Injection molding resembles a precise dance. Every step matters. I found out that the gate’s size and length often guide the entire process.
The gate’s size and length in injection molding are vital. These factors influence plastic melt flow, pressure, temperature and solidification. Flow control affects mold fill. Mold fill influences finished product appearance. Product appearance and quality matter. Internal quality matters too.
When I first worked with molds, I was amazed at how small changes could create big differences. This understanding is only the start. The interaction between gate sizes, materials and mold designs really matters. Big benefits arise from this. Let us explore some strategies and important factors to achieve the best results with your gate sizes.
Gate size affects the flow rate in injection molding.True
Larger gates allow higher flow rates, impacting mold filling efficiency.
Longer gates reduce pressure in injection molding.False
Longer gates increase resistance, requiring more pressure to fill molds.
Why is Gate Size Crucial for Product Quality?
Have you ever thought about how a tiny gate really affects a product’s quality?
Gate size affects product quality. It influences how well materials fill, how they look and the stress inside them. Correct gate size leads to even filling. It gives better surface quality and reduces stress in molded parts. Correct gate size is very important.
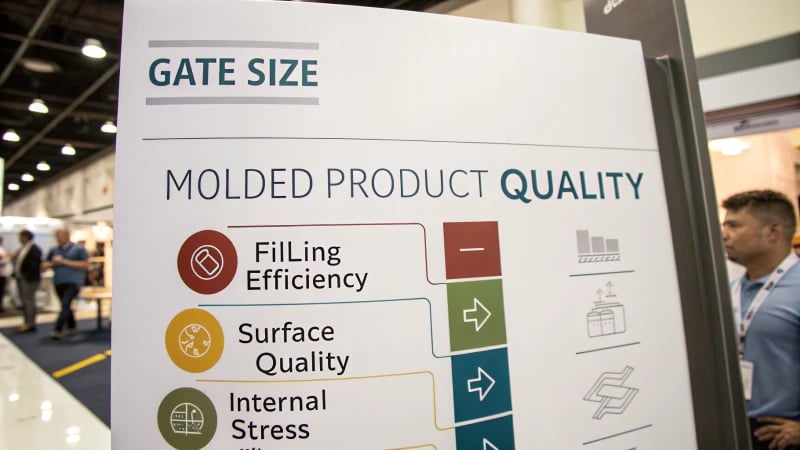
Influence on Filling Efficiency
Gate size directly impacts the filling efficiency during the injection molding process. A larger gate, such as 4-6mm wide, lets the melt flow smoothly into the mold, beneficial for large or complex structures like a car dashboard. Every corner fills up well, resulting in fewer defects and a smoother process. Conversely, when working with electronic parts with tiny gates under 0.5mm, limited melt flow can lead to issues similar to squeezing ketchup out of a tiny opening—it doesn’t work well.
Effect on Appearance Quality
Think about the last time you bought something because it looked perfect. This is the same idea. A moderate gate size ensures that the melt enters gently, reducing unwanted marks like flow or weld lines. For clear plastic items, using a fan-shaped gate of appropriate size helps spread the surface evenly and creates a smooth finish. However, an overly large gate can cause problems by leaving spray marks on thin parts.
Gate Size | Effect on Appearance |
---|---|
Moderate | Smooth surfaces |
Too Large | Spray marks |
Internal Stress and Quality
In one early project with polycarbonate, I learned about internal stress and its effect on product strength. Larger gates lower shear rates at the gate, reducing stress and heat generation—keeping products strong and stable. Tiny gates increase shear rates which can warp or crack items; it’s like pulling a rubber band too much—it might snap back.
Considerations for Gate Length
Length is important too! Longer gates increase pressure loss due to longer flow paths, causing temperature drops similar to running in a long narrow hallway—you feel resistance just as the melt does. For thin or long items, this creates filling issues as longer gates also mean more solidification time and waste.
In summary, balancing gate size and length is essential for optimizing both aesthetic appeal and structural quality of molded products.
A larger gate size improves filling efficiency.True
Larger gates allow more melt flow, aiding in even cavity filling.
Smaller gates reduce internal stress in molded products.False
Smaller gates increase shear rates, leading to higher internal stress.
How Does Gate Length Influence Mold Efficiency?
Have you ever thought about how the length of a gate in injection molding affects your product’s efficiency?
Gate length impacts mold efficiency. It changes pressure loss, temperature drop and solidification time. Longer gates create more resistance. This results in pressure drops. Cooling problems likely occur. Shorter gates allow better flow. They really cut down on waste.
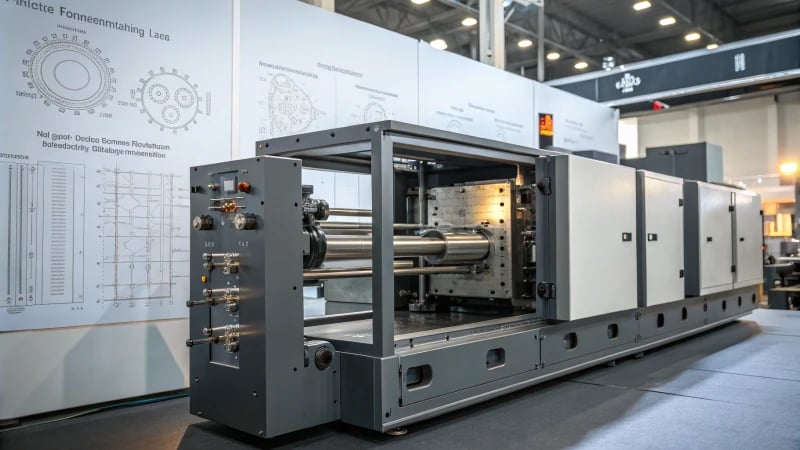
Pressure Loss and Temperature Drop
At the start of my journey into mold design, simple things like gate length amazed me. Gate length affects how the melt moves. Longer gates create more resistance, causing pressure to drop. Imagine squeezing honey through a long straw; it struggles to get through. This pressure drop often results in unfilled thin or detailed parts. Pressure is vital.
Simultaneously, temperature drop also matters. Heat-sensitive plastics remind me of its importance. As the melt slides along long gates, it cools too much. A very long gate makes the melt sluggish, like a cold morning. This is not good when you need smooth flow.
Gate Length | Pressure Loss Impact | Temperature Drop Impact |
---|---|---|
Short | Minimal | Minimal |
Long | Significant | Significant |
Solidification Time and Waste Generation
In my early projects, gate length taught me about timing issues. Longer gates slow solidification, extending the cycle and increasing waste. It’s like baking a cake in a slow oven; more time and leftover batter. Once, a small product had so much gate waste, it felt like we discarded most of it.
Shorter gates change the game. They let the melt flow quickly, reducing solidification time and waste. Picture speeding up production, like fast-forwarding a movie.
- Example: For a small part, a long gate almost doubled gate waste.
- Efficiency Tip: Adjust gate length to speed up production and lower waste.
Analyzing Gate Length in Mold Design
What to take from this? Knowing gate length involves balancing product needs and material traits. I once worked on a complex shape where a longer gate helped spread the melt evenly but increased waste—there is always a trade-off.
Factors to Consider:
- Product Complexity: Difficult designs might need longer gates for even filling.
- Material Sensitivity: Temperature-sensitive materials? Choose shorter gates for smoother flow.
Discover more about better gate designs1 by exploring case studies and expert advice on tuning these aspects for efficient mold designs.
Longer gates increase pressure loss in molds.True
Longer gates cause increased resistance, leading to higher pressure loss.
Shorter gates result in more material waste.False
Shorter gates reduce gate waste by minimizing solidification time.
How Do Gate Dimensions Affect Material Properties?
Think about the last time you put together a jigsaw puzzle. Gate sizes in injection molding work in a similar way, fitting all parts just right for the end product.
Gate size affects material traits by changing flow speed, shear force and cooling duration during injection molding. Correct gate sizing improves filling speed, looks and internal stress control. This action optimizes product efficiency. Gate dimensions are very important.
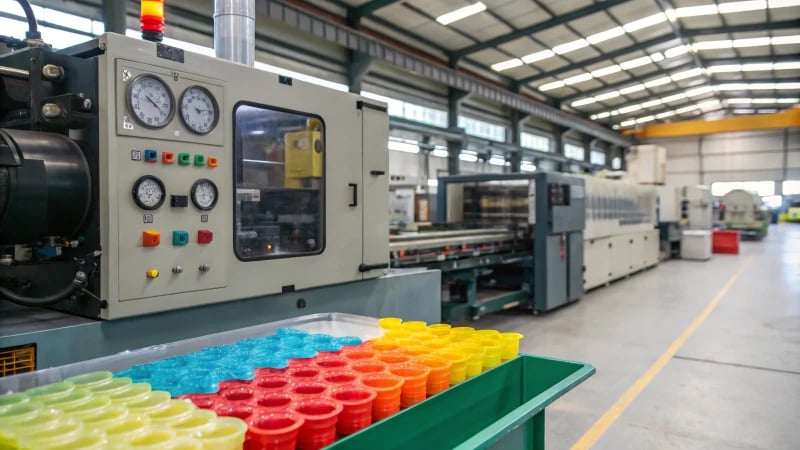
The Role of Gate Size
I remember the first time I chose the right gate size for a project. It felt like finding the last piece of a difficult puzzle. Gate diameter, width, and thickness are more than just numbers. These hidden champions help the plastic flow smoothly into the mold.
Think of a large gate as a wide opening letting creativity flow. It fits big or detailed structures like car dashboard covers. This entry lets the plastic fill quickly and evenly, preventing problems with incomplete filling. From experience, small gates feel like pushing a river through a straw. It’s slow and leaves parts unfilled. This can be troublesome in precision electronics where accuracy is vital.
Appearance and Internal Quality
Looks matter in molding! A well-sized gate makes melt flow without leaving ugly marks. I learned this when using a fan-shaped gate for clear plastic. The result was a super smooth and clear surface, almost like a mirror.
Inside the product, gate size affects stress. Larger gates lower shear rates and orientation, especially for sensitive materials like polycarbonate. This balancing act improves strength and stability, keeping the product strong under pressure.
Gate Size | Effect on Filling | Effect on Appearance | Effect on Internal Quality |
---|---|---|---|
Large | Efficient filling | Reduces surface defects | Low shear stress |
Small | Potential short shots | Increased defects | High shear stress |
The Influence of Gate Length
Gate length deserves attention. Imagine the melt running through a long gate. Longer gates cause pressure loss and temperature drops. I’ve observed that gates longer than 10mm can struggle to fill thin products well.
Longer gates cool and harden slowly, extending production and causing waste. Shorter gates work faster, reducing cooling time and waste – a real advantage.
For deeper understanding of gate length effects2, analyze how these impact your design in practice. Grasping these details helps improve molding processes.
Practical Considerations for Designers
- Use simulations to see how gate sizes change material traits.
- Choose gate sizes based on material and product needs.
- Try different gate designs3 in prototypes to find the best fit.
Applying these steps guides you in balancing efficiency and quality in molding. Use this wisdom to improve designs and achieve better results in projects.
Larger gates reduce shear stress in injection molding.True
Larger gates decrease shear rates, reducing molecular orientation and stress.
Smaller gates always enhance the appearance of molded products.False
Smaller gates can increase defects like flow marks due to restricted flow.
How Does Gate Design Affect Production Costs?
Do you ever think about how the size and form of a gate might change production costs when molding?
Gate design impacts production costs through material flow, cycle time and product quality. Bigger gates help flow but might waste materials. Ideal lengths balance efficiency and cut down on waste.
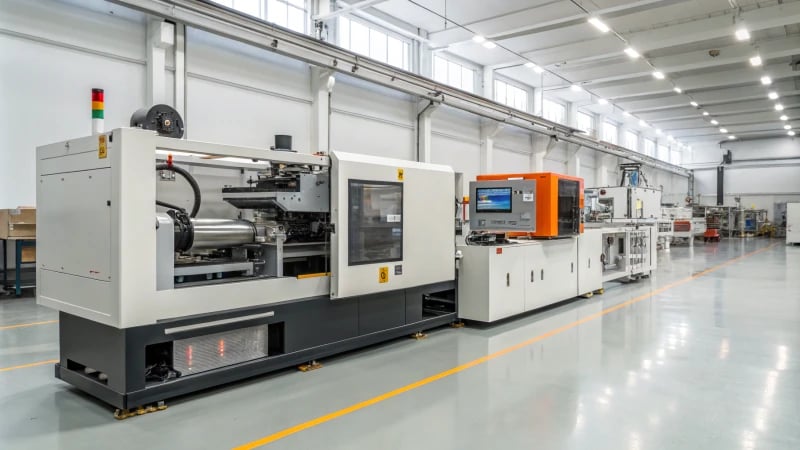
The Role of Gate Size in Cost Management
Imagine filling a big bucket with water using a hose. A wider hose lets you fill it faster. Larger gates in molding work this way too. When designing car dashboard covers, a bigger side gate was necessary. It allowed the melt to fill the mold quickly and evenly. This process is like fitting puzzle pieces together perfectly to prevent defects.
Gate Size | Application Example | Benefit |
---|---|---|
Large | Automobile dashboards | Faster filling |
Small | Precision electronics | Reduced defects |
But, like too much water spills over, a too-large gate might waste material and cause unwanted marks. With thin-walled products, I noticed big gates left spray marks4. Fixing these took a lot of effort.
Importance of Gate Length
Gate length is like a long walk where you tire halfway. In molding, longer gates mean the melt travels more, losing pressure and heat. Thin-walled products taught me this usually results in lower temperatures and affects fluidity.
Gate Length | Pressure Impact | Temperature Impact |
---|---|---|
Long | Increased loss | Significant drop |
Short | Reduced loss | Minimal drop |
Long gates also take longer to harden, much like waiting patiently for ketchup to ooze out. Short gates help minimize waste and shorten solidification time5.
Balancing Quality and Cost
Finding the right balance between quality and cost is crucial. Well-sized gates allow stable melt entry, enhancing both look and internal quality. When working with clear products, a fan-shaped gate reduced flow marks greatly.
However, small gates can raise shear rates, increasing internal stress and risks like warping. Materials like polycarbonate need stable dimensions, making this balance tricky.
For materials sensitive to internal stress such as polycarbonate (PC), selecting the right gate size is crucial for maintaining dimensional stability6 and mechanical properties.
In my manufacturing journey, I learned gate design optimization isn’t just about cutting costs – it’s about reaching top quality too. Considering gate sizes can mean less waste and faster production cycles while still achieving excellent results.
Larger gates reduce production costs.False
Larger gates may increase material usage, raising production costs.
Shorter gates minimize waste in injection molding.True
Shorter gates reduce solidification time and waste, enhancing efficiency.
Conclusion
Gate size and length in injection molding significantly impact flow efficiency, product appearance, internal quality, and production costs, making their optimization crucial for high-quality molded products.
-
Gain insights from real-world examples of effective gate design strategies. ↩
-
Learn how varying gate lengths can impact pressure and temperature during molding. ↩
-
Explore different gate designs to find configurations that suit your project needs. ↩
-
Learn how spray marks form during injection molding and how to prevent them. ↩
-
Explore why managing solidification time is crucial for reducing production costs. ↩
-
Find strategies to ensure dimensional stability in molded products sensitive to stress. ↩