Have you ever wondered how so many everyday items are made?
Injection molding is a game-changing manufacturing process that allows for the efficient production of a wide array of products, including plastic tableware, electronic shells, automotive parts, medical devices, and packaging materials. It enables mass production with high precision and cost efficiency across numerous industries.
While this brief overview scratches the surface of injection molding’s vast applications, stick around as we dive deeper into specific examples and benefits that highlight why this process is indispensable in today’s industrial landscape.
Injection molding is used for manufacturing plastic tableware.True
Plastic tableware like plates and bowls are mass-produced using injection molding.
How Does Injection Molding Enhance Daily Necessities?
Injection molding revolutionizes daily necessities, transforming ordinary items into affordable, durable, and stylish essentials.
Injection molding enhances daily necessities by enabling mass production of diverse and intricate plastic items like tableware, containers, toys, and household goods. This process ensures cost-effectiveness, high efficiency, and versatility in design, meeting the varied demands of modern consumers.
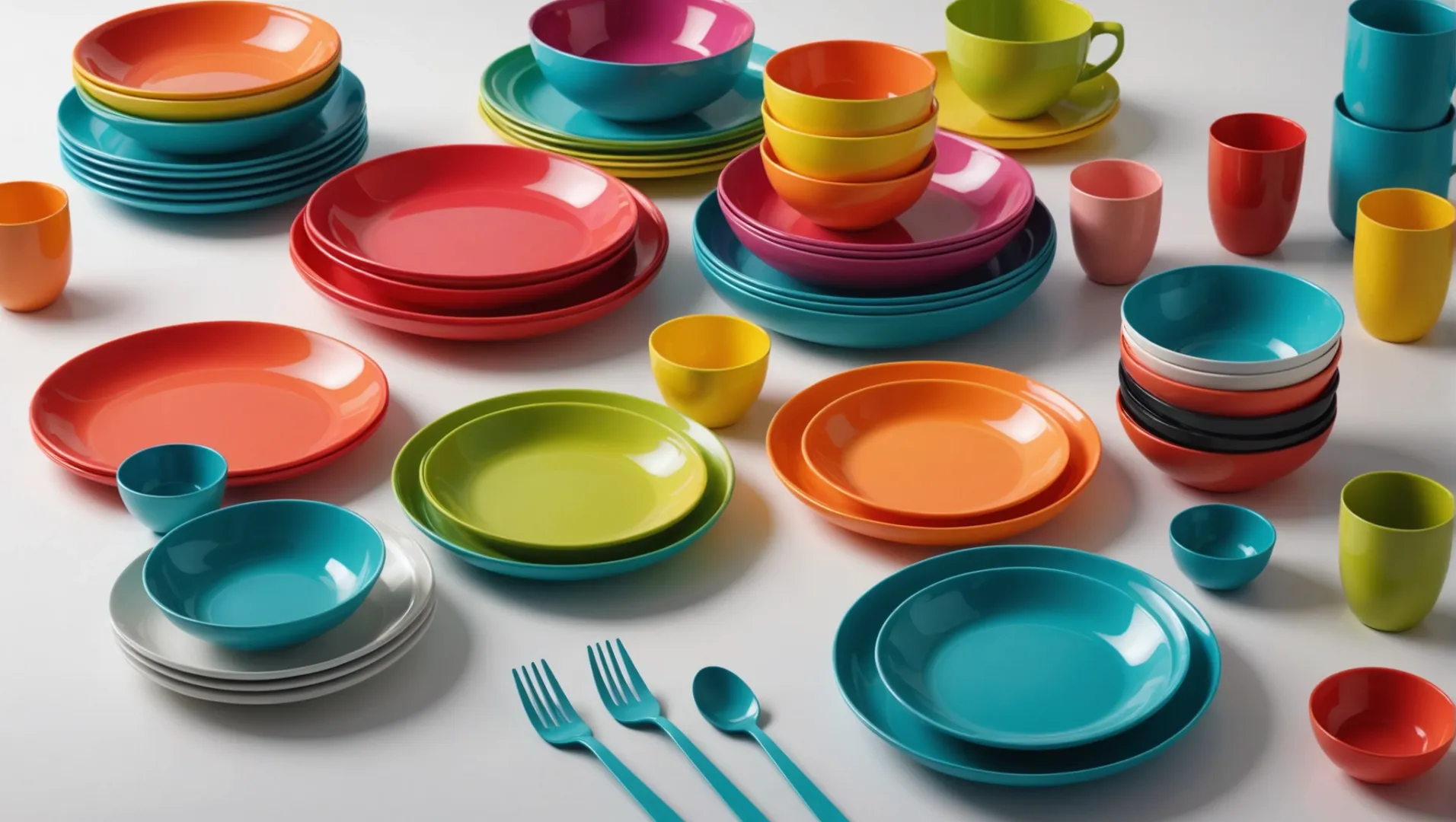
The Role of Injection Molding in Plastic Tableware
From vibrant dinner plates to intricately designed chopsticks, plastic tableware1 owes its accessibility and variety to injection molding. This process allows manufacturers to produce large quantities at low costs while maintaining high production efficiency. It also offers the flexibility to create unique shapes and colors, catering to diverse consumer tastes.
Versatility in Plastic Containers
Plastic containers like water cups, beverage bottles, and trash cans benefit significantly from injection molding. These items require good sealing and durability, attributes injection molding provides by creating robust structures resistant to falls and wear. This reliability ensures that everyday storage solutions are both practical and long-lasting.
Precision in Plastic Toys Manufacturing
Toys such as building blocks and puzzles often have complex shapes that demand precision. Injection molding meets these requirements by accurately shaping parts to fit stringent design specifications. This precision guarantees that toys not only meet safety standards but also deliver the intended play experience.
Household Items and Strength Requirements
Household goods like stools, chairs, and storage boxes must be strong and stable. Injection molding uses materials that meet these needs, producing items that can withstand daily use without compromising on quality or performance. This process is key to manufacturing reliable and sturdy household essentials that support everyday life.
Injection molding reduces the cost of plastic tableware.True
Injection molding allows mass production, lowering costs significantly.
Plastic toys made by injection molding are less precise.False
Injection molding ensures high precision, meeting design specifications.
What Role Does Injection Molding Play in Electronics?
Injection molding is a game-changer for the electronics industry, enabling precise, high-volume production of essential components.
In electronics, injection molding is vital for producing durable, precise components like device shells and electrical accessories. It ensures cost-effective mass production while maintaining high quality and consistency.
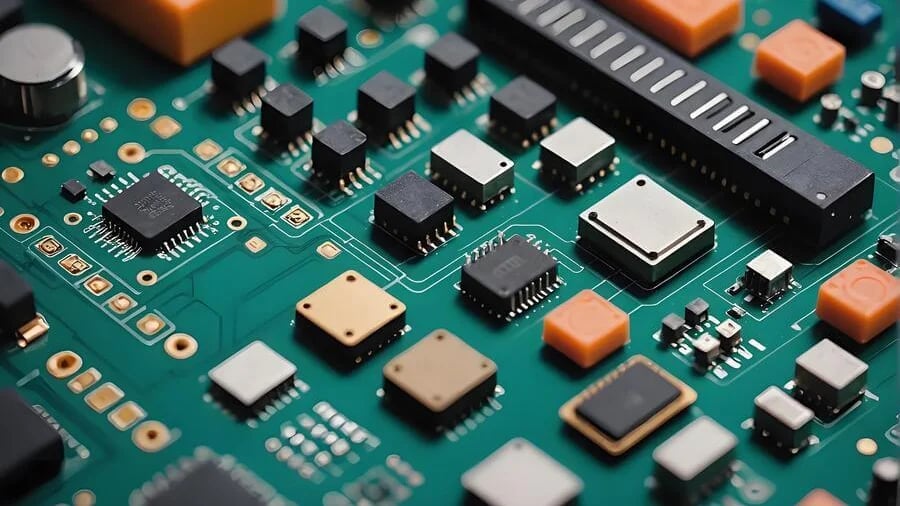
Injection Molding in Electronic Product Shells
Electronic product shells are crucial not only for protecting delicate internal components but also for ensuring effective heat dissipation and attractive aesthetics. Injection molding provides the flexibility to create complex and customized designs required by modern devices such as smartphones and computers.
For instance, mobile phone shells2 crafted through injection molding can be precisely designed to accommodate intricate internal configurations while offering durability and style. This process allows manufacturers to produce these shells in bulk, maintaining uniformity and quality across thousands of units.
Precision in Electrical Accessories
Electrical accessories, including plugs, sockets, and switch panels, demand precision manufacturing to ensure reliability and safety. Injection molding excels in producing components with exact dimensions, crucial for maintaining the consistency of electrical connections.
This precision is also vital for plastic parts within appliances where slight deviations can lead to functional failures. Injection molding ensures that each piece is identical, reducing the risk of defects and enhancing the overall performance of electrical products.
Enhancing Wire and Cable Accessories
The production of wire connectors and cable protective sleeves benefits significantly from injection molding. These accessories require properties like insulation and wear resistance, which are achievable through specialized injection-molded plastics.
This method ensures that each component meets stringent quality standards, safeguarding against electrical failures and prolonging the lifespan of cables and connectors. Moreover, it allows for innovative designs that contribute to more efficient installations and enhanced product performance.
Injection molding enables mass production of phone shells.True
Injection molding allows for the bulk production of uniform phone shells.
Electrical accessories are not made using injection molding.False
Injection molding is used to manufacture precise electrical accessories.
Why Is Injection Molding Crucial for Automotive Manufacturing?
Injection molding revolutionizes automotive manufacturing by enabling the production of durable and precise parts efficiently.
Injection molding is crucial for automotive manufacturing due to its ability to produce lightweight, durable, and cost-effective components. It ensures high precision and efficiency in creating both interior and exterior parts of vehicles, contributing to performance and aesthetic appeal.
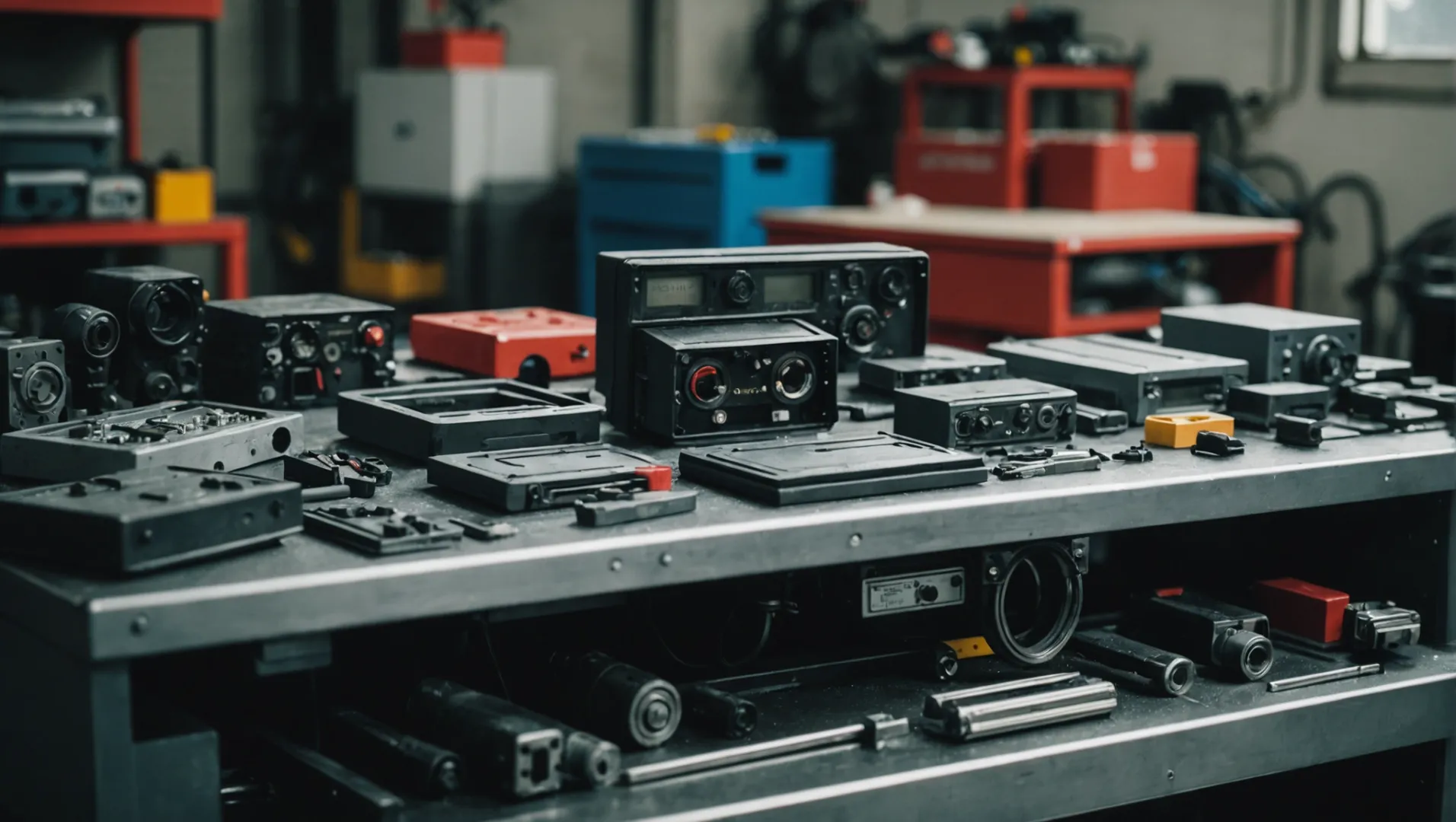
Versatility in Interior Components
Injection molding plays a vital role in producing interior parts3 like dashboards, center consoles, and door panels. These components not only demand aesthetic appeal but also require durability and resistance to wear and tear. Injection molding allows manufacturers to meet these demands by using a variety of materials that can be tailored for specific properties such as UV resistance or tactile quality.
This method also enables complex geometries and designs that are otherwise difficult to achieve, facilitating innovative designs that enhance the overall look and feel of a vehicle’s interior.
Enhancing Exterior Part Production
For exterior automotive components like bumpers, grilles, and mirror housings, injection molding is indispensable. These parts require a balance between strength and lightweight characteristics to improve vehicle efficiency and safety. The process enables the use of advanced materials like thermoplastics, which can withstand harsh environmental conditions while maintaining structural integrity.
Moreover, injection molding allows for consistent production with minimal defects, ensuring each component meets stringent industry standards for safety and performance.
Engine and Under-the-Hood Applications
Injection molding also extends to engine peripherals such as intake manifolds and oil pans. These components must endure high temperatures and pressures, necessitating materials that provide both heat resistance and robust sealing capabilities. The precision of injection molding ensures these parts fit perfectly within engine assemblies, optimizing engine performance and longevity.
Cost Efficiency and Environmental Impact
From an economic perspective, injection molding significantly reduces manufacturing costs through automation and rapid production cycles. This efficiency is crucial in the automotive sector, where cost management directly impacts competitiveness. Additionally, the ability to recycle plastic waste into new components reduces environmental impact, aligning with the industry’s sustainability goals.
The significance of injection molding in automotive manufacturing cannot be overstated; its versatility, precision, and cost-effectiveness make it an essential process for producing high-quality vehicles.
Injection molding ensures durable automotive parts.True
Injection molding uses materials that enhance durability and resistance.
Injection molding increases vehicle weight significantly.False
It produces lightweight components, enhancing vehicle efficiency.
How Are Medical Devices Benefiting from Injection Molding?
Injection molding revolutionizes medical device manufacturing with precision, efficiency, and safety.
Injection molding benefits medical devices by enabling high-precision production of complex components, ensuring sterility, and offering cost-effective scalability. This method supports the creation of both disposable medical consumables and durable device casings, essential for modern healthcare demands.
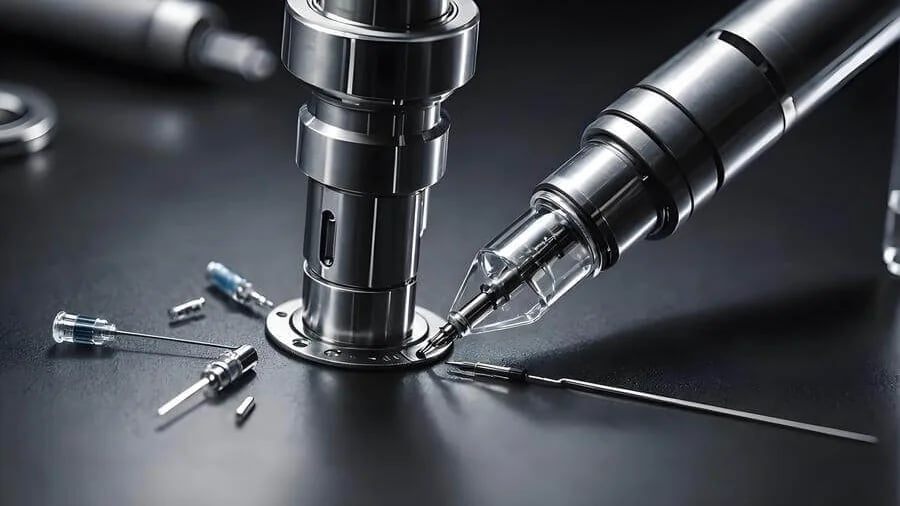
The Precision Advantage
One of the primary benefits of injection molding in medical device manufacturing4 is its precision. The process allows for the creation of intricate components with tight tolerances, which is crucial for devices such as syringes, infusion sets, and blood collection tubes. These components must meet stringent regulatory standards to ensure patient safety and efficacy.
For example, disposable syringes require precise calibration to deliver accurate dosages. Injection molding ensures that each syringe is identical, minimizing the risk of dosage errors.
Sterility and Biocompatibility
Medical devices, especially consumables, must maintain high levels of sterility and biocompatibility. Injection molding supports these requirements by producing components in controlled environments using medical-grade materials. This process reduces the risk of contamination, which is vital for devices like blood collection tubes and infusion sets.
The use of biocompatible plastics ensures that the products are safe for human use, reducing adverse reactions and improving patient outcomes.
Cost Efficiency and Scalability
Injection molding is known for its cost-effectiveness, making it an ideal choice for mass-producing medical devices. Once a mold is created, the cost per unit decreases significantly, allowing manufacturers to produce large quantities at a lower price point.
This scalability is particularly beneficial for high-demand items such as disposable medical consumables. The ability to produce vast quantities quickly meets the healthcare sector’s growing needs without compromising quality or increasing costs.
Versatility in Design
The versatility offered by injection molding is unmatched, allowing for the production of both simple and complex medical device components. This adaptability extends to the creation of durable medical device shells5, such as those used in monitors and ultrasound machines.
These shells require not only strength and protection but also aesthetic appeal and electromagnetic compatibility. Injection molding meets these demands, producing shells that protect sensitive electronics while providing a sleek design.
Medical Device | Injection Molding Benefit |
---|---|
Disposable Syringes | Precise dosage calibration |
Infusion Sets | Sterile production environment |
Blood Collection Tubes | Biocompatibility assurance |
Medical Device Shells | Durable protection and design |
By leveraging the benefits of injection molding, the medical industry can continue to innovate and meet the evolving needs of healthcare providers and patients alike.
Injection molding ensures sterility in medical devices.True
Controlled environments and medical-grade materials reduce contamination risk.
Injection molding is unsuitable for complex medical components.False
It enables high-precision production of intricate components efficiently.
Conclusion
Injection molding is a versatile and efficient process impacting various industries from consumer goods to automotive manufacturing. By understanding its applications, we can appreciate how it shapes our daily lives.
-
Explore the production process of plastic tableware via injection molding.: The cutlery is molded in step one in a cold mold, followed by step two in which the cutlery is annealed in a convection oven set at the PLA crystallization … ↩
-
Discover the precision and customization involved in crafting phone shells.: The process is usually filled with high mold temperature, high material temperature; The gate used is usually the point gate, and graded injection molding … ↩
-
Explore how injection molding transforms vehicle interiors with innovative designs.: Injection molding is better than other manufacturing techniques as it can create products with intricate forms, high-quality surface finishes, precise … ↩
-
Explore how precision impacts medical device safety and performance.: Precision molding stands as a critical stage that drives the reliability, safety, and effectiveness of these modern medical devices. ↩
-
Discover why injection molding is ideal for protective medical casings.: Medical device injection molding has a faster production time, and a lower cost per part, and uses medical-grade plastics that make it ideal for cases and … ↩