Balancing hardness and toughness in materials is similar to discovering life’s perfect balance. People need to pick smart and lasting options very carefully.
Finding the right balance between hardness and toughness matters greatly. Mold type, plastic material features and work conditions are key. Small precision molds need high hardness. Hardness increases accuracy. Large complex molds need more toughness. Toughness helps manage stress.
I remember my first big project at the factory. My job was to design a mold for a complicated electronic part. The task carried great importance and I learned that finding the right balance involved more than just technical details. It was about really understanding the small details of the materials.
Tiny precision molds need to be very hard – around 50-54HRC – to keep accuracy sharp. But toughness is also very important; it’s like wearing a seatbelt for surprise bumps. Very important.
Larger, more complex molds, such as those for car parts, present a different challenge. Here, toughness is the key because these molds must handle a lot of pressure without failing. Toughness should be about 8-10J/cm² while reducing hardness slightly. Important matter.
Then there are different types of plastic. Highly filled plastics are rough, needing a hard outer layer to avoid wear. They also create stresses inside that can break a mold if it isn’t tough enough.
In the end, understanding these delicate balances is like creating art. Each material has its own unique properties and as designers, we need to listen and pay attention to build things that are both beautiful and strong.
Small precision molds require higher hardness.True
Small precision molds need hardness for maintaining dimensional accuracy.
Large complex molds prioritize hardness over toughness.False
Large complex molds prioritize toughness to withstand stress.
How Does Mold Type Affect Hardness and Toughness Balance?
Picture a world where the smallest details in mold design decide your product’s success. This scenario is my everyday challenge. Balancing hardness and toughness in mold materials is vital. Perfection is the goal.
The mold type is crucial in balancing hardness and toughness. Its size, complexity and working conditions are important factors. Smaller molds usually need higher hardness. Larger molds demand greater toughness to function well. This is very important.
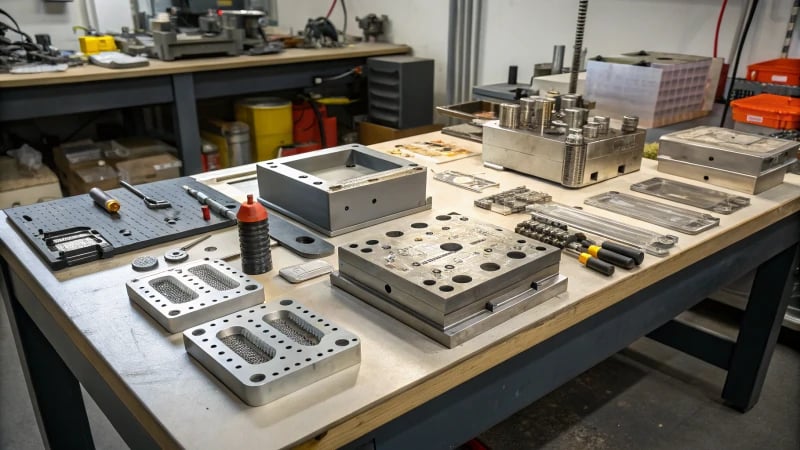
Mold Size and Structure
I worked with tiny precision molds and noticed how important every tiny part was. Each mold required strong hardness (50-54HRC) for perfect accuracy. They also needed to be tough (3-5J/cm²) to survive small accidents. It’s like putting together a delicate watch. Every piece should fit just right.
In contrast, I discovered that large molds for car parts focused on toughness (8-10J/cm²). They needed to handle a lot of pressure and bend without breaking. It’s like building a skyscraper. Stand firm, but sway in the wind.
Mold Type | Hardness (HRC) | Toughness (J/cm²) |
---|---|---|
Small Precision Mold | 50-54 | 3-5 |
Large Complex Mold | 48-50 | 8-10 |
Plastic Material Characteristics
I remember handling projects with tough plastics filled with particles. These particles were always wearing down the mold. We needed very hard molds (52-56HRC) to resist wear, but flexible enough to avoid cracks (4-6J/cm²). Think of it as finding the right shoes for running a long marathon – strong but flexible.
With softer plastics like soft PVC, the challenge was not about wear. It was more about dealing with them sticking to the mold. A softer mold (46-48HRC) worked fine if it stayed tough (6-8J/cm²) to prevent bending when removing plastic.
Working Environment Considerations
Working in hot places taught me materials act differently when warm. We used special die steel to keep molds strong with balanced hardness (48-52HRC) and toughness (5-7J/cm²). Think of wearing layers to stay warm. Materials needed to work well even when hot.
For molds used over and over, like in big productions, the trick was finding a balance between hardness (50-54HRC) and toughness (4-6J/cm²). It’s like making a long-lasting bridge—strong and reliable.
Learning about these things showed me how choosing the right mold helps in making things efficiently and well. I really improved designs for certain uses—strong and efficient manufacturing became possible.
For more ideas on choosing mold materials, check this guide1.
Small precision molds need 50-54HRC hardness.True
Small molds require high hardness for dimensional accuracy and quality.
Large complex molds prioritize 10-12J/cm² toughness.False
Large molds need 8-10J/cm² toughness to handle injection pressures.
How Do Plastic Material Characteristics Influence Material Choice?
Do you ever ask yourself why selecting the correct plastic material is vital for your project?
Plastic properties such as hardness, toughness and thermal resistance are important in selecting materials. These features decide if the plastic fits well for certain environments and functional needs. It results in the best performance. Also, it affects durability. Costs might be very favorable for your purpose.
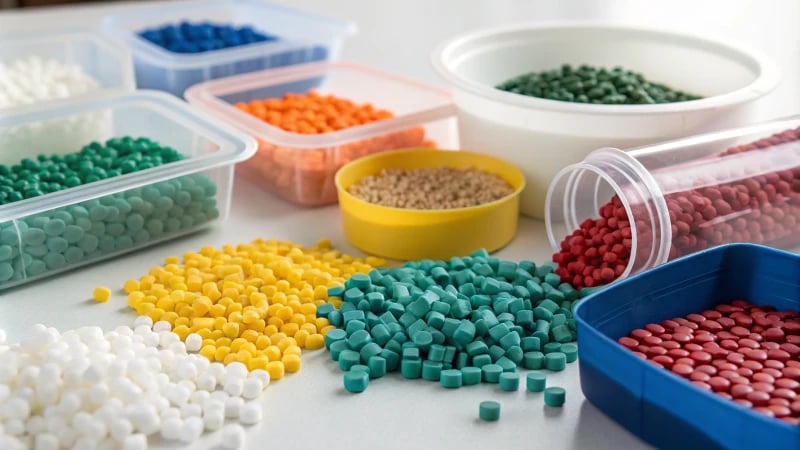
Understanding Plastic Characteristics
When I first started with plastics, the different qualities amazed me. Knowing these traits isn’t just for learning; it’s key to wise design choices. Below are important properties that I rely on:
Property | Definition |
---|---|
Hardness | Resistance to surface deformation. Affects wear resistance. |
Toughness | Ability to absorb energy and resist fracture. |
The Role of Hardness and Toughness
-
Highly Filled Plastics:
- Using plastics filled with glass fiber2 taught me that high hardness (52-56HRC) protects against wear from fillers.
- Toughness (4-6J/cm²) prevents cracking under pressure.
-
Soft Plastics:
- Softer plastics like PVC need lower hardness (46-48HRC) because they wear less.
- Yet, they still need good toughness (6-8J/cm²) for demolding.
Tailoring Material for Specific Mold Types
-
Small Precision Molds:
- Creating small molds, I find high hardness (50-54HRC) crucial for accuracy.
- Balancing with moderate toughness avoids damage from impacts.
-
Large Complex Molds:
- Large molds, much like solving a puzzle, need more toughness (8-10J/cm²) due to injection pressures.
- A bit lower hardness helps with stress issues.
Environmental Considerations
High Temperature Environments
Working in hot environments3 challenges me to keep things stable. Using materials like hot-working die steels keeps hardness and toughness even when hot. This is vital for long-term results.
High Life Requirement Molds
Molds used often need balanced hardness (50-54HRC) and toughness (4-6J/cm²). Keeping accuracy over many uses is important to avoid wearing out.
Exploring these aspects, I’ve learned to choose wisely and really improve product efficiency. My friend Jacky also excels by balancing looks and function.
Highly filled plastics need high hardness for wear resistance.True
Highly filled plastics require high hardness (52-56HRC) to resist wear from fillers.
Soft plastics require lower toughness than hard plastics.False
Soft plastics need higher toughness (6-8J/cm²) to withstand demolding forces.
Why Is the Working Environment Crucial for Material Performance?
Have you ever thought about why some materials work better in particular places? This guide helps you learn how the environment affects how materials behave.
The working environment greatly changes how materials perform by modifying conditions like temperature, humidity and pressure. These factors impact the strength and effectiveness of materials. Designers and producers must really think about them. It is very important.
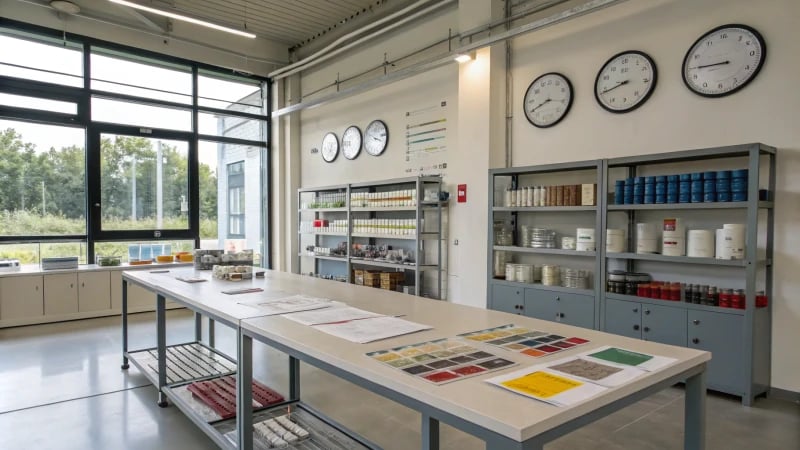
Temperature’s Role in Material Performance
Think of working with mold steel in hot conditions. It resembles baking a cake – if the temperature is off, the outcome won’t be good. Mold steel must keep its properties to be dependable when it heats up. A few degrees can change how hard or strong the material is, which impacts the whole production line.
Temperature | Hardness (HRC) | Toughness (J/cm²) |
---|---|---|
Room Temp | 50-54 | 4-6 |
High Temp | 48-52 | 5-7 |
These numbers are not just figures; they are crucial for mold survival in high heat. Learn more about high temperature environments4.
Impact of Humidity and Pressure
Baking on a humid day shows how moisture can alter everything. The same goes for materials. Humidity influences how they grow and wear out, especially in mass production molds. Once, a batch of molds almost failed because we ignored plant moisture levels.
- High Humidity: The chance of rust goes up, needing materials that resist it.
- Pressure Variations: Pushing on a sponge and a rock is different – pressure affects durability, needing stronger materials.
Materials like those used for high life requirement molds need specific balances between hardness and toughness to withstand varied humidity levels.
Balancing Hardness and Toughness
Finding the right mix of hardness and toughness is important. Many hours go into adjusting these for small precise molds and big complex ones, each needing something special.
- Small Precision Molds: Like gentle watchmakers; need high hardness but medium toughness.
- High hardness (50-54HRC) with moderate toughness (3-5J/cm²).
- Large Complex Molds: More like strong builders; need less hardness but more toughness for stress.
- Lower hardness (48-50HRC) but higher toughness (8-10J/cm²).
These adjustments ensure that molds withstand different operational stresses, maintaining accuracy and longevity.
Material Adaptation in Various Environments
It’s interesting how materials change, like dressing for summer or winter. Filled plastics need more hardness to avoid wearing out, while softer plastics need more toughness for exact molding.
Highly Filled Plastics versus Soft Plastic environments illustrate how materials must adapt:
- Highly Filled Plastics: Require higher hardness (52-56HRC) to resist wear.
- Soft Plastics: Demand higher toughness (6-8J/cm²) for demolding accuracy.
Understanding these changes is more than just technical; it’s a plan that could really change how we pick materials and design molds. From car dashboards to tiny electronics, getting this right is like the harmony of an orchestra – it makes everything work beautifully together. These insights do more than solve current problems; they open doors for new solutions, maybe even changing industry norms. Further insights5 into these changes might lead to amazing breakthroughs.
High temperature reduces mold steel hardness.True
High temperatures lower mold steel hardness from 50-54 HRC to 48-52 HRC.
Humidity increases the toughness of all materials.False
Humidity can cause corrosion, not necessarily increase toughness.
How Do You Ensure Molds Meet High Life Requirements?
Building long-lasting molds involves more than just choosing the right materials. It means creating a legacy marked by accuracy and strength.
Designing molds with high life requirements needs a balance between hardness and toughness. Mold type, material characteristics and working environment are important factors. Durable and precise molds are essential for long use. Molds must remain strong. Very strong and reliable!
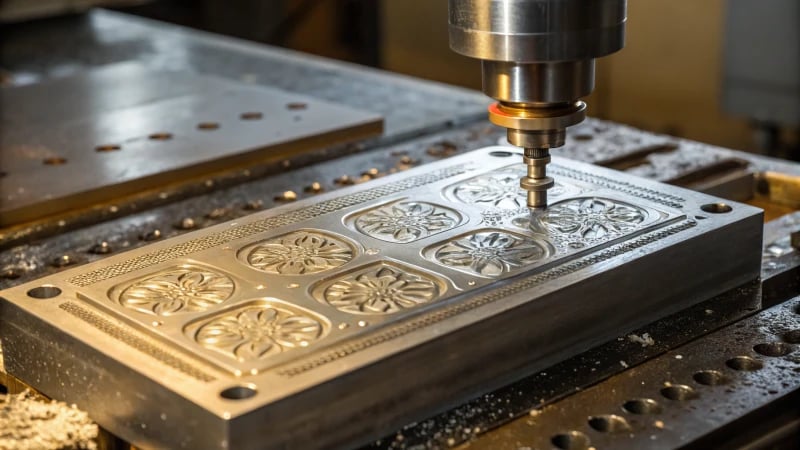
Understanding Impact of Mold Type
Choosing a material for a mold is like picking the right clothes for a special event. You need to know exactly what role it will play. I remember working on tiny molds6 for electronic parts. These molds needed to be very hard (50-54HRC) to keep their shape. For big and complicated molds, such as those for car parts, toughness (8-10J/cm²) became very important. It was like dressing for an adventure in the wild – practicality was key.
Balancing Material Traits
The plastic type you work with changes everything. Imagine it like cooking; ingredients define the dish. Plastics filled with many particles, similar to coarse flour, need more hardness (52-56HRC) to resist wear. Soft plastics are more like butter – requiring a gentle approach but more toughness to manage without damage. It’s important to think about how much plastic filler7 wears down the molds.
Plastic Type | Hardness (HRC) | Toughness (J/cm²) |
---|---|---|
Highly Filled | 52-56 | 4-6 |
Soft Plastic | 46-48 | 6-8 |
Adapting to Conditions
Consider entering a sauna in a wool sweater – dealing with high heat calls for smart material choices. Molds used in heat must stay cool, like those made from hot working die steel. Hardness of 48-52HRC and toughness of 5-7J/cm² help molds remain stable under heat. Handling high temperature8 plastics means focusing on heat’s impact on molds.
Long-Lasting Molds for High Use
Running a marathon demands stamina – molds used millions of times require endurance too. Wear resistance is crucial here. It’s as if ensuring shoes have strong soles. Hardness between 50-54HRC and toughness from 4-6J/cm² help avoid cracks, letting molds stay precise through many cycles.
Requirement | Hardness (HRC) | Toughness (J/cm²) |
---|---|---|
High Life Molds | 50-54 | 4-6 |
Recognizing these factors changes mold design into an art, crafting longevity and reliability in different production settings. Explore each element to better match designs and materials to their specific purposes.
High life molds require hardness of 50-54HRC.True
High life molds need 50-54HRC hardness for wear resistance and durability.
Soft plastics require molds with high toughness of 8-10J/cm².False
Soft plastics need lower toughness, typically 6-8J/cm², not 8-10J/cm².
Conclusion
Achieving the right balance between hardness and toughness in molds is crucial for performance, influenced by mold type, plastic characteristics, and working conditions.
-
Gain insights into selecting appropriate mold materials for various injection molding applications. ↩
-
Explore this link to understand why high hardness is crucial in handling abrasive fillers in plastics. ↩
-
Learn about materials that retain their properties at high temperatures, ensuring mold longevity and stability. ↩
-
Learn how high-temperature die steel maintains stability, crucial for long-term mold operations. ↩
-
Explore how environmental factors influence material properties in manufacturing settings. ↩
-
Learn more about why small precision molds need high hardness for accuracy. ↩
-
Discover how highly filled plastics affect mold wear and durability. ↩
-
Find out how high temperatures influence mold performance and material choice. ↩