The world of electronics is changing faster than ever, with a growing demand for smaller, more efficient components. Enter micro injection molding technology—a true game-changer in this dynamic industry.
Micro injection molding technology revolutionizes electronic components by enabling the production of highly precise, miniaturized parts. This advancement supports the creation of complex designs and structures while maintaining high functionality and efficiency in electronic devices.
While this technology offers immediate benefits such as precision and miniaturization, its full impact extends across various aspects of electronics manufacturing. Let’s delve into how it not only meets current industry needs but also sets the stage for future innovations.
Micro injection molding creates high-precision connectors.True
Micro injection molding ensures dimensional accuracy for stable signal transmission.
- 1. What Are the Key Advantages of Micro Injection Molding in Electronics?
- 2. How Does Micro Injection Molding Compare to Traditional Manufacturing Techniques?
- 3. What Are the Current Industrial Applications of Micro Injection Molding?
- 4. How Will Future Innovations in Micro Injection Molding Shape Electronics?
- 5. Conclusion
What Are the Key Advantages of Micro Injection Molding in Electronics?
Micro injection molding offers precision and efficiency, transforming how electronic components are manufactured.
Micro injection molding provides the precision needed for miniaturized electronic components, enhancing functionality and design complexity while maintaining durability and efficiency.
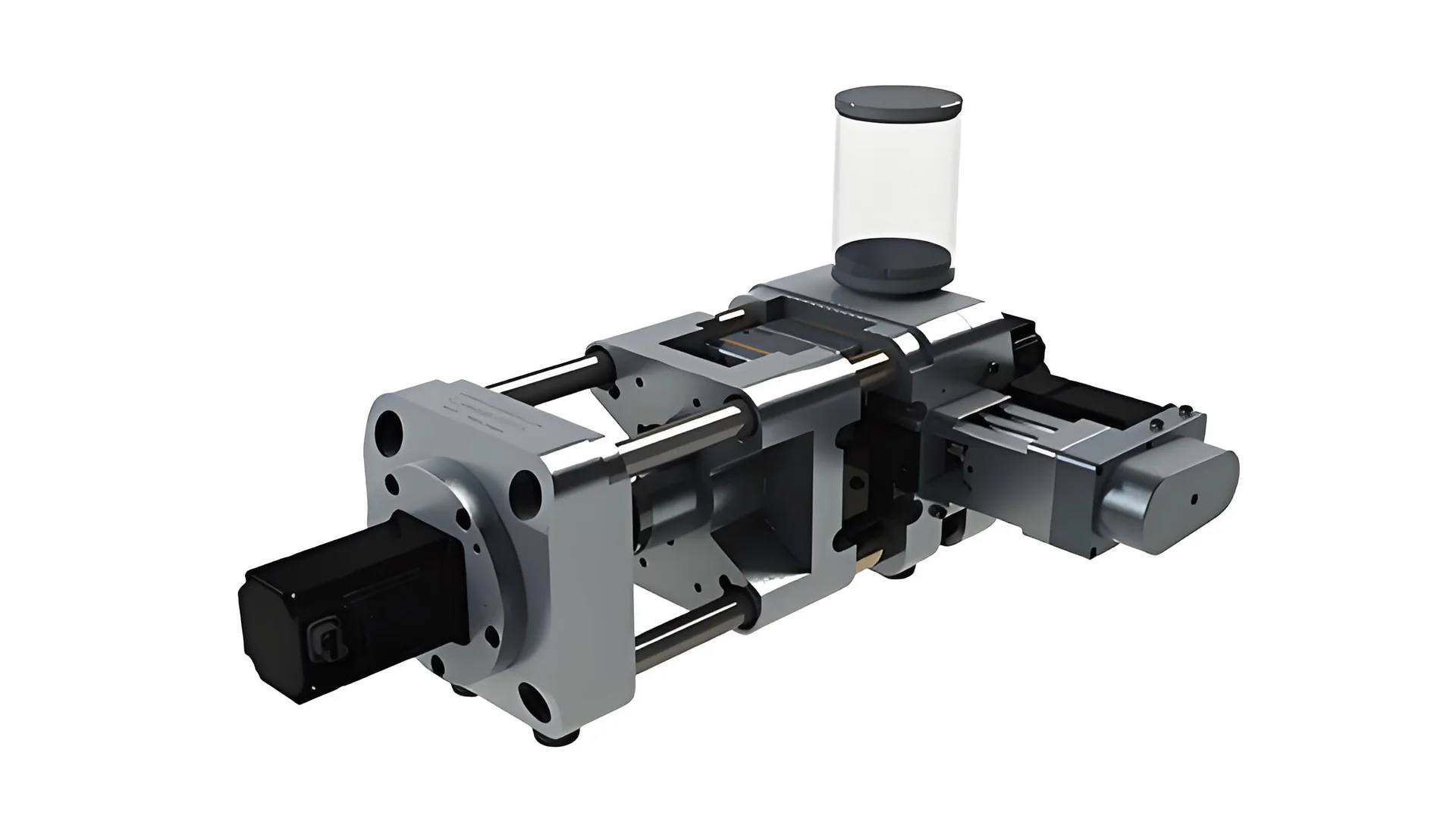
Precision in Miniaturization
One of the standout advantages of micro injection molding is its ability to produce miniaturized housings and packages1 for electronic devices. As electronics continue to shrink in size, the demand for compact and efficient housings grows. This technology meets such demands by enabling the production of extremely small, yet highly precise components. For instance, smart watches, which require waterproof, dustproof, and anti-fall capabilities, benefit significantly from this molding technique. The precision in creating these housings not only ensures protection but also enhances aesthetic appeal.
High-Accuracy Connectors and Connectors
Connectors are crucial in ensuring stable signal transmission in electronic devices. With micro injection molding, producing connectors with high dimensional accuracy2 becomes feasible. For example, connectors on computer motherboards like USB or HDMI interfaces are crafted using this technology to ensure accurate connections. This precision prevents signal loss and enhances performance.
Advancements in Optical Components
The production of optical components3 such as lenses and light guides is another arena where micro injection molding excels. This method produces components with uniform refractive indexes and high transparency, crucial for devices like display screens and mobile phone cameras. The flash lenses in phones benefit from this technology by effectively gathering light, improving photo quality.
Enhanced Sensor and MEMS Production
In the realm of sensors and micro-electromechanical systems (MEMS)4, micro injection molding facilitates the creation of complex and tiny structures. For instance, tire pressure sensors in cars utilize this technology to manufacture sensitive elements that accurately detect pressure changes. The ability to produce such intricate components is vital for enhancing sensor performance across various applications.
Battery and Insulation Component Innovation
Micro injection molding also plays a critical role in manufacturing battery components. It allows for the creation of insulation sheets5 and seals with exceptional insulation properties and mechanical strength. This is crucial for ensuring battery safety and efficiency. Furthermore, the ability to produce components with complex shapes enhances space utilization within batteries, improving overall device efficiency.
Advantages | Applications |
---|---|
Miniaturization | Smart watch casings, mobile phones |
High-accuracy connectors | Computer motherboard interfaces |
Optical component advancements | Mobile phone camera lenses |
Sensor and MEMS component creation | Tire pressure monitoring systems |
Battery innovation | Lithium-ion battery shells |
The implementation of micro injection molding technology represents a significant leap forward in the electronics industry, offering solutions that cater to current needs while paving the way for future advancements.
Micro injection molding enhances miniaturization in electronics.True
It allows for precise production of small electronic components.
Micro injection molding decreases battery efficiency.False
It actually improves efficiency by optimizing component shapes.
How Does Micro Injection Molding Compare to Traditional Manufacturing Techniques?
In the race to innovate, manufacturing techniques have continuously evolved, but how does micro injection molding stack up against its traditional counterparts?
Micro injection molding surpasses traditional manufacturing by offering higher precision, efficiency, and the ability to produce miniaturized components ideal for modern electronics.
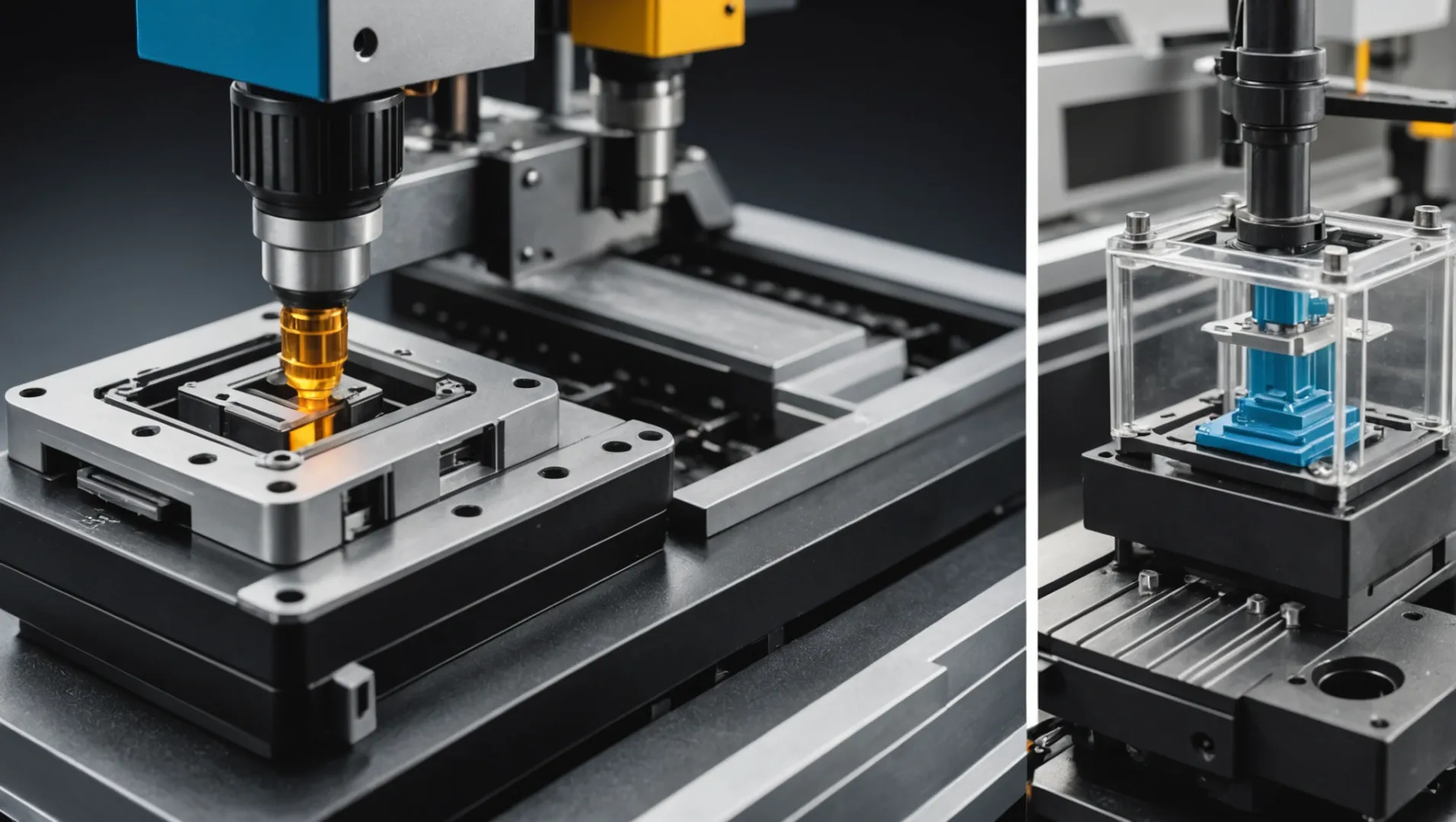
Precision and Miniaturization: A Game Changer
Micro injection molding is renowned for its ability to produce extremely precise and miniature components. Traditional techniques, such as standard injection molding or machining, often fall short when it comes to producing parts with intricate details and tight tolerances.
For instance, consider the manufacturing miniaturized housings and packages6 for electronic devices like smartphones. Traditional methods might struggle with achieving the necessary detail without compromising on strength. In contrast, micro injection molding delivers high-precision parts that meet both aesthetic and functional demands.
Efficiency in Material Use
Unlike conventional methods that might lead to excess material wastage, micro injection molding optimizes material use. This results in lower production costs and a more sustainable manufacturing process.
The production of precision connectors7 exemplifies this efficiency. Traditional methods might involve multiple steps and higher material consumption, whereas micro injection molding allows for single-step production with minimal waste.
Versatility Across Industries
Micro injection molding isn’t just limited to electronics; its applications span across medical devices, automotive components, and even optical equipment. Traditional manufacturing might be versatile, but micro injection molding provides unmatched detail and quality in small-scale production.
For example, the creation of optical components and light guide components8 is significantly improved with micro injection molding. Traditional methods may not offer the same level of precision needed for advanced optics.
Comparative Table: Micro Injection Molding vs. Traditional Techniques
Feature | Micro Injection Molding | Traditional Manufacturing |
---|---|---|
Precision | High | Moderate to Low |
Material Efficiency | High | Variable |
Production Speed | Fast for small parts | Generally slower, especially for complex designs |
Application Range | Electronics, medical, optics, automotive | Broader but less effective for miniature parts |
Conclusion: Not a Conclusion
While micro injection molding clearly has advantages in specific scenarios, it’s crucial to note that each manufacturing technique has its own unique strengths. The choice between micro injection molding and traditional methods ultimately depends on the specific requirements of the project at hand.
Micro injection molding offers higher precision than traditional methods.True
Micro injection molding excels in producing intricate details with tight tolerances.
Traditional manufacturing is more efficient in material use than micro molding.False
Micro injection molding minimizes waste, optimizing material use and reducing costs.
What Are the Current Industrial Applications of Micro Injection Molding?
Micro injection molding is shaping the future of electronics by enabling precise manufacturing of tiny, complex components.
Micro injection molding finds extensive applications in electronics, creating miniaturized housings, precision connectors, optical components, sensors, and battery parts. This technology enhances device functionality and efficiency by producing components with high precision and complexity.
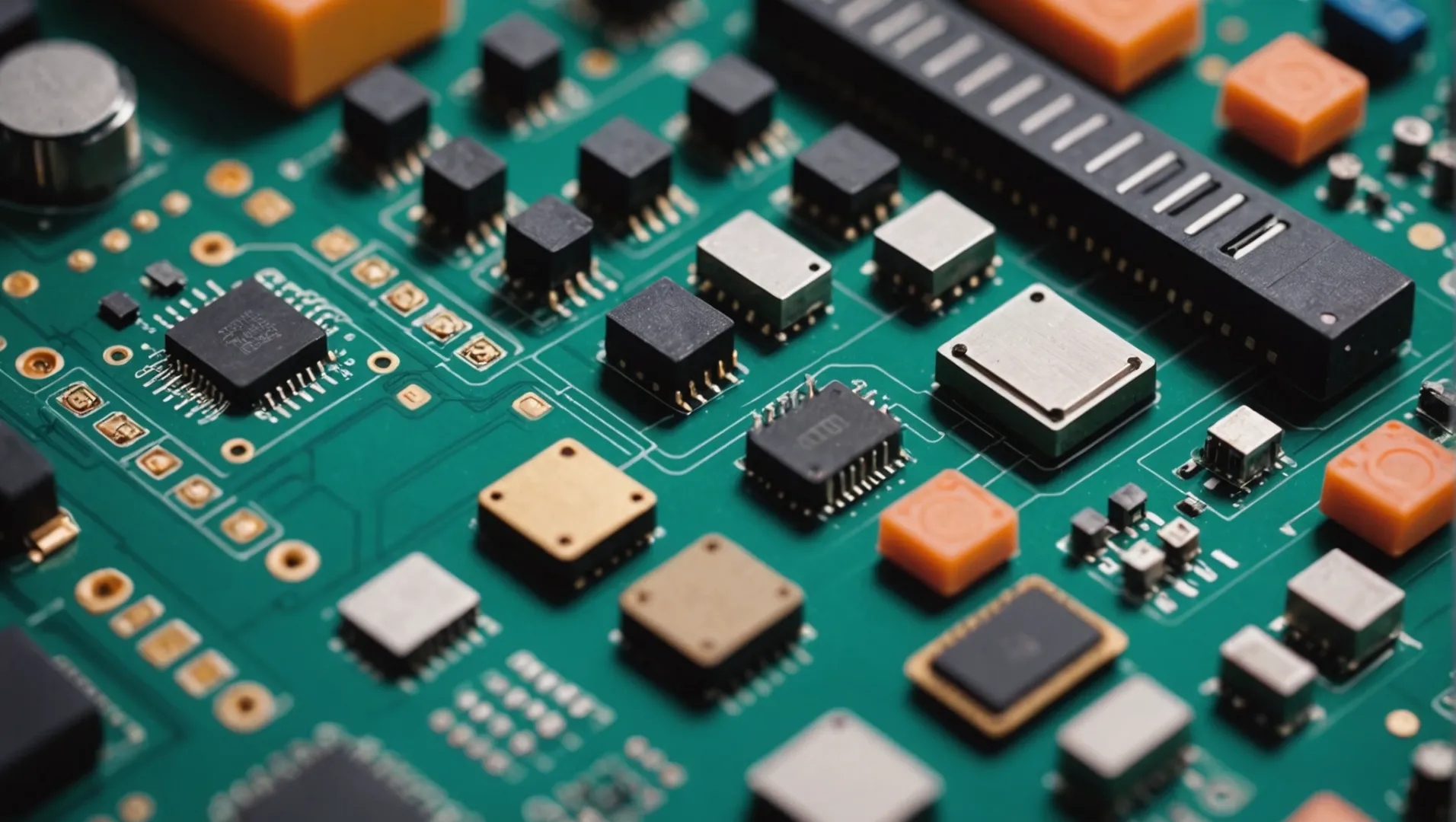
Miniaturized Housings and Packages
Micro injection molding is pivotal in producing miniaturized housings and packages for electronic devices. As the demand for compact and lightweight gadgets grows, this technology enables the creation of small yet robust housings that protect delicate internal components. For instance, smart watches benefit from micro injection molding through cases that are not only sleek but also resistant to water, dust, and impact, thus enhancing both durability and aesthetic appeal.
Precision Connectors and Connectors
Connectors are critical in ensuring reliable connections within electronic devices. Micro injection molding allows for the production of high-precision connectors with excellent dimensional accuracy. In applications such as USB and HDMI interfaces on computer motherboards, this technology ensures stable signal transmission by maintaining tight tolerances and consistent performance.
Optical Components and Light Guides
In devices requiring light manipulation, such as display screens and indicator lights, micro injection molding excels in creating optical components with special properties. The technology is used to manufacture lenses and light guide plates with uniform refractive indices, enhancing light efficiency and achieving desired optical effects. For example, mobile phone flash lenses produced using this method can significantly improve flash brightness and photo clarity.
Sensors and MEMS Components
Micro injection molding is ideal for the production of sensors and micro-electromechanical systems (MEMS) components, which are crucial for detecting and controlling physical quantities in electronics. The technology facilitates the creation of tiny structures with complex shapes necessary for devices like pressure sensors and MEMS microphones. Tire pressure monitoring systems in cars often rely on such precisely molded sensitive elements.
Battery and Insulation Components
In battery manufacturing, micro injection molding is utilized to produce key components such as shells, insulation sheets, and seals. These parts need excellent insulation properties and mechanical strength to ensure battery safety. Moreover, intricate shapes created through this process maximize space utilization within batteries, as seen in lithium-ion battery casings.
To explore more about the precise applications of micro injection molding in electronics, consider looking into recent advancements in miniaturized housings9 or optical components10.
Micro injection molding enhances battery safety.True
It produces components with excellent insulation and mechanical strength.
Micro injection molding is not used for optical components.False
It's used to create lenses and light guides with uniform refractive indices.
How Will Future Innovations in Micro Injection Molding Shape Electronics?
The electronics landscape is on the brink of transformation, driven by future advancements in micro injection molding.
Future innovations in micro injection molding will enable even more precise, complex, and cost-effective electronic components, pushing the boundaries of miniaturization and functionality.
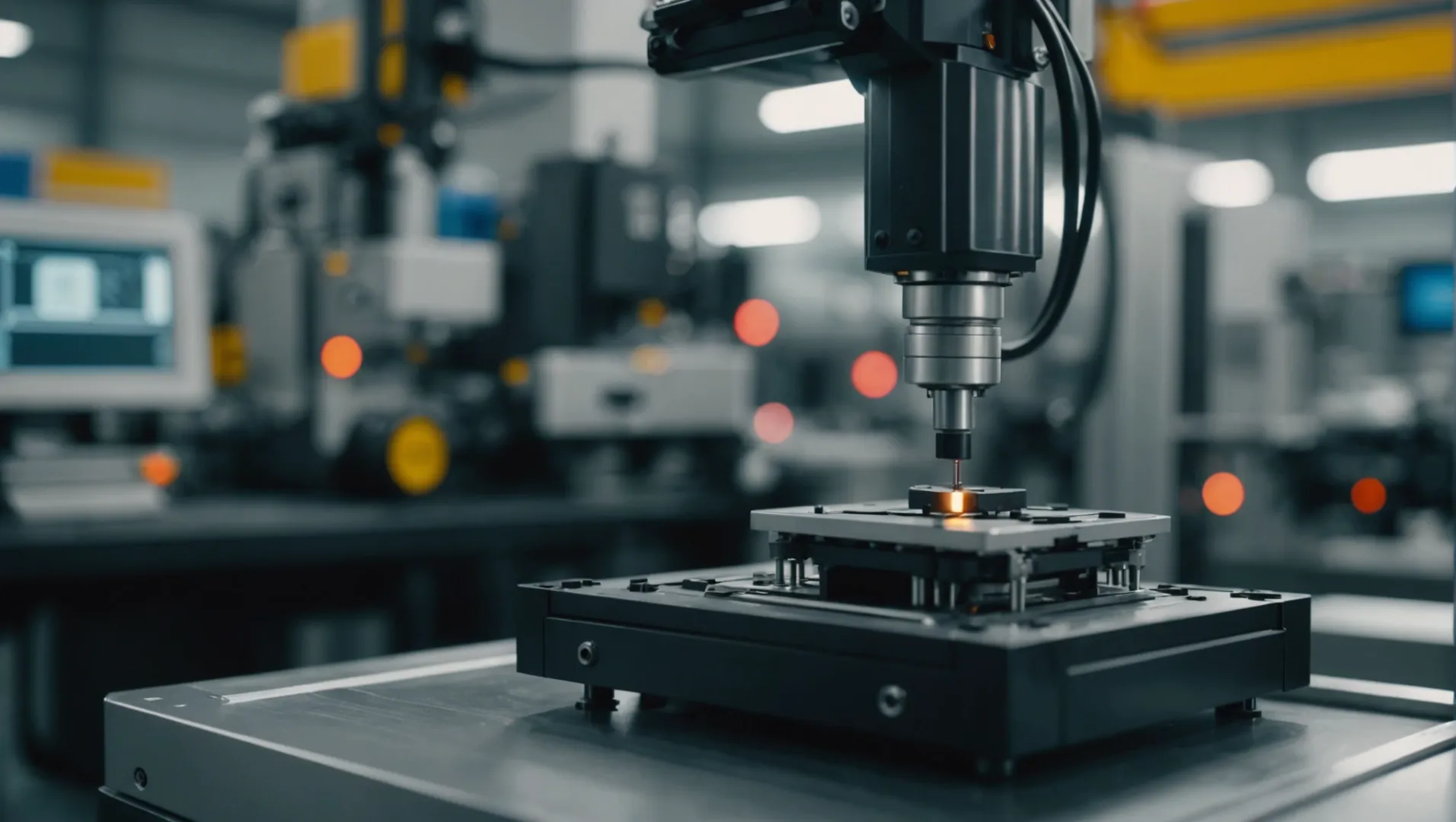
Pioneering Miniaturization with Enhanced Precision
Micro injection molding is already known for its ability to produce intricate designs with precision. As the technology advances, we can anticipate even greater precision, allowing for the production of components that are smaller yet more complex than ever before. This will be essential for the next generation of electronic devices, where size reduction without compromising functionality is crucial. Consider the evolution of wearables like smartwatches; future innovations in this technology could lead to devices that are virtually invisible yet packed with features.
Advanced Materials for Enhanced Performance
A key area of development is the use of novel materials that offer superior properties. Future innovations could see the integration of smart materials that respond to environmental changes, enhancing device functionality. For instance, electronic devices could incorporate components made from self-healing polymers, extending their lifespan and reducing maintenance costs. By adopting these advanced materials, manufacturers can produce electronics that are not only smarter but also more durable and energy-efficient.
Sustainability through Eco-Friendly Production
Environmental concerns are becoming increasingly important in manufacturing. Future innovations in micro injection molding are expected to focus on sustainability by reducing waste and energy consumption. This could involve the development of biodegradable plastics or the use of recycled materials in production processes. Such advancements will not only make electronics more eco-friendly but also appeal to a growing base of environmentally conscious consumers.
Integration with Emerging Technologies
The future of micro injection molding is not just about improving the technology itself but also integrating it with other cutting-edge technologies. Imagine combining this molding process with 3D printing11 to create hybrid manufacturing systems that offer unmatched flexibility and customization options. These systems could revolutionize the production of electronic components by enabling manufacturers to produce bespoke parts on demand, thereby reducing lead times and inventory costs.
Revolutionizing Electronics Manufacturing
Future innovations in micro injection molding will redefine electronics manufacturing by pushing the boundaries of what’s possible. With enhanced precision, advanced materials, sustainability, and integration with other technologies, this field holds the potential to reshape how electronic components are designed and produced. As we look towards a future where electronics are more integrated into every aspect of our lives, micro injection molding will play a pivotal role in making this vision a reality.
Micro injection molding enables invisible wearables.True
Advancements allow smaller, feature-rich devices, like invisible smartwatches.
3D printing hinders micro injection molding integration.False
3D printing complements and enhances micro injection molding flexibility.
Conclusion
Micro injection molding is pivotal in advancing electronics manufacturing, offering precision and efficiency. By understanding its capabilities, industries can innovate further, enhancing device performance and design.
-
Discover how miniaturized housings improve device functionality.: Micro injection molding produces tiny, intricate components through specialized techniques. Learn how it achieves precision at the microscale for … ↩
-
Learn how precision connectors enhance electronic reliability.: Micro injection molding refers to the production of highly precise plastic components where the molded products typically weigh less than 0.01 grams to several … ↩
-
Explore how optical components enhance visual device quality.: Micro-optics are typically tiny lenses, beam-splitters, prisms, light-pipes, and other optical components in the range of 20 microns to 1 mm in size. ↩
-
Understand how MEMS technology improves sensor performance.: MEMS (microelectromechanical systems): Used in the manufacture of miniature sensors, actuators, and micro-mechanical components, micro-injection … ↩
-
Find out how insulation sheets ensure battery safety.: These insulator sheets are asbestos free, oil and moisture resistant plus have high hot compressive strength. PCS Company’s insulator sheets are found on … ↩
-
Explore how micro injection achieves superior precision in tiny components.: The data-based comparison revealed that μIM was better suitable for meeting the high precision and accuracy demands typical of micro productions. ↩
-
Discover why micro injection is preferred for high-precision connectors.: It enables manufacturers to meet the demands for small, exact components while ensuring scalability for high-volume production. In this … ↩
-
Learn about its role in producing advanced optical components.: Use of injection molding for micro-optic manufacture, however, requires the optimization of design, mastering, tooling, and production steps, … ↩
-
Discover how micro molding creates robust, compact electronic device casings.: Micro injection molding produces tiny, intricate components through specialized techniques. Learn how it achieves precision at the microscale for … ↩
-
Learn how micro molding enhances optical component efficiency and design.: Micro-optics molding is a precision injection mold process that produces optical components on a smaller scale than is attainable than with traditional molding … ↩
-
Explore how 3D printing enhances micro injection molding processes.: Learn how to create 3D printed injection molds for low-volume, in-house injection molding to produce small, functional parts in production plastics. ↩