Have you ever thought about how a small gate design might change the whole injection molding process?
Gate design affects the injection molding process. It influences main factors like pressure, speed and time. The size, position and number of gates decide how the melted material moves. This also affects how well the material fills the mold.
In my years working with mold designs, I noticed how important gate design is. I remember adjusting a design for the first time. Changing the gate size and position improved efficiency a lot. It felt like finding a puzzle’s missing piece. Let’s now look into these details more and see how they really improve the molding process.
Each part of gate design affects the molding process greatly. Gate size changes the injection pressure and speed needed to fill the mold properly. Putting the gate in the right place lowers unwanted pressure changes and weld marks. The number of gates also matters. It affects how quickly and evenly a mold fills. Knowing these small details is key. Mastering them really improves both the quality and speed of manufacturing processes.
Gate design affects injection pressure in molding.True
Different gate designs alter flow dynamics, impacting required pressure.
The number of gates has no effect on mold filling speed.False
Multiple gates can enhance or reduce filling speed by altering flow paths.
What Is the Role of Gate Size in Injection Molding?
Have you ever thought about how the gate size in injection molding helps create the ideal product?
Gate size in injection molding is crucial for controlling the flow of molten material. A larger gate lets the material flow smoothly with less force. This lowers the chance of defects. A smaller gate increases pressure. This raises the risk of imperfections.
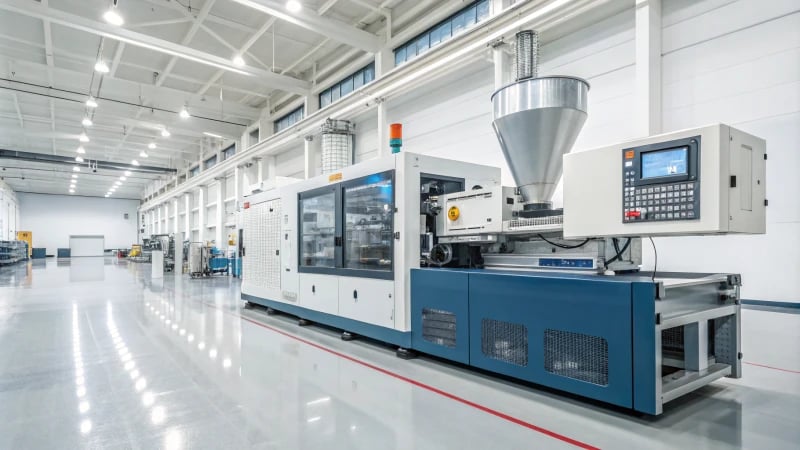
Understanding Injection Pressure
I remember learning about gate size’s effect on injection pressure1. On a project, a small gate choice led to unexpected defects. The melt had difficulty passing through, causing pressure to rise sharply, which slightly deformed the product. However, a larger gate let the melt flow smoothly, lowering injection pressure significantly and avoiding potential issues.
Gate Size | Injection Pressure | Potential Defects |
---|---|---|
Large | Low | Minimal |
Small | High | Deformation |
Controlling Injection Speed
Gate size really affects injection speed2 decisions. Picture this: one time, a large gate allowed the melt to flow faster without causing defects. But with a small gate, I had to slow it down to avoid flow marks on the product’s surface.
Managing Pressure Holding
The pressure holding phase was also greatly influenced by gate size. Once, I realized a large gate helped refill melt volume during cooling, which meant less shrinkage and improved product quality. But with a small gate, greater pressure loss brought difficulties.
Gate Size | Pressure Holding Efficiency | Shrinkage Reduction |
---|---|---|
Large | High | Yes |
Small | Low | No |
Learning these factors was eye-opening. It helped in optimizing mold design and achieving top product quality. Curious about gate position3 in molding? Dive into details like changing injection speed and managing weld marks for stronger and better-looking products.
Larger gates decrease injection pressure in molding.True
Larger gates reduce resistance, lowering the required pressure for melt entry.
Smaller gates reduce shrinkage during pressure holding.False
Smaller gates increase pressure loss, reducing melt replenishment and increasing shrinkage.
How Does Gate Position Affect Product Quality?
Ever curious how placing the gate correctly in injection molding might change a product’s quality from average to outstanding?
Gate location in injection molding plays a big role in shaping product quality. It changes the melt flow path. It affects the pressure needed. It really influences defect formation. Proper gate placement lowers pressure demands. It also reduces defects such as weld marks.
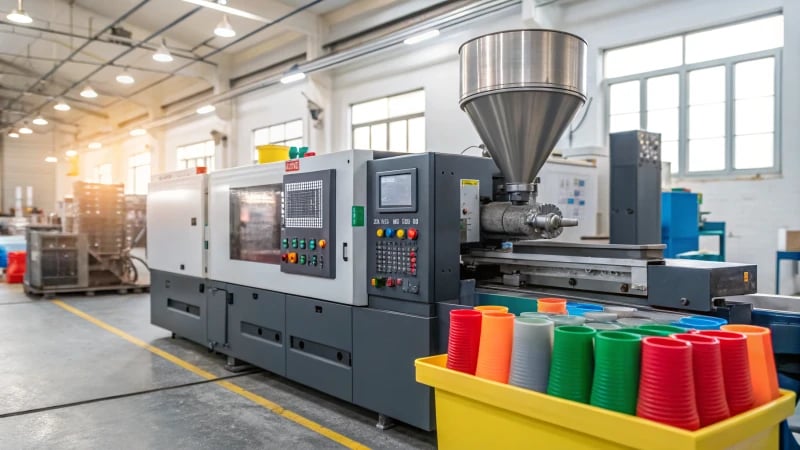
Influence of Gate Position on Injection Pressure
I have worked in mold design for over ten years. Gate position is crucial for injection molding. Once, we molded a complex piece with detailed designs. Initially, we placed the gate at the cavity’s edge. This caused high injection pressure due to long flow paths, putting stress on equipment. Moving the gate to the center lowered the pressure. Life became much easier.
The gate position directly impacts the flow path length of the melt. When centrally located, the melt diffuses with minimal injection pressure. Conversely, off-center gates require higher pressure due to extended flow paths.
Impact on Injection Speed and Weld Marks
Getting gate position right is an art. I once designed a product with different wall thicknesses. We positioned the gate poorly, leading to ugly weld marks—an early career mistake of mine. By moving the gate closer to thicker sections, we achieved smoother flow and eliminated weld marks.
Proper gate positioning ensures consistent melt flow across varying wall thicknesses:
Gate Position | Effect on Weld Marks |
---|---|
Near holes/ribs | Reduces weld marks |
Long flow paths | Increases weld marks |
To learn more about weld marks4, explore how they affect mold design.
Relation to Injection Speed
Gate position affects how fast the melt travels. On a thin-walled project, a misplaced gate led to quick ejection and defects; I learned that slower can be better.
Gate position dictates the melt’s flow direction and velocity:
- Gates in thin sections may cause quick ejection, needing reduced speed.
- Thicker areas allow higher speeds without defects.
Investigating injection speed5 effects can enhance your understanding of its importance in reducing product defects and ensuring quality control.
Number of Gates and Their Impact
Adding more gates might seem simple but creates challenges. In a large flat panel project, we used multiple gates; pressure reduced and production sped up but too many gates increased weld marks.
Adding gates can reduce injection pressure by shortening flow paths:
- Multiple gates allow flexible speed settings as melt disperses across cavities.
- However, excess gates might cause weld marks.
Consider exploring gate number6 implications for optimal distribution in complex molds.
Understanding these details helps me create better mold designs by reducing defects like flow marks and shrinkage—it’s about finding balance where design meets function. Mold design is always evolving.
Centrally located gates reduce injection pressure.True
Centrally located gates minimize flow path length, reducing injection pressure.
Multiple gates always reduce weld marks.False
Excessive gates can cause weld marks due to improper melt flow distribution.
Why Is the Number of Gates Important in Mold Design?
Have you ever thought about why the number of gates in mold design matters so much? Mold crafting holds the secret. This factor shapes the whole injection molding process.
The number of gates in mold design influences flow path, injection pressure, speed and time. More gates often reduce pressure and decrease time. However, they might also lead to more weld marks. These marks really affect the quality of the product. Quality might suffer due to these marks.
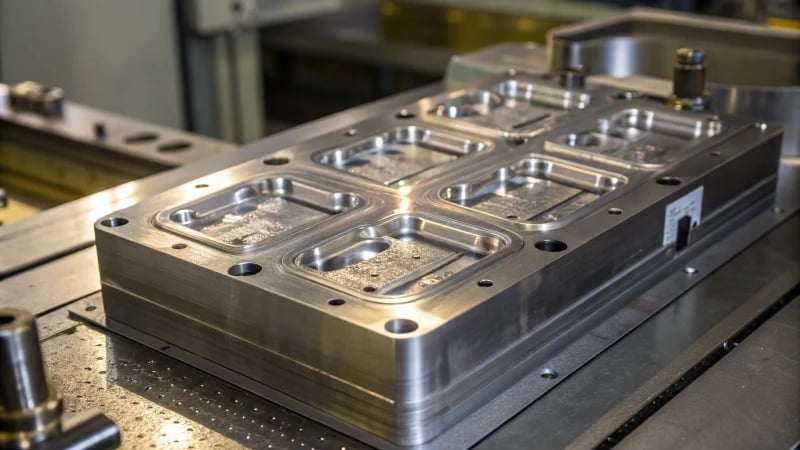
Influence on Injection Pressure
I remember a project with a big flat product. We had issues with pressure spreading evenly. Using several gates changed everything. It really cut down the pressure needed by giving the melt a shorter path, which was very important for filling each cavity well. For molds with many cavities, this way fills them all at once, easing the burden on any single gate.
Consider watering your garden: using many hoses instead of one spreads the work and makes it easier and faster.
Number of Gates | Pressure Required |
---|---|
Single | High |
Multiple | Low |
Impact on Injection Speed
In another project, I realized that more gates offered more control with injection speed7. Melt moving from several directions lowers the risk of quick, uneven flow, letting us go faster without losing quality.
But it comes with challenges. Too many gates might bring too many meeting points in the cavity, raising the chance of weld marks. Finding the right balance is key – like baking, too many ingredients can ruin the flavor.
Effect on Injection Time
More gates meant filling the cavity faster, which was a real help for complex designs. The melt reached every corner quickly, speeding up production. Yet, it needed careful planning to avoid weld marks and poor quality looks.
Learning these details, we thoughtfully pick the number of gates to boost efficiency and keep product quality high. If you’re curious about how gate positioning8 affects these factors, think about looking into how it helps achieve perfect mold design.
More gates reduce injection pressure.True
Multiple gates shorten the flow path, reducing the required pressure.
Multiple gates increase injection time.False
More gates decrease injection time by filling cavities quicker.
How can gate design reduce injection molding defects?
Curious about how a simple gate design transforms your injection molding process? The right choices in gate size, position and number dramatically upgrade product quality. Fewer defects result. The right gate decisions bring very noticeable changes.
Gate design in injection molding greatly cuts down on defects by improving how the molten material flows. The right gate size, position and quantity help with filling. This decision lowers pressure and reduces weld marks. Better quality products result from this method. Truly, better quality.
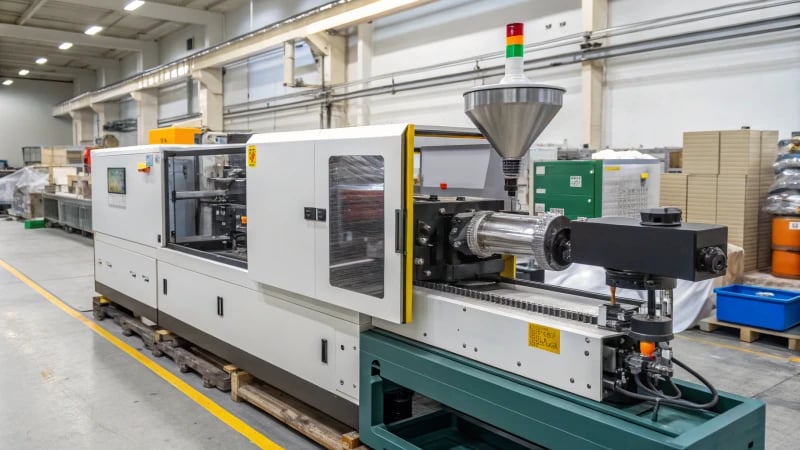
The Role of Gate Size
I remember my first challenge with choosing the right gate size for a complex electronic part. The stakes were high. Too small a gate risked damage from too much pressure. A larger gate allowed the melt to flow smoothly into the cavity, reducing injection pressure9 and improving flow. This change really transformed things. It helped the product meet both looks and function.
Gate Size | Impact on Injection Pressure | Impact on Injection Speed |
---|---|---|
Large | Lower pressure needed | Higher speed allowed |
Small | Higher pressure needed | Lower speed required |
Impact on Injection Speed
Once, I worked on a project with delicate surface finishes. I noticed that a larger gate controlled higher injection speeds without losing quality. It taught me about balance. Smaller gates needed careful speed control to avoid bad flow marks.
Strategic Gate Positioning
Positioning the gate in the center was like finding a perfect match in a puzzle. It shortened the melt’s path, needing less pressure. I saw how off-center gates created more problems, increasing pressure requirements10.
Influence on Weld Marks
There was one time when placing the gate near structural features like ribs really made a difference. It reduced weld marks a lot, improving the product’s appearance11 and strength.
Number of Gates: A Balancing Act
To reduce pressure, adding more gates seemed like an easy fix, but it had downsides. Multiple gates created points where materials met, causing unwanted weld marks sometimes. Finding that perfect balance was important.
Number of Gates | Effect on Injection Pressure | Potential Issues |
---|---|---|
Single | Higher pressure | Uniform flow needed |
Multiple | Lower pressure | Increased weld marks |
By carefully choosing gate design—thinking about size, position, and number—I learned it’s possible to cut down on injection molding defects significantly. These smart choices not only lift product quality but promote consistency by improving melt flow and really minimizing common defects12.
Larger gates reduce injection pressure in molding.True
Larger gates allow smoother melt flow, decreasing required injection pressure.
Multiple gates always reduce weld marks.False
Multiple gates can introduce convergence points, increasing weld marks.
Conclusion
Gate design significantly influences injection molding parameters, affecting pressure, speed, and quality. Proper gate size, position, and number enhance material flow and reduce defects in molded products.
-
Learn how different gate sizes impact the required injection pressure, affecting overall product quality. ↩
-
Discover how varying gate sizes alter the flow rate and speed during injection molding. ↩
-
Understand how positioning gates differently can influence the molding process and final product outcomes. ↩
-
Understanding weld marks helps in designing molds that minimize defects, improving product aesthetics and strength. ↩
-
This link explores how controlling injection speed reduces defects, ensuring high-quality products. ↩
-
Learn how the number of gates affects mold efficiency and product quality by optimizing flow paths. ↩
-
This link explains how gate numbers allow flexibility in injection speed, optimizing production. ↩
-
Learn how strategic gate placement can further refine injection processes. ↩
-
Explore how gate size influences injection pressure requirements in molding processes. ↩
-
Explore how gate size influences injection pressure requirements in molding processes. ↩
-
Learn how strategic gate positioning can improve product appearance by reducing weld marks. ↩
-
Discover which injection molding defects can be minimized through effective gate design. ↩