Curious about how plastic devices start their journey? ABS injection molding is key.
The ABS injection molding process involves heating ABS plastic pellets until they melt and then injecting the molten plastic into a pre-designed mold. Once cooled, the mold opens to release a formed product, offering high strength and surface finish.
While it seems simple, achieving skill in this process involves knowing complicated material characteristics and exact mold creation. Investigate further to learn what drives ABS injection molding.
ABS injection molding uses acrylonitrile butadiene styrene.True
ABS represents the material applied in this molding process, famous for its characteristics.
What Are the Key Steps in ABS Injection Molding?
ABS injection molding uses a detailed method to change raw plastic into very good products.
The ABS injection molding process begins with material preparation and drying, followed by precise mold setup, injection of the melted ABS, cooling, and final demolding. Each step requires careful control of parameters to ensure product quality and efficiency.
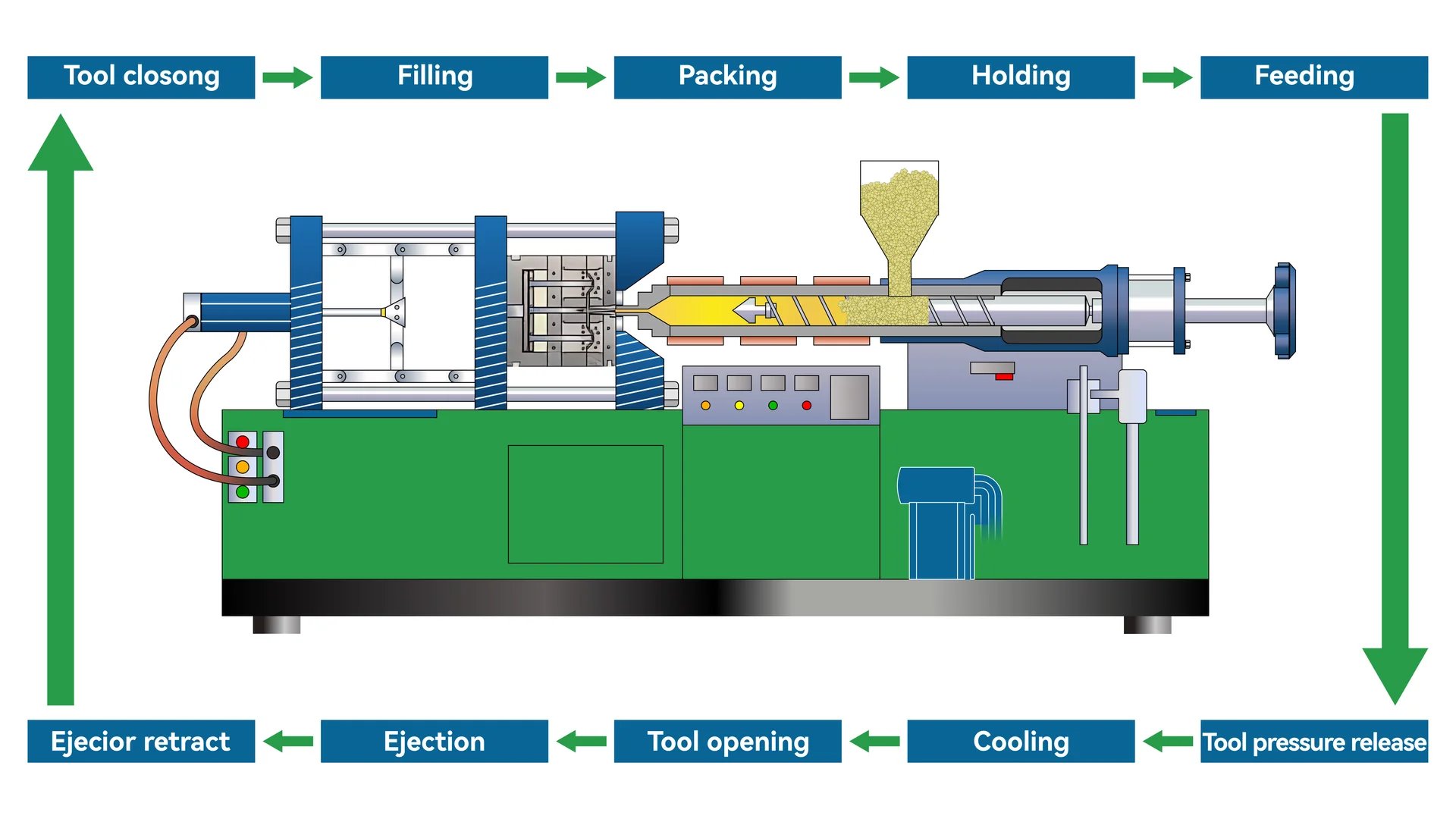
Material Preparation
The first important action in the ABS injection molding is getting the material ready. This includes choosing the right type of ABS resin suited for the product’s needs. It’s important to check for any impurities and moisture in the raw material.
Drying removes moisture from the ABS resin because leftover moisture might cause problems during molding. Normally, the resin dries at temperatures between 80 – 100°C for 2 – 4 hours until moisture is below 0.1%. This achieves the best flow and product quality during molding.
Mold Setup
Selecting the correct mold materials is key for strength and quality. For most uses, P20 steel is suggested due to its good processing and affordable cost. For items needing a better surface finish, 718 steel is better because of its greater hardness and resistance to wear.
The mold should include an efficient cooling system, with water channels put in the right places to keep even temperature in the mold. This arrangement helps in better productivity and product quality.
Injection Process
The injection step melts the ABS pellets, then this melted plastic goes into the mold cavity at controlled pressures and speeds. Parameters like injection pressure (70 – 150 MPa), injection speed (50 – 150 mm/sec) and screw speed (30 – 100 rpm) change based on product needs and material properties.
The right gate design—be it direct, side or spot gate—is necessary to balance filling speed and surface quality. Injection speed1 and pressure must be precisely handled to avoid issues such as flow marks or fusion lines.
Cooling and Demolding
Cooling is an important step where the molded part hardens. Cooling channels must be placed well to help even cooling without causing internal stress.
In the end, the mold opens and the part comes out. The ejector system—using pins, plates or barrels—must be designed to prevent bending or harming the product. Good ejection keeps products in their correct shape and size.
Learning these main steps in ABS injection molding helps creators produce steady and high-quality parts well. For more knowledge on improving these actions, think about searching more materials like mold design strategies2 or troubleshooting defects3.
ABS resin must be dried below 0.1% moisture content.True
ABS resin becomes better for molding when dried with less than 0.1% moisture.
P20 steel is unsuitable for general mold applications.False
P20 steel is suggested for its work quality and price.
Why Choose ABS for Injection Molding Over Other Plastics?
Picking the correct plastic is key for good injection molding. Why is ABS often chosen?
ABS, or Acrylonitrile Butadiene Styrene, is favored in injection molding due to its excellent balance of strength, toughness, and surface finish. It offers better processability and chemical resistance compared to many other plastics, making it ideal for diverse applications from automotive parts to consumer electronics.
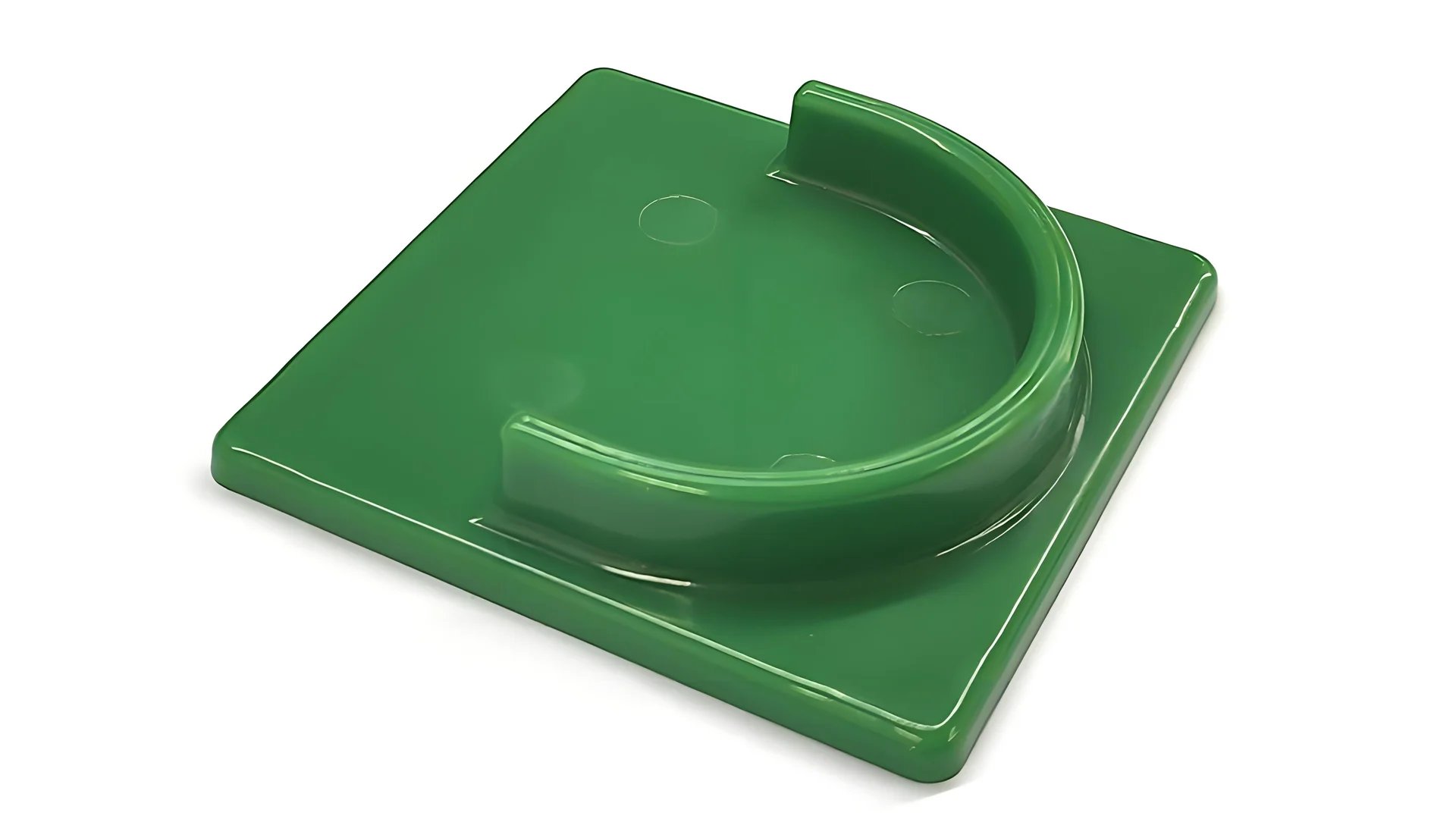
Using Benefits of ABS Over Other Plastics
When selecting a material for injection molding, ABS impresses with a great mix of properties.
Strength and Toughness: ABS has a strong mechanical nature with high pulling and bending strength. This suits products that require lasting durability. It offers more stiffness and heat resistance than polyethylene4 but costs more and is heavier.
Surface Look: The shiny surface of ABS makes it ideal for consumer items where appearance is important. Compared to polypropylene5, ABS delivers better looks and strength, though it is less resistant to weather.
Economic Value: While polycarbonate6 is stronger and more heat-resistant, ABS remains cheaper and simpler to mold, providing a big edge in large-scale settings.
Areas Where ABS Shines
ABS‘s traits make it useful in various fields:
- Home Appliances: Used for TV covers and fridge linings due to its tough and appealing surface.
- Car Industry: Common in inside parts like control panels where sturdiness and visual appeal are required.
- Toys and Office Tools: Its bright color keeping and ease of shaping suit toys and printer frames well.
Processing Benefits of ABS
Mold Design: ABS‘s steady shrinking rate (0.4-0.7%) eases mold planning, reducing issues from uneven shrinking in other plastics. This steadiness offers top-quality final products with few flaws.
Heat Stability: Able to handle up to 100°C, ABS tolerates higher processing heat than many plastics without losing product quality.
Points to Think About When Choosing ABS
Though it has many merits, consider these factors with ABS:
- Weight and Price: While having great traits, ABS‘s higher weight might not fit all uses. Its price can also exceed some options.
- Weather Tolerance: For uses needing lots of exposure to tough outdoor conditions, materials with better UV resistance might suit better.
Summary
ABS‘s mix of mechanical strength, visual quality, and processing ease makes it a top pick for injection molding in many sectors. By knowing its special advantages and downsides, producers can wisely use ABS to create sturdy, reliable products.
ABS offers superior surface finish over polypropylene.True
ABS is favored for its very shiny surface and strength.
Polycarbonate is more cost-effective than ABS.False
ABS costs less and processes more simply than polycarbonate.
How to Optimize Mold Design for ABS Injection Molding?
Improving mold design is important for successful ABS injection molding. This gives high-quality and faultless items.
To optimize mold design for ABS injection molding, focus on selecting appropriate mold materials, designing effective cooling systems, and ensuring uniform wall thickness to enhance product quality and reduce defects.
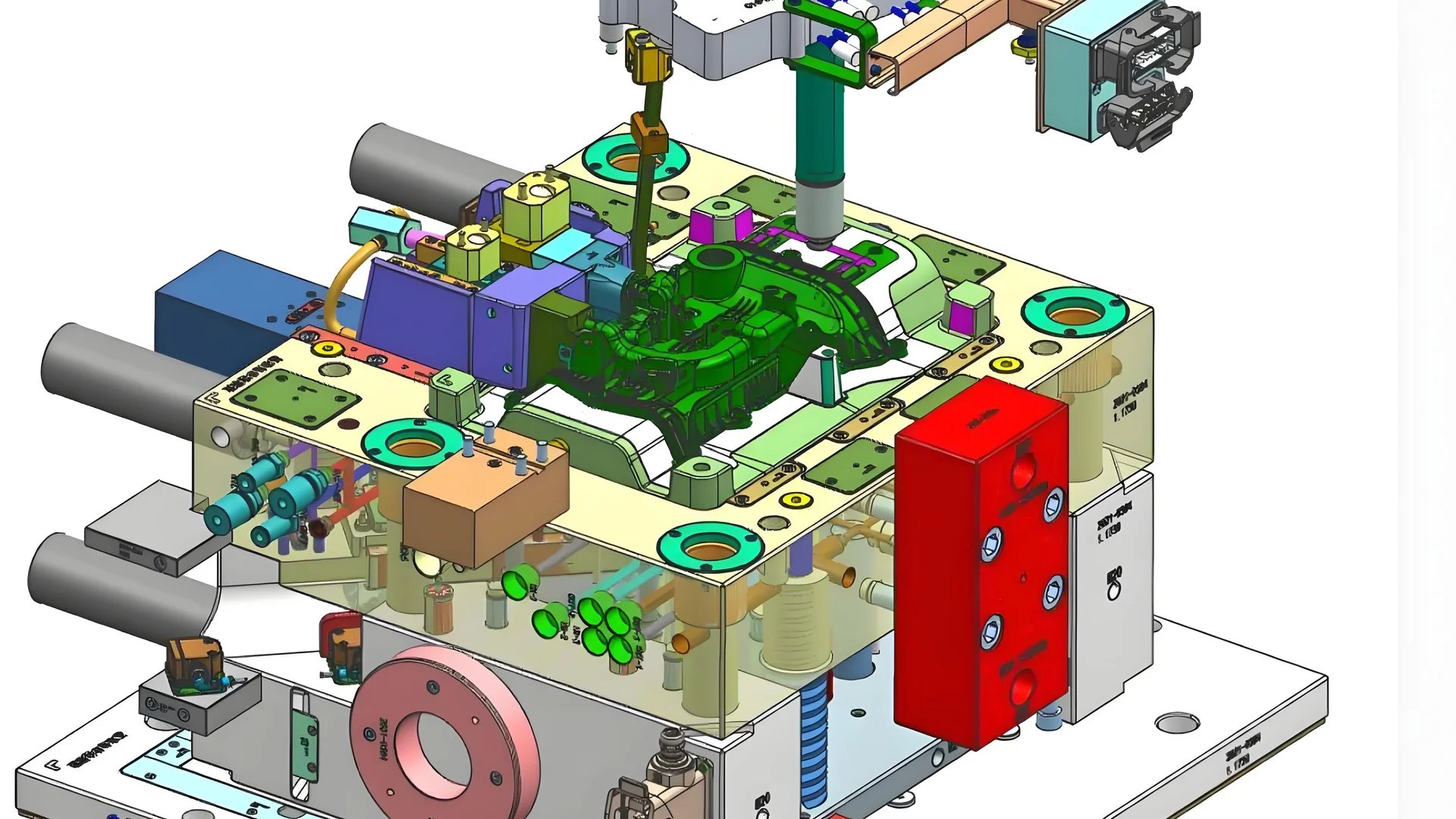
Selecting the Right Mold Material
Choosing suitable materials for the mold is a foundational step in optimizing mold design for ABS injection molding. ABS requires mold materials that can withstand high pressure and temperature. Common options include P20 steel7, known for its good processing performance and economical price, and 718 steel, which offers higher surface finish quality. The choice between these should be informed by the product’s surface quality requirements.
Designing Effective Cooling Systems
A well-designed cooling system is critical to maintain uniform mold temperature, which directly impacts productivity and product quality. Typically, water cooling systems are utilized, with cooling waterways arranged inside the mold to ensure effective heat dissipation. Considerations such as the diameter of the cooling channels (generally 8-12 mm) and their spacing (20-50 mm) are tailored to the product’s wall thickness and shape. Symmetrical positioning of the inlet and outlet ensures even water flow across the mold, which helps in achieving consistent cooling.
Ensuring Uniform Wall Thickness
Uniformity in wall thickness minimizes stress concentrations and warping during the molding process. For ABS products, a typical wall thickness ranges from 1-5 mm, depending on the product’s size and application. In products with complex shapes, gradual transitions in wall thickness are crucial to avoid stress concentrations that might lead to defects.
Parameter | Typical Range |
---|---|
Wall Thickness | 1-5 mm |
Cooling Channel Diameter | 8-12 mm |
Cooling Channel Spacing | 20-50 mm |
Mold Release Mechanism
The mold release mechanism should be designed to facilitate smooth demolding, preventing issues such as straining or deformation. The design of parting surfaces and ejector mechanisms should accommodate the product’s shape and structure, ensuring balanced release forces. Ejector mechanisms like ejector pins are generally used, but for larger or more complex products, alternatives like push plate ejectors may offer better results.
Gate Design Considerations
Selecting the appropriate gate design is vital for controlling the flow of molten ABS into the mold. Options include direct gating for faster filling but noticeable traces, side gating to reduce visible marks but potentially affecting appearance, and sprue gating for high-quality surfaces at a slower fill rate. The chosen method should align with both aesthetic and structural needs of the final product.
Optimizing each of these aspects ensures that ABS injection molding is not only efficient but also produces components that meet desired quality standards without defects.
ABS requires mold materials that withstand high pressure.True
ABS molds require strong materials such as P20 or 718 steel.
Direct gating offers slower fill rates for ABS molding.False
Direct gating allows quicker filling but might leave marks.
What Are Common Defects in ABS Injection Molding and How Can They Be Fixed?
Flaws in ABS injection molding might harm product quality. However, solutions probably solve these problems efficiently.
Common defects in ABS injection molding include insufficient filling, shrink marks, flow marks, fusion lines, and warp deformation. These can be fixed by adjusting injection pressure, speed, mold temperature, cooling time, and optimizing design parameters.
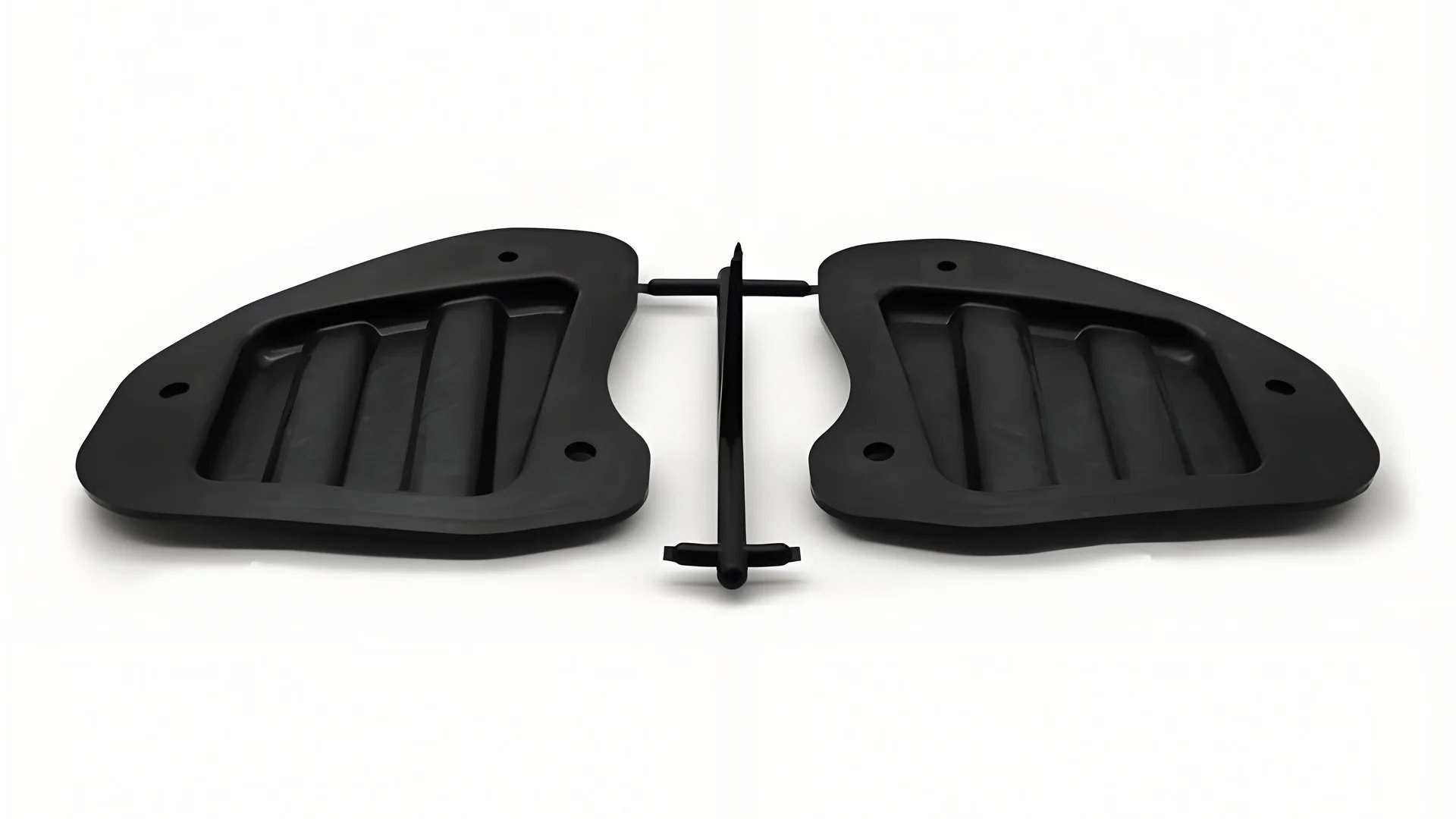
Understanding Common Defects in ABS Injection Molding
ABS (Acrylonitrile Butadiene Styrene) is prized for its toughness and surface finish, but like any material, it’s prone to certain defects during injection molding. Identifying these defects early can save costs and ensure product reliability.
1. Insufficient Filling
This occurs when the mold cavity is not completely filled with molten plastic. It results in incomplete parts that fail quality checks.
- Causes: Low injection pressure, slow injection speed, low mold temperature, or small gate size.
- Solutions: Increase injection pressure and speed. Raise the mold temperature and adjust the gate size to enhance flow.
2. Shrink Marks
These appear as surface depressions where the material has pulled back from the surface during cooling.
- Causes: Excessive shrinkage due to cooling or insufficient holding time.
- Solutions: Extend the holding time and cooling period. Modify the part design to ensure uniform wall thickness.
3. Flow Marks
Visible patterns on the surface caused by varying flow speeds of the plastic.
- Causes: High injection speed or low mold temperature.
- Solutions: Lower the injection speed and increase the mold temperature. Use a resin with better fluidity for smoother flow.
4. Fusion Lines
These lines are formed where two flow fronts meet but do not fuse properly, leading to weak spots.
- Causes: Multiple gates, slow injection speed, or uneven mold temperature.
- Solutions: Optimize gate placement, increase injection speed, and ensure even mold temperatures.
5. Warp Deformation
Warping results in products that are bent or twisted, making them unusable.
- Causes: Uneven shrinkage, excessive internal stress, short cooling time.
- Solutions: Improve part design to minimize stress points. Adjust processing parameters and extend cooling time.
Strategies for Effective Defect Management
To address these defects effectively, it is crucial to understand material properties8 and how they interact with mold design and processing parameters. Utilizing simulation software can help predict potential defects and refine processes before actual production begins.
In addition, continuous monitoring of machine conditions and regular maintenance can prevent anomalies that lead to defects. Educating personnel about common issues and their solutions enhances operational efficiency.
Implementing a robust quality control process ensures that products meet desired standards and reduces waste. Consider using statistical process control to identify trends and make data-driven decisions. This approach not only improves product quality but also boosts overall productivity in ABS injection molding operations.
Increasing injection pressure fixes insufficient filling.True
Elevated injection pressure helps fill the mold cavity fully.
Warp deformation is caused by high mold temperature.False
Warping happens because of unequal shrinking, not because of high mold temperatures.
Conclusion
Knowing ABS injection molding improves item quality and productivity. Grasping its details helps producers create top-notch parts. Delve into these ideas for the best outcomes.
-
Discover how varying speeds impact product quality.: The injection pressure of the ABS resin melt is in the range of 60 to 150 MPa. … 12O ~ 150MPa. The holding pressure of injection moulding … ↩
-
Explore innovative approaches to enhance mold efficiency.: ABS injection molding is one of the most popular plastic injection molding processes available today. During this process, liquefaction occurs at 221°F. ↩
-
Learn effective strategies to prevent common molding defects.: Often excessive temperature or low thermal conductivity of the molten material can worsen the problem. ↩
-
Learn how polyethylene’s properties compare with ABS for various applications.: ABS typically has a smooth, glossy surface, whereas PE has a waxier or smoother appearance. ABS is often used in applications emphasizing aesthetics, such as … ↩
-
Discover differences in durability and surface quality between these plastics.: A quick look at ABS vs. Polypropylene, their cons and pros, and how they square up against each other when it comes to plastic molding. ↩
-
Explore cost advantages of using ABS over polycarbonate in production.: Polycarbonate costs approximately 50% more than ABS, with both being relatively inexpensive materials. Standard PC sheet material typically … ↩
-
Discover why P20 steel is ideal for cost-effective mold making.: Physical Properties · Density: 0.284 lb/in3 (7861 kg/m3) · Specific Gravity: 7.86 · Modulus of Elasticity: 30 x 106 psi (207 GPa) · Thermal Conductivity: 24 Btu/ft/ … ↩
-
Understanding ABS properties helps in predicting molding behavior.: ABS Material Properties ; Mold Shrinkage – Flow (73 °F), 4.0e-3* to 7.0e-3** inches ; Water Absorption (24 hr., 73 °F), 0.16 to 0.25% ; Mechanical … ↩