials are fascinating. I’ve seen how fine carbides can offer superior protection compared to simpler martensitic designs9. It’s like tiny warriors standing guard against wear.
Understanding these elements helps me pick materials that do well in specific friction settings. They stay strong under pressure and last as long as needed.
Higher hardness equals better wear resistance.True
High hardness materials resist wear by reducing material loss during friction.
Material toughness doesn't affect wear resistance.False
Toughness impacts wear resistance; low toughness can lead to cracking.
Why Isn’t Hardness the Sole Determinant of Wear Resistance?
Hardness is not the only factor that matters for wear resistance. Let’s explore why there’s more to it.
Hardness alone is not enough to judge wear resistance. Other things matter, too, like how tough the material is. The structure of the material plays a role in how much wear it resists. The environment around the material can change its durability. These factors significantly impact wear resistance.
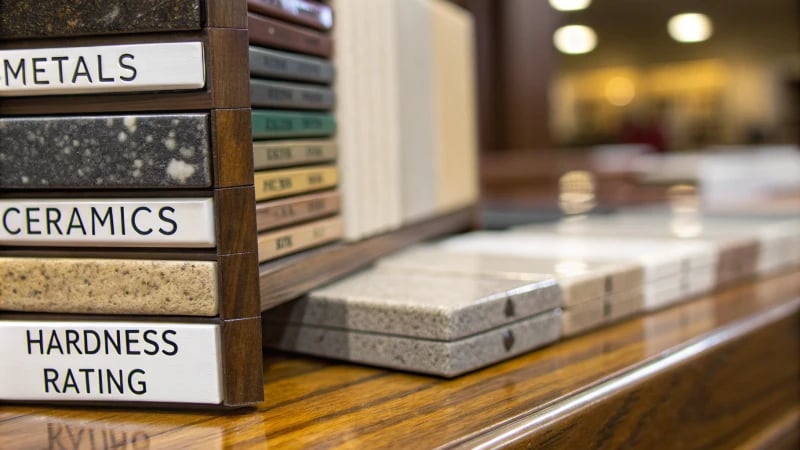
The Influence of Material Toughness
I once worked on a project using high-hardness steel, believing it was ideal for durability. We ignored its low toughness. Soon, small cracks formed and stress caused the material to break apart. I discovered that toughness, which is a material’s capacity to endure energy without breaking, is vital. Even the hardest materials could crumble under pressure without it.
While hardness indicates a material’s ability to resist deformation, toughness refers to its ability to absorb energy without fracturing. A material with high hardness but low toughness may crack or fragment under stress, reducing its wear resistance.
Organizational Structure and Phase Composition
Think about baking a cake. You might have the finest ingredients, but without proper mixing, the cake may flop. In materials, similar hardness can have different outcomes based on their organizational structure10. Once, I used die steel with small carbides in a project. It performed better than others since the carbides absorbed much of the friction, shielding the rest from wear.
Material Type | Structure Type | Wear Resistance |
---|---|---|
Die Steel | Fine Carbides | High |
Martensitic | Simple Martensitic | Lower |
Environmental Factors Affecting Friction
Once, I designed for a dry setting, assuming high hardness was enough. But without good lubrication, friction soon damaged the material. In lubricated environments, friction environment11 compatibility and surface smoothness often matter more than hardness. Every environment has its unique traits and grasping them is crucial.
The friction environment impacts wear resistance significantly. In dry conditions, high hardness is crucial; however, in lubricated environments other factors like compatibility with lubricants and surface roughness gain importance.
Mechanism of Resistance to Wear
High-hardness materials combat wear with elastic bending and tiny cutting. When abrasive bits hit a surface, high-hardness materials lessen cut depth by creating an elastic return force. This mechanism stops easy surface abrasion which really helps its wear resistance.
Overall, the complex mix of factors defines how well a material handles wear. Understanding this balance is key to choosing materials wisely as I’ve learned from both achievements and failures in my projects.
Higher hardness equals better wear resistance.True
High hardness materials resist wear by preventing surface atom detachment.
Toughness is irrelevant to wear resistance.False
Lack of toughness can lead to cracks, reducing wear resistance.
How Can Material Selection Improve Mold Durability?
Have you ever thought about how picking the right material could be the key to your mold lasting longer?
Choosing the best material for molds is essential. It really helps them resist wear and reduces maintenance. Materials with high hardness fight against abrasion. Toughness prevents cracks. Balancing these factors results in durable and economical molds.
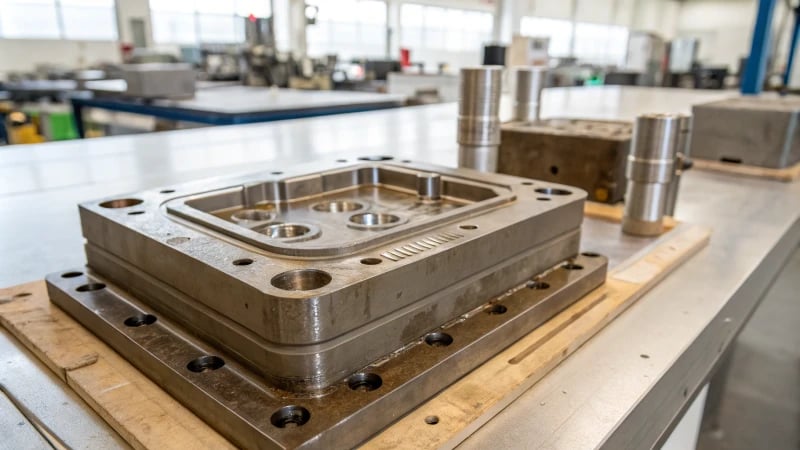
The Importance of Hardness
When I began working with molds, the importance of material hardness really surprised me. Hard materials last longer. It reminds me of how sturdy hiking boots protect feet on rocky paths. Materials that are very hard don’t get scratched easily. Cemented carbide has an impressive hardness of HRA89-92.5. It survives harsh environments better than regular carbon steel, ensuring the mold retains its precision over time.
This positive correlation12 between hardness and durability is crucial for maintaining mold integrity.
Balancing Hardness and Toughness
Hardness is not everything, though. I realized this, learning from mistakes. It’s similar to cooking steak; you need both hardness and softness to get it right. Toughness stops cracks and chips under stress. I’ve seen strong steels break during heavy tasks due to insufficient toughness.
Thus, balancing these properties is essential for improving mold longevity.
Role of Material Structure
The way a material is made inside is also important. Imagine books in a library—well-arranged fine carbides increase wear resistance more than simple structures.
Material Type | Structure Characteristics | Wear Resistance |
---|---|---|
Die Steel | Fine carbide distribution | High |
Martensitic Material | Simple structure | Moderate |
I’ve learned two materials might have the same hardness but work differently because of their internal structure.
Environmental Considerations
Where you use the mold also matters, like choosing the right shoes for the beach or snow. In places with oil, hardness is not the only concern; compatibility with lubricants and surface smoothness become critical factors.
Conversely, in abrasive environments, a material’s hardness becomes paramount to keep molds strong over time.
By considering these things, designers like me—and maybe you—can choose materials wisely for different uses in consumer electronics manufacturing, as seen in mold design trends13. It’s interesting to see how mold design ideas change with new experiences.
High hardness improves mold wear resistance.True
Higher hardness leads to stronger atomic bonds, reducing surface abrasion.
Toughness is irrelevant to wear resistance.False
Poor toughness can cause cracks and spalling, reducing wear resistance.
Conclusion
Hardness significantly influences mold materials’ wear resistance, but toughness, microstructure, and environmental factors are also crucial for optimal performance and longevity in various applications.
-
Explore this link to understand how material toughness helps prevent wear by resisting crack formation. ↩
-
Learn about mold materials that balance hardness and toughness for improved durability. ↩
-
Gain insights into selecting materials that maintain performance in various wear environments. ↩
-
Explore how fine carbide distributions enhance material durability and stress distribution under friction. ↩
-
Learn about the unique properties of high-entropy alloys that contribute to exceptional wear resistance. ↩
-
Understand how different friction environments alter the effectiveness of material structures. ↩
-
Exploring this link offers insights into how material choice affects performance in lubricated environments. ↩
-
This link explains the significance of balancing hardness and toughness for enhanced wear resistance. ↩
-
Discover how microstructural differences impact material wear resistance through this link. ↩
-
Learn about how different structures in steel affect its wear resistance. ↩
-
Explore how varying friction environments influence material wear resistance. ↩
-
Explore why materials with higher hardness offer better wear resistance, crucial for extending mold life. ↩
-
Discover the latest trends influencing mold design and how they impact manufacturing efficiency. ↩