Have you ever wondered why some molded products come out flawless while others have defects? It all starts with the injection rate in the molding process!
The injection rate in molding affects product quality by influencing shrinkage and cavity packing. An optimal rate ensures proper filling, reduces defects, and maintains material integrity. Factors like plastic type, product design, and machine capabilities play critical roles.
While this gives a snapshot of how injection rates impact molding quality, diving deeper reveals complex interactions between material properties, machine performance, and product design. Let’s explore these dynamics to enhance your production outcomes.
Higher injection rates reduce molding defects.True
Higher rates ensure better cavity filling, reducing shrinkage and warping.
What Role Does Plastic Material Play in Determining Injection Rate?
Plastic material selection is pivotal in defining the injection rate during molding, affecting product quality and efficiency.
Plastic material influences the injection rate by determining fluidity and fillability. Materials with higher fluidity allow faster injection rates, facilitating complete cavity filling, whereas materials with lower fluidity necessitate slower rates to prevent defects.
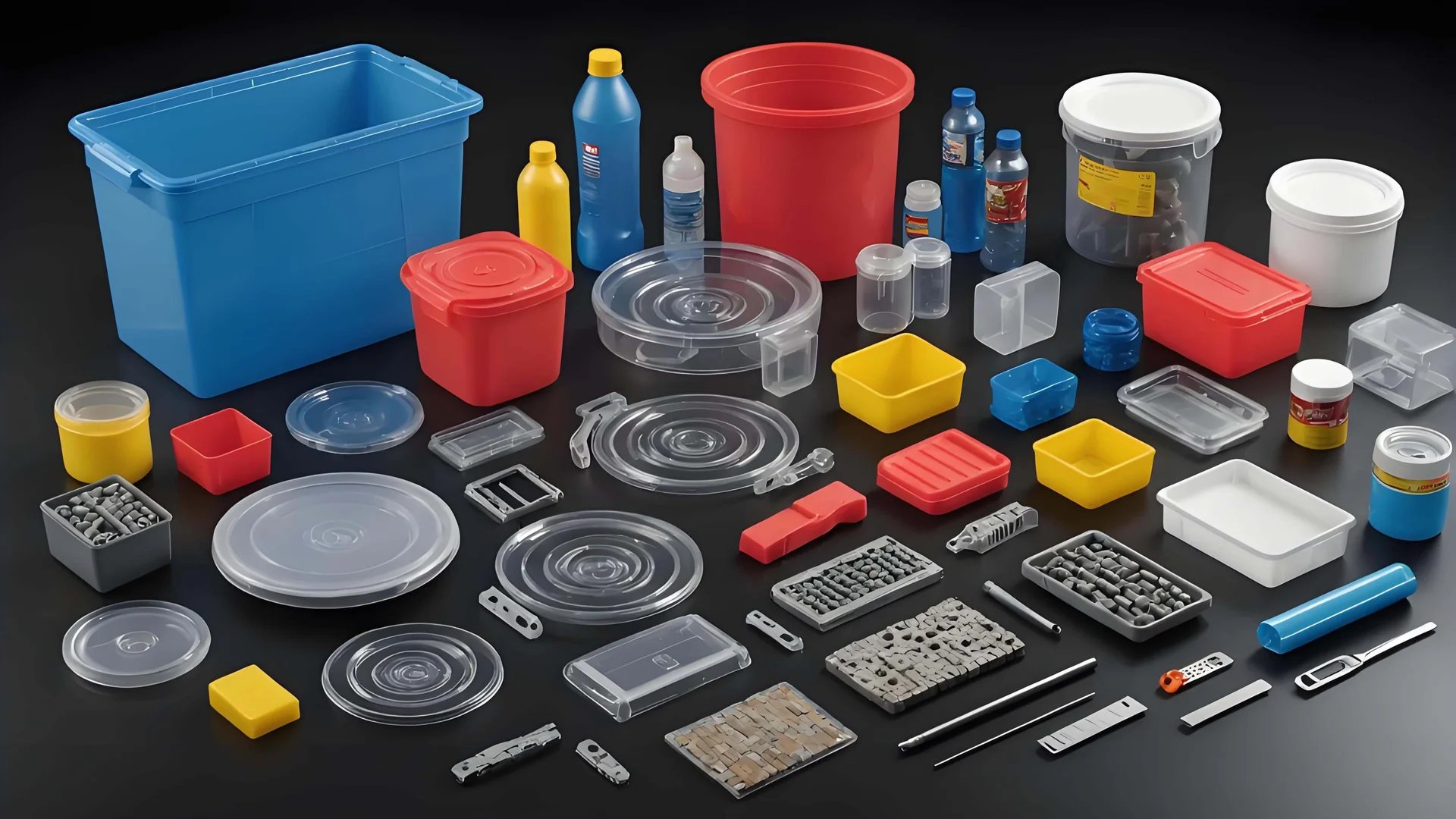
Understanding Plastic Fluidity
The fluidity of plastic material is a critical factor in determining the injection rate1. Higher fluidity plastics, such as polypropylene, can be injected at faster rates, allowing for efficient cavity filling and reduced cycle times. Conversely, materials like polycarbonate, which exhibit lower fluidity, require slower injection rates to avoid issues like incomplete filling or excessive internal stress.
Material-Specific Considerations
Polypropylene vs. Polycarbonate
Property | Polypropylene | Polycarbonate |
---|---|---|
Fluidity | High | Low |
Typical Injection Rate (cm/s) | 30-50 | 10-20 |
Fillability | Excellent | Moderate |
Polypropylene, with its high fluidity, allows for higher injection rates, making it ideal for complex shapes and thin-walled products. On the other hand, polycarbonate requires careful control of the injection rate to ensure adequate filling without compromising structural integrity.
Balancing Injection Rate with Material Properties
Achieving an optimal balance between material properties2 and injection rate is crucial. This balance ensures that the material’s integrity remains intact while achieving the desired product specifications. For instance, increasing the injection rate for a high-viscosity material can lead to problems like warping or shrinkage.
Practical Insights from Industry Experts
Industry experts suggest conducting thorough material testing to determine the appropriate injection rate settings for different plastics. Such testing includes evaluating viscosity under varying temperatures and shear rates to establish an optimal range that aligns with production goals.
In practice, adjustments are made based on the specific product requirements and the performance capabilities of the injection molding machine. Thus, understanding and accommodating the unique properties of each plastic type is essential for optimizing injection rate settings.
Polypropylene has higher fluidity than polycarbonate.True
Polypropylene's high fluidity allows faster injection rates than polycarbonate.
Lower fluidity plastics require faster injection rates.False
Lower fluidity plastics need slower rates to prevent defects.
How Does Product Shape Influence Injection Molding Outcomes?
The shape of a product significantly impacts the efficiency and quality of injection molding processes. Understanding these influences is crucial for optimal manufacturing.
Product shape affects injection molding by dictating the flow and cooling of plastic within the mold. Complex shapes require careful consideration of injection rates to prevent defects like warping or incomplete filling. Shape intricacies can significantly alter the outcomes, necessitating adjustments in process parameters.
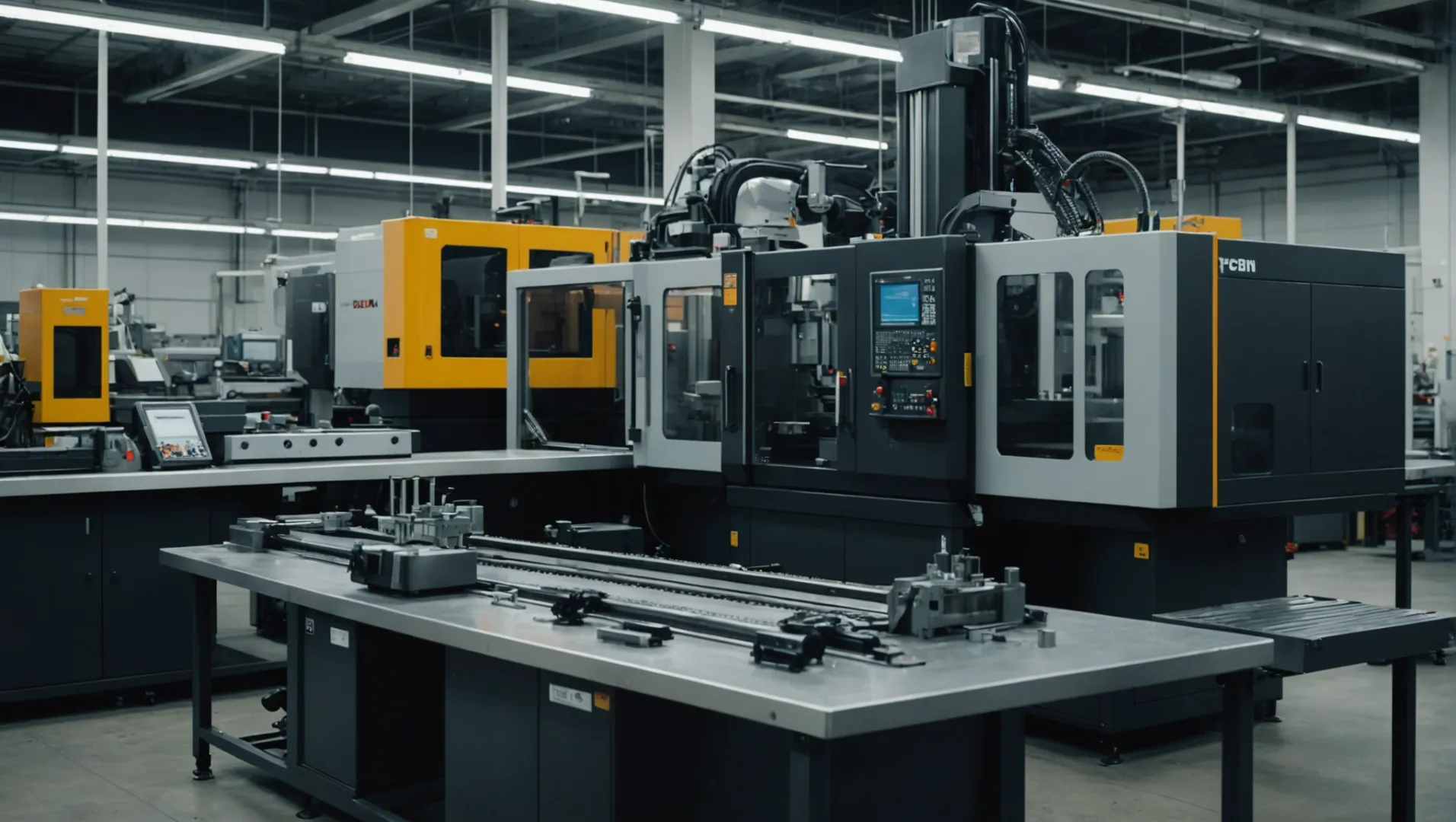
The Impact of Product Geometry on Injection Molding
Product geometry plays a pivotal role in determining the flow behavior of molten plastic within the mold. For instance, thin-walled sections demand higher injection rates to fill cavities effectively and reduce cycle time. However, complex geometries with intricate features require a nuanced approach to balance filling and minimize defects such as voids or warping.
Considerations for Thin-Walled and Complex Structures
Thin-walled products often necessitate faster injection rates to ensure that the plastic reaches all parts of the mold before it cools and solidifies. This helps in maintaining uniform thickness and structural integrity. Conversely, complex structures may benefit from controlled, slower rates to allow for better control over the flow path and reduce shear stress.
To illustrate:
Product Type | Recommended Approach |
---|---|
Thin-walled | Higher injection rate for rapid filling |
Complex shapes | Slower, controlled rate for precision |
Influence of Symmetry and Surface Complexity
Symmetrical designs typically experience more uniform stress distribution during molding, leading to fewer defects. In contrast, asymmetric or highly detailed surfaces might require custom gating solutions to prevent localized cooling and shrinkage.
Injection molding gate design3 can be optimized based on product symmetry to enhance the flow of plastic and ensure even distribution throughout the mold. Such optimizations are crucial in maintaining high quality across varied production runs.
Balancing Product Design and Material Properties
Different materials react uniquely to changes in product design. For example, materials with high fluidity may accommodate complex shapes more easily than those with lower fluidity, influencing the selection of both material and design parameters. Hence, collaborating with material experts during the design phase can yield better molding results.
Choosing the right plastic material4 involves understanding how material properties align with the intended product shape, ensuring both efficient production and product durability.
Complex shapes need slower injection rates.True
Slower rates help control flow path and reduce defects in complex shapes.
Thin-walled sections require slower injection rates.False
Thin-walled sections need higher rates for effective cavity filling.
What Are the Effects of Mold Design on Injection Rate Efficiency?
Mold design significantly influences the efficiency of the injection rate, impacting overall product quality and manufacturing speed.
Mold design affects injection rate efficiency by controlling the flow path of the material. Proper gate size, runner layout, and venting are crucial for optimizing the flow, reducing cycle time, and minimizing defects. Efficient mold design can enhance fill speed without sacrificing product quality.
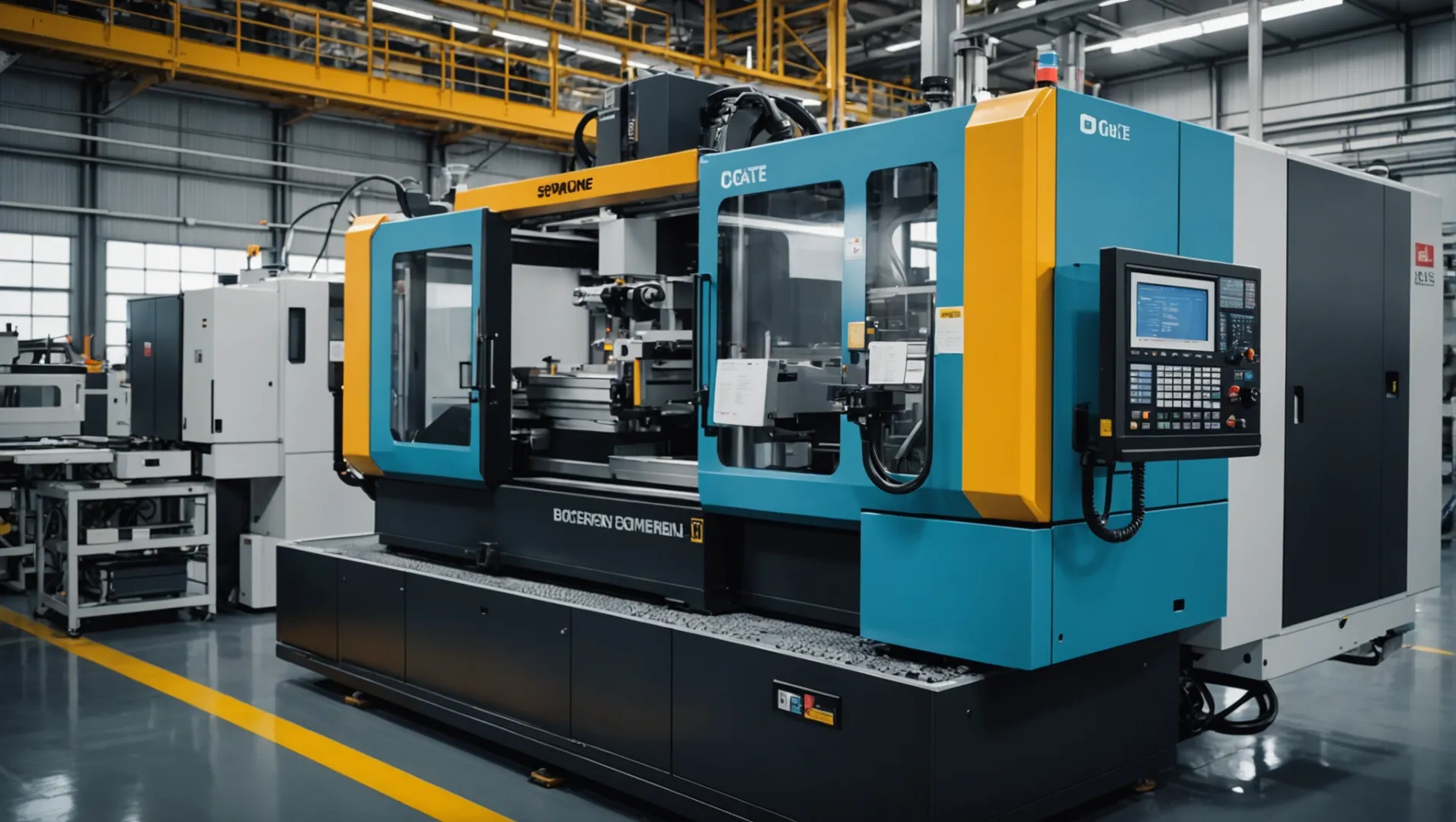
Understanding Mold Design Elements
Mold design encompasses various elements like gate size, runner system, and venting. Each component plays a vital role in determining how efficiently the material flows within the mold cavity.
-
Gate Size: The gate is the entry point for molten plastic into the mold. A well-sized gate allows for an adequate flow rate, preventing issues such as jetting or burn marks. Adjusting gate dimensions can help manage the injection rate to suit different materials and product requirements.
-
Runner Layout: Runners channel the molten plastic from the machine nozzle to the gate. Their design, whether they are hot or cold runners, directly impacts the flow characteristics and speed. A streamlined runner system minimizes pressure loss and enhances the injection rate.
-
Venting: Proper venting is essential for air escape during injection. Without adequate vents, trapped air can hinder filling and lead to defects like voids or burn marks. Optimizing vent placement ensures that air is efficiently expelled, allowing for a smoother injection process.
Impact on Cycle Time and Product Quality
An efficient mold design can significantly reduce cycle times by ensuring that materials fill the mold quickly and evenly. This not only increases production throughput but also maintains material integrity by preventing premature cooling or stress concentration in certain areas.
Mold Design Element | Effect on Injection Rate |
---|---|
Gate Size | Controls entry flow, affects fill speed |
Runner System | Influences flow dynamics and pressure loss |
Venting | Allows air escape, prevents defects |
Properly designed molds facilitate higher injection rates while maintaining product quality. For instance, an optimized gate size and runner layout can accommodate rapid injection without causing warpage or sink marks.
Challenges and Considerations
While mold design aims to optimize injection rate efficiency, several challenges must be considered:
-
Material Compatibility: Different plastics require different flow characteristics. Mold designs must be tailored to accommodate these variations to prevent issues like incomplete filling or excessive flashing.
-
Complex Geometries: Intricate product shapes may necessitate specific mold designs to ensure uniform flow distribution. This might involve advanced techniques like conformal cooling or custom runner geometries.
Understanding these dynamics empowers manufacturers to make informed decisions that enhance production efficiency. By focusing on mold design optimization5 and considering factors like material properties and product complexity, manufacturers can achieve superior outcomes in their injection molding processes.
Gate size affects injection rate efficiency.True
The gate size controls the entry flow, impacting fill speed.
Venting has no effect on injection rate efficiency.False
Proper venting allows air escape, preventing defects and aiding flow.
How Can Machine Performance Be Optimized for Better Injection Rates?
Optimizing machine performance is pivotal for achieving efficient injection rates in molding processes.
Machine performance optimization involves calibrating injection systems, maintaining equipment, and ensuring compatibility with materials. This leads to enhanced injection rates, improving product quality and production efficiency.
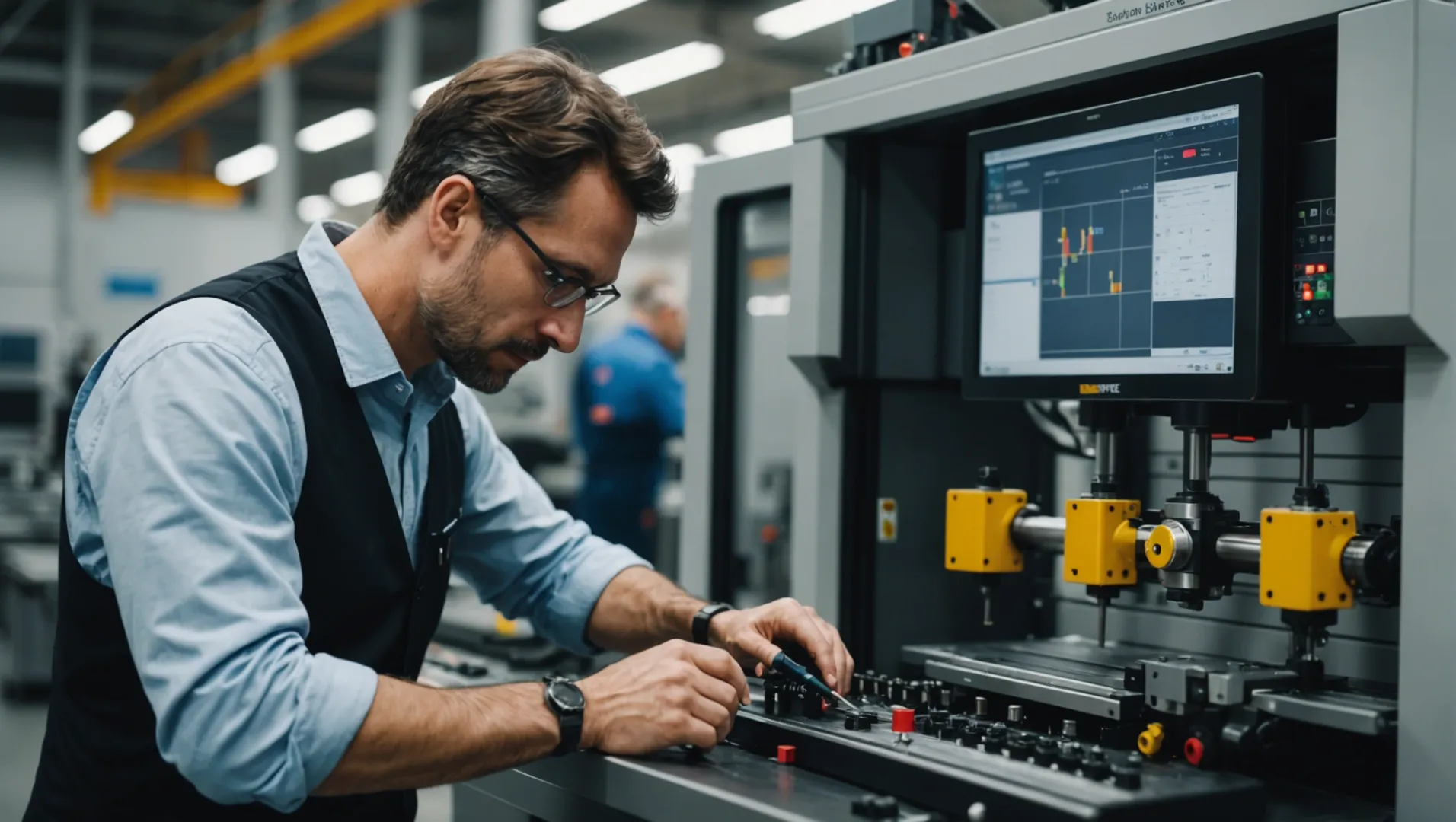
Calibration of Injection Systems
To optimize machine performance for better injection rates, regular calibration of the injection systems is essential. Calibration ensures that the machine delivers the precise amount of force and speed needed to achieve the desired injection rate. This can be achieved by adjusting the screw speed, pressure settings, and other relevant parameters. Regular calibration helps in maintaining consistency and reducing variability in production outcomes.
Maintenance of Equipment
Routine maintenance of injection molding machines is crucial. This includes checking and replacing worn-out parts, lubricating moving components, and ensuring that the hydraulic and electrical systems are functioning correctly. A well-maintained machine operates efficiently and is less likely to encounter unexpected downtimes that can affect injection rates. Predictive maintenance strategies6 can also be employed to foresee potential failures and address them before they impact production.
Compatibility with Material Properties
Machine settings must be compatible with the materials being used. Different plastics exhibit varied flow characteristics; hence, machines should be adjusted to accommodate these differences. For example, plastics with higher viscosity may require adjustments in temperature and pressure to ensure optimal flow. Material compatibility charts7 can provide valuable guidelines for setting machine parameters that align with specific material properties.
Leveraging Advanced Technologies
Incorporating advanced technologies such as smart sensors and automation can significantly enhance machine performance. Smart sensors can monitor real-time data, enabling quick adjustments to maintain optimal injection rates. Automation reduces human error and increases the precision of machine operations.
Training and Skill Development
Lastly, investing in the training and development of operators can also contribute to optimizing machine performance. Well-trained operators can identify issues quickly and adjust machine settings to maintain optimal injection rates. They are also better equipped to implement new technologies and maintenance practices effectively.
By focusing on these key areas, manufacturers can ensure their machines are well-optimized to deliver superior injection rates, ultimately enhancing product quality and manufacturing efficiency.
Regular calibration enhances injection rates.True
Calibration ensures precise force and speed, improving consistency.
Automation increases human error in machine operations.False
Automation reduces human error, enhancing precision and efficiency.
Conclusion
By understanding and adjusting the injection rate, we can significantly improve injection molding quality, leading to better products and enhanced manufacturing processes.
-
Explores how different plastic fluidities impact molding processes.: The fluidity of plastic molding material refers to the ability of plastic materials to flow within the injection mold in the manufacturing of plastic products. ↩
-
Compares fluidity and other properties of these common plastics.: Polypropylene is cheaper and more flexible but has lower impact resistance compared to polycarbonate which is stronger, more transparent, and more heat … ↩
-
Explore how gate design affects plastic flow and product quality.: Compare manual and automatic injection molding gate trimming techniques, and discover crucial design considerations. ↩
-
Learn how material selection influences design flexibility and molding outcomes.: Learn how to select the right material for your injection molding design with this technical overview of thermoplastic resins. ↩
-
Explore techniques to improve mold efficiency and production quality.: Get in-depth design advice to optimize your plastic parts for injection molding. Designing with moldability in mind can accelerate production time and … ↩
-
Learn how predictive maintenance prevents machine failures and boosts efficiency.: We introduce a generalized framework for implementation of predictive maintenance in injection molding process by integrating a variety of different data … ↩
-
Find guidelines for setting machine parameters according to material properties.: Access the Chemical Resistance Chart at Plastics International to select the right materials for your needs. Ensure compatibility and durability for your ↩