If you’re in the world of manufacturing, you know that precision is everything. Injection molding is no exception.
The key factors for achieving high precision in injection molding include mold design rationality, material properties like shrinkage rate and flowability, optimal process parameters such as temperature and pressure, and the accuracy of injection molding equipment.
Understanding these factors can drastically improve the efficiency and quality of your injection molding operations. Let’s dive deeper into each aspect together.
Mold design affects injection molding precision.True
Proper mold design ensures uniform material distribution, reducing defects.
How Does Mold Design Affect Precision in Injection Molding?
Mold design is pivotal in determining the precision and quality of injection molded products, influencing every aspect from product shape to material flow.
Mold design impacts precision in injection molding through cavity structure, demolding design, processing accuracy, and maintenance. Effective mold design ensures uniform material distribution, precise assembly, and longevity of molds, directly affecting the dimensional accuracy of the final product.
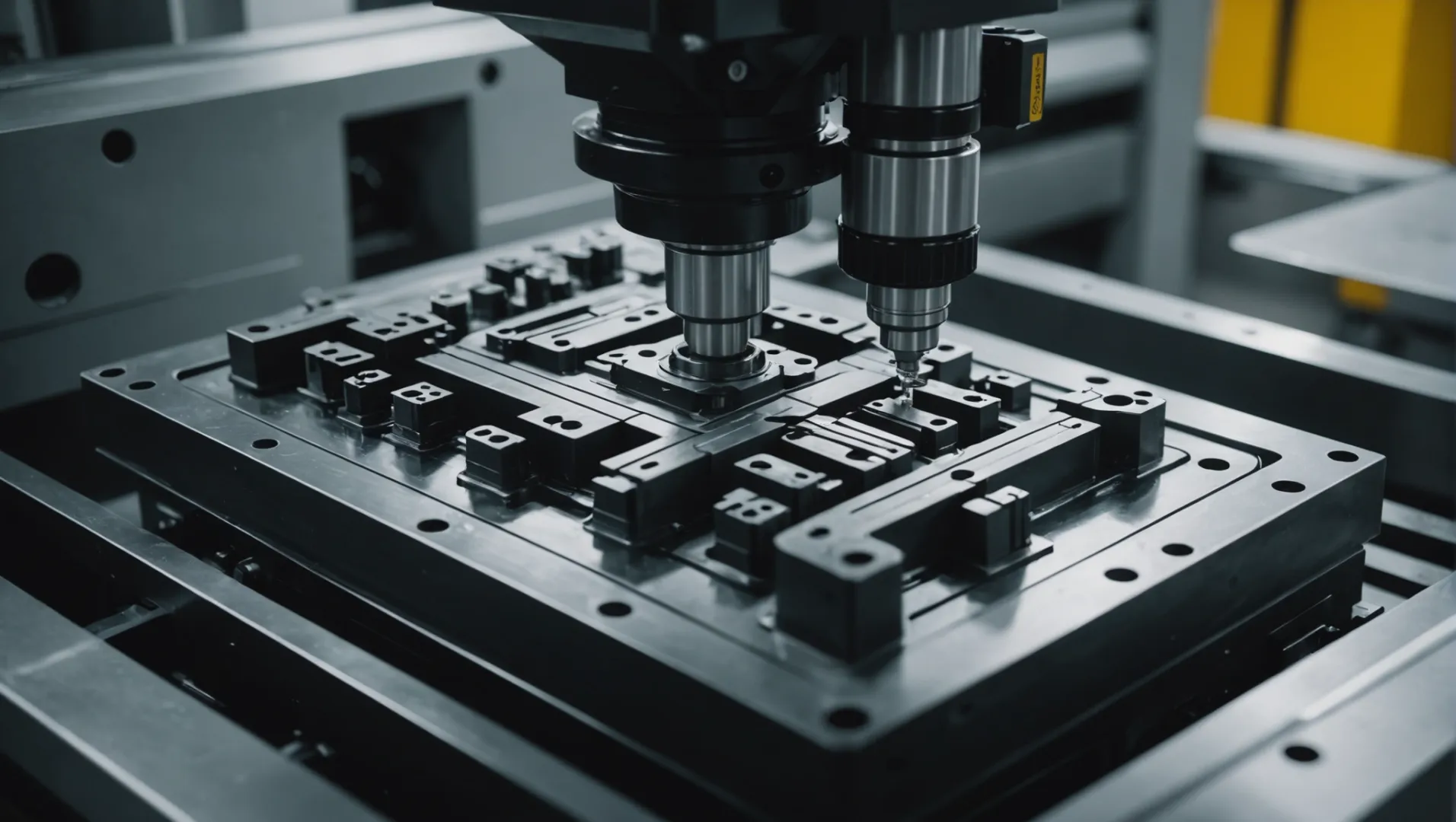
Cavity Structure Design
The cavity structure1 is crucial for achieving precision in injection molding. A well-designed cavity ensures that the melted plastic fills uniformly, preventing defects like voids or warping. For complex shapes, strategic placement of gates and runners is essential to maintain flow balance and avoid underfilling or overfilling.
Consider an intricate automotive component where the material must reach all sections without causing stress. Designing the cavity with these considerations allows for consistent quality across multiple production runs.
Demolding Structure Design
An efficient demolding structure2 ensures that products are released smoothly from the mold without compromising their integrity. A properly designed demolding slope can prevent strains or deformation during ejection.
For instance, electronic casings often have precise surface requirements. A poor demolding design could lead to scratches or distortions, affecting product functionality and aesthetics.
Manufacturing Accuracy
Processing Accuracy
High-precision processing equipment like CNC machines and EDM (Electrical Discharge Machining) are vital for achieving tight tolerances in mold components such as cores and sliders. This precision impacts the mold’s ability to produce parts that meet exact specifications.
Assembly Accuracy
Precision during the assembly of mold components is equally important. Tools and detection methods should ensure uniform assembly gaps and tight fits to preserve overall mold accuracy.
For example, a multi-component toy where each piece must fit perfectly requires meticulous assembly to avoid misalignment or gaps that could affect performance.
Mold Maintenance
Regular mold maintenance3 is necessary to sustain precision over time. Wear repair and cleaning ensure that molds remain in optimal condition, preventing accuracy degradation due to corrosion or residue build-up.
In long production cycles, neglected maintenance can lead to dimensional deviations, impacting product quality and leading to increased waste or rework.
Cavity design prevents defects like voids or warping.True
A well-designed cavity ensures uniform filling, preventing defects.
Neglected mold maintenance has no effect on product quality.False
Poor maintenance leads to dimensional deviations, affecting quality.
Why Is Material Selection Critical for Injection Molding Accuracy?
Material selection is pivotal in injection molding, affecting precision and product quality. Choosing the right material influences shrinkage, flowability, and thermal stability, crucial for dimensional accuracy.
Material selection impacts injection molding accuracy by influencing shrinkage rates, flowability, and thermal stability. Proper material choice ensures precise dimensions and optimal product performance, reducing defects and improving overall quality.
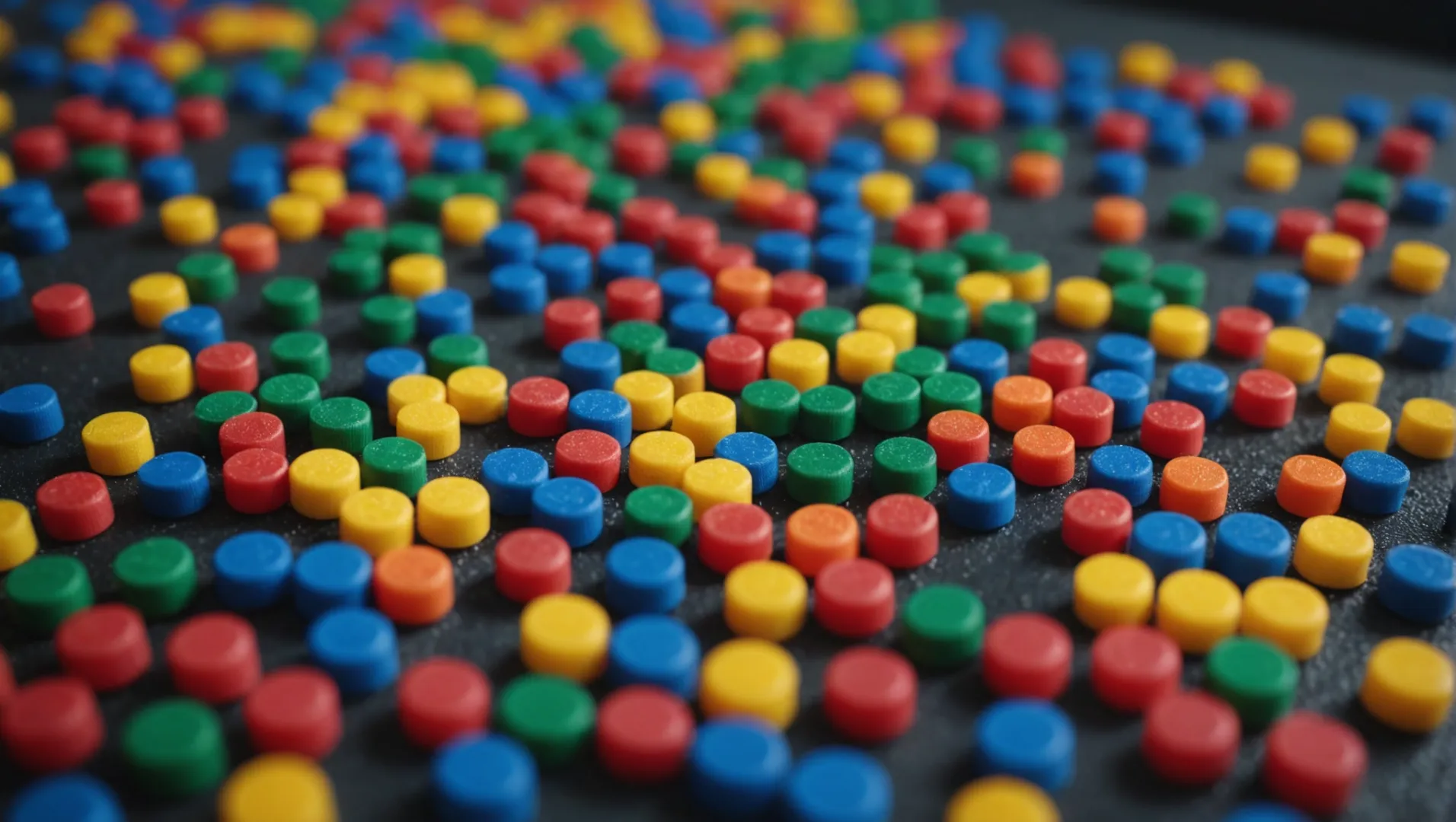
Understanding Shrinkage Rates
The shrinkage rate4 of a material is a fundamental factor affecting injection molding accuracy. Different plastics shrink at varying rates during cooling. Selecting materials with predictable shrinkage ensures that the final product meets the specified dimensions. For instance, crystalline plastics like polyethylene often exhibit higher shrinkage compared to amorphous plastics like polycarbonate.
Assessing Material Flowability
Flowability refers to how easily a material can fill the mold cavity. Materials with high flowability ensure that the molten plastic reaches all areas of the mold uniformly, minimizing defects like voids or incomplete filling. This is especially crucial for complex designs where uniform distribution is essential to maintaining precision. High-flow materials can also reduce cycle times by filling molds faster.
Evaluating Thermal Stability
Thermal stability determines a material’s resistance to decomposition at elevated temperatures during molding. Materials with poor thermal stability may degrade, leading to defects such as discoloration or compromised mechanical properties. Stable materials ensure consistent performance and dimensional accuracy across production runs.
Case Study: Polypropylene vs. Nylon
A practical example can be seen in the comparison between polypropylene and nylon. Polypropylene has excellent flowability and low shrinkage, making it suitable for parts requiring tight tolerances. In contrast, nylon, known for its toughness and high melting point, may exhibit greater shrinkage but provides superior mechanical strength, making it ideal for more robust applications.
By carefully considering these factors, manufacturers can select materials that optimize precision, reduce waste, and enhance product quality. For more insights into material selection strategies, explore resources on injection molding material characteristics5.
Polypropylene has lower shrinkage than nylon.True
Polypropylene exhibits low shrinkage, suitable for tight tolerances.
Amorphous plastics have higher shrinkage than crystalline ones.False
Amorphous plastics like polycarbonate have lower shrinkage rates.
What Role Do Process Parameters Play in Achieving Precision?
Precision in injection molding hinges significantly on process parameters like temperature, pressure, and speed. These parameters dictate the quality and accuracy of the final product.
Process parameters such as temperature, pressure, and speed are critical in determining the dimensional accuracy and quality of injection molded products. Proper adjustment and control of these parameters ensure optimal flow, fill, and cooling, leading to precise results.
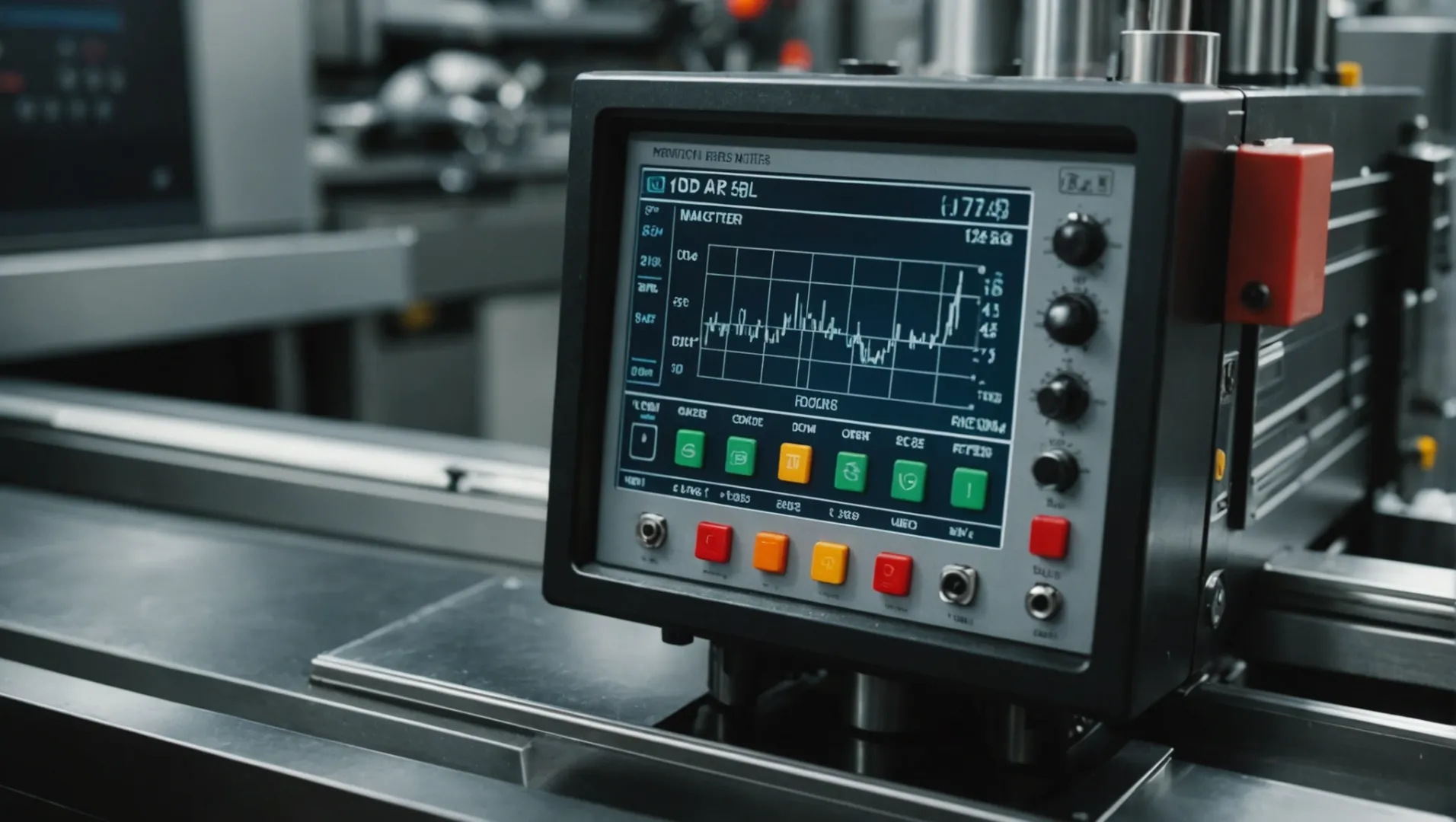
Temperature Control in Injection Molding
Temperature settings are vital for achieving precision in injection molding. The barrel temperature6 must be adjusted according to the material’s melting point to ensure proper flow without degradation. Similarly, mold temperature impacts the cooling rate, which affects shrinkage and dimensional stability.
For instance, if the barrel temperature is too high, it may cause material degradation, leading to defects such as warping or discoloration. Conversely, if it is too low, the material might not flow adequately, resulting in incomplete fills or weld lines. Thus, maintaining optimal temperature settings tailored to specific materials is crucial.
Importance of Pressure Management
Injection pressure is another crucial factor in molding precision. The pressure needs to be sufficient to fill the mold cavity completely but not so high that it causes flash or other defects. Adjusting the holding pressure can help mitigate shrinkage issues by ensuring consistent packing during the cooling phase.
The following table illustrates the impact of different pressure settings:
Pressure Setting | Potential Outcome |
---|---|
Low Pressure | Incomplete fills, low density |
Optimal Pressure | Full fills, balanced packing |
High Pressure | Flash, internal stresses |
The Role of Injection Speed
Injection speed influences the flow behavior of the material. A fast injection speed can lead to defects such as jetting or spray phenomena, while a slow speed might not fill the cavity before cooling occurs. The key is to find a balanced speed that allows for complete cavity filling while minimizing defects.
Adjusting the speed according to the complexity and size of the part being molded is essential. For intricate designs, a slower initial speed followed by a faster pace as the cavity fills can optimize flow dynamics.
Setting Holding Time and Pressure
The holding time and pressure are critical in preventing sink marks and ensuring dimensional accuracy. Holding too long or at too high a pressure can induce stresses that may cause cracking or deformation over time.
Monitoring and adjusting these parameters requires a thorough understanding of the material properties and mold design to achieve precision consistently.
By carefully managing these process parameters, manufacturers can enhance the precision of their injection molded products, ensuring quality and performance standards are met.
Temperature settings impact material flow in molding.True
Temperature affects the melting and flow of materials during molding.
High pressure always improves injection molding quality.False
Excessive pressure can cause defects like flash and internal stress.
How Does Equipment Maintenance Impact Injection Molding Quality?
Proper equipment maintenance is crucial in injection molding, directly influencing the quality and precision of the final products.
Equipment maintenance ensures that injection molding machines function optimally, reducing defects and improving product quality. Regular checks and servicing prevent wear and tear, ensuring accurate injection parameters and consistent operation.
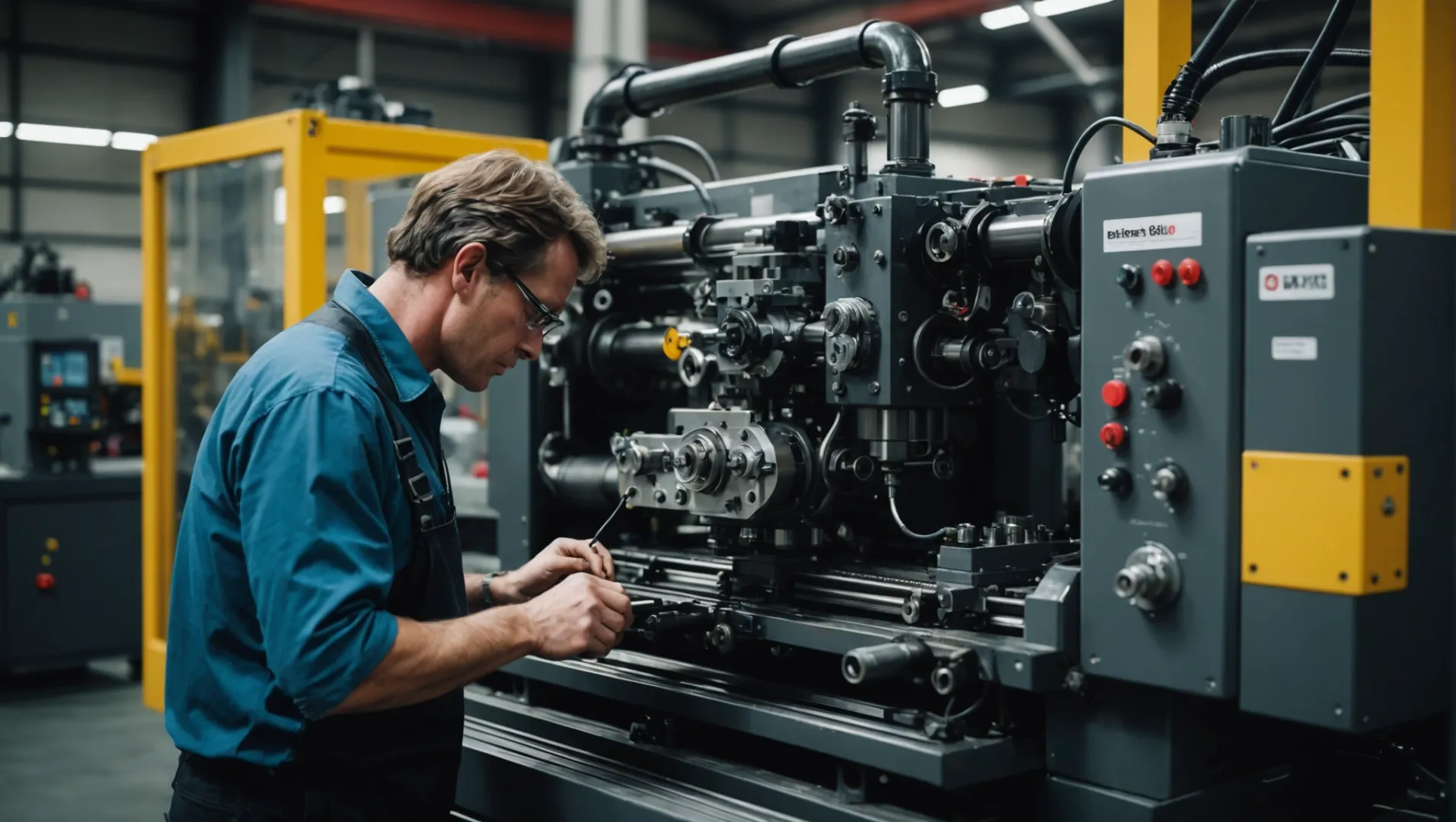
The Importance of Regular Equipment Checks
Injection molding machines are complex pieces of equipment requiring regular maintenance7 to ensure their precision components function correctly. Regular checks involve inspecting hydraulic systems, electrical connections, and mechanical parts, which helps in identifying potential issues before they escalate into major problems. For example, a malfunctioning hydraulic system can lead to inconsistent clamping force, resulting in defects like flashing or incomplete fills.
Preventive Maintenance and Its Benefits
Preventive maintenance is a proactive approach to managing equipment health. It includes scheduled servicing and part replacements based on usage metrics rather than waiting for components to fail. This method reduces unexpected downtimes and maintains the accuracy of parameters like injection pressure and speed. Consistent parameter control ensures high-quality molds with minimal dimensional deviations.
Maintenance Aspect | Potential Issue | Solution |
---|---|---|
Hydraulic System | Pressure fluctuations | Regular fluid checks |
Electrical Connections | Power inconsistencies | Routine inspections |
Mechanical Components | Wear and tear leading to part failures | Scheduled replacements |
The Role of Calibration in Maintaining Quality
Regular calibration of injection molding machines is essential. Calibration ensures that measurement devices and sensors on the machine provide accurate readings. An uncalibrated machine may display incorrect data, leading to errors in temperature settings or pressure applications, impacting the quality8 of the molded products.
Case Study: Prolonged Equipment Life through Maintenance
A study conducted in a high-volume manufacturing plant showed that implementing a robust maintenance program reduced machine downtime by 30% and extended the lifespan of the machines by 20%. This was achieved through detailed logs and predictive analytics that helped preemptively address issues before they resulted in costly repairs.
By focusing on these aspects of equipment maintenance, manufacturers can ensure the longevity and reliability of their injection molding machines, ultimately leading to superior product quality.
Regular maintenance reduces injection molding defects.True
Proper maintenance prevents wear, ensuring accurate machine operation.
Ignoring equipment checks leads to better product quality.False
Neglecting maintenance causes defects due to inconsistent parameters.
Conclusion
Mastering precision in injection molding involves careful attention to mold design, material selection, process control, and equipment maintenance. Implement these strategies for improved quality and reduced defects.
-
Learn how cavity design impacts material flow and product quality.: Cavity arrangement of precision injection mold should meet requirements of balance of runner and arrangement with main runner as center, and … ↩
-
Discover why proper demolding is key for product integrity.: Impact on Product Quality · Dimensional Accuracy: Precise mould design leads to parts that consistently meet specified tolerances. · Surface … ↩
-
Understand how maintenance prolongs mold life and ensures precision.: Routine maintenance ensures that you can make the best use of the mold. With regular maintenance, your regular operation does not cause stress … ↩
-
Learn about shrinkage rates’ impact on product dimensions.: The shrinkage of molded plastic parts can be as much as 20% by volume when measured at the processing and ambient temperature. ↩
-
Explore detailed guides on choosing the right materials.: In this guide, we explore the most common materials, their strengths, molding temperatures, common applications, and other important properties. ↩
-
Learn how barrel temperature influences flow and material integrity.: But the questions are: What temperature do you want the melt to be, and what temperature profile of the barrel zones will get what you want? ↩
-
Discover why consistent maintenance prevents costly machine failures.: However, like any machinery, injection molding equipment requires regular maintenance to ensure optimal performance, longevity, and safety. ↩
-
Understand how calibration ensures precision in molding processes.: After finished the machine calibration, the quality Difference is reduced by 67%. Abstract. Achieving production quality is a key issue faced in injection … ↩