I remember the first time I chose mold steel. It felt like selecting the right tool for a grand masterpiece.
Hardness and toughness in mold steels are very important for injection molding. Hard steels provide excellent dimensional stability and good quality. Tough steels resist breaking. However, hard steels prove difficult to process. Tough steels, however, might wear down quickly. This affects efficiency and durability.
Thinking back to my first projects, choosing the right mold steel was like figuring out a tricky puzzle. Each type of steel has its own good and bad sides. High hardness steels give very precise shapes. This is vital for tiny parts like watch pieces. I saw these steels keep their shape well under heavy pressure. Parts fit just right every time.
But working with hard materials is very tough. I spent many hours dealing with the hard process of cutting these steels. A small mistake leads to tiny cracks or worse, damages a mold completely. While these steels offer precise shape and last a long time, they are hard to process.
High toughness steels are very appealing. They rescued me many times in projects with detailed shapes and strong forces. For example, thin electronic cases. These steels are really strong; they don’t crack under stress. But they are not always perfect. Their lower hardness means they wear out over time, especially with rough materials.
Choosing requires thinking carefully. Seeing these details helps me pick the right steel for each case. Success and long use depend on this choice.
High hardness mold steel resists dimensional changes.True
High hardness steel maintains dimensional accuracy under injection pressures.
High toughness mold steel has excellent wear resistance.False
High toughness steels have low hardness, leading to faster wear.
What Are the Key Differences Between High Hardness and High Toughness Mold Steels?
Have you ever thought about how your choice of mold steel might help or ruin your next big project?
Mold steel with high hardness keeps its shape and fights wear and tear. It is great for precise parts. Mold steel with high toughness deals well with impacts. It works well for complicated designs. Complex molds need this type of steel.
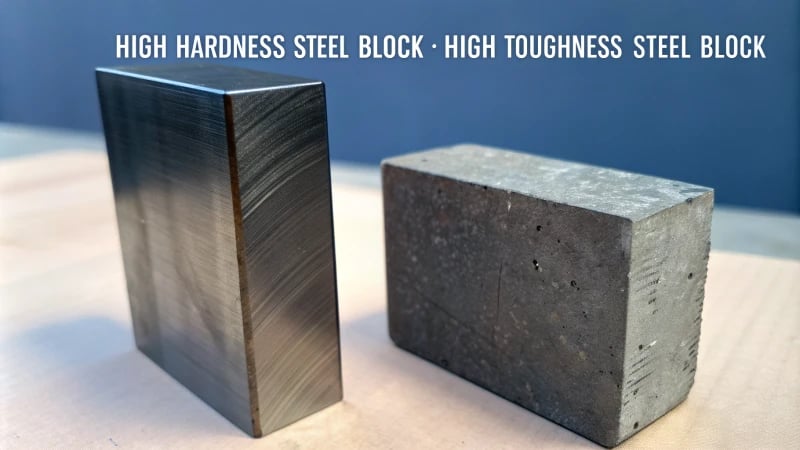
High Hardness Mold Steel
High hardness mold steel is essential for creating precision parts where every tiny detail matters. It resists heavy processing yet maintains its shape, making it ideal for components like watch parts. For instance, S136 steel retains exact sizes even after many cycles, ensuring a tolerance of ±0.03mm.
However, there are notable disadvantages1. This type of steel lacks toughness and can crack under stress, especially with large or unevenly thick plastic pieces. I’ve observed this issue when dealing with big plastic molds where uneven stress results in mold breaks.
Advantages | Disadvantages |
---|---|
Good dimensional accuracy | Poor toughness and easy to break |
High surface quality | Difficult processing |
Strong wear resistance |
High Toughness Mold Steel
In contrast, high toughness mold steel is best suited for complex designs like phone casings. Its good fracture resistance makes it less prone to breaking upon impact, which is crucial for uninterrupted production.
Despite its resilience, high toughness steel may lose some accuracy over time. When used for items like plastic gears, expect slight deviations in precision after prolonged use. This experience has taught me the importance of selecting the right steel for each job.
Advantages | Disadvantages |
---|---|
Good fracture resistance | Slightly poor dimensional stability |
Strong adaptability to conditions | Poor wear resistance |
Understanding these differences is vital for me and others like Jacky. Selecting wisely helps designs meet and often exceed expectations in manufacturing. Discovering more about real-world applications2 can offer new insights into picking the right materials.
High hardness mold steel ensures dimensional accuracy.True
High hardness mold steel resists deformation, maintaining precise dimensions.
High toughness mold steel is highly wear-resistant.False
High toughness mold steel lacks wear resistance, leading to faster wear.
How does mold steel selection affect precision and product quality?
Have you ever thought about how choosing the right mold steel affects product quality?
Picking the right mold steel greatly affects both precision and product quality. Steel with high hardness gives excellent dimensional stability and a nice surface finish. In contrast, steel with high toughness provides really good fracture resistance. Every choice has its own trade-offs, changing how products are manufactured and the final results.
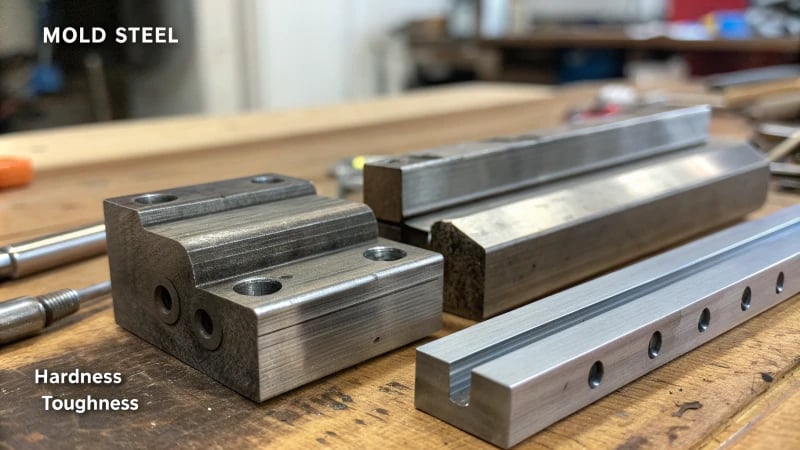
Advantages of High Hardness Mold Steel
High hardness mold steels like S136 offer remarkable dimensional accuracy. During injection molding, they resist the pressure of plastic melt effectively, maintaining cavity dimensions within tight tolerances. Think of a project where every tiny bit matters – like making the small gears of a watch. That’s the job for high hardness mold steels like S136. They give exact measurements, standing strong against plastic melt during molding.
These steels also facilitate high surface quality. Carbide steels yield surfaces with minimal roughness, essential for producing optical lenses. The surface was extremely smooth, like glass. However, there’s a downside: poor toughness3. I learned this during a car dashboard project; the steel broke under pressure, teaching me that even strong materials have limits.
Benefits of High Toughness Mold Steel
On the flip side, high toughness steels such as P20 excel in fracture resistance. These materials withstand impact forces and manage complex shapes easily, ensuring molds remain intact during production. High toughness steels act as protectors and are particularly beneficial for delicate products.
These steels adapt well to complex conditions. For example, creating toy molds from soft PVC showed me how adaptable they are; H13 steel held its shape well during demolding processes.
Yet, there are trade-offs. Dimensional stability may fade over time; molds wear out after many uses, changing product details slightly.
Steel Type | Advantages | Disadvantages |
---|---|---|
High Hardness | Dimensional accuracy, surface quality | Poor toughness |
High Toughness | Fracture resistance, adaptability | Dimensional instability |
Designers like Jacky4 must know this well. Each project is different; choosing the right steel means balancing these factors with material qualities5 and project needs to achieve precision and quality in final products.
High hardness mold steel ensures minimal dimensional changes.True
High hardness mold steel resists pressure, maintaining dimensions.
High toughness mold steel has excellent wear resistance.False
High toughness mold steel lacks wear resistance against fillers.
What Are Common Challenges Faced When Working with High Hardness or High Toughness Steels?
When I first held these strong and tough steels, it felt like exploring unknown lands. These steels challenge the craftsman while giving satisfaction. They need a special approach and lots of patience.
Working with steels that are very hard causes processing problems and quick tool damage. Such steels also break easily. Steels with high toughness face problems with resisting wear and keeping their shape. Special methods and materials are necessary to solve these challenges.
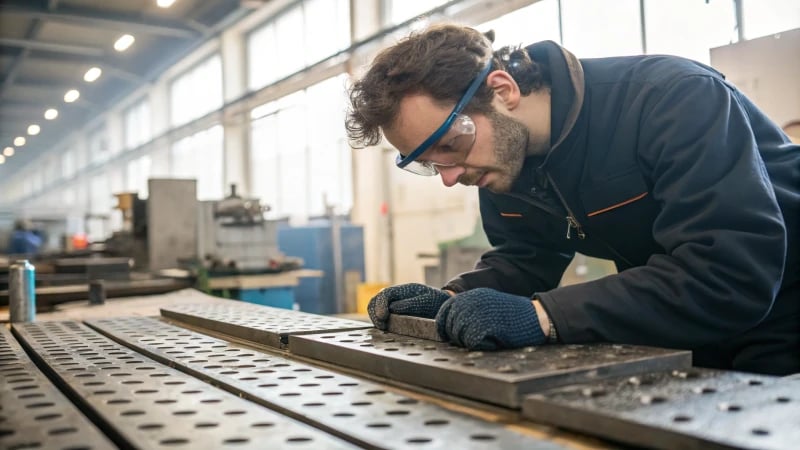
Challenges with High Hardness Steels
I remember working with high hardness steels for the first time. It felt like wrestling a bear. These steels offer really good resistance to wear and maintain accurate sizes, but they very much damage tools quickly due to strong cutting forces. Specialized equipment was necessary, and keeping a close watch on processing was essential.
Challenge | Description |
---|---|
Tool Wear | High hardness results in faster tool degradation. |
Brittleness | Susceptible to fracture under stress or impact. |
Processing Difficulty | Requires advanced tools and expertise. |
- Brittleness: Despite their advantages, these steels are prone to cracking when subjected to impact or uneven stress. I once designed a mold that broke because stress was not spread evenly, teaching me the need to balance hardness and flexibility.
Challenges with High Toughness Steels
High toughness steels feel like a strong friend who takes hits but drops things occasionally. They resist fractures well and handle difficult situations but struggle to keep their shape over time.
- Dimensional Stability: Over prolonged use, these steels might show changes due to wear, affecting precision tools like plastic gears.
Challenge | Description |
---|---|
Wear Resistance | Prone to surface wear, especially with abrasive materials. |
Dimensional Changes | Susceptible to size changes after repeated use. |
- Wear Resistance: Less hardness brings more flexibility but also more vulnerability in rough conditions. I learned this when molds for glass fiber plastics wore out faster than I thought they would.
The choice of the right steel type6 for each task is crucial. Balancing hardness and toughness helps in many cases. Protective coatings and creative methods have saved me in tough situations.
High hardness mold steel improves dimensional accuracy.True
High hardness mold steel resists deformation, maintaining precision.
High toughness mold steel is ideal for high-wear applications.False
High toughness steel lacks wear resistance, unsuitable for high-wear use.
Conclusion
Understanding the impact of hardness and toughness in mold steels is crucial for optimizing injection molding processes, balancing precision, durability, and efficiency in manufacturing.
-
Learn about the challenges of using high hardness steel in molds. ↩
-
See examples of how different mold steels are used in industries. ↩
-
Learn how high hardness materials influence mold durability and performance in injection molding. ↩
-
Understand why choosing the right steel is crucial for mold designers to meet production needs. ↩
-
Explore the varying properties of mold steels to better match material selection with project goals. ↩
-
Explore which steel types offer the best balance for injection molding applications. ↩