I look at the product’s size, design details, mold dimensions and materials to select the correct tonnage for an injection molding machine. The clamping force is found using the formula F = p × A. Here, p stands for injection pressure and A represents the projected area. Remember to add a safety margin for reliable operation. It’s important.
When I began using injection molding machines, I discovered it’s not just about using equations. These formulas are only a starting point. The true skill lies in understanding each special factor. The shape of the product and the material’s unique traits are important. Think of thin-walled containers. They need higher pressures because they cool quickly. This means you need a stronger machine. Complex designs add another challenge. Extra clamping force becomes crucial. This stops the mold from expanding under pressure. Matching the mold size with machine specifications is really important. This helps prevent unexpected issues. Exploring these details is vital. This way, everything runs smoothly.
Thin-walled products need higher injection pressure.True
Thin-walled products cool quickly, requiring higher pressure to fill cavities.
All plastics require the same tonnage for molding.False
Different plastics have varying flow and shrinkage characteristics, affecting tonnage needs.
- 1. Why is the Product Projection Area Crucial for Machine Selection?
- 2. How Do Product Shape and Structural Characteristics Affect Tonnage?
- 3. Why Are Mold Dimensions Important in Choosing Injection Molding Machines?
- 4. How Do Material Properties Influence Injection Molding Machine Selection?
- 5. Conclusion
Why is the Product Projection Area Crucial for Machine Selection?
Have you ever stood puzzled by technical details, trying to decide on the best machine for injection molding? I have experienced that confusion as well. Believe me, grasping the product projection area changes everything.
The product projection area is vital for choosing the correct injection molding machine. It shows the needed clamping force. Calculated from the mold’s parting surface, it affects the machine’s tonnage. The tonnage is very important. It really helps in achieving good performance and safety during molding.
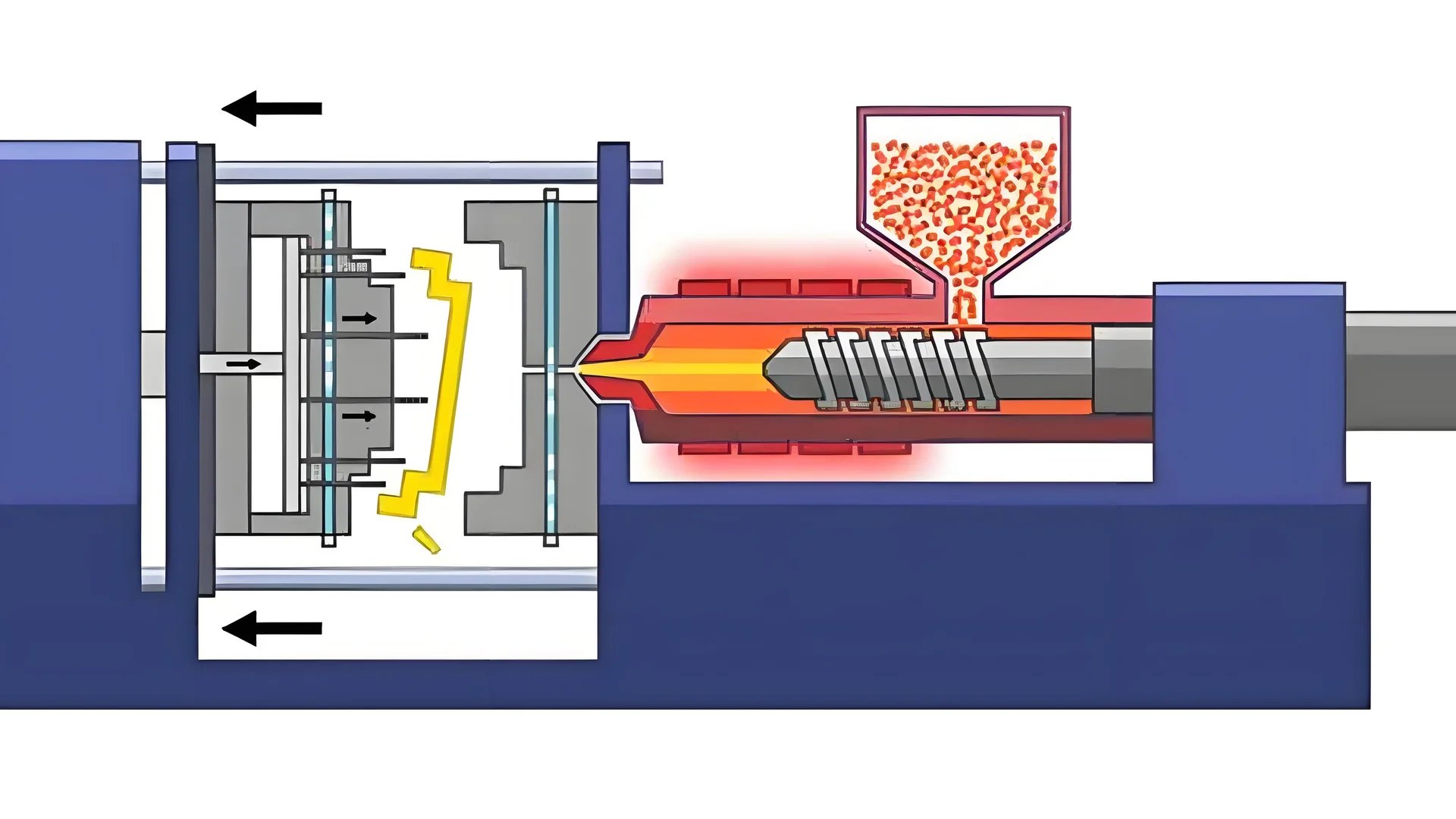
Why Product Projection Area Matters
I remember my first time with injection molding. It felt like entering a world full of new numbers. The product projection area was my guide. This area is important as it tells us the clamping force needed to keep the mold closed during injection molding1. Imagine molten plastic pushing on mold walls, trying to break free. Without enough clamping force, problems happen.
Safety Factors and Tonnage Decisions
Safety is not just a word – it is a must. I learned this fast. Applying a safety factor, usually between 1.2 and 1.5, matters a lot. Say you have a force of 500kN; choosing a machine with at least 650kN clamping force when using a 1.3 safety factor is wise. A small change makes the operation smooth and ensures the machine can handle unforeseen stress without compromising product quality2.
Shape and Structure Influence
Product shape and structure are key too. Thin-walled items cool quickly and need more pressure, requiring machines with higher tonnage to prevent defects like warping or incomplete filling. I once worked with thin plastic containers that needed bigger machines to seal properly—this was surprising! Complex designs also pose challenges; products with internal grids or reinforcements increase melt flow resistance, necessitating machines that can deliver sufficient pressure to maintain mold integrity for complex structural designs3.
Aligning Mold Dimensions with Machine Capabilities
I also learned to match mold dimensions to machine specs. Miss this step and problems arise; ensuring mold size and tie bar spacing fit well avoids issues such as operational inefficiencies or even damage to both the mold and machine.
Material Properties Impact Machine Selection
Finally, materials really matter as some need more pressure because they flow poorly or shrink significantly during cooling, demanding machines that compensate for these forces effectively. I discovered this with glass fiber-reinforced plastics—adjusting for material differences improves efficiency and reduces defects, keeping production smooth by enhancing production efficiency4.
These factors turn choosing an injection molding machine into an informed task—that’s what we probably all want, right?
Thin-walled products need higher injection pressure.True
Thin walls cool quickly, requiring higher pressure to fill molds.
Larger molds can fit any injection molding machine.False
Mold dimensions must match the machine's template size and tie bar spacing.
How Do Product Shape and Structural Characteristics Affect Tonnage?
Do you ever think about how the design of a product impacts the equipment required to produce it?
The shape and structure of products affect the tonnage needs for injection molding machines. Thin-walled designs usually need more tonnage. Complex designs also require more pressure and force. More pressure is needed during production. It’s really important. Choose the right machine by looking at the product’s projected area. Consider also the material properties. These factors matter.
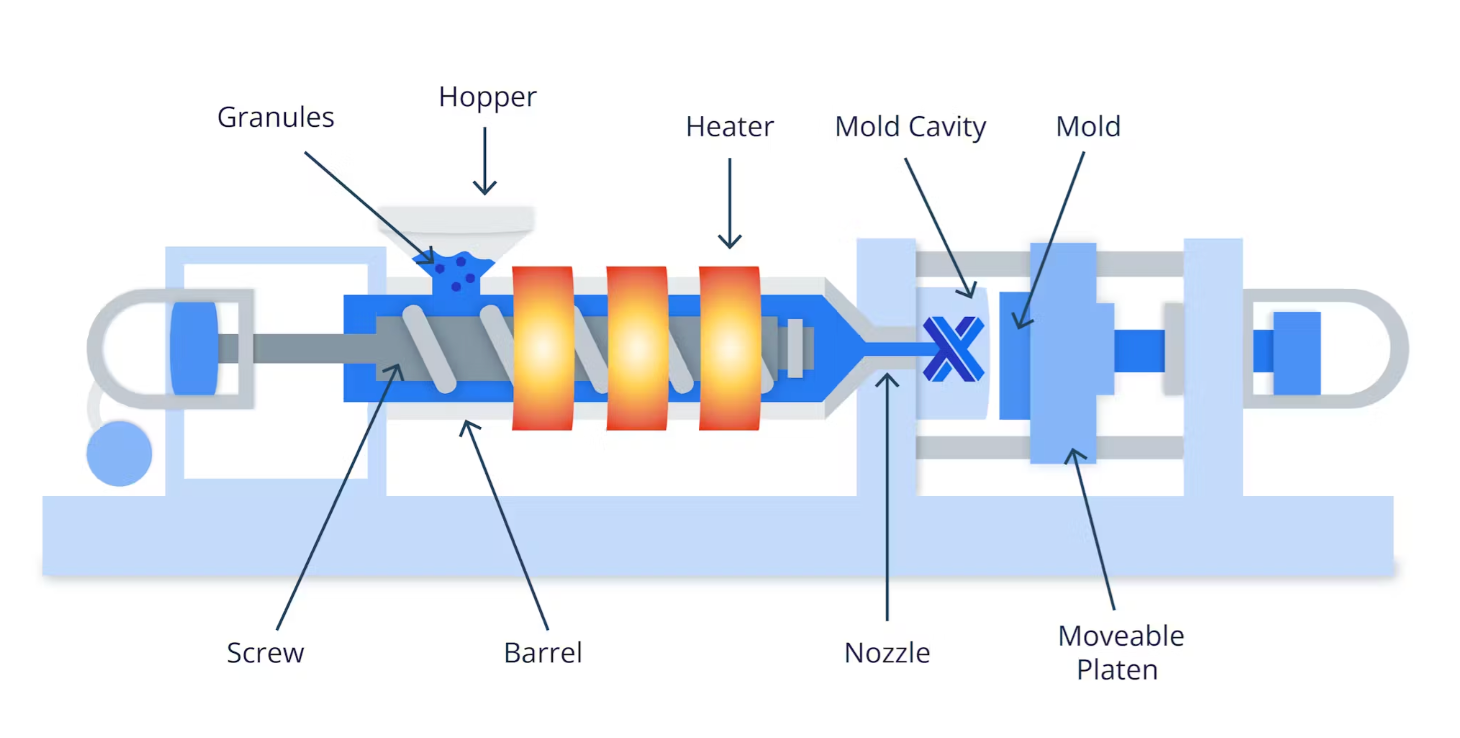
Calculating the Projected Area
Imagine you are in the kitchen, trying to store groceries in a small cupboard. It is similar to picking the right size for an injection molding machine. Figure out the projected area of the product, like spreading groceries on the counter before putting them away. Use the formula (F = p \times A), where (F) is clamping force, (p) is injection pressure and (A) is the projected area. This helps you see the needed clamping force. Usually, add a safety margin (from 1.2 to 1.5). If the expansion force is 500kN, choose a machine of at least 650kN. No spills happen.
Influence of Thin-Walled Products
Thin-walled items remind me of pushing a thick milkshake through a slim straw. These cool quickly and require higher injection pressures to fill every space well. The melt pushes harder, necessitating machines with more strength to keep it tidy. Fragile plastic containers with walls less than 1mm need stronger machines than thicker ones.
Complex Structural Products
Handling complex structural products is like putting together IKEA furniture with too many parts. These intricate designs often have elements like reinforcing bars and face high resistance when the melt flows. More power is needed from the machine—higher injection pressure and clamping force—to prevent mold expansion under pressure, ensuring efficient mold closure5.
Adapting to Mold Dimensions
Imagine trying to fit an oversized book on a small shelf; mold dimensions matter for injection molding machines similarly. The machine must match the mold’s size and tie bar spacing. If the mold’s size is too large for a smaller machine, you need a bigger machine as mounting holes must also align.
Material Properties Impact
Think about using different materials, like cooking with or without gluten; each needs special care. Materials with poor fluidity, such as glass fiber-reinforced plastics, require higher pressures to fill cavities, increasing expansion forces on the machine. Some materials shrink as they cool, adding stress—for example, using polyamides with 30% glass fibers requires stronger machines than regular polyethylene.
Understanding these factors assists in better machine choices for smoother operation—it’s like planning a very well-organized dinner party.
Thin-walled products require higher injection pressure.True
Thin-walled products cool quickly, needing more pressure to fill cavities.
All plastic materials need the same injection pressure.False
Different materials have varying flow characteristics, affecting pressure needs.
Why Are Mold Dimensions Important in Choosing Injection Molding Machines?
Do you ever feel like choosing an injection molding machine is like solving a big puzzle? I do. The mold size is usually very important. It really matters a lot.
Mold size matters a lot when choosing injection molding machines. Mold dimensions must fit with machine details. This includes correct clamping force and smooth production. The external size, shape and structure of the mold need to match the machine’s template size and tie bar spacing. This alignment helps prevent problems. Size and fit really matter.
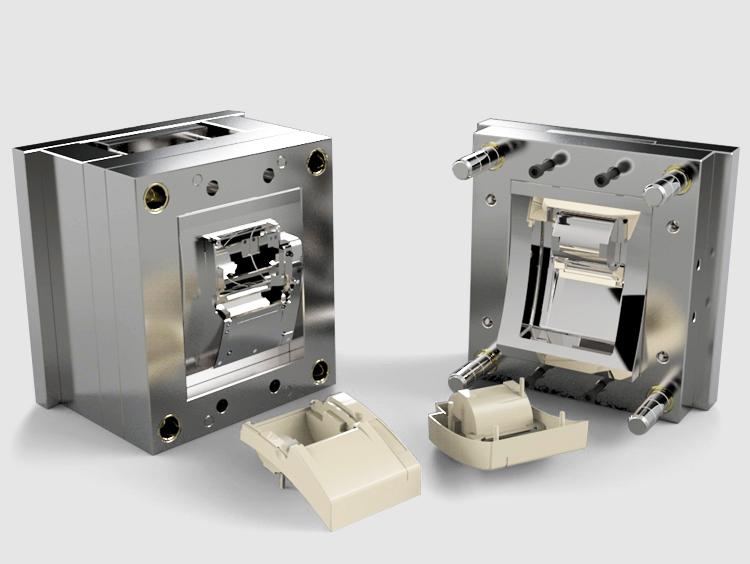
Compatibility with Machine Specifications
I remember when I first tried matching a mold to an injection molding machine. It was confusing, like trying to fit a square peg in a round hole! Mold sizes must fit within the template size6 and tie bar space of the machine. Once, I thought a mold would fit, but it didn’t. I had to look for a bigger machine. Always double-check those measurements!
Clamping Force
I used to think calculating clamping force was difficult. It’s about understanding the projected area on the mold’s face. The formula is (F = p \times A), where (p) is injection pressure and (A) is the projected area. It gets easy once you are familiar with it. For thin-walled products like delicate plastic containers, the machines need enough power to keep molds shut during injection.
Production Efficiency
Larger molds need machines with big shot sizes and fast cycle times. It is very important to know the material properties. If the material doesn’t flow well, you need higher injection pressure. Working with glass fiber-reinforced plastics taught me that high-tonnage machines are a must for smooth production.
Product Design
The shape and structure of a product determine mold size. Complex designs, like intricate grids, need machines with plenty of clamping force. Finding the right machine for design needs guarantees mold performance and makes products shine.
These experiences show how important it is for manufacturers to choose equipment based on production needs and product details. This prevents costly errors from mismatched molds and machines.
Higher tonnage machines are needed for thin-walled products.True
Thin-walled products require higher injection pressure and clamping force.
Mold dimensions do not affect machine selection.False
Mold dimensions must match machine template size and tie bar spacing.
How Do Material Properties Influence Injection Molding Machine Selection?
Picking the correct injection molding machine resembles fitting a puzzle piece perfectly. Every material property holds a crucial role. Material traits are very important.
Material properties like flowability, shrinkage and reinforcement shape the choice of injection molding machines. They influence the needed pressure, clamping force and machine size. Material properties guide the selection process.
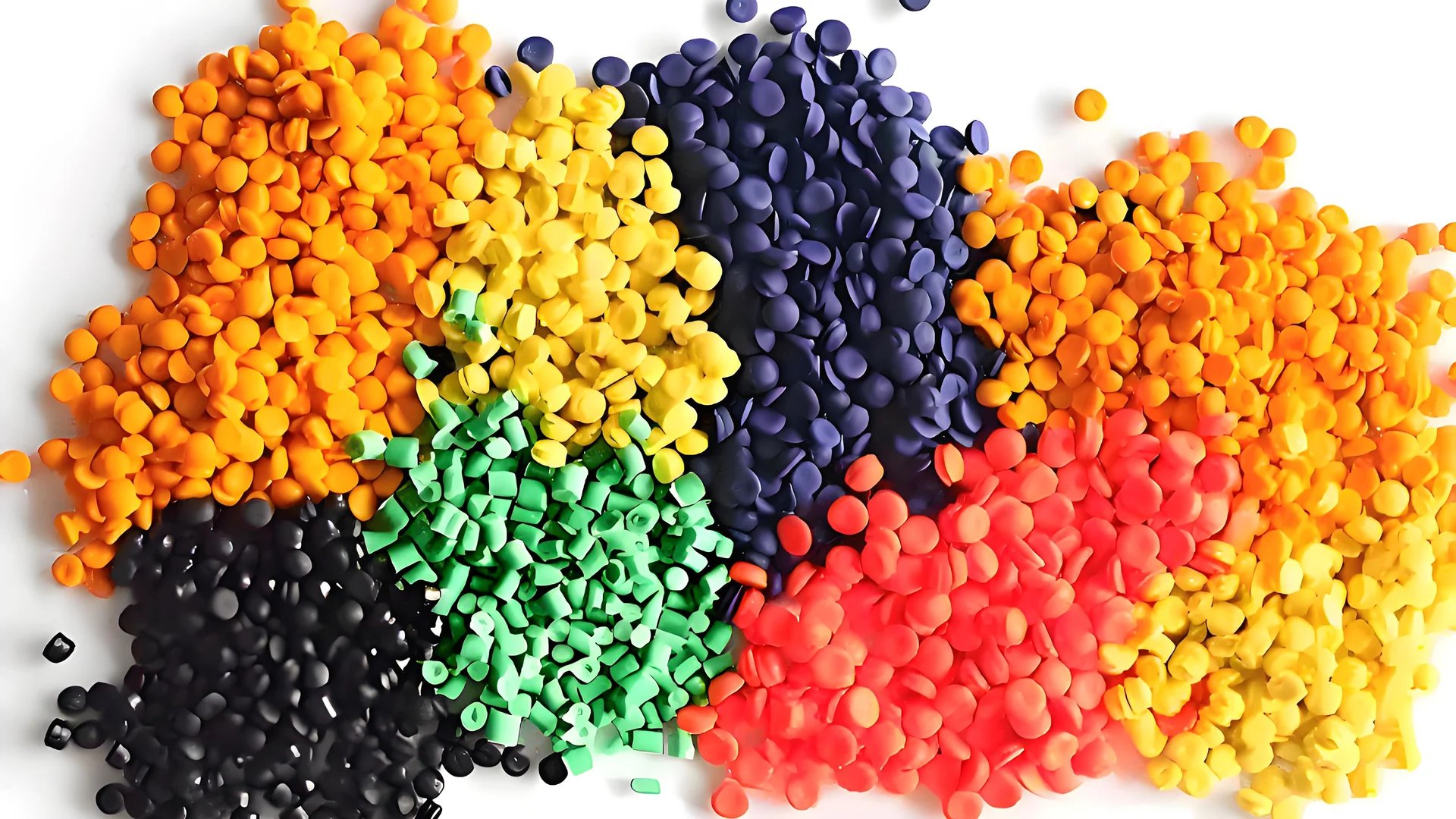
Understanding Material Flowability
Picture trying to pour a thick milkshake through a straw. Sounds tough, right? This is similar to dealing with materials that barely flow, like glass-fiber plastics. I worked on a project where these materials required high injection pressures7. We needed a powerful machine for this task. Every corner of the mold had to fill correctly. It had to.
The Role of Shrinkage Characteristics
Shrinkage affects more than just laundry. It impacts injection molding too. Some materials, like glass-fiber polyamide, shrink a lot when cooled. This applies huge force on molds and machines. I experienced this and had to pick a strong machine to control it. It opened my eyes. Shrinkage really changes machine choices.
Impact of Reinforcement on Machine Choice
Reinforced plastics add strength, but they bring problems. I found that glass fibers raised the expansion force during molding. This changed the clamping needs. The machine needed to handle this to keep the mold closed and the product safe. Choosing the right machine is like picking perfect shoes for a big race. You need the best fit.
Compatibility with Mold Dimensions
Imagine fitting a square peg into a round hole. Mold size and machine specs can feel like this if they don’t match. Larger molds must have machines with the right template and tie bar spacing. I’ve faced cases where this alignment was crucial. Misalignment led to big problems. It really did.
Effects of Product Shape and Structure
Thin-walled or complex structures are tricky. I dealt with thin-walled containers requiring fast cooling and high pressures. Complex shapes needed machines to resist melt flow. Knowing your product’s shape is key to picking the right machine.
Grasping these interactions among materials and machines is like solving a tough puzzle. Each choice matters for effective production and high-quality products.
Thin-walled products need higher injection pressure.True
Thin walls cool quickly, needing more pressure to fill molds.
Glass fiber plastics require lower injection pressure.False
Glass fiber plastics have poor fluidity, needing higher pressure.
Conclusion
Selecting the right tonnage for an injection molding machine involves considering product projection area, shape, mold dimensions, and material properties to ensure optimal performance and quality.
-
Learn how projection area influences machine selection for optimal molding. ↩
-
Understand how safety factors ensure reliable and defect-free production. ↩
-
Explore challenges and solutions for molding intricate product structures. ↩
-
Discover how material choice affects machine efficiency and product quality. ↩
-
Explores how proper mold closure affects product quality. ↩
-
Understand how machine specifications affect mold installation. ↩
-
Explore how different injection pressures influence machine choice. ↩