I remember my first encounter with gas marks in injection molding and the frustration it brought.
Gas marks in injection molding, caused by trapped gases, can harm both aesthetics and structural integrity. Effective venting and optimizing the process are crucial to preventing these defects.
To effectively tackle gas mark issues, I’ve learned it’s important to delve deeper into their causes and explore solutions that address these challenges. By understanding how these marks form and implementing best practices, manufacturers can achieve superior product quality. Sharing these insights has become a personal mission of mine, helping others avoid the same pitfalls I once faced.
Gas marks only affect the aesthetic of molded parts.False
Gas marks also compromise structural integrity, not just aesthetics.
Effective venting can prevent gas marks in injection molding.True
Proper venting allows trapped gases to escape, preventing blemishes.
Why do gas marks affect product quality?
Ever had a project go south because of those pesky gas marks? I’ve been there, and it’s no picnic! Let’s dive into why these little devils are a big deal in injection molding and how we can tackle them.
Gas marks in injection molding result from trapped air or gases, causing surface flaws and weakened strength. Addressing this requires adjustments in mold designs and processing settings.
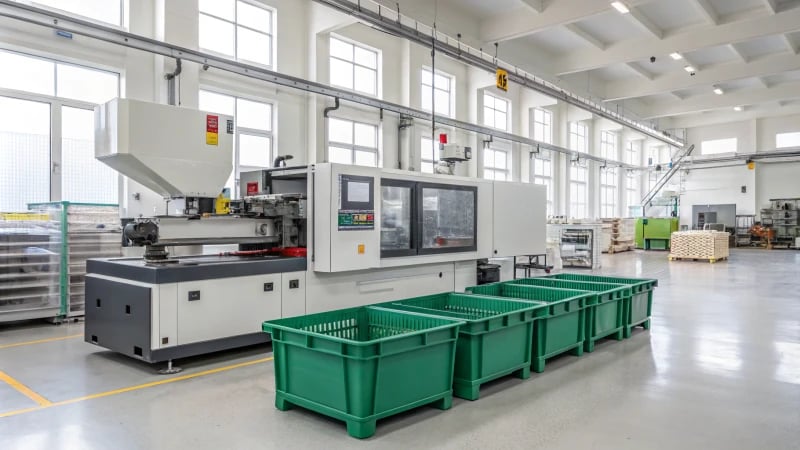
Understanding Gas Marks in Injection Molding
Imagine this: you’re finally holding the molded piece you designed, only to notice unsightly blemishes on its surface. It’s like finding out your favorite dessert has gone bad. That’s what gas marks do—they appear when gases or air bubbles are trapped during the injection molding process1. These marks are more than just an eyesore; they can weaken parts of the product, compromising its overall strength.
Causes of Gas Marks
I remember the first time I encountered gas marks. I was baffled, wondering how something so small could cause such a big problem. Turns out, there are several culprits:
- Material Degradation: Overheating polymers can break them down, releasing gases.
- Poor Venting: If molds aren’t vented properly, gases get trapped.
- High Injection Speed: Fast injection traps air in the mold cavity.
Effects on Product Quality
When I first saw a gas mark, it reminded me of a time I bought a shiny new gadget only to find a dent on it. Gas marks can do that to your products. They’re not just ugly; they weaken the product, making it prone to damage. In consumer electronics, these marks can be a deal-breaker, leading customers to return items.
Issue | Effect on Product |
---|---|
Surface Imperfection | Reduced aesthetic appeal |
Weak Points | Increased risk of mechanical failure |
Customer Perception | Negative impact on brand image |
Mitigating Gas Marks
So, how do we tackle these gas mark gremlins? I’ve found success with a few strategies:
- Optimizing Mold Design: Adding proper venting channels can help.
- Adjusting Processing Parameters: Slowing down the injection speed or reducing temperatures can curb gas formation.
- Material Selection: Picking polymers that don’t degrade easily helps minimize gas release.
Each project is unique, and understanding its specifics is crucial. I often turn to simulation tools2 and design experts to anticipate and solve these issues before they start.
Insights from Industry Experts
Experts like Jacky remind me of the balancing act between making a product look good and ensuring it functions well. The challenge is using modern techniques like advanced CAD systems3 to predict and eliminate defects during the design phase, which ultimately results in smoother production and top-notch product quality.
Gas marks only affect the aesthetics of products.False
Gas marks also compromise mechanical integrity, not just aesthetics.
High injection speed can cause gas marks in molding.True
Rapid injection traps air, leading to gas mark formation.
How Can Venting Techniques Help Reduce Gas Marks?
Ever watched a seemingly perfect mold turn out imperfect due to pesky gas marks? There’s a way to tackle this with finesse!
Venting techniques in injection molding use channels to release trapped gases, reducing defects like gas marks and burn marks, resulting in smoother finishes on molded products.
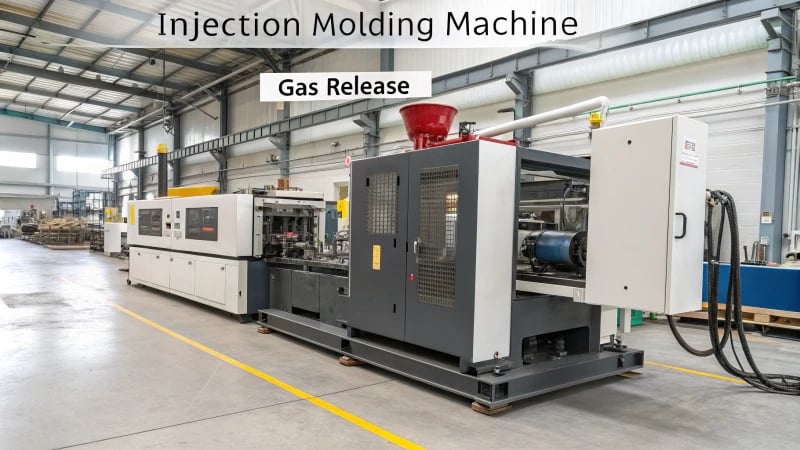
The Role of Venting in Injection Molding
Imagine the frustration of completing a meticulous design only to find those dreaded gas marks. It reminds me of a project early in my career when I faced this exact issue. I learned then that venting techniques4 are key in injection molding, letting gases escape during the process to prevent surface flaws like gas marks and burn marks.
Key Techniques for Effective Venting
-
Vent Size and Placement: One of the first lessons I learned was about vent size and placement. It’s like baking – too much or too little of anything can spoil the outcome. Oversized vents might cause flash, while undersized ones leave gas trapped, leading to imperfections.
-
Vent Design: Using micro vents or adding vent inserts can efficiently manage gas flow. It was as if I had discovered a secret ingredient that ensured a smooth surface finish, just as a well-chosen spice can transform a dish.
Designing Efficient Vents
When it came to designing vents, I realized the process was as meticulous as crafting the perfect piece of furniture. You have to think about:
Design Aspect | Consideration |
---|---|
Thickness | Should be thin to allow gas escape but prevent material flow. |
Location | Positioned at points of expected gas accumulation. |
Material | Heat-resistant materials prevent degradation during the process. |
Benefits of Adequate Venting
Understanding venting transformed my work in the same way a great mentor can shape a career. Proper venting not only improved the surface quality but also reduced cycle times and increased mold longevity. This technique felt like finding the perfect balance between aesthetic beauty and functional efficiency, enhancing product quality5 and optimizing production.
Monitoring and Adjusting Venting Techniques
Monitoring venting methods became a habit, much like regularly checking the oil in my car. Sensors detecting gas pressure and simulations testing vent designs helped fine-tune the molding process6, ensuring optimal results.
By embracing these strategies, I found that manufacturers, like myself, could significantly reduce defects caused by gas interference in injection molding. An efficient venting system became synonymous with higher-quality outputs and streamlined operations.
Venting size affects gas mark reduction in molding.True
Proper vent size is crucial; too large causes flash, too small traps gas.
Micro vents are ineffective in managing gas flow.False
Micro vents efficiently manage gas flow, ensuring smooth surface finishes.
How does mold design prevent gas marks?
Ever wondered how a tiny detail like mold design can make or break a product’s quality?
Mold design prevents gas marks by optimizing venting systems to allow trapped gases to escape during injection molding, ensuring the quality of plastic components through proper vent placement and size.
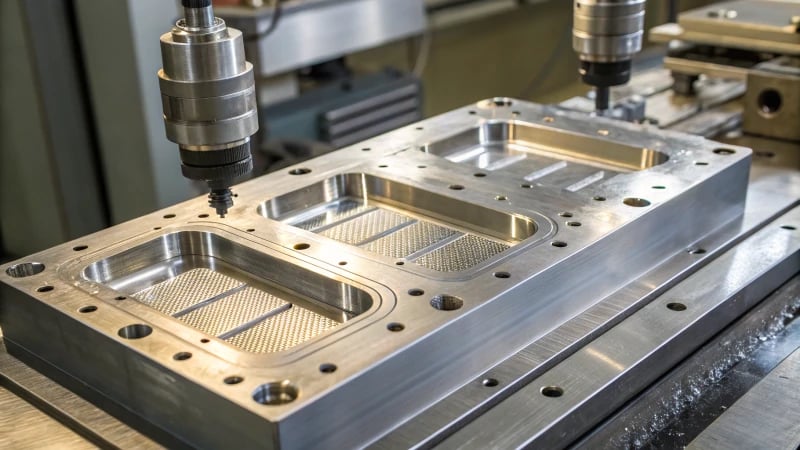
Understanding Gas Marks
I remember when I first encountered gas marks on a batch of plastic components. They were meant to be flawless, but instead, they came out with unsightly burn marks. It was a stark reminder of how critical mold design is in our field. Gas marks usually appear when trapped gases within the mold burn the material, leading to discoloration or surface imperfections. This defect often arises from inadequate venting, poor design, or improper injection settings.
Cause | Effect on Product |
---|---|
Trapped gases | Burn marks |
Inadequate venting | Surface defects |
Key Aspects of Mold Design
-
Venting Systems
Venting is like the unsung hero in mold design; it ensures gases escape from the mold cavity efficiently. An effective design includes strategically placed vents at critical points to prevent pressure build-up. Once, I made the mistake of underestimating vent size – too small, and the gases just wouldn’t escape; too large, and there was a risk of material leakage.
-
Gate Location
Correct gate placement is another crucial element. When done right, it helps minimize gas entrapment by ensuring the flow of material pushes out air efficiently. I’ve seen designs fail because of improper gate placement, so it’s always been a focus in my projects.
-
Material Selection
Different plastics release varying amounts of gas during molding. Choosing a material with low gas emission properties can significantly impact the end product’s quality. I once switched materials mid-project and saw a noticeable improvement in quality.
Advanced Techniques in Mold Design
In recent years, I’ve found using CAD software for simulation invaluable. It helps predict potential problem areas where gas might accumulate, allowing me to adjust the mold design before production starts.
Collaborative Design Process
Bringing together experts from different departments—engineering, production, and quality assurance—has always enriched our design process. This collaboration ensures that all production aspects are considered, which significantly reduces defects like gas marks.
Example: Collaborative Design Table
Team Member | Role | Contribution |
---|---|---|
Engineer | Design Optimization | Ensures effective venting |
QA Specialist | Quality Check | Identifies potential flaws |
Production Manager | Process Efficiency | Streamlines mold production |
I’ve learned so much through these collaborations and believe exploring these advanced techniques9 will only continue to enhance our designs and prevent gas marks.
Venting systems prevent gas marks in mold design.True
Proper venting allows trapped gases to escape, reducing burn marks.
Gate location has no impact on gas entrapment.False
Correct gate placement helps minimize gas entrapment by directing material flow.
How Can I Reduce Gas Mark Formation in Injection Molding?
Ever had a project that looked promising until gas marks showed up, ruining your perfect design? I’ve been there too. Let’s explore how to tackle this pesky issue.
To reduce gas marks in injection molding, adjust mold temperature, improve venting, and fine-tune injection speed for better resin flow and fewer trapped gases.
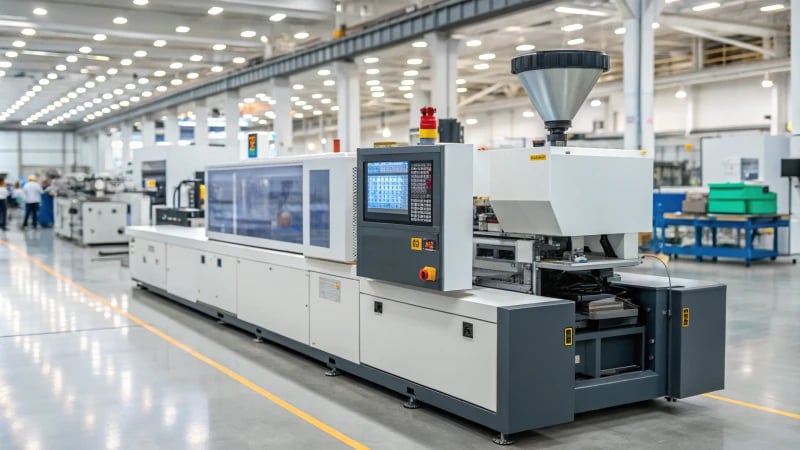
Understanding Gas Mark Formation
When I first encountered gas marks on my molded parts, they were like unwanted blemishes on an otherwise flawless project. These marks, which look like discolorations or blemishes, are due to trapped gases during injection molding10. The impact is not just cosmetic but can also affect the product’s appeal, especially in consumer electronics where every detail matters.
Key Process Adjustments
Optimize Mold Temperature
I remember a time when tweaking the mold temperature transformed a project from drab to fab. It’s amazing how a slight change can help the resin flow more smoothly and reduce gas entrapment. Here’s a handy table I used to track the temperature changes:
Mold Component | Current Temp (°C) | Recommended Temp (°C) |
---|---|---|
Core | 70 | 80 |
Cavity | 65 | 75 |
Enhance Venting Techniques
Once, a mentor of mine suggested looking at venting systems with fresh eyes. That advice led me to modify vent locations and add new ones, which made a huge difference in how efficiently trapped air escaped. Utilizing venting simulation tools11 can provide deeper insights into potential improvements.
Optimize Injection Speed
I found out the hard way that too much speed can be a bad thing. Adjusting the injection speed to be slower and more controlled allowed for better venting and smoother resin flow. Here’s a speed analysis I often refer back to:
Injection Parameter | Current Speed (mm/s) | Recommended Speed (mm/s) |
---|---|---|
Initial Fill | 150 | 130 |
Packing | 100 | 90 |
These adjustments, along with regular maintenance and quality checks12, are essential in creating defect-free products. Exploring advanced techniques and materials can further improve outcomes in injection molding projects. I hope sharing my experiences helps you achieve that flawless finish you’re aiming for.
Lower mold temperature reduces gas marks.True
Adjusting mold temperature affects resin flow, reducing gas entrapment.
Increasing injection speed prevents air traps.False
Slower injection speeds allow better venting and smoother resin flow.
How Can Advanced Technologies Help Me Tackle Gas Marks?
Ever faced a gnarly problem that just won’t budge? For designers like me, gas marks on molded products are exactly that kind of challenge.
Advanced technologies, such as improved venting systems, vacuum-assisted molding, and simulation software, are revolutionizing mold design by reducing gas marks, enhancing product quality, and minimizing defects.
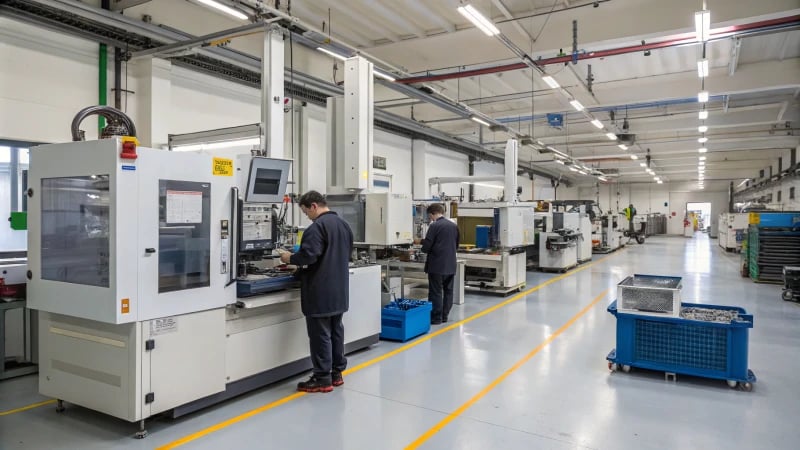
The Role of Improved Venting Systems
If you’ve ever been knee-deep in a project and felt the frustration of persistent imperfections, you’ll understand why I get excited about advanced venting systems. Imagine spending hours designing a sleek gadget, only to have unsightly gas marks ruin the aesthetic. These systems allow gases to escape more efficiently, preventing their accumulation and the dreaded surface marks. It’s like finding that perfect tool in your toolbox that solves a stubborn problem. Engineers have come up with innovative venting solutions13 tailored for different molds and materials, and it’s a game-changer.
Venting System | Benefit |
---|---|
Micro Vents | Enhanced precision |
Valve Vents | Reduced gas accumulation |
Ejector Pin Vents | Increased airflow |
Vacuum-Assisted Molding Techniques
Think of vacuum-assisted molding techniques as the vacuum cleaner for your mold designs, sucking out all the unwanted air like crumbs from a carpet. It’s this technology that ensures our designs maintain their integrity by minimizing gas entrapment. The result? A surface finish that makes you proud to say, "I made that." Explore further14 into how vacuum technology can be your new best friend in design.
Utilization of Simulation Software
Simulation software is like having a crystal ball for mold design. Before the manufacturing wheels even start turning, I can predict and avoid issues such as gas marks. It allows me to simulate gas flow, spot potential problem areas, and make informed decisions. This tech has revolutionized how I approach design challenges, offering insights not just into gas issues but across various facets of the process. Learn about top software15 options that could make your design journey smoother.
Simulation software provides a comprehensive analysis that enhances decision-making, leading to optimized production processes and superior end products.
Benefits of Integrating Advanced Technologies
What I’ve found remarkable is how these technologies don’t just stop at fixing problems—they elevate the entire production process. They lead to higher quality outputs with fewer defects, increased production efficiency with faster cycle times, and cost-effectiveness through reduced material waste and energy consumption.
The synergy between advanced venting, vacuum-assisted molding, and simulation software paves the way for more efficient and sustainable mold design practices. These innovations16 have not only helped me enhance product quality but also provided valuable insights into refining overall manufacturing processes.
Micro vents enhance precision in mold design.True
Micro vents allow precise gas escape, reducing surface defects.
Simulation software increases material waste in production.False
Simulation software optimizes processes, reducing material waste.
Conclusion
Gas marks in injection molding arise from trapped gases, affecting product quality. Effective venting and process optimization are crucial for preventing these defects and ensuring superior molded parts.
-
Learn about injection molding to understand how gas marks form and affect product quality. ↩
-
Discover how simulation tools can predict and prevent defects like gas marks. ↩
-
Explore how advanced CAD systems aid in identifying and resolving design defects early. ↩
-
Discover how venting can improve product finishes and reduce defects in molding. ↩
-
Understand how venting impacts the final product quality and manufacturing efficiency. ↩
-
Explore the influence of venting on optimizing injection molding operations. ↩
-
Explore how simulation software can identify potential gas trap areas before production, enhancing mold design efficiency. ↩
-
Discover top CAD tools that streamline the mold design process, minimizing defects like gas marks. ↩
-
Learn about innovative techniques that enhance mold designs and reduce defects such as gas marks. ↩
-
Understand the fundamentals of injection molding to better grasp how process changes affect gas mark formation. ↩
-
Exploring venting tools can offer insights into improving mold designs to minimize defects. ↩
-
Discover methods to ensure your production process consistently meets high-quality standards. ↩
-
Discover state-of-the-art venting technologies that help reduce gas marks by improving airflow during the molding process. ↩
-
Learn how vacuum technology can minimize gas entrapment and improve product surface quality. ↩
-
Explore powerful simulation tools that predict gas flow issues and enhance design accuracy. ↩
-
Uncover cutting-edge innovations that streamline mold design and manufacturing processes. ↩