Do you ever think about how using the correct steel helps an injection mold last longer?
Hardness ensures wear resistance, enhancing mold steel durability, while toughness prevents cracking under stress. Together, they significantly extend injection mold longevity by balancing resilience and strength.
I started in the mold industry with a sense of wonder about material changes and their effects on mold life. A simple shift in material could really extend a mold’s lifespan. It is truly fascinating how hardness and toughness work well together. These two qualities allow the mold to handle tough production demands.
Hardness is crucial for resisting damage and wear. Imagine the mold cavity as a finely-tuned device, with hardness acting as its protective shield. This shield guards against the constant rubbing from plastic melts. Molds without enough hardness wore down quickly. Such wear leads to shape changes and expensive replacements. For example, using steel like H13, treated to a hardness between HRC48-52, reduces wear significantly. This is especially true with plastics that have abrasive fillers like glass fibers.
Toughness involves resilience. It is the mold’s ability to recover from hits without breaking under pressure. I remember times when molds faced sudden impacts or unusual conditions during use. In these situations, toughness absorbed blows without damaging the mold’s structure.
These properties are essential when selecting steel for your needs. They guarantee durability and accuracy in production. Next time you plan your design, consider these details carefully. A little focus on these aspects might really help avoid future problems.
Hardness increases mold steel's wear resistance.True
Higher hardness reduces surface wear, extending mold life.
Toughness decreases mold's impact resistance.False
Toughness enhances a material's ability to absorb impact.
Why is Hardness Important for Wear Resistance?
Hardness may appear as just one more material characteristic. However, in engineering, it significantly changes the situation.
Hardness is very important for wear resistance. It determines how well a material resists surface abrasion and deformation. Often, greater hardness improves wear resistance. This is essential for extending the service life of components such as molds. Molds benefit significantly from high hardness.
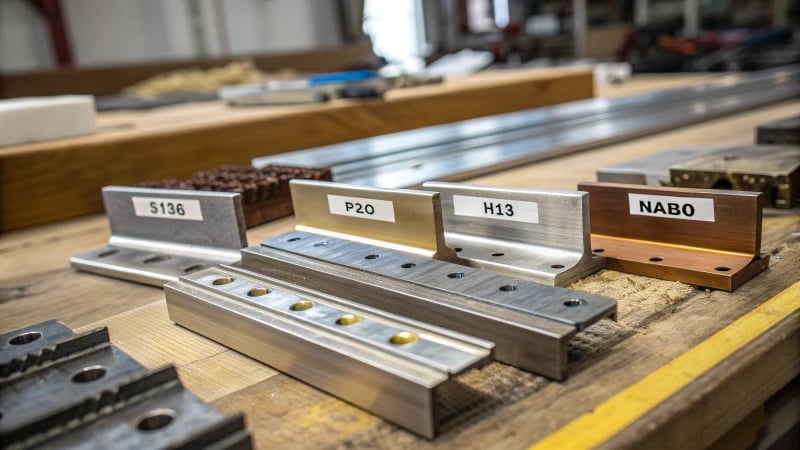
Hardness and Surface Wear
Years of working with molds taught me that material hardness is key to resisting wear. Hardness is the ability of a material to resist scratches and dents. A harder material withstands friction and abrasive forces better, making it highly resistant to wear.
Take injection molds1, for instance. I recall a project where we used molds with high hardness levels for handling plastic melts filled with abrasive materials like glass fibers. Over time, these molds maintained their shape and dimensions fantastically, leading to consistently high-quality products. The molds showed much less wear compared to those with lower hardness.
Influence on Service Life
Hardness directly affects how long components last. I worked with mold steels like H13, which reached impressive hardness levels of HRC48 – 52 after heat treatment. These steels resisted wear significantly more than softer materials, lasting much longer.
The table below illustrates the relationship between hardness and service life:
Mold Steel Type | Hardness (HRC) | Estimated Service Life (Cycles) |
---|---|---|
Standard Steel | 40 | 100,000 |
Hardened Steel | 50 | 250,000 |
Deformation and Hardness
Hardness involves withstanding pressure, not just resisting scratches. High-hardness materials resist elastic deformation well. This is important during high-pressure processes like injection molding. Keeping mold cavities in shape means fewer defects such as size variations or flash.
Producing large plastic items involves intense injection pressure. Suitable mold steels2 with enough hardness handle this without bending or deforming, extending their service life.
Balancing Hardness with Toughness
However, hardness must be balanced with toughness. A material that is hard but brittle can develop cracks under stress. I seek a balance where wear resistance and durability coexist beautifully. Materials balancing hardness with impact resistance3 can extend the lifespan of components under cyclic loading or harsh conditions.
Choosing the right materials is crucial in industries where components face different mechanical and thermal challenges. I often rely on standards and data to make decisions, considering factors such as expected load, environmental conditions, and desired service life.
Higher hardness improves wear resistance in materials.True
Hardness increases a material's ability to resist abrasion, enhancing wear resistance.
High hardness always ensures better toughness in materials.False
While hardness improves wear resistance, it must be balanced with toughness to prevent cracking.
How Does Toughness Affect Impact Resistance in Molds?
Have you ever wondered why some molds survive longer than others, even in difficult conditions? Toughness plays a crucial role. It helps absorb energy and stop damage. This is very important. Let’s explore why.
The toughness of molds helps them resist impact by absorbing shocks. This prevents cracks from forming. Mold durability is very important during fast processes such as injection molding. Tough molds last a long time. Integrity of the mold stays intact. This quality really extends the mold’s lifespan.
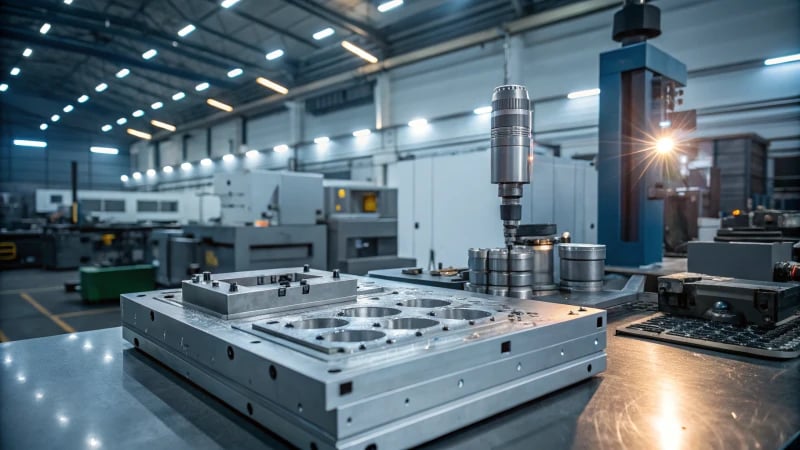
The Role of Toughness in Mold Design
I remember my first mold design for a fast injection process. I thought everything was perfect until I noticed tiny cracks appearing after a few cycles. This taught me the importance of toughness. It’s not just about withstanding impacts; it’s about bending without breaking.
Absorbing Impact Energy
Imagine the mold opening and closing hundreds of times daily. Tough materials absorb all that energy, like a sponge soaks up water. This prevents sudden fractures during rapid moves or unexpected hits.
Example Table: Toughness vs. Impact Resistance | Material Type | Toughness Level | Impact Resistance |
---|---|---|---|
Standard Steel | Moderate | Medium | |
Toughened Steel | High | High | |
Composite Materials | Very High | Very High |
Preventing Mold Damage
Think about a tiny piece of debris getting caught in your mold during a crucial run. A tough material withstands these sudden shocks, keeping the mold intact and prolonging its life.
Factors Influencing Toughness
Over time, I discovered that several factors affect material toughness:
- Material Composition: Like cooking, different ingredients create different results. Adding things like nickel and chromium to steel improves its ability to handle impacts.
- Heat Treatment: It’s like a spa day for metals, strengthening them to endure quick operations without cracking.
- Microstructure: The small details inside the material matter, like grain size. Fine grains spread impact energy more effectively.
To understand these elements better, you might want to explore material science studies4 in metallurgical engineering.
Practical Applications in Industry
In my experience, tough materials for molds in high-speed injection machines are like reliable cars. You spend less time fixing and more time running smoothly. They maintain top quality even with constant use, preserving the mold’s shape.
Markdown Example:
- Point 1: Proper heat treatment strengthens toughness.
- Point 2: Microstructure greatly affects impact resistance.
For more on how different materials perform in toughness, check out industry case studies5. These insights may help choose the right material for your specific needs, balancing quality with efficiency.
Toughness prevents mold fractures during rapid operations.True
High toughness absorbs kinetic energy, reducing fracture risk in molds.
Microstructure does not affect impact resistance of molds.False
Microstructure influences energy distribution, affecting toughness and resistance.
Why Is Deformation Resistance Critical for Mold Longevity?
Do you ever think about why some molds last a really long time while others stop so quickly?
Resistance to deformation is very important for the life of a mold. This is because it keeps the mold’s structure strong under high pressure. It really reduces damage and helps keep precision for a long time.
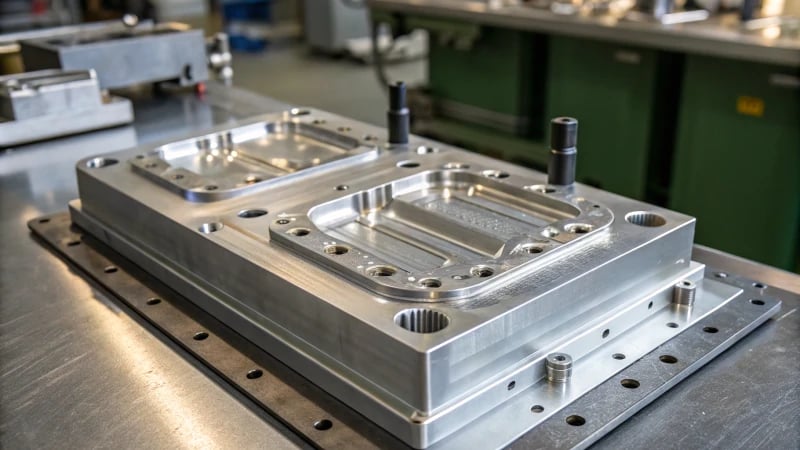
The Role of Hardness in Deformation Resistance
I remember my early days in the mold industry. I stood in awe of the gigantic machines that seemed to bring plastic products to life. One thing became clear quickly: harder mold steel resists deformation better. During injection molding, the mold faces high pressures, which might cause unwanted elastic deformation if the steel is too soft. Imagine trying to mold large, thick-walled products; high injection pressure could permanently bend a softer steel mold, leading to expensive mistakes and inaccuracies.
Table 1: Hardness Impact on Mold Deformation
Steel Type | Hardness (HRC) | Deformation Rate |
---|---|---|
H13 | 48-52 | Low |
Standard | 35-40 | Medium |
This really shows why high-hardness steel6, like H13, is essential for keeping mold cavities stable under pressure. Using high-hardness steel is very important for stability.
Toughness and Its Contribution to Longevity
But there’s a catch: hardness alone is not enough. Toughness plays a huge role too. During rapid mold openings and closings, the mold experiences big impacts. If the steel lacks toughness, you risk cracks and eventual mold failure. I learned this lesson when molds cracked under pressure from a high-speed machine—it was costly.
Table 2: Toughness Impact on Fatigue Resistance
Steel Type | Toughness Level | Fatigue Resistance |
---|---|---|
Premium | High | Excellent |
Standard | Medium | Fair |
Toughness must never be overlooked during rapid mold opening and closing7. Maybe toughness is more important than we think.
Fatigue Resistance and Thermal Cycles
Another challenge is fatigue resistance. Injection molds endure countless thermal cycles. Without high toughness, fatigue cracks appear easily. I have seen hot work molds suffer from surface fatigue cracks because the steel couldn’t handle stress from repeated temperature changes—it happens all the time.
Choosing high-toughness steels8 is vital as it maintains mold integrity across many cycles and extends their service life—really, it makes a huge difference.
Conclusion
Balancing hardness and toughness in mold steels is crucial; it’s not just a technical necessity but also a cornerstone of better mold longevity9. Improving deformation resistance while reducing wear and fatigue ensures efficient production and cost savings over time. From my experience, investing in the right materials upfront saves countless headaches later—using the right materials may change everything.
High hardness steel resists mold deformation.True
High hardness in steel, like H13, reduces deformation under pressure.
Low toughness increases mold crack risk.True
Low toughness leads to crack propagation during rapid mold operations.
How Can Steel Selection Optimize Mold Life?
When I first started learning about mold design, choosing the right steel seemed like a very difficult puzzle. But over time, I understood it is the key to making the mold last longer. Really, it’s essential to mold durability.
Steel choices for mold life are about balancing between hardness and toughness. Hard materials help resist wear. Tough materials stop cracks during mold use.
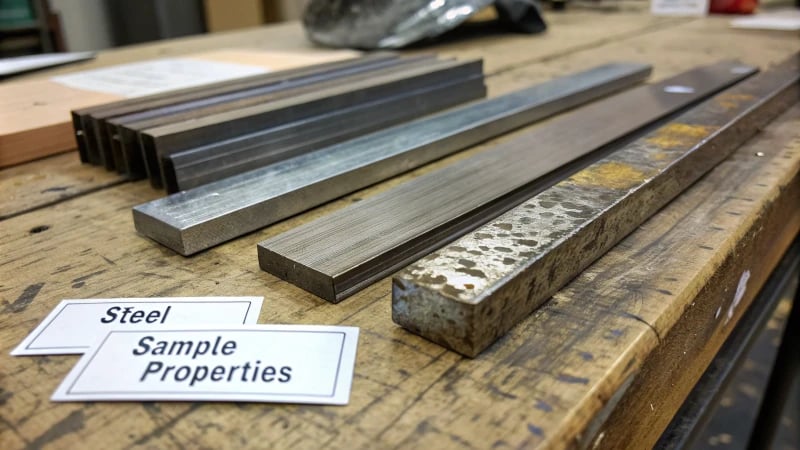
Understanding Hardness in Mold Steel
That feeling of crafting a perfect mold is unmatched. Success often depends on the hardness of the steel. Hard steel has high wear resistance10. This feature is essential for handling abrasive plastic melts, especially those with gritty fillers like glass fibers. Think of it as a powerful shield that protects the mold cavity from changing shape.
Steel Type | Typical Hardness (HRC) |
---|---|
H13 | 48-52 |
P20 | 28-32 |
My experience taught me that higher hardness steels like post heat-treated H13 change everything. They reduce wear during demolding, and scratches on the mold surface decrease, extending the life of the mold.
The Role of Toughness in Mold Longevity
I have seen molds survive countless cycles on fast machines. Toughness is very important as it absorbs impact during quick mold operations, preventing major failures like fractures.
Impact Resistance
I remember when high pressure almost ruined a project. Thankfully, choosing tough steel saved the project by preventing cracks under stress.
Scenario | Steel Response |
---|---|
Rapid Mold Closure | Absorbs impact without cracking |
Sudden Pressure Increase | Maintains structural integrity |
Balancing Hardness and Toughness
Balancing hardness and toughness is tricky. I have spent hours studying mold environments to find a point where steel is hard enough to resist wear and tough enough for impacts. This balance helps molds last longer, lowers maintenance costs, and keeps production lines moving smoothly. Finding the right balance fits specific molding needs; it’s not just about choosing the hardest steel but achieving sustained efficiency11 over time.
H13 steel is harder than P20 steel.True
H13 has a hardness of 48-52 HRC, while P20 has 28-32 HRC.
Higher hardness reduces mold surface damage.True
High hardness withstands abrasives, maintaining mold precision.
Conclusion
Hardness and toughness in mold steel significantly influence injection mold longevity by enhancing wear resistance, impact absorption, and deformation stability, ultimately ensuring efficient production and reduced maintenance costs.
-
Learn how increased hardness reduces wear in injection molds by resisting abrasion from plastic melts. ↩
-
Understand why selecting mold steels with optimal hardness is critical for maintaining shape under pressure. ↩
-
Discover how balancing these properties enhances material performance in demanding environments. ↩
-
Learn about advanced studies that explore the relationship between toughness and impact resistance. ↩
-
Discover real-world examples of material selection based on toughness for various industrial applications. ↩
-
Clicking this link will provide detailed insights into how hardness affects deformation resistance in mold steel. ↩
-
Explore this link to understand how toughness contributes to mold durability and resistance to impacts. ↩
-
Discover practical strategies for enhancing mold longevity through improved material properties and design. ↩
-
Discover practical strategies for enhancing mold longevity through improved material properties and design. ↩
-
Explore how hardness enhances wear resistance and preserves mold precision. ↩
-
Discover how balanced steel properties ensure long-term efficiency. ↩